基于整体车架模态分析的悬置支架优化设计研究
《2024年汽车动力总成悬置系统振动分析及优化设计》范文

《汽车动力总成悬置系统振动分析及优化设计》篇一一、引言随着汽车工业的快速发展,汽车动力总成悬置系统的性能逐渐成为影响汽车乘坐舒适性和驾驶稳定性的关键因素。
本文旨在通过对汽车动力总成悬置系统的振动进行分析,提出有效的优化设计方案,以提高汽车的整体性能。
二、汽车动力总成悬置系统概述汽车动力总成悬置系统是连接发动机、变速器等动力总成部件与车身的重要装置,其作用是减少动力总成振动对车身的影响,保证汽车行驶的平稳性和舒适性。
该系统主要由橡胶悬置、金属部件以及相应的控制系统组成。
三、振动分析1. 振动来源汽车动力总成悬置系统的振动主要来源于发动机的燃烧振动、曲轴转动引起的惯性力振动以及路面不平引起的整车振动等。
这些振动通过动力总成传递到悬置系统,进而影响汽车的乘坐舒适性和驾驶稳定性。
2. 振动传递路径振动在动力总成悬置系统中的传递路径主要包括:发动机振动通过橡胶悬置传递到金属部件,再通过金属部件传递到车身。
此外,控制系统也会对振动传递产生影响。
3. 振动影响过大的振动会导致车身抖动、噪音增大,影响乘坐舒适性;同时,也会对动力总成部件产生损伤,降低汽车的使用寿命。
因此,对动力总成悬置系统的振动进行分析至关重要。
四、优化设计1. 设计原则针对汽车动力总成悬置系统的振动问题,优化设计应遵循以下原则:减小振动传递、提高系统刚度、优化控制系统等。
同时,还需考虑系统的轻量化、可靠性以及制造成本等因素。
2. 优化方案(1)材料选择:选用高弹性模量、高阻尼性能的橡胶材料,提高悬置系统的减振性能。
(2)结构优化:通过有限元分析等方法,对悬置系统的结构进行优化设计,减小振动传递,提高系统刚度。
例如,可以调整橡胶悬置的形状、尺寸以及布置位置等。
(3)控制系统优化:通过引入先进的控制算法和传感器技术,实现动力总成悬置系统的智能控制,提高系统的响应速度和减振效果。
(4)多场耦合分析:综合考虑发动机、变速器等动力总成部件的振动特性以及车身的动态响应,进行多场耦合分析,为优化设计提供依据。
汽车发动机悬置支架结构优化与可靠性研究
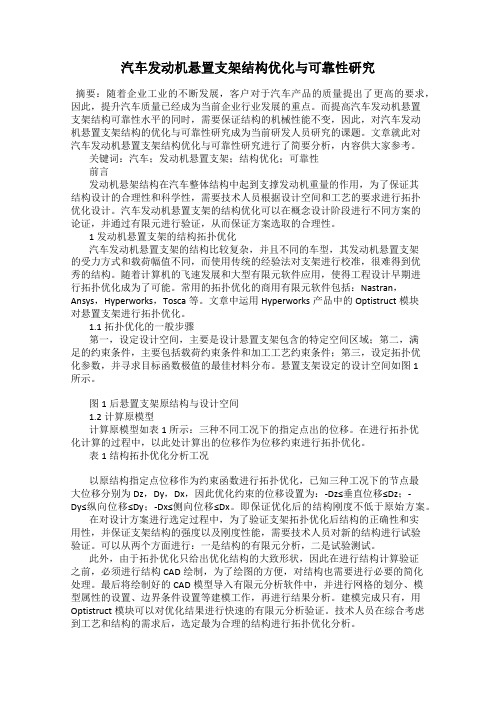
汽车发动机悬置支架结构优化与可靠性研究摘要:随着企业工业的不断发展,客户对于汽车产品的质量提出了更高的要求,因此,提升汽车质量已经成为当前企业行业发展的重点。
而提高汽车发动机悬置支架结构可靠性水平的同时,需要保证结构的机械性能不变,因此,对汽车发动机悬置支架结构的优化与可靠性研究成为当前研发人员研究的课题。
文章就此对汽车发动机悬置支架结构优化与可靠性研究进行了简要分析,内容供大家参考。
关键词:汽车;发动机悬置支架;结构优化;可靠性前言发动机悬架结构在汽车整体结构中起到支撑发动机重量的作用,为了保证其结构设计的合理性和科学性,需要技术人员根据设计空间和工艺的要求进行拓扑优化设计。
汽车发动机悬置支架的结构优化可以在概念设计阶段进行不同方案的论证,并通过有限元进行验证,从而保证方案选取的合理性。
1发动机悬置支架的结构拓扑优化汽车发动机悬置支架的结构比较复杂,并且不同的车型,其发动机悬置支架的受力方式和载荷幅值不同,而使用传统的经验法对支架进行校准,很难得到优秀的结构。
随着计算机的飞速发展和大型有限元软件应用,使得工程设计早期进行拓扑优化成为了可能。
常用的拓扑优化的商用有限元软件包括:Nastran,Ansys,Hyperworks,Tosca等。
文章中运用Hyperworks产品中的Optistruct模块对悬置支架进行拓扑优化。
1.1拓扑优化的一般步骤第一,设定设计空间,主要是设计悬置支架包含的特定空间区域;第二,满足的约束条件,主要包括载荷约束条件和加工工艺约束条件;第三,设定拓扑优化参数,并寻求目标函数极值的最佳材料分布。
悬置支架设定的设计空间如图1所示。
图1后悬置支架原结构与设计空间1.2计算原模型计算原模型如表1所示:三种不同工况下的指定点出的位移。
在进行拓扑优化计算的过程中,以此处计算出的位移作为位移约束进行拓扑优化。
表1结构拓扑优化分析工况以原结构指定点位移作为约束函数进行拓扑优化,已知三种工况下的节点最大位移分别为Dz,Dy,Dx,因此优化约束的位移设置为:-Dz≤垂直位移≤Dz;-Dy≤纵向位移≤Dy;-Dx≤侧向位移≤Dx。
发动机悬置支架模态分析
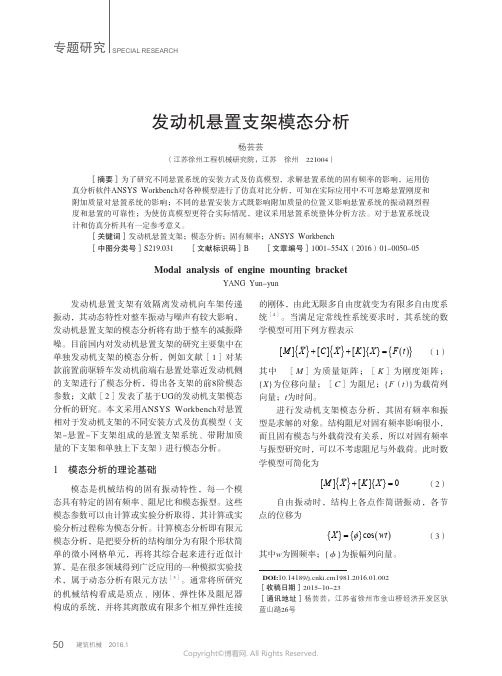
>M>M@^@X^`X`>K>C@^@X^X` ` 0>K @^X`(2^)F t `
点的位自移由为振动时^,X>M结` @构^IX上``c各os>点K w@作t^ X简` 谐0振动,各节
>^KX@ ` w^2I>M`co@ s^ Iw`t 0
(3)
其中w为圆频率;> K{ φ>@K}@为w2振>wM2幅>@M列@0向 ^I量` 。0
悬置、铁芯和悬置护罩
图2 带附加质量的下支架 图3 单独下支架
螺栓和螺母
上支架 下支架
图1 发动机悬置支架系统
进行模态分析时,将图1悬置简化成3个互相 垂直的线性弹簧,悬置的轴向刚度为8250N/mm, 径向刚度为5700N/mm。图1模型的约束边界条 件为下支架的前端面、上支架的端截面和上支架 与发动机连接上端面的螺栓孔附近区域进行全约
1 模态分析的理论基础
模态是机械结构的固有振动特性,每一个模 态具有特定的固有频率、阻尼比和模态振型。这些 模态参数可以由计算或实验分析取得,其计算或实 验分析过程称为模态分析。计算模态分析即有限元 模态分析,是把要分析的结构细分为有限个形状简 单的微小网格单元,再将其综合起来进行近似计 算,是在很多领域得到广泛应用的一种模拟实验技 术,属于动态分析有限元方法[3]。通常将所研究 的机械结构看成是质点、刚体、弹性体及阻尼器 构成的系统,并将其离散成有限多个相互弹性连接
基于nastran的悬置支架模态分析

早期开发过程中具有指导作用,对提高悬置系统的隔振效果,改善整车的 NVH 性能有重要意义。 关键词:模态
Abstract: This paper introduces the modal analysis method for suspension bracket based on MSC.NASTRAN software. This method is very important in the early designing stage of the suspension bracket, especially in enhancing vibration isolation and improving the NVH performance of the vehicle. Keywords: mode FEA NVH mount system
rpm 900 1250 1500 1750 2000 2250 2500 2750 3000 3250 3500 3750 4000 4250 4500 4750 5000 90 80 75
Pa dB(A)
5500 90.00
70 65 60 55 50 40 F F F F
Overall level DOE:S (A ) Order 2.00 DOE :S (A) 30.00 Order 4.00 DOE :S (A) Order 6.00 DOE :S (A)
图 3-4
右侧主动支架改进后模型
4 总结
通过使用 MSC.NASTRAN 软件对支架进行有限元模态分析,并与实验数据进行对比,验 证了仿真结果的准确性。事实证明了有限元法的结果与实验结果非常接近,同样反映出实际 问题。所以,汽车悬置支架模态分析在支架设计过程中有重要的指导意义。 参考文献:
汽车动力总成悬置支架的优化设计

汽车科技第3期2007年5月汽车动力总成悬置支架的优化设计汽车动力总成悬置支架是动力总成悬置系统的安全件和功能件。
一方面,悬置支架连接发动机与车身(或车架、副车架),在汽车的各种行驶工况下,传递作用在动力总成上的一切力和力矩;另一方面,悬置支架的一阶固有频率对车内噪声的影响很大。
因此,在进行动力总成的悬置系统设计时,应对支架的强度和固有频率进行优化设计和试验验证。
在对悬置支架进行设计时,常常将其设计的较重,虽然提高了其强度,但浪费材料,并且由于设计得不合理,可能会导致其一阶固有频率太低,在发动机的工作转速范围内,使悬置支架产生共振,从而增大车内噪声;相反的情况是:支架设计得较薄,在汽车行驶或者进行试验时,造成支架断裂,严重影响汽车的安全性。
因此,悬置支架设计是动力总成悬置系统设计的重要内容之一。
本文以某轿车动力总成发动机悬置支架为例,阐述了悬置支架设计和试验时载荷工况的确定、悬置支架的拓扑优化与形状优化方法,并与试验结果进行了对比分析,证明了本文所述方法的有效性。
1存在的问题在开发某新款轿车时,新车型的动力总成与原车型不一样,因此要对其悬置系统进行重新设计。
按照新车型悬置系统的载荷工况,对原车型动力总成的发动机支架进行疲劳试验时,支架出现了开裂的现象,如图1所示。
因此,在新车型的悬置系统中,不可以借用原车型的支架,应重新进行支架的设计。
为了从理论上解释原支架在新车型的动力总成悬置系统中被破坏的原因,按照新车型的载荷工况,对原支架进行了应力分析。
计算结果表明,在新车型的悬置系统中,如果仍然借用原车型的动力总成的支架,在汽车的极限行驶工况下,原支架的应力会大于支架材料的屈服强度,从而导致支架的疲劳破坏。
图2为原支架的几何模型及有限元模型,该支架为铸钢件,具体材料参数如表1所示。
支架与发动机的连接面为固定约束,与悬置的连接点为加载点,作用在支架上的计算载荷如表2所示,共有四种载荷工况。
(a)几何模型(b)有限元模型图2原支架表1支架材料参数表2悬置支架的计算载荷工况N载荷工况x方向y方向z方向11874.8-564.27023.92-3693.1-1239.2-2485.83153.5-17093217.34-179.41721.7-1870材料杨氏模量/MPa泊松比密度/kg・m-3屈服强度/MPa抗拉强度/MPaZG270-5002.1E+050.37800270500赵艳青1,刘本元2,上官文斌1(1.华南理工大学汽车工程学院,广州510640;2.宁波拓减震系统有限公司,宁波315800)摘要:汽车动力总成悬置支架是动力总成悬置系统的安全件和功能件,它的结构强度影响汽车的安全性,其一阶固有频率对车内噪声有较大的影响。
悬置支架的NVH性能优化设计

悬置支架的NVH性能优化设计宋立爽【摘要】利用有限元分析技术对某车型的发动机悬置支架进行了约束模态分析,得到了发动机悬置支架的第一阶模态频率和振型,并对分析结果进行了评价和分析.为了满足NVH性能要求,对悬置支架进行了结构优化,并对优化后的支架进行了验证分析,优化后的悬置支架模态固有频率满足NVH性能要求.【期刊名称】《机械研究与应用》【年(卷),期】2019(032)002【总页数】2页(P141-142)【关键词】悬置支架;模态;NVH;有限元;优化设计【作者】宋立爽【作者单位】河北中兴汽车制造有限公司,河北保定 071000【正文语种】中文【中图分类】TH1220 引言发动机是汽车的动力源,也是汽车最主要的噪声源和振动源。
发动机的振动如果没有有效地被隔离开来,就会传到汽车的各个部位,最后到达驾驶员和乘客,从而影响人的听力和舒适性。
动力装置隔振系统的设计是减小发动机振动与噪声的一项关键技术。
隔振装置的隔振效果取决于隔振器的刚度,为了达到良好的隔振效果,支架的刚度必须要比隔振器的刚度大到一定程度。
通常遵循两个标准,一个标准是支架刚度应该是隔振器刚度的6~10倍,另一个标准是支架的最低模态频率应该在500 Hz以上[1]。
模态是机械结构的固有振动特性,每一个模态具有特定的固有频率、阻尼比和模态振型。
这些模态参数可以由计算或实验分析取得,其计算或实验分析过程称为模态分析。
计算模态分析即有限元模态分析,是把要分析的结构细分为有限个形状简单的微小网格单元,再将其综合起来进行近似计算,是在很多领域得到广泛应用的一种模拟实验技术,属于动态分析有限元方法[2]。
1 有限元模型建立1.1 几何模型处理悬置支架一般为铸件或者钣金件。
本文以某皮卡车型的左悬置下支架为研究对象,对其进行约束模态分析和结构优化,其结构如图1所示。
首先,将悬置支架的三维模型导入到前处理软件中,导入的几何模型可能会存在多余的点、线和面,及细小几何特征如小的工艺孔、小圆角等。
发动机悬置支架模态分析实践

I阶固有频率。本文通过悬置支架优化设计及模态分析实践,总结出提高模态方法,为设计提供理
论的参考依据。
2对模态影响的因素
2.1
材料对模态的影响
针对材料物理属性:弹性模量、泊松比及密度等情况下对某一悬置支架进行模态分析,并结合
实际材料的应用,考察材料的物理属性对模态的影响。
2.2弹性模量对悬置支架的模态影响
选取两组弹性模量分别为175GPa及210GPa,U=O.30,p=7.8X103Kg/m3,按上述材料物理属性
进行模态分析,约束与发动机装配的螺栓孔,其I阶模态振型如图l所示。结果表明弹性模量的增
加会使悬置支架的I阶固有频率增加。
2.3泊松比对悬置支架的模态影响
选取两组泊松比分别为0.25及0.30,E=210GPa,p=7.8X103Kg/m3,按上述材料物理属性进行模 态分析,约束与发动机装配的三个螺栓孔,其I阶模态振型如图1、图2所示。结果表明泊松比对
E戮
鹾
崮2
I阶楼态振型图(441
7Hz
夕:|1I夕
斟3 I阶模态振型圈(440 5Hz) 图4 I阶模志振型留(441 7Hz
3结构设计对模态的影响
以两个悬置支架的模态分析为例,找出薄弱点或对结构刚度产生影响的原因,为结构的改进设 计提供理论依据。咧6为悬置支架原优化设计方案,模态较低。从模态振型图可看出,红色圈所示 部分为应变能较大的区域,对此部分进行加强可有效改善支架模态。增加加强筋后的结构模态分析 见图7,从上述模态分析可看出,在应变能太部位合理设置加强筋可有效改普模态。
实际应用中以铸钢和球墨铸铁材料为主。如ZGD410—700和QT450-10材料,其参数为
E=2IOGPa/150GPa,lJ=0.30/0.25,p=7.8X103Kg/m3/7.3X103Kg/m3;铸钢材料的悬置支架的模态分析 见图4,球黑铸铁的悬置支架模态分析见图5,结果表明铸钢材料的悬置支架比球墨铸铁材料的悬置 支架I阶固有频率要高。
《2024年汽车动力总成悬置系统振动分析及优化设计》范文

《汽车动力总成悬置系统振动分析及优化设计》篇一一、引言汽车作为现代社会出行的重要工具,其舒适性和安全性已成为消费者选购车辆的重要考量因素。
动力总成悬置系统作为汽车的重要组成部分,其性能直接影响到整车的振动噪声水平及乘坐舒适性。
因此,对汽车动力总成悬置系统的振动进行分析,并进行优化设计,对于提升汽车性能具有重要意义。
本文将就汽车动力总成悬置系统的振动分析及优化设计进行探讨。
二、汽车动力总成悬置系统概述汽车动力总成悬置系统主要由发动机、变速箱、传动系统等组成,其作用是将发动机产生的动力传递至车轮,同时起到减震、降噪、提高乘坐舒适性的作用。
该系统的性能直接影响到整车的运行平稳性和乘坐舒适性。
三、汽车动力总成悬置系统振动分析1. 振动产生原因汽车动力总成悬置系统的振动主要来源于发动机的燃烧、气缸内的工作过程、燃油的喷入以及各种力的相互作用等因素。
此外,路面不平、车身结构等因素也会对系统产生一定的振动影响。
2. 振动分析方法针对汽车动力总成悬置系统的振动分析,可采用理论分析、仿真分析和实车测试等方法。
理论分析主要依据动力学原理和弹性力学原理对系统进行建模和分析;仿真分析则通过建立系统的有限元模型,对系统进行动力学仿真分析;实车测试则是通过在真实环境下对车辆进行测试,获取系统的振动数据。
四、汽车动力总成悬置系统优化设计1. 设计目标汽车动力总成悬置系统的优化设计目标主要包括降低系统振动、提高乘坐舒适性、减少噪声等。
通过对系统进行优化设计,可提高整车的性能和品质。
2. 优化设计方法(1)材料选择:选用高强度、轻量化的材料,如铝合金、复合材料等,以降低系统重量,提高刚度和减震性能。
(2)结构优化:通过优化结构布局和刚度分配,使系统在受到外界力时能够快速恢复稳定状态,减少振动。
(3)主动控制技术:采用主动控制技术,如主动悬挂系统、电磁减震器等,对系统进行实时控制,以降低振动和噪声。
(4)仿真分析:利用仿真软件对系统进行动力学仿真分析,预测系统的振动性能,为优化设计提供依据。
- 1、下载文档前请自行甄别文档内容的完整性,平台不提供额外的编辑、内容补充、找答案等附加服务。
- 2、"仅部分预览"的文档,不可在线预览部分如存在完整性等问题,可反馈申请退款(可完整预览的文档不适用该条件!)。
- 3、如文档侵犯您的权益,请联系客服反馈,我们会尽快为您处理(人工客服工作时间:9:00-18:30)。
第36卷第2期2019年2月机㊀㊀电㊀㊀工㊀㊀程JournalofMechanical&ElectricalEngineeringVol.36No.2Feb.2019收稿日期:2018-08-30基金项目:2017浙江省新苗人才计划项目(2017R405075)ꎻ宁波大学人才工程资助项目(421806920)作者简介:何海涛(1993-)ꎬ男ꎬ江苏淮安人ꎬ硕士研究生ꎬ主要从事结构物仿真与测试方面的研究ꎮE ̄mail:2741717703@qq.com通信联系人:陈振雷ꎬ男ꎬ教授ꎬ博士生导师ꎮE ̄mail:chenzhenlei@nbu.edu.cnDOI:10.3969/j.issn.1001-4551.2019.02.014基于整体车架模态分析的悬置支架优化设计研究∗何海涛1ꎬ陈振雷1∗ꎬ廖俊雄1ꎬ李坚成1ꎬ赵㊀北2(1.宁波大学海运学院ꎬ浙江宁波315800ꎻ2.三一重机有限公司ꎬ江苏昆山215300)摘要:针对某挖掘机发动机悬置系统振动放大问题ꎬ通过采用试验测试和计算机仿真的方法ꎬ评估并优化了其隔振性能ꎮ分析了对应的加速度频谱及该悬置系统在290Hz等频段的共振问题ꎬ采用整车架模态分析方法实现了故障再现ꎻ根据仿真结果ꎬ对悬置支架和车架进行了优化设计ꎬ并对该优化方案进行了试验验证ꎮ研究结果表明:有问题的悬置3点振动传递率得到优化ꎬ达到了减振目标ꎻ悬置2点传递率出现略有升高的情况ꎬ而该位置的振动加速度峰值在优化后得到大幅降低ꎻ传递率升高是整体加速度略有增加引起的ꎮ关键词:悬置支架ꎻ振动加速度ꎻ模态分析ꎻ优化设计中图分类号:TH122ꎻTH113.1ꎻU461.2㊀㊀㊀㊀文献标志码:A文章编号:1001-4551(2019)02-0185-05Mountingbracketoptimizationbasedonintegralframe smodalanalysisHEHai ̄tao1ꎬCHENZhen ̄lei1ꎬLIAOJun ̄xiong1ꎬLIJian ̄cheng1ꎬZHAOBei2(1.FacultyofMaritimeandTransportationꎬNingboUniversityꎬNingbo315800ꎬChinaꎻ2.SANYHeavyMachineryCo.ꎬLtd.ꎬKunshan215300ꎬChina)Abstract:Inordertoresolvethevibrationamplificationissueinthepowertrainmountingsystemofagivenexcavatorꎬthevibrationisolationperformancewasevaluatedandoptimizedbythemethodsofexperimentaldataanalysisandcomputersimulation.Thecorrespondingaccelera ̄tionspectrumandresonanceofthemountingsystemin290Hzandotherfrequencybandswereanalyzedandstudied.Thereasonofthefaultwascapturedbythewholeframemodalanalysismethod.Meanwhileꎬtheoptimizationschemeofthesuspensionbracketandframesuggestedbythesimulationresultswasverifiedbytheexperiment.Theresultsshowthatthevibrationaltransmissionrateofthe#3suspensiongetsopti ̄mizedandreachesthetargetofdecreasingthevibration.Althoughthetransmissionrateofthe#2suspensionbecomesworseslightlyꎬthepeakvalueofthevibrationalaccelerationatthe#2positionisgreatlyreducedbytheoptimization.Theincreaseofthetransmissionrateofthe#2suspensionisduetothetinyraiseoftheoverallacceleration.Keywords:suspensionbracketꎻvibrationaccelerationꎻmodalanalysisꎻoptimumdesign0㊀引㊀言液压挖掘机结构复杂ꎬ相对应的振动和噪声源也较多ꎬ其中动力总成产生的振动噪声是挖掘机振动噪声的主要来源之一[1]ꎮ挖掘机由于其工作的特殊性ꎬ工作过程中振动较大ꎬ缩短了发动机及其他附件的使用寿命ꎬ同时也严重影响驾驶员驾乘舒适性[2 ̄3]ꎮ为解决挖掘机工作过程中振动过大的问题ꎬ发动机悬置系统受到关注ꎮ在悬置系统中ꎬ悬置起到支承发动机㊁衰减和隔离发动机振动的重要作用ꎮ国内外学者对悬置系统减振方面已经做了广泛研究ꎮ杨武森等[4]用有限元软件建立单个悬置支架的有限元模型ꎬ对其模态进行了分析ꎬ并根据模态分析结果对该悬置支架设计进行了优化ꎻ唐因放[5]对动力总成悬置支架进行模态分析ꎬ发现了原支架固有频率为267Hzꎬ与发动机工作转速的激频接近ꎬ会引起共振ꎻ文献[6]对某典型发动机支架进行了有限元分析ꎬ确定了其固有频率ꎻ文献[7]以能量解耦理论对悬置系统进行了解耦优化设计ꎬ优化后使转向柱及座椅处的振动加速度均下降ꎮ许多先进的研究方法及其结果已经应用于工程机械领域的减振降噪研究ꎮ本文将通过某挖掘机在各个工况下的振动测试ꎬ针对测试数据中的问题频段进行单个支架和整体车架模态分析ꎬ提出一套结合测试数据与仿真分析的方法ꎮ1㊀挖掘机振动测试与分析1.1㊀试验测试本文分析的动力总成悬置布置采用4点悬置布置型式ꎬ悬置布置方式和测点布置示意图如图1所示ꎮ图1㊀悬置布置方式和测点布置示意图X 挖掘机行驶方向ꎻY 挖掘机左右方向ꎻZ 竖直方向测试设备为LMS公司的16通道测试仪SCM05ꎮ按照挖掘机前进的方向ꎬ悬置1点是左后ꎬ2点是左前ꎬ3点是右前ꎬ4点是右后ꎮ每个悬置点的主动侧(发动机侧测点)及被动侧(车架侧测点)分别布置1个测点(三向加速度传感器)ꎮ试验测试该挖掘机在低速行走s11档㊁高速行走s11档㊁模拟挖掘s11档㊁怠速s1到s11档下的各测点前后的振动加速度值ꎮ1.2㊀数据分析在悬置系统的隔振性能分析中ꎬ主要关注测试得到的系统振动频率及计算悬置的加速度隔振率ꎬ需对实验测得的加速度信号的功率谱进行分析ꎮ在测试数据中ꎬ将这些正常的数据进行时域到频域的转换ꎬ计算有效值(有效值是一种能够表征随机振动信号振动能量的物理量[8])ꎻ频谱形式为功率谱密度PSDꎮ样本随机振动信号在f1~f2频率区间的均方根值RMS的计算公式为:RMS=A0Δf2+ðk-1i-=1AiΔf+AkΔf2(1)式中:A0 起始采样点的幅值ꎻAk 终止采样点的幅值ꎻAi i频率对应的幅值ꎻΔf 频率步长ꎮ为了更有效地对比振动前后的效果ꎬ工程上采用振动传递率的概念ꎮ传递率定义为:传递率=减振后的振动/减振前的振动[9]ꎮ根据测试结果ꎬ对传递率不满足目标(小于70%)的工况需进行分析改进ꎬ整理得到的图1中4个悬置点各方向不满足目标的RMS值与传递率ꎬ如表1所示ꎮ表1㊀悬置振动加速度RMS值与传递率工况/(r min-1)减振前/g减振后/g传递率/(%)悬置2点Y方向s6(1350)0.310.31100s7(1400)0.390.3077s11(1850)0.560.5293模拟挖掘(1850)0.910.8189悬置3点Z方向s6(1350)0.320.33103s7(1400)0.330.3194s11(1850)0.670.85127模拟挖掘(1850)1.070.8176㊀㊀由表1可以看出:在怠速s6㊁s7㊁s11工况和模拟挖掘工况下ꎬ悬置2点在Y方向传递率较高ꎻ悬置3点在Z方向的传递率达到了100%以上ꎬ存在振动放大现象ꎮ悬置系统是为了隔离发动机在工作过程中的激励振动ꎬ因此其要求隔振后频谱曲线上对应加速度值都减少ꎮ但如果悬置系统所受激励的频率与该系统的某阶固有频率相接近时ꎬ隔振后该频率上加速度会出现不降反升现象ꎬ导致上述传递率超过100%的情况ꎮ悬置2点㊁3点振动信号处理图如图2所示ꎮ(a)悬置2在S6档位Y方向的振动前后信号频谱图681 机㊀㊀电㊀㊀工㊀㊀程第36卷(b)悬置2在S7档位Y方向的振动前后信号频谱图(c)悬置3在S7档位Z方向的振动前后信号频谱图(d)悬置3在S6档位Y方向的振动前后信号频谱图图2㊀悬置2点㊁3点振动信号处理图㊀㊀从振动信号处理图2可知:悬置2点Y方向减振前振动信号在大部分频段都高于减振后的信号ꎬ说明该悬置大部分频段隔振效果明显ꎮ但是在300Hz附近存在严重的振动放大效应ꎬ说明该悬置在该频率点Y方向存在隔振失效或者悬置支架在该频率点存在共振模态ꎬ需要进一步分析改进ꎮ同时ꎬ悬置3点Z方向在290Hz附近也存在严重的振动放大效应ꎮ2㊀模态分析2.1㊀模态分析理论基础模态是机械结构的固有振动特性ꎬ每一个模态具有特定的固有频率㊁阻尼比和模态振型ꎮ这些模态参数可以由计算或实验分析取得ꎬ其计算或实验分析过程称为模态分析ꎮ本文采用有限元模态分析方法[10]ꎮ对于多自由度振动系统的弹性体ꎬ系统运动微分方程为:[M]{㊆x(t)}+[C]{̇x(t)}+[K]{x(t)}={f(t)}(2)式中:[M] 系统质量矩阵ꎻ{x(t)}ꎬ{̇x(t)}ꎬ{㊆x(t)} 系统节点位移㊁速度和加速度ꎻ[C] 系统阻尼矩阵ꎻ[K] 系统刚度矩阵ꎻ{f(t)} 外载荷向量[11]ꎮ对发动机支架进行模态分析ꎬ其固有频率和振型是求解的对象ꎮ结构阻尼对固有频率影响很小ꎬ此处暂不考虑阻尼影响ꎬ因此ꎬ其对应数学模型可简化为:[M]{㊆x(t)}+[K]{x(t)}=0(3)自由振动时结构上各点作简谐振动ꎬ设各节点的位移为:{x(t)}={φ}cos(ωt)(4)式中:ω 圆频率ꎻ{φ} 振幅列向量ꎮ由式(3ꎬ4)可得:([K]-ω2[M]){φ}=0求解[K]-ω2[M]=0ꎬ可求出特征值ω㊁{φ}等系统各阶固有频率和模态振型[12]ꎮ2.2㊀支架有限元模型本文建立原悬置系统上支架与下支架的几何模型及有限元模型ꎬ采用二阶四面体网格ꎮ其上支架通过4个螺栓连接安装在安装座上ꎬ分析时对螺栓孔进行约束ꎮ下支架与车架的连接面为固定约束ꎮ支架的材料均为钢ꎬ其对应的弹性模量为210GPaꎬ密度为7800kg/m3ꎬ泊松比为0.3ꎮ2.3㊀单支架模态仿真分析在进行动力总成悬置设计时ꎬ一般要求外部激励频率与系统固有频率之比至少达到1.414倍时才能起到隔振作用[13]ꎮ该悬置对应的发动机额定转速为2000r min-1ꎬ基频为100Hzꎮ对于该悬置系统ꎬ为规避发动机前4阶激振频率ꎬ要求动力总成悬置支架的一阶模态频率在400Hz以上ꎮ该发动机悬置系统上㊁下支架模态计算结果如表2所示ꎮ表2㊀模态结果部件阶次固有频率/Hz悬置2上支架一阶507.3二阶702.7悬置2下支架一阶445.2二阶859.8悬置3上支架一阶537.1二阶672.4悬置3下支架一阶730.8二阶1588.4781第2期何海涛ꎬ等:基于整体车架模态分析的悬置支架优化设计研究㊀㊀所对应的一阶模态对应的振型图如图3所示ꎮ图3㊀悬置2及悬置3支架振型图根据计算的结果得知:上下支架的一阶频率都在400Hz以上ꎬ满足要求ꎮ但这和实际测试在290Hz附近有共振现象矛盾ꎬ所以需要进一步对整体车架进行模态分析ꎮ2.4㊀整体车架模态分析挖掘机动力总成的整体车架几何模型比较复杂ꎬ需要进行几何清理ꎬ其中对分析结果影响不大的小部件进行简化处理ꎮ本研究建立车架有限元模型ꎬ对整体车架的回旋盘底部螺栓孔进行约束ꎬ计算车架整体模态ꎮ计算的整体车架的模态结果如图4所示ꎮ图4㊀整体车架模态结果在305.8Hz下ꎬ振型最大变形量位于悬置2点下支架的顶端ꎬ支架有明显向Y方向运动ꎬ与试验测试中在304Hz附近支架Y方向振动放大现象一致ꎮ该支架发生较强烈的振动ꎬ进而影响发动机及与其连接零件的振动ꎮ在285.1Hz下ꎬ悬置3点下支架Z向振型变形量较大ꎬ与试验结果相一致ꎮ支架在290Hz附近发生共振ꎬ需要对其进行优化ꎮ3㊀优化设计本研究通过整车模态分析与试验测试数据的对比分析ꎬ证实悬置支架与发动机激励频率300Hz发生共振ꎬ需要对支架进行优化ꎮ在动力总成悬置支架进行优化时需要注意优化后支架不与周围的零件发生干涉ꎬ并保证支架安装方便ꎮ对悬置支架结构的优化方案如图5所示ꎮ图5㊀悬置支架优化图其中ꎬ悬置2下支架在弧形过渡处沿车架边缘进行焊接ꎬ悬置3下支架侧板增加2mmꎬ弧形过渡处沿车架边缘进行焊接ꎮ通过如图4(b)所示的整体车架振型图发现ꎬ车架底板的连接板处振动明显ꎬ带动悬置3下支架的振动ꎬ需对车架进行结构优化ꎮ改进方案如图6所示ꎮ图6㊀改进车架几何模型本研究在车架底板与连接板处加焊一块40mm厚的三角板ꎬ底部椭圆形中空处ꎬ将其焊上一半钢材ꎮ对改进后的悬置支架进行模态分析ꎬ计算模态结果如表3所示ꎮ表3㊀改进悬置支架模态结果悬置2点下支架改进前改进后问题频率/Hz293.6331.5问题频率/Hz305.8悬置3点下支架改进前改进后问题频率/Hz285.1307.4㊀㊀本研究优化的悬置支架模态结果显示:悬置2下881 机㊀㊀电㊀㊀工㊀㊀程第36卷支架模态331.5Hzꎬ悬置3下支架模态307.4Hzꎮ从模态分析结果中可以发现:支架的固有频率升高ꎬ避开了共振频率ꎮ4㊀试验验证本研究根据上述优化方案进行整车改进ꎬ并进行测试ꎬ测试结果如表4所示ꎮ表4㊀改进前后悬置点的传递率工况/(r min-1)改进前传递率/(%)改进后传递率/(%)改进后减振前RMS值/g改进后减振后RMS值/g悬置2点Y方向s6(1350)100730.300.22s7(1400)77870.310.27s11(1850)931130.470.53模拟挖掘(1850)89701.110.78悬置3点Z方向s6(1350)103740.420.31s7(1400)94450.560.25s11(1850)127470.990.47模拟挖掘(1850)76342.060.70㊀㊀由表4可知:改进后悬置3的各工况振动传递率明显下降ꎬ达到良好的减振效果ꎮ悬置2点尽管在s6和模拟挖掘工况改进至目标值ꎬ但在s7㊁s11档的传递率比之前有上升ꎮ进一步分析发现ꎬ该悬置点Y方向在s7档处的振动加速度功率谱密度峰值由改进前的0.03g2/Hz降到0.00799g2/Hzꎻ在s11档振动加速度功率谱密度峰值(在293Hz处)从0.04g2/Hz降为0.00794g2/Hzꎮ整改后悬置在290Hz附近振动响应显著变小ꎬ振动得到改善ꎮ5㊀结束语本研究介绍了悬置系统隔振性能测试ꎬ并结合数值模拟实现了悬置支架减振的目的ꎬ设计了试验测试㊁计算机仿真分析㊁试验验证的研发方案ꎬ对挖掘机动力总成悬置支架的减振分析提供了指导ꎮ针对动力总成悬置振动放大的问题ꎬ当用传统的单支架分析不能实现故障再现时ꎬ采用整体车架模型进行模态分析方法有效ꎬ并据此对悬置支架进行结构优化ꎮ试验结果证明:优化后悬置支架在频率290Hz左右的共振达到明显改善ꎬ对于改进支架后出现振动传递率略有升高的情况ꎬ仔细分析发现其最大振动加速度峰值降低ꎮ参考文献(References):[1]㊀廖瘦石.液压挖掘机动力总成悬置系统隔振性能分析与优化[D].湘潭:湖南科技大学机电工程学院ꎬ2016.[2]㊀王㊀力ꎬ王莉莉ꎬ陆永能ꎬ等.振动压路机驾驶室减振试验研究[J].工程机械ꎬ2011ꎬ42(8):23 ̄26ꎬ7.[3]㊀张㊀一.小型挖掘机驾驶室低频噪声的结构件振动影响研究[D].济南:山东大学机械工程学院ꎬ2017.[4]㊀杨武森ꎬ杨玉玲ꎬ宋树森.关于某动力总成悬置支架的优化设计[J].汽车实用技术ꎬ2014(7):10 ̄11ꎬ43.[5]㊀唐因放.景逸汽车动力总成悬置支架的优化设计[J].汽车技术ꎬ2009(4):34 ̄36.[6]㊀GHORPADEUSꎬCHAVANDSꎬPATILVꎬetal.Finiteelementanalysisandnaturalfrequencyoptimizationofenginebracket[J].InternationalJournalofMechanicalandIndustrialEngineeringꎬ2012ꎬ2(3):1 ̄6[7]㊀CHOS.ConfigurationandsizingdesignoptimizationofPow ̄ertrainmountingsystems[J].InternationalJournalofVehicleDesignꎬ2000ꎬ24(4):32 ̄34.[8]㊀潘德君.汽车运转状态下发动机悬置减振性能测试与评价研究[D].沈阳:东北大学机械工程与自动化学院ꎬ2014.[9]㊀吴业强ꎬ何㊀锋ꎬ占㊀刚ꎬ等.工程车辆驾驶室振动特性分析及悬置优化[J].现代机械ꎬ2017(4):35 ̄39.[10]㊀周永新.应用模态分析的振动支架优化设计[J].现代制造工程ꎬ2009(8):105 ̄107.[11]㊀戚东元.轿车内饰车身模态分析及试验研究[D].合肥:合肥工业大学汽车与交通工程学院ꎬ2017.[12]㊀杨芸芸.发动机悬置支架模态分析[J].建筑机械ꎬ2016(1):50 ̄54.[13]㊀辛㊀雨ꎬ火㊀进ꎬ梁耕龙.动力总成悬置支架振动噪声设计[C].Altair2013技术大会ꎬ北京:Altairꎬ2013.[编辑:李㊀辉]本文引用格式:何海涛ꎬ陈振雷ꎬ廖俊雄ꎬ等.基于整体车架模态分析的悬置支架优化设计研究[J].机电工程ꎬ2019ꎬ36(2):185-189.HEHai ̄taoꎬCHENZhen ̄leiꎬLIAOJun ̄xiongꎬetal.Mountingbracketoptimizationbasedonintegralframe smodalanalysis[J].JournalofMechanical&Elec ̄tricalEngineeringꎬ2019ꎬ36(2):185-189.«机电工程»杂志:http://www.meem.com.cn981 第2期何海涛ꎬ等:基于整体车架模态分析的悬置支架优化设计研究。