粉体混合原理及常见工艺难题
固体药物制剂工艺的混合过程及混合机理
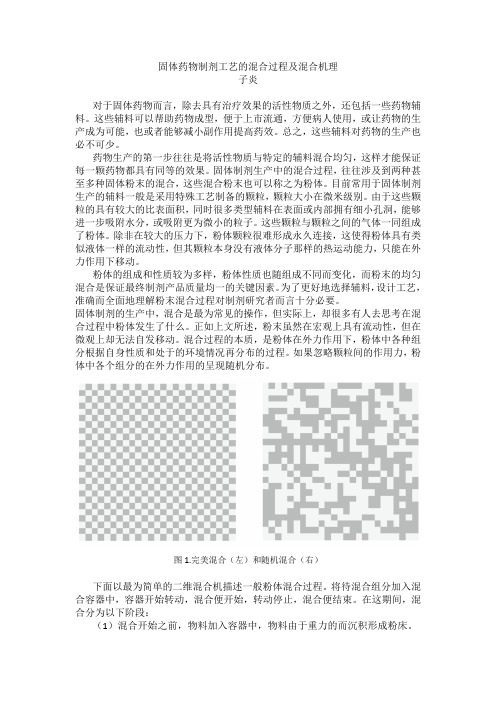
固体药物制剂工艺的混合过程及混合机理子炎对于固体药物而言,除去具有治疗效果的活性物质之外,还包括一些药物辅料。
这些辅料可以帮助药物成型,便于上市流通,方便病人使用,或让药物的生产成为可能,也或者能够减小副作用提高药效。
总之,这些辅料对药物的生产也必不可少。
药物生产的第一步往往是将活性物质与特定的辅料混合均匀,这样才能保证每一颗药物都具有同等的效果。
固体制剂生产中的混合过程,往往涉及到两种甚至多种固体粉末的混合,这些混合粉末也可以称之为粉体。
目前常用于固体制剂生产的辅料一般是采用特殊工艺制备的颗粒,颗粒大小在微米级别。
由于这些颗粒的具有较大的比表面积,同时很多类型辅料在表面或内部拥有细小孔洞,能够进一步吸附水分,或吸附更为微小的粒子。
这些颗粒与颗粒之间的气体一同组成了粉体。
除非在较大的压力下,粉体颗粒很难形成永久连接,这使得粉体具有类似液体一样的流动性,但其颗粒本身没有液体分子那样的热运动能力,只能在外力作用下移动。
粉体的组成和性质较为多样,粉体性质也随组成不同而变化,而粉末的均匀混合是保证最终制剂产品质量均一的关键因素。
为了更好地选择辅料,设计工艺,准确而全面地理解粉末混合过程对制剂研究者而言十分必要。
固体制剂的生产中,混合是最为常见的操作,但实际上,却很多有人去思考在混合过程中粉体发生了什么。
正如上文所述,粉末虽然在宏观上具有流动性,但在微观上却无法自发移动。
混合过程的本质,是粉体在外力作用下,粉体中各种组分根据自身性质和处于的环境情况再分布的过程。
如果忽略颗粒间的作用力,粉体中各个组分的在外力作用的呈现随机分布。
图1.完美混合(左)和随机混合(右)下面以最为简单的二维混合机描述一般粉体混合过程。
将待混合组分加入混合容器中,容器开始转动,混合便开始,转动停止,混合便结束。
在这期间,混合分为以下阶段:(1)混合开始之前,物料加入容器中,物料由于重力的而沉积形成粉床。
(2)仪器开始运转,容器的运动对粉末中粒子产生了作用力,粒子之间的作用力被激活,粒子之间形成间隙,这些间隙使得不同组分的粒子的穿插和交织成为可能。
粉体混合技术和原理分析
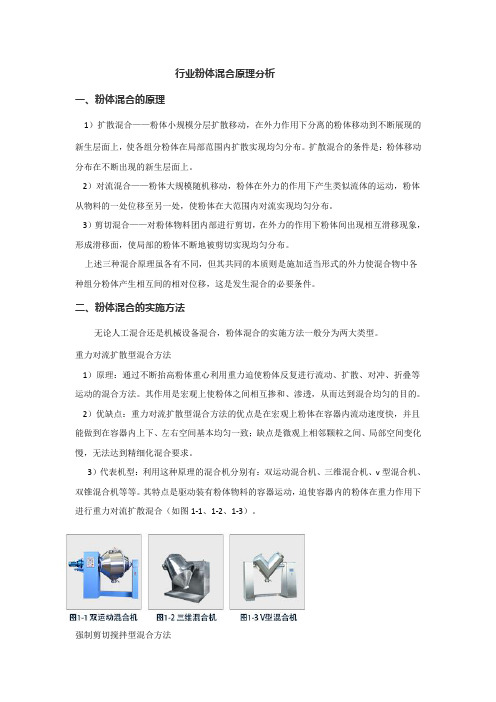
行业粉体混合原理分析一、粉体混合的原理1)扩散混合——粉体小规模分层扩散移动,在外力作用下分离的粉体移动到不断展现的新生层面上,使各组分粉体在局部范围内扩散实现均匀分布。
扩散混合的条件是:粉体移动分布在不断出现的新生层面上。
2)对流混合——粉体大规模随机移动,粉体在外力的作用下产生类似流体的运动,粉体从物料的一处位移至另一处,使粉体在大范围内对流实现均匀分布。
3)剪切混合——对粉体物料团内部进行剪切,在外力的作用下粉体间出现相互滑移现象,形成滑移面,使局部的粉体不断地被剪切实现均匀分布。
上述三种混合原理虽各有不同,但其共同的本质则是施加适当形式的外力使混合物中各种组分粉体产生相互间的相对位移,这是发生混合的必要条件。
二、粉体混合的实施方法无论人工混合还是机械设备混合,粉体混合的实施方法一般分为两大类型。
重力对流扩散型混合方法1)原理:通过不断抬高粉体重心利用重力迫使粉体反复进行流动、扩散、对冲、折叠等运动的混合方法。
其作用是宏观上使粉体之间相互掺和、渗透,从而达到混合均匀的目的。
2)优缺点:重力对流扩散型混合方法的优点是在宏观上粉体在容器内流动速度快,并且能做到在容器内上下、左右空间基本均匀一致;缺点是微观上相邻颗粒之间、局部空间变化慢,无法达到精细化混合要求。
3)代表机型:利用这种原理的混合机分别有:双运动混合机、三维混合机、v型混合机、双锥混合机等等。
其特点是驱动装有粉体物料的容器运动,迫使容器内的粉体在重力作用下进行重力对流扩散混合(如图1-1、1-2、1-3)。
强制剪切搅拌型混合方法1)原理:利用容器内的运动桨叶强制对粉体进行反复地搅拌、剪切等运动的混合方法。
其作用是微观上不断打散粉体颗粒之间的相邻关系,让粉体颗粒充分地移动、互换,达到粉体混合均匀的目的。
2)优缺点:强制搅拌剪切型混合方法的优点是微观上能够达到精细化混合均匀的目的,并因粉体内部流动效率高,而使混合效率比较高;缺点是没有有效措施实现容器内上下、左右宏观上整体均匀。
粉末混合工艺
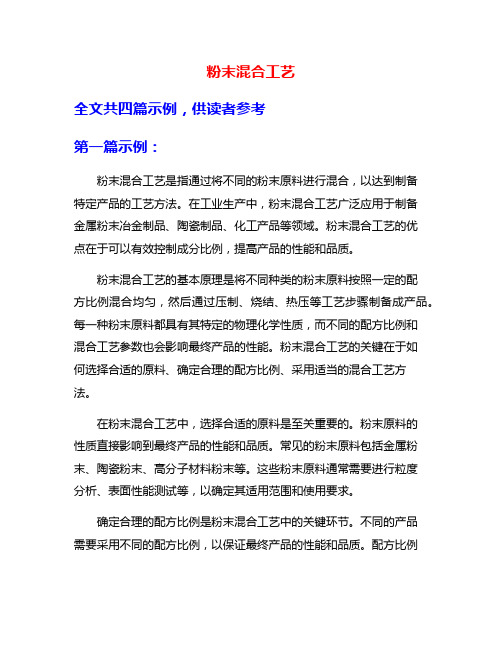
粉末混合工艺全文共四篇示例,供读者参考第一篇示例:粉末混合工艺是指通过将不同的粉末原料进行混合,以达到制备特定产品的工艺方法。
在工业生产中,粉末混合工艺广泛应用于制备金属粉末冶金制品、陶瓷制品、化工产品等领域。
粉末混合工艺的优点在于可以有效控制成分比例,提高产品的性能和品质。
粉末混合工艺的基本原理是将不同种类的粉末原料按照一定的配方比例混合均匀,然后通过压制、烧结、热压等工艺步骤制备成产品。
每一种粉末原料都具有其特定的物理化学性质,而不同的配方比例和混合工艺参数也会影响最终产品的性能。
粉末混合工艺的关键在于如何选择合适的原料、确定合理的配方比例、采用适当的混合工艺方法。
在粉末混合工艺中,选择合适的原料是至关重要的。
粉末原料的性质直接影响到最终产品的性能和品质。
常见的粉末原料包括金属粉末、陶瓷粉末、高分子材料粉末等。
这些粉末原料通常需要进行粒度分析、表面性能测试等,以确定其适用范围和使用要求。
确定合理的配方比例是粉末混合工艺中的关键环节。
不同的产品需要采用不同的配方比例,以保证最终产品的性能和品质。
配方比例经常通过试验和实践来确定,通常需要考虑到原料的化学成分、物理性质、烧结性能等因素。
混合工艺方法的选择也对最终产品的性能有重要影响。
常见的混合工艺方法包括机械混合、溶液混合、气液混合等。
机械混合是最常用的混合工艺方法,通过搅拌、研磨等机械力作用将粉末原料混合均匀。
溶液混合则是将粉末原料溶解在溶剂中,再进行混合。
气液混合则是将气体和液体一起混合,常用于颗粒状粉末原料的混合。
粉末混合工艺是一种重要的工艺方法,广泛应用于工业生产中。
通过选择合适的原料、确定合理的配方比例、采用适当的混合工艺方法,可以制备出高性能、高品质的产品。
粉末混合工艺的发展也为工业生产提供了更多的可能性,促进了产品的创新和升级。
希望随着科技的不断进步,粉末混合工艺能够得到更大的发展和应用。
第二篇示例:粉末混合工艺是工业生产中常用的一种工艺方法,它主要用于将不同性质的粉末原料混合在一起,以制备出符合特定要求的混合物。
粉体刷筛混合技术

粉体刷筛混合技术1 背景介绍粉体混合是磨料、磨具、冶金、化工、食品、医药、饲料和陶瓷等行业中常见的操作,现有常用的粉体混合技术有三维混合、双锥混合、球磨混合、双运动混合等,其原理是通过搅拌、混合容器运动带动粉末颗粒在混合容器中运动,使不同成分的粉体颗粒在混合容器中随机分布,使混合容器中的粉体不均匀性逐渐降低,进而达到一定的均匀程度,其混合存在以下缺点。
耗时长。
通过运动中粉体颗粒的随机分布获得均匀性,这需要反复地长时间的运动,才能达到一定的均匀度。
有夹生。
受混合原理的缺陷、受混合容器边角等区域的影响、物料特性(黏性、附着性等)、静电等影响,混合容器中不可避免地存在不参与混合或运动不充分的部分,形成物料夹生以及部分区域不均匀。
质量稳定性差。
物料和生产环境的温度和湿度以及物料特性(黏性、附着性等)对混料工艺影响较大,尤其是季节性温度、湿度变化,影响混料的均匀性,导致生产质量波动。
为了解决现有粉体混合技术的上述缺点,我们提出粉体刷筛混合技术的概念模型。
并制作对应的自动混料装置进行验证,确定刷筛混合技术相对于现有的混合技术耗时可降低一半,可消除夹生现象,提高质量的稳定性。
2 粉体刷筛混合技术2.1 粉体刷筛混合技术原理刷筛混合技术原理为:根据粉体粒度,选择合适目数的特制筛网,将各种粉末通过刷子过筛,刷子旋转一圈则各种粉末通过筛网下漏一部分,在接料容器中形成一个薄层,刷子不断旋转,即可使粉末在接料容器中形成一个个薄层实现交叉混合,将粉体多次过筛即可快速完成均匀混合。
刷筛混合技术原理图如图1所示(1为各种混合的粉末原料,2为特制筛网,3为定制旋转刷,4为接料容器,5为层层交叉的混合物料)。
2.2 粉体刷筛混合技术优点现有粉体混合设备多为二维混合机、“V”型混合机、双锥混合机、双螺旋锥形混合机、卧式无重力混合机、卧式犁刀混合机、卧式螺带混合机、三维混合机、双运动混料机。
现有粉体混合技术的原理为将粉末原料装入混料容器中,驱动容器运动或搅拌容器,使容器内各种粉末相互扩散运动,实现混合。
混合机设备工艺原理

混合机设备工艺原理混合机是混合固体粉末和液体的一种设备,用于制造各种不同种类的化工产品,例如颜料、染料、食品、药品等。
混合机的工艺包括干混和湿混两种类型,根据产品的不同需要,可以选择使用不同的混合方式。
干混方式干混方式是指将不同种类的固体粉末混合在一起,并通过混合机设备进行混合。
该方式适用于易于分散和均匀的粉末,如颜料、干燥剂、填料等。
干混工艺流程1.原料准备:将需要混合的原料粉末按照配比准备好;2.加入混合机:将原料粉末加入已经启动的混合机;3.混合:等待一定的混合时间,让粉体充分混合;4.取出混合好的粉末:将混合后的粉末从混合机中取出;5.检测:对混合好的粉末进行质量检测和分析。
干混工艺优点1.操作简单,成本低;2.可以混合不同种类的粉末;3.混合速度快,可大量生产。
干混工艺缺点1.需要有良好的流动性;2.粉末固定颗粒大小,难以混合大小不一的粉末;3.温度控制困难,混合过程可能会引起热量,影响混合效果。
湿混方式湿混方式是将液体溶液和固体粉末混和在一起,通过混合机装置将液体均匀地涂覆到粉末表面,形成固体颗粒,然后将其干燥成所需产品。
该方式适用于液体浓度不高的环境,液体一般是水或溶剂。
湿混工艺流程1.原料准备:将需要混合的液体和固体粉末分别准备好;2.加入混合机:将计量好的液体和固体粉末加入混合机;3.混合:通过混合机装置将液体均匀地涂覆到粉末表面,形成固体颗粒;4.干燥:将湿混后的颗粒干燥成所需产品;5.检测:对混合好的颗粒进行质量检测和分析。
湿混工艺优点1.可以混合不同种类的粉末,也可以混合极小颗粒;2.液体不仅可以润湿粉末,还可使其粘结在一起;3.操作简单,易于控制。
湿混工艺缺点1.需要进行干燥处理,增加了设备和时间成本;2.对混合通气性和孔隙度影响较大,影响混合效果;3.对液体浓度及配合比例要求苛刻。
混合机设备原理混合机是利用干混和湿混方式将液体和粉体混合在一起。
混合机设备包括混合机主机、电控柜、螺旋加料机、进出料口等。
粉体合成法总结
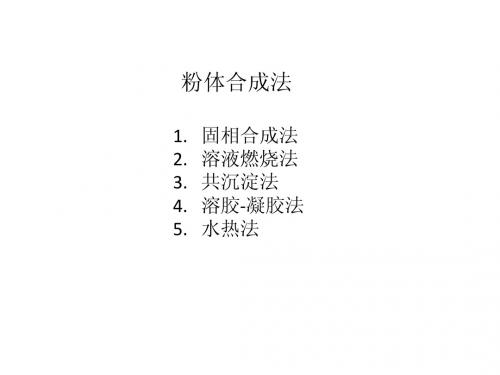
3. 粉体表征:德拜-谢乐公式(Scherrer公式) 计算晶粒尺寸:
D=Kλ/Bcosθ
K为Scherrer常数,其值为0.89 D为晶粒尺寸(nm) B为积分半高宽度,转化为弧度(rad) θ为衍射角 λ为X射线波长,为0.154056 nm
要点
1. 扫描速度有影响,要尽可能慢。一般2如硝酸铵,影响粉体形貌和粒径。事实上, 助燃剂用量影响最终燃烧类型(smothering, volumetric, self-propagating, or mixed-combustion type),进一步影 响最终的预烧
三.共沉淀法(以SDC制备为例)
1. 将溶解的金属离子以一定的速度滴入碳酸盐溶液中, 形成均匀的碳酸盐沉淀,洗涤,烘干,灼烧,最终形 成复合氧化物Ce0.8Sm0.2O1.9 反应方程式: 沉淀步:0.8Ce(NO3)3· 2O + 0.2Sm(NO3)3· 2O+ (NH4)2CO3 6H 6H x → Ce0.8Sm0.2(OH)CO3· H2O 煅烧步:Ce0.8Sm0.2(OH)CO3· H2O → Ce0.8Sm0.2O1.9 + H2O x +CO2 2. 控制参数:碳酸铵与金属离子摩尔比R影响前驱溶液组分、 沉淀完全程度和粒子形貌。一般,R较大时(R >10),得 到的粉体为棒状;R较小时(2 ~3),粉体为球形。R过小, 则沉淀不完全
6.材料中的晶粒大小并不完全一样,所得实为不同大小晶
粒的平均值。又由于晶粒不是球形,在不同方向厚度不同, 由不同衍射线求得的D常是不同的。一般求取数个(如n个) 不同方向(即不同衍射峰)的晶粒厚度,取平均值得晶粒尺 寸,据此亦可估计晶粒外形。
四.溶胶-凝胶法
1. 前驱体在液相下均匀混合反应形成稳定的溶胶体系, 放置转变为凝胶,之后借助蒸发或萃取除去液体介质 溶胶的起始原料可以是金属无机盐、金属有机盐、金 属有机络合物或金属醇盐 2. 络合剂:配体电负性控制电子转移方向。如在水体系 中,选择电负性小于水的配体(如羧酸根离子),电子 由配体向水转移,配体负电荷减少,与金属离子形成 稳定的复合物 3. 络合剂、溶剂与金属离子的比例也是影响反应动力学、 凝胶形成时间和产物成相及形貌的重要因素
粉体混料器文献
粉体混料器文献粉体混料器是一种广泛应用于工业生产中的设备,用于混合和均匀分散粉体物料。
本文将介绍粉体混料器的原理、分类、应用领域以及发展趋势。
一、粉体混料器的原理粉体混料器通过机械运动和流体力学原理实现粉体物料的混合。
其主要原理包括:1. 机械运动:粉体混料器中的搅拌装置通过旋转、翻转或振动等运动方式,使粉体物料发生相对位移,从而达到混合的目的。
2. 流体力学原理:粉体物料在混料器中经过搅拌装置的作用,形成了复杂的流动状态,包括对流、弥散、剪切等,促进了物料之间的相互作用和混合。
二、粉体混料器的分类粉体混料器根据不同的混合原理和结构特点,可以分为以下几类:1. 强迫混合器:通过外力的作用,将粉体物料强制进行混合。
常见的强迫混合器有搅拌机、螺旋传送机、刮板混合器等。
2. 自由混合器:粉体物料在混料器中进行自由流动和碰撞,实现混合。
常见的自由混合器有容器式混合器、喷射混合器等。
3. 流化床混合器:粉体物料通过气体的流动形成流化床,在流化床中实现混合。
流化床混合器具有高效、连续运行等优点。
4. 旋转桶混合器:通过旋转桶体使粉体物料进行多向、多轴向的运动,实现混合。
旋转桶混合器适用于对物料要求较高的混合过程。
三、粉体混料器的应用领域粉体混料器在许多工业领域中都有重要应用,特别适用于以下几个方面:1. 化工领域:粉体混料器广泛应用于颜料、染料、塑料、橡胶等化工物料的混合过程。
2. 医药领域:药物的制备过程中需要对不同的成分进行混合,粉体混料器在制药工业中扮演着重要角色。
3. 食品领域:粉体混料器可以用于混合面粉、糖粉、调料等食品原料的加工。
4. 矿山领域:矿石选矿和冶炼过程中,常需要将不同粒度和成分的矿石进行混合,粉体混料器可以满足这一需求。
四、粉体混料器的发展趋势随着科学技术和工业生产的不断发展,粉体混料器也在不断改进和创新。
未来粉体混料器的发展趋势有以下几个方面:1. 数字化控制:通过引入自动化和智能化技术,提高设备的操作精度和稳定性,实现对混合过程的精确控制。
粉体混合及输送讲解
气力输送特点:
输送过程为密闭式,无粉尘外扬和尘爆,安全可靠,改善了劳 动条件。输送线路简单、灵活,输送距离较大,吨公里运输成本低。 设备简单,投资低。
主要缺点:动力消耗大,噪音大,对物料的粒度(<30mm)、均匀 性、黏度、温度等有一定要求,使用于短途输送。
刮板输送机:在物料装卸、食品、轻工、煤炭、水泥等行业中。 主要种类:普通刮板输送机、埋刮板输送机两种。
刮板输送机
2.6.2气力输送
气力输送也称为管道输送,它是利用气体的流动动能 和压能,携带粉体物料沿管道从一处输送到另一处。
广泛用于各个行业,伴随无菌、卫生、防尘、便捷、 高质量、自动化等高标准工艺要求,气力输送将越来 越成为首选。
带式输送机的输送能力理论计算散体物料输送量:
Q KCvb
式中:
Q ——带式输送机的输送量,t/h;
K ——带上物料断面修正系数,查表;
C ——输送带倾斜角修正系数,查表 ;
——物料堆积密度,t/m3 ;
v ——输送带线速度,一般输送作业取0.8~2.5m/s,
产品检查或分选时取0.05~0.1m/s;
2.5 粉体的混合
物料的混合是最古老的生产工艺过程之一
(1)为了创造良好的反应条件而混合:如水泥原料、 陶瓷原料;
(2)为了提高强度和性能的混合:如冶金原料、玻璃原料; (3)为了提高药效的混合:如制药、药剂、复合药物; (4)为了提高味道和食欲的混合:如食品、烹饪等。
混合类型:
固体与固体、固体与液体、液体与液体、液体与气体、 固体-液体-气体
(4)胶带和螺旋输送为主: 如:煤炭、冶金等。
粉体混合机的分类原理和阐述
【粉体混合机的分类原理和阐述】金昶泰粉体混合机一般用于粘性或有凝聚性的粉粒体的混合以及粉粒体中添加液体及糊状物料的混合,随着中国工业的不断发展,混合系统及混合设备的发展将越来越强大。
混合覆盖着整个工业领域,如化工、食品、建材、药品、化肥,我们每天每时使用的产品在生产中至少有一步混合工艺。
一、混合原理及概述:混合时要求所有参与混合的物料均匀分布。
混合的程度分为理想混合、随机混合和完全不相混三种状态。
各种物料在混合机械中的混合程度,取决于待混物料的比例、物理状态和特性,以及所用混合机械的类型和混合操作持续的时间等因素。
混合包括自流混合和机械混合。
自流混合指物料间运动,通过自身摩擦达到最后的均匀混合;机械混合指物料通过机械强制作用达到最后的均匀混合。
一般气体混合为自流混合;三维混合设备混合为自流混合与机械混合的结合;所有混合中混合容器不运动的混合均为机械混合。
二、粉体混合机种类粉体混合机的种类繁多,本文主要就机械混合设备中目前中国市场上常用设备双螺旋锥形混合机,卧式无重力混合机,卧式犁刀混合机,卧式螺带混合机作分析:(一)双螺旋锥形混合机A、混合空间为倒圆锥型,桶体内有两条、三条或单条螺旋轴在自转的情况下又沿着桶壁公转,电机减速机等动力装置处于混合机的上端。
B、混合物料适用范围大,对混合的物料密度偏差,粒径偏差要求不很严格,易控制物料的摩擦起热或起静电 C、混合物料时对晶体的破坏作用小。
D、设备混合时动力要求低,同样型号的设备电机功率大大降低。
E、设备型号可以扩大到很大,中国国产在用最大为30立方。
F、混合时间相对比较长,但大型设备制造成三螺旋形式,可以大大缩短混合时间。
G、主要应用与粉体与粉体的混合,可以在混合时往物料中喷入大量的液体,但混合的整个过程中物料体现为固态粉体,应用例染料、味精、添加剂、塑料粒子等。
粉体混合(均化)原理及混合质量分析
粉体混合(均化)原理及混合质量分析粉体混合(均化)原理及混合质量分析一、概述粉体混合(均化)就是指二种以上的固态粉体物料在外力的作用下,使其不均匀性降到最低的过程。
例如药品生产过程的总混就是让药品的有效成份能均匀的分布到辅料内,满足生产质量的要求。
二、混合(均化)机理由于粉体均化目的不一样,对均化的要求和评价方式也不完全一样,均化的途径也是不一样的,但均化的过程的基本原理是基本相同的(这里主要讲固态粉体物料的均化混合和评价),归纳起来,主要有三种:1.对流混合:物料的团块从物料的一处移动到另一处,类似于流体的对流。
2.扩散混合:分离的粒子分散到不断展现的斜面上,如同一般的扩散作用那样,相互掺和、渗透而得到均匀的混合。
3.剪切混合:在物料团堆内部,粒子之间的相对移动,在物料中形成若干滑动面,像薄层状的流体一样相互混合和掺和。
三、混合的随机性以粒度相同的两种等量物料固体A和固体B为混合例,如A与B 的密度相同,在理论上达到完全的混合状态,似应十分的简单,只要使A和B相互交错排列即可,即达到完全的理想的混合。
但A是B的一倍的量,则必须有两个A粒子与一个B粒子排列在一起。
有若A与B的密度不同,B为A的两倍,就必须一个A与2粒B并列。
这样一来绝对的均化在工业生产中就不大可能出现了,那么最佳的混合的状态就是无序的不规则排列了,一般认为混合的过程就是一个“随机过程”,也称“概率混合”,他能所达到的最佳程度称为随机完全混合。
实际的混合问题比上述的情况要复杂的多,不仅颗粒的大小是不均匀的,密度也不相同,而且影响固体粒子混合的固体粉料特性远远不止密度和粒度两项,还有混合机内(堆料内)的混合作用(指复杂的混合运动的状态)。
三、影响混合的因素由于混合的物料性质和运动的方式等状态在混合过程中的改变,使混合的过程不能达到最佳混合状态,尤其是较细的粒子,由于粉体的凝聚以及静电的效应的原因,产生了逆混合均化的现象称为反混合,也叫偏析。
- 1、下载文档前请自行甄别文档内容的完整性,平台不提供额外的编辑、内容补充、找答案等附加服务。
- 2、"仅部分预览"的文档,不可在线预览部分如存在完整性等问题,可反馈申请退款(可完整预览的文档不适用该条件!)。
- 3、如文档侵犯您的权益,请联系客服反馈,我们会尽快为您处理(人工客服工作时间:9:00-18:30)。
粉体混合原理及常见工艺难题
文章阐述了粉体混合的机理和影响混合的主要物理特性。
总结了粉体混合在实践过程常见的工艺难题,并对如何解决进行了探讨。
标签:粉体混合;颗粒;机理;影响因素
混合是将不同物理性质和化学性质的颗粒在空间上分布均匀的过程[1],是两种以上的固态粉体物料在外力的作用下,其不均匀性降到最低的过程[2]。
如对粉末冶金生产而言,粉体混合質量将直接影响粉末冶金零件的内在质量。
1 混合的机理
粉末混合的方法和所用的设备不一样,混合的效果肯定不一样,但是混合机理是基本相同的。
(1)扩散混合:粉体小规模分层扩散移动,在外力作用下分离的粉体移动到不断展现的新生层面上,使各组粉体在局部氛围内扩散实现分布均匀。
(2)对流混合:粉体大规模的随机移动,粉体在外力作用下产生类似流体的运动,粉体从物料的一处移至另一处,使粉体在大范围内对流实现均匀分布。
(3)剪切混合:对粉体物料团内进行剪切,在外力的作用下粉体间出现相互滑移现象,形成滑移面,使局部的粉体不断被剪切实现均匀分布。
以上三种混合原理虽各有不同,但是共同的本质则是施加适当形式的外力使混合物中各种组分粉体产生相互间的相对位移,这是发生混合的必要的条件。
不少学者把粉体混合的各个阶段大致用图1来标示[3]。
从图中分析得出,粉体混合的第Ⅰ阶段表现为宏观整体混合很快,为对流混合;第Ⅱ阶段的混合速度有所减慢,是对流和剪切的共同作用阶段;第Ⅲ阶段时,粉体的混合均匀度在某一值上下波动,表明粉体的混合与分离相平衡,粉体处于微观阶段,为扩散混合阶段[4]。
由于粉体本身的物化性质不同、设备结构与操作条件的不同,实际生产中粉体的混合过程是一个很复杂的过程,不仅可能三种混合方式同时存在,而且混合的常常伴随着粉体颗粒的分离。
(4)混合的随机性:以粒度相同的两种等量物料固体A和固体B混合为例,如A与B的密度相同,在理论上似可轻易达到完全的混合状态,只要使A和B 相互交错排列,即达到完全的理想的混合。
若A是B的2倍的量,则必须有2个A粒子与一个B粒子排列在一起。
若A与B的密度不同,B为A的2倍,就必须1个A与2个B并列。
这样,绝对的均化在工业生产中就不大可能出现了,那么最佳的混合状态就是无序的不规则排列,一般认为混合的过程就是一个“随
机过程”,也称“概率混合”,其所能达到的最佳程度称为随机的完全混合。
2 影响粉体混合的主要物理特性
物料粉体所具有的形状、粒径及粒度分布、装填密度、表面性质、休止角、流动性、含水量、粘结性等都会影响混合过程,从实践经验来看,其中最具有影响力的是装填密度、粒径和流动性。
(1)粉体装填密度。
包含松装密度和振实密度,是研究粉体的一个重要的标准特征值。
实际应用中一定数量的粉体堆积密度是介于松装密度和振实密度之间的。
因此,要考虑松装密度与振实密度两个因素的影响。
(2)粉体粒径。
表示颗粒的平均尺寸,绝大多数粉体形状都是不规则的,本文所指的粒径是在假设粉体形状是规则的前提下,用粉体直径来标示。
根据现有粉体理论和实践经验表明,粉体越细,越不容易混合均匀。
(3)粉体的流动性。
一般情况下,粉体流动性越好,混合进程进行的就越快。
粉体实际流动时,通常用堆粉角和崩溃角标示,如图2所示。
只有流动性不好的粉体才会有崩溃角的产生。
3 常见混合工艺难题探讨
(1)流动性差的粉体。
在实际工作中,我们经常会遇到流动性很差的粉体,根据实践观察,堆粉角≥40°的粉体,要混合均匀就变得十分困难了。
依靠只有料桶运动的混合设备达到均匀混合的目的几乎是不可能的,延长混合时间也很难做到。
改善方法:由于流动性不好,粉体不易分开,因此在混合时需要强制搅拌手段,使用带有搅拌叶片的混合机,克服由于流动不好带来的混合难度。
(2)轻重粉不易混合难题。
例如:在调味料混合中要把较重的盐粒和较轻的辣椒粉混合均匀,根据现有粉体液态化模型可知,比重轻的辣椒粉一直漂浮在容器的上方,难以混合均匀。
改善方法:选用双运动混合机,如图3所示。
由于双运动混合容器转动与内部叶片转动在同方向进行,但是转速不一致,这样叶片就会裹挟漂浮于上方的轻粉进入主体重粉中,从而使轻粉得以均匀的混合。
(3)超细粉不易混合难题。
超细粉通常指1000目以上的粉体,当一种粉体细小到一定程度时,他外部的物理特征就会发生巨大的变化,原来不会漂浮的变得会漂浮,并极易出现团聚,形成假颗粒现象,极难混合均匀。
改善方法:降低设备运动速度,尽量避免超细粉的漂浮运动;选用双运动混合设备,将漂浮在容器上方的超细粉压入主体粉中;装料时,物料装到混合机器
容的80~85%,减少超细粉漂浮的可能性,增加粉体的压力,有利于叶片剪切的效果。
(4)添加微量元素的粉体。
在食品、医药等行业中,产品往往会添加对质量起关键作用并且特别贵重的微量元素。
微量元素一旦聚集在容器死角或混合不均匀,就会造成产品报废。
改善方法:针对易聚集在料桶死角的难点,需采用料桶可以运动的混合设备,避免死角的产生;针对微量元素添加极少和主体粉流动性不好的难点,采用带有强制剪切搅拌功能的混合设备,避免粉体流动性不好的难点。
同时采用逐次增量的混合方法来解决,不断稀释微量元素,达到混合均匀的目的。
4 结束语
目前,粉体混合已经发展成为一门跨学科,垮行业的综合性极强的技术科学,他的应用遍及材料、冶金、食品、医药等诸多领域。
粉体对象成千上万,而且个体特性复杂,因此粉体混合是个比较庞杂而困难的工作。
期待在不久的将来,可更深刻地揭示混合过程中粉体的运动机理,达到更好的混合效果和更高的混合效率。
参考文献:
[1]German. Pow der Met allurgy Science.New York :Chemical Publishing Co.Inc,1995
[2]孙楠,秦家峰,张锡兵,等.粉体混合原理及混合质量分析[J].机电信息,2012,14:42.
[3]赵洪义.绿色高性能生态水泥的合成技术[M].北京:化学工业出版社,2007:139-141.
[4]叶涛.多组分粉体混合过程的理论分析与实验研究[D].武汉:武汉理工大学,2009.。