精益造船——日本造船模式研究
再谈精益造船模式

造船模式通过消除造船过程中的无效时间来减少资源浪费 、 提 高资源利 用 0 0 5 , 2 7 ( o 6 ) : 7 6 - 8 0 在确定 中间产 品过程 中, 需 要探 讨价值 因数 , 即生产周 期 ( T) 、 生 2 [ 5 】 张明华 , 黄胜 . 精 益造船— — 日本造船 模 式研 究[ J ] . 船舶 工程 , 产 资源 ( N) 和 作业环 境 ( Q) , 是否有利 于生 产价值 ( P V ) 的上升。 P V - f
国内外主要船厂智能制造技术应用现状研究
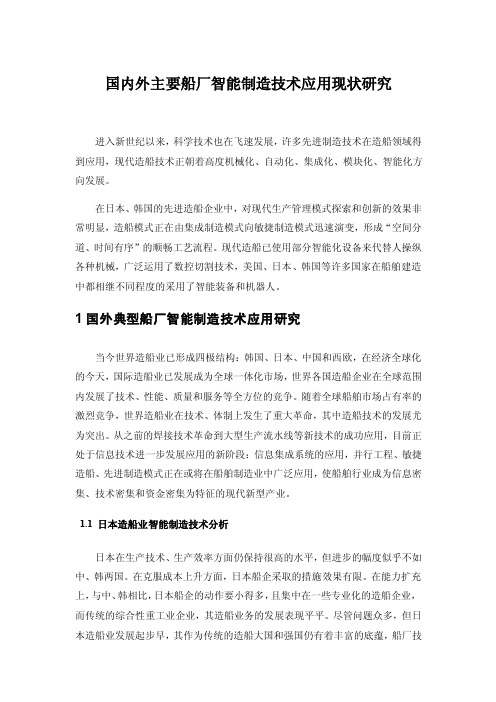
国内外主要船厂智能制造技术应用现状研究进入新世纪以来,科学技术也在飞速发展,许多先进制造技术在造船领域得到应用,现代造船技术正朝着高度机械化、自动化、集成化、模块化、智能化方向发展。
在日本、韩国的先进造船企业中,对现代生产管理模式探索和创新的效果非常明显,造船模式正在由集成制造模式向敏捷制造模式迅速演变,形成“空间分道、时间有序”的顺畅工艺流程。
现代造船已使用部分智能化设备来代替人操纵各种机械,广泛运用了数控切割技术,美国、日本、韩国等许多国家在船舶建造中都相继不同程度的采用了智能装备和机器人。
1国外典型船厂智能制造技术应用研究当今世界造船业已形成四极结构:韩国、日本、中国和西欧,在经济全球化的今天,国际造船业已发展成为全球一体化市场,世界各国造船企业在全球范围内发展了技术、性能、质量和服务等全方位的竞争。
随着全球船舶市场占有率的激烈竞争,世界造船业在技术、体制上发生了重大革命,其中造船技术的发展尤为突出。
从之前的焊接技术革命到大型生产流水线等新技术的成功应用,目前正处于信息技术进一步发展应用的新阶段:信息集成系统的应用,并行工程、敏捷造船、先进制造模式正在或将在船舶制造业中广泛应用,使船舶行业成为信息密集、技术密集和资金密集为特征的现代新型产业。
1.1 日本造船业智能制造技术分析日本在生产技术、生产效率方面仍保持很高的水平,但进步的幅度似乎不如中、韩两国。
在克服成本上升方面,日本船企采取的措施效果有限。
在能力扩充上,与中、韩相比,日本船企的动作要小得多,且集中在一些专业化的造船企业,而传统的综合性重工业企业,其造船业务的发展表现平平。
尽管问题众多,但日本造船业发展起步早,其作为传统的造船大国和强国仍有着丰富的底蕴,船厂技术实力、生产效率、船用配套装备等都处在很高的水平;而且日本航运业充足的需求也是支持其造船业发展的重要因素,由此,日本在全球造船业中的地位仍可维持。
日本在智能制造方面的基础研究做的比较到位,其中硬件方面的机器人技术和软件方面的数字化造船具有领先地位。
日本造船核心技术为何长盛不衰?
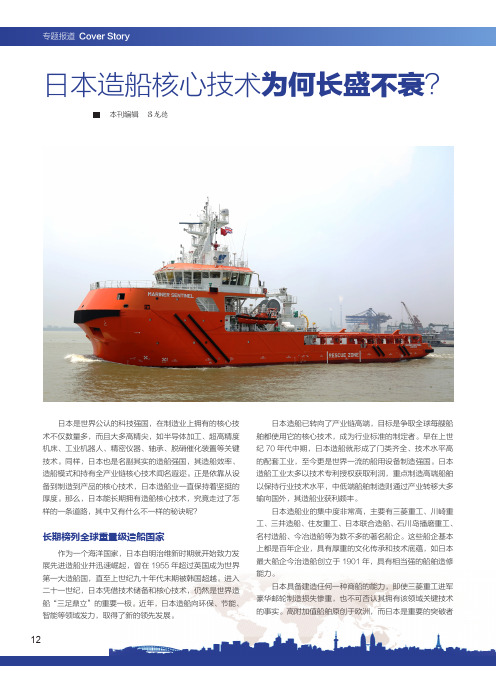
专题报道 Cover Story12日本造船核心技术为何长盛不衰?日本是世界公认的科技强国,在制造业上拥有的核心技术不仅数量多,而且大多高精尖,如半导体加工、超高精度机床、工业机器人、精密仪器、轴承、脱硝催化装置等关键技术。
同样,日本也是名副其实的造船强国,其造船效率、造船模式和持有全产业链核心技术闻名遐迩。
正是依靠从设备到制造到产品的核心技术,日本造船业一直保持着坚挺的厚度。
那么,日本能长期拥有造船核心技术,究竟走过了怎样的一条道路,其中又有什么不一样的秘诀呢?长期榜列全球重量级造船国家作为一个海洋国家,日本自明治维新时期就开始致力发展先进造船业并迅速崛起,曾在1955年超过英国成为世界第一大造船国,直至上世纪九十年代末期被韩国超越。
进入二十一世纪,日本凭借技术储备和核心技术,仍然是世界造船“三足鼎立”的重要一极。
近年,日本造船向环保、节能、智能等领域发力,取得了新的领先发展。
日本造船已转向了产业链高端,目标是争取全球每艘船舶都使用它的核心技术,成为行业标准的制定者。
早在上世纪70年代中期,日本造船就形成了门类齐全、技术水平高的配套工业,至今更是世界一流的船用设备制造强国。
日本造船工业太多以技术专利授权获取利润,重点制造高端船舶以保持行业技术水平,中低端船舶制造则通过产业转移大多输向国外,其造船业获利颇丰。
日本造船业的集中度非常高,主要有三菱重工、川崎重工、三井造船、住友重工、日本联合造船、石川岛播磨重工、名村造船、今冶造船等为数不多的著名船企。
这些船企基本上都是百年企业,具有厚重的文化传承和技术底蕴,如日本最大船企今治造船创立于1901年,具有相当强的船舶造修能力。
日本具备建造任何一种商船的能力,即使三菱重工进军豪华邮轮制造损失惨重,也不可否认其拥有该领域关键技术的事实。
高附加值船舶原创于欧洲,而日本是重要的突破者本刊编辑 吕龙德专题报道 Cover Story13之一,诸如LNG 船等高端船舶制造它就相当出色,其中汽车运输船更是呈垄断局面。
日本造船业发展趋势调研报告

日本造船业发展趋势调研报告一、引言日本造船业在过去的几十年里一直是全球市场的领导者,其卓越的技术实力和精细的工艺使日本的船舶产品在全球范围内享有盛誉。
然而,随着全球经济形势的变化和新兴市场的崛起,日本造船业面临着前所未有的挑战和机遇。
为了深入了解日本造船业的发展趋势,本文将从行业现状、技术发展、市场竞争和政策环境等方面进行调研分析。
二、行业现状近年来,随着全球经济的低迷和航运市场的萎缩,造船行业经历了严重的衰退。
然而,日本造船业凭借其深厚的技术积累和强大的创新能力,依然在全球市场中占据重要地位。
目前,日本造船业以高技术含量、高品质和定制化服务为优势,主要集中在邮轮、液化天然气船、汽车运输船等高附加值船舶领域。
三、技术发展日本造船业在技术研发和创新方面一直走在世界前列。
随着环保意识的提高和新能源技术的快速发展,日本造船业正在积极探索更加环保、高效和智能的船舶技术。
例如,在船舶设计方面,日本企业采用先进的数值模拟技术和优化算法,提高了船舶的能效和稳定性;在船舶制造方面,日本企业通过引入智能制造技术和机器人生产线,提高了生产效率和产品质量。
四、市场竞争虽然日本造船业在全球市场中仍具有显著的优势,但来自中国、韩国等国家的竞争压力正在逐渐增大。
这些国家在劳动力成本和市场规模方面具有优势,使得它们能够在一些中低端船舶市场占据一定的份额。
为了应对市场竞争,日本造船业需要进一步加强技术创新和品质管理,提高船舶产品的附加值和市场竞争力。
五、政策环境政府的政策对造船业的发展具有重要影响。
近年来,日本政府加大了对造船业的支持力度,通过提供研发资金、税收优惠等政策措施,鼓励企业加大技术研发和创新投入。
同时,随着全球环保法规的趋严,日本政府也在积极推动绿色造船技术的发展,为造船业的长远发展提供了有力保障。
六、未来展望未来,随着全球经济的复苏和航运市场的回暖,造船业有望迎来新的发展机遇。
日本造船业将继续保持技术创新和品质管理的优势,积极拓展高附加值船舶市场,提高企业核心竞争力。
精益造船计划管理体系研究和应用

精益造船计划管理体系研究和应用一、精益造船的起源与发展要说精益造船,得从精益生产说起。
精益生产嘛,大家应该都不陌生吧,就是那种讲究高效、减少浪费的管理理念。
你看,无论做啥生意,时间紧、任务重,如何不踩坑?怎么让钱花得更值、工作做得更快?“精益”这两个字就是为了解决这些问题诞生的。
它最早出现在日本,丰田公司一炮打响,后来迅速传遍了世界。
中国的造船行业,虽然历史悠久,但在现代化管理方面,一直稍微落后那么一点点。
这种情况,随着全球竞争的加剧,早就不能再拖了。
于是,精益造船应运而生。
说白了,就是要把那些不值一提的浪费给剔除掉,把工作做得更精细、更高效。
就像做饭一样,你不能只知道加盐,却忘了火候;你得精细,得知道什么时候开火,什么时候关火,甚至哪种锅最合适。
二、精益造船计划管理体系的实施要真说到怎么实施精益造船计划管理体系,那可真不是三言两语能讲清楚的事儿。
我们得把船厂的生产流程捋一捋,从最基础的原料采购、零部件制造,到最后的总装、验收,每一个环节都得精细规划。
而且要明确,计划管理不仅仅是一个“策划”的问题,更是一个“执行”的问题。
要落实到每一位员工的实际工作中,大家都得明白自己的责任和分工。
不管是工程师还是技工,每个人都是这个庞大机器的一颗小螺丝钉,缺了一颗,整个船厂的工作就会乱套。
精益造船的计划管理体系,可不仅仅是安排每天的生产任务这么简单。
它涉及到生产线的平衡、资源的优化利用、甚至包括供应商管理,简直是一个系统工程。
比如,船厂最头疼的就是交货期,一拖再拖的情况层出不穷。
结果就是,一家船厂忙得像热锅上的蚂蚁,工人们也是“上得了马,打不着枪”,想要的材料总是“迟到”,设备总是“罢工”。
而精益造船管理体系的出现,正是为了解决这些难题。
它要求每一项工作都得做到精确的时间控制,谁做什么、什么时候做,都得清清楚楚、明明白白。
每一块木板、每一根钢材,都必须在指定的时间出现在指定的位置。
三、精益造船的实际应用与效果讲到这儿,可能有人会问,精益造船的管理体系到底有没有用?答案是:有!前提是你得真心去执行,光说不做,那是没用的。
分段建造车间精益生产的分析

分段建造车间精益生产分析精益生产模式是目前世界上最先进的生产模式之一,它体现在制造业方面特别的明显,是制造成本最低的生产方式,日本的造船生产模式就是一个很好的代表,即以精益造船的模式f精细管理、精益求精的生产模式。
分段制造车间,是现代造船模式中的中间产品,分段的中间产品就是组件,组件的中间产品就是部件,部件的中间产品就是零件,零件的中间产品就是未加工好的工件(含切割件),未加工好的中间产品是已喷丸处理的板材,我们所要研究的是如何在从钢板库领料开始到分段完工的约37个工序里的运作路线、程序、加工方法、制造方法、技术准备文件、生产组织文件、技术工艺文件、员工的状态、设备的能力、场地的分布等。
一、分段建造流程材料仓库备料f领料f按分段分堆f抛丸f出料f分料中转f上车转运f 入跨…切割备料f上切割台…切割、记号、进托盘f转运加工(冷、热)f 二次加工卜入托盘f转运送料f部件分料排料f装焊打磨f划线切割f翻身f 校正f打包集配f配套转运f组件铺料f组件装焊打磨卜反身f校正f上胎架f一阶段安装f一阶段焊接f二阶段安装f二阶段焊接f测量切割f翻身f 焊接fQCf完整性安装校正f船检、船东直接生产一一直接为船体制作的作业内容间接生产一一不直接为船体制作的作业阶段和准备阶段共约37个主要程序,直接生产|15道,间接生产22道,吊运25道。
1、生产程序精益生产把产品生产全过程分成两大部分,一部分是直接生产时间,另一部分叫间接生产时间,传统的造船模式间接生产时间远远大于直接生产时间(有些专家讲造船70%的时间用在了等候与运输上,这不是无道理的,从有关的资料体现,我们的劳动量是日本人的3一5倍,过去我曾测算过我们是日本人的1 /4劳动效率,后经三年的努力,提高了接近一倍,也达不到日本人的一半,当然当时的设备、生产设计、体制等都相差太远),从上段可看到,直接生产的劳动只有15道,占约不到40%,从道理讲,我们可以提高生产效率1倍以上,用什么方法呢?这是我们提出的问题根源,用什么方法呢?这是我们共同研究要解决的根和源的方法。
造船精度管理的探索和实施

摘
要: 主要对造船精 度管理的实施方案 进行探索 , 将精度管理的过程贯穿到整个船体建造的生命周期里 , 通过
前期实施策划 、 中期落实前 道控制管理和后道 总组搭载定位操作 、 后期进行分析和改进的方法 , 逐步提 高船体建 造精度管理水平 。
关键 词 : 精度管理 ; 精度策划 ; 余量 ; 补偿量
消 除或减 少变形 。 1 . 4 施 工 图纸安 装信息 详细 施 工 图纸设计 过程 中对 每一 个分 段上 的构 件定
对 中国造船 业一 直 以来都 是采 取技术 封锁 。国 内船 厂经 历 了多年 的探 索 和 实践 , 也 形成 了一 些 开 展造 船精 度控 制 的基 本 方法 。但 国 内船 厂 与 日韩两 国等 船 厂在 造船 精度控 制方 面 尚存在 着较 大 的差 距 。
第 2期
江创宏 : 造船精度管理 的探索 和实施
3 7
生产 过程 中进 行 的 自我 控制 。 日本船 舶企 业 的员 工
度 管 理往往 就失 去作 用 。精度 管理 仅注重 现 场测量
管理 , 并 没有 精度 策 划 , 不 重 视 精 度 全 过程 控 制 , 精 度 测控 员大 多忙 于 测量 和 阶段 性 的整 改 分析 , 这样
1 日本 和韩 国造 船 精 度 管 理
日本 和 韩 国船 厂 重 视精 度 设计 的实 施 , 并 有专 门的《 建 造 精 度 控 制 图》 。这些 船 厂 已掌握 用 补偿 量 代替 余量 的设计 方 法 , 通过 设 计 将 精 度管 理 的理 念 和控 制方 法写 进 图 纸 , 从 源头 上 实 现 造船 的精 度
到 了一定 水平 , 其他 各 项 工 艺 的实 施 才 能 得 以发 展
分析精益造船在挖泥船建造中的应用

分析精益造船在挖泥船建造中的应用摘要:本文主要对精益造船在挖泥船建造中的应用进行分析和了解。
精益生产模式是当前工业界公认的最佳的一种生产组织体系和方式。
它成功地在世界掀起了精益管理的热潮,精益管理的思想已经在世界范围内给各类制造也带来了巨大的进步。
关键词:精益造船;挖泥船;建造;概述引言:疏浚工程业处于一轮高速发展中,挖泥船的市场需求量巨大,经济前景非常乐观。
然而长期以来,国内挖泥船建造水平不高,效益不佳的问题存在。
精益造船模式的出发点是通过消除造船过程中的无效时间(不增值部分)来减少资源浪费、提高资源利用率,从而获得缩短造船周期、降低造船成本、扩大造船产量和提高造船效益的结果。
一、造船精益管理的概述造船精度管理的定义是用数理统计的方法,对造船生产过程中的加工误差和焊接热变形的精度进行监督、控制和改进,用补偿量代替加工余量,减少造船加工、装配和焊接过程中的无效劳动,从而改善造船生产设计、造船计划和造船工艺的水平,提高造船的生产效率。
合理的精度要求不仅仅是保证产品质量的需要,它还直接关系到降低船舶建造成本,提高工艺过程的经济性。
过高的精度要求会使船体建造成本大大增加,这点容易为人理解然而,在船台装配精度要求不变的情况下,某一工序精度过低,则必然会影响下道工序而使修整工作量增加,其结果也会使生产成本增加,此点却容易被人忽略。
就船体构件或分段尺寸精度与成本之间的关系,英国船舶研究协会认为:如果所要求的质量标准不超出规定的各道工序的加工能力,则为控制质量而增加的成本对于船舶总成本来说,是微不足道的。
二、精益造船在挖泥船建造中的精度管理分析精益造船过程中,对于船体制造需要进行精度控制,否则在建造过程中就会由于焊接和加工热变形出现大量的加工误差,造成大量返修,直接影响了生产质量和进度直接影响了精益造船计划的执行。
造船精度管理是贯穿船舶建造全过程,通过对整艘船设定精度目标,并将精度目标层层分解落实到造船生产的各道主利用补偿量代替余量的办法控制建造过程中各种加工、切割、装配和焊按等,并经过天数次对精度实施过程进行数理统计分析,不断积累建造绎验数据,不断修错、浦逼近设定精度目标,最大化的减少无效劳动和不必要浪说迟到高液率,度、低成本的造船目的对现代造船的每道部必进行有数的尺于稻度控制,否则难以保证正常的生产过程和船舶的各性的于的液义来说,大型船、特种船和工作条件较悲劣的船母小集特种船舶和工作条件较悲劣的船角两种因素,松泥的前理在其建造中显得尤为重要。
- 1、下载文档前请自行甄别文档内容的完整性,平台不提供额外的编辑、内容补充、找答案等附加服务。
- 2、"仅部分预览"的文档,不可在线预览部分如存在完整性等问题,可反馈申请退款(可完整预览的文档不适用该条件!)。
- 3、如文档侵犯您的权益,请联系客服反馈,我们会尽快为您处理(人工客服工作时间:9:00-18:30)。
精益造船——日本造船模式研究发表时间:2006-4-20 张明华黄胜来源:《船舶工程》关键字:精益生产船舶造船模式先进制造技术信息化应用调查在线投稿加入收藏发表评论好文推荐打印文本通过对日本造船模式的研究,提出了精益造船模式,用有造船特征的精益生产理论,详细论述了造船生产过程中的精益生产方法,介绍了一种可供我国造船企业借鉴的现代造船模式。
1、引言1995年5月,中船总公司第二次缩短造船周期会议对现代造船模式做了如下定义:"以统筹优化理论为指导,应用成组技术原理,以中间产品为导向,按区域组织生产,壳舾涂作业在空间上分道、时间上有序,实现设计、生产、管理一体化,均衡、连续地总装造船"。
这一论述对现代造船模式作了很好的诠释。
但是在将近十年的时间里,我国船厂与世界先进造船企业的差距依然很大,在许多方面依然是"形似"不是"神似",即在实现现代造船模式的方法、途径和机理上仍然有许多需要提高的地方。
仔细观察日本制造企业,可以发现,几乎所有的制造业,无论是汽车、飞机、化工、计算机、家具,还是造船,其生产模式都惊人地相似,运作原理也基本相同。
许多国家的学者对日本制造业(特别是丰田汽车公司)的生产模式进行了研究,认为以丰田汽车公司为代表的生产模式是迄今为止世界上最先进、制造成本最低的生产模式,并把它定义为精益生产模式(Lean Production System)。
精益生产模式是目前世界上最先进的生产模式之一,它的成功掀起了精益管理的热潮,精益管理思想已经给各类制造业带来了巨大的进步,精益生产理论适用于所有制造企业。
日本造船业比汽车业发展更早更快,汽车业在 20 世纪 60 年代才达到国际水平[1],而造船业早在 1956 年就已经成为世界第一[2]了。
在发展过程中,造船业的生产模式与其它制造业相互取长补短,共同发展了今天的日本精益生产模式。
笔者认为,日本的造船模式是当今世界上最先进的造船模式,只要认真研究和学习日本造船业的生产模式,一定会对发展和提升我国造船企业的生产力水平起到积极的推动作用。
2、精益造船模式介绍[3~5]精益生产模式是满足市场和客户要求,获取更高利润的方法和途径。
它旨在通过全员的激励和努力,优化生产组织结构,去掉一切无效(不增值)的生产过程和环节,通过减少生产过程中的一切浪费来缩短生产周期,提高生产效率,降低生产成本,保证生产质量,从而获得好的产品利润。
"精益造船"就是以精益生产模式造船。
2.1 产品价值链(Product Value Chain)分析精益造船把产品生产全过程分成两大部分:一部分为有效时间(Value Added Time);另一部分为无效时间(Non-Value Added Time)。
传统造船模式中的无效时间远远多于有效时间。
产品生产的全部意义是为了满足客户的需要。
从满足客户需要的角度考虑,有效时间是客户需要的,无效时间是客户不需要的。
因此,任何生产过程中产生无效时间的现象就是浪费。
丰田汽车公司把生产过剩、次品、库存、人和物移动、过度加工、运输及人和物等工 7 种现象描述为无效时间内产生的浪费。
仔细分析船体制作过程(见图1),可以清楚地看到,任何无效时间都会造成生产停顿,产生浪费。
传统的造船模式往往注重提高作业加工的生产效率,精益造船模式更注重于缩短无效时间,减少中间环节的浪费,从而大大缩短生产周期。
这种主要通过缩短无效时间来缩短造船周期、提高造船效率、保证造船质量和降低造船成本的思想被称为"精益造船思想"。
图1 船体制作过程有效和无效时间分析2.2 单件流水作业(One-Piece Flow)为了扩大生产,传统造船模式追求设备利用率组织批量生产。
生产准备时间长和在制品库存多是组织批量生产的特征,生产过剩就成为必然。
造船生产的最大浪费就是生产过剩。
精益造船让每一个部件和中间产品做到连续不断地生产,按客户(内部和外部)的要求按时完成生产,不提前,也不拖后。
把相同类型的中间产品一件一件地连续不断地组织传送带式的生产流程,称为单件流水作业。
组织单件流水作业,做到连续不断生产,实行零库存管理,就可以减少生产过剩。
只要单件流水作业一出问题,就需要立即解决,否则生产就会停顿,直接影响后续生产。
比如,传统造船的板材和型材加工都是成批量的。
大量板材和型材加工完成后,存放在堆场里,然后按进度进行理料,再分类分批提供给构件装配、平面和曲面分段加工车间。
精益造船模式的板材和型材都是在工场直接按构件装配平面和曲面分道切割加工的,然后再连续不断地提供给构件装配、平面分段和曲面分段流水线,这样不但节约了大量的堆放场地和理料时间,减少了在制品库存和资金占用,同时大大缩短了生产周期。
由于连续不断的作业要求,今天切割加工好的材料,明天就用于装配和分段制作了。
一旦有质量问题,也能马上反馈解决。
在批量加工情况下,往往要一周后才会用到这批材料,才会发现质量问题。
那时候,可能同样的质量问题已经在其它许多地方发生,后患无穷。
单件流水作业的质量问题能够迅速反馈,马上解决,否则就会影响下道工序生产。
这样,作业者就学会了思考,提高了发现和解决问题的能力,许多好的预防措施、生产组织形式、工作标准也就应运而生,生产效率随之大大提高。
2.3 拉动计划体系(Pull System)传统造船模式通常由管理部门制定公司生产计划,然后层层下达计划,由下面制定具体的实施计划。
这样的计划要求纵向到底、横向到边,从上到下、从前向后地推动,是推动计划体系(Push System)。
推动计划体系要求计划策划人员必须熟悉全公司的情况和资源,否则计划就难以落实。
一般情况下,计划工作很难做得非常具体和细致。
这样,计划执行的随意性比较大,执行过程的控制比较难。
单件流水作业需要按照客户需求建立从后向前、由下而上的拉动计划体系。
由后道工序向前道工序提出订货计划,前道工序则严格按照后道工序的交货要求,不提前,也不拖后地安排生产。
在单件流水作业生产线上,每一道工序既是生产者,又是客户;既需要满足下一道工序的交货要求,同时又需要向上一道工序提出订货要求。
精益造船的单船生产是按照交船期和总体生产安排的要求,制定大合拢计划和分段制造计划。
然后从大合拢计划和分段制造计划出发,按平面分段和曲面分段、涂装和预舾装、板材和型材、管子加工等等,按照拉动原理从后向前一级一级地由作业者制定各自的作业、物料和劳动力计划。
然后由生产主管部门综合平衡,做到作业与物料计划、作业与劳动力计划的统一,最后汇总成全公司的年度和月度生产计划。
2.4 JIT 生产和无缺陷施工(Just in Time and Built-in Quality)JIT 生产(Just in Time)和无缺陷施工(Built-in Quality)是精益造船模式的两个重要理念,是保证质量、成本和周期目标实现的根本。
JIT 生产就是在需要的时候,按照需要的数量生产需要的产品。
组织 JIT 生产的最大优点是可以大大减少人工和物资的浪费,没有库存,没有闲置劳动力。
JIT 造船就是要组织单件流水作业生产线,运用成组技术和族制造原理,按照造船作业的阶段、类型和区域,组织柔性的相似的中间产品分道或流水的作业生产线,真正形成一件接着一件、按照生产节拍交付产品的传送带式生产。
造船的板材加工、型材加工、管材加工、构件装配、平面分段和曲面分段的生产都可以组织单件流水作业,其中间产品可以按零部件和组件来划分,也可以按分段和托盘来划分。
无缺陷施工就是要把所有的质量问题都消除在源头,这就需要实施造船精度管理和全员质量管理。
谁做谁检查,谁做谁负责修复缺陷。
要求作业者严格按作业标准一次作业合格,保证自检互检后的产品质量 100%合格,决不允许次品流入下道工序。
无缺陷施工的最大优点是把质量问题消除在源头,可节约大量人工检验和缺陷返修成本。
2.5 均衡生产和生产节拍(Level Production and Takt Time)为了保证连续生产,同时又能满足产品需求的节奏,需要组织均衡生产(Level Production),让生产处于一种稳定有序的状态当中,这就需要运用成组技术原理合理设计单件流水生产的作业量,计算出生产节拍(Takt Time)。
生产节拍也称为客户需求周期(Customer Demand Rate),可以描述为总生产时间除以客户需求数量,表示生产客户的一个产品所需的平均必要时间:生产节拍 = 总生产时间/客户需求数量对于造船,生产节拍可以是每半小时交付一个托盘的管子,或者每天合拢两个标准分段。
生产节拍是生产管理的一个目标,通过建立生产节拍组织均衡生产,让生产更加流畅。
生产节拍不一定等于生产周期。
比如,1.5 个小时可生产交付一个托盘的管子,而下道工序每2小时需要一个托盘的管子。
这样,生产周期就小于生产节拍。
如果满足生产节拍要求,生产能力就会放空,造成人员等工或设备能力闲置;如果上一工序生产连续不断,就会造成库存积压。
这两种情况都造成浪费。
反之,如果生产周期大于生产节拍,就需要加班或提前安排生产,储备一定库存,以满足生产节拍需要,无论加班或加大库存都需要增加成本。
因此,在组织均衡生产过程中,一定要使生产周期与生产节拍基本一致。
理想状态下,生产周期应该等于生产节拍。
按照生产节拍组织单件流水作业也可能出现不经济现象。
比如,A和B两种类型的分段需要预舾装,A分段要安装大量管子,B分段要安装大量结构件。
按照大合拢进度,交货次序分别为A,A,A,B,A,B,B,A,A,这种不规则的生产节奏可以满足船台大合拢要求,却给提供管子和结构件的前道工序带来忙闲不均。
为减少浪费,使前道工序能够实现连续不断的均衡生产,可以在不影响大合拢进度的情况下,适当调整分段装配次序为 A,A,B,A,A,B,A,A,B。
这样,管子、结构件以及 A、B 两分段都可以组织起均衡有节拍的生产。
同样,按照精益生产理论,造船分段制造也完全可以组织节拍生产(图2)。
图2 均衡有节拍的分段制作组织均衡的节拍生产能够大幅度减少浪费,提高劳动生产率,因此,要尽可能组织有生产节拍的流水作业。
为了适应造船流水作业,劳动组织形式也要按照阶段、类型、区域来划分,如内业(切割加工)、构件、分段装配,外业(船体大合拢)、管子、机装、船装、电装、内装、涂装等。
实行一工多能的岗位技能制度,以便于劳动力合理使用,也便于在组织节拍生产的过程中合理调整作业量。
2.6 4S 管理(4S Control)好的工作场所应该清洁、整齐、稳定而有序,且有一系列浅显易见的工作标准,保证所有工作都处于有标准的可控状态。
只要系统出现一点偏离工作标准的现象,这种偏离就会在系统中迅速暴露。