半导体制造工艺课件(47页)
合集下载
半导体制造工艺过程培训课件.pptx
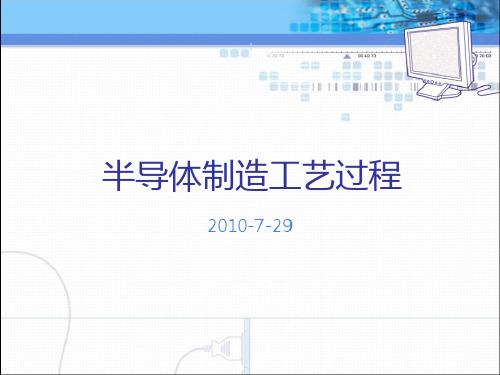
光刻与刻蚀
• 干法刻蚀:利用等离子体将不要的材料去除(亚微 米尺寸下刻蚀器件的最主要方法)。
• 干法刻蚀种类很多,如光挥发、气相腐蚀、等离子 体腐蚀等。
• 其优点是:各向异性好,选择比高,可控性、灵活 性、重复性好,细线条操作安全,易实现自动化, 无化学废液,处理过程未引入污染,洁净度高。
• 缺点是:成本高,设备复杂。干法刻蚀主要形式有 纯化学过程(如屏蔽式,下游式,桶式),纯物理 过程(如离子铣),物理化学过程,常用的有反应 离子刻蚀RIE,离子束辅助自由基刻蚀ICP。
薄膜沉积
• 化学气象沉积指利用化学反应的方式在反应室内将 反应物(通常为气体)生成固态的生成物,并沉积 在硅片表面的一种薄膜沉积技术。
• 气相淀积具有很好的台阶覆盖特性 • APCVD = Atmospheric Pressure CVD,常压CVD • LPCVD = Low Pressure CVD,低压CVD • PECVD = Plasma Enhanced CVD,等离子体CVD • HDPCVD = High-Density CVD,高密度CVD
晶体生长与圆晶制造晶体生长与圆晶制造 Nhomakorabea 热氧化
• SiO2的基本特性
• 杂质阻挡特性好 • 硅和SiO2的腐蚀选择特性好
热氧化
• 反应方程:
• Si(固体)+O2(气体)SiO2 • Si(固体)+2H2O (气体)SiO2 +H2(气体)
热氧化
• 硅热氧化工艺,可分为:干氧氧化、水汽氧化和湿氧氧化。 干氧氧化是以干燥纯净的氧气作为氧化气氛,在高温下氧直 接与硅反应生成二氧化硅。水汽氧化是以高纯水蒸汽为氧化 气氛,由硅片表面的硅原子和水分子反应生成二氧化硅。水 汽氧化的氧化速率比干氧氧化的为大。而湿氧氧化实质上是 干氧氧化和水汽氧化的混合,氧化速率介于二者之间。
第三章半导体制造工艺简介ppt课件
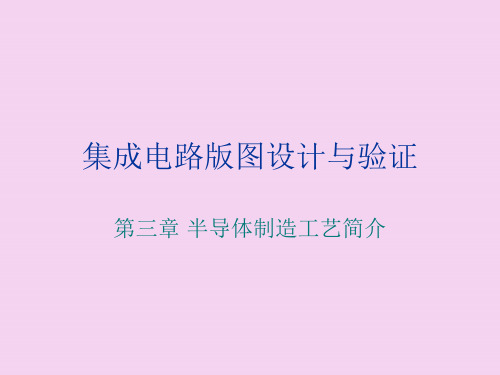
8 常用工艺之五:薄膜制备
❖ 四种薄膜:氧化膜;电介质膜;多晶硅膜; 金属膜
8 常用工艺之五:薄膜制备
❖ (1〕氧化 ❖ SiO2的作用 ❖ 屏蔽杂质、栅氧化层、介质隔离、器件保护和表面
钝化 ❖ SiO2的制备 ❖ 需要高纯度,目前最常用的方法是热氧化法。主要
分为干氧氧化、水汽氧化和湿氧氧化三种。 ❖ 氮化硅的制备 ❖ 主要用作:金属上下层的绝缘层、场氧的屏蔽层、
主要内容
❖ 3.1半导体基础知识 ❖ 3.2 工艺流程 ❖ 3.3 工艺集成
3.2 工艺流程
❖ 1 制造工艺简介 ❖ 2 材料的作用 ❖ 3 工艺流程 ❖ 4 常用工艺之一:外延生长 ❖ 5 常用工艺之二:光刻 ❖ 6 常用工艺之三:刻蚀 ❖ 7 常用工艺之四:掺杂 ❖ 8 常用工艺之五:薄膜制备
扩散和离子注入的对比
离子注入
注入损伤
❖ 注入损伤:带有能量的离子进入半导体衬底, 经过碰撞和损失能量,最后停留下来。
❖ 电子碰撞:电子激发或新的电子空穴对产生 ❖ 原子核碰撞:使原子碰撞,离开晶格,形成
损伤,也称晶格无序
晶格无序
退火
❖ 由于离子注入所造成的损伤区及无序团,使 迁移率和寿命等半导体参数受到严重影响。
❖ 每层版图都有相对应的掩膜版,并对应于不 同的工艺。
4 常用工艺之一:外延生长
❖ 半导体器件通常不是直接做在衬底上的, 而是先在沉底上生长一层外延层,然后将 器件做在外延层上。外延层可以与沉底同 一种材料,也可以不同。
❖ 在双极型集成电路中:可以解决原件间的 隔离;减小集电极串联电阻。
❖ 在CMOS集成电路中:可以有效避免闩锁 效应。
度取决于温度。
3.1半导体基础知识
❖ 关于扩散电阻: ❖ 集成电路中经常见到的扩散电阻其实就是利
半导体工艺 ppt课件
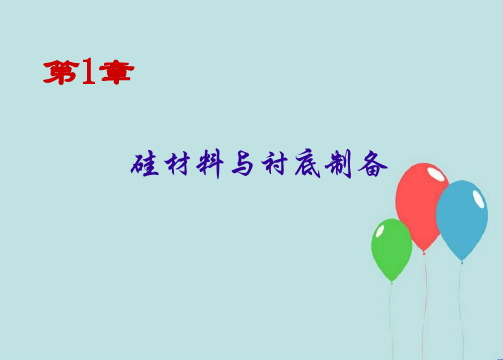
半导体器件以 半导体材料为 基本原材料
绝缘体 >109
铝、铜、金 硅、锗、砷化镓 陶瓷、二氧化硅
2. 半导体材料按组分划分
容易形成SiO2 ; Eg大→高温器件; 元素半导体(如:硅Si和锗Ge) 成本低。
化合物半导体(如:砷化镓GaAs 、磷化铟InP)
2018年11月2日 24
二. 半导体材料的基本特性
2018年11月2日
•8
在纯金属不能满足一些重要的电学参数、达不到可靠度 的情况下,IC金属化工艺中采用合金。
硅铝、铝铜、铝硅铜等合金已用于减小峰值、增大电子 迁移率、增强扩散屏蔽,改进附着特性等。或用于形成 特定的肖特基势垒。例如,稍微在Al中多加1wt%的Si 即可使Al导线上的缺陷减至最少,而在Al中加入少量 Cu,则可使电子迁移率提高101000倍; 通过金属之间或与Si的互相掺杂可以增强热稳定性
2018年11月2日 •20
材料系统
材料系统指的是在由一些基本材料,如Si, GaAs或InP制成的衬底上或衬底内,用其 它物质再生成一层或几层材料。 材料系统与掺杂过的材料之间的区别 : 在掺杂材料中, 掺杂原子很少
在材料系统中,外来原子的比率较高
2018年11月2日 •21
半导体材料系统
磷化铟 (InP)
能工作在超高速超高频
三种有源器件: MESFET、HEMT和HBT
广泛应用于光纤通信系统中
2018年11月2日
•18
硅 (Si)
①储量丰富,便宜,占地壳重量25%以上,
SiO2性质很稳定、良好介质,易于热氧化生长;
较大的禁带宽度(1.12eV),较宽工作温度范围;
绝缘体 >109
铝、铜、金 硅、锗、砷化镓 陶瓷、二氧化硅
2. 半导体材料按组分划分
容易形成SiO2 ; Eg大→高温器件; 元素半导体(如:硅Si和锗Ge) 成本低。
化合物半导体(如:砷化镓GaAs 、磷化铟InP)
2018年11月2日 24
二. 半导体材料的基本特性
2018年11月2日
•8
在纯金属不能满足一些重要的电学参数、达不到可靠度 的情况下,IC金属化工艺中采用合金。
硅铝、铝铜、铝硅铜等合金已用于减小峰值、增大电子 迁移率、增强扩散屏蔽,改进附着特性等。或用于形成 特定的肖特基势垒。例如,稍微在Al中多加1wt%的Si 即可使Al导线上的缺陷减至最少,而在Al中加入少量 Cu,则可使电子迁移率提高101000倍; 通过金属之间或与Si的互相掺杂可以增强热稳定性
2018年11月2日 •20
材料系统
材料系统指的是在由一些基本材料,如Si, GaAs或InP制成的衬底上或衬底内,用其 它物质再生成一层或几层材料。 材料系统与掺杂过的材料之间的区别 : 在掺杂材料中, 掺杂原子很少
在材料系统中,外来原子的比率较高
2018年11月2日 •21
半导体材料系统
磷化铟 (InP)
能工作在超高速超高频
三种有源器件: MESFET、HEMT和HBT
广泛应用于光纤通信系统中
2018年11月2日
•18
硅 (Si)
①储量丰富,便宜,占地壳重量25%以上,
SiO2性质很稳定、良好介质,易于热氧化生长;
较大的禁带宽度(1.12eV),较宽工作温度范围;
半导体制造工艺培训课程(56页)

图1-9 PN结电容结构
13
1.2 基本半导体元器件结构
图1-10 MOS场效应晶体管电容结构
14
1.2 基本半导体元器件结构
1.2.2 有源器件结构 有源器件,如二极管和晶体管与无源元件在电子控制方式上
有很大差别,可以用于控制电流方向,放大小的信号,构成复杂的 电路。这些器件与电源相连时需要确定电极(+或-)。工作时利用 了电子和空穴的流动。 1.二极管的结构
4. CMOS结构
图1-15 CMOS反相器电路的电路图、顶视图和剖面图
19
1.3 半导体器件工艺的发展历史
图1-16 生长型晶体管生长示意图
20
1.3 半导体器件工艺的发展历史
图1-17 合金结结型晶体管示意图
21
1.3 半导体器件工艺的发展历史
图1-18 台面型结型晶体管示意图
22
1.3 半导体器件工艺的发展历史
50
1.8 芯片制造的生产环境
1.8.1 净化间沾污类型 净化间沾污类型可以分为5大类:颗粒、金属杂质、有机物沾污、
自然氧化层和静电释放。 1.颗粒
图1-30 颗粒引起的缺陷
51
1.8 芯片制造的生产环境
2.金属杂质 3.有机物沾污 4.自然氧化层 5.静电释放 1.8.2 污染源与控制
应严格控制硅片加工生产厂房里的各种沾污,以减小对芯片的 危害。作为硅片生产厂房的净化间其主要污染源有这几种:空气、 人、厂房、水、工艺用化学品、工艺气体和生产设备。 1.空气
30
1.4 集成电路制造阶段
表1-2 1μm以下产业的技术节点列表
(2)提高芯片的可靠性 芯片的可靠性主要指芯片寿命。 (3)降低芯片的成本 半导体芯片的价格一直持续下降。
13
1.2 基本半导体元器件结构
图1-10 MOS场效应晶体管电容结构
14
1.2 基本半导体元器件结构
1.2.2 有源器件结构 有源器件,如二极管和晶体管与无源元件在电子控制方式上
有很大差别,可以用于控制电流方向,放大小的信号,构成复杂的 电路。这些器件与电源相连时需要确定电极(+或-)。工作时利用 了电子和空穴的流动。 1.二极管的结构
4. CMOS结构
图1-15 CMOS反相器电路的电路图、顶视图和剖面图
19
1.3 半导体器件工艺的发展历史
图1-16 生长型晶体管生长示意图
20
1.3 半导体器件工艺的发展历史
图1-17 合金结结型晶体管示意图
21
1.3 半导体器件工艺的发展历史
图1-18 台面型结型晶体管示意图
22
1.3 半导体器件工艺的发展历史
50
1.8 芯片制造的生产环境
1.8.1 净化间沾污类型 净化间沾污类型可以分为5大类:颗粒、金属杂质、有机物沾污、
自然氧化层和静电释放。 1.颗粒
图1-30 颗粒引起的缺陷
51
1.8 芯片制造的生产环境
2.金属杂质 3.有机物沾污 4.自然氧化层 5.静电释放 1.8.2 污染源与控制
应严格控制硅片加工生产厂房里的各种沾污,以减小对芯片的 危害。作为硅片生产厂房的净化间其主要污染源有这几种:空气、 人、厂房、水、工艺用化学品、工艺气体和生产设备。 1.空气
30
1.4 集成电路制造阶段
表1-2 1μm以下产业的技术节点列表
(2)提高芯片的可靠性 芯片的可靠性主要指芯片寿命。 (3)降低芯片的成本 半导体芯片的价格一直持续下降。
半导体工艺流程简介ppt

半导体工艺流程的成就与挑战
进一步缩小特征尺寸
三维集成技术
绿色制造技术
智能制造技术
未来半导体工艺流程的发展趋势
01
02
03
04
THANKS
感谢观看
互连
通过金属化过程,将半导体芯片上的电路元件连接起来,实现芯片间的通信和电源分配功能。
半导体金属化与互连
将半导体芯片和相关的电子元件、电路板等封装在一个保护壳内,以防止外界环境对芯片的损伤和干扰。
封装
对封装好的半导体进行功能和性能的检测与试验,以确保其符合设计要求和实际应用需要。
测试
半导体封装与测试
半导体工艺流程概述
02
半导体制造步骤-1
1
半导体材料的选择与准备
2
3
通常使用元素半导体,如硅(Si)、锗(Ge)等,或化合物半导体,如砷化镓(GaAs)、磷化铟(InP)等。
材料类型
高纯度材料对于半导体制造至关重要,杂质含量需要严格控制。
纯净度要求
材料应具有立方、六方或其他特定晶体结构。
晶格结构
蚀刻
使用化学试剂或物理方法,将半导体基板表面未被光刻胶保护的部分进行腐蚀去除。根据蚀刻方法的不同,可以分为湿蚀刻和干蚀刻两种。
去胶
在完成蚀刻后,使用去胶液等化学试剂,去除光刻胶。去胶过程中需要注意控制温度和时间,以避免对半导体基板造成损伤或污染。
半导体的蚀刻与去胶
05
半导体制造步骤-4
金属化
通常使用铝或铜作为主要材料,通过溅射、蒸发或电镀等手段,在半导体表面形成导线图案。
涂布
在半导体基板上涂覆光刻胶,使其覆盖整个基板表面。通常使用旋转涂布法,将光刻胶滴在基板中心,然后通过旋转基板将其展开并涂布在整个表面上。
半导体制造工艺流程课件

04
半导体制造的后处理
金属化
01
02
03
金属化
在半导体制造的后处理中 ,金属化是一个关键步骤 ,用于在芯片上形成导电 电路。
金属材料
通常使用铜、铝、金等金 属作为导电材料,通过物 理或化学沉积方法将金属 薄膜沉积在芯片表面。
连接电路
金属化过程将芯片上的不 同元件连接成完整的电路 ,实现电子信号的传输和 处理。
高纯度材料
半导体制造需要使用高纯度材料,以确保芯片的性能和可 靠性。然而,高纯度材料的制备和加工难度较大,需要克 服许多技术难题。
制程控制
半导体制造过程中,制程控制是至关重要的。制程控制涉 及温度、压力、流量、电流、电压等众多参数,需要精确 控制这些参数以确保芯片的性能和可靠性。
环境影响
能源消耗
半导体制造是一个高能耗的过程 ,需要大量的电力和能源。随着 半导体产业的发展,能源消耗也 在不断增加,对环境造成了很大 的压力。
废弃物处理
半导体制造过程中会产生大量的 废弃物,如化学废液、废气等。 这些废弃物如果处理不当,会对 环境造成很大的污染和危害。
碳排放
半导体制造过程中的碳排放也是 一个重要的问题。减少碳排放是 半导体产业可持续发展的关键之 一。
未来发展趋势
先进封装技术
随着摩尔定律的逐渐失效,先进封装技术成为半导体制造的重要发展方向。通过将多个 芯片集成在一个封装内,可以实现更小、更快、更低功耗的芯片系统。
沉积薄膜质量
影响沉积薄膜质量的因素包括反应温度、气体流量、压强等,需通 过实验优化获得最佳工艺参数。
外延生长
外延生长目的
在半导体材料表面外延生长一层单晶层,用 于扩展器件尺寸、改善材料性能和提高集成 度。
最新半导体制造工艺第1章绪论课件PPT
图1-9 PN结电容结构
1.2 基本半导体元器件结构
图1-10 MOS场效应晶体管电容结构
1.2 基本半导体元器件结构
1.2.2 有源器件结构 有源器件,如二极管和晶体管与无源元件在电子控制方式上
有很大差别,可以用于控制电流方向,放大小的信号,构成复杂的 电路。这些器件与电源相连时需要确定电极(+或-)。工作时利用 了电子和空穴的流动。 1.二极管的结构
图1-21 半导体芯片制造的关键工艺
1.4 集成电路制造阶段
(3)掩膜版制作 掩膜版中包括构成芯片的各层图形结构,现在最常 用的掩膜版技术是石英玻璃涂敷铬,在石英玻璃掩膜版表面的铬层 上形成芯片各层结构图形。 (4)装配与封装 芯片制造完成后,封装之前芯片要经过测试/拣选进 行单个芯片的电学测试,拣选出合格芯片和不合格芯片,并作出标 识,合格芯片包装在保护壳体内。 (5)终测 为了确保芯片的功能,要对每个被封装的集成电路进行测 试,以保证芯片的电学和环境特性参数满足要求,即保证发给用户 的芯片是合格芯片。
1.2 基本半导体元器件结构
图1-5 利用基区、发射区扩散形成电阻的结构
1.2 基本半导体元器件结构
图1-6 外延层电阻结构
1.2 基本半导体元器件结构
图1-7 MOS集成电路中的多晶硅电阻
1.2 基本半导体元器件结构
2.集成电路பைடு நூலகம்容结构
图1-8 集成电路中电容的结构
1.2 基本半导体元器件结构
图1-15 CMOS反相器电路的电路图、顶视图和剖面图
1.3 半导体器件工艺的发展历史
图1-16 生长型晶体管生长示意图
1.3 半导体器件工艺的发展历史
图1-17 合金结结型晶体管示意图
1.2 基本半导体元器件结构
图1-10 MOS场效应晶体管电容结构
1.2 基本半导体元器件结构
1.2.2 有源器件结构 有源器件,如二极管和晶体管与无源元件在电子控制方式上
有很大差别,可以用于控制电流方向,放大小的信号,构成复杂的 电路。这些器件与电源相连时需要确定电极(+或-)。工作时利用 了电子和空穴的流动。 1.二极管的结构
图1-21 半导体芯片制造的关键工艺
1.4 集成电路制造阶段
(3)掩膜版制作 掩膜版中包括构成芯片的各层图形结构,现在最常 用的掩膜版技术是石英玻璃涂敷铬,在石英玻璃掩膜版表面的铬层 上形成芯片各层结构图形。 (4)装配与封装 芯片制造完成后,封装之前芯片要经过测试/拣选进 行单个芯片的电学测试,拣选出合格芯片和不合格芯片,并作出标 识,合格芯片包装在保护壳体内。 (5)终测 为了确保芯片的功能,要对每个被封装的集成电路进行测 试,以保证芯片的电学和环境特性参数满足要求,即保证发给用户 的芯片是合格芯片。
1.2 基本半导体元器件结构
图1-5 利用基区、发射区扩散形成电阻的结构
1.2 基本半导体元器件结构
图1-6 外延层电阻结构
1.2 基本半导体元器件结构
图1-7 MOS集成电路中的多晶硅电阻
1.2 基本半导体元器件结构
2.集成电路பைடு நூலகம்容结构
图1-8 集成电路中电容的结构
1.2 基本半导体元器件结构
图1-15 CMOS反相器电路的电路图、顶视图和剖面图
1.3 半导体器件工艺的发展历史
图1-16 生长型晶体管生长示意图
1.3 半导体器件工艺的发展历史
图1-17 合金结结型晶体管示意图
半导体制造工艺技术PPT(共68页)
Si2H6(气态) (反应半
3) Si2H6(气态) 品形成)
2Si (固态) + 3H2(气态) (最终产
以上实例是硅气相外延的一个反应过程
• 速度限制阶段
在实际大批量生产中,CVD反应的时间长 短很重要。温度升高会促使表面反应速度增加 。基于CVD反应的有序性,最慢的反应阶段会 成为整个工艺的瓶颈。换言之,反应速度最慢 的阶段将决定整个淀积过程的速度。
种新的化合物。
以上5中基本反应中,有一些特定的 化学气相淀积反应用来在硅片衬底上淀 积膜。对于某种特定反应的选择通常要 考虑淀积温度、膜的特性以及加工中的 问题等因素。
例如,用硅烷和氧气通过氧化反应 淀积SiO2膜。反应生成物SiO2淀积在硅 片表面,副产物事是氢。
SiH4 + O2
SiO2 + 2H2
• CVD 过程中的掺杂
CVD淀积过程中,在SiO2中掺入杂质对硅 片加工来说也是很重要。例如,在淀积SiO2的 过程中,反应气体中加入PH3后,会形成磷硅 玻璃。化学反应方程如下:
SiH4(气)+2PH3(气)+O2(气) SiO2(固)+2P(固)+5H2(气)
在磷硅玻璃中,磷以P2O5的形式存在,磷 硅玻璃由P2O5和SiO2的混合物共同组成;对于 要永久黏附在硅片表面的磷硅玻璃来说, P2O5 含量(重量比)不超过4%,这是因为磷硅玻 璃(PSG)有吸潮作用。
CVD 反应
• CVD 反应步骤
基本的化学气相淀积反应包含8个主要步骤, 以解释反应的机制。 1)气体传输至淀积区域; 2)膜先驱物的形成; 3)膜先驱物附着在硅片表面; 4)膜先驱物黏附; 5)膜先驱物扩散; 6)表面反应; 7)副产物从表面移除; 8)副产物从反应腔移除。
半导体工艺技术PPT课件
半导体工艺技术
精选ppt课件最新
1
目录
第一章:半导体产业介绍 第二章:器件的制造步骤 第三章:晶圆制备 第四章:芯片制造 第五章:污染控制 第六章:工艺良品率
精选ppt课件最新
2
第一章 半导体产业介绍
概述
微电子从40年代末的第一只晶体管(Ge合金 管)问世,50年代中期出现了硅平面工艺,此工 艺不仅成为硅晶体管的基本制造工艺,也使得将 多个分立晶体管制造在同在一硅片上的集成电路 成为可能,随着制造工艺水平的不断成熟,使微 电子从单只晶体管发展到今天的ULSI。
精选ppt课件最新
11
第二章 器件的制造步骤
半导体器件制造分4个不同阶段: 1.材料准备 2.晶体生长与晶圆准备 3.芯片制造 4.封装
材料 准备
晶体生 长与晶 圆准备
晶圆 制造
精选ppt课件最新
封装
12
第一步 材料准备
第二步晶体生长与晶圆准备
精选ppt课件最新
13
第三步 芯片制造
制造
电性测试 (芯片分捡)
尺寸和数量是IC发展的两个共同目标。
芯片上的物理尺寸特征称为特征尺寸,将此定义 为制造复杂性水平的标准。
通常用微米来表示。一微米为1/10000厘米。
Gordon Moore在1964年预言IC的密度每隔18~24 个月将翻一番,------摩尔定律。
精选ppt课件最新
8
一个尺寸相同的芯片上,所容纳的晶体管数量, 因制程技术的提升,每18个月到两年晶体管数量会 加倍,IC性能也提升1倍。现以1961年至2006年 期间半导体技术的发展为例加以说明,IC电路线宽由 25微米减至65纳米,晶圆直径由1英寸增为12英寸, 每一芯片上由6个晶体管增为80亿个晶体管, DRAM密度增加为4G位,晶体管年销售量由1000 万个增加到10的18次方至19次方个,但晶体管平均 售价却大幅下降10的9次方倍。
精选ppt课件最新
1
目录
第一章:半导体产业介绍 第二章:器件的制造步骤 第三章:晶圆制备 第四章:芯片制造 第五章:污染控制 第六章:工艺良品率
精选ppt课件最新
2
第一章 半导体产业介绍
概述
微电子从40年代末的第一只晶体管(Ge合金 管)问世,50年代中期出现了硅平面工艺,此工 艺不仅成为硅晶体管的基本制造工艺,也使得将 多个分立晶体管制造在同在一硅片上的集成电路 成为可能,随着制造工艺水平的不断成熟,使微 电子从单只晶体管发展到今天的ULSI。
精选ppt课件最新
11
第二章 器件的制造步骤
半导体器件制造分4个不同阶段: 1.材料准备 2.晶体生长与晶圆准备 3.芯片制造 4.封装
材料 准备
晶体生 长与晶 圆准备
晶圆 制造
精选ppt课件最新
封装
12
第一步 材料准备
第二步晶体生长与晶圆准备
精选ppt课件最新
13
第三步 芯片制造
制造
电性测试 (芯片分捡)
尺寸和数量是IC发展的两个共同目标。
芯片上的物理尺寸特征称为特征尺寸,将此定义 为制造复杂性水平的标准。
通常用微米来表示。一微米为1/10000厘米。
Gordon Moore在1964年预言IC的密度每隔18~24 个月将翻一番,------摩尔定律。
精选ppt课件最新
8
一个尺寸相同的芯片上,所容纳的晶体管数量, 因制程技术的提升,每18个月到两年晶体管数量会 加倍,IC性能也提升1倍。现以1961年至2006年 期间半导体技术的发展为例加以说明,IC电路线宽由 25微米减至65纳米,晶圆直径由1英寸增为12英寸, 每一芯片上由6个晶体管增为80亿个晶体管, DRAM密度增加为4G位,晶体管年销售量由1000 万个增加到10的18次方至19次方个,但晶体管平均 售价却大幅下降10的9次方倍。
半导体制造工艺流程通用课件
半导体制造工艺流程通用课件
目录
• 半导体制造概述 • 半导体制造的前处理 • 半导体制造的核心工艺 • 半导体制造的后处理 • 半导体制造的挑战与解决方案 • 半导体制造的发展趋势与未来展望
01
半导体制造概述
半导体制造的定义
半导体制造
指通过一系列精密的物理和化学 工艺,将单晶硅或其他半导体材 料转化为集成电路的过程。
采用高k金属栅极材料, 可以提高芯片的性能和降 低功耗。
新型绝缘材料
采用新型绝缘材料,可以 提高芯片的集成度和可靠 性。
新型封装材料
采用新型封装材料,可以 提高芯片的散热性能和可 靠性。
系统集成与封装技术的发展
系统集成技术
通过系统集成技术,将多个芯片集成在一个封装 内,实现更高的性能和更小的体积。
封装类型
常见的封装类型包括塑料封装、陶瓷封装和金属封装等,它们具有不同的特点和适用范围 。
封装工艺
封装工艺涉及到多个环节,包括芯片贴装、引脚焊接、密封和标记等,每个环节都对保证 芯片的性能和可靠性至关重要。
测试与验证
测试与验证
在半导体制造的后处理过程中,测试与验证是确保芯片性能和质量 的重要环节。
化学气相沉积
总结词
化学气相沉积是通过化学反应在半导体表面形成薄膜的过程。
详细描述
化学气相沉积是在高温下,将气态物质在半导体表面进行化学反应,形成固态薄膜的过程。沉积的薄膜可以作为 绝缘层、导电层或保护层,对半导体器件的性能和稳定性具有重要影响。
04
半导体制造的后处理
金属化
金属化
在半导体制造的后处理过程中,金属化是关键的一步,它 涉及到在芯片表面沉积金属,以实现电路的导电连接。
半导体制造的工艺流程简介
目录
• 半导体制造概述 • 半导体制造的前处理 • 半导体制造的核心工艺 • 半导体制造的后处理 • 半导体制造的挑战与解决方案 • 半导体制造的发展趋势与未来展望
01
半导体制造概述
半导体制造的定义
半导体制造
指通过一系列精密的物理和化学 工艺,将单晶硅或其他半导体材 料转化为集成电路的过程。
采用高k金属栅极材料, 可以提高芯片的性能和降 低功耗。
新型绝缘材料
采用新型绝缘材料,可以 提高芯片的集成度和可靠 性。
新型封装材料
采用新型封装材料,可以 提高芯片的散热性能和可 靠性。
系统集成与封装技术的发展
系统集成技术
通过系统集成技术,将多个芯片集成在一个封装 内,实现更高的性能和更小的体积。
封装类型
常见的封装类型包括塑料封装、陶瓷封装和金属封装等,它们具有不同的特点和适用范围 。
封装工艺
封装工艺涉及到多个环节,包括芯片贴装、引脚焊接、密封和标记等,每个环节都对保证 芯片的性能和可靠性至关重要。
测试与验证
测试与验证
在半导体制造的后处理过程中,测试与验证是确保芯片性能和质量 的重要环节。
化学气相沉积
总结词
化学气相沉积是通过化学反应在半导体表面形成薄膜的过程。
详细描述
化学气相沉积是在高温下,将气态物质在半导体表面进行化学反应,形成固态薄膜的过程。沉积的薄膜可以作为 绝缘层、导电层或保护层,对半导体器件的性能和稳定性具有重要影响。
04
半导体制造的后处理
金属化
金属化
在半导体制造的后处理过程中,金属化是关键的一步,它 涉及到在芯片表面沉积金属,以实现电路的导电连接。
半导体制造的工艺流程简介
- 1、下载文档前请自行甄别文档内容的完整性,平台不提供额外的编辑、内容补充、找答案等附加服务。
- 2、"仅部分预览"的文档,不可在线预览部分如存在完整性等问题,可反馈申请退款(可完整预览的文档不适用该条件!)。
- 3、如文档侵犯您的权益,请联系客服反馈,我们会尽快为您处理(人工客服工作时间:9:00-18:30)。
2. 过腐蚀最小(一般要求过腐蚀10%,以保证整片刻蚀完全)
3. 选择性好 4. 均匀性和重复性好
两类刻蚀方法:
5. 表面损伤小 6. 清洁、经济、安全
➢湿法刻蚀——化学溶液中进行 反应腐蚀,选择性好
➢干法刻蚀——气相化学腐蚀 (选择性好)或物理腐蚀(方向 性好),或二者兼而有之
半导体制造工艺基础
另外,HDP等离子体源对衬底的损伤较小(因为衬底有独立的偏压源与 侧电极电势),并有高的的各向异性(因为在低压下工作但有高活性的 等离子体密度)。
然而,由于其复杂且成本较高,这些系统可能不会使用于非关键性的工 艺,如侧壁间隔与平坦化工艺。
半导体制造工艺基础
第五章 刻蚀原理
37
介电板
RF
等离子体
RF
半导体制造工艺基础
第五章 刻蚀原理
28
在CF4中加入少量H2, 可使CFx:F*的浓度比 增加。 从而使SiO2:Si 及Si3N4:Si的腐蚀速 率比增大
半导体制造工艺基础
第五章 刻蚀原理
29
增加F/C比(加氧气),可以增加刻蚀速率 减少F/C比(加氢气),刻蚀过程倾向于形成高分子膜
半导体制造工艺基础
终点控制
干法刻蚀必须配备一个用来探测刻蚀工艺结束点的监视器,即终点探
测系统。激光干涉度量法用来持续控制晶片表面的刻蚀速率与终止点。
在刻蚀过程中,从晶片表面反射的激光会来回振荡,这个振荡的发生是
因为刻蚀层界面的上界面与下界面的反射光的相位干涉。因此这一层材
料必须透光或半透光才能观测到振荡现象。振荡周期与薄膜厚度的变化
实 际 用
BOE:buffered oxide etching 或BHF: buffered HF
加入NH4F缓冲液:弥补 F和降低对胶的刻蚀
例2:Si采用HNO3和HF腐蚀(HNA)
各
向
例3:Si3N4采用热磷酸腐蚀
同 性
半导体制造工艺基础
第五章 刻蚀原理
8
例4:Si采用KOH腐蚀 Si + 2OH- + 4H2O Si(OH)2++ + 2H2 + 4OH-
第五章 刻蚀原理
3
过腐蚀(钻蚀):
A=0
0<A<1
A=1
假定S=时
A
1
b d
U Uniformity/non-uniformity
均匀性/非均匀性
RhighRlow Rhigh: 最大刻蚀速率 RhighRlow Rlow: 最小刻蚀速率
半导体制造工艺基础
第五章 刻蚀原理
4
刻蚀要求:
1. 得到想要的形状(斜面还是垂直图形)
半导体制造工艺基础
第五章 刻蚀原理
1
图形转移=光刻+刻蚀
两大关键问题: 待刻材料的刻蚀
速率
选择性
S r1 r2
掩膜或下层材料 的刻蚀速率
图形转移过程演示
A 1 rlat rvert
横向
刻蚀
方向纵蚀性向速:刻率各向同性速率
半导体制造工艺基础
第五章 刻蚀原理
2
刻蚀的性能参数
方向性:
半导体制造工艺基础
关系为:
d
2n
半导体制造工艺基础
第五章 刻蚀原理
21
硅化物
多晶硅
反射系数(任意单位)
硅化物/多晶硅刻蚀实验曲线 刻蚀时间(任意单位)
半导体制造工艺基础
第五章 刻蚀原理
22
Sputtering mode:硅 片置于右侧电极,该 电极接地(反应腔体 通常也接地,则增大 该电极有效面积); 右侧暗区电压差小, 通过离子轰击的物理 刻蚀很弱
RIE mode:硅片置于面积较小的左侧电极,右电 极仍接地;左侧暗区电压差大,通过离子轰击的 物理刻蚀很强
半导体制造工艺基础
第五章 刻蚀原理
23
反应离子刻蚀(RIE):常用刻蚀气体为含卤素 的物质,如CF4,SiF6,Cl2,HBr等,加入添加 气体如:O2,H2,Ar等。O2 用于刻蚀光刻胶。
干法刻蚀
SiO2——HF MEMS
纯物 理刻
蚀
反应离子刻蚀RIE 增加方向性、选择 性的方法CF4/O2
纯化 学刻
蚀
半导体制造工艺基础
第五章 刻蚀原理
32
反应等离子体刻蚀技术与设备
一个反应等离子体刻蚀反应器包括一个真空腔、抽气泵系统、电源供应 产生器、压力探测器、流量控制器与终点探测器等。
半导体制造工艺基础
第五章 刻蚀原理
25
氧气的作用
在CF4进气中加入少量氧气会提高硅和二氧化硅的刻蚀 速率。人们认为氧气与碳原子反应生成CO2,这样从等离 子体中去掉一些碳,从而增加F的浓度,这些成为富氟等离 子体。往CF4等离子体中每增加12%的氧气,F浓度会增加 一个数量级,对硅的刻蚀速率增加一个数量级。
半导体制造工艺基础
第五章 刻蚀原理
26
CF4等离子体
半导体制造工艺基础
第五章 刻蚀原理
27
硅、Si3N4和SiO2刻蚀
Si+4F*SiF4 SiO2+4F*SiF4 +O2 Si3N4+12F*3SiF4 +2N2
少量添加气体可增加选择性
CF4中添加少量O2可增加对Si,SiO2 和Si3N4的腐蚀速率
10%O2可获得最大的Si/SiO2刻蚀比
半导体制造工艺基础
第五章 刻蚀原理
39
AlCu刻蚀腔
TiW刻蚀腔
钝化层剥蚀腔
真空装载锁住腔
卡式装/卸载腔
多层金属互联(TiW/AlCu/TiW)
半导体制造工艺基础
反应等第离五子章 体刻刻蚀原蚀理的应用
40
等离子体刻蚀系统已由应用于简单、整批的抗蚀剂剥蚀快速发展到大的 单片晶片加工。下表列举了不同刻蚀工艺所用到的一些化学剂。
第五章 刻蚀原理
33
1000 100
低压整批RIE
单片晶片RIE
10
低于高密度 ECR,ICP
1
桶状等离 子体刻机
1
10
100 1000
半导体制造工艺基础
第五章 刻蚀原理
34
反应离子刻蚀(RIE)
平行板系统
RF
RF
半导体制造工艺基础
第五章 刻蚀原理
35
电子回旋共振(ECR)等离子体刻蚀机
大多数的等离子体抗蚀机,除了三极RIE外,都无法提供独立控制等离子 体参数的能力。导致轰击损伤的严重问题。ECR结合微波电源与静电场 来驱使电子沿磁场线作一定角频率的回旋。当此频率等于外加微波频率 时,电子能量与外加磁场产生共振耦合,造成大量的分解与电离。
半导体制造工艺基础
第五章 刻蚀原理
19
半导体制造工艺基础
第五章 刻蚀原理
20
等离子体探测
大多数的等离子体工艺中发出的射线范围在红外光到紫外光之间,一 个简单的缝隙方法是利用光学发射光谱仪(OES)来测量这些发射光谱 的强度与波长的关系。利用观测到的光谱波峰与已知的发射光谱比较, 通过可以决定出中性或离子物质的存在。物质相对的密度,也可以通过 观察等离子体参数改变时光强度的改变而得到。这些由主要刻蚀剂或副 产物所引起的发射信号在刻蚀终点开始上升或下降。
半导体制造工艺基础
第五章 刻蚀原理
13
干法刻蚀
✓化学刻蚀(各项同性,选择性好) ——等离子体激活的化学反应(等离子体刻蚀)
✓物理刻蚀(各向异性,选择性差) ——高能离子的轰击 (溅射刻蚀)
✓离子增强刻蚀(各向异性,选择性较好) ——反应离子刻蚀
半导体制造工艺基础
第五章 刻蚀原理
14
化学刻蚀
物理刻蚀
基本刻蚀方式为: 物理方式:溅射刻蚀,正离子高速轰击表面; 化学方式:等离子体产生的中性反应物与物质表面相互作用产生挥发性产物。 化学方式有高腐蚀速率、高的选择比与低的离子轰击导致的缺陷,但有各向 同性的刻蚀轮廓。物理方式可以产生各向同性的轮廓,但伴随低的选择比与 高的离子轰击导致的缺陷。将二者结合,如反应离子刻蚀(RIE)。
质聚集状态。
固态
液态
气态
等离子体
由于物质分子热运动加剧,相互间的碰撞就会使气体分子产生电离,这样 物质就变成由自由运动并相互作用的正离子和电子组成的混合物(蜡烛的火 焰就处于这种状态)。我们把物质的这种存在状态称为物质的第四态,即等 离子体(plasma)。因为电离过程中正离子和电子总是成对出现,所以等离 子体中正离子和电子的总数大致相等,总体来看为准电中性。
变压器耦合等离子体反应设备示意图
半导体制造工艺基础
第五章 刻蚀原理
38
集成等离子体工艺
半导体晶片都是在洁净室里加工制作,以减少大气中的尘埃污染。当器 件尺寸缩小,尘埃的污染成为一个严重的问题。为了减少尘粒的污染, 集成等离子体设备利用晶片操作机将晶片置于高真空环境中从一个反应 腔移到另一个反应腔。同时可以增加产率。
各向异性
硅湿法腐蚀由于晶向而产生的各向异性腐蚀
半导体制造工艺基础
第五章 刻蚀原理
9
原子密度:<111> > <110> > <100> 腐蚀速度:R(100) 100 R(111)
半导体制造工艺基础
第五章 刻蚀原理
10
HNA各向同性腐蚀
自终止
半导体制造工艺基础
第五章 刻蚀原理
11
利用Si的各向异性湿法腐蚀制作的MEMS (MicroElectroMechanical Systems)结构
程并不是两个相互独立的过程,有助于表面化学过程
而且相互有增强作用
/化学反应的进行