脱丁烷塔主要将 C4 和 C4 以上的组分分开
脱丁烷塔改造及运行分析

脱丁烷塔改造及运行分析摘要:详细介绍了首套煤制烯烃项目脱丁烷塔运行原理及改造背景,结合上游原料关键组分含量和下游MTBE产品中重组分含量分析改造的必要性及设计需求,并对改造后的脱丁烷塔进行工艺参数优化,达到降低混合C4损失、满足碳四装置原料需求的目的。
关键词:脱丁烷塔改造混合C4损失重组分一、项目介绍神华包头煤制烯烃项目烯烃分离装置采用的是美国Lummus公司的前脱丙烷后加氢、丙烷洗工艺技术,将来自甲醇制烯烃装置的产品气通过三级压缩、酸性气体脱除、洗涤和干燥后,在高、低压脱丙烷塔进行初次分离。
高压脱丙烷塔顶物流经产品气四段压缩后送至脱甲烷塔,其塔顶产品主要是甲烷,经冷箱换热后得到燃料气。
高压脱丙烷塔底物流送至脱丁烷塔,得到C5以上产品和混合C4产品。
脱甲烷塔底物流送至脱乙烷塔进行C2和C3分离,塔顶C2进入乙烯精馏塔塔,塔顶产品即为聚合级乙烯产品。
塔底C3进入丙烯精馏塔,塔顶馏分便是聚合级丙烯。
聚合级的乙烯和丙烯产品分别送入聚乙烯装置和聚丙烯装置作原料,混合C4送至C4装置作为深加工原料。
同时,随着原油价格上涨、能源消费结构的变化、加工技术的进步,混合碳四作为石油化工基础原料用于生产具有高附加值的精细化工产品和合成橡胶等技术已成为石油化工研究和投资热点[1]。
因此,为了有效降低脱丁烷塔釜物料中的碳四损失,增加混合碳四产量,同时保证混合碳四质量满足下游装置原料需求,我公司经分析决定对脱丁烷塔进行改造。
二、脱丁烷塔改造1.脱丁烷塔运行原理脱丁烷塔为板式塔,塔内安装有47块塔盘,塔径1100mm,塔高为29000mm,进料口在28块塔盘上,塔顶设有热旁路调节塔压,塔釜设有蒸汽再沸器。
脱丁烷塔(160T605)从C5’s及更重的组分中分离出C4,s组分。
脱丁烷塔的进料来自低压脱丙烷塔(160T502)塔釜。
从界区外来的混合C4’s物流作为回流的补充。
脱丁烷塔顶采出C4产品送往烯烃罐区,作为碳四装置原料储备。
有机化工生产技术-10-裂解气分离工艺流程

裂解气分离工艺流程授课内容:●裂解气分离工艺流程●裂解气分离过程操作知识目标:●掌握裂解气分离原则流程●掌握裂解气分离过程操作步骤和方法能力目标:●混合物精馏分离方案设计●混合物精馏分离过程操作条件制定思考与练习:●裂解气分离工艺流程主要由哪些过程构成?●裂解气分离过程操作主要异常现象及处理方法第四节裂解气深冷分离一、深冷分离流程1.深冷分离的任务裂解气经压缩和制冷、净化过程为深冷分离创造了条件—高压、低温、净化。
深冷分离的任务就是根据裂解气中各低碳烃相对挥发度的不同,用精馏的方法逐一进行分离,最后获得纯度符合要求的乙烯和丙烯产品。
2.三种深冷分离流程深冷分离工艺流程比较复杂,设备较多,能量消耗大,并耗用大量钢材,故在组织流程时需全面考虑,因为这直接关系到建设投资、能量消耗、操作费用、运转周期、产品的产量和质量、生产安全等多方面的问题。
裂解气深冷分离工艺流程,包括裂解气深冷分离中的每一个操作单元。
每个单元所处的位置不同,可以构成不同的流程。
目前具有代表性三种分离流程是:顺序分离流程,前脱乙烷分离流程和前脱丙烷分离流程。
(1)顺序分离流程顺序分离流程是按裂解气中各组分碳原子数由小到大的顺序进行分离,即先分离出甲烷、氢,其次是脱乙烷及乙烯的精馏,接着是脱丙烷和丙烯的精馏,最后是脱丁烷,塔底得碳五馏分。
图2-4 顺序分离工艺流程简图1—压缩Ⅰ、Ⅱ、Ⅲ段;2—碱洗塔;3—压缩Ⅳ、Ⅴ段;4—干燥器;5—冷箱;6—脱甲烷塔;7—第一脱乙烷塔;8—第二脱甲烷塔;9—乙烯塔;10—加氢反应器;11—脱丙烷塔;12—第二脱乙烷塔;13—丙烯塔;14—脱丁烷塔;15-甲烷化;16-氢气干燥器顺序深冷分离流程如图2-4所示。
裂解气经过压缩机Ⅰ、Ⅱ、Ⅲ段压缩(1),压力达到1.0MPa,送入碱洗塔(2),脱除酸性气体。
碱洗后的裂解气再经压缩机的Ⅳ、Ⅴ段压缩(3),压力达到3.7MPa,送入干燥器(4)用分子筛脱水。
干燥后的裂解气进入冷箱(5)逐级冷凝,分出的凝液分为四股按其温度高低分别进入脱甲烷塔(6)的不同塔板,分出的富氢经过甲烷化(15)脱除CO及干燥器(16)脱水后,作为碳二馏分和碳三馏分加氢脱炔用氢气。
脱丁烷塔碳四产品质量波动原因及处理_宫钦月

ABSTRACTS
ETHYLENE INDUSTRY Started Publication in 1989,Quarterly. Mar. 2011 Vol. 23 No. 1 Total 85th
REVIEW OF SINOPEC ’S ETHYLENE PRODUCTION IN 2010 Ji Weiyi,Xu Yuehua,Guo Xin. Chemical Department of SINOPEC,Beijing,P. C. 100728 Abstract: The achievement and performance of SINOPEC’s ethylene production in 2010 are introduced and analyzed briefly,and some suggestions and attentive points on SINOPEC’s ethylene production in 2011 are put forward. Keywords: SINOPEC; Ethylene; Operation; Review
根据脱丁 烷 塔 系 统 各 种 波 动 表 现,初 步 分 析 混合碳四产品质量波动的原因如下:
( 1) DA - 405 塔内浮阀、降液管、受液槽等部 件因结焦物 堵 塞,流 体 流 通 不 畅,产 生 液 泛,导 致 脱丁烷塔工 作 不 正 常,传 质 传 热 不 良 致 使 混 合 碳 四产品质量波动;
关键词: 乙烯 碳四产品 质量
1 乙烯装置脱丁烷塔系统简介 1. 1 工艺流程
乙烯生产工艺流程组织—裂解气的分离流程的组织
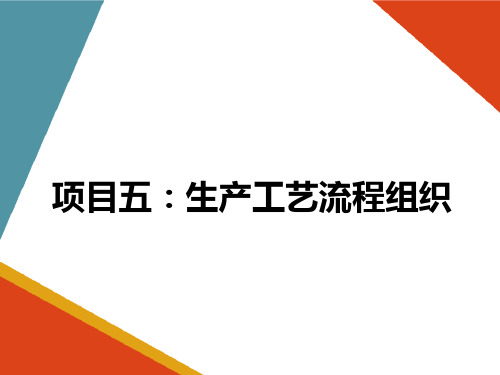
任务三 裂解气的分离流程的组织
二.前脱乙烷流程 前脱乙烷分离流程的特点是: 由于脱乙烷塔的操作压力比较高,这样势必
任务三 裂解气的分离流程的组织
任务三 裂解气的分离流程的组织
一.顺序分离流程
裂解气经过离心式压缩机一、二、三段压缩,压 力达到1MPa,送入碱洗塔,脱去H2S、CO2等酸 性气体。碱洗后的裂解气经过压缩机的四、 五段 压缩,压力达到3.7MPa. 经冷却到15℃,去干燥 器用3A分子筛脱水,使裂解气的露点温度达到70℃左右。
任务三 裂解气的分离流程的组织
一.裂解气组成
二、裂解气的净化
(一) 酸性气体的脱除
1、酸性气体的来源
• CO2,H2S和其他气态硫化物 • 气体裂解原料带入的气体硫化物和CO2 • 液体裂解原料中所含的硫化物高温氢解生成
的CO2和H2S • 结炭与水蒸气反应生成CO和CO2 • 裂解炉中有氧进入时,氧与烃类反应生成CO2
(1)催化剂 活性组分:钴(Co)、镍(Ni)、钯
(Pd) 助催化剂:铁(Fe)和银(Ag) 载体:分子筛或a-Al2O3
催化加氢脱炔的工艺方法
前加氢 利用裂解气中H2进行加氢 特点:流程简单,投资少。但操作稳定性差。
后加氢 先分离出C2、C3后,再分别加氢 特点:温度易控,不易飞温。
(5) 乙烯精馏塔 将乙烯与乙烷进行分离的塔,称乙烯精馏塔,
简称乙烯塔。 (6) 丙烯精馏塔
将丙烯与丙烷进行分离的塔,称丙烯精馏塔, 简称丙烯塔。
任务三 裂解气的分离流程的组织
三.塔的操作条件与相对挥发度
各塔中的组分的相对挥发度和分离的难易程 度见表6-1。从沸点数据可以看出,不同碳 原子数的烃类易分,同碳原子数的烃类难分。 一般先将不同碳原子数的烃类分开,再分离 同一碳原子数的烯烃和烷烃,采取先易后难 的分离顺序。
液化气(C3+C4)烃类组分不合格原因分析及解决方法
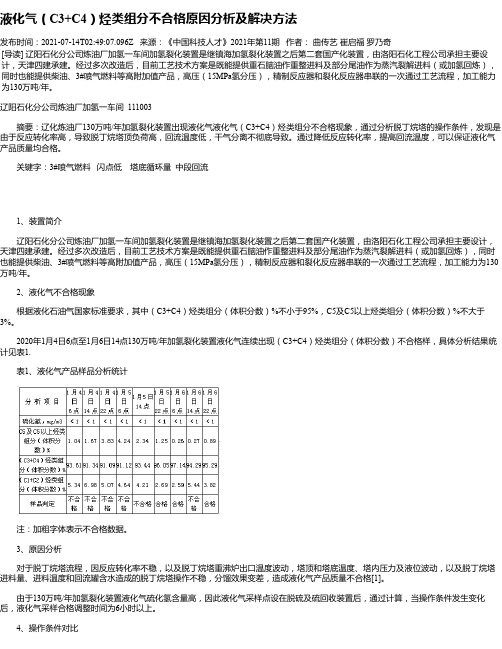
液化气(C3+C4)烃类组分不合格原因分析及解决方法发布时间:2021-07-14T02:49:07.096Z 来源:《中国科技人才》2021年第11期作者:曲传艺崔启福罗乃奇[导读] 辽阳石化分公司炼油厂加氢一车间加氢裂化装置是继镇海加氢裂化装置之后第二套国产化装置,由洛阳石化工程公司承担主要设计,天津四建承建。
经过多次改造后,目前工艺技术方案是既能提供重石脑油作重整进料及部分尾油作为蒸汽裂解进料(或加氢回炼),同时也能提供柴油、3#喷气燃料等高附加值产品,高压(15MPa氢分压),精制反应器和裂化反应器串联的一次通过工艺流程,加工能力为130万吨/年。
辽阳石化分公司炼油厂加氢一车间 111003摘要:辽化炼油厂130万吨/年加氢裂化装置出现液化气液化气(C3+C4)烃类组分不合格现象,通过分析脱丁烷塔的操作条件,发现是由于反应转化率高,导致脱丁烷塔顶负荷高,回流温度低,干气分离不彻底导致。
通过降低反应转化率,提高回流温度,可以保证液化气产品质量均合格。
关键字:3#喷气燃料闪点低塔底循环量中段回流1、装置简介辽阳石化分公司炼油厂加氢一车间加氢裂化装置是继镇海加氢裂化装置之后第二套国产化装置,由洛阳石化工程公司承担主要设计,天津四建承建。
经过多次改造后,目前工艺技术方案是既能提供重石脑油作重整进料及部分尾油作为蒸汽裂解进料(或加氢回炼),同时也能提供柴油、3#喷气燃料等高附加值产品,高压(15MPa氢分压),精制反应器和裂化反应器串联的一次通过工艺流程,加工能力为130万吨/年。
2、液化气不合格现象根据液化石油气国家标准要求,其中(C3+C4)烃类组分(体积分数)%不小于95%,C5及C5以上烃类组分(体积分数)%不大于3%。
2020年1月4日6点至1月6日14点130万吨/年加氢裂化装置液化气连续出现(C3+C4)烃类组分(体积分数)不合格样,具体分析结果统计见表1.表1、液化气产品样品分析统计注:加粗字体表示不合格数据。
催化重整装置氯腐蚀问题分析及处理方法

催化重整装置氯腐蚀问题分析及处理方法摘要:氯腐蚀是重整装置常见的腐蚀原因,这是因为氯具有很高的电子亲合力和迁移性,易与金属离子反应,且常随工艺气体向下游迁移,对设备造成严重的腐蚀并阻塞管道,严重时会导致装置被迫停工检修。
因此,研究氯腐蚀分布及防护措施对保障装置运行稳定性和操作安全性非常重要。
基于此,本文结合某催化重整装置氯腐蚀问题实例,就重整装置氯来源、腐蚀方式及分布情况进行了详细分析,并对当前主流的氯腐蚀防护技术进行了详细阐述。
关键词:催化重整装置;氯腐蚀;脱氯处理0前言重整装置是将石脑油转化为在高辛烷值汽油、芳烃及氢气等产品的关键生产装置。
氯腐蚀是重整装置常见的腐蚀原因,这是因为氯具有很高的电子亲合力和迁移性,易与金属离子反应,且常随工艺气体向下游迁移,对设备造成严重的腐蚀并阻塞管道,严重时会导致装置被迫停工检修。
因此,研究氯腐蚀分布及防护措施对保障装置运行稳定性和操作安全性非常重要。
1重整装置氯的种类及来源石脑油中氯的存在形式有无机氯和有机氯两类,其中无机氯和大部分有机氯在上游化工装置得到去除,重整装置中氯的来源有两种,一是在重整装置运行过程中,针对催化剂运行情况和生产负荷,加入全氯乙烯或甲基氯仿等有机氯化物调整催化剂的酸性功能以维持活性,二是开采原油过程中的加入了含氯助剂,这部分氯在原油中绝大部分集中在汽油馏分中,经过加氢裂化和加氢处理后随着原料进入重整装置。
2重整装置氯腐蚀分布及方式2.1预加氢部分预加氢的作用是除去原料油中的硫、氮、氯及氧等杂质以保护重整催化剂。
预加氢部分的氯腐蚀主要容易发生在预加氢反应器后,分布在换热器、蒸发塔、调节阀等处[1],主要因为在原料的加氢精制过程中,反应生成的NH3和HCl在各自分压作用下,在气相发生反应,生成NH4Cl。
NH4Cl大约在213℃时升华,低于213℃变成固体NH4Cl 沉积在金属表面,NH4Cl吸水性强,在NH4Cl垢层之下与金属接触处形成一个溶解层,发生水解反应:NH4C1→NH4+Cl-在金属表面产生盐酸,它和FeS膜争夺Fe2+,发生下列反应:FeS+HCI→FeCl2+H2SFe+HCl→FeCl2+H2盐酸破坏FeS膜,使金属表面暴露出来,新的表面继续与盐酸反应发生腐蚀,两者互相促进,加剧腐蚀,这种腐蚀体系的腐蚀速度要比单纯的HCl或H2S腐蚀更加强烈,最终导致设备因孔蚀而报废。
DHX轻烃回收工艺能耗优化研究

管理·实践/Management &Practice从天然气、凝析气或伴生气中进行轻烃回收,不仅可以提高天然气的附加值,还能降低系统能耗,优化资源配置占比。
轻烃回收是利用提高压力、降低温度使天然气中C 3及以上的重组分冷凝,再利用气液平衡原理,通过脱乙烷塔和脱丁烷塔,将液化石油气和稳定轻油脱出[1-2]。
目前,轻烃回收工艺主要有低温冷凝法和油吸收法两种,并以低温冷凝法中的DHX (直接接触法)工艺应用最为广DHX 轻烃回收工艺能耗优化研究王媛媛(大庆油田有限责任公司第五采油厂)摘要:为提高DHX (直接接触法)轻烃回收工艺的C 3收率,降低生产过程中的综合能耗,利用Hysys 软件建立轻烃回收工艺流程模型。
通过单因素影响实验确定决策变量及取值范围,利用响应面进行实验设计,得到目标函数的多元二次方程,并进行最佳工艺参数的迭代优化。
结果表明:影响C 3收率和综合能耗的单因素从强至弱依次为低温分离器温度、膨胀机出口压力、DHX 塔塔顶进料循环量和DHX 塔塔顶回流压力;交互项中只有低温分离器温度和膨胀机出口压力对响应值影响显著,其余交互项均不显著;当优化前后的综合能耗相近时,C 3收率可提高1.78个百分点,当优化前后的C 3收率相近时,综合能耗可减少109kW。
研究结果可为同类工艺流程的参数优化提供实际参考。
关键词:轻烃回收;DHX;能耗;C 3收率;Hysys DOI :10.3969/j.issn.2095-1493.2023.11.011Research on the energy consumption optimization of DHX lighter hydrocarbons recov⁃ery process WANG YuanyuanNo.5Oil Production Plant of Daqing Oilfield Co .,Ltd .Abstract:In order to improve the C 3yield of DHX lighter hydrocarbons recovery process and reduce the comprehensive energy consumption in the production process,the Hysys software is used to estab-lish lighter hydrocarbons recovery process.The decision variables and their value range are determined through the single factor experiment and the experimental design is carried out using response surfaces,which obtains the multivariate quadratic equation of the objective function and carries out the iterative optimization of the best process parameters.The results show that the single factors affecting the C 3yield and comprehensive energy consumption from strong to weak are cryoseparator temperature,out-let pressure of expander,feed circulation amount on top of DHX tower and return pressure on top of DHX tower.Among the interaction terms,only the cryoseparator temperature and the outlet pressure of the expander have significant effects on the response value,while the other interaction terms are not significant.When the comprehensive energy consumption before and after optimization is similar,the C 3yield can be increased by 1.78percentage points,and when the C 3yield is similar before and after optimization,the comprehensive energy consumption can be reduced by 109kW.The research re-sults can provide practical reference for the parameter optimization of similar process.Keywords:lighter hydrocarbons recovery;DHX;energy consumption;C 3yield;Hysys 作者简介:王媛媛,工程师,2003年毕业于东北农业大学(电子信息工程专业),从事数据库及油气集输管理工作,引文:王媛媛.DHX 轻烃回收工艺能耗优化研究[J].石油石化节能与计量,2023,13(11):47-51.WANG Yuanyuan.Research on the energy consumption optimization of DHX lighter hydrocarbons recovery process[J].Ener-gy Conservation and Measurement in Petroleum &Petrochemical Industry,2023,13(11):47-51.王媛媛:DHX轻烃回收工艺能耗优化研究第13卷第11期(2023-11)泛[3-4]。
脱丁烷塔改造及运行分析

脱丁烷塔改造及运行分析摘要:详细介绍了首套煤制烯烃项目脱丁烷塔运行原理及改造背景,结合上游原料关键组分含量和下游MTBE产品中重组分含量分析改造的必要性及设计需求,并对改造后的脱丁烷塔进行工艺参数优化,达到降低混合C4损失、满足碳四装置原料需求的目的。
关键词:脱丁烷塔改造混合C4损失重组分一、项目介绍神华包头煤制烯烃项目烯烃分离装置采用的是美国Lummus公司的前脱丙烷后加氢、丙烷洗工艺技术,将来自甲醇制烯烃装置的产品气通过三级压缩、酸性气体脱除、洗涤和干燥后,在高、低压脱丙烷塔进行初次分离。
高压脱丙烷塔顶物流经产品气四段压缩后送至脱甲烷塔,其塔顶产品主要是甲烷,经冷箱换热后得到燃料气。
高压脱丙烷塔底物流送至脱丁烷塔,得到C5以上产品和混合C4产品。
脱甲烷塔底物流送至脱乙烷塔进行C2和C3分离,塔顶C2进入乙烯精馏塔塔,塔顶产品即为聚合级乙烯产品。
塔底C3进入丙烯精馏塔,塔顶馏分便是聚合级丙烯。
聚合级的乙烯和丙烯产品分别送入聚乙烯装置和聚丙烯装置作原料,混合C4送至C4装置作为深加工原料。
同时,随着原油价格上涨、能源消费结构的变化、加工技术的进步,混合碳四作为石油化工基础原料用于生产具有高附加值的精细化工产品和合成橡胶等技术已成为石油化工研究和投资热点[1]。
因此,为了有效降低脱丁烷塔釜物料中的碳四损失,增加混合碳四产量,同时保证混合碳四质量满足下游装置原料需求,我公司经分析决定对脱丁烷塔进行改造。
二、脱丁烷塔改造1.脱丁烷塔运行原理脱丁烷塔为板式塔,塔内安装有47块塔盘,塔径1100mm,塔高为29000mm,进料口在28块塔盘上,塔顶设有热旁路调节塔压,塔釜设有蒸汽再沸器。
脱丁烷塔(160T605)从C5’s及更重的组分中分离出C4,s组分。
脱丁烷塔的进料来自低压脱丙烷塔(160T502)塔釜。
从界区外来的混合C4’s物流作为回流的补充。
脱丁烷塔顶采出C4产品送往烯烃罐区,作为碳四装置原料储备。
- 1、下载文档前请自行甄别文档内容的完整性,平台不提供额外的编辑、内容补充、找答案等附加服务。
- 2、"仅部分预览"的文档,不可在线预览部分如存在完整性等问题,可反馈申请退款(可完整预览的文档不适用该条件!)。
- 3、如文档侵犯您的权益,请联系客服反馈,我们会尽快为您处理(人工客服工作时间:9:00-18:30)。
脱丁烷塔主要将C4 和C4 以上的组分分开,
塔顶温度为45. 6 C,塔底为109. 1 C,塔顶压力
为425 Kpa,脱丁烷塔顶气体在塔顶冷凝器被工业
水冷凝后进入脱丁烷塔回流槽,凝液一部分回流,
另一部分作为C4 产品送出装置,塔底液为裂解汽
油冷却器,它与汽油解析塔塔底也一起经冷却后
送到加氢装置.DN3000*4792
精馏是化工生产中分离互溶液体混合物的典型单元操作,其实质是多级蒸馏,即在一定压力下,利用互溶液体混合物各组分的沸点或饱和蒸汽压不同,使轻组分(沸点较低或饱和蒸汽压较高的组分)汽化,经多次部分液相汽化和部分气相冷凝,使气相中的轻组分和液相中的重组分浓度逐渐升高,从而实现分离。
精馏过程的主要设备有:精馏塔、再沸器、冷凝器、回流罐和输送设备等。
精馏塔以进料板为界,上部为精馏段,下部为提留段。
一定温度和压力的料液进入精馏塔后,轻组分在精馏段逐渐浓缩,离开塔顶后全部冷凝进入回流罐,一部分作为塔顶产品(也叫馏出液),另一部分被送入塔内作为回流液。
回流液的目的是补充塔板上的轻组分,使塔板上的液体组成保持稳定,保证精馏操作连续稳定地进行。
而重组分在提留段中浓缩后,一部分作为塔釜产品(也叫
残液),一部分则经再沸器加热后送回塔中为精馏操作提供一定量连续上升的蒸气气流。