如何进行产能负荷计算
负荷计算公式

负荷计算公式一.三相用电设备组计算负荷的确定:1.单组用电设备负荷计算: P30=KdPe Q30=P30tanφS30=P30/cosφI30=S30/(1.732UN)2.多组用电设备负荷计算: P30=K∑p∑P30,i Q30=K∑q∑Q30,i S30=(P²30+Q&s u p2;30)&f r a c12;I30=S30/(1.732U N)注: 对车间干线取K∑p=0.85~0.95 K∑q=0.85~0.97对低压母线①由用电设备组计算负荷直接相加来计算时取K∑p=0.80~0.90K∑q=0.85~0.9 5②由车间干线计算负荷直接相加来计算时取K∑p=0.90~0.95 K∑q=0.93~0.973.对断续周期工作制的用电设备组①电焊机组要求统一换算到ε=100﹪,Pe=PN(εN)&fr ac12; =Sncosφ(εN)½(PN.SN为电焊机的铭牌容量;εN为与铭牌容量对应的负荷持续率;cosφ为铭牌规定的功率因数. )②吊车电动机组要求统一换算到ε=25﹪,P e=2P N(εN)&f r a c12;二. 单相用电设备组计算负荷的确定:单相设备接在三相线路中,应尽可能地均衡分配,使三相负荷尽可能的平衡.如果三相线路中单相设备的总容量不超过三相设备总容量的15﹪,则不论单相设备容量如何分配,单相设备可与三相设备综合按三相负荷平衡计算.如果单相设备容量超过三相设备容量15﹪时,则应将单相设备容量换算为等效三相设备容量,再与三相设备容量相加.1. 单相设备接于相电压时等效三相负荷的计算: Pe=3Pe.mφ( Pe.mφ最大单相设备所接的容量)2.单相设备接于线电压时等效三相负荷的计算:①接与同一线电压时P e=1.732P e.φ②接与不同线电压时P e=1.732P1+(3-1.732)P2Qe=1.732P1tanφ1+(3-1.732)P2tanφ2设P1>P2>P3,且c osφ1≠co sφ2≠co sφ3,P1接与UA B,P2接与U BC,P3接与U C A.③单相设备分别接与线电压和相电压时的负荷计算首先应将接与线电压的单相设备容量换算为接与相电压的设备容量,然后分相计算各相的设备容量和计算负荷.而总的等效三相有功计算负荷为其最大有功负荷相的有功计算负荷P30.mφ的3倍.即P30=3P30.mφQ30=3Q30.mφ5施工用电准备现场临时供电按《工业与民用供电系统设计规范》和《施工现场临时用电安全技术规范》设计并组织施工,供配电采用TN—S接零保护系统,按三级配电两级保护设计施工,PE线与N线严格分开使用。
工厂需要系数法负荷公式
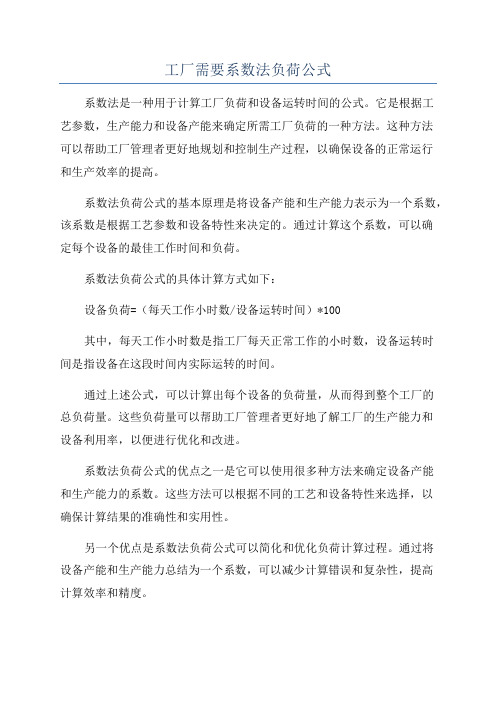
工厂需要系数法负荷公式系数法是一种用于计算工厂负荷和设备运转时间的公式。
它是根据工艺参数,生产能力和设备产能来确定所需工厂负荷的一种方法。
这种方法可以帮助工厂管理者更好地规划和控制生产过程,以确保设备的正常运行和生产效率的提高。
系数法负荷公式的基本原理是将设备产能和生产能力表示为一个系数,该系数是根据工艺参数和设备特性来决定的。
通过计算这个系数,可以确定每个设备的最佳工作时间和负荷。
系数法负荷公式的具体计算方式如下:设备负荷=(每天工作小时数/设备运转时间)*100其中,每天工作小时数是指工厂每天正常工作的小时数,设备运转时间是指设备在这段时间内实际运转的时间。
通过上述公式,可以计算出每个设备的负荷量,从而得到整个工厂的总负荷量。
这些负荷量可以帮助工厂管理者更好地了解工厂的生产能力和设备利用率,以便进行优化和改进。
系数法负荷公式的优点之一是它可以使用很多种方法来确定设备产能和生产能力的系数。
这些方法可以根据不同的工艺和设备特性来选择,以确保计算结果的准确性和实用性。
另一个优点是系数法负荷公式可以简化和优化负荷计算过程。
通过将设备产能和生产能力总结为一个系数,可以减少计算错误和复杂性,提高计算效率和精度。
然而,系数法负荷公式也存在一些局限性。
首先,它假设设备的产能和生产能力是恒定不变的,而实际情况往往是变化的。
因此,在使用该公式时需要不断调整和更新系数,以反映设备和生产能力的实际变化。
其次,系数法负荷公式只考虑了设备的负荷情况,而没有考虑到其他因素对工厂负荷的影响,例如人力资源和物料供应等。
因此,在实际应用中,需要综合考虑这些因素,以确保负荷计算的全面性和准确性。
综上所述,系数法负荷公式是一种常用的工厂负荷计算方法,可以帮助工厂管理者了解和控制设备运转时间和负荷情况。
通过合理使用该公式及其优化,可以提高工厂的生产效率和设备利用率,从而为工厂的成功运营和发展做出贡献。
生产计划负荷计算公式

生产计划负荷计算公式
一、生产计划负荷的基本概念。
生产计划负荷是指在一定的生产计划期内,生产设备、人员或工作中心等资源所承担的工作量。
它是衡量生产资源利用程度和生产任务分配合理性的重要指标。
1. 设备负荷计算。
- 设备负荷率(%)=(设备实际工作时间/设备计划工作时间)×100%
- 设备实际工作时间 = ∑(每批产品加工时间×该批产品数量)
- 例如,某设备加工一种产品,每件产品加工时间为2小时,计划生产100件产品,则设备实际工作时间 = 2×100 = 200小时。
如果设备计划工作时间为250小时,那么设备负荷率=(200/250)×100% = 80%。
2. 人员负荷计算。
- 人员负荷率(%)=(人员实际工作时间/人员计划工作时间)×100%
- 人员实际工作时间 = ∑(每个任务所需人工工时×任务数量)
- 假设一名工人完成一项任务需要5小时,计划要完成20项这样的任务,则人员实际工作时间 = 5×20 = 100小时。
如果该工人计划工作时间为120小时,人员负荷率=(100/120)×100%≈83.33%。
3. 工作中心负荷计算。
- 工作中心负荷 = ∑(产品的计划产量×产品在该工作中心的单位工时定额)
- 例如,工作中心A有两种产品经过,产品X计划产量为50件,在工作中心A的单位工时定额为3小时;产品Y计划产量为30件,单位工时定额为4小时。
则工作中心A的负荷 = 50×3+30×4 = 150 + 120 = 270小时。
车间负荷计算步骤

车间负荷计算步骤
车间负荷计算是确定车间电力需求的重要步骤,通常包括以下几个步骤:
1. 确定负荷类型:首先需要确定车间内的负荷类型,如照明、动力设备、空调、通风设备等。
不同类型的负荷具有不同的功率需求和使用特点。
2. 收集负荷数据:收集每个负荷设备的相关数据,如设备功率、使用时间、启动电流等。
这些数据可以从设备制造商的规格说明书、电气图纸或现场测量中获得。
3. 确定负荷系数:负荷系数是考虑负荷设备的实际使用情况和同时使用系数的因素。
根据车间的生产工艺和工作模式,确定每个负荷设备的同时使用系数和负荷系数。
4. 计算负荷总和:将每个负荷设备的功率乘以其对应的负荷系数,然后将所有负荷设备的计算结果相加,得到车间的总负荷需求。
5. 考虑无功功率:除了有功功率外,还需要考虑无功功率的需求。
无功功率主要用于支持电动机、变压器等感性负载的运行。
根据负荷设备的特性,确定无功功率的需求。
6. 预留容量:为了应对未来可能的负荷增长和设备扩充,通常会预留一定的容量。
根据车间的发展规划和预期增长,确定预留容量的大小。
7. 审核和验证:完成负荷计算后,需要进行审核和验证,确保计算结果的准确性和合理性。
可以与电气工程师、设备供应商或相关专业人士进行讨论和确认。
需要注意的是,车间负荷计算是一个复杂的过程,需要综合考虑各种因素。
如果你对负荷计算不确定或需要更详细的指导,建议咨询专业的电气工程师或相关技术人员。
工厂负荷计算
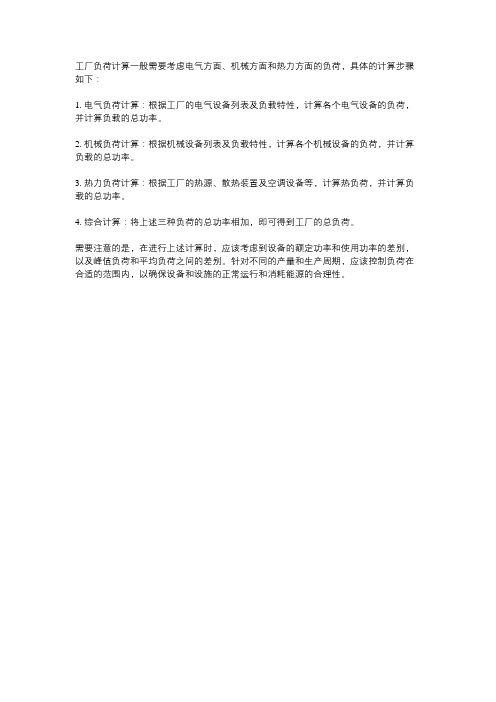
工厂负荷计算一般需要考虑电气方面、机械方面和热力方面的负荷,具体的计算步骤如下:
1. 电气负荷计算:根据工厂的电气设备列表及负载特性,计算各个电气设备的负荷,并计算负载的总功率。
2. 机械负荷计算:根据机械设备列表及负载特性,计算各个机械设备的负荷,并计算负载的总功率。
3. 热力负荷计算:根据工厂的热源、散热装置及空调设备等,计算热负荷,并计算负载的总功率。
4. 综合计算:将上述三种负荷的总功率相加,即可得到工厂的总负荷。
需要注意的是,在进行上述计算时,应该考虑到设备的额定功率和使用功率的差别,以及峰值负荷和平均负荷之间的差别。
针对不同的产量和生产周期,应该控制负荷在合适的范围内,以确保设备和设施的正常运行和消耗能源的合理性。
产能负荷计划
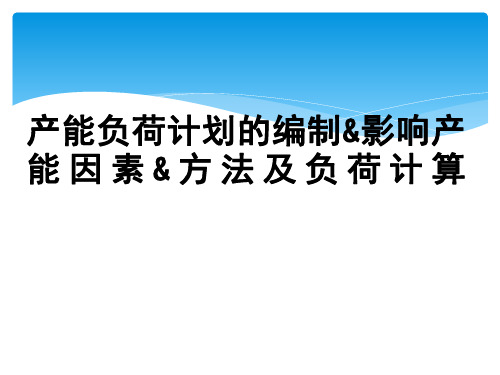
505
721
6、负荷计算
机器别负荷计划法
机器设备
1
L
2
M
3
D
产品 A B B 小计 A
B
小计 A B 小计
10
制程 1 1 3
2
2
3 4
负荷数 (9H6RS) 165 110 371 72
90
162 48 140 188
7、产能负荷计划编制
途程资料
生产年/月计划
内外订单资料
产能负荷计划
自制排程或 外包排程
产能负荷不平衡之对策
项目\判断 方式1
方式2
方式3Βιβλιοθήκη 分析产能>负荷 产能<负荷 产能=负荷
状况
淡季
旺季
平时
对策(例)
1接单 2库存法 3改善营销
13
1外包/分单 2加班 3减单 4改善
1维持 2改善
谢谢观赏
11
设备资料 人员资料
产能负荷计划表(范例)
月 份 工 作 制程名称 产能
天
(机器代号)
工比
时 率%
A
100
负荷
余力
工 比率 工 比
时%
时 率%
B B/A C
100-
B/A
工时单位:人天、人时、人分 工时:(a)产能(A)=每日可用工时×工作天数 (b)负荷(B)=标准工时×计划数量 (C)余力(C)12 =产能(A)-负荷(B)
4
3、产能分析目的
近期: 确定生产能力之现况,作为生产安排及接单交货期之决 定依据。
远期: ➢ 预估市场需求,以对长期内产能需求预做安排,并对前
置期较长的设备及机器事先规划订购。 ➢ 分析现行生产方法,利用工业工程手法,提高产能以减
负荷计算方法和步骤详解
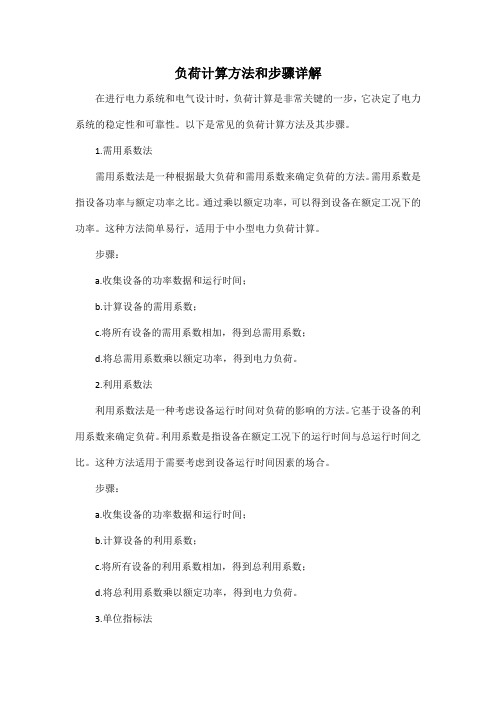
负荷计算方法和步骤详解在进行电力系统和电气设计时,负荷计算是非常关键的一步,它决定了电力系统的稳定性和可靠性。
以下是常见的负荷计算方法及其步骤。
1.需用系数法需用系数法是一种根据最大负荷和需用系数来确定负荷的方法。
需用系数是指设备功率与额定功率之比。
通过乘以额定功率,可以得到设备在额定工况下的功率。
这种方法简单易行,适用于中小型电力负荷计算。
步骤:a.收集设备的功率数据和运行时间;b.计算设备的需用系数;c.将所有设备的需用系数相加,得到总需用系数;d.将总需用系数乘以额定功率,得到电力负荷。
2.利用系数法利用系数法是一种考虑设备运行时间对负荷的影响的方法。
它基于设备的利用系数来确定负荷。
利用系数是指设备在额定工况下的运行时间与总运行时间之比。
这种方法适用于需要考虑到设备运行时间因素的场合。
步骤:a.收集设备的功率数据和运行时间;b.计算设备的利用系数;c.将所有设备的利用系数相加,得到总利用系数;d.将总利用系数乘以额定功率,得到电力负荷。
3.单位指标法单位指标法是一种根据单位面积或单位产品所需的功率来确定负荷的方法。
这种方法适用于大型建筑物或工业生产线的负荷计算。
通过将单位指标乘以面积或产量,可以确定电力负荷。
步骤:a.确定单位面积或单位产品的功率指标;b.乘以面积或产量,得到电力负荷。
4.功率平衡法功率平衡法是一种通过平衡输入和输出的功率来确定负荷的方法。
这种方法适用于电力系统中的功率平衡计算。
通过测量输入和输出的功率,可以确定电力负荷。
步骤:a.测量输入和输出的功率;b.通过比较输入和输出功率,确定电力负荷。
5.单位面积功率法单位面积功率法是一种根据单位面积所需的功率来确定负荷的方法。
这种方法适用于住宅和办公楼等建筑物的负荷计算。
通过将单位面积功率乘以面积,可以确定电力负荷。
步骤:a.确定单位面积的功率指标;b.乘以面积,得到电力负荷。
6.单位产品功率法单位产品功率法是一种根据单位产品所需的功率来确定负荷的方法。
负荷计算方法

负荷计算方法和步骤详解
负荷计算的方法:
(1)需要系数法。
用设备功率乘以系数和同时系数。
直接求出计算负荷。
这种方法比较简便,应用广泛,尤其适用于配、变电所的负荷计算。
(2)利用系数法。
采用利用系数求出最大负荷斑的平均负荷,再考虑设备台数和功率差异的影响,乘以与有效台数有关的最大系数得出计算负荷。
这种方法的理论根据是概率论和数理统计,因而计算结果比较接近实际,但因利用系数的实侧与统计较难,在民用建筑电气设什中一般不采用。
(3)二项式法。
在设备组容量之和的基础上。
考虑若干容量最大设备的影响,采用经验系数进行加权求和法计算负荷。
(4)单位面积功率法、单位指标法。
负荷计算方法一般可按下列原则选取:
①在方案设计阶段可采用单位指标法;在初步设计及施工图设计阶段,宜采用需要系数法;对于住宅,在设计的各个阶段均可采用单位指标法
②用电设备台数较多,各台设备容量相差不悬殊时,宜采用需要系数法.一般用于干线、配变电所的负荷计算;
③用电设备台数较少,各台设备容虽相差悬殊时。
宜采用二项式法,一般用于支干线和配电屏(箱)的负荷计算。
- 1、下载文档前请自行甄别文档内容的完整性,平台不提供额外的编辑、内容补充、找答案等附加服务。
- 2、"仅部分预览"的文档,不可在线预览部分如存在完整性等问题,可反馈申请退款(可完整预览的文档不适用该条件!)。
- 3、如文档侵犯您的权益,请联系客服反馈,我们会尽快为您处理(人工客服工作时间:9:00-18:30)。
如何进行产能负荷计算
产能分析主要针对产品
1、做哪些产品。
2、产品的制程。
3、每个制程的使用机器设备(设备负荷)。
4、产品的总标准时间,每个制程的标准时间(个人负荷)。
5、材料的准备前置时间。
6、生产线及他仓库需用之场所大小(场所负荷)
一般,着重于人力负荷及机器设备的能力分析。
一、人力负荷分析步骤
1 、依椐期间月的销售计划所预订的生产计划,针对各种产品的数量、标准时间,计算出生产该产品所需的人力。
标准时间又称“标准工时”。
标准时间 =实际时间×( 1+ 宽裕率)
一般的宽裕可分为:
物的宽裕:作业宽裕(清理作业台、工具不适用)。
人的宽裕:需要宽裕(上洗手间、喝水)。
疲劳宽裕(因工作疲劳降低工作速度)。
---------------------------------------------------------------
首先要确定标准工时,再确定标准产能。
标准时间的定义
所谓的标准时间,就是指在正常条件下,一位受过训练的熟练工作者,在不受外在不
良影响的条件下以规定的作业方法和用具,完成一定的质和量的工作所需的时间。
标准时间( ST)的构成=观测时间x 评比因素 +私事宽放 +疲劳宽放 +程序宽放 +特别宽放 +政
策宽放
净时间:用跑表法或其他方法进行实际观测而得到的结果(取平均值或代表值)乘以评估系数,而得到的在标准作业速度下的时间。
净时间 =具有代表性的观测时间x 评估系数
评估系数分为速读评估法、西屋法(熟练度、努力程度、工作条件、一致性四个因素)
标准时间 =观测时间x 评比率 x (1+ 宽放率 )
例如:某一单元观测时间为0.8min ,评比率为110%,宽放为5%,则
=0.8*110*(1+0.05/100)
=0.88*1.05
=0.924min
产能:是指生产设备在一定的时间内所能生产的产品数量,产能通常以标准直接工时为单位。
1 决定毛产能
假定所有的机器每周工作7 天,每天工作 3 班,每班 8 小时且没有任何停机时间,这是生产设备在完全发挥最理想的状态下的最高生产潜力。
毛产能是个理论值,它是个理想值或
者可以说是个标准参考值,作为以后计算实际产能的基准。
部门可用机器数人员编制总人数可用天数每天班数每班时数毛产能标准直接工时
车床101107381680
铣床8187381344
磨床121127382016
装配2367381008
以车床为例,可用车床有10 台,每台配置车工 1 人,总人为 10人。
按每周工作7 天,每天 3 班,每班 8 小时, 10 人 1 周毛产能标准工时为10x7x3x8=1680工时。
2决定计划产能
此计算基于每周的工作天数,每台机器排定的班数和每班的工作时数。
这是算完毛产能的进一步修正,但仍不足以代表有效产出的实际产能。
可用机器数人员编制总人数可用天数每天班数每班时数毛产能标准直接工时
部门
车床1011052101000
铣床8185210800
磨床1211252101200
装配2365210600
实际上机器每周计划开 5 天,每天 2 班,每班开10 小时,因此计划产能标准工时为10x5x2x10=1000 工时。
3决定有效产能
有效产能是以计划产能为基础,减去因停机和良率所造成标准工时损失。
良率损失,包括可避免和不可避免的报废品的直接工时。
计划标准工时工作时间目标百分比良率百分比有效产能标准直接工时部门
车床100080%90%720
铣床80095%80%608
磨床120085%90%918
装配60090%85%459
机器生产有机器检修、保养、待料等时间,实际的工作时间达不到计划时间,且生产的
产品有不良品,因此有效产能标准直接工时为1000x80 % x90% =720 工时。
人力负荷分析:
1.依据计划产量、标准工时计算所需总工时。
零件一零件二零件三总计
标准工时 5 分钟10 分钟12 分钟
计划产量1800 个1200 个600个3600 个
需要工时150 小时200 小时120小时470 小时
2.设定每周工作 6 天,每天工作时间为10 小时,则其人员需求为:
工作时间X 每周工作日)X(1 十时间宽松率)
时间宽松率 =1-工作时间目标百分比(假设为90%)= 10%
人员需求 =470÷( 10x6) X(1+ 10%) =8.6 人
总需工时÷(每人每天
机器负荷分析
1.对机器进行分类
2.计算每种机器的产能负荷
例:啤机每 6 秒成型 1 次,每次出每分钟生产80pcs
每天作业时间 =24 小时 =1440 分钟工作时间目标百分比=90%
时间宽松率 =1- 工作时间目标百分比总啤机数 =10 台
开机率 =90%
则 10 台机 24 小时总产能
=每分钟生产量X 每天作业时间÷(=80X1440÷( 1+ 10%) X10X90%8 个( 1 出 8 模),即每分钟成型10 次=10%
1+时间宽松率)X 机器台数X 开机率
=942545
即10 台啤机 24 小时总产能为 942545pcs 。
3.计算出生产计划期间,每种机器的每日应生产数
每种机器设备的总计划生产数÷计划生产日数=每日应生产数
4.比较现有机器设备生产负荷和产能调整
每日应生产数小于此机器总产能者,生产计划可执行;每日应生产数大于此种机器总产能者,需要进行产能调整(加班、增补机器或外协等)
案例练习:
1.某加工中心有 2 台设备,每天一班,每班 8 小时, 5 月份工作天数为 23 天,设备开动率为 90% ,该加工中心的设备能力为多少?
2x8x23x90%= 331.2
2.某加工件批量n=4 件,需顺序经过 4 道工序加工,各工序的单件作业时间分别为:t1=10分, t2=5 分, t3=20 分, t4=15 分,若采用顺序移动方式组织生产,则该批加工件的加工总
周期为多少?。