长输管道腐蚀缺陷的评价
浅析长输压力管道无损检测技术
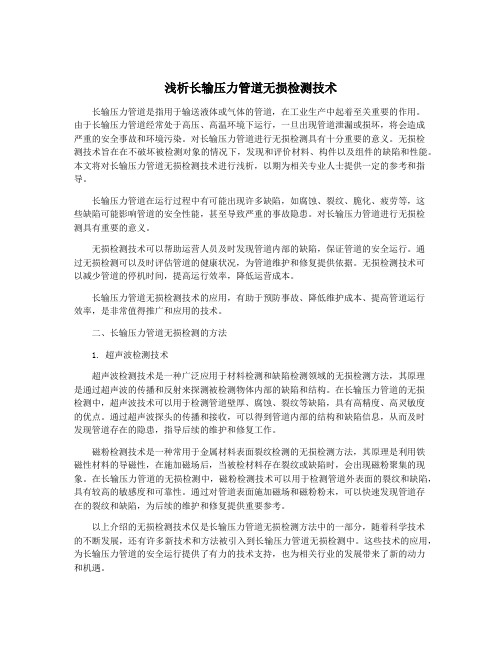
浅析长输压力管道无损检测技术长输压力管道是指用于输送液体或气体的管道,在工业生产中起着至关重要的作用。
由于长输压力管道经常处于高压、高温环境下运行,一旦出现管道泄漏或损坏,将会造成严重的安全事故和环境污染。
对长输压力管道进行无损检测具有十分重要的意义。
无损检测技术旨在在不破坏被检测对象的情况下,发现和评价材料、构件以及组件的缺陷和性能。
本文将对长输压力管道无损检测技术进行浅析,以期为相关专业人士提供一定的参考和指导。
长输压力管道在运行过程中有可能出现许多缺陷,如腐蚀、裂纹、脆化、疲劳等,这些缺陷可能影响管道的安全性能,甚至导致严重的事故隐患。
对长输压力管道进行无损检测具有重要的意义。
无损检测技术可以帮助运营人员及时发现管道内部的缺陷,保证管道的安全运行。
通过无损检测可以及时评估管道的健康状况,为管道维护和修复提供依据。
无损检测技术可以减少管道的停机时间,提高运行效率,降低运营成本。
长输压力管道无损检测技术的应用,有助于预防事故、降低维护成本、提高管道运行效率,是非常值得推广和应用的技术。
二、长输压力管道无损检测的方法1. 超声波检测技术超声波检测技术是一种广泛应用于材料检测和缺陷检测领域的无损检测方法,其原理是通过超声波的传播和反射来探测被检测物体内部的缺陷和结构。
在长输压力管道的无损检测中,超声波技术可以用于检测管道壁厚、腐蚀、裂纹等缺陷,具有高精度、高灵敏度的优点。
通过超声波探头的传播和接收,可以得到管道内部的结构和缺陷信息,从而及时发现管道存在的隐患,指导后续的维护和修复工作。
磁粉检测技术是一种常用于金属材料表面裂纹检测的无损检测方法,其原理是利用铁磁性材料的导磁性,在施加磁场后,当被检材料存在裂纹或缺陷时,会出现磁粉聚集的现象。
在长输压力管道的无损检测中,磁粉检测技术可以用于检测管道外表面的裂纹和缺陷,具有较高的敏感度和可靠性。
通过对管道表面施加磁场和磁粉粉末,可以快速发现管道存在的裂纹和缺陷,为后续的维护和修复提供重要参考。
长输管道腐蚀缺陷检测技术与应用
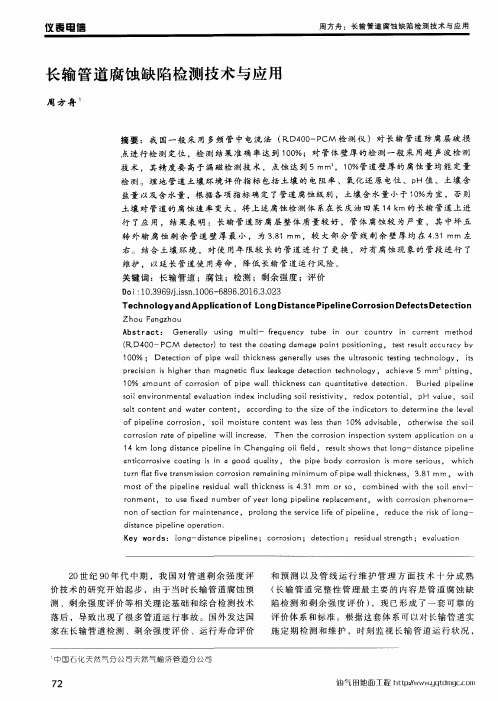
20世 纪 9O年 代 中期 ,我 国对 管 道 剩 余 强度 评 和 预 测 以及 管 线 运 行 维 护 管理 方 面技 术 十分 成 熟 价技 术 的研究 开始起 步 ,由于当 时长输 管道腐 蚀预 (长输 管 道 完整 性管 理 最 主要 的 内容 是管 道 腐蚀 缺 测 、剩余 强度 评价 等相 关理论 基 础和综 合检 测技术 陷检测 和 剩余 强 度评 价 ),现 已形成 了一 套 可靠 的 落后 ,导致 出现 了很多 管道 运行 事故 。 国外 发达 国 评 价体 系和标 准 。根据 这套 体系可 以对 长输 管道 实 家 在长 输管道 检测 、剩 余强 度评 价 、运 行 寿命评 价 施 定 期 检 测 和 维 护 , 时 刻 监 视 长 输 管 道 运 行 状 况 ,
仪 表电 信
周方舟:长输管道腐蚀缺陷测 技 术 与应 用
周 方 舟
摘 要 :我 国一般 采 用 多频 管 中电流 法 (R.D400一PCM 检 测仪 )对 长输 管 道 防腐 层破 损 点进行 检 测定 位 ,检 测结 果 准确 率达 到 1 00%;对 管体 壁厚 的检 测一般 采 用超 声 波检 测 技 术 ,其 精度要 高 于漏磁检 测技 术 ,点蚀 达到 5 mm ,1 O%管道 壁厚 的腐 蚀 量均 能定 量 检 测 。埋 地 管道 土壤 环境评 价 指标 包括 土壤 的 电 阻率 、氧化 还 原 电位 、pH值 、土壤 含 盐量 以及含 水量 ,根 据各 项指标 确 定 了管道腐蚀 级 别 ,土壤 含 水量 小于 10%为宜 ,否则 土壤 对 管道 的腐蚀 速率 变大 。将上 述腐蚀 检 测体 系在 长庆 油田 某 1 4 km的长输 管道 上进 行 了应 用 ,结 果表 明 :长输 管道 防 腐层 整 体质 量较 好 ,管体 腐 蚀较 为 严重 ,其 中坪 五 转 外输 腐 蚀 剩 余 管道 壁 厚 最 小 ,为 3.81 mm,较 大部 分 管线 剩 余 壁厚 均 在 4_31 mm左 右 。结合 土壤 环境 ,对使 用年 限较 长 的 管道进 行 了更换 ,对有 腐蚀 现 象的 管段 进 行 了 维护 ,以延 长 管道使 用寿命 ,降低 长 输 管道 运行 风险 。 关键 词 :长输管 道 ;腐 蚀 ;检测 ;剩余 强度 ;评 价
ICDA管道内腐蚀直接评价方法探析
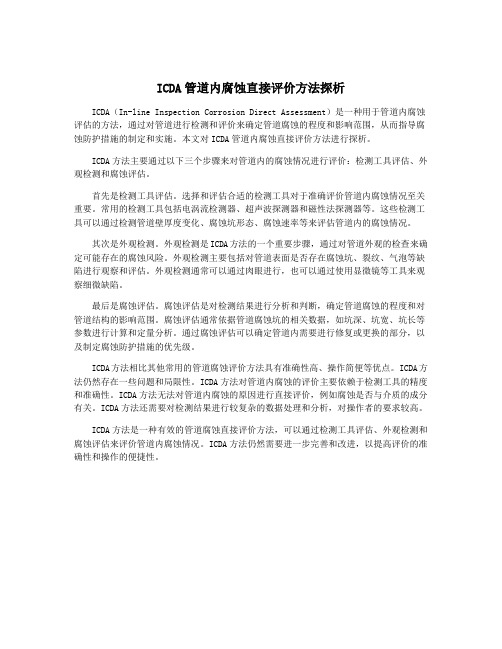
ICDA管道内腐蚀直接评价方法探析ICDA(In-line Inspection Corrosion Direct Assessment)是一种用于管道内腐蚀评估的方法,通过对管道进行检测和评价来确定管道腐蚀的程度和影响范围,从而指导腐蚀防护措施的制定和实施。
本文对ICDA管道内腐蚀直接评价方法进行探析。
ICDA方法主要通过以下三个步骤来对管道内的腐蚀情况进行评价:检测工具评估、外观检测和腐蚀评估。
首先是检测工具评估。
选择和评估合适的检测工具对于准确评价管道内腐蚀情况至关重要。
常用的检测工具包括电涡流检测器、超声波探测器和磁性法探测器等。
这些检测工具可以通过检测管道壁厚度变化、腐蚀坑形态、腐蚀速率等来评估管道内的腐蚀情况。
其次是外观检测。
外观检测是ICDA方法的一个重要步骤,通过对管道外观的检查来确定可能存在的腐蚀风险。
外观检测主要包括对管道表面是否存在腐蚀坑、裂纹、气泡等缺陷进行观察和评估。
外观检测通常可以通过肉眼进行,也可以通过使用显微镜等工具来观察细微缺陷。
最后是腐蚀评估。
腐蚀评估是对检测结果进行分析和判断,确定管道腐蚀的程度和对管道结构的影响范围。
腐蚀评估通常依据管道腐蚀坑的相关数据,如坑深、坑宽、坑长等参数进行计算和定量分析。
通过腐蚀评估可以确定管道内需要进行修复或更换的部分,以及制定腐蚀防护措施的优先级。
ICDA方法相比其他常用的管道腐蚀评价方法具有准确性高、操作简便等优点。
ICDA方法仍然存在一些问题和局限性。
ICDA方法对管道内腐蚀的评价主要依赖于检测工具的精度和准确性。
ICDA方法无法对管道内腐蚀的原因进行直接评价,例如腐蚀是否与介质的成分有关。
ICDA方法还需要对检测结果进行较复杂的数据处理和分析,对操作者的要求较高。
ICDA方法是一种有效的管道腐蚀直接评价方法,可以通过检测工具评估、外观检测和腐蚀评估来评价管道内腐蚀情况。
ICDA方法仍然需要进一步完善和改进,以提高评价的准确性和操作的便捷性。
含腐蚀缺陷管道的安全评价
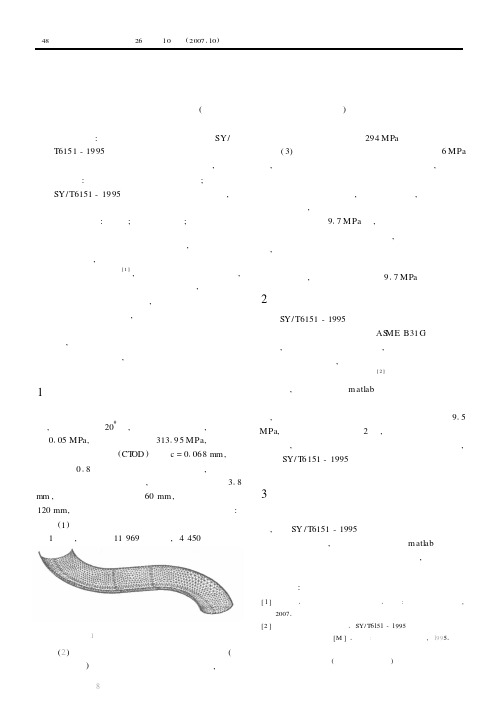
含腐蚀缺陷管道的安全评价吴绍明(福建省南平市锅炉压力容器检验所) 摘要:分别用有限元法和标准SY/T6151-1995的方法分析计算了含腐蚀性体积缺陷弯管的极限载荷和安全服役状况,结果表明:两种方法的计算结果接近;标准SY/T6151-1995所编制的分析评定软件,可简便而有效地评价管道腐蚀损伤。
关键词:管道;腐蚀性缺陷;安全评价 石油天然气管道服役时间比较长,普遍存在腐蚀性体积缺陷,以及第三方破坏、地质灾害和误操作等因素造成的损伤[1],为保障管道的安全运行,避免管体腐蚀所导致的爆裂、泄漏事故,确定是否需要立即停产检修更换管段,或因生产繁忙暂时不能停产而采取降压运行,需要及时发现缺陷并评估其安全可靠性。
鉴于含缺陷管道的极限应力分析比较复杂,本文试用有限元法分析某一天然气管道的极限强度及安全状况,并与有关评价标准进行了对比。
1 管道极限载荷的有限元分析本文研究对象为一含硫天然气输送管道的弯管段,管道材质为20#钢,工作温度为常温,工作压力0105MPa,最小屈服强度313195MPa,管材的裂纹尖端张开位移(CT OD )值δc =01068mm ,焊缝系数为018。
该管段在内部介质作用下,出现比较严重的腐蚀和减薄现象,最大蚀坑深度为318mm ,最大纵向投影长度60mm ,环向腐蚀长度120mm,利用有限元法分析其极限承载情况如下:(1)有限元模型。
管段的有限元单元模型如图1所示,共划分11969个单元,4450个节点。
图 含蚀坑管道有限元单元模型()材料的本构模型。
材料的本构模型(应力应变关系)用双线性表示。
经计算分析,材料的塑性极限许用应力值为294MPa 。
(3)弯管的弹塑性分析。
当内压增大到6MPa 时,管道内弯处局部材料开始进入屈服状态,但其屈服区域较小。
此时屈服区域外围未屈服的材料可限制屈服区域材料的变形,随载荷的增加,管道不会无限制地变形,因此管段还有进一步承载的能力。
当内压达到917MPa 时,最大应力处沿厚度方向整体屈服。
输气管道内腐蚀缺陷剩余强度评估方法分析
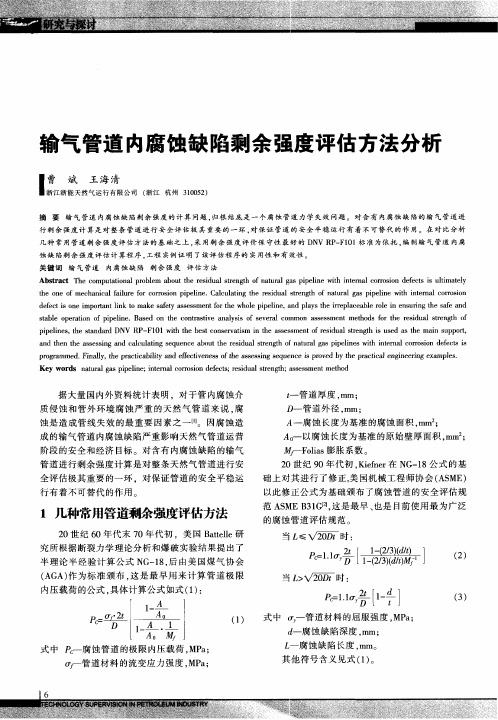
p i p e l i n e s , t h e s t a n d a r d DNV RP - F I O 1 wi t h t h e b e s t c o n s e r v a t i s m i n t h e a s s e s s me n t o f r e s i d u a l s t r e n th g i s u s e d a s t h e ma i n s u p p o t, r
输气 管道 内腐蚀缺 陷剩余 强度评估 方法分析
l 浙 然 公 司 浙 江 ㈤ 。 。
摘 要 输 气 管道 内腐 蚀 缺 陷剩 余 强度 的计 算 问题 , 归根 结底 是 一 个 腐 蚀 管道 力 学失 效 问题 。 对 含 有 内腐 蚀 缺 陷的 输 气管 道 进 行 剩余 强度 计 算 是 对 整 条 管道 进 行 安 全评 估 极 其 重要 的 一 环 . 对 保 证 管道 的安 全 平 稳 运 行 有 着不 可 替 代 的 作 用 。在 对 比分 析
据大 量 国内外 资料 统计表 明 ,对于管 内腐 蚀介 质侵 蚀 和 管外 环境 腐 蚀严 重 的天然 气 管 道来 说 . 腐 蚀 是造 成 管线 失 效 的最 重要 因素 之- -[ ” 。 因腐 蚀造 成 的输气 管道 内腐 蚀缺 陷严 重影 响天然 气管 道运 营 阶段 的安全 和经济 目标 。对 含有 内腐蚀 缺 陷的输气
腐蚀管道的剩余强度评价
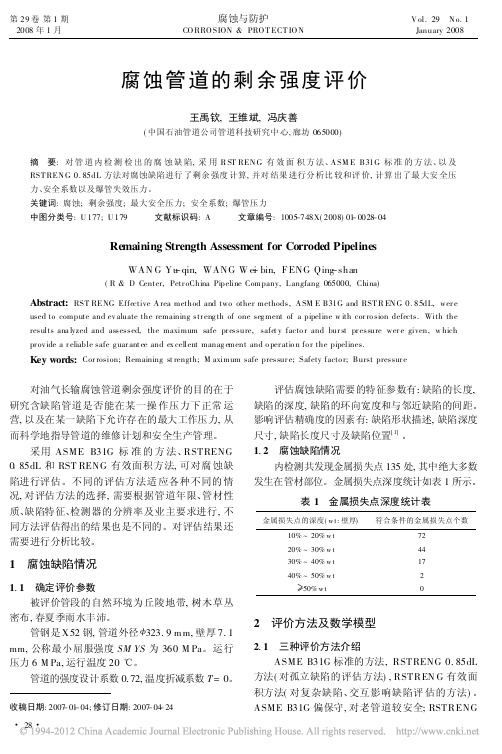
d Pc3 = 1 . 1P 1 ( 10) t 式中 : L total 是腐蚀缺陷长度 , d 是腐蚀缺陷深度, t 是
# 29 #
王禹钦等 : 腐蚀管道的剩余强度评价
管壁厚度 , D 是管道外径 , M 3 是 F olias 因子。 1 + 0. 8 L Dt 预测的爆管失效压力 P burs t3 M3 = 对于 L total [ 20: Dt 2t = 1. 1 D S M YS 11- 2 3 2 3 d t d 1 M3 t ( 12) 对于 L total > 20: Dt P burst3 = 1. 1 2t SM YS 1 - d D t ( 13)
第 29 卷 第 1 期 2008 年 1 月
腐蚀与防护
CO RRO SION & PRO T ECT IO N
V ol. 29 N o. 1 January 2008
腐蚀管 道的剩 余强度评 价
王禹钦, 王维斌, 冯庆善
( 中国石油管道公司管道科技研究中 心 , 廊坊 065000) 摘 要 : 对 管 道 内 检 测 检 出 的 腐 蚀 缺 陷 , 采 用 R ST REN G 有 效 面 积 方 法、 A SM E B31G 标 准 的 方 法、 以及
金属损失点的深度 ( w t : 壁厚) 10% ~ 20% w t 20% ~ 30% w t 30% ~ 40% w t 40% ~ 50% w t \ 50% w t 符合条件的金属损失点个数 72 44 17 2 0
浅析长输管道清管及内检测
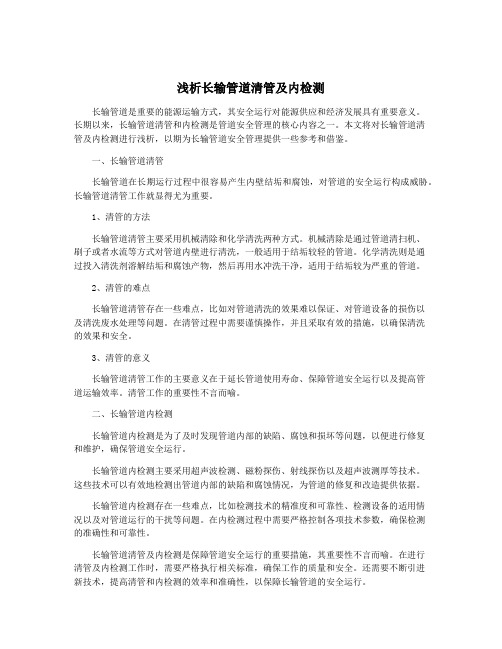
浅析长输管道清管及内检测长输管道是重要的能源运输方式,其安全运行对能源供应和经济发展具有重要意义。
长期以来,长输管道清管和内检测是管道安全管理的核心内容之一。
本文将对长输管道清管及内检测进行浅析,以期为长输管道安全管理提供一些参考和借鉴。
一、长输管道清管长输管道在长期运行过程中很容易产生内壁结垢和腐蚀,对管道的安全运行构成威胁。
长输管道清管工作就显得尤为重要。
1、清管的方法长输管道清管主要采用机械清除和化学清洗两种方式。
机械清除是通过管道清扫机、刷子或者水流等方式对管道内壁进行清洗,一般适用于结垢较轻的管道。
化学清洗则是通过投入清洗剂溶解结垢和腐蚀产物,然后再用水冲洗干净,适用于结垢较为严重的管道。
2、清管的难点长输管道清管存在一些难点,比如对管道清洗的效果难以保证、对管道设备的损伤以及清洗废水处理等问题。
在清管过程中需要谨慎操作,并且采取有效的措施,以确保清洗的效果和安全。
3、清管的意义长输管道清管工作的主要意义在于延长管道使用寿命、保障管道安全运行以及提高管道运输效率。
清管工作的重要性不言而喻。
二、长输管道内检测长输管道内检测是为了及时发现管道内部的缺陷、腐蚀和损坏等问题,以便进行修复和维护,确保管道安全运行。
长输管道内检测主要采用超声波检测、磁粉探伤、射线探伤以及超声波测厚等技术。
这些技术可以有效地检测出管道内部的缺陷和腐蚀情况,为管道的修复和改造提供依据。
长输管道内检测存在一些难点,比如检测技术的精准度和可靠性、检测设备的适用情况以及对管道运行的干扰等问题。
在内检测过程中需要严格控制各项技术参数,确保检测的准确性和可靠性。
长输管道清管及内检测是保障管道安全运行的重要措施,其重要性不言而喻。
在进行清管及内检测工作时,需要严格执行相关标准,确保工作的质量和安全。
还需要不断引进新技术,提高清管和内检测的效率和准确性,以保障长输管道的安全运行。
缺陷评价标准
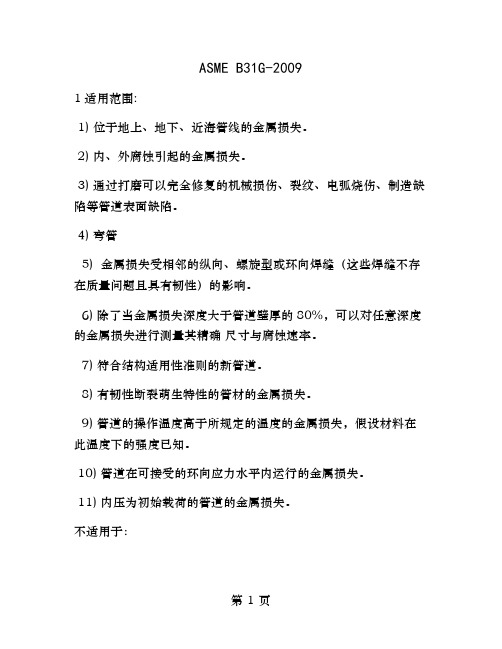
ASME B31G-20091适用范围:1) 位于地上、地下、近海管线的金属损失。
2) 内、外腐蚀引起的金属损失。
3) 通过打磨可以完全修复的机械损伤、裂纹、电弧烧伤、制造缺陷等管道表面缺陷。
4) 弯管5) 金属损失受相邻的纵向、螺旋型或环向焊缝(这些焊缝不存在质量问题且具有韧性)的影响。
6) 除了当金属损失深度大于管道壁厚的80%,可以对任意深度的金属损失进行测量其精确尺寸与腐蚀速率。
7) 符合结构适用性准则的新管道。
8) 有韧性断裂萌生特性的管材的金属损失。
9) 管道的操作温度高于所规定的温度的金属损失,假设材料在此温度下的强度已知。
10) 管道在可接受的环向应力水平内运行的金属损失。
11) 内压为初始载荷的管道的金属损失。
不适用于:1) 通过打磨仍不能恢复其光滑外形的裂纹型缺陷与表面机械损伤型缺陷。
2) 当管壁上由凹陷或褶曲导致的径向变形大于管道外壁的6%(除非依照三级评价参数与 2.3保持一致)。
3) 槽型腐蚀、选择性腐蚀或优先腐蚀对管道接缝与环形焊缝的影响。
4) 除了弯头弯管其他配件的金属损失。
5) 影响材料萌生脆性断裂的金属损失。
6) 管道运行的温度超出了标准允许操作温度范围,或工作温度在蠕变范围。
格外考虑:在一些特殊情况下,用户也要做格外的考虑,如下:1) 管道由于内压不足(如低于25%SMYS)在低环向应力条件下运行,易发生腐蚀从而导致穿孔,该标准里的方法不能解决此类穿孔失效问题。
2) 受均匀腐蚀的管壁(如因腐蚀而导致整个管道表面减薄)可以在一个较高的环向应力(高于原始管壁的额定环向应力)下有效运行。
评价均匀腐蚀区内存在的深凹陷对管道的影响时,应该考虑到均匀腐蚀造成的管壁减薄对管道的影响。
3) 对于普通的埋地管道,由内压引起的环向应力最大,它将会控制管道的失效形式。
在非固定管道上,大面积圆周范围的金属损失受拉伸作用产生高的纵向应力,该应力可以从纵向与环向改变失效形式。
该标准里所提供的方法不能够处理由很高的纵向拉伸应力而产生的环向失效。
- 1、下载文档前请自行甄别文档内容的完整性,平台不提供额外的编辑、内容补充、找答案等附加服务。
- 2、"仅部分预览"的文档,不可在线预览部分如存在完整性等问题,可反馈申请退款(可完整预览的文档不适用该条件!)。
- 3、如文档侵犯您的权益,请联系客服反馈,我们会尽快为您处理(人工客服工作时间:9:00-18:30)。
第3 2 卷第 6 g g( 2 0 1 3 . 0 6 )( 基建管理)
长输管道腐蚀缺陷的评价
郭宏 大 庆 油田 设 计院
摘要 :对埋 地 输 油 管线 全线 腐 蚀检 测 数据 分析 表 明 ,管线 不 同 区段 腐 蚀程 度 差 别很 大 ,在 预 测其 腐蚀 管道 剩余 寿命 时 亦应 采 用分段 预 测 的原 则进 行 。 最普遍 的预测 腐 蚀增 长 率 的方 法就 是 对 比 两组 近 些 年 内的检 测数 据 。全 寿 命 腐 蚀 增 长 率 预 测 适 用 于 两 次检 测 间 隔时 间较 短 的情 况 ;半寿命 腐蚀 增 长率 预 测适 用 于 两次检 测 间隔 时间较 长 或 只有 一 次且距 投 产之 日起 时 间较 长 的情况。依据腐蚀增长速率可预测腐蚀缺 陷的未来发展 I 青 况 ,从 而判定 出计划修复时间和再检测时 间。
时间。
高的 高强度 钢 。
1 . 3 R S T R E N G 有效 面积法 该 方 法 不 再需 要 用 B 3 1 G法 中 的抛 物线 或 矩形
对腐蚀 的几何形 状进 行 面积近 似 。 由于 在对 检测数 据进 行分 析过 程 中 ,很难 获取 有效 面积 ,故 此方 法
金属损 失 面积 的表达 式 。 同样 不适 用于 强度 等级较
安全策略和可接受准则, 来确定所采用的腐蚀增长率 。 全寿 命腐 蚀增 长率 预测适 用 于两 次检测 间隔 时
间 较短 的情况 ;半 寿命腐 蚀增 长率 预测 适用 于两 次 检 测 间隔时 间较长 或 只有一 次且距 投产 之 日起 时 间 较 长 的情 况 。依据 腐蚀增 长 速率可 预测 腐蚀缺 陷 的 未 来发 展情况 ,从 而判 定 出计划修 复 时间 和再 检测
该 方 法 针 对 中高 强 度 等 级 管 道 ( 可达 到 X 8 0 ) ,
2 腐蚀 缺陷寿命 预测
对 埋 地输 油 管 线 全线 腐蚀 检 测 数据 分 析 表 明 ,
余强度 , 应该考虑更复杂的情况 ,如正确地考虑轴 向载 荷和 弯 曲载荷 ,及其 联合 作用下 以及更 复 杂 的
数 据 ,给 出 下 一 阶 段 的腐 蚀 速率 。检 测 的 次数 越 多 ,所获得 的结果 与 实际腐 蚀速率 越相 符合 。
A S ME B 3 1 G法依 其 准 则 简 单 、保 守 及 有 效 性 最普 遍 的预测腐 蚀增 长率 的方法 是对 比两 组 近 广 泛 用 于腐 蚀 管线 的评 估 。对 复杂 几 何 形 状 的腐 些 年 内的 检 测 数 据 。如果 仅 仅 有 一 次 的 内 检 测数 蚀 、相邻腐蚀 、环向腐蚀和有轴 向应力存在时,不 据 ,可 以采用 全寿命 或半 寿命 的方法 来 预测腐速率 ;预测
d o i : 1 0 . 3 9 6 9 / j . i s s n . 1 0 0 6 — 6 8 9 6 . 2 0 1 3 . 6 . 0 6 3
1 腐蚀 缺陷剩余 强度评估
1 . 1 A S M E B 3 1 G法
而是 应该 隔一定 时 间后再进 行 检测 ,结 合历次 检测
能用它来进行评估。也不适用于管材等级较高的高 陷的增长速率 ,获取最深腐蚀缺陷的腐蚀增长速率 强 度钢 管道 ,例 如 X 7 0 、X 8 0 管道 。 和全部腐蚀缺陷的平均增长速率 , 根据运营公司的
1 . 2 修正 的 B 3 1 G 方 法
该 方 法 采 用 失 效 爆 破 压 力 预 测 公 式 的形 式 与 A S ME B 3 1 G法 基本 相 同 ,主要 修 正 了 F o l i a s 系数 和
实际应 用 性差 。
1 . 4 D N V R P F 1 0 1 方法
3 结论
( 1 )对 于 腐 蚀 缺 陷剩 余 强 度 评 估 , A S ME
B 3 1 G法 、R S T R E N G 0 . 8 5 d L法 、R S T R E NG有 效 面
积法适 合 中 、低强 度钢 的评 价 ,D N V R P F 1 0 1 法适 更适 合 于现代 高强 度大 口径管 道 的安全 评价 。但 不 合 中 、高强 度等级 管道 的缺 陷评定 。 适 用于 超过 X 8 0 钢 的管线 钢 或深 度大 于 8 5 %壁厚 的 ( 2 )腐蚀管道剩余强度评价应在以下两个方面 缺陷。 进 一 步深入 研究 :用 有 限元 方法 研究 腐蚀 管道 的剩
腐蚀 形状 等 ;进 一步 研究 在 内压和 附加 载荷联 合作 用下 环 向腐蚀 缺陷 的剩余强 度评 价 。 ( 3 )基 于定期全 线腐 蚀检 测数 据为 基础 的剩余
管线不同区段腐蚀程度差别很大 。因此 ,在预测其 腐蚀管道剩余 寿命 时亦应 采用分段预测 的原则进 行 。随着漏磁内检测的深入开展,获取了管道腐蚀 缺陷 的大量 基础 数据 。通 过对 现场 管线 进行 阶段性 的腐蚀检测 , 得到腐蚀深度随时间的变化趋势 , 从 而得 到腐 蚀速 率发 展趋势 ,拟合 出经验 公式 ,即可 预测下一阶段的腐蚀速率 。预测 的时间不宜太长 ,
一
寿命预测模型,在数据依据充分的条件下 ,能充分 显 示管 段不 同 区段 腐蚀 发展差 别 ,预测 精度 和可 信
度 高 ,可为 管道再 检测周 期决 策提供 支持 。
( 栏 目主持 焦 晓梅 )
1 1 0一
油气 田地面 工程 ( h
t t p : / / 、 w, w. y q t d mg c . c o m)