塔里木油田高温高压气井完井工艺技术
塔里木油田保护储层的固井技术_安崇清

TECHNOLOGY SUPERVISION IN PETROLEUM INDUSTRY 石油工业技术监督·2013年9月塔里木油田大规模使用深井和超深井、较小间隙井钻完井技术,其地层有几个显著的特点:井底压力高;井底温度高,塔里木油田深井、超深井井底温度平均在100℃以上;特殊岩性分布多,塔里木盆地在沉积过程中,由于沉积相以及沉积物源,使得盐膏层、巨厚砾石层、泥岩层等特殊岩性广泛发育;环境腐蚀性强,部分区块原油伴生气含腐蚀性气体,如H2S、CO2。
此外,铁离子和氯离子含量高。
正是由于这样,使得塔里木油田在固井过程中更要注重对储层的保护,否则,将大大降低油田经济采收率。
1固井质量与保护油气层之间的关系1.1固井质量的主要技术指标是水泥环胶结质量水泥环胶结质量对储层的伤害主要表现在以下几个方面:(1)塔里木油田的压力体系比较复杂,如果环空封固质量不好,会使油气水层发生相互窜流和干扰,可能会诱发储层中的潜在损害因素,比如形成有机碎屑、无机垢、发生乳化堵塞、水锁、微粒的运移、相渗透率变化等[1]。
(2)由于塔里木油田地层压力高,环境腐蚀性强,如果环空封固质量不好,将会对套管造成机械挤压损坏和腐蚀,使得产液相互窜流,伤害储层。
(3)当油气井在进行注水增产等作业时,如果环空封固质量不过关,工作液便在地层中发生互窜,会对储层造成很严重的伤害。
(4)环空封固质量的好坏决定油气是否会上窜到非产层,若封固不好,则会造成油气资源的浪费。
1.2水泥强度衰退问题是影响固井质量的另外一个因素在高温高压情况下,水泥强度衰退是硅酸盐水泥水化过程中不可避免的问题,如果该问题得不到解决,就会形成气窜通道,对油气储层带来损害。
综上所述,固井质量不好是对油气层的最大损害,还会影响到油气井正常生产和后期增产措施的全过程。
2深井固井问题原因分析在塔里木油田的深井固井中,由于高温高压问题在施工过程中遇到很多技术难题,通过实践和研究,总结出了以下几个主要原因:(1)复杂的地层压力体系、环空顶替效率低下、套管不居中、水泥浆的失重、H2S气体的存在等都会造成气窜,发生气窜的气体如果到达井口,可能会造成严重的危害。
高压高产气井试油及完井工艺技术(PPT 90页)

高压高产气井井筒评价
套管腐蚀性评价
判断方式:MIT,MTT,MIDK,内径测量及壁厚测量
高压深井射孔技术
校深方法简介
高压深井射孔技术
校深方法简介
高压深井射孔技术
克拉近 203年来克塔拉里205木油柯田深部10分1 高压迪那深1井1 射孔迪作那业22 技术迪数那据202 迪那201 东秋8
射孔段
射
枪型
孔 枪
试验压力
额定压力
实际工作压力
射
弹型
孔 弹
药性
井下温度
时间指标
起 起爆类型
爆 器
高压高产气井井筒评价
井身结构对测试管柱的影响评价 套管抗外挤评价 套管抗内压评价 射孔套管剩余强度评价 套管悬挂器评价 套管腐蚀性评价 固井质量评价 井口密封性评价 漏失评价 人工井底评价
高压高产气井井筒评价
井身结构对测试管柱的影响评价
塔里木油田部分高压高产气井井身结构和管柱情况
6651.06807.0 86型 173MPa 140MPa 151MPa YD89 HMX 145℃ >200H
2支 无 6根
5518.05549.0
4748.04774.0
89型
86型
170MPa 173MPa
140MPa 140MPa
127Mpa 107MPa
YD89
YD89
HMX
HMX
塔里木油田高温高压气井完井工艺技术

根据现场酸化作业程序及作业时间,依次对入井液进行了静态腐蚀评价及动 态腐蚀评价。在迪那酸化液中采用的缓蚀剂TG201,严格按行业规范进行了评价, 达到了3级协作标准要求,并在DN2-B1井进行了现场试验、确认符合要求后,才正 式用于酸化作业中。
经过本次室内实验评价后,为了进一步减缓酸液对油管的腐蚀,在DN2-8进 二次完井中,在预前置液新添加了TG201,并根据国内外资料调研成果,用清水 +TG201代替了原体系中的NH4Cl顶替液。
未见明显腐蚀
图
片
静态评价结论:
注入鲜酸过程中,油管没有发生腐蚀; 反排过程中,残酸未对管柱产生明显腐蚀;
动态腐蚀评价试验
状态
无应力 鲜酸实验
有应力
温度 0C
时间
认识
鲜酸试验中,
90 128分钟
腐蚀现象较 轻,有应力试 样的腐蚀比无
90 128分钟 应力的试样稍
严重
无应力
残酸实验 有应力
残酸试验中,
90 128小时 试样腐蚀非常
参 数类别
优选油管标准
JFE出厂标准
密封直径(×0.001")
±3.5
±4
完 美 螺 纹(mm)
>=40.8
36.6
其余参数以JFE出厂标准为准,其中公扣紧密距:0-1.9mm;母扣紧密距:8.9110.81mm.
油管密封面检测
1.齿高; 2.螺距; 3.锥度; 4.密封径;
5.鼻端内径(接箍内 径); 6.紧密距; 7.完美螺纹长度; 8.台肩位置。
高温高压气井开发特色技术
现场油管检测(DN2-8/DN2-6)
内
DN2-8油管现场检查六个方面:
塔里木高压气田集输和处理经验谈

塔里木高压气田集输和处理经验谈作为一个重要的天然气产区,中国的新疆地区拥有着丰富的油气资源,其中塔里木盆地的天然气储量位居全国前列。
为了更好地开发利用这一宝贵资源,塔里木盆地相继建设了多个高压气田集输和处理工程。
本文将结合笔者在该领域的实际经验,分享一些关于塔里木高压气田集输和处理方面的技术及注意事项。
一、面对复杂的地质构造,注重勘探开发塔里木盆地的地质条件非常复杂,地质构造和沉积条件极为多变,同时还存在大范围的沙漠区和地表沉降等自然特征。
针对这些复杂的地质特征,在进行气田勘探开发时,需要注重以下几个问题:1. 了解地质构造:在进入气田开发前,必须对该地区的地质构造有一个全面的了解,了解该地区是否存在断层、岩溶等上下构造,是否有子汇、储气层和油气藏等气田开发必要的构造特征。
2. 制定勘探计划:制定详细的地质勘探计划,根据不同地带和地貌特点合理安排勘探方法和区块划分。
3. 选取开发的单元:在已经进入气田开发阶段时,应该选取具有重要意义的开发单元进行开发,将资源进行有效利用。
二、确保集输线路安全运行,保持生产稳定针对高压气田集输以及处理,保证线路的安全运行是至关重要的因素。
通常,高压气田集输和处理项目需要经过前期勘探、设计、施工、调试等多个环节,这些环节需要保持高度的配合与标准化,同时还需要采用多种技术保证安全运行:1. 合理选址:在选址时,需要考虑周边环境、地形地貌、交通条件、气藏构造等方面的因素,保证站点建设的安全性,防止可能带来的危险。
2. 采用优质产品:在进行原材料的选择时,必须采用高质量的金属材料和强度高、耐压性好的管道材料,以保证集输线路的可靠性。
3. 定制化的设计:在进行设计阶段时,应根据实际需要设计出符合标准、易于安装维护的集输线路,同时还应对线路内部相应的各项关键指标、运行数据等都进行详细的规定,以确保线路安全运行。
4. 停车检修:定期进行停车检修,以发现并解决隐患,预防故障发生,以确保生产稳定。
高温高压深井试油完井探析
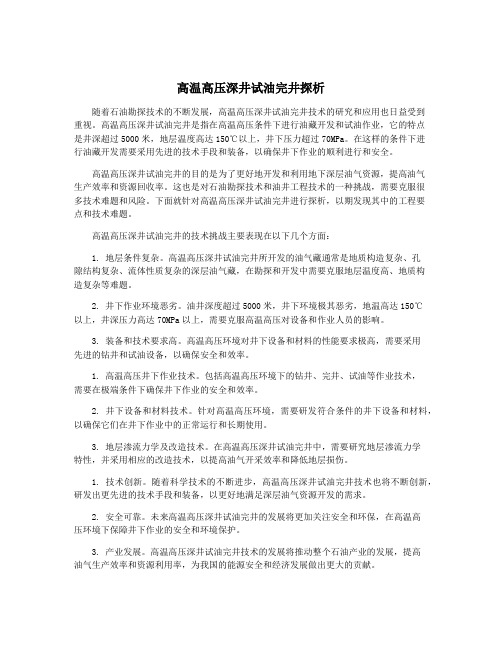
高温高压深井试油完井探析随着石油勘探技术的不断发展,高温高压深井试油完井技术的研究和应用也日益受到重视。
高温高压深井试油完井是指在高温高压条件下进行油藏开发和试油作业,它的特点是井深超过5000米,地层温度高达150℃以上,井下压力超过70MPa。
在这样的条件下进行油藏开发需要采用先进的技术手段和装备,以确保井下作业的顺利进行和安全。
高温高压深井试油完井的目的是为了更好地开发和利用地下深层油气资源,提高油气生产效率和资源回收率。
这也是对石油勘探技术和油井工程技术的一种挑战,需要克服很多技术难题和风险。
下面就针对高温高压深井试油完井进行探析,以期发现其中的工程要点和技术难题。
高温高压深井试油完井的技术挑战主要表现在以下几个方面:1. 地层条件复杂。
高温高压深井试油完井所开发的油气藏通常是地质构造复杂、孔隙结构复杂、流体性质复杂的深层油气藏,在勘探和开发中需要克服地层温度高、地质构造复杂等难题。
2. 井下作业环境恶劣。
油井深度超过5000米,井下环境极其恶劣,地温高达150℃以上,井深压力高达70MPa以上,需要克服高温高压对设备和作业人员的影响。
3. 装备和技术要求高。
高温高压环境对井下设备和材料的性能要求极高,需要采用先进的钻井和试油设备,以确保安全和效率。
1. 高温高压井下作业技术。
包括高温高压环境下的钻井、完井、试油等作业技术,需要在极端条件下确保井下作业的安全和效率。
2. 井下设备和材料技术。
针对高温高压环境,需要研发符合条件的井下设备和材料,以确保它们在井下作业中的正常运行和长期使用。
3. 地层渗流力学及改造技术。
在高温高压深井试油完井中,需要研究地层渗流力学特性,并采用相应的改造技术,以提高油气开采效率和降低地层损伤。
1. 技术创新。
随着科学技术的不断进步,高温高压深井试油完井技术也将不断创新,研发出更先进的技术手段和装备,以更好地满足深层油气资源开发的需求。
2. 安全可靠。
未来高温高压深井试油完井的发展将更加关注安全和环保,在高温高压环境下保障井下作业的安全和环境保护。
高温高压深井试油完井探析

高温高压深井试油完井探析近年来,随着人们对能源的需求不断增长,深海油气资源的开发成为石油行业的重要任务。
高温高压深井试油完井是一项关键的技术,主要用于在深海条件下开采油气资源。
本文将探析高温高压深井试油完井的工艺与挑战,并提出解决方案。
高温高压深井试油完井过程主要分为井下工艺、地面工艺和完井装备三个部分。
井下工艺包括井筒控制、井内裸眼评价和环空工艺等步骤。
地面工艺包括水泥混凝土浆注入、井口螺纹加密和综合数据监测等工作。
完井装备主要包括井底测试仪器、油管套管和井身联接件等。
高温高压深井试油完井的挑战在于复杂的地质条件、高温高压环境和井下作业的潜在风险。
复杂的地质条件可能导致井眼塌陷、岩石碎裂和地层不稳定等问题。
高温高压环境使得设备和材料的选择变得更加困难,同时也增加了作业人员的工作强度和安全风险。
井下作业的潜在风险包括井口失效、压力超限和环境污染等,这些问题可能导致严重的事故和经济损失。
为解决这些挑战,需要采取一系列的技术措施。
应对复杂的地质条件进行优化井眼设计和钻井技术,确保井筒的稳定性和作业的顺利进行。
在选择设备和材料时,需要考虑其适用于高温高压环境的特性,如高温高压下的抗腐蚀性能和力学强度等。
加强设备维护和安全检查,确保其正常运行和井下作业人员的安全。
加强对井下作业的监测和控制,及时发现和解决潜在的安全问题,减少事故发生的可能性。
高温高压深井试油完井是一项复杂而重要的任务,既有挑战也有机遇。
通过合理的工艺设计和技术措施,可以克服各种困难,确保试油完井的顺利进行。
深海油气资源的开发也将为能源供给带来新的活力,推动石油行业的发展。
在深入研究和综合利用已有技术的基础上,还需要不断创新和提高,为高温高压深井试油完井提供更加可靠、高效的技术和设备。
高温高压气井完井技术难点与对策
琏金项 目:『 家科技重人 々项课题 “ = } _ : 『 低渗油气阳完井关键技术 ”( 号:2 0 Z 0 0 2 0 6 编 0 8 X 5 2— 0 ) 作者简介 :熊昕尔 (9 3 ,博上,高级] 程师 ,从事油气田开发 I :E m i xs p@13CI 17 一) 作 - a :xdw i 6 . I l OI
1 完井及测试主要技术难点
高温 、高压气井 由于埋藏深 、高温 、高压 、高 腐蚀等特征 ,完井及测试过程中面临套管磨损与挤 毁 、腐蚀失效 、连接漏失 、封 隔失效 、成本居高不
收 稿 日期 :2 1 0 0—0 6一i 8 修 订 日期 :2 1 一l 一种腐蚀预测方法具有普遍适应性 。 材质选择过低 ,气井面临安全风险 。而由于材 质价格差异 巨大 ,材质选择过高 ,将带来 巨大的资
58 / a rl a eh o g N t aG s cnl y u T o
总第 2 期 4
天然气技术 ・ 钻井工程
面和 纵 向上 产 能差 异 大 ,易导 致 低 产 能 高投 入 的现 象 发生 ,存 在 巨大投 资风 险 。 1 连接 漏 失和封 隔失效 威胁 油气 井安全 . 2 过 高 的关 井 压力 使 油 管 、套 管 、井 下 工 具 及 采 气 井 口都 将 承受 很 大 的 密 封压 差 。 同时 ,深 井 不 同 作 业 工 况 下 管 柱 变 形 量 大 ,如 酸化 测 试 联 作 工 艺 , 大 排 量 注 入 时 ,管 柱 因温 度 降低 和 内 “ 胀 效 应 ” 鼓 而 大 幅 缩 短 ,测 试 时 因温 度 升 高管 柱 又 大 幅 伸 长 ,
含 量 62 . 5%。 在 高 温 、高 压 气 井 完 井 及 测 试 过 程 中 ,面 临安 全性 与经 济性 矛盾 突 出 、连接 漏 失 和 封 隔 失效 、作业 工况 及 井 下条 件 复 杂 、完 井 装 置及 工 具 性能 要 求 高 等诸 多 难点 和 问题 ,有 必 要 对该 类 气 井 完井 测 试技 术 难 点 、对 策 进 行研 究 ,为 高 温 、高 压 含硫 气藏 开发提 供相 应 的技 术支 撑 。
高温高压深井试油完井探析
高温高压深井试油完井探析一、高温高压深井试油完井的定义和特点高温高压深井试油完井是指在高温高压地层条件下进行完井和试油作业的一种技术。
其主要特点在于井深较大、井壁状况复杂、地层温度和压力较高、井筒内外流体环境条件苛刻等。
由于这些特点,高温高压深井试油完井技术对钻井设备、完井工艺、地质勘探等方面的要求都较高。
1. 钻井设备的要求针对高温高压深井试油完井技术,首先要求钻井设备具有良好的耐高温高压性能。
钻井液的性能也要求很高,要能够在高温高压条件下保持稳定,同时具有良好的泥浆堵漏和防漏失的能力。
2. 完井工艺的要求在高温高压深井试油完井过程中,完井工艺显得尤为重要。
特别是对于油气井的完井工艺,要求井筒修井质量高、井下工业的性能稳定、操作易于控制。
典型的完井工艺包括井下动态防漏措施、井下固井工艺、井下井轨技术、井下热回收等。
3. 地质勘探的要求在高温高压深井试油完井阶段,地质勘探要求也相应提高。
这主要表现在一是对目的层的深度、温度、压力等参数的准确测定,二是对方解石与一些特殊性地质类型的特殊地层中的损害分析。
以某油田为例,该油田以深层资源为主要开发对象,采用高温高压深井试油完井技术进行勘探和开发。
通过多年的试验和实践,该油田在高温高压深井试油完井技术方面积累了较为丰富的经验。
该油田对钻井设备进行了改造和升级,加强了在高温高压条件下的稳定性和可靠性。
针对完井工艺的要求,该油田总结了一套适合高温高压条件下的完井工艺,包括动态防漏措施、井下固井工艺、井下井轨技术、井下热回收等。
在地质勘探方面,该油田加强了对目的层的测定和损害分析工作,并建立了高温高压条件下的地质勘探数据库。
通过对高温高压深井试油完井技术的研究和实践,该油田取得了良好的效果。
不仅提高了油气勘探开发的效率,而且提高了油井的整体储量和采收率。
随着能源消耗的不断增加和传统资源的枯竭,高温高压深井试油完井技术将在石油资源的开发利用中扮演越来越重要的角色。
高温高压气井完井工艺介绍
高温高压气井完井工艺介绍
高温高压气井是指井底温度高于150℃,井口压力高于70MPa的气井。
这类气井的开发难度较大,需要采用特殊的完井工艺来确保井口安全和生产效率。
下面将介绍高温高压气井完井工艺的主要内容。
1.井口安全措施
高温高压气井的井口安全措施是完井工艺的重中之重。
首先,需要在井口设置防喷器和防爆器,以防止井口喷出高温高压气体和引起爆炸。
其次,需要在井口设置安全阀,当井口压力超过设定值时,安全阀会自动打开,释放部分气体,以保证井口安全。
2.井筒完井
井筒完井是指在井筒内部设置完井管柱,以保证井筒的完整性和稳定性。
在高温高压气井中,井筒完井的重要性更加突出。
井筒完井需要选择高强度、高温耐受性好的材料,如钛合金、镍基合金等。
同时,需要采用特殊的完井管柱设计,以适应高温高压环境下的井筒变形和应力变化。
3.井底完井
井底完井是指在井底设置完井装置,以保证井底的安全和生产效率。
在高温高压气井中,井底完井需要采用特殊的装置,如高温高压阀
门、高温高压泵等。
同时,需要对井底进行特殊的处理,如加强井底固化、防腐蚀等。
4.井口生产控制
高温高压气井的生产控制需要采用特殊的控制系统,以确保井口生产效率和安全。
控制系统需要具备高温高压环境下的稳定性和可靠性,同时需要具备远程监控和控制功能,以便及时处理井口异常情况。
高温高压气井完井工艺是一项复杂的工程,需要采用特殊的技术和装备。
在完井过程中,需要注重井口安全、井筒完整性、井底安全和生产控制等方面的问题,以确保高温高压气井的安全和生产效率。
高温高压气井完井工艺介绍
高温高压气井完井工艺介绍高温高压气井完井工艺介绍高温高压气井是指井身内部的温度和压力较高的气井,在完井过程中需要特殊注意。
本文将介绍高温高压气井完井工艺,包括工艺流程、材料选择、垂直井段完井和水平井段完井等内容。
一、工艺流程高温高压气井完井流程包括以下步骤:1、钻井和固井前期准备工作:井深确认、井眼直径确定、井眼清洗、井内管柱设计和材质选择、井口装备及固井液、球皮相关物料选择。
2、井下水平井段完井:包括套管下入加积清洗泥浆,水平近段放线聚合物物料、远段啮合工艺流程。
3、井下垂直井段完井:包括套管下入、喷砂、完成水泥浆固井、压裂等工序。
4、固井质量控制及完井流体性能监控:测试工具的应用,完井过程现场液体检测。
5、井筒待完井区域的加固:包括井壁处理和油管环保附着水平井段放线。
6、井口安全事项的安装:防喷器、管线及翻译装备的防爆和避风措施。
二、材料选择在高温高压气井完井过程中,材料的选择很重要。
以下是一些材料选择建议:1、钻井、完井管材料:要求正确选择材料,按设计完井压力要求设计,耐高温、耐腐蚀、耐磨损,避免选择劣质管材。
2、固井液:要求选择高温材料和加高压消泡剂剂量,同时要确保固井水泥浆使用合格、无松散泥层等。
3、完井液:高压液体选用密度大、黏度小的高压石油液体,也可以选择氮气气体。
4、水平井段放线材料:具有良好的抗拉力和耐高温性能的材料,例如高强度聚酰胺。
5、其他材料:防喷器、管线及其它翻译装备需要选择高温、高压耐受性好的材料。
三、垂直井段完井1、套管固定:要选择耐高温、耐腐蚀、强度高的材料。
在套管下入的时候需要注意尺寸,以保证套管能够顺利下入,避免套管因太大或太小而造成完井失败。
2、压裂:压裂技术能够有效提高井壁固定性,防止井壁塌陷。
要注意选择合适的压裂液和压裂参数,可以使用经过模拟和模拟试验的缝隙固结压裂液,同时要确保压裂参数在固井参数内,以确保压裂效果。
四、水平井段完井1、井内完井压力控制可使用压缩空气或压缩氮气来取代液体物料。
- 1、下载文档前请自行甄别文档内容的完整性,平台不提供额外的编辑、内容补充、找答案等附加服务。
- 2、"仅部分预览"的文档,不可在线预览部分如存在完整性等问题,可反馈申请退款(可完整预览的文档不适用该条件!)。
- 3、如文档侵犯您的权益,请联系客服反馈,我们会尽快为您处理(人工客服工作时间:9:00-18:30)。
111t)。
该试样工厂端在塔里木试验发生泄漏,在管材研
6.45mm旧油管
1
0/1 究所按塔里木油田、管材研究所及JFE共同确定的
方案进行试验,未发生泄漏。
材 料 理化性能 检测
实验内容
样品数
分析结果
硬度试验
符合JFE生产厂标准
金相组织 屈服强度 抗拉强度 冲击韧性
7.34mm壁厚2组新样, 6.45mm壁厚2组新样、2 组旧样
为了保证入井管柱和工具的完整性,现场制定了油管及工具入井前三道检测程序:
入井工具井口车间试压及检测 管材和井下工具现场检查
❖ 油管丝扣清洗、检查及本体的检查; ❖ 安全阀外观检查、试压,封隔器及其他工具检查 入井前油管及工具检测:在钻台完成
高温高压气井开发特色技术
加强对油管钳扭矩值的标定
调研了油田公司5家油管服务队的装备现状及应用情况,发现油管钳压力传感器 和拉力传感器存在很大误差,为保证上扣过程中扭矩的准确性,研制了新型扭矩仪校 正棒。
井下安全阀
流动短节
(9 5/8"+9 7/8")*VM140HC
3 1/2"HP1-13Cr110Fox油 管(7.34mm+6.45mm)
3 ½*7.34mm*2000m
7"*5"尾管悬挂器 7"VM140HC
5"VM140HC
7"液压式永久封隔器
坐封球座
生产筛管 死堵 射孔枪窜 灰塞面 5"机桥
高压气井修井作业难点
压井 在关井油压高达90MPa条件下进行挤压井,再采用电缆传输对油管进行打孔后循环压
井,并长时间观察; 管柱切割
气密性扣的上扣扭矩高,与封隔器采用丝扣连接,必须采取切割分离措施后,才能安 全起出油管;但上部井下安全阀内径影响切割工艺,通常需分两步、采取两种切割工艺; 封隔器钻磨与尾管打捞
高温高压气井开发特色技术
制定了管理规范与技术标准
编制管材和丝扣选用标准 制定入井油管质量检测规范 编制三高气井完井设计规范 Q/SY
高温高压气井开发特色技术
入井选材质量控制
选材控制: ❖制定气密性入井油管关键参数的质量检测标准 ❖逐根检测,合格的产品方可送达现场, ❖现场进行二次检测
入井油管选择标准
用密度2.4g/cm3、粘度105s的泥浆41.45m3正循环压井, 再反挤隔离液2m3、密度2.4g/cm3,粘度:95-105s的泥浆65m3。 用密度2.4g/cm3,粘度100-115s的泥浆正循环压井,消耗泥浆39.7m3,井有漏失(漏速:1m3/h) 观察,井口一直有油、套压。
扭矩校正棒
优选施工作业队伍
挑选油管队的原则: 设备先进 人员整体素质高 现场服务态度好 业绩突出
高温高压气井开发特色技术
使用对扣器
手动上到位后液压钳上扣
油管密封面检查
高温高压气井开发特色技术
4、高温高压气井修井技术
修井目的:无法通过放压或其他手段使压力值下降到合理范围的高压气井,采取
修井措施,解决环空超压问题(DN2-8/DN2-6/KL203)。
组织无异常 符合JFE生产厂标准 符合JFE生产厂标准 符合JFE生产厂标准
化学成分
符合JFE生产厂标准 螺纹检测
样品规格
样品数
检测结果
7.34mm新油管内螺纹
6
符合JFE厂规定标准
7.34mm新油管外螺纹
6
符合JFE厂规定标准
6.45mm新油管内螺纹
15 经拉伸/压缩及内压循环试验和卸扣后进 行检测,合格
在HTHP气井进行钻磨,时间长,风险大。
高温高压气井开发特色技术
高压气井修井作业工艺流程
正挤压井
油管穿孔 循环压井
下油管堵塞器 换装放喷器
油管切割 (两次)
打捞封隔器 以上油管柱
放喷测试
重新下管柱 二次完井
查找套压 升高原因
测试方案: 目的:检测封隔器以下管柱与地层是否连通: 方法: 在重泥浆中下入测试管柱; 替入低密度坂土浆,形成小于35MPa的压差; 用小油嘴进行放喷测试。
高温高压气井开发特色技术
引进配套气密封检测装置和气动卡盘
引进气动卡盘装置---解决工厂端及现场端同时紧扣 引进气密封检测装置---解决油管下入丝扣过程中气密封性
高压He气传送 管
气动吊卡与气动卡盘
氦气储能器
封隔器 检测仪
密封筒 封隔器
气密封检测装置
高温高压气井开发特色技术
严格入井油管和井下工具的检测
严重。有应力 状态下的腐蚀 要比无应力
90 128小时 状态下严重
图
片
动态评价结论:
注入鲜酸过程,油管没有发生明显腐蚀; 反排殘酸过程中,若在油管连接处的缝隙出现
滞留,则会产生腐蚀。
高温高压气井开发特色技术
通过油管性能检测、酸化腐蚀实验及综合分析,查清了DN2-8、DN2-6井
完井管柱失效原因。
DN2-8井丝扣渗漏原因
试验内容:
•材料实验 •螺纹上卸扣试验 •拉伸水压试验气 •密封试验
7.34mm壁厚新油管 3 1 上扣曲线和台肩扭矩正常
6.45mm壁厚旧油管 8
1 5组油管试样上扣台肩扭矩偏高; 一根试样(369)卸扣后密封面损伤。
6.45mm壁厚新油管
8
4组3次 一根试样上扣台肩扭矩偏高;一根试样 4组1次 (P11-B12)卸扣后螺纹粘扣。
参 数类别
优选油管标准
JFE出厂标准
密封直径(×0.001")
±3.5
±4
完 美 螺 纹(mm)
>=40.8
36.6
其余参数以JFE出厂标准为准,其中公扣紧密距:0-1.9mm;母扣紧密距:8.9110.81mm.
油管密封面检测
1.齿高; 2.螺距; 3.锥度; 4.密封径;
5.鼻端内径(接箍内 径); 6.紧密距; 7.完美螺纹长度; 8.台肩位置。
❖由于上扣扭矩不足,导致密封面接触 应力不够,在酸化及放喷过程中,受温 度及压力的影响,管柱受力发生变化,
油管规格
接头端别
HP1-13Cr 73.0×5.51mm 110 FOX HP1-13Cr 88.9×6.45mm 110 FOX HP1-13Cr 88.9×7.34mm 110 FOX
现场端 工厂端 两者之差 现场端 工厂端 两者之差 现场端 工厂端 两者之差
未见明显腐蚀
图
片
静态评价结论:
注入鲜酸过程中,油管没有发生腐蚀; 反排过程中,残酸未对管柱产生明显腐蚀;
动态腐蚀评价试验
状态
无应力 鲜酸实验
有应力
温度 0C
时间
认识
鲜酸试验中,
90 128分钟
腐蚀现象较 轻,有应力试 样的腐蚀比无
90 128分钟 应力的试样稍
严重
无应力
残酸实验 有应力
残酸试验中,
90 128小时 试样腐蚀非常
油管规格
7.34mm新油管 6.45mm新油管 6.45mm旧油管 (密封面完好)
复合载荷气密封性能试验
样品数
泄漏/ 未泄漏
说明
2
0/2
无泄漏
7
0/7
无泄漏
2
1/1
第2Z号试样泄漏(内压84MPa、轴向载荷117t)
第2T号试样第一次试验泄漏(内压52MPa、轴
6.45mm旧油管 (密封面损伤)
3
2/1 向载荷42t),第2次试验未泄漏; 第3T号试样泄漏(内压91MPa、轴向载荷
漏点形貌
检查发现一根油管腐蚀穿孔。
DN2-6井开孔周围局部腐蚀宏观形貌
局部放大
高温高压气井开发特色技术
油管室内评价试验(DN2-8)
依据ISO 13679:2002/API
RP 5C5 3rd标准,试样采用
上 卸扣试验
7.34mm和6.45mm两种壁厚, 油管规格
样品数
上卸扣 次数
结果
总计38根。
下由CO2引起腐蚀,加剧了渗漏。
DN2-6井管柱失效原因
在油管局部缺陷处,由氯化物应力腐蚀 导致油管开裂。
DN2-6应力开裂穿孔
高温高压气井开发特色技术
5、高温高压气井完井质量控制技术
鉴于迪那2气田DN2-8、DN2-6井管柱失效导致环空压力异常高压的教训,结合研 究成果,为全面加强和提高塔里木油田高压气井的完井质量水平。对完井工艺和完井 质量控制提出了优化、改进与完善。
油管腐蚀试验(DN2-8)
根据现场酸化作业程序及作业时间,依次对入井液进行了静态腐蚀评价及动 态腐蚀评价。在迪那酸化液中采用的缓蚀剂TG201,严格按行业规范进行了评价, 达到了3级协作标准要求,并在DN2-B1井进行了现场试验、确认符合要求后,才正 式用于酸化作业中。
经过本次室内实验评价后,为了进一步减缓酸液对油管的腐蚀,在DN2-8进 二次完井中,在预前置液新添加了TG201,并根据国内外资料调研成果,用清水 +TG201代替了原体系中的NH4Cl顶替液。
最小 2450 2820 370 4080 4690 610 4450 5120 670
上扣扭矩 N·m 最佳 2630 2940 310 4390 4895 505 4790 5340 550
最大 2820 3060 240 4690 5100 410 5120 5560 440
引起丝扣失封
❖管柱在发生渗漏后,在高温高压工况
DN2-8井油管现场检查
高温高压气井开发特色技术
现场油管检测(DN2-8/DN2-6)
DN2-6油管现场检查:
局部放大
入井的第244号油管出现穿孔,漏 点2293.99m,漏点距油管外螺纹端部约 133mm,沿油管周向长约53mm,约占油 管整个圆周的1/5,宽约20~30mm。刺 穿方向为横向,由于冲刷作用,周边光 滑明亮,部分区域显示紫铜色。