数控车床刀补及换刀技术
广州数控GSK980TD操作步骤(刀补对刀)
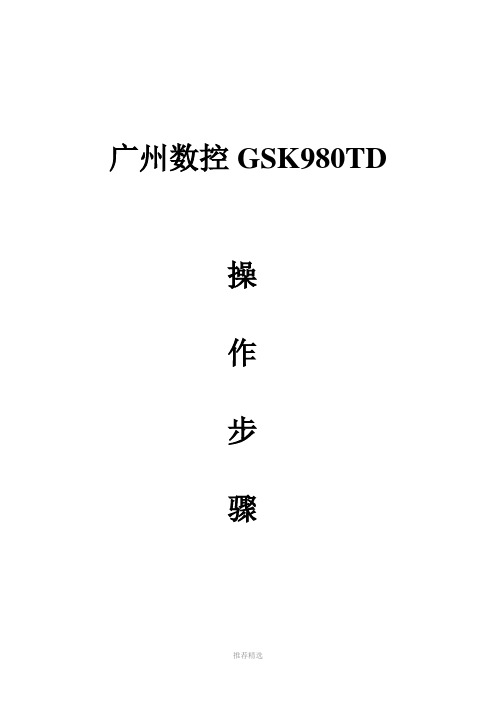
广州数控GSK980TD操作步骤广州数控GSK980TD操作步骤(刀补对刀)第一部分:熟悉机床面板操作(一~十一,其中三、四、五条自己阅读,自行练习,也可以不练)第二部分:练习对刀及检验对刀是否正确(十二~十五)第三部分:加工零件(十六~二十三)二、打开一个程序:(举例:打开O 0001三、按顺序快速打开程序目录里的所有程序。
举例:在编辑下打开O0001。
按O0002;再按动打开下一个程序O0003;余此类推。
反之,按四、把当前程序复制到新建程序里:(举例:把O 0001号程序复制到新建程序O 0008号程序里)在编辑下打开O 0001号程序,按—,复制完成。
五、把当前程序改名:(举例:把O 0001号程序名改为O 0008号程序名)在编辑下打开O 0001号程序,按—,改名完成。
六、编写新的程序:(举例:编写O 0001号程序)七、删除一个程序:(举例:删除O 0001九、输入转速:(举例:输入S800转速)十、转动刀架:(举例:把刀架转动到1号刀位)方法1或方法2十二、对1号外圆刀(把刀架转到T0100):Z X轴方向车一刀端面(约0.5㎜),再X到“刀具偏置”界面,光标移到001X Z轴方向车一刀外圆,再Z轴方向退刀,(光标移到001假如外圆测量值是φ25.32)十三、对2号切断刀(把刀架转到T0200):方法和对1号外圆刀相同。
(注意:把光标移到002序号。
在对Z向时,由于1号刀已车好端面,因此2号刀不能再车端面,只能轻碰端面。
)十四、对3号螺纹刀(把刀架转到T0300):方法和对1号、2号刀相同。
(注意:把光标移到003序号。
在对Z向时,由于车刀刀尖是60度,因此刀尖不能轻碰端面,刀尖只能与端面基本对齐。
)十五、检验对刀是否正确: (记得检验时要带刀补)检验Z 向时,车刀要在毛坯直径外面;检验X向时,车刀要在毛坯端面外面,以防车刀直接与毛坯碰撞1号外圆刀(把刀架转到T0101)摇至Z0,查看车刀刀尖是否与端面对齐;再用手轮把车刀摇至X25.32(假如外圆测量值是φ25.32),查看车刀刀尖是否在φ25.32外圆上面。
数控车床刀具补偿知识

(2)刀尖方位的设置
车刀形状很多,使用时安装位置也各异,由此 决定刀尖圆弧所在位置。 要把代表车刀形状和位置的参数输入到数据库中。 以刀尖方位号表示。
从图示可知,
若刀尖方位码设为0或9时,机床将以刀尖圆弧中 心为刀位点进行刀补计算处理; 当刀尖方位码设为1~8时,机床将以假想刀尖为 刀位点,根据相应的代码方位进行刀补计算处理。
为什么需要刀具刀具补偿?
刀具使用一段时间后会磨损 ,会使加工尺寸
产生误差.
解决: •将磨损量测量获得后进行补偿.
可以不修改加工程序.
为什么需要刀具刀具补偿
数控程序一般是针对刀位点 ,
按工件轮廓尺寸编制的 . 当刀 尖不是理想点而是一段圆弧时 , 会造成实际切削点与理想刀位 点的位置偏差.
解决: •对刀尖圆弧半径进行补偿.
N11 M30
五、换刀程序编写
G27、G28、G29. ----- 参考点控制
1、格式:
1、关于参考点操作的指令
G27 X... Z... T0000 ; 回指令参考点检验 G28 X... Z... T0000 ; 经指令中间点再自动回参考点 G29 X... Z... ; 从参考点经中间点返回指令点
过程:
将某把车刀的几何偏置和磨损补偿值存入相应的刀补地址 中。 当程序执行到含 Txxxx的程序行的内容时,即自动到刀补 地址中提取刀偏及刀补数据。
驱动刀架拖板进行相应的位置调整。
T XX 00取消几何补偿。
对于有自动换刀功能的车床来说,执行T指令时, 将先让刀架转位,按刀具号选择好刀具后,再调 整刀架拖板位置来实施刀补。
O1111
例2:考虑刀尖半径补偿
N1 G92 X40.0 Z10.0
FANUC数控车床加工过程中刀具补偿的应用介绍

数控车床加工过程中刀具补偿的应用介绍前言数控车床通常连续实行各种切削加工,刀架在换刀时前一刀具刀尖位置和新换的刀具位置之间会产生差异,刀具安装也存在误差、刀具磨损和刀尖圆弧半径等误差,若不利用刀具补偿功能予以补偿,就切削不出符合图样要求形状的零件。
此外,合理利用刀具补偿还可以简化编程。
数控车床的刀具补偿可分为两类,即刀具位置补偿和刀具半径补偿。
1 刀具位置补偿加工过程中,若使用多把刀具,通常取刀架中心位置作为编程原点,即以刀架中心! 为程序的起始点,如图1所示,而刀具实际移动轨迹由刀具位置补偿值控制。
由图1(a)可见,刀具位置补偿包含刀具几何补偿值和磨损补偿值。
图1 刀具位置补偿由于存在两种形式的偏移量,所以刀具位置补偿使用两种方法,一种方法是将几何补偿值和磨损补偿值分别设定存储单元存放补偿值,其格式为:另一种方法是将几何偏移量和磨损偏移量合起来补偿,如图(b)所示,其格式为:总补偿值存储单元编号有两个作用,一个作用是选择刀具号对应的补偿值,并执行刀具位置补偿功能;另一个作用是当存储单元编号00时可以取消位置补偿,例如T0100,表示消去+号刀具当前的补偿值。
图2表示位置补偿的作用,图2中的实线是刀架中心A 点的编程轨迹线,虚线是执行位置补偿时A 点的实际轨迹线,实际轨迹的方位和X、Z轴的补偿值有关,其程序为:N010 G00 X10 Z-10 T0202;N020 G01 Z-30;N030 X20 Z-40 T0200;图2 刀具位置补偿作用数控车床系统刀具结构如图3所示,图3中P为假想刀尖,S为刀头圆弧圆心,r为刀头半径,A为刀架参考点。
图3 车刀结构车床的控制点是刀架中心,所以刀具位置补偿始终需要。
刀具位置补偿是用来实现刀尖圆弧中心轨迹与刀架参考点之间的转换,对应图3中A与S之间的转换,但是实际上我们不能直接测得这两个中心点之间的距离矢量,而只能测得假想刀尖! 与刀架参考点$ 之间的距离。
数控加工中的三种补偿和补偿技巧
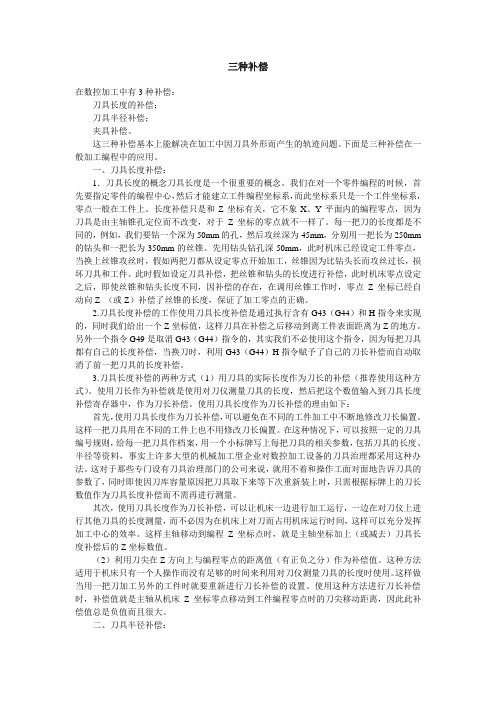
三种补偿在数控加工中有3种补偿:刀具长度的补偿;刀具半径补偿;夹具补偿。
这三种补偿基本上能解决在加工中因刀具外形而产生的轨迹问题。
下面是三种补偿在一般加工编程中的应用。
一、刀具长度补偿:1.刀具长度的概念刀具长度是一个很重要的概念。
我们在对一个零件编程的时候,首先要指定零件的编程中心,然后才能建立工件编程坐标系,而此坐标系只是一个工件坐标系,零点一般在工件上。
长度补偿只是和Z坐标有关,它不象X、Y平面内的编程零点,因为刀具是由主轴锥孔定位而不改变,对于Z坐标的零点就不一样了。
每一把刀的长度都是不同的,例如,我们要钻一个深为50mm的孔,然后攻丝深为45mm,分别用一把长为250mm 的钻头和一把长为350mm的丝锥。
先用钻头钻孔深50mm,此时机床已经设定工件零点,当换上丝锥攻丝时,假如两把刀都从设定零点开始加工,丝锥因为比钻头长而攻丝过长,损坏刀具和工件。
此时假如设定刀具补偿,把丝锥和钻头的长度进行补偿,此时机床零点设定之后,即使丝锥和钻头长度不同,因补偿的存在,在调用丝锥工作时,零点Z坐标已经自动向Z (或Z)补偿了丝锥的长度,保证了加工零点的正确。
2.刀具长度补偿的工作使用刀具长度补偿是通过执行含有G43(G44)和H指令来实现的,同时我们给出一个Z坐标值,这样刀具在补偿之后移动到离工件表面距离为Z的地方。
另外一个指令G49是取消G43(G44)指令的,其实我们不必使用这个指令,因为每把刀具都有自己的长度补偿,当换刀时,利用G43(G44)H指令赋予了自己的刀长补偿而自动取消了前一把刀具的长度补偿。
3.刀具长度补偿的两种方式(1)用刀具的实际长度作为刀长的补偿(推荐使用这种方式)。
使用刀长作为补偿就是使用对刀仪测量刀具的长度,然后把这个数值输入到刀具长度补偿寄存器中,作为刀长补偿。
使用刀具长度作为刀长补偿的理由如下:首先,使用刀具长度作为刀长补偿,可以避免在不同的工件加工中不断地修改刀长偏置。
广州数控GSK980TD操作步骤(刀补对刀)
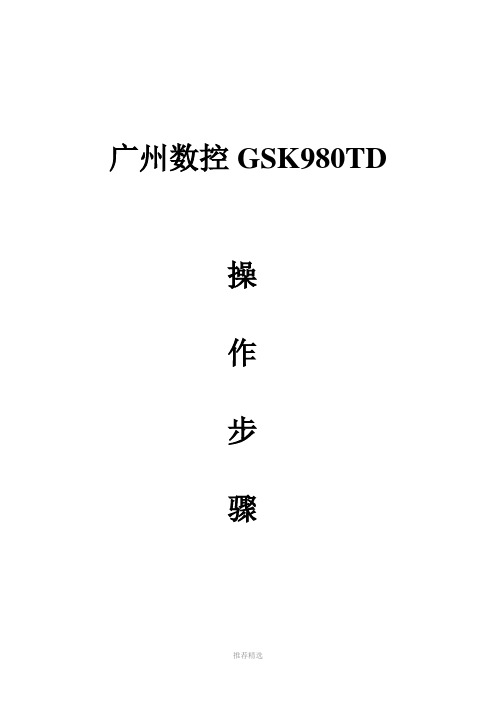
广州数控GSK980TD操作步骤广州数控GSK980TD操作步骤(刀补对刀)第一部分:熟悉机床面板操作(一~十一,其中三、四、五条自己阅读,自行练习,也可以不练)第二部分:练习对刀及检验对刀是否正确(十二~十五)第三部分:加工零件(十六~二十三)二、打开一个程序:(举例:打开O 0001三、按顺序快速打开程序目录里的所有程序。
举例:在编辑下打开O0001。
按O0002;再按动打开下一个程序O0003;余此类推。
反之,按四、把当前程序复制到新建程序里:(举例:把O 0001号程序复制到新建程序O 0008号程序里)在编辑下打开O 0001号程序,按—,复制完成。
五、把当前程序改名:(举例:把O 0001号程序名改为O 0008号程序名)在编辑下打开O 0001号程序,按—,改名完成。
六、编写新的程序:(举例:编写O 0001号程序)七、删除一个程序:(举例:删除O 0001九、输入转速:(举例:输入S800转速)十、转动刀架:(举例:把刀架转动到1号刀位)方法1或方法2十二、对1号外圆刀(把刀架转到T0100):Z X轴方向车一刀端面(约0.5㎜),再X到“刀具偏置”界面,光标移到001X Z轴方向车一刀外圆,再Z轴方向退刀,(光标移到001假如外圆测量值是φ25.32)十三、对2号切断刀(把刀架转到T0200):方法和对1号外圆刀相同。
(注意:把光标移到002序号。
在对Z向时,由于1号刀已车好端面,因此2号刀不能再车端面,只能轻碰端面。
)十四、对3号螺纹刀(把刀架转到T0300):方法和对1号、2号刀相同。
(注意:把光标移到003序号。
在对Z向时,由于车刀刀尖是60度,因此刀尖不能轻碰端面,刀尖只能与端面基本对齐。
)十五、检验对刀是否正确: (记得检验时要带刀补)检验Z 向时,车刀要在毛坯直径外面;检验X向时,车刀要在毛坯端面外面,以防车刀直接与毛坯碰撞1号外圆刀(把刀架转到T0101)摇至Z0,查看车刀刀尖是否与端面对齐;再用手轮把车刀摇至X25.32(假如外圆测量值是φ25.32),查看车刀刀尖是否在φ25.32外圆上面。
数控车床上刀补用法
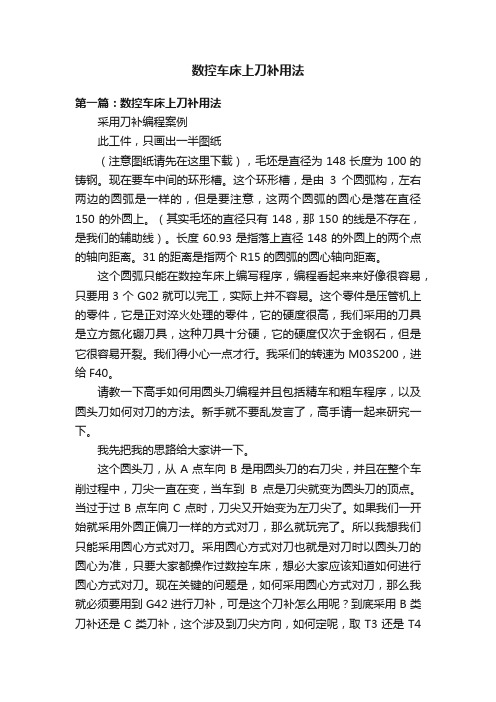
数控车床上刀补用法第一篇:数控车床上刀补用法采用刀补编程案例此工件,只画出一半图纸(注意图纸请先在这里下载),毛坯是直径为148长度为100的铸钢。
现在要车中间的环形槽。
这个环形槽,是由3个圆弧构,左右两边的圆弧是一样的,但是要注意,这两个圆弧的圆心是落在直径150的外圆上。
(其实毛坯的直径只有148,那150的线是不存在,是我们的辅助线)。
长度60.93是指落上直径148的外圆上的两个点的轴向距离。
31的距离是指两个R15的圆弧的圆心轴向距离。
这个圆弧只能在数控车床上编写程序,编程看起来来好像很容易,只要用3个G02就可以完工,实际上并不容易。
这个零件是压管机上的零件,它是正对淬火处理的零件,它的硬度很高,我们采用的刀具是立方氮化硼刀具,这种刀具十分硬,它的硬度仅次于金钢石,但是它很容易开裂。
我们得小心一点才行。
我采们的转速为M03S200,进给F40。
请教一下高手如何用圆头刀编程并且包括精车和粗车程序,以及圆头刀如何对刀的方法。
新手就不要乱发言了,高手请一起来研究一下。
我先把我的思路给大家讲一下。
这个圆头刀,从A点车向B是用圆头刀的右刀尖,并且在整个车削过程中,刀尖一直在变,当车到B点是刀尖就变为圆头刀的顶点。
当过于过B点车向C点时,刀尖又开始变为左刀尖了。
如果我们一开始就采用外圆正偏刀一样的方式对刀,那么就玩完了。
所以我想我们只能采用圆心方式对刀。
采用圆心方式对刀也就是对刀时以圆头刀的圆心为准,只要大家都操作过数控车床,想必大家应该知道如何进行圆心方式对刀。
现在关键的问题是,如何采用圆心方式对刀,那么我就必须要用到G42进行刀补,可是这个刀补怎么用呢?到底采用B类刀补还是C类刀补,这个涉及到刀尖方向,如何定呢,取T3还是T4还是T8呢?看起在每个不同时间,刀尖的方向都不同,到底应该如何取刀尖方向呢?还有刀补从哪个程序开始补呢?又在哪里结束呢?我第一次编写这个程序时,我采用圆心方式对刀,我将圆弧分成两半,我用T0101车左边圆弧,用T0102车圆弧,在中间开始换刀偏。
数控设备刀具补偿技术讲解
刀具长度补偿:
补偿刀具长度方向尺寸的变化.
三、刀具补偿的方法
• •
人工预刀补:人工计算刀补量进行编程 机床自动刀补:数控系统具有刀具补偿功能。
四、刀具半径补偿功能
1、刀具半径补偿的作用
在数控铣床上进行轮廓铣削时,由于刀具半径的 存在,刀具中心轨迹与工件轮廓不重合。
从上述程序可以大致了解钻孔加工的走刀路线及钻孔的基本 编程方法,当所使用的数控铣床不具备更高级的钻孔专用指令 时,通常都需要这样一步步地编程,更方便的钻孔编程方法将 在后面的章节中逐步介绍。
返回上层
3、刀具长度补偿指令
刀具长度补偿G43,G44,G49 (1)格式
G43
G44 G49
G00
G01
Z— H—
G00
G01
Z—
G43 刀具长度正补偿
G49取消刀长补偿
G44 刀具长度负补偿
G43 G44 G49 均为模态指令
其中Z 为指令终点位置,H为刀补号地址,用H00~ H99来指定,它用来调用内存中刀具长度补偿的数值。
t01t02t031010刀补引入刀补取消采用刀座对刀后来安装刀具h0145d010004g92x1500y1600z1200g90g00x1000y600g43z20h01s100m03g42g01x750d01f100x350g02x150r100g01y700g03x150r150g01y600g02x350r100g01x750g09y0主程序号建立工件坐标系绝对值方式快进到x100y60指令高度z2实际到达高z43处刀径补偿引入插补至x75y60直线插补至x35y60顺圆插补至x15y60直线插补至x15y7015y70直线插补至x15y6035y60直线插补至x75y60直线插补至x75y0处程序单g01x450x750y200y650g40g00x1000y600g49z1200x1500y1600m05m30直线插补至x45y45直线插补至x75y20直线插补至x75y65轮廓切削完毕取消刀补快速退至10060的下刀处快速抬刀至z120的对刀点平面主轴停程序结束复位
数控车床刀具补偿及换刀程序编写
重庆市工业学校论文浅谈数控车床刀尖圆弧半径补偿功能与应用浅谈数控车床刀尖圆弧半径补偿功能与应用【摘要】:在数控车削加工中,刀位点与切削点不重合影响零件加工精度。
本文主要介绍刀尖圆弧半径补偿的目的和补偿的具体方法,为简化编程,直接按工件轮廓的实际尺寸编写程序,利用刀具半径补偿指令,数控系统就能加工出符合尺寸要求和精度要求的零件。
【关键词】:数控车削加工刀尖圆弧半径补偿功能与应用一、为什么要用刀尖圆弧半径补偿在数控切削加工,为了提高刀尖的强度,降低加工表面粗造度值,通常在车刀刀尖处制有一圆弧过渡刃。
一般的不重磨刀片刀尖处均呈圆弧过渡,且有一定的半径值,不可能绝对是尖角。
因此,实际上真正的刀尖是不存在的,为简化编程,通常将车刀刀尖看作是一个点—假想刀尖点。
通常说的刀尖只是一“假想刀尖”而已。
但是,编程计算点是根据理论刀尖“假想刀尖”来计算的。
圆弧刀的刀位点在圆弧中心,这样就存在着刀位点与切削点不重合而影响零件的加工精度。
在编制加工程序时,一般是将刀尖看作是一个点,然而实际上刀尖是有圆弧的。
在车端面时,刀尖圆弧的实际切削点与理想刀尖点的Z坐标值相同;车外圆柱表面和内圆柱孔时,实际切削点与理想刀尖点的X坐标值相同。
刀尖圆弧不影响工件尺寸及形状,因此,车端面和内外圆柱表面时不需要对刀尖圆弧半径进行补偿。
当加工轨迹与机床轴线不平行(斜线或圆弧时),则实际切削点与理想刀尖点之间在X、Z轴方向都存在位置偏差。
图表示圆弧刀尖有半径补偿和无半径补偿时的轨迹。
从图中可以看出,采用假想刀尖P编程时,刀具圆弧中心轨迹如图中双点划线所示,刀具实际加工轨迹和工件要求的轮廓形状存在误差,误差大小和圆弧半径r有关。
若采用刀具圆弧中心编程并使用半径补偿功能时刀具圆弧中心的轨迹是图中的细实线,加工轨迹和工件要求的轮廓相等。
在实际加工过程中,刀具切削点在刀圆弧上的位置是变动的,从而在加工过程中可能产生过切或少切现象,具体表现如下:加工台阶面或端面时,对加工表面的尺寸和形状影响不大,但在端面的中心位置和台阶的清角位置会产生残留误差。
数控车床加工刀具补偿功能怎么用?
数控车床加⼯⼑具补偿功能怎么⽤?⼀、数控车床⽤⼑具的交换功能1. ⼑具的交换指令格式⼀:T0101;该指令为FANUC系统转⼑指令,前⾯的T01表⽰换1号⼑,后⾯的01表⽰使⽤1号⼑具补偿。
⼑具号与⼑补号可以相同,也可以不同。
指令格式⼆:T04D01;该指令为SIEMENS系统转⼑指令,T04表⽰换4号⼑,D01表⽰使⽤4号⼑的1号⼑沿作为⼑具补偿存储器。
2. 换⼑点所谓换⼑点是指⼑架⾃动转位时的位置。
⼤部分数控车床,其换⼑点的位置是任意的,换⼑点应选在⼑具交换过程中与⼯件或夹具不发⽣⼲涉的位置。
还有⼀些机床的换⼑点位置是⼀个固定点,通常情况下,这些点选在靠近机床参考点的位置,或者取机床的第⼆参考点来作为换⼑点。
⼆、⼑具补偿功能1. ⼑具补偿功能的定义在数控编程过程中,为使编程⼯作更加⽅便,通常将数控⼑具的⼑尖假想成⼀个点,该点称为⼑位点或⼑尖点。
数控机床根据⼑具实际尺⼨,⾃动改变机床坐标轴或⼑具⼑位点位置,使实际加⼯轮廓和编程轨迹完全⼀致的功能,称为⼑具补偿(系统画⾯上为“⼑具补正”)功能。
数控车床的⼑具补偿分为:⼑具偏移(也称为⼑具长度补偿)⼑尖圆弧半径补偿2. ⼑位点的概念所谓⼑位点是指编制程序和加⼯时,⽤于表⽰⼑具特征的点,也是对⼑和加⼯的基准点。
数控车⼑的⼑位点如图所⽰。
尖形车⼑的⼑位点通常是指⼑具的⼑尖;圆弧形车⼑的⼑位点是指圆弧刃的圆⼼;成形⼑具的⼑位点也通常是指⼑尖。
三、⼑具偏移补偿1. ⼑具偏移的含义⼑具偏移是⽤来补偿假定⼑具长度与基准⼑具长度之长度差的功能。
车床数控系统规定X轴与Z 轴可同时实现⼑具偏移。
⼑具⼏何偏移:由于⼑具的⼏何形状不同和⼑具安装位置不同⽽产⽣的⼑具偏移。
⼑具磨损偏移:由⼑具⼑尖的磨损产⽣的⼑具偏移。
⼑具偏移补偿功能⽰例:FANUC系统的⼑具⼏何偏移参数设置如图所⽰,如要进⾏⼑具磨损偏移设置则只需按下软键[磨耗]即可进⼊相应的设置画⾯。
图中的代码“T”指⼑沿类型,不是指⼑具号,也不是指⼑补号。
数控机床的加工中心的刀具互换技巧
数控机床的加工中心的刀具互换技巧数控机床(Computer Numerical Control, CNC)的加工中心是现代工业制造中常见的关键设备之一。
它以高精度和高效率的加工方式,广泛应用于各个领域,例如汽车制造、航空航天、机械制造等。
在加工过程中,刀具的选择和互换技巧起着至关重要的作用。
本文将介绍数控机床加工中心常用的刀具互换技巧,旨在帮助读者更好地了解和应用这些技巧,提高加工效率和产品质量。
首先,为了实现高效率的加工,刀具的快速互换是必不可少的。
在数控机床加工中心中,常用的刀具互换方式包括手动互换和自动互换。
手动互换一般适用于简单的加工操作,操作人员需经过培训和经验积累,以确保刀具更换的准确性和安全性。
而自动互换则通过机械装置实现,提高了切削过程的连续性和稳定性。
在进行刀具的互换时,要确保机床的电源已关闭,并按照正确的步骤进行操作,以避免造成人员伤害和设备损坏。
其次,刀具的选择和互换要考虑到加工材料的特性和工艺流程的要求。
不同的加工材料对刀具的要求不同,例如钢材的加工需要使用硬质合金刀具,而铝合金的加工适合使用高速钢刀具。
在进行刀具互换时,应根据加工材料的特性选择合适的刀具,并根据工艺流程的要求进行设置和调整。
例如,对于需要进行内外轮廓加工的工件,可以选择带有刀具切割边缘的刀柄,以提高加工效果和精度。
此外,刀具的保养和维修也是刀具互换技巧的重要组成部分。
良好的刀具维护可以延长刀具的使用寿命,提高加工效率和产品质量。
在刀具每次互换后,要及时进行清洁和润滑,以去除切削液、切屑和其它杂质。
对于刀具的磨损和损坏情况,要及时进行检查和更换,以确保刀具的正常运行。
此外,还要注意刀柄和刀片之间的配合精度,确保互换时的可靠性和稳定性。
最后,对于数控机床加工中心的刀具互换技巧,操作人员的技能和经验也是至关重要的。
操作人员应具备良好的机械知识和职业素养,熟悉机床的结构和工作原理,了解刀具的使用和维护方法。
在实践中,操作人员应不断积累经验,注重安全和效率,及时总结和反思,以提高自己的技能水平和工作质量。
- 1、下载文档前请自行甄别文档内容的完整性,平台不提供额外的编辑、内容补充、找答案等附加服务。
- 2、"仅部分预览"的文档,不可在线预览部分如存在完整性等问题,可反馈申请退款(可完整预览的文档不适用该条件!)。
- 3、如文档侵犯您的权益,请联系客服反馈,我们会尽快为您处理(人工客服工作时间:9:00-18:30)。
2、刀具补偿的概念
刀具补偿:是补偿实际加工时所用的刀具与编程时 使用的理想刀具或对刀时使用的基准刀具之间的偏 差值,保证加工零件符合图纸要求的一种处理方法。
3、刀具补偿的种类
刀具补偿
刀具的偏置补偿
(TXXXX实现)
几何位置补偿 磨损补偿
刀尖圆弧半径补偿
(G41、G42实现)
4、刀具的偏置补偿
⑴几何位置补偿 刀具几何位置补偿是用于补偿各刀具安
5、刀尖圆弧半径补偿
⑴刀具半径补偿的目的
➢ 若车削加工使用尖角车刀,刀位点即为刀尖,其 编程轨迹和实际切削轨迹完全相同。
➢ 若使用带圆弧头车刀(精车时),在加工锥面或 圆弧面时,会造成过切或少切。
➢ 为了保证加工尺寸的准确性,必须考虑刀尖圆角 半径补偿以消除误差。
➢ 由于刀尖圆弧通常比较小(常用 r1.2~1.6 mm), 故粗车时可不考虑刀具半径补偿.
➢ 将某把车刀的几何偏置和磨损补偿值存入相应的刀补地址 中。
➢ 当程序执行到含 Txxxx的程序行的内容时,即自动到刀补 地址中提取刀偏及刀补数据。
➢ 驱动刀架拖板进行相应的位置调整。
➢ T XX 00取消几何补偿。
对于有自动换刀功能的车床来说,执行T指令时,将 先让刀架转位,按刀具号选择好刀具后,再调整 刀架拖板位置来实施刀补。
第一节 数控车床刀具补偿
1、为什么需要刀具补偿?
⑴编程时,通常设定刀架上各刀在工作 位时,其刀尖位置是一致的.但由于刀 具的几何形状、安装不同,其刀尖位置 不一致,相对于工件原点的距离不相同.
解决:
•各刀设置不同的工件原点. •各刀位置进行比较,设定刀具偏差补偿.
可以使加工程序不随刀尖位置的不同 而改变.
批量加工后,各把车刀都应考虑磨损补偿 (包括基准车刀)
⑶刀具几何补偿的合成
若设定的刀具几何位置补偿和磨损补偿 都有效存在时,实际几何补偿将是这两者
的矢量和。
X=Xj+Xm、 Z=Zj+Zm
⑷刀具几何补偿的实现
刀具的几何补偿是通过引用程序中使用的 Txxxx来实现的。
T xx xx
过程:
当前刀具号 刀补地址号
装好后,其刀位点(如刀尖)与编程时理 想刀具或基准刀具刀位点的位置偏移的。
通常是在所用的多把车刀中选定一把车 刀作基准车刀,对刀编程主要是以该车刀 为准。
图示
补偿数据获取:
➢分别测出各刀尖相对于刀架基准面的偏离距离[X1,
Z1]、[X2,Z2] 、[X3,Z3]…
➢若选刀具1为对刀用的基准刀具,则各刀具的几何
⑵刀具使用一段时间后会 磨损,会使加工尺寸产生误 差.
解决:
•将磨损量测量获得后进行补偿.
可以不修改加工程序.
⑶数控程序一般是针对刀位点, 按工件轮廓尺寸编制的.当刀尖 不是理想点而是一段圆弧时,会 造成实际切削点与理想刀位点 的位置偏差.
解决:
•对刀尖圆弧半径进行补偿.
可以使按工件轮廓编程不受影响.
⑵刀具半径补偿的方法
• 人工预刀补:人工计算刀补量进行编程 • 机床自动刀补
⑶机床自动刀具半径补偿
机床自动刀补原理
➢当编制零件加工程序时,不需要计算刀具中心运
动轨迹,只按零件轮廓编程。
➢ 使用刀具半径补偿指令。
➢ 在控制面板上手工输入刀具补偿值。
➢ 执行刀补指令后,数控系统便能自动地计算出刀
具中心轨迹,并按刀具中心轨迹运动。即刀具自 动偏离工件轮廓一个补偿距离,从而加工出所要 求的工件轮廓。
第二节、换刀程序编写
1、关于参考点操作的指令
G27、G28、G29. ----- 参考点控制
⑴格式:
G27 X... Z... T0000 ; 回指令参考点检验
G28 X... Z... T0000 ; 经指令中间点再自动回参考点
G29 X... Z... ;
从参考点经中间点返回指令点
⑵各指令功能:
⑷刀具半径补偿指令
❖格式:
G41 G00 X __ Z __
G42 G01
G40 G00 X__ Z __
❖说明:
G41 —刀具半径左补偿
G42 —刀具半径右补偿
G42
G41
G40—取消刀具半径补偿
指令说明:
X、Z 为建立或取消刀补程序段中,刀具移动的 终点坐标。
❖执行刀补指令应注意:
(1)、刀径补偿的引入和取消应在不加工的空行程段上, 且在G00或G01程序行上实施。
偏置分别为 [Xj ,Zj ]
Xj1=0、
Zj1=0
Xj2 =(X2-X1) x 2、Zj2 = Z2-Z1 Xj3 =(X3-X1) x 2、Zj3 = Z3-Z1
⑵磨损补偿 主要是针对某把车刀而言,当某把车刀
批量加工一批零件后,刀具自然磨损后而 导致刀尖位置尺寸的改变,此即为该刀具 的磨损补偿。
2>刀径补偿进行
刀具中心始终与编程 轨迹保持设定的偏置 距离.
3>刀径补偿的取消
❖刀具中心从与编 程轨迹偏离过度到 与编程轨迹重合的 过程.
刀径补偿的引入和取 消必须是不切削的空 行程上.
例1:考虑刀尖半径补偿
D
C (24,-24)
O
O1111 N1 G92 X40.0 Z10.0 N2 T0101 N3 M03 S400 N4 G00 X40.0 Z5.0 N5 G00 X0.0 N6 G42 G01 Z0 F60 (加刀补) N7 G03 X24.0 Z-24 R15 N8 G02 X26.0 Z-31.0 R5 N9 G40 G00 X30 (取消刀补) N10 G00 X45 Z5 N11 M30
(2)、刀径补偿引入和卸载时,刀具位置的变化是一个渐 变的过程。
(3)、当输入刀补数据时给的是负值,则G41、G42互相转 化。
(4)、G41、G42指令不要重复规定,否则会产生一种特殊 的补偿。
⑸刀具补偿的编程实现 1>刀径补偿的引入(初次加载):
❖刀具中心从与编 程轨迹重合到过度 到与编程轨迹偏离 一个偏置量的过程.
刀尖方位的设置
➢ 车刀形状很多,使用时安装位置也各异,由此
决定刀尖圆弧所在位置。
➢要把代表车刀形状和位置的参数输入到数据库中。 ➢以刀尖方位号表示。
从图示可知,
➢ 若刀尖方位码设为0或9时,机床将以刀尖圆弧中 心为刀位点进行刀补计算处理;
➢ 当刀尖方位码设为1~8时,机床将以假想刀尖为
刀位点,根据相应的代码方位进行刀补计算处理。
➢G27用于检查X轴与Z轴是否能正确返回参考点。
X Z 值指机床参考点在工件坐标系的绝对坐标值.