氯脆——氯化物应力腐蚀破裂
氯化物应力腐蚀开裂
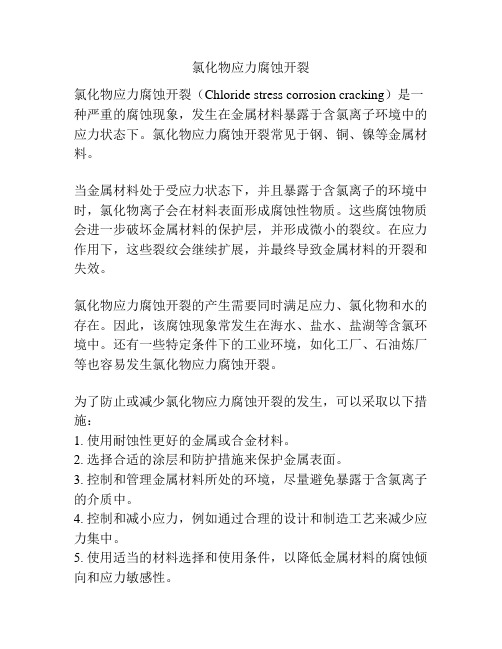
氯化物应力腐蚀开裂
氯化物应力腐蚀开裂(Chloride stress corrosion cracking)是一种严重的腐蚀现象,发生在金属材料暴露于含氯离子环境中的应力状态下。
氯化物应力腐蚀开裂常见于钢、铜、镍等金属材料。
当金属材料处于受应力状态下,并且暴露于含氯离子的环境中时,氯化物离子会在材料表面形成腐蚀性物质。
这些腐蚀物质会进一步破坏金属材料的保护层,并形成微小的裂纹。
在应力作用下,这些裂纹会继续扩展,并最终导致金属材料的开裂和失效。
氯化物应力腐蚀开裂的产生需要同时满足应力、氯化物和水的存在。
因此,该腐蚀现象常发生在海水、盐水、盐湖等含氯环境中。
还有一些特定条件下的工业环境,如化工厂、石油炼厂等也容易发生氯化物应力腐蚀开裂。
为了防止或减少氯化物应力腐蚀开裂的发生,可以采取以下措施:
1. 使用耐蚀性更好的金属或合金材料。
2. 选择合适的涂层和防护措施来保护金属表面。
3. 控制和管理金属材料所处的环境,尽量避免暴露于含氯离子的介质中。
4. 控制和减小应力,例如通过合理的设计和制造工艺来减少应力集中。
5. 使用适当的材料选择和使用条件,以降低金属材料的腐蚀倾向和应力敏感性。
总之,氯化物应力腐蚀开裂是一种复杂和严重的腐蚀现象,在实际的材料选择和设计中需要充分考虑和预防。
硫化氢腐蚀的机理及影响因素.
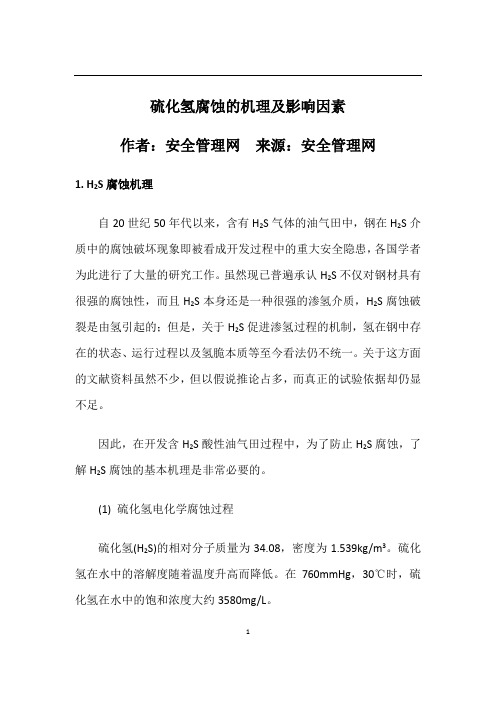
硫化氢腐蚀的机理及影响因素作者:安全管理网来源:安全管理网1. H2S腐蚀机理自20世纪50年代以来,含有H2S气体的油气田中,钢在H2S介质中的腐蚀破坏现象即被看成开发过程中的重大安全隐患,各国学者为此进行了大量的研究工作。
虽然现已普遍承认H2S不仅对钢材具有很强的腐蚀性,而且H2S本身还是一种很强的渗氢介质,H2S腐蚀破裂是由氢引起的;但是,关于H2S促进渗氢过程的机制,氢在钢中存在的状态、运行过程以及氢脆本质等至今看法仍不统一。
关于这方面的文献资料虽然不少,但以假说推论占多,而真正的试验依据却仍显不足。
因此,在开发含H2S酸性油气田过程中,为了防止H2S腐蚀,了解H2S腐蚀的基本机理是非常必要的。
(1) 硫化氢电化学腐蚀过程硫化氢(H2S)的相对分子质量为34.08,密度为1.539kg/m3。
硫化氢在水中的溶解度随着温度升高而降低。
在760mmHg,30℃时,硫化氢在水中的饱和浓度大约3580mg/L。
1在油气工业中,含H2S溶液中钢材的各种腐蚀(包括硫化氢腐蚀、应力腐蚀开裂、氢致开裂)已引起了足够重视,并展开了众多的研究。
其中包括Armstrong和Henderson对电极反应分两步进行的理论描述;Keddamt等提出的H2S04中铁溶解的反应模型;Bai和Conway对一种产物到另一种产物进行的还原反应机理进行了系统的研究。
研究表明,阳极反应是铁作为离子铁进入溶液的,而阴极反应,特别是无氧环境中的阴极反应是源于H2S中的H+的还原反应。
总的腐蚀速率随着pH的降低而增加,这归于金属表面硫化铁活性的不同而产生。
Sardisco,Wright和Greco研究了30℃时H2S-C02-H20系统中碳钢的腐蚀,结果表明,在H2S分压低于0.1Pa时,金属表面会形成包括FeS2,FeS,Fe1-X S在内的具有保护性的硫化物膜。
然而,当H2S分压介于0.1~4Pa时,会形成以Fe1-X S为主的包括FeS,FeS2在内的非保护性膜。
管道保温层下腐蚀泄漏分析与应对措施

管道保温层下腐蚀泄漏分析与应对措施发布时间:2021-06-22T06:54:28.571Z 来源:《防护工程》2021年5期作者:杨富淋[导读] 本文通过分析某企业制氢换热器管道泄漏现象,发现管道外保温破损严重导致水汽和保温层中氯离子在管道外壁富集,当温度降低时,管道处于发生应力腐蚀破坏的适应温度下,因奥氏体不锈钢是应力腐蚀敏感材料,是发生了应力腐蚀开裂,同时也提出已知缺陷做防腐缠绕碳纤维加固、喷丸处理施加保温层及外防护层等措施。
杨富淋身份证号:21030319820xxxx616摘要:本文通过分析某企业制氢换热器管道泄漏现象,发现管道外保温破损严重导致水汽和保温层中氯离子在管道外壁富集,当温度降低时,管道处于发生应力腐蚀破坏的适应温度下,因奥氏体不锈钢是应力腐蚀敏感材料,是发生了应力腐蚀开裂,同时也提出已知缺陷做防腐缠绕碳纤维加固、喷丸处理施加保温层及外防护层等措施。
关键词:CUI腐蚀、隐患排查、失效分析一、概述某企业于2020年10月发现换热器E304副线管道发生泄漏。
拆除管道保温后,发现两处漏点。
副线管道于2018年投用,管道材质304L不锈钢。
管内介质:中温变换气(80%H2及CO、CO2、水蒸气、微量H2S等);操作压力2.0MPa;当管道内的介质流动时,操作温度300℃;管道内的介质不流动时,温度高于150℃。
从外观来看,漏点处位于管道水平管段的底部,漏点共有2处。
管道漏点处有垢物和裂纹存在;而且,管道上有多处锈蚀,锈蚀处有腐蚀产物和保温棉粘附在一起,漏点在其中一处粘附区域的边缘,见图1。
图3 管道断口的SEM+EDS可见,管道开裂是由氯离子引发的应力腐蚀开裂,即氯脆。
我们认为管道的开裂泄漏是从管道外壁发生和发展的,与管道内的中温变换气介质无关。
主要影响因素是管道外部的环境介质、管道应力状态和运行温度等。
保温层下不锈钢设备和管道应力腐蚀破裂(ESCC)是由水及其氯离子等杂质,在一定拉应力和温度的共同作用下造成的。
承压设备损伤模式识别试题和答案

一、单选题【本题型共44道题】1.下列选项中()不属于机械疲劳损伤发展阶段。
A.微观裂纹萌生B.宏观裂纹扩展C.变形D.瞬时断裂正确答案:[C]用户答案:[C] 得分:1.002.如果已经发现了碱腐蚀,还应注意下列哪些可能伴随的损伤?()A.蒸汽阻滞B.球化C.蠕变D.敏化正确答案:[A]用户答案:[A] 得分:1.003.下面几种材料之间比较,哪一种抗环烷酸腐蚀性能最好?()A.Q245RB.304LC.316D.304正确答案:[C]4.下列哪种已知合金可以耐受所有条件下的金属粉化影响?()A.低合金钢B.奥氏体不锈钢C.碳钢D.目前没有正确答案:[D]用户答案:[D] 得分:1.005.盐酸腐蚀速度随温度(),腐蚀速率()。
A.升高,减小B.升高,增大C.升高,不变D.降低,不变正确答案:[B]用户答案:[B] 得分:1.006.冲刷流体可以分为几种?()A.2种B.3种C.4种D.5种正确答案:[B]7.运行期间可采用什么方法来检测冷壁设备的高温部位、判断耐火材料的损伤程度?()A.红外热像仪B.目视检测C.超声检测D.射线检测正确答案:[A]用户答案:[A] 得分:1.008.渗碳损伤导致材料表面硬度(),高温蠕变延展性、常温力学性能、焊接性能和耐腐蚀性能()。
A.增高;增高B.增高;降低C.降低;降低D.降低;增高正确答案:[B]用户答案:[C] 得分:0.009.下列叙述中,()为常见于装置的金属盐酸腐蚀特点描述。
A.常压塔塔顶系统中,塔顶油气冷却形成含盐酸的冷凝液,PH值较低,可对管道和热交换器(包括壳体、管束和管箱)造成快速腐蚀;减压塔顶真空喷射器和冷凝设备会发生盐酸腐蚀B.催化剂中被置换出来的氯化物会反应形成盐酸,流向反应产物系统、再生系统、稳定塔、脱丁烷塔和进料/预加热热交换器;氯化氢也可能随着工艺流穿过分馏单元,在注水点及其下游发生严重的酸露点腐蚀C.催化剂中含有氯化物,如三氯化钛,在聚丙烯的合成工艺中,与水蒸气或谁接触的设备和管线D.反应产物含有HCl,在冷凝后形成盐酸腐蚀;废气系统含有氨和盐酸,对热进料/出料交换器形成氯化铵盐的垢下腐蚀;蒸馏工段可发生严重的盐酸露点腐蚀正确答案:[A]用户答案:[A] 得分:1.0010.检查燃灰腐蚀的最有效的方法为()。
应力腐蚀断裂
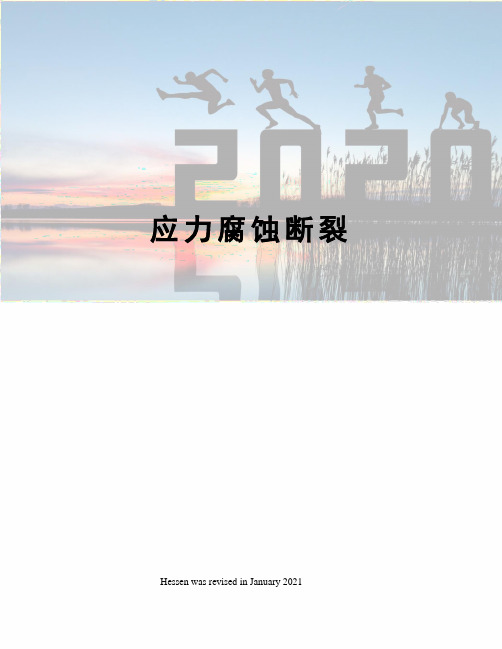
应力腐蚀断裂 Hessen was revised in January 2021应力腐蚀断裂一.概述应力腐蚀是材料、或在静(主要是拉应力)和腐蚀的共同作用下产生的失效现象。
它常出现于用钢、黄铜、高强度铝合金和中,凝汽器管、矿山用钢索、飞机紧急刹车用高压气瓶内壁等所产生的应力腐蚀也很显着。
常见应力腐蚀的机理是:零件或构件在应力和腐蚀介质作用下,表面的氧化膜被腐蚀而受到破坏,破坏的表面和未破坏的表面分别形成阳极和阴极,阳极处的金属成为离子而被溶解,产生电流流向阴极。
由于阳极面积比阴极的小得多,阳极的电流密度很大,进一步腐蚀已破坏的表面。
加上拉应力的作用,破坏处逐渐形成裂纹,裂纹随时间逐渐扩展直到断裂。
这种裂纹不仅可以沿着金属晶粒边界发展,而且还能穿过晶粒发展。
应力腐蚀过程试验研究表明:当金属加上阳极电流时可以加剧应力腐蚀,而加上阴极电流时则能停止应力腐蚀。
一般认为压应力对应力腐蚀的影响不大。
应力腐蚀的机理仍处于进一步研究中。
为防止零件的应力腐蚀,首先应合理选材,避免使用对应力腐蚀敏感的材料,可以采用抗应力腐蚀开裂的不锈钢系列,如高镍奥氏体钢、高纯奥氏体钢、超纯高铬铁素体钢等。
其次应合理设计零件和构件,减少。
改善腐蚀环境,如在腐蚀介质中添加缓蚀剂,也是防止应力腐蚀的措施。
采用金属或非金属保护层,可以隔绝腐蚀介质的作用。
此外,采用阴极保护法见也可减小或停止应力腐蚀。
本篇文章将重点介绍应力腐蚀断裂失效机理与案例研究,并分析比较应力腐蚀断裂其他环境作用条件下发生失效的特征。
,由于应力腐蚀的测试方法与本文中重点分析之处结合联系不大,故不再本文中加以介绍。
二.应力腐蚀开裂特征(1)引起应力腐蚀开裂的往往是拉应力。
这种拉应力的来源可以是:1.工作状态下构件所承受的外加载荷形成的抗应力。
2.加工,制造,热处理引起的内应力。
3.装配,安装形成的内应力。
4.温差引起的热应力。
5.裂纹内因腐蚀产物的体积效应造成的楔入作用也能产生裂纹扩展所需要的应力。
压力容器的破裂形式有哪些

压力容器的破裂形式有哪些压力容器及其承压部件在使用过程中,其尺寸、形状或材料性能发生改变,完全失去或不能良好实现原定功能,继续使用会失去可靠性和安全性,需要立即停用修复或更换,这种情况称作压力容器及其承压部件的失效。
压力容器最常见的失效形式是破裂失效,有韧性破裂、脆性破裂、疲劳破裂、腐蚀破裂、蠕变破裂5种类型。
1.韧性破裂韧性破裂又称延性破裂,是指容器壳体承受过高的内部应力,以致超过或远远超过其屈服极限和强度极限,使壳体产生较大的塑性变形,最终导致破裂。
容器发生韧性破裂时,爆破压力一般超过容器剩余壁厚计算出的爆破压力。
如化学反应过载破裂,一般产生粉碎性爆炸;物理性超载破裂,多从容器强度薄弱部分突破,一般无碎片抛出。
韧性破裂的特征主要表现在断口有缩颈,其断面与主应力方向成45°角,有较大剪切唇,断面多呈暗灰色纤维状。
当严重超载时,爆炸能量大、速度快,金属来不及变形,易产生快速撕裂现象,出现正压力断口。
压力容器发生韧性破裂的主要原因是容器过压。
2.脆性破裂脆性破裂是指容器在断裂时没有宏观的塑性变形,器壁平均应力远没有达到材料的强度极限,有的甚至低于屈服极限,其断裂现象和脆性材料的破坏很相似,常发生在截面不生明显塑性变形就破坏的破裂形式称为脆性破裂。
连续处,并伴有表面缺陷或内部缺陷,即常发生在严重的应力集中处。
因此,把容器未发化工压力容器常发生低应力脆断,主要原因是热学环境、载荷作用和容器本身结构缺陷所致、所处理的介质易造成容器应力腐蚀、晶间腐蚀、氢损伤、高温腐蚀、热疲劳、腐蚀疲劳、机械疲劳等,使焊缝和母材原发缺陷易于扩展开裂,或在应力集中区易产生新的裂纹并扩展开裂,使容器承受的应力低于设计应力而破坏。
3.疲劳破裂疲劳破裂是指压力容器由于受到反复作用的交变应力(如反复加压、泄压)的作用,使容器壳体材料的某些应力集中部位在短时间由于疲劳而在低应力状态下突然发生的破裂形式。
与脆性破裂一样,发生疲劳破裂时,容器外观没有明显的塑性变形,而且也是突发性的。
压力管道开裂腐蚀
压力管道开裂腐蚀摘要:压力管道开裂腐蚀是压力管道的主要损伤模式,处在开裂腐蚀环境中压力管道危险性很大,本文对压力管道开裂腐蚀机理进行了归纳总结,提出了压力管道检验和安全使用的关键控制点。
关键词:压力管道开裂腐蚀敏感性材质腐蚀性介质拉应力随着我国经济的快速发展,石化企业数量众多,成为国民经济的重要基础,压力管道是石化企业重要设备,数量大,类别多,在使用中事故频发,其安全状况直接关系到安全生产和经济效益,已成为影响人民生命财产的严重隐患。
压力管道腐蚀是引起压力管道事故的主要原因,在压力管道腐蚀中,开裂腐蚀隐患大,后果严重,在正常检测中不易发现,隐蔽性强。
开裂腐蚀主要包括:氯化物应力腐蚀开裂、碳酸盐应力腐蚀开裂、硝酸盐应力腐蚀开裂、碱应力腐蚀开裂、氨应力腐蚀开裂、湿硫化氢破坏、氢脆。
开裂腐蚀是敏感性材质在拉应力和相应腐蚀性介质作用下产生的使材质开裂的一种腐蚀。
开裂腐蚀的发生必须同时具备三个条件:敏感性材质、相应介质、拉应力。
一旦条件具备,开裂腐蚀就发生,速度快,不易控制,不易察觉。
有效控制开裂腐蚀发生条件,是保证压力管道安全的重要基础。
奥氏体不锈钢及镍基合金钢、碳钢、低合金钢、高强度钢在压力管道中使用普遍,对相应介质来说都是开裂腐蚀的敏感性材质;氯化物、碳酸盐、硝酸盐、碱、氨、湿硫化氢、氢是相应的腐蚀性介质;压力管道承受的内压力较高,特别是压力管道现场焊接时,绝大多数未进行消除应力的热处理,在焊接部位存在更高的拉应力集中。
这就造成许多使用的压力管道处在开裂腐蚀环境中。
具体腐蚀机理如下:1 氯化物应力腐蚀开裂奥氏体不锈钢及镍基合金在拉应力和氯化物溶液的作用下,氯离子易吸附在金属表面的钝化膜上,取代氧原子后和钝化膜中的阳离子结合形成可溶性氯化物,导致钝化膜破坏。
破坏部位的新鲜金属遭腐蚀形成一个小坑,小坑表面的钝化膜继续遭氯离子破坏生成氯化物。
在坑里氯化物水解,使小坑内PH值下降,局部溶液呈酸性,对金属进行腐蚀,造成多余的金属离子,为平衡蚀坑内的电中性,外部的氯离子不断向坑内迁移,使坑内氯离子浓度升高,水解加剧,加快金属的腐蚀。
承压设备损伤之应力腐蚀开裂
承压设备损伤之应力腐蚀开裂承压设备损伤之应力腐蚀开裂1.3 应力腐蚀开裂(SCC)应力腐蚀开裂是指承受应力的合金在腐蚀性环境中由于裂纹的扩展而互生失效的一种通用术语。
发生应力腐蚀开裂的必要条件是要有拉应力(不论是残余应力还是外加应力,或者两者兼而有之)和特定的腐蚀介质存在。
裂纹的形成和扩展大致与拉应力方向垂直。
这个导致应力腐蚀开裂的应力值,要比没有腐蚀介质存在时材料断裂所需要的应力值小得多。
《承压设备损伤模式识别》、《容器定检规》中称为“环境开裂”(共列出13种):氯化物应力腐蚀开裂、碳酸盐、硝酸盐、碱、氨、胺、湿硫化氢破坏(氢鼓包、氢致开裂、应力导向型氢致开裂、硫化物应力腐蚀开裂)、氢氟酸致氢应力开裂、氢氰酸致氢应力开裂、氢脆、高温水、连多硫酸、液体金属脆断等等。
>>裂纹特征应力腐蚀的宏观裂纹均起自于表面且分布具有明显的局部性;裂纹的走向与所受应力,特别是与残余应力有密切关系;裂纹常呈龟裂和风干木材状,裂纹附近未见塑性变形;除裂纹部位外,其它部位腐蚀轻微,且常有金属光泽。
>>在微观上,穿过晶粒的裂纹称为穿晶裂纹,而沿晶界扩展的裂纹称为沿晶裂纹。
应力腐蚀裂纹的微观形貌多为穿晶型,但也多见沿晶型和穿晶+沿晶混合型;裂纹的宽度较小,而扩展较深,裂纹的纵深常较其宽度大几个数量级;>>裂纹既有主干也有分支,典型裂纹多貌似落叶后的树干和树枝,裂纹尖端较锐利。
典型的应力腐蚀开裂裂纹及其微观形貌沿晶裂纹穿晶裂纹>>断口形貌应力腐蚀的宏观断口多呈脆性断裂。
断口的微观形貌,穿晶型多为准解理断裂,并常见河流,扇形,鱼骨,羽毛等花样;而沿晶型则多为冰糖块状花样。
断口扫描电镜微观形貌-解理+微裂纹沿晶断口,晶间存在微裂纹1.3.1 氯化物应力腐蚀开裂奥氏体不锈钢及镍基合金在拉应力和氯化物溶液的作用下发生的表面开裂。
>>损伤机理氯离子易吸附在奥氏体不锈钢表面的钝化膜上,取代氧原子后和钝化膜中的阳离子结合形成可溶性氯化物,导致钝化膜破坏。
关注300系列不锈钢的氯化物应力腐蚀开裂
并得出一些结论。然而,在低氯浓度情况下,测试时间会 变得很长。 实验中必须观察到应力腐蚀开裂(由于不能证 明否定的假设,即应力腐蚀开裂不会发生),并且获得结 论非常低浓度的氯离子(如:小于 10 ppm)也会导致应力 腐蚀开裂。
表面膜和沉淀 在工业实践中,另外两个因素会使得临界浓度的问题复杂 化。其一是缝隙或蒸汽空间内氯化物(或其他腐蚀种类) 浓缩的可能性,因为在这些地方稀释液会蒸发和损耗。二 是表面膜能够吸收或阻挡氯化物,从而使其浓度会比其在 大体积的溶液中的浓度要高出几个量级。水中的碳酸钙沉 淀,蒸汽中的水合铝或氧化铁,冷凝物或水相/有机物的 混合物、有机或生物膜,都会在金属表面吸收并局部富集 氯物质,从而导致应力腐蚀开裂。0.02 ppm 的较低浓度水 平的溶液会在金属表面通过氧化铝膜被浓缩至 10000 ppm。
氯化物 氯,作为卤素的代表,是最常见的造成奥氏体不锈钢应力 腐蚀开裂的物质。报告表明在各种媒介中,比如自然水、 地热蒸汽、工业蒸汽冷凝物和碱性物等,都会发生应力腐 蚀开裂。在大多数情况下,除了碱(其自身也会造成应力 腐蚀开裂),其余的裂纹都可以归因于无机氯离子。
除了少数的一些敏感的金属结构(如晶界有的碳化铬析出 物)在特定环境下的情况外,氯化物应力腐蚀开裂表现为 多分支的穿晶裂纹。图1 的显微照片显示的是氯化物应力 腐蚀开裂的形如闪电的穿晶裂纹形态。
热壁效应
“热壁”的影响除了水中盐本身的沉积,也涉及到腐蚀机理方面。通常 观察到的水冷式热交换器就会在传热最大的地方发生应力腐蚀开裂,而 在同等条件下,简单浸泡的不锈钢部件没有观察到开裂现象。
硫化物-氯化物开裂 硫化氢(或来源于其他方面的硫化物)和氯化物的同时存 在会协同影响 18-8 不锈钢。304 不锈钢在硫化氢溶液中去 (其中氯化物含量低至 2-8 ppm),在室温下可观察到穿 晶应力腐蚀开裂现象。显然,相较于氧,硫化氢在膜形成 过程中有特殊作用。
氯化物会导致点蚀和应力腐原理
氯化物会导致点蚀和应力腐原理氯化物在工程材料中的应用广泛,但同时也存在一些潜在风险,其中包括点蚀和应力腐蚀。
本文将以氯化物导致点蚀和应力腐蚀为主题,从原理、影响因素、预防措施等方面进行详细讨论。
一、点蚀的原理点蚀是指金属表面局部区域产生的小孔洞或凹坑。
氯化物是导致点蚀的主要因素之一。
其作用机理主要包括两个方面:一是氯化物的存在导致金属表面的局部腐蚀,形成小孔洞;二是氯化物通过极化效应,降低了金属的极化能力,使得金属更易腐蚀。
二、应力腐蚀的原理应力腐蚀是指金属在受到外界应力作用下,在特定介质中发生的腐蚀现象。
氯化物也是导致应力腐蚀的重要因素之一。
其作用机理主要包括三个方面:一是氯化物在介质中能够增加金属的应力集中程度,使得金属表面出现微小的应力集中区域;二是氯化物作为电解质,加速了金属的电化学反应速度,使得腐蚀更为迅速;三是氯化物可以影响金属的裂纹扩展行为,导致金属在应力作用下更易发生断裂。
三、影响因素氯化物导致点蚀和应力腐蚀的影响因素主要包括:氯化物浓度、温度、氯化物类型、金属材料和应力状态等。
1.氯化物浓度:氯化物的浓度越高,对金属的腐蚀作用越大。
2.温度:温度越高,金属和氯化物之间的反应速率越快,导致腐蚀加剧。
3.氯化物类型:不同类型的氯化物对金属的腐蚀效果有所不同,如氯化铵和氯化钙的腐蚀作用较大。
4.金属材料:不同金属对氯化物的腐蚀抵抗能力不同,某些金属对氯化物的腐蚀更为敏感。
5.应力状态:应力作用下,金属的腐蚀形式和速率有所变化,更易发生应力腐蚀。
四、预防措施为了避免氯化物导致的点蚀和应力腐蚀,工程实践中可以采取以下预防措施:1.选择适当的材料:选择抗氯化物腐蚀性能较好的金属材料,如不锈钢、高合金钢等。
2.提高金属表面的耐氯化物能力:通过表面处理技术,如防腐涂层、阳极处理等,提高金属表面对氯化物的耐蚀性能。
3.合理设计和施工:在工程设计和施工过程中,考虑到氯化物的影响,采取合理的措施,如增加材料厚度、减少应力集中等。
- 1、下载文档前请自行甄别文档内容的完整性,平台不提供额外的编辑、内容补充、找答案等附加服务。
- 2、"仅部分预览"的文档,不可在线预览部分如存在完整性等问题,可反馈申请退款(可完整预览的文档不适用该条件!)。
- 3、如文档侵犯您的权益,请联系客服反馈,我们会尽快为您处理(人工客服工作时间:9:00-18:30)。
关于氯脆问题
金属的氯化物应力腐蚀破裂又称氯脆,是指金属在腐蚀介质Cl-和应力(残余应力、热应力、工作应力等)共同作用下,产生的脆断现象。
铝合金、高强度低合金钢、不锈钢、马氏体时效钢以及钛合金,在一定条件下都会发生氯脆。
其中,不锈钢的氯脆现象是比较常见的。
下面以不锈钢的氯脆为例来解释说明氯脆原理。
多数情况下,氯脆是以点蚀或缝隙腐蚀为起点的。
不锈钢具有优良的机械性能和良好的耐腐蚀性能,Cr和Ni是不锈钢获得耐腐蚀性能最主要的合金元素,其在不锈钢表面生成一层十分致密、光亮的氧化物保护膜,大大提高了不锈钢的耐腐蚀性能。
氯离子(Cl-)半径小、穿透能力强,能够穿透这层氧化物保护膜,并且由于Cl-有很强的可被金属吸附的能力,它们会从金属表面把氧化物中的氧排挤掉,自身取代氧与金属形成氯化物。
但氯化物与金属表面的吸附不稳定,于是形成了可溶性物质,破坏了氧化保护膜,形成坑点或缝隙,成为氯脆发生的起点。
在应力作用下,金属内部稳定的组织受到破坏,导致晶粒在应力方向的作用下位错而形成滑移台阶,这些滑移台阶的构成给Cl- 带来了吸附和渗透的机会。
Cl-在坑点或缝隙处聚集,在应力造成的晶格破坏协助下,渗入到金属基体,通过电化学的阳极过程形成穿晶腐蚀或晶间腐蚀,阴极则由氢离子(酸性溶液)或溶解氧(中性水溶液)担任。
阳极:M →M+ + e
阴极:H+ + e →H (酸性)
H2O + 1/2O2 + 2e →2OH-(中性)
通过上述腐蚀萌生点的形成、应力作用、阳极腐蚀过程的进行,金属晶格被破坏,形成腐蚀破裂现象,即氯化物应力腐蚀破裂。
氯脆的腐蚀裂纹萌生处为坑点或缝隙,通常较宽,而延伸多呈穿晶、沿晶或二者的混合形式,故整体且呈树枝状。
青岛清达环保总工韩泰清高工(国家化学清洗标准HG/T2387-92《工业设备化学清洗质量标准》的起草人和起草组负责人,具有40多年的防腐清洗和工业水处理实践经验)1975年发表的文章《奥氏体不锈钢换热器的氯化物应力腐蚀破裂》中提出,发生氯化物应力腐蚀破裂的极限氯离子浓度是相当低的。
即使在氯离子含量很低的水中,由于有局部沸腾(如热
水锅炉、热交换器等设备)而引起氯离子浓缩,如果温度适当,再有溶解氧和一定应力的共同作用,就易发生腐蚀破裂。
另外,在高温水中,有氯离子存在的条件下,溶解氧对应力腐蚀破裂起决定作用。
清达环保韩泰清高工1975年做的氯化物应力腐蚀破裂实验图片
清达环保韩泰清高工1975年做的氯化物应力腐蚀破裂实验图片。