选择性焊接工艺的优化
ersa selective soldering

ersa selective soldering标题:ERSA Selective Soldering:深度解析与应用指南一、引言ERSA selective soldering,即ERSA选择性焊接技术,是一种先进的电子制造工艺,主要用于复杂电路板的精细焊接。
本文将详细解析ERSA选择性焊接的原理、设备、工艺流程、优势及其在电子制造业中的应用。
二、ERSA选择性焊接原理ERSA选择性焊接是一种精确的焊接方法,主要通过精确控制焊锡的施加位置和量,只对需要焊接的部位进行焊接,避免对不需要焊接或者敏感部件造成影响。
其工作原理主要包括以下步骤:1. 预热:首先,电路板经过预热区,使得电路板和元器件达到合适的焊接温度,减少热冲击并提高焊接质量。
2. 焊接定位:然后,通过视觉系统或机械定位系统,精确地将电路板定位到焊接头下方。
3. 焊接:焊接头在精确的位置上施加适量的焊锡,只对需要焊接的部位进行焊接。
4. 冷却:焊接完成后,电路板进入冷却区,快速冷却以稳定焊接效果并防止元器件因温度变化而受损。
三、ERSA选择性焊接设备ERSA公司的选择性焊接设备主要包括以下几个部分:1. 运输系统:用于承载和输送电路板。
2. 预热系统:包括红外线或热风预热,用于加热电路板和元器件。
3. 定位系统:包括视觉系统和机械定位系统,用于精确地定位电路板。
4. 焊接系统:包括焊锡喷嘴和焊锡供应系统,用于施加焊锡。
5. 冷却系统:用于快速冷却电路板。
6. 控制系统:包括软件和硬件,用于控制整个焊接过程。
四、ERSA选择性焊接工艺流程以下是ERSA选择性焊接的一般工艺流程:1. 电路板装载:将待焊接的电路板放入运输系统。
2. 预热:电路板通过预热区,达到合适的焊接温度。
3. 定位:通过视觉或机械定位系统,精确地将电路板定位到焊接头下方。
4. 焊接:焊接头在精确的位置上施加适量的焊锡,只对需要焊接的部位进行焊接。
5. 冷却:焊接完成后,电路板进入冷却区,快速冷却。
选择性焊接工艺

现代电子装配中的选择性焊接工艺选择性焊接既可以在线路板装配完其它元器件以后进行,也可以在此之前,不过一般情况下都是在其它元器件组装以后完成,这是因为大多数需要采用选择性焊接的元器件都无法承受表面安装器件在回焊炉里进行大批量焊接时所经受的高温。
选择性焊接的最大优点在于它的适用性比较强,能够很好地焊接各种元器件、引脚以及处于不同位置的焊点,例如它可以焊接线路板底面的表面安装器件,也可以翻转线路板在板子的两面进行焊接,不论是大面积针栅阵列(PGA)封装还是带有较大散热器的元器件,它都能轻松焊接。
由于选择性焊接是一种由机器控制的工艺,所以和受个人技术影响的手工焊不同,它的重复性较好,可以得到非常一致的焊接效果。
焊接时需要将焊接双方如引脚与焊盘、焊盘与焊盘或者其它形式的组合连结在一起,要想使焊料浸润这些焊接的地方,其表面需保持清洁,而且应提高双方接触表面的温度,使其超过焊料的熔点,这样焊料才能浸润整个焊接面。
毛细现象在大多数焊接过程中都起着重要的作用,它在选择性焊接中也很关键。
简单的选择性焊接设备利用锡槽和一种泵压结构,使融熔焊料向上喷出,通过特殊的喷嘴形成一定的流量和形状,喷出的焊料再接触到线路板的底部和要进行焊接的元器件。
复杂选择性焊接设备则是一种全自动化系统,每台设备装有许多微小的喷嘴,可一次同时完成多个元件或线路板的焊接,并且可以和全自动生产线整合在一起。
热传导与毛细作用选择性焊接的巧妙之处在于它能够将微量焊料送到线路板下面而浸润某一个引脚,实现理想的热传导过程,热量可通过导热体很快传播,如这里的通孔和引脚。
如果线路板已经经过了预热,则当融熔的焊锡波峰接触到PCB底部时,被焊元件和焊接表面温度迅速升高,并超过焊料熔化温度达到浸润要求,此时只需要很短的停留时间就可以形成焊点。
融熔的焊料是一种理想的热载体,它的传热速度很快,只要条件合适即可形成非常好的弯月型液面。
它可以同时在板子的上面和下面进行回流焊,由于波峰的高度并不重要,所以它的重复性能做到非常好。
改善焊接结构疲劳强度的工艺方法
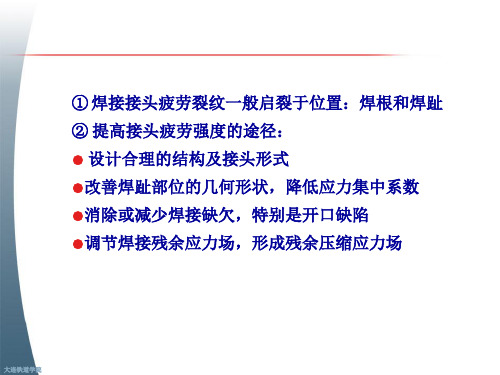
5.降低应力集中和产生压缩应力的复合方法
5.1 锤击法
锤击法属于冷加工方法,其作用是在接头焊趾处表面造成压缩应力,并减小缺口尖 锐度,降低应力集中,从而提高疲劳强度。非承载T型接头锤击后2×106循环下疲劳强度 提高54%。
IIW推荐: ● 锤头顶部直径:8~12mm ● 气锤压力:5~6 Pa ● 锤击深度:采用4次冲击以保证锤击深度0.6mm
图15 点状局部加热位置及其效果
大连铁道学院
大连铁道学院
图16 点状局部加热位置及其应力分布
表4 2×106循环次数下局部加热的效应(疲劳强度MPa)
大连铁道学院
大连铁道学院
△
提高53%
△
△ a)— 在不正确位置加热
▲ b)— 在不正确位置加热
拉伸残余应力 压缩残余应力
图17 点状加热位置对提高疲劳强度的影响
大连铁道学院
1.合理设计结构形式
大连铁道学院
图1 板梁的合理与不合理设计
大连铁道学院
图2 翼板的合理与不合理设计
a)改变盖设计
a)加筋形状突然改变 b)加筋形状有所改进但仍不合理 c)良好设计
大连铁道学院
2.合理选择接头形式
基本原则: ● 尽量减少焊缝的数量且避免交叉焊缝 ● 尽量采用连续焊缝,少用断续焊缝,其端部造成应力集中 ● 设计中尽量采用应力集中系数小的对接接头 ● 角焊缝疲劳强度低,设计中尽量采用不承载角焊缝 ● 承载角焊缝尽量采用开坡口焊接并焊透 ● 保证基本金属与焊缝之间的平滑过渡
182.7
179.4
157.8
164.8
118.3
124.9
113.0
11%
23%
41%
选择性波峰焊实习报告

一、实习背景随着电子产品的快速发展,焊接技术在电子产品制造中扮演着至关重要的角色。
选择性波峰焊作为一种先进的焊接技术,具有自动化程度高、焊接质量稳定等优点,在电子产品制造中得到广泛应用。
为了深入了解选择性波峰焊技术,我于2023年7月至9月在XX电子科技有限公司进行了为期两个月的实习。
二、实习内容1. 理论学习实习期间,我首先进行了选择性波峰焊的理论学习。
通过查阅资料、参加公司组织的培训课程,我对选择性波峰焊的原理、工艺流程、设备操作等方面有了较为全面的了解。
2. 实际操作在理论学习的指导下,我参与了选择性波峰焊的实际操作。
实习期间,我主要学习了以下内容:(1)设备操作:掌握了选择性波峰焊机的操作流程,包括预热、焊接、冷却等环节。
(2)焊接工艺:了解了焊接参数的设置,如焊接温度、时间、压力等,并学会了根据不同元件和焊接要求调整焊接参数。
(3)焊接质量检测:学会了使用显微镜等工具对焊接质量进行检测,确保焊接质量符合要求。
3. 项目实践在实习过程中,我参与了公司某款电子产品的焊接生产项目。
从元件挑选、焊接工艺制定到焊接生产,我全程参与了项目的实施。
通过实际操作,我深刻体会到了选择性波峰焊技术在电子产品制造中的重要性。
三、实习体会1. 提高自身技能通过这次实习,我对选择性波峰焊技术有了更加深入的了解,提高了自己的专业技能。
在实际操作中,我学会了如何根据不同元件和焊接要求调整焊接参数,确保焊接质量。
2. 增强团队协作能力在实习过程中,我与同事们共同完成了多个焊接项目。
通过团队合作,我学会了如何与同事沟通、协调,提高了自己的团队协作能力。
3. 培养职业素养实习期间,我严格遵守公司规章制度,认真完成各项工作任务。
在遇到困难时,我主动寻求解决方案,培养了自己的职业素养。
四、总结选择性波峰焊实习使我受益匪浅,不仅提高了我的专业技能,还锻炼了我的团队协作能力和职业素养。
在今后的学习和工作中,我将继续努力,不断提升自己,为我国电子产品制造业的发展贡献自己的力量。
焊接的工艺特点及流程介绍
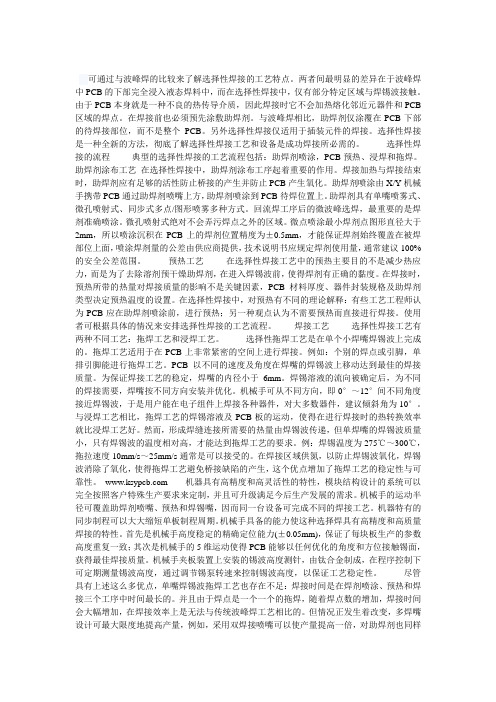
可通过与波峰焊的比较来了解选择性焊接的工艺特点。
两者间最明显的差异在于波峰焊中PCB的下部完全浸入液态焊料中,而在选择性焊接中,仅有部分特定区域与焊锡波接触。
由于PCB本身就是一种不良的热传导介质,因此焊接时它不会加热熔化邻近元器件和PCB 区域的焊点。
在焊接前也必须预先涂敷助焊剂。
与波峰焊相比,助焊剂仅涂覆在PCB下部的待焊接部位,而不是整个PCB。
另外选择性焊接仅适用于插装元件的焊接。
选择性焊接是一种全新的方法,彻底了解选择性焊接工艺和设备是成功焊接所必需的。
选择性焊接的流程典型的选择性焊接的工艺流程包括:助焊剂喷涂,PCB预热、浸焊和拖焊。
助焊剂涂布工艺在选择性焊接中,助焊剂涂布工序起着重要的作用。
焊接加热与焊接结束时,助焊剂应有足够的活性防止桥接的产生并防止PCB产生氧化。
助焊剂喷涂由X/Y机械手携带PCB通过助焊剂喷嘴上方,助焊剂喷涂到PCB待焊位置上。
助焊剂具有单嘴喷雾式、微孔喷射式、同步式多点/图形喷雾多种方式。
回流焊工序后的微波峰选焊,最重要的是焊剂准确喷涂。
微孔喷射式绝对不会弄污焊点之外的区域。
微点喷涂最小焊剂点图形直径大于2mm,所以喷涂沉积在PCB上的焊剂位置精度为±0.5mm,才能保证焊剂始终覆盖在被焊部位上面,喷涂焊剂量的公差由供应商提供,技术说明书应规定焊剂使用量,通常建议100%的安全公差范围。
预热工艺在选择性焊接工艺中的预热主要目的不是减少热应力,而是为了去除溶剂预干燥助焊剂,在进入焊锡波前,使得焊剂有正确的黏度。
在焊接时,预热所带的热量对焊接质量的影响不是关键因素,PCB材料厚度、器件封装规格及助焊剂类型决定预热温度的设置。
在选择性焊接中,对预热有不同的理论解释:有些工艺工程师认为PCB应在助焊剂喷涂前,进行预热;另一种观点认为不需要预热而直接进行焊接。
使用者可根据具体的情况来安排选择性焊接的工艺流程。
焊接工艺选择性焊接工艺有两种不同工艺:拖焊工艺和浸焊工艺。
改善焊接结构疲劳强度的工艺方法

改善焊接结构疲劳强度的工艺方法焊接接头疲劳裂纹一般启裂位置存在于焊根和焊趾两个部位,如果焊根部位的疲劳裂纹启裂的危险被抑制,焊接接头的危险点则集中于焊趾部位。
许多方法可以用于提高焊接接头的疲劳强度,① 减少或消灭焊接缺欠特别是开口缺陷;②改善焊趾部位的几何形状降低应力集中系数;③调节焊接残余应力场,产生残余压缩应力场。
这些改进方法可以分为两大类,如表1所示。
焊接过程优化方法不仅是针对提高焊接结构疲劳强度而考虑,同时对焊接结构的静载强度、焊接接头的冶金性能等各方面都有极大的益处,这方面的资料很多在此不多赘述。
表1 焊接结构疲劳强度的改善方法下面从工艺方法角度考虑分三部分详细论述改善焊接接头疲劳强度的主要方法。
3.1 改善焊趾几何形状降低应力集中的方法1) TIG熔修国内外的研究均表明,TIG熔修可大幅度提高焊接接头的疲劳强度,这种方法是用钨极氩弧焊方法在焊接接头的过渡部位重熔一次,使焊缝与基本金属之间形成平滑过渡。
减少了应力集中,同时也减少了该部位的微小非金属夹渣物,因而使接头部位的疲劳强度提高。
熔修工艺要求焊枪一般位于距焊趾部位0.5~处,并要保持重熔部位洁净,如果事先配以轻微打磨效果更佳。
重要的是重熔中发生熄弧时,如何处理重新起弧的方法,因为这势必影响重熔焊道的质量,一般推荐重新起弧的最好位置是在焊道弧坑之前面6mm处,最近国际焊接学会组织欧洲一些国家和日本的一些焊接研究所,采用统一由英国焊接研究所制备的试样进行了—些改善接头疲劳强度方法有效性的统一性研究,证实经该方法处理后该接头的2×106循环下的标称疲劳强度提高58%,如果将得到的211MPa的疲劳强度标称值换算成相应的特征值(K指标) 为144MPa。
它己高出国际焊学会的接头细节疲劳强度中的最高的FAT值。
2) 机械加工若对焊缝表面进行机械加工,应力集中程度将大大减少,对接接头的疲劳强度也相应提高,当焊缝不存在缺陷时,接头的疲劳强度可高于基本金属的疲劳强度。
选择性波峰焊工艺设计指南
选择性波峰焊工艺设计指南1.简介实现最佳焊接结果,需满足特殊工艺条件高标准工艺可靠性取决于以下几点:●pad设计(pad类型,pad之间距离)●pad及周边元件pad距离(如,不应触碰SMD器件)●PIN脚长度不应超过电路板板下PIN脚长度●PIN脚间距(如,连接器间距)这些影响系数直接影响流动焊料的剥离。
为了避免产生锡桥,需要重复剥离。
锡桥是导致焊接失败的主要原 因(占80%以上)。
通常来说,小型拖焊工艺和浸焊工艺存在明显区别。
每道工艺都需特殊的印刷电路板设计。
如下设计指南可确保最佳工艺条件。
如果您不采纳如下建议,工艺窗口将会受到局限,而且需额外步骤稳定 此工艺。
这些额外步骤所需维护要求更高,并会增加模具零件的磨损。
> 3.0 mm> 5.0 mm2. 浸焊工艺最佳布局●优先使用圆垫●圆垫之间距离: >0.60mm ●PIN脚距离: >2.54mm2.2 PIN脚长度不应超过电路板板下PIN脚长度2.3 焊料喷嘴间隙 - 到邻垫距离(不被焊接)●在3面上: > 3.0mm ●在第四面上: > 5.0mm> 1.9 mm3. 微波/拖焊焊接工艺最佳布局3.1 pad之间的间隙●优先使用圆垫●圆垫之间距离: >0.60mm ●PIN脚距离: > 1.9mm3.2 PIN脚长度不应超过电路板3.3 微波间隙 - 到邻垫距离(不被焊接)●在3面上: > 2.0mm ●在第四面上: > 5.0mmØ 3.0 mm4. 焊料喷嘴最小尺寸4.1 矩形焊料喷嘴●焊接面积 <40mm ²4.2 圆形焊料喷嘴●焊接区 <7mm ²5. 相邻元件最大高度底部(焊接面)所能容纳的最大元件高度受限于焊料喷嘴的高度。
标准焊料喷嘴高度为32mm。
因此, 最大元件高度不应超过25mm。
更高的元件需要更高的焊料喷嘴设计,我们可根据您的要求设计。
pcb焊接技巧及注意事项
pcb焊接技巧及注意事项焊电路板技巧1:选择性焊接的工艺流程包括:助焊剂喷涂,电路板预热、浸焊和拖焊。
助焊剂涂布工艺在选择性焊接中,助焊剂涂布工序起着重要的作用。
焊接加热与焊接结束时,助焊剂应有足够的活性防止桥接的产生并防止电路板产生氧化。
助焊剂喷涂由X/Y机械手携带电路板通过助焊剂喷嘴上方,助焊剂喷涂到pcb电路板焊位置上。
焊电路板技巧2:回流焊工序后的微波峰选焊,重要的是焊剂准确喷涂,微孔喷射式不会弄污焊点之外的区域。
微点喷涂焊剂点图形直径大于2mm,所以喷涂沉积在电路板上的焊剂位置精度为±0.5mm,才能保证焊剂始终覆盖在被焊部位上面。
焊电路板技巧3:可以通过与波峰焊的比较来了解选择性焊接的工艺特点,两者间明显的差异在于波峰焊中电路板的下部完全浸入液态焊料中,而在选择性焊接中,仅有部分特定区域与焊锡波接触。
由于电路板本身就是一种不良的热传导介质,因此焊接时它不会加热熔化邻近元器件和电路板区域的焊点。
在焊接前也必须预先涂敷助焊剂,与波峰焊相比,助焊剂仅涂覆在电路板下部的待焊接部位,而不是整个pcb电路板。
另外选择性焊接仅适用于插装元件的焊接,选择性焊接是一种全新的方法,彻底了解选择性焊接工艺和设备是成功焊接所必需的。
电路板焊接注意事项1、提醒大家拿到PCB裸板后首先应进行外观检查,看是否存在短路、断路等问题,然后熟悉开发板原理图,将原理图与PCB丝印层进行对照,避免原理图与PCB不符。
2、PCB焊接所需物料准备齐全后,应将元器件分类,可按照尺寸大小将所有元器件分为几类,便于后续焊接。
需要打印一份齐全的物料明细表。
在焊接过程中,没焊接完一项,则用笔将相应选项划掉,这样便于后续焊接操作。
焊接之前应采取戴静电环等防静电措施,避免静电对元器件造成伤害。
焊接所需设备准备齐全后,应保证烙铁头的干净整洁。
初次焊接推荐选用平角的焊烙铁,在进行诸如0603式封装元器件焊接时烙铁能更好的接触焊盘,便于焊接。
选择性焊接工艺技术的研究
选择性焊接工艺技术的研究烽火通信科技股份有限公司鲜飞摘要: 本文介绍了选择性焊接的概念、特点、分类和使用工艺要点。
选择性焊接是现代组装技术的新概念,它的出现促进了SMT(表面贴装技术)的发展,并为PCB设计者提供了新的工艺选择。
可以确信选择性焊接将会被更多地应用于电子组装上,成为一种具有竞争力的焊接技术。
关键词:选择性焊接;印刷线路板;波峰焊The Research of Selective SolderingXIAN Fei(Fiberhome Telecommunication Technologies Co., Ltd, Wuhan 430074,China)Abstract: The things of selective soldering’s concept, characteristics, division and technical gist are described in this paper. Selective soldering is a new concept of the contemporary assembly technology. It is said that selective soldering has developed and innovated SMT since it was appeared and also provides a new choice for PCB designer. It is believed that selective soldering will more be adopted in electronics assembly, and will also be a competitive soldering technology. Keywords:Selective Soldering;PCB;Wave Soldering1 引言回顾近年来电子工业工艺发展历程,可以注意到一个很明显的趋势就是回流焊技术。
选择性波峰焊技术选型
摘要选择性波峰焊技术不是一项新工艺,它已经在汽车和 医疗产品行业通孔元件的应用上有30年的历史了。
如 今,越来越多的制造业正努力使SMD技术微型化以便 降低PCB板的复杂性及平衡电路板元件密度,从而保 证良好的组装工艺。
说到这里,有人要问,为什么选 择性波峰焊技术一直沿用至今?难道是因为元件可靠 性,独特性和复杂性才不得不用此技术么?先记住这 个疑问,下一个问题就讨论哪种平台最适合此产品。
本文介绍选择性波峰焊技术的评估过程。
本文将低成 本平台和高成本平台分别归为平台A和平台B。
通过对 比分析和模拟,本文目的是放大两种平台的本质差异。
两种平台建立的原理相同,但不同的性能会对生产率 有所影响。
了解选择性波峰焊技术非常重要,能够在 生产过程中,避免质量成本的花费及产量缺陷。
研究表明,在焊接工艺中,零件和其功能会影响焊接 的可焊性。
本文将对助焊剂喷涂,预热,锡槽和喷嘴 材料间分析进行实际模拟操作,做出评估。
另外,每 种平台的投资成本也将考虑在内。
本文旨在为选择焊接平台提供信息,同时也可为有相 同工艺和应用需求的制造商提供参考。
关键词:选择性焊接,混合技术,平台,制造,指南简介选择性波峰焊技术不是一项新工艺,自1980年以来, 在有限规模的生产中,已经使用此技术进行通孔元件 的应用。
客户总是要求在不损害产品质量的情况下降低产品价 格,因此,对制造商来说,为特定的产品选择合适的 平台是一个不小的挑战。
根据我们的经验,需要考虑 三个主要的因素:产量,周期时间和质量。
最好是有一个良好的周期时间,但是许多因素会影响 这个周期时间,比如传送带设计,参数设置和焊接焊 点的数量。
最后也相当重要的是质量方面的影响。
有几个方面影 响着产品质量,如材料,设计,工艺参数,处理方式 和设备本身引起的错误。
实验材料I. 助焊剂,Alpha Metal SLS65II. 焊锡条,通过无铅认证的SAC 305III.PCB板,280×200mm×1.6mm+/-0.2mm包括焊 料标签,4层铜,2层墨IV. PCB夹具(金属)焊接概念本文将工艺平台概念分为如下几类:ConceptProcess 1Process 2 Process 3 Process 4Platform A Platform B 50 dots/sec 60 dots/sec 4.0 – 6.0 mm3.0 – 8.0mm平台A 平台B 装载装载助焊助焊焊接+预热预热焊接图1 机器基本概念图1 列出了两种平台在选择性焊接过程中简单的工艺 流程。
- 1、下载文档前请自行甄别文档内容的完整性,平台不提供额外的编辑、内容补充、找答案等附加服务。
- 2、"仅部分预览"的文档,不可在线预览部分如存在完整性等问题,可反馈申请退款(可完整预览的文档不适用该条件!)。
- 3、如文档侵犯您的权益,请联系客服反馈,我们会尽快为您处理(人工客服工作时间:9:00-18:30)。
选择性焊接工艺的优化
合理的印制板布局和焊接喷嘴设计可以显著提高选择性波峰焊工艺的质量和成本
结构
市场全球化导致了基于成本压力上的激烈竞争。
因此,在保证产品一贯高品质的基础上,电子产品制造企业必须想方设法降低生产成本。
基于对品质和制造流程再现性的要求,人工焊接方式因其费钱费时和成本敏感性强,已不再具有优势。
另外,高密度多层板及小型化和高引脚数的细间距器件很难实现高质量/高效率的维修。
因此,诸如生产率、操作培训和错误装配所造成的“隐形成本”也必须在总成本中加以考虑。
还要特别关注的是,无铅工艺应用中人工返修焊接过程将导致极大的热应力损伤问题。
因此,目标是要建立一个零缺陷的选择性波峰焊工艺。
在这里,一个合理的印制板设计是非常重要的。
例如,焊盘的形状和它们之间的间距如果采用了合理的设计,就会大大降低短路缺陷发生的可能性。
焊盘和邻近不被润湿的焊盘之间的距离设计,也需要遵循一定的规则。
引脚之间的距离和引脚的长度,也同样需要加以考虑。
此外,选择合适的焊接喷嘴,可以避免在自动选择性焊接工艺中发生焊接缺陷。
焊接喷嘴的形状或尺寸以及所采用的技术(比如润湿性和非润湿性焊接喷嘴)的设计也是重要的考虑因素。
新增的创新功能,比如“去桥接刀”(debridging Knives),可以有效降低桥接缺陷的形成,特别是在浸焊(dip)工艺中。
不同的焊接工艺
在焊点和邻近器件之间没有空隙的条件下很难实施焊接, 这是在选择性焊接工艺中最普遍
的问题, 通常是因为焊接过程中容易将SMD器件冲洗掉或焊接喷嘴容易刮擦和损坏有引脚器件的封装外壳.
在其他许多情况下,主要的缺陷是焊接短路和填充不良;此外,锡珠也会导致缺陷。
形成良好的焊点基于多种因素,而选择性焊接工艺可提供可靠的焊接结果。
通常,不同的选择性波峰焊工艺有不同的焊接模式。
如果采用单“迷你波”(Miniwave)焊接工艺(图1),可选择拖焊(drag)或浸焊模式进行操作,并允许以一定的角度进行焊接。
这种系统柔性更强,而且对板子的设计约束也较少。
但是, 根据焊点的数量,采用单“迷你波”工艺所需要的操作周期相对较长, 从1分钟到10分钟不等。
另一方面,多喷嘴浸焊工艺(图2)使用特定的焊接喷嘴工具,在一定程度限制了柔性。
不过,所有焊点在装配过程中是同时被焊接的,多喷嘴浸焊工艺可以提供更短的操作周期,大约20到30秒。
这类设备大多数是不能设定焊接角度的。
部分这类工艺对设计有着不同的要求。
印制板设计规范
为避免在选择性焊接工艺中发生问题,相关印制板设计规范主要集中在对焊点周围间隙的设定上。
可采取一些措施来改善孔填充效率,比如正确的器件引脚长度,引脚直径和通孔之间的正确比例,热解耦效应(thermal decoupling)等。
为了降低桥接缺陷产生的风险,必须考虑器件引脚及其长度的范围;但是,采用特殊设计的焊接喷嘴也可以帮助减少桥接缺陷。
此外,通过合理的印制板设计或采用特殊的焊接喷嘴设计,也可以降低锡珠缺陷的产生。
焊点周围的间隙
为了获得可靠的焊接工艺效果,单“迷你波”焊接工艺的喷嘴内径一般为3mm,外径则在4mm 左右。
如果采用多喷嘴浸焊工艺,则外部尺寸至少为5mm×8mm。
为避免由边界间隙导致的焊接困难,在多喷嘴浸焊工艺过程中,需要焊接的焊点与周边器件或不需要焊接的焊点之间必须至少保持2 mm 的间距。
一个最小为5 mm × 8 mm 的喷嘴至少需要在焊点周围留出9mm×12mm的空间(图3)。
根据特殊的工艺条件,很小间距的焊接也能实现;当然,这需要做彻底的检查。
它主要根据周围器件的型号以及可能需要采取特殊地措施,例如使用有定位脚的夹子或润湿型焊接喷嘴等。
对于“迷你波”焊接工艺,板子设计者需要在引脚或引脚排的三边留出2mm的空间,并在器件离开波峰的一边留出5mm的空间,以便正确进行焊接脱离(图4)。
让波峰保持一定的角度或者采用润湿型焊接喷嘴将有利于解决有时根本不可能留出的5 mm 空间的问题(图5)。
当设计者难于在焊点三边留出至少2mm间隙时,周边的SMD器件应该进行内部对齐(图6)。
这种设计的好处在于,如果这些回流焊接器件必须在选择性焊接工艺中进行浸润,它们不会被立即冲洗掉。
使用在拖焊中的单“迷你波”焊接还需要考虑焊点及其附近高度超过10mm器件之间的距离。
当以一定角度进行焊接时,高于10mm的器件可能碰到焊接喷嘴或气体罩。
根据经验,对于这类特殊器件的设计,要求必须保证焊点与器件之间的距离等于或大于器件的高度。
改善孔填充率
焊点孔填充率不足的现象主要来自于不完全的热传导率,合理的印制板设计可以改善这一问题。
特别在多喷嘴浸焊工艺中,器件引脚的长度在改善焊点孔填充率不足的过程中扮演着重要的角色。
多喷嘴浸焊工艺要求引脚长度超过2.5mm,这与影响通孔渗透情况的能量传输率是直接相关的。
稍长的器件引脚可以更深地浸入液态焊料中,由此可增加热量的传导并最终得到较满意的孔填充率。
另一个影响孔填充率的因素是引脚和通孔直径间的合理比例。
如果比例过大,就不能形成毛细管作用;如果比例太小,助焊剂无法深入通孔,也无法形成良好的焊点。
根据经验,通孔的直径必须等于引脚直径加上0.2~0.4mm。
在无铅工艺中,可能要求加上0.5mm。
如果焊盘尺寸放大到一定的程度或者采用椭圆形焊盘,热能传导的效果会比较好。
如果可能,应避免阻焊膜过分靠近焊点,这样可以帮助在焊盘上保持一定的热量,同时也可以帮助防
止锡珠的产生。
热解耦设计也是一个值得注意的因素。
考虑了合理热解耦设计的PCB板,热能就不会完全被引脚带走,而是会在焊盘上保留更长的一段时间(图7)。
在浸焊工艺中,通常也希望在焊接过程中有连续流动的焊锡流,这样可以防止焊接过程中发生氧化,而且可以源源不断地提供正常加温的焊接合金以形成焊点。
这样能够保证即使是在最消耗热能的接触阶段,附雍辖鹨膊换? 冷却。
无论是在焊接很多引脚的情况下,还是引脚需要连接到印制板内层抑或引脚置于组件边缘的情况下,系统都可以达到显著改善孔填充率的效果。
减少桥接缺陷
桥接是发生在选择性焊接过程中的主要缺陷,主要是由于器件引脚间距离过小。
所以,多喷嘴浸焊焊接工艺要求引脚间距大于2.54mm,而单“迷你波”焊接工艺要求相对较低,引脚间距要求大于1.27mm。
满足上述条件后,系统可以设定合适的焊接角度以帮助达成良好的焊接脱离效果,减少桥接风险;或系统可配置润湿型焊接喷嘴,以达到同样的效果。
尽管引脚间距小于2.54mm的焊点排在浸焊工艺中有较大的桥接缺陷风险,但是,如果考虑板面的基本布局规则,这些引脚也是可以被良好焊接的。
在引脚附近设计不同形状的引流焊盘,比如小尺寸的焊盘或者椭圆形的焊盘,可以帮助将多余的液体焊料引离焊点,以减少桥接缺陷。
对多喷嘴焊接工具进行特殊的调整,也可以使 2.0mm引脚间距的焊接应用达到良好的效果。
器件引脚的长度对桥接缺陷的产生有着相当重要的影响。
多喷嘴浸焊工艺要求引脚长度大于2.5mm(图8)。
器件引脚长可以增加焊接脱离速度,使多余焊料不再堆积在焊点上,从而降低桥接风险。
在单迷你波焊接工艺中,板子是移动的,并通常设置一定的焊接角度以改善焊接脱离效果。
这时对引脚长度的要求大约为1mm(图9)。
较短的引脚可能造成有缺陷的焊点形状,例如:较差的半月板焊点和球状焊点。
在浸焊工艺中,有一种特别的焊接喷嘴设计,也可以减少桥接缺陷。
这种设计被称为“去桥接刀”;举例来说,就是在焊接喷嘴内安装润湿性金属板,在浸焊后用于从引脚上移除多余的液体焊料(图10)。
“去桥接刀”可用于特殊的焊接应用,例如对不能满足先前所提及的理想设计标准,引脚长度小于2.5mm,以及引脚间距介于2.0mm 到2.54mm 之间的情况。
减少锡珠缺陷
锡珠现象存在于所有的波峰焊工艺中,在无铅焊接过程中更易发生,因为无铅的工艺温度较之传统的焊接工艺有了较大的提高。
较高的工艺温度对阻焊膜有不利影响。
取决于质量状况,阻焊膜可能在预热期间就被软化,由此增加了锡珠粘连的机会。
在传统有铅相关或者高质量无铅阻焊膜的工艺应用中,生成的锡珠会即刻弹散开。
所以,在条件许可下,应使阻焊膜远离焊点(图11)。
在多喷嘴浸焊工艺中,特殊设计的喷嘴可以帮助避免锡珠缺陷的产生。
通过采用引流片的方法引导需要产生的锡流。
同时,完整的喷嘴工具上部还覆盖有一层金属板,图11:阻焊膜应远离焊点任何在液体焊料回流过程中可能出现的飞溅,都没有机会接触到印制板上。
结论
在所有的自动焊接工艺中,选择性焊接也许是要求最高的工艺,它需要很多经验以及有关于工艺本身和相关材料的基本知识。
不过,最新的选择性焊接系统已经排除了大多数可能在工艺过程中发生的问题。
对比一些基本的PCB设计规范,耗时和成本敏感型的返修焊接将成为过去,采用选择性焊接将获得良好的焊接效率并保持产品的高质量水准。
关于作者:
Reiner Zoch是SEHO公司的产品经理;Christian Ott是SEHO公司的高级销售和产品经理。