中英文文献翻译-汽车磁流变减振器
应用于汽车减振的磁流变液阻尼器的设计原理
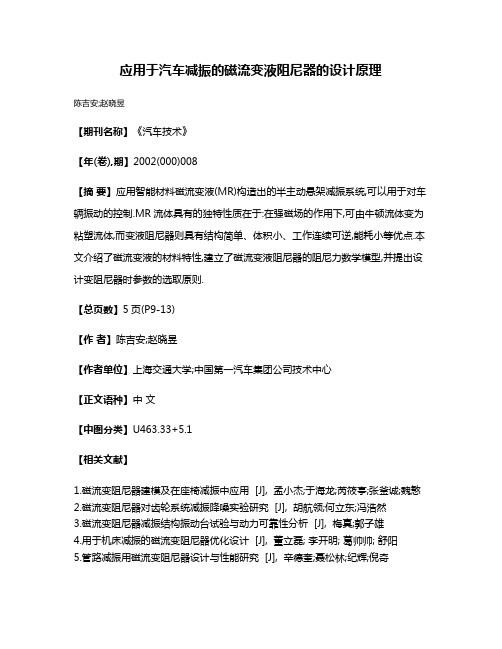
应用于汽车减振的磁流变液阻尼器的设计原理
陈吉安;赵晓昱
【期刊名称】《汽车技术》
【年(卷),期】2002(000)008
【摘要】应用智能材料磁流变液(MR)构造出的半主动悬架减振系统,可以用于对车辆振动的控制.MR流体具有的独特性质在于:在强磁场的作用下,可由牛顿流体变为粘塑流体,而变液阻尼器则具有结构简单、体积小、工作连续可逆,能耗小等优点.本文介绍了磁流变液的材料特性,建立了磁流变液阻尼器的阻尼力数学模型,并提出设计变阻尼器时参数的选取原则.
【总页数】5页(P9-13)
【作者】陈吉安;赵晓昱
【作者单位】上海交通大学;中国第一汽车集团公司技术中心
【正文语种】中文
【中图分类】U463.33+5.1
【相关文献】
1.磁流变阻尼器建模及在座椅减振中应用 [J], 孟小杰;于海龙;芮筱亭;张釜诚;魏慜
2.磁流变阻尼器对齿轮系统减振降噪实验研究 [J], 胡航领;何立东;冯浩然
3.磁流变阻尼器减振结构振动台试验与动力可靠性分析 [J], 梅真;郭子雄
4.用于机床减振的磁流变阻尼器优化设计 [J], 董立磊; 李开明; 葛帅帅; 舒阳
5.管路减振用磁流变阻尼器设计与性能研究 [J], 辛德奎;聂松林;纪辉;倪奇
因版权原因,仅展示原文概要,查看原文内容请购买。
电磁减震器设计中英文对照
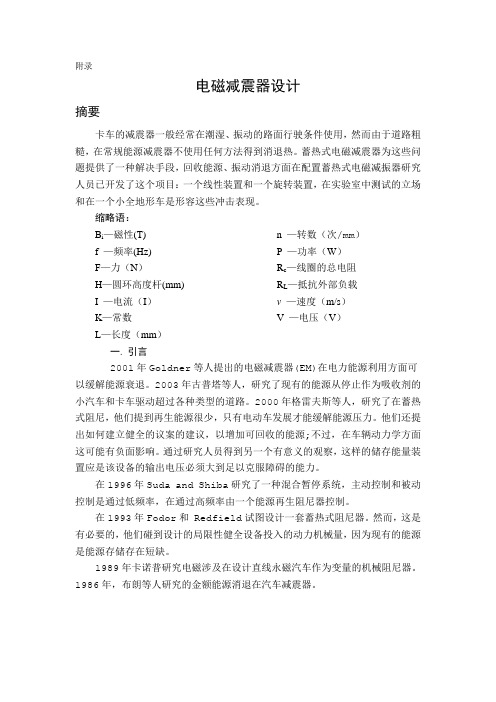
附录电磁减震器设计摘要卡车的减震器一般经常在潮湿、振动的路面行驶条件使用,然而由于道路粗糙,在常规能源减震器不使用任何方法得到消退热。
蓄热式电磁减震器为这些问题提供了一种解决手段,回收能源、振动消退方面在配置蓄热式电磁减振器研究人员已开发了这个项目:一个线性装置和一个旋转装置,在实验室中测试的立场和在一个小全地形车是形容这些冲击表现。
缩略语:B i—磁性(T)f —频率(Hz)F—力(N)H—圆环高度杆(mm) I —电流(I)K—常数L—长度(mm)n —转数(次/mm)P —功率(W)R c—线圈的总电阻R L—抵抗外部负载v—速度(m/s)V —电压(V)一.引言2001年Goldner等人提出的电磁减震器(EM)在电力能源利用方面可以缓解能源衰退。
2003年古普塔等人,研究了现有的能源从停止作为吸收剂的小汽车和卡车驱动超过各种类型的道路。
2000年格雷夫斯等人,研究了在蓄热式阻尼,他们提到再生能源很少,只有电动车发展才能缓解能源压力。
他们还提出如何建立健全的议案的建议,以增加可回收的能源;不过,在车辆动力学方面这可能有负面影响。
通过研究人员得到另一个有意义的观察,这样的储存能量装置应是该设备的输出电压必须大到足以克服障碍的能力。
在1996年Suda and Shiba研究了一种混合暂停系统,主动控制和被动控制是通过低频率,在通过高频率由一个能源再生阻尼器控制。
在1993年Fodor和 Redfield试图设计一套蓄热式阻尼器。
然而,这是有必要的,他们碰到设计的局限性健全设备投入的动力机械量,因为现有的能源是能源存储存在短缺。
1989年卡诺普研究电磁涉及在设计直线永磁汽车作为变量的机械阻尼器。
1986年,布朗等人研究的金额能源消退在汽车减震器。
2005年有趣地注意到,Rani在一本杂志上宣布,百色发言人(制造商著名的百色)经过24年的秘密研究已建立了电磁减振器,然而,没有数据可在表现这些能量的休克吸收。
环形磁路磁流变减振器设计与优化
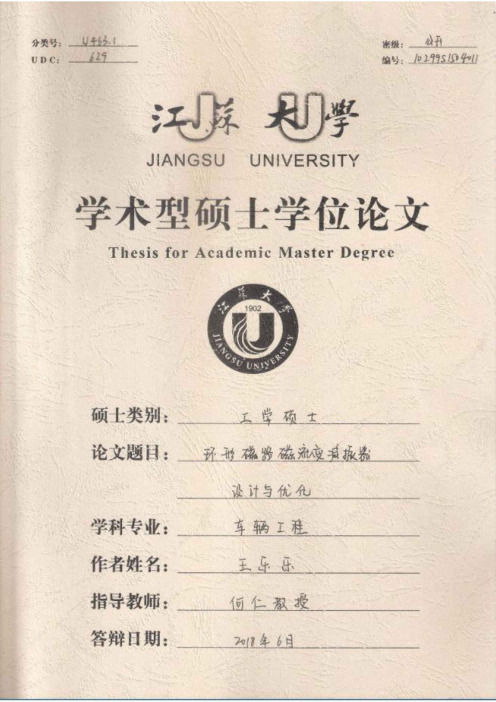
环形磁路磁流变减振器设计与优化Design and Optimization of Annular Magnetic CircuitMR Damper专业名称车辆工程指导教师何仁姓名王乐乐2018年6月摘要悬架作为缓和路面冲击的关键部件,其性能优劣直接影响汽车舒适性。
磁流变(Magnetorheological,MR)减振器作为新型电磁半主动悬架的核心部件,具有响应速度快、阻尼力连续可调、调节范围广、能耗低等诸多优点,其研究与应用前景广阔。
为了对MR减振器进行设计与优化,本文主要研究内容包括:首先,基于Bingham模型与平板模型建立了阀式MR减振器阻尼力模型,基于磁路欧姆定律建立了磁场数学模型。
为了验证理论模型的正确性、进一步研究双级线圈MR减振器的优缺点,基于所建立的理论模型设计加工了MR减振器样机并进行了相关台架试验,获得了样机的示功图与速度特性曲线,结果表明所设计样机性能达标,理论值与试验结果相吻合,说明所建立的数学模型准确有效。
其次,提出一种新型MR减振器。
该减振器具有环形磁路,磁路结构简单,由4个弧形螺线管组成,可以解决双级线圈MR减振器阻尼通道磁场分布不均匀、不利于行程优化等缺点。
以双级线圈MR减振器样机为设计目标,对环形磁路MR减振器进行了结构设计与参数选择。
然后利用改进的非支配排序遗传算法(NSGA-II),以减振器响应时间γ、能耗P、最大行程S以及动力可调系数λ作为优化目标,相关性能要求与空间限制为约束条件,对环形磁路MR减振器进行参数优化,根据优化结果,选取最优设计参数。
最后,对环形磁路MR减振器进行Ansoft磁场有限元分析,结果显示阻尼通道内磁场分布均匀,边缘磁场迅速减弱,漏磁较少。
通过减振器性能仿真,发现在活塞长度较小的前提下,新型减振器的性能达到并超越了双级线圈MR减振器,证明了新型结构的先进性。
通过对阀式MR减振器的研究,发现环形磁路MR减振器在磁场分布以及行程优化上较双级线圈MR减振器存在较大优势,具有实际应用价值,为汽车MR减振器的研究开发提供了新的思路。
磁流变式汽车减振器设计
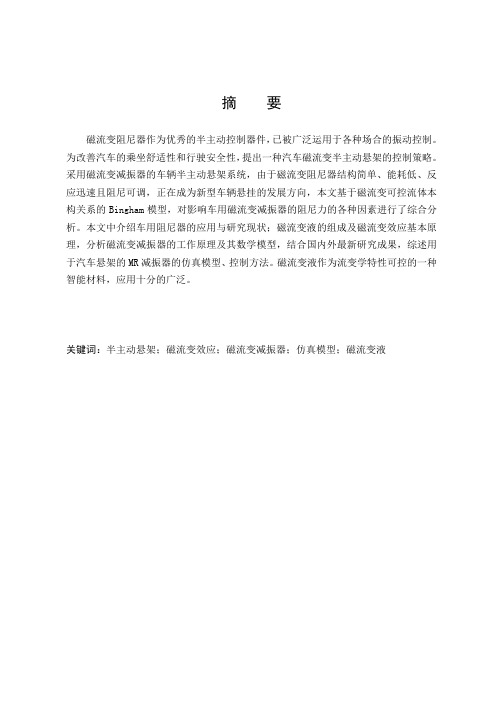
摘要磁流变阻尼器作为优秀的半主动控制器件,已被广泛运用于各种场合的振动控制。
为改善汽车的乘坐舒适性和行驶安全性,提出一种汽车磁流变半主动悬架的控制策略。
采用磁流变减振器的车辆半主动悬架系统,由于磁流变阻尼器结构简单、能耗低、反应迅速且阻尼可调,正在成为新型车辆悬挂的发展方向,本文基于磁流变可控流体本构关系的Bingham模型,对影响车用磁流变减振器的阻尼力的各种因素进行了综合分析。
本文中介绍车用阻尼器的应用与研究现状;磁流变液的组成及磁流变效应基本原理,分析磁流变减振器的工作原理及其数学模型,结合国内外最新研究成果,综述用于汽车悬架的MR减振器的仿真模型、控制方法。
磁流变液作为流变学特性可控的一种智能材料,应用十分的广泛。
关键词:半主动悬架;磁流变效应;磁流变减振器;仿真模型;磁流变液ABSTRACTMagnetorheological damper is one of the most excellent new devices for semi-active control.A control strategy of automobile magneto-rheological semi-active suspension was proposed to improve the riding comfortableness and traveling safety of automobile.Mage- torhological dampers will be an ideal componet of semi-active vibration control in vehicle suspension system for reasons of structure,small volume,energy saving,rapid response and smooth damping.In this paper,based on Bingham model,the damping force of a MRF da- mper is analyzed.And all the factors that affect the damping force of an MRF damper are discussed.In addition the application and research status of automobile damper were intro- duce as well as the principle of magneto-rheological effect and the composition of the mag- neto-rheological fluid.Working principles and models of the automobile magneto-rheologi- acl damper was analyzed and the future focus was discussed after summaring the simulation models,control method and testing technology of automobile mageneto-rheologiacl damper of automobile suspensionAs a kind of controllable smart material,magneto-rheological fluid has gained the extensive attention.Key words: Semi-active suspension;Magneto-rheological effect;Magneto-rheological damper;Simulation model;Magneto-rheologica fluid目录摘要......................................................................................................................................... ІAbstract ................................................................................................................................ Π第1章绪论 .. (1)1.1 概述 (1)1.2 磁流变液的研究 (1)1.3 磁流变阻尼器研究现状 (2)1.4 研究的主要内容 (3)第2章磁流变阻尼器的力学模型 (5)2.1磁流变液效应及流变机理 (5)2.2 磁流变阻尼器工作模式 (6)2.3 参数计算模型 (7)2.4 本章小结 (9)第3章磁流变阻尼器的设计 (10)3.1 磁路设计的影响因素 (10)3.1.1密封件的选择 (10)3.1.2 漏磁分析 (11)3.1.3磁性材料的选择 (12)3.1.4退磁 (13)3.1.5磁流变阻尼器的动态范围 (13)3.1.6阻尼间隙的选取对阻尼器性能的影响 (13)3.1.7阻尼通道有效长度的选取对阻尼器性能的影响 (13)3.1.8磁路结构的分析 (14)3.2磁流变减振器线圈的设计 (14)3.3磁流变减振器的结构设计 (15)3.3.1结构方案的确定 (15)3.3.2磁流变减振器结构优点 (16)3.4磁流变减振器磁路的设计 (16)3.4.1有关参数的初步确定 (16)3.4.2已有参数的确定 (17)3.5磁路相关参数的计算 (19)3.5.1 磁路的计算 (19)3.6 工作缸的计算 (20)3.7 本章小结 (22)第4章磁流变减振器基于Matlab的仿真分析 (23)4.1减振器的阻尼力计算模型 (24)4.2磁流变减振器的仿真分析 (28)4.3本章小结 (29)结论 (31)参考文献 (32)致谢 (33)附录 (34)附录A外文文献原文 .................................................................... 错误!未定义书签。
车用新型旋转式磁流变减振器的设计与仿真
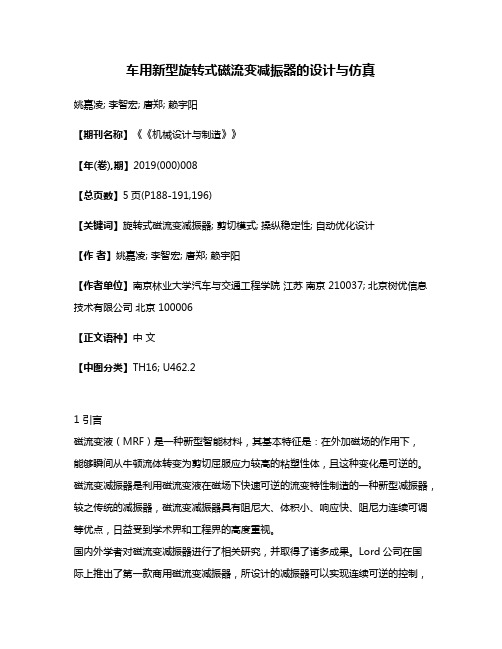
车用新型旋转式磁流变减振器的设计与仿真姚嘉凌; 李智宏; 唐郑; 赖宇阳【期刊名称】《《机械设计与制造》》【年(卷),期】2019(000)008【总页数】5页(P188-191,196)【关键词】旋转式磁流变减振器; 剪切模式; 操纵稳定性; 自动优化设计【作者】姚嘉凌; 李智宏; 唐郑; 赖宇阳【作者单位】南京林业大学汽车与交通工程学院江苏南京 210037; 北京树优信息技术有限公司北京 100006【正文语种】中文【中图分类】TH16; U462.21 引言磁流变液(MRF)是一种新型智能材料,其基本特征是:在外加磁场的作用下,能够瞬间从牛顿流体转变为剪切屈服应力较高的粘塑性体,且这种变化是可逆的。
磁流变减振器是利用磁流变液在磁场下快速可逆的流变特性制造的一种新型减振器,较之传统的减振器,磁流变减振器具有阻尼大、体积小、响应快、阻尼力连续可调等优点,日益受到学术界和工程界的高度重视。
国内外学者对磁流变减振器进行了相关研究,并取得了诸多成果。
Lord公司在国际上推出了第一款商用磁流变减振器,所设计的减振器可以实现连续可逆的控制,通过调节电流实现减振器内部阻尼系数与外部环境的连接,该减振器能量消耗低,且工作稳定[1]。
文献[2]提出了一种基于混合模式的减振器,该减振器具有磁场强度大、阻尼力高等一系列优点,但这种减振器在同时具有剪切、挤压工作模式时的行程较短。
文献[3]设计了一种采用旁通阀的磁流变减振器,有效减小了单个减振器缸筒的体积,但占用了较大的安装空间。
文献[4]研发了一种采用Bifold阀的磁流变减振器,提高了发生磁流变效应的有效长度,但结构复杂,成本较高。
文献[5]设计了一种外置式磁流变减振器,当活塞杆受到外加载荷时,发生左右移动并挤压其两侧的磁流变液,磁流变液在压力差的作用下不断进出外置装置中的阻尼通道,从而产生一定的阻尼力,通过调节励磁线圈中电流的大小来改变阻尼通道中的阻尼力大小,这种结构设计简单可靠,热能耗散快。
磁力矩传感器论文中英文对照资料外文翻译文献
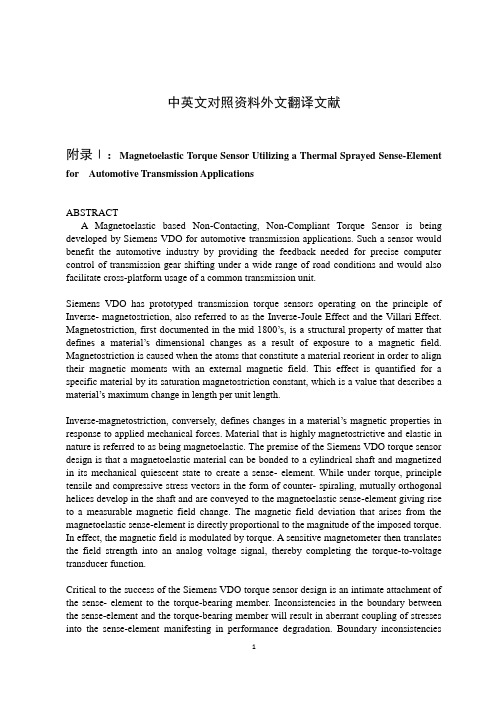
中英文对照资料外文翻译文献附录Ⅰ:Magnetoelastic Torque Sensor Utilizing a Thermal Sprayed Sense-Element for Automotive Transmission ApplicationsABSTRACTA Magnetoelastic based Non-Contacting, Non-Compliant Torque Sensor is being developed by Siemens VDO for automotive transmission applications. Such a sensor would benefit the automotive industry by providing the feedback needed for precise computer control of transmission gear shifting under a wide range of road conditions and would also facilitate cross-platform usage of a common transmission unit.Siemens VDO has prototyped transmission torque sensors operating on the principle of Inverse- magnetostriction, also referred to as the Inverse-Joule Effect and the Villari Effect. Magnetostriction, first documented in the mid 1800’s, is a structural property of matter that defines a material’s dimensional changes as a result of exposure to a magnetic field. Magnetostriction is caused when the atoms that constitute a material reorient in order to align their magnetic moments with an external magnetic field. This effect is quantified for a specific material by its saturation magnetostriction constant, which is a value that describes a material’s maximum change in length per unit length.Inverse-magnetostriction, conversely, defines changes in a material’s magnetic properties in response to applied mechanical forces. Material that is highly magnetostrictive and elastic in nature is referred to as being magnetoelastic. The premise of the Siemens VDO torque sensor design is that a magnetoelastic material can be bonded to a cylindrical shaft and magnetized in its mechanical quiescent state to create a sense- element. While under torque, principle tensile and compressive stress vectors in the form of counter- spiraling, mutually orthogonal helices develop in the shaft and are conveyed to the magnetoelastic sense-element giving rise to a measurable magnetic field change. The magnetic field deviation that arises from the magnetoelastic sense-element is directly proportional to the magnitude of the imposed torque. In effect, the magnetic field is modulated by torque. A sensitive magnetometer then translates the field strength into an analog voltage signal, thereby completing the torque-to-voltage transducer function.Critical to the success of the Siemens VDO torque sensor design is an intimate attachment of the sense- element to the torque-bearing member. Inconsistencies in the boundary between the sense-element and the torque-bearing member will result in aberrant coupling of stresses into the sense-element manifesting in performance degradation. Boundary inconsistenciescan include such imperfections as voids, contaminates, lateral shearing, and localized zones of stress pre-load. Such inhomogeneities may be inherent to an attachment method itself or may subsequently be caused by systemically rendered malformations.Thermal spray, the process where metal particles are deposited onto a substrate to form a coating, was used to address the issue of securely affixing magnetic material to a torque-bearing member. In addition to achieving the prerequisite of an intimate and secure bond, the thermal spray process can be regulated such that the deposited magnetic material is pre-loaded with the internal stresses needed to invoke the inverse- magnetostriction effect.Summarizing, the passive nature of the magnetic sense- element provides an intrinsically simple kernel for the Siemens VDO torque sensor that makes for a highly reliable and stable design. The thermal spray process adds robustness to the mechanical aspect by permitting torque excursions to an unprecedented ±2000% of full scale (per prototype validation testing of certain constructs) without the need for ancillary torque limiting protection devices. Furthermore, accuracy, repeatability, stability, low hysteresis, rotational position indifference, low cost and amenability to the high-volume manufacturing needs of the automotive marketplace are all attributes of this torque sensing technique. When coupled with a magnetometer that is grounded in well- established fluxgate technology, the resultant sensor is inherently dependable and can potentially establish a new standard for torque measuring sensors.INTRODUCTIONAs is well known, automotive transmissions are designed to alter the power transfer ratio between the engine and the drive wheels effectively optimizing engine loading. The engine thereby runs in a narrow and efficient operating band even though the vehicle travels over a wide range of speeds. For automatic transmissions, shift valves select the gear ratio based generally on the throttle position, engine vacuum and the output shaft governor valve state. With the advent of electronic sensors and computerized engine controllers, transmission shift functions have been migrating towards closed-loop operation under software processing control. Along with this progression came the realization that the transmission output torque would provide a valuable feedback parameter for shift and traction control algorithms. The measurement of output torque, however, proved elusive due to the extremely harsh operating conditions. One particular SUV application under consideration required 1% accuracy in measurements of roughly 2700 Nm with possible torque excursion of 4700 Nm; all while exposed to temperature extremes -45 to +160 o C.One method for measuring torque is to examine the physical stresses that develop in a shaft when it is subjected to an end-to-end twisting force. The principle stresses are compressive and tensile in nature and develop along the two counter-spiraling, mutually orthogonal 45 o helices. They are defined by the equation :t = Tr / JWhere T is the torque applied to the shaft, r is the shaft radius and J is the polar moment of inertia.Setting p r4/ 2 = J for a solid cylindrical shaft and r = d/2 yields:t = 16T / p dOnce again, T is the torque applied to the shaft and d is the shaft diameter.Furthermore, the degree of twist experienced by the shaft for a given torque is given by2: q = 32(LT) / (p d4G)Where L is the length of the shaft, T is the applied toque, d is the diameter of the shaft and G is the modulus of rigidity of the shaft. The modulus of rigidity defines the level of elasticity of the shaft material, thus, a lower G value would manifest in a shaft with a higher degree of twist for any given applied torque.Torque induced stresses that occur in the shaft material are transferred into an affixed magnetic coating and give rise to measurable changes in its surrounding magnetic field that are directly proportional to the magnitude of the applied torque; with the polarity of the magnetic field, i.e., north or south, governed by the direction of the applied torque. In essence, this is the premise of torque sensing by means of inverse magnetostriction.TORQUE SENSOR EMBODIMENTTo effectively invoke the inverse-magnetostriction effect, the magnetic material must be correctly pre-loaded with stress anisotropy in its quiescent state. In the case of a cylindrically shaped magnetic element, the anisotropic forces must be circumferential (i.e., tangential) in nature and can be either compressive or tensile –depending on the polarity or sign of the material’s saturation magnetostriction constant. Achieving a homogenous pre-load throughout the magnetic material is crucial if the sensor is to accurately interpret torque regardless of its rotational position within a stationary magnetometer.POSITIVE MAGNETOELASTIC DEVICESEarlier efforts to create such a torque sensing element relied on a sense element made of material with a positive saturation magnetostriction constant. This embodiment was realized with a ring-shaped magnetoelastic element made from 18% nickel-iron alloy that intrinsically requires tensile circumferential pre- loading 3 . Such a pre-load was achieved by pressing the ring onto a tapered area of the base shaft – effectively stretching it. The effect of tensile stress on the magnetic hysteresis behavior is shown in Figure 1 where the remnant inductance, B r , nearly triples. The “easy-axes” of the magnetic domains align circumferentially due to the anisotropy defined by the principal tensile stress vector. When magnetically biased, the system in effect operates as a circumferentially shorted magnet with B approaching B r and H approaching zero.NEGATIVE MAGNETOELASTIC DEVICESTo advance the state of the art, Siemens VDO Automotive has opted for a magnetoelastic element witha negative saturation magnetostriction constant. In this case, the alloy is very high in nickel content exhibiting a saturation magnetostriction, l s , in the range of -3e-5 dl/l and requires the stress pre-load to be tangentially compressive in nature. To achieve this embodiment, the magnetoelastic material that constitutes the sense element is “deposited” onto the base shaft using a high- velocity-oxygen-fuel (HVOF) thermal spray process. The coating thickness is only 0.5mm with an axial length of 25mm. The sense element material is endowed with compressive stress by means of precise control of the thermal spray process parameters. This proprietary procedure transforms a deposition process that normally confers isotropic material properties into one that renders the requisite stress anisotropy.Prototype FabricationMagnetoelastic ElementThe specification for the shaft requires the measurement of torque levels of 2700 Nm with no deleterious effects following exposures of up to 4700 Nm. Operating temperature is -45 o C to 160 o C.By converting from the earlier torque sensor “pressed-on ring” concept to one based on a magnetoelastic material with a negative saturation magnetostriction constant, l s , the design is advanced in several respects. Primarily, its resiliency against stress/corrosion cracking is enhanced by 1) the inherent insusceptibility of high nickel content alloys towards corrosives and 2) by the lower porosity of material in compression. This is in distinct contrast with the high iron content ring placed in tension which is vulnerable to fissuring, material creep and stress corrosion cracking which can, over time, relieve the necessary anisotropic forces causing performancedegradation.An important consequence of using the thermal spray technology is the intimate bond provided between the deposited magnetoelastic element and the base shaft. By using a thermal spray process, the boundary whereby torque induced stresses are transferred is free of such imperfections as voids, galled or furrowed material and localized stress gradients that are all characteristically associated with the pressed-on ring technique. These imperfections can induce aberrations in the magnetic field shape thereby imparting torque measurement errors relative to the rotational position of the shaft with respect to a stationary magnetometer. Furthermore, the strong bond at the interface effectively eliminates the slippage commonly associated with the interference fit of a pressed-on ring during extreme torque exposures. Any movement at this interface will manifest as a biasing of material stresses causing a zero-shift measurement error. This is not a concern when the magnetoelastic element is deposited using an HVOF thermal spray gun. Torque excursions to an unprecedented ±2000% of full scale have been successfully applied directly to prototype sensors without ancillary torque limiting protection devices.In addition, depositing the magnetoelastic element onto a rotating shaft provides an inherently mechanically balanced assembly that imposes no angular velocity (RPM) or angular acceleration limits on the system.Other thermal spray technology attributes are its amenability to high volume manufacturing environments, the robustness of the process insuring consistent reproducibility, and an overall reduction in fabrication steps –such as the elimination of machining procedures to mass-produce rings, cutting operations for precisely matching tapers on the shaft and ring, and pressing operations to install rings onto shafts.Magnetic Field ShapingContributions from the mechanical mounting tolerances of system components (e.g., bearings and bushings) can manifest as a misalignment between the centroid centerlines of the magnetometer and the magnetoelastic element. Once calibrated, any displacement in the positional relationship between these two components will alter the system’s transfer function, possibly causing the overall error to exceed specification. The sharply focused nature of the magnetic field radially emanating from the magnetoelastic element during the application of torque (see Figure 3) accentuates this effect. This error can be minimized by shaping the physical structure of the magnetoelastic element resulting in a contouring of the magnetic field to a more favorable shape. As shown in Figure 4, the magnetic field is made to be less pronounced with an hourglass shaped magneto elastic element and sensitivity to misalignment is, thus, reduced. In this example, the magneto elastic element is contoured such that the air gap between the magneto elastic element and the magnetometer is reduced when axial displacement between their centroid centerlines occurs. The expected reduction in magnetic signal strength caused by this displacement is thus compensated by the air gap reduction.Shafts can be fabricated with a variety of contoured surface adaptations and the thermal sprayed magnetoelastic element’s shape will expectedly follow suit. As is evident, a pressed-on ring manifestation of the magnetoelastic element would be incompatible with this technique. Various contours are being considered for further reducing the sensitivity to misalignment and for improving other performance parameters such as magnetic field strength and hysteresis.Cylindrical Shaft Shown with Superimposed Associated Magnetic Field (i.e., Radially Directed Flux Density)Contoured Shaft (Hourglass Shape) Shown with Superimposed Associated Magnetic Field (i.e., Radially Directed Flux Density)In Figures 3 and 4, the spatial image of the shaft is mapped using a laser displacement system and the superimposed magnetic field is mapped in 3-space with a hall cell.MagnetometerRounding out the torque sensor hardware complement is a non-contacting magnetometer that translates the magnetic signal emitted by the shaft’s sense element into an electrical signal that can be read by system-level devices. Coupling the torque signal to some interim conditioning electronics magnetically is an attractive option due to its “non-contacting” attribute. A signal transference scheme capable of spanning an air gap is advantageous sinceit requires no slip rings, brushes or commutators that can be affected by wear, vibration, corrosion or contaminants.The fundamental magnetometer embodiment, shown in Figure 5, is circular with the shaft passing through its center. The magnetometer encompasses the magnetoelastic element of the shaft and the shaft is allowed to freely rotate within the fixed magnetometer. Power and the output signal pass through the magnetometer’s wiring harness.Transmission Torque Sensor MagnetometerThe magnetometer actually performs several functions beyond measuring a magnetic field’s strength. These functions include magnetic signal conditioning, electrical signal conditioning, implementation of self-diagnostics, and the attenuation of magnetic and electromagnetic noise sources.The magnetic detection method chosen for the torque sensor is fluxgate magnetometry, also known as saturable-core magnetometry. This is a well-established technology that has been in use since the early 1900’s. Fluxgate ma gnetometers are capable of measuring small magnetic field of strengths down to about 10 -4 A/m (or 10 -6 Oe) with a high level of stability. This performance is roughly three orders of magnitude better than that achieved by Hall Effect devices. Although many fluxgate designs use separate drive and pickup coils, the torque sensor magnetometer was designed to use a single coil for both functions.Magnetic signal conditioning is accomplished by use of flux guides integral to the magnetometer. These flux guid es amplify the magnetic signal radiating from the shaft’s sense element prior to detection by the fluxgates thereby improving the signal-to-noise ratio. The flux guides provide additional signal conditioning by integrating inhomogeneities in the magnetic signal relative to the shaft rotational position that might otherwise be misinterpreted as torque variations. The flux guide configuration is shown in Figure 6 and a magnetic simulation of the resulting field concentration is shown in Figure 7.Flux guides surrounding magnetoelastic elementAxial view of magnetic simulation with flux guide material’s relative DC permeability set to 50,000 (e.g., HyMu “80”)To further improve the magnetometer’s immunity to stray signals present in the ambient, common-mode rejection schemes are employed in the design of both the electronic and magnetic circuits. For example, wherever possible, differential circuitry was used in theelectronic design in order to negate common-mode noise. This practice was carried over to the magnetic design through the use of symmetrically shaped flux guides and symmetrically placed fluxgates that cancel common- mode magnetic signals that originate outside the system.Finally, to augment the electrical and magnetic common- mode rejection strategies, EMI and magnetic shielding practices were incorporated into the design to further improve the signal-to-noise ratio. Stray magnetic and electro-magnetic signals found in the ambient are prevented from reaching the fluxgates and the shaft’s magnetic torque-sensing element through the use of shielding material that encompasses these critical components.The functional diagram of Figure 8 depicts the concept of the magnetometer by showing a simplified version of the circuitry with extraneous components removed for additional clarity. An application specific integrated circuit (ASIC) contains all the circuitry necessary to perform the indicated functions.Magnetometer Functional DiagramSummarizing, the multi-function, fluxgate based magnetometer design provides the optimal platform for detecting the modulated magnetic field that emanates from the shaft’s torque-sensing magnetic element. By coupling time-proven fluxgate technology with an innovative flux guide configuration and with sophisticated electronic circuitry, the resultant magnetometer is durable, accurate, and stable and comprehensively achieves the design goals dictated by the application.CONCLUSIONThe latest developments in the magnetoelastic torque sensor that are presented here advance the current state of the technology by addressing many obstacles that have delayed itsacceptance by the automotive industry. Thermal spray deposition of the magnetoelastic element has resolved problems that have plagued earlier versions of the magnetoelastic torque sensor’s active element. The lack of integrity of the shaft/magnetoelastic element interface, stress-corrosion cracking, long term stability, inhomogeneity of magnetic properties and manufacturing processes that run counter to high volume production, are no longer hindering the introduction of magnetoelastic torque sensors into the automotive marketplace. With design goals clearly defined and an aggressive development program invariably progressing, the prospect of an automotive, magnetoelastic based non-compliant torque sensor is now more readily attainable.ACKNOWLEDGMENTSI would like to acknowledge the efforts of Ivan Garshelis who pioneered this approach to torque sensing and who had the unwavering vision to recognize this technology’s potential; and Carl Gandarillas whose scientific and analytical investigative approach has explicated much of the mystery associated with thermal sprayed magnetics. I would also like to express my gratitude to the torque sensor development team at Siemens VDO Automotive for their dedication and the extra effort that they put forth; and to Siemens VDO Automotive management for having the courage to invest in a new technology and the patience to see it through.REFERENCES1. Raymond J. Roark and Warren C. Young, Formulas for Stress and Strain, 5 th Edition, McGraw-Hill; Chapter 9, Torsion2. Stephen H.Crandall and Norman C. Dahl, An Introduction to the Mechanics of Solids, McGraw-Hill; Chapter 6, Torsion3. Ivan J. Garshelis, Magnetoelastic Devices, Inc., IEEE Transaction On Magnetics ; 0018-9464/92 V ol. 28, No. 5 September 5, 1992ADDITIONAL SOURCES1. Richard L. Carlin, Magnetochemistry; Springer-Verlag2. Rollin J. Parker, Advances In Permanent Magnetism; John Wiley & Sons3. Etienne du Tremolet de Lachhesserie, Magnetostriction Theory and Applications of Magnetostriction; CRC Press4. Richard M. Bozorth, Ferromagnetism; IEEE Press附录Ⅱ:磁力矩传感器利用一个热喷涂感知元件在汽车变速器中的应用摘要一个非接触式的,非兼容扭矩的传感器是由西门子VDO正在开发应用于汽车传动之中。
关于车辆减震器的外文文献翻译、中英文翻译
外文翻译减震器减震器(Absorber) ,减震器主要用来抑制弹簧吸震后反弹时的震荡及来自路面的冲击。
在经过不平路面时,虽然吸震弹簧可以过滤路面的震动,但弹簧自身还会有往复运动,而减震器就是用来抑制这种弹簧跳跃的。
减震器太软,车身就会上下跳跃,减震器太硬就会带来太大的阻力,妨碍弹簧正常工作。
在关于悬挂系统的改装过程中,硬的减震器要与硬的弹簧相搭配,而弹簧的硬度又与车重息息相关,因此较重的车一般采用较硬的减震器。
与引震曲轴相接的装置,用来抗衡曲轴的扭转震动(即曲轴受汽缸点火的冲击力而扭动的现象)。
减震器的名词解释减震器(Absorber) ,减震器主要用来抑制弹簧吸震后反弹时的震荡及来自路面的冲击。
减震器的工作原理悬架系统中由于弹性元件受冲击产生震动,为改善汽车行驶平顺性,悬架中与弹性元件并联安装减震器,为衰减震动,汽车悬架系统中采用减震器多是液力减震器,其工作原理是当车架(或车身)和车桥间震动而出现相对运动时,减震器内的活塞上下移动,减震器腔内的油液便反复地从一个腔经过不同的孔隙流入另一个腔内。
此时孔壁与油液间的摩擦和油液分子间的内摩擦对震动形成阻尼力,使汽车震动能量转化为油液热能,再由减震器吸收散发到大气中。
在油液通道截面和等因素不变时,阻尼力随车架与车桥(或车轮)之间的相对运动速度增减,并与油液粘度有关。
减震器与弹性元件承担着缓冲击和减震的任务,阻尼力过大,将使悬架弹性变坏,甚至使减震器连接件损坏。
因面要调节弹性元件和减震器这一矛盾。
(1) 在压缩行程(车桥和车架相互靠近),减震器阻尼力较小,以便充分发挥弹性元件的弹性作用,缓和冲击。
这时,弹性元件起主要作用。
(2) 在悬架伸张行程中(车桥和车架相互远离),减震器阻尼力应大,迅速减震。
(3) 当车桥(或车轮)与车桥间的相对速度过大时,要求减震器能自动加大液流量,使阻尼力始终保持在一定限度之内,以避免承受过大的冲击载荷。
在汽车悬架系统中广泛采用的是筒式减震器,且在压缩和伸张行程中均能起减震作用叫双向作用式减震器,还有采用新式减震器,它包括充气式减震器和阻力可调式减震器。
仿真工具,建模和识别,适用于车辆动力学背景下的汽车减震器外文文献翻译、中英文翻译
附录 1仿真工具,建模和识别,适用于车辆动力学背景下的汽车减震器STEFAAN W.R. DUYM为了模拟车辆动力学,汽车减震器的物理模型一直用多种软件开发和实施进行多体模拟。
在本文中,阻尼器模型结构与一些测量和估计技术一起被简要地阐述,以仅可能从测力计测量中检索模型参数。
这些技术通常用在宝马7系列前悬架上的减震器上。
1.引言减震器的设计包括几个阶段,诸如强调几何形状,强度,耐用性和功能。
功能方面主要用于减震阀调节,目前仍在进行调整乘坐工作的手段,在乘坐工作中,几个原型由乘坐工程师通过一系列测试轨道驾驶汽车进行测试。
然后,乘坐工程师给出他们测试的减震器的评估,并可能调整这一点,以获得更好的驾乘感受来处理汽车的属性。
但是,整个调整过程显然是更偏向主观评估,这可能在很大程度上因人而异甚至随时间变化。
减振器调谐过程中,对乘坐工程师困难的训练过程是导致主观因素的第二大原因。
由于这个原因,业界开始开发一个完整的CAE办法来处理调谐问题(图1)。
这种方法可以分解成三个连续的步骤。
首先,一个阻尼器模型与一组可调谐模型参数将允许获得力、速度和位移的函数。
其次,通过多体模拟的装置,车辆行为的特点通过借助于从给定道路获得的一组力和加速度输入。
最后,这些力和加速度的时间历史通过启发式的装置转换成行驶和操控的量度。
启发式通常导出的信号作为量化度量的加权总和,如RMS值,波峰因素和临界参数。
该启发式计算表示用于乘坐和/或处理一个测量值的标量值。
基于启发式,最佳的设计可以提出。
这些启发式理想地从特定的汽车公司的工程师乘坐的代表性基团而获得,并且可以为每个单独的类型的汽车而变化。
例如,跑车不应该提供与旅行车相似的驾驶行为。
本文介绍了一种阻尼器模型的开发和确定预测阻尼力作为阻尼器位移和速度的函数给定的一组参数。
为了直接涉及该模型的系数提供给可调谐阻尼器组件黑盒模型中,如在神经网络或受力状态图的方法中,被放弃有利于所谓的白盒模型提供的在阻尼器物理必要的洞察力。
一种汽车碰撞磁流变减振器[实用新型专利]
专利名称:一种汽车碰撞磁流变减振器专利类型:实用新型专利
发明人:谭和平,谢宁,刘强,谭晓婧
申请号:CN201120404044.2
申请日:20111021
公开号:CN202251636U
公开日:
20120530
专利内容由知识产权出版社提供
摘要:本实用新型公开了一种汽车碰撞磁流变减振器,其包括工作缸、撞击活塞、撞击活塞杆和阻尼管;撞击活塞置于工作缸内的一端,撞击活塞的一端与撞击活塞杆的一端固定,撞击活塞杆的另一端通过工作缸一端的滑动轴承从工作缸内伸出,撞击活塞的另一端的外圆周上安装有滑动轴承和密封圈,在撞击活塞的另一端与工作缸底部的空间内充满了磁流变液;工作缸的底部固定有阻尼管,且固定在工作缸底部的阻尼管的一端与工作缸是连通的,在阻尼管与工作缸连通处的阻尼管一端的口部安装有密封膜片,在阻尼管另一端的底部密封并固定有圆柱形永久磁体,圆柱形永久磁体的直径小于阻尼管的内径并留有磁流变液流动的间隙,在阻尼管底部的圆周上均布有多个通孔。
申请人:谭晓婧
地址:400084 重庆市大渡口区新山村8号附76号
国籍:CN
更多信息请下载全文后查看。
基于DSP的汽车磁流变减振悬架系统控制策略设计与研究外文文献
RUCK SUSPENSION SYSTEM OPTIMIZATIONINTRODUCTIONTruck suspension systems, hardware innovations for improvements, analytical investigations to improve design,techniques for testing, and computer simulation to predict performance have been described in numerous previous technical papers。
Many of these investigators have been seeking,in some sense,that elusive design which might be termed an optimum suspension system。
The difficulty associated with obtaining an optimal design is primarily due to the difficulty of determining the operating environment (input)and a realistic figure of merit or criterion for optimization (output)。
The fundamental purpose of a vehicle suspension system is to act as a vibration isolation system between the frame,chassis,passengers,and cargo,and the vibratory input caused by road or terrain irregularities. The lack of a firm deterministic definition of the profile to which a vehicle is subjected throughout its lifetime requires a statistical approach,that of random vibration. The author and others,for example ,have previously made some progress in the statistical definition of the input. It appears that a fairly realistic approximation of road or cross-country terrain can be made by assuming a white (equal probability of all frequencies) Gaussian distribution for the slope (or first special derivative)。
- 1、下载文档前请自行甄别文档内容的完整性,平台不提供额外的编辑、内容补充、找答案等附加服务。
- 2、"仅部分预览"的文档,不可在线预览部分如存在完整性等问题,可反馈申请退款(可完整预览的文档不适用该条件!)。
- 3、如文档侵犯您的权益,请联系客服反馈,我们会尽快为您处理(人工客服工作时间:9:00-18:30)。
附录A外文文献原文Magnetorheological damper car.1.Research status of magnetorheological damperMagnetorheological fluid refers to the additional magnetic field,under the action of rheological materials performance changes took place in the liq- uid.Will magnetorheological fluid into the magnetic fluid damper,though the control of magnetic field intensitymcan realize continuous magnetorhological damper,adjustable steplessly.Magnetorhelolgical damper usually adopts piston cylinder structure ,the pathway of MPF damper is on the piston or separate bypass,in the path of MRF,according to the structure of magnetic field can be divided into a bar and a single piston cylinder structure of dual pole.Magnetorheological damper can produce bigger,and according to the damping force of the external environment different easy adjustment magnetic field intensity,the change of shock absorber system to reduce vibration damping, achieve the goal.In the development of MFR devices and Lord,the Unites States and Delphi corporation in automobile damping application research holds June In 1995,the Lord of the fifth international electorheological fluids,and r- elated technologies of MRF,demonstrates a large trucks for semi-active sus- pension seat vibration isolation system p.Lord company recently issued a s- uitable automobile suspension of magnetorhological damper and Rheonetie series of current controller RD.3002.American Delphi company has developed magnet- orheological fluid using semi-active suspension system MagneRide team move suspension system applied in Seville Cadillac STS high-grade car,the suspe- nsion system can be changed according to the driving conditions.University ofVirginia utilization of magnetorhological damper Lord company in Volvo truck Fururecar heavy suspension frame for the cars on experiment,made the obvious eggect of vibration reduction.University ofMaryland and development of auto- motive air compensation structure air compensation structure of magnetorhe- ological damper.The damper adopts flow mode,simple stucture,the damping force change range is 250-1500N.Bok.CHOi Seung Korean coach suspension system isdeveloped magnetorheological damper,dual cylinder structure,damping cylinder located at work channels in damper was design of PID boratory tests show that:the use of magnetorheological damper can greatly improve the traffic safety and comfort.Ford motor company BASF,Germany,etc have invested heavily rd magnetorheological fluid and related componets.In the application of magnetoreohological damper is doing a lot of res- earch.Chongqing university of magnetorheological damper Liao Changrong as the design and control methods are studied,Chenjian of Shanghai jiaotong univer- sity for vehicle damping,the design of nanjing university of aeronautics Guo DALEI of magenorthological damper such vehicles in the semi-active control are studied,jingsu university on the adjustable jd.liu semi-active suspension d- amper control methods are studied,etc,damping design and control research has become hot.2.Semi-active suspension control strategy and research status.Most current semi-active suspension system is to shock absorber real-time control of damping and adjust,its essence is measured by real-time sensor of vehicles running environment and body state,the data to microprocesser control algorithm is calculated according to the optimal damper,and then control re- gulation,shock absorhers damping force to achieve the ideal damping force, imporve the performance of the suspension,one of the key technologies is to control strategy.In the semi-active suspension of 30 years,and veicle engi- neering half-anf-half active suspension control strategy for a lot of resea- rch,the representative of control method can be summarized as follows:(1)The optimal control strategy.The optimal control is simply stated in the given conditions and evaluation function for the performance of the system ,the index optimal control laws.Its theoretical basis is linear optimal control theory,though the establishment of the state equation is proposed control system,target and weighting coeff- icients in the application of target set by the control theory of optimal control law to achieve optimal control.(2)Predictive control.Predictive control refers to the road ahead through the sensor will su-spension devices to information in advance,the parameters adjustment and the actual demand synchronization and reflect the real situation in the road..附录B外文文献翻译汽车磁流变减振器1.磁流变减振器的研究状况磁流变液体是指在外加磁场的作用下,磁流变材料性能发生急剧变化的液体。