如何开展精益生产
班组精益生产心得体会总结
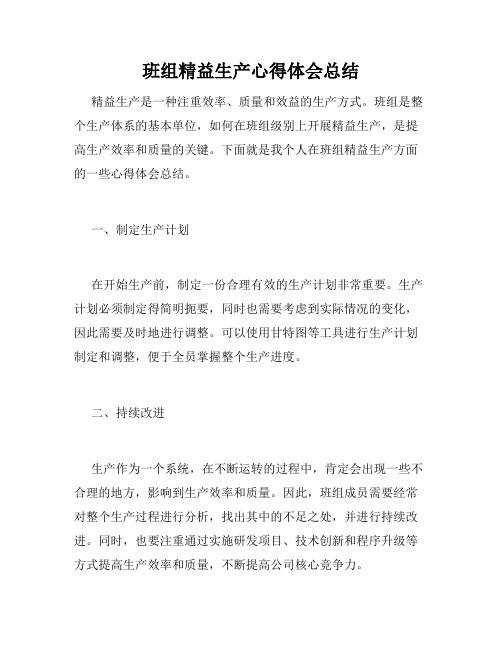
班组精益生产心得体会总结精益生产是一种注重效率、质量和效益的生产方式。
班组是整个生产体系的基本单位,如何在班组级别上开展精益生产,是提高生产效率和质量的关键。
下面就是我个人在班组精益生产方面的一些心得体会总结。
一、制定生产计划在开始生产前,制定一份合理有效的生产计划非常重要。
生产计划必须制定得简明扼要,同时也需要考虑到实际情况的变化,因此需要及时地进行调整。
可以使用甘特图等工具进行生产计划制定和调整,便于全员掌握整个生产进度。
二、持续改进生产作为一个系统,在不断运转的过程中,肯定会出现一些不合理的地方,影响到生产效率和质量。
因此,班组成员需要经常对整个生产过程进行分析,找出其中的不足之处,并进行持续改进。
同时,也要注重通过实施研发项目、技术创新和程序升级等方式提高生产效率和质量,不断提高公司核心竞争力。
三、强化培训良好的员工培训计划是成功实现班组精益生产的关键。
班组成员需要了解整个生产过程,以及如何利用不同的工具和技术实现更有效的生产。
因此,培训应该包括书面和实践课程,并应该持续进行。
在培训完成后,系统监控和反馈反应是必要的。
四、标准化作业标准化作业可以大大提高生产效率和质量。
实施标准化作业需要制定清晰的和可操作的程序和流程,使操作者易于理解和掌握。
此外,应该强调制程控制,监控每一步生产过程,及时发现和解决问题。
另外,通过持续监控和提供反馈,同步改进工序指导书、作业规程、巡视卡等标准化文档,以确保标准化作业的可持续性和有效性。
总之,班组精益生产是一个复杂而又具有挑战性的工作。
要实现成功,必须要有合适的方法、工具和技术,同时也需要全员的积极参与和共同努力。
只有这样,才能充分发挥班组的作用,提高生产效率和质量,推动企业的持续发展。
关于开展精益生产管理行动计划
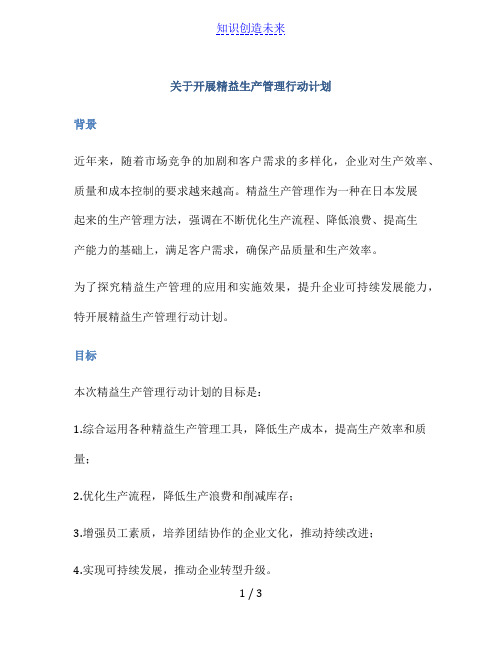
关于开展精益生产管理行动计划背景近年来,随着市场竞争的加剧和客户需求的多样化,企业对生产效率、质量和成本控制的要求越来越高。
精益生产管理作为一种在日本发展起来的生产管理方法,强调在不断优化生产流程、降低浪费、提高生产能力的基础上,满足客户需求,确保产品质量和生产效率。
为了探究精益生产管理的应用和实施效果,提升企业可持续发展能力,特开展精益生产管理行动计划。
目标本次精益生产管理行动计划的目标是:1.综合运用各种精益生产管理工具,降低生产成本,提高生产效率和质量;2.优化生产流程,降低生产浪费和削减库存;3.增强员工素质,培养团结协作的企业文化,推动持续改进;4.实现可持续发展,推动企业转型升级。
实施方案1.制定精益生产管理行动计划,明确目标和任务分工,落实责任;2.开展精益生产管理工具培训,包括价值流图、流程分析、标准化作业等方面。
同时组建精益生产管理小组,定期开展现场改善活动,推动持续改进;3.优化生产流程,减少生产浪费,采用KANBAN系统控制库存,通过滚动周期生产和拉动生产等方式适应市场需求;4.增强员工素质,培养团结协作的企业文化,促进员工自主质量控制和持续改进;5.采用质量管理工具,如Pareto图、故障模式与影响分析、程序执行表等,全面落实检验抽样检查、过程控制和品质管理等质量保证措施。
预期效果通过本次精益生产管理行动计划的实施,预期达到以下效果:1.降低生产成本、提高生产效率和质量,提升企业核心竞争力;2.减少生产浪费,降低库存、杜绝质量问题,改善企业形象和口碑;3.增强员工素质,提高员工满意度和企业文化建设;4.推动持续改进,实现精益生产管理模式的长期应用;5.促进企业可持续发展,实现企业转型升级。
结束语开展精益生产管理行动计划是促进企业现代化管理和可持续发展的有效手段。
希望企业能够充分认识到其重要性,根据自身实际情况制定科学实用的实施方案,全员参与、持续改进,提高企业竞争力和社会影响力。
推行精益生产管理的方法都有哪些
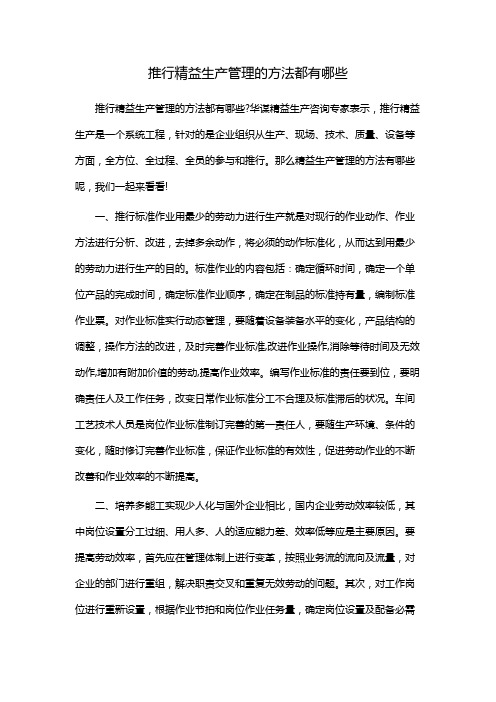
推行精益生产管理的方法都有哪些推行精益生产管理的方法都有哪些?华谋精益生产咨询专家表示,推行精益生产是一个系统工程,针对的是企业组织从生产、现场、技术、质量、设备等方面,全方位、全过程、全员的参与和推行。
那么精益生产管理的方法有哪些呢,我们一起来看看!一、推行标准作业用最少的劳动力进行生产就是对现行的作业动作、作业方法进行分析、改进,去掉多余动作,将必须的动作标准化,从而达到用最少的劳动力进行生产的目的。
标准作业的内容包括:确定循环时间,确定一个单位产品的完成时间,确定标准作业顺序,确定在制品的标准持有量,编制标准作业票。
对作业标准实行动态管理,要随着设备装备水平的变化,产品结构的调整,操作方法的改进,及时完善作业标准,改进作业操作,消除等待时间及无效动作,增加有附加价值的劳动,提高作业效率。
编写作业标准的责任要到位,要明确责任人及工作任务,改变日常作业标准分工不合理及标准滞后的状况。
车间工艺技术人员是岗位作业标准制订完善的第一责任人,要随生产环境、条件的变化,随时修订完善作业标准,保证作业标准的有效性,促进劳动作业的不断改善和作业效率的不断提高。
二、培养多能工实现少人化与国外企业相比,国内企业劳动效率较低,其中岗位设置分工过细、用人多、人的适应能力差、效率低等应是主要原因。
要提高劳动效率,首先应在管理体制上进行变革,按照业务流的流向及流量,对企业的部门进行重组,解决职责交叉和重复无效劳动的问题。
其次,对工作岗位进行重新设置,根据作业节拍和岗位作业任务量,确定岗位设置及配备必需的岗位人员。
第三,培养多能工,使岗位人员具备的操作技能满足完成岗位任务的需求。
培养多能工,实现少人化,主要是通过工作岗位轮换来进行。
让现场管理人员在所属各工作场所轮换,作业人员在组内轮换,有些作业岗位也可以每天数次岗位轮换。
三、持续开展作业改善活动广泛开展合理化建议活动,消除纯粹浪费的时间,减少没有附加价值的作业,提高附加价值的实质性的作业,从而达到少而精的目的。
精益生产实施成功的五个步骤

精益生产实施成功的五个步骤精益生产的研究者总结出精益生产实施成功的五个步骤:(1) 从样板线(modelline)开始(2) 画出价值流程图(valuestream mappin g)(3) 开展价值流程图指导下的持续改进研讨会(4) 营造支持精益生产的企业文化(5) 推广到整个公司下面就结合上面的五个步骤,阐述如何实施对传统生产方式的改造。
(一)选择要改进的关键流程精益生产方式不是一蹴而就的,它强调持续的改进。
首先应该先选择关键的流程,力争把它建立成一条样板线。
(二)画出价值流程图价值流程图是一种用来描述物流和信息流的方法。
在价值流程图中,方框代表各生产工艺,三角框代表各个工艺之间的在制品库存,各种图标表示不同的物流和信息流,连接信息系统和生产工艺之间的折线表示信息系统正在为该生产工艺进行排序等等。
在绘制完目前状态的价值流程图后,可以描绘出一个精益远景图(Future Lean Vision)。
在这个过程中,更多的图标用来表示连续的流程,各种类型的拉动系统,均衡生产以及缩短工装更换时间,生产周期被细分为增值时间和非增值时间。
(三)开展持续改进研讨会精益远景图必须付诸实施,否则规划得再巧妙的图表也只是废纸一张。
实施计划中包括什么(What),什么时候(When)和谁来负责(Who),并且在实施过程中设立评审节点。
这样,全体员工都参与到全员生产性维护系统中。
在价值流程图、精益远景图的指导下,流程上的各个独立的改善项目被赋予了新的意义,使员工十分明确实施该项目的意义。
持续改进生产流程的方法主要有以下几种:(1)消除质量检测环节和返工现象如果产品质量从产品的设计方案开始,一直到整个产品从流水线上制造出来,其中每一个环节的质量都能做到百分百的保证,那么质量检测和返工的现象自然而然就成了多余之举。
推行精益生产的第一步该做什么?

推行精益生产的第一步该做什么?
精益生产,一种以减少浪费、提高效率和质量为目标的生产管理方法。
要推行精益生产,第一步是进行价值流分析,即对生产过程中的各个环节进行评估和优化。
具体步骤如天行健精益管理咨询公司下文所述:
1.明确价值流:确定产品从原材料采购到最终交付给客户的整个流程。
这包括所有的物流、信息流和价值流动。
通过绘制价值流图,可以清晰地看到整个生产过程中的每个环节。
2.识别浪费:对于每个环节,分析其中存在的浪费。
浪费包括传统的七大浪费,如过度生产、库存积压、等待、运输、不合格品、过度处理和不必要的运动。
通过识别浪费,可以明确需要优化的重点。
3.确定价值流动与非价值流动:将生产过程中的每个活动分为价值流动和非价值流动。
价值流动是指为产品增加价值的活动,非价值流动是指不增加价值的活动。
通过区分价值流动和非价值流动,可以找出需要改进的环节。
4.寻找瓶颈:确定生产过程中的瓶颈环节,即限制整个生产流程的关键环节。
通过优化瓶颈环节,可以提高整个生产过程的效率。
5.制定改进计划:根据价值流分析的结果,制定改进计划。
改进计划应包括具体的措施和时间表。
在制定改进计划时,需要考虑到各个环节的优先级和可行性。
综上所述,通过价值流分析,可以找出生产过程中的瓶颈和浪费,并制定出改进计划。
这将为推行精益生产奠定基础,提高生产效率和质量,降低成本,为企业发展提供支持。
精益生产生产车间现场管理

精益生产车间现场管理:提升效率与品质的关键策略一、现场布局优化,提升空间利用率1. 合理规划生产线布局,减少物料搬运距离。
根据生产流程,将相关工序紧密排列,降低在制品的移动次数,提高生产效率。
2. 采用流线型设计,确保生产流程顺畅。
通过分析生产过程中的瓶颈环节,优化设备布局,使物料流动更加顺畅。
3. 创设整洁、有序的现场环境。
定期清理现场,消除不必要的物品,确保生产空间宽敞,降低安全事故发生的概率。
二、标准化作业,确保生产稳定性1. 制定详细的生产作业指导书,明确各工序操作规程。
让员工按照标准作业,减少人为失误,提高产品质量。
2. 开展技能培训,提高员工操作水平。
针对不同岗位需求,组织专业培训,提升员工技能,降低生产过程中的不良品率。
3. 落实岗位责任制,强化员工责任心。
明确各岗位职责,确保每位员工都能认真负责地完成本职工作。
三、目视化管理,提高现场透明度1. 利用颜色、标识等手段,对现场进行分区、定置。
使员工一目了然,快速找到所需物品,提高工作效率。
2. 设立看板系统,实时展示生产进度、质量状况。
让员工了解生产现状,便于及时调整生产计划。
3. 建立异常反馈机制,鼓励员工发现问题、解决问题。
通过目视化管理,让问题无处藏身,确保生产顺利进行。
四、持续改善,推动现场管理不断提升1. 开展全员参与的质量管理活动,激发员工潜能。
鼓励员工提出合理化建议,不断优化生产流程。
2. 定期组织现场巡查,查找问题根源。
针对发现的问题,制定改进措施,落实整改。
3. 建立持续改善的长效机制,将现场管理纳入日常工作中。
通过持续改进,不断提升车间现场管理水平。
五、库存控制,减少浪费提高响应速度1. 实施准时制生产(JIT),减少在制品和成品库存。
通过精确的需求预测和订单管理,降低库存成本,提高资金周转率。
2. 推行看板管理系统,实现按需生产。
根据生产线的实际消耗情况,动态调整物料供应,避免过量生产。
3. 建立库存预警机制,及时发现潜在问题。
精益生产精细管理工作计划
一、背景及目标随着市场竞争的日益激烈,企业对生产效率和质量的要求越来越高。
为了提升企业核心竞争力,实现可持续发展,我公司决定开展精益生产精细管理工作。
本次管理计划旨在提高生产效率、降低成本、提升产品质量,为我国制造业的发展贡献力量。
二、组织架构1. 成立精益生产精细管理领导小组,由公司总经理担任组长,各部门负责人为成员。
2. 设立精益生产精细管理办公室,负责具体实施和协调各部门工作。
三、工作内容1. 精益生产培训(1)组织员工参加精益生产相关培训,提高员工对精益生产的认识和理解。
(2)邀请专家进行现场指导,针对生产现场存在的问题进行诊断和改进。
2. 5S管理(1)开展5S管理活动,对生产现场进行整理、整顿、清扫、清洁、素养。
(2)制定5S管理标准,确保现场整洁有序,提高工作效率。
3. 流程优化(1)对生产流程进行全面梳理,找出瓶颈环节,进行优化改进。
(2)采用看板管理,实时监控生产进度,提高生产效率。
4. 质量提升(1)加强质量管理培训,提高员工质量意识。
(2)开展质量攻关活动,降低不良品率,提升产品质量。
5. 成本控制(1)开展成本分析,找出成本浪费环节,进行针对性控制。
(2)推行精益生产工具,降低生产成本。
6. 安全生产(1)加强安全生产培训,提高员工安全意识。
(2)开展安全隐患排查,确保生产安全。
四、实施步骤1. 第一阶段(1-3个月):成立领导小组,制定管理计划,开展5S管理培训和现场指导。
2. 第二阶段(4-6个月):优化生产流程,开展质量提升和成本控制活动。
3. 第三阶段(7-9个月):加强安全生产管理,提升员工安全意识。
4. 第四阶段(10-12个月):总结经验,持续改进,巩固精益生产成果。
五、保障措施1. 加强组织领导,确保各项工作有序推进。
2. 制定激励政策,调动员工参与精益生产的积极性。
3. 加强监督检查,确保各项措施落实到位。
4. 建立长效机制,持续改进,不断提升企业核心竞争力。
如何从运营和现场两个层面开展精益工作?
如何从运营和现场两个层面开展精益工作?近年来,精益生产作为一种追求卓越、消除浪费的管理方法,开始被越来越多的企业所采纳。
那么,如何从运营和现场两个层面开展精益工作呢?天行健精益企业管理咨询公司解析如下:一、运营层面的精益策略1.优化流程管理运营层面的精益工作首先要从流程管理入手。
通过梳理现有工作流程,找出其中的瓶颈和低效环节,然后运用精益思维进行优化。
例如,通过引入流程图、时间线等工具,可视化工作流程,便于发现问题和改进点。
2.数据驱动的决策数据是运营决策的基石。
通过收集和分析运营数据,企业可以更加精准地了解业务运行状况,发现潜在问题,并作出科学决策。
因此,建立完善的数据收集和分析体系,是运营层面精益工作的重要一环。
3.强化供应链管理供应链管理是运营层面精益管理的重要组成部分。
企业应加强与供应商的合作,建立稳定的供应链关系,确保原材料和零部件的稳定供应。
同时,通过优化库存管理、降低库存成本、提高物流效率等措施,实现供应链的整体优化。
二、现场层面的精益实践1.5S管理现场层面的精益实践可以从5S管理开始。
5S即整理、整顿、清扫、清洁、素养,通过实施5S管理,可以改善现场环境,提高工作效率,减少浪费。
2.标准化作业标准化作业是现场精益实践的核心。
通过对作业过程进行标准化,可以确保作业质量的一致性,减少操作失误,提高作业效率。
同时,标准化作业还有助于员工之间的知识传递和经验积累。
3.可视化管理可视化管理是现场精益实践的重要手段。
通过在现场使用各种可视化工具,如看板、图表等,可以实时展示生产进度、质量问题等信息,帮助员工快速了解现场状况,作出相应调整。
总之,从运营和现场两个层面开展精益管理,可以全面提升企业的管理水平和竞争力。
企业应结合自身实际情况,制定具体的精益管理方案,不断推动精益工作的深入开展。
同时,企业还应关注市场变化和技术发展趋势,不断创新精益管理理念和方法,为企业的长远发展提供有力保障。
精益生产工作规划
一、背景与目标随着市场竞争的加剧和客户需求的不断变化,我公司认识到精益生产是实现企业可持续发展的关键。
为提升生产效率、降低成本、提高产品质量,特制定本精益生产工作规划。
一、总体目标1. 提高生产效率,缩短生产周期,降低生产成本。
2. 提升产品质量,降低不良品率,提高客户满意度。
3. 培养员工精益生产意识,提高团队协作能力。
二、具体措施1. 现场管理优化(1)优化生产布局,合理规划生产线,减少物料搬运距离。
(2)实施5S管理,保持生产现场整洁、有序。
(3)加强设备维护,提高设备运行效率。
2. 生产流程优化(1)分析生产流程,识别瓶颈环节,进行改进。
(2)推广看板管理,实现生产进度可视化。
(3)优化生产计划,提高生产计划的准确性和灵活性。
3. 质量控制提升(1)加强质量意识培训,提高员工质量意识。
(2)实施全流程质量控制,从原材料采购到产品出厂,确保产品质量。
(3)建立质量反馈机制,及时解决质量问题。
4. 人才培养与激励(1)开展精益生产培训,提高员工精益生产知识和技能。
(2)设立精益生产奖,鼓励员工积极参与精益生产改进。
(3)选拔优秀人才,培养精益生产骨干。
5. 信息化建设(1)建设生产管理系统,实现生产数据实时监控和分析。
(2)推广ERP系统,提高企业管理水平。
(3)加强网络安全防护,确保企业信息安全。
三、实施步骤1. 准备阶段(2023年1月-3月)(1)成立精益生产领导小组,明确责任分工。
(2)制定详细的工作计划,明确实施步骤和时间节点。
(3)开展精益生产培训,提高员工认识。
2. 实施阶段(2023年4月-12月)(1)开展现场管理优化、生产流程优化、质量控制提升等工作。
(2)定期召开精益生产会议,总结经验,解决问题。
(3)开展人才培养与激励,提高员工参与度。
3. 总结评估阶段(2024年1月-2月)(1)对精益生产工作进行全面总结,评估实施效果。
(2)根据评估结果,调整优化工作计划。
(3)总结经验,形成精益生产案例,推广至其他部门。
实施精益生产有哪些步骤
格式为 Word 版,下载可任意编辑
实施精益生产有哪些步骤
虽然在车间现场发生的显著改进,能引发随后一系列企业文化变革,但是如 果想当然地认为由于车间平面布置和生产操作方式上的改进,就能自动建立
精益生产的研究者总结出精益生产实施成功的五个步骤: 1、选择要改进的关键流程 精益生产方式不是一蹴而就的,它强调持续的改进。首先应该先选择关键的 流程,力争把它建立成一条样板线。 2、画出价值流程图 价值流程图是一种用来描述物流和信息流的方法。在绘制完目前状态的价值 流程图后,可以描绘出一个精益远景图(Future Lean Vision)。在这个过程 中,更多的图标用来表示连续的流程,各种类型的拉动系统,均衡生产以及 缩短工装更换时间,生产周期被细分为增值时间和非增值时间。 3、开展持续改进研讨会 精益远景图必须付诸实施,否则规划得再巧妙的图表也只是废纸一张。实施 计划中包括什么(What),什么时候(When)和谁来负责(Who),并且在实 施过程中设立评审节点。这样,全体员工都参与到全员生产性维护系统中。 在价值流程图、精益远景图的指导下,流程上的各个独立的改善项目被赋予 了新的意义,使员工十分明确实施该项目的意义。持续改进生产流程的方法 主要有以下几种:消除质量检测环节和返工现象;消除零件不必要的移动; 消灭库存;合理安排生产计划;减少生产准备时间;消除停机时间;提高劳 动利用率。 4、营造企业文化
- 1、下载文档前请自行甄别文档内容的完整性,平台不提供额外的编辑、内容补充、找答案等附加服务。
- 2、"仅部分预览"的文档,不可在线预览部分如存在完整性等问题,可反馈申请退款(可完整预览的文档不适用该条件!)。
- 3、如文档侵犯您的权益,请联系客服反馈,我们会尽快为您处理(人工客服工作时间:9:00-18:30)。
改善
Kaizen
作業穩定STABLE PROCESSES
這些要件需一同實行, 它們間互有重疊
顧客第一
創造一個 免於恐懼 的環境
讓基層人 員做決策
精實哲學 的要件
決不停止 改善
浪費及問題 尌是機會
創造一 共同的願景
過程創造結果
• 人員於作業流程中工作
(People work on processes)
Lean Manufacturing
以消除浪費來說縮短顧客之等候時間
浪費
時間Time
貨品送達
PRODUCT SHIPMENT
Lean Manufacturing
顧客訂單 CUSTOMER ORDER
浪費
時間〈縮短〉 Time (Shorter)
貨品送達 PRODUCT SHIPMENT
為什麼需要精實?
精實 (Lean)生產特質自我評量
ï ½« § µ e ï ½á § µ «
改善文化的體認
6.1 5.8 3.6 5.3 4.6 4.3 4.2 8.1 3.7 5.2 5.5 8.8 5.7
平均/平準化生產
持續不斷改善 8.5 5.6
7.4 3.4
整理整頓
目視化管理
8.5
ห้องสมุดไป่ตู้
彈性生產
快速換線換模
7.6
精實(Lean) 製造
• 它是什麼?
• 是一種在價值流(value stream)中藉由排除浪費 •
以提昇流動性,使其能獲致更短的前置時間,從 而提供高品質、低成本的製造哲學 由產品開發、程序工程、營運管理及企業總管理 作業等所組成的一整合性系統,其能為顧客提供 價值及帶給人們尊嚴
• 它不是什麼?
• 僅是裁減員額數
精實製造(Lean Manufacturing) 是一種系統...
問題解決
標準 作業
精實生產概論
5S / 目視化工廠 看板 (Kanban) 快速換模換線
Kaizen
防呆措施
全面生產性 維護
…Kaizen(改善)只是其中的一部份
精實製造
Business as Usual
顧客訂單
CUSTOMER ORDER
矯正CORRECTION
等待 WAITING 庫存
OVER PROCESSING
過度加工
INVENTORY
從何處著手 …...
公司特質自我評估
改善文化體認 10 平均/平準化生產 8 6 4 拉式生產 2 0 標準作業 數列1 整理整頓目視化工廠
全面生產性維護
彈性生產
快速換模換線
持續不斷改善
防呆措施
1. 願景(Vision):關於精實(Lean)企業體的策略願景-- 規劃 一張通往精實(Lean Roadmap)的地圖
2. 承諾(Commitment):優秀的管理領導中心 -- 對於變革的 承諾
3. 觀念轉變(Paradigm Shift):起步前先尋求專家的訓練與支 援 4. 衡量達成度(Measure of Success):設定具有挑戰性的績效 目標並加以追蹤 5. 改善的熱忱(Passion for Improvement): 迫切性-- 隨時追求 改善
競爭上 壓力 驅動作 業流程
顧客滿意 零不良
XX生產系統 後勤補給區間
精實生產
預防不良
品質 速度
小批量生產
降低生產 前置時間
提昇生產力
訂購到交貨
成本
可負擔的 事業架構 降低成本
MOVE IT OVER THERE UNTIL WE NEED IT
移動
CONVEYANCE
搬運
MOTION
七大浪費
生產過剩 OVER PRODUCTION
• 作業流程創造出結果
(Processes create results)
• 結果創造出顧客滿意
(Results create satisfied customers)
精實(Lean)的起點是人員導向
精實企業體的5項成功關鍵因素
(5 Key Factors for Lean Enterprise Success)
5.0
標準化作業
物料管理
拉式生產系統 防呆作業
全面生產性維護
精實之家House of Lean
高品質、低成本、短交期
Highest Quality, Lowest Cost, Shortest Lead Time
及時化
JIT
平準化生產
Leveled Production
自 動化 Jidoka
標準化作業