薄壁套类零件车削加工方法
数控技能大赛中车削薄壁零件的技巧
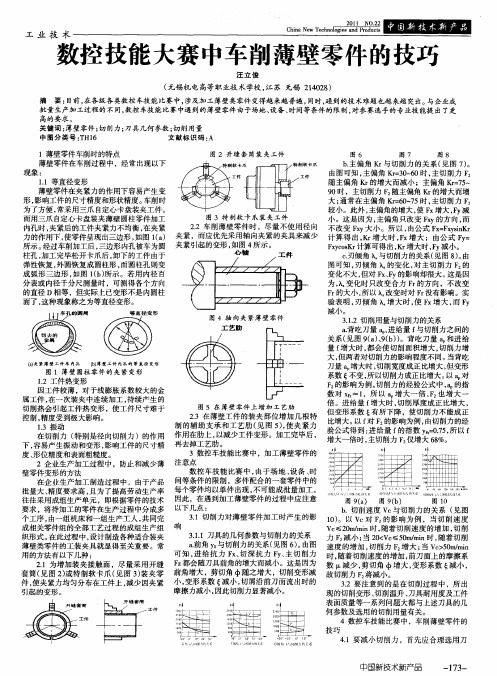
工艺肋
减小 。 31 —2切 削用 量与切 削力 的关 系
( 央g薄壁 工件 车内孔 -
( 浮壁 工件 内孔 的等直径 变形 b )
图 1 薄壁 圆柱零 件 的夹 紧变 形
1 . 件热 变形 2工 因工 件较 薄 ,对 于线 膨胀 系 数较 大 的金 属 工件 , 一次 装 夹 中连续 加 工 , 续 产生 的 在 持 切削 热会 引起 工 件热 变形 ,使 工 件尺 寸难 于 控制 , 精度 受到 极 大影 响。 1 _ 动 3振 在 切 削力 ( 别是 径 向切 削力 )的作 用 特 下 , 易产 生振 动 和变 形 , 响工件 的尺寸 精 容 影 度 、 位精 度和 表面 粗糙度 。 形 2 企业 生 产加 工过 程 中 ,防止 和减 少 薄 壁 零件 变形 的方 法 在 企业 生 产加 工制 造 过程 中 ,由于产 品 批 量大 、 要 求高 , 为 了提 高劳 动生 产 率 精度 且 往往 采 用成 组生 产 单元 ,即根据 零 件 的技术 要求 ,将 待 加工 的零 件 在 生产 过程 中分 成 多 以下几 点 : 31切 削力 对薄 壁零 件 加 工 时产 生 的影 . 个 工序 , 组 机床 和一 组 生产 工人 , 同完 由一 共 成相 关零 件组 的全部 工 艺过 程 的成 组生 产组 响 31 .1刀具 的几 何参 数 与切 削力 的关 系 . 织形 式 。 在此 过程 中 , 计 制造 各种 适合 装夹 设 a. 前角 Y与切 削力 的关 系 ( 图 6 。 。 见 ) 由图 薄壁 类零 件 的工 装 夹具 就显 得 至关 重要 。常 可 知 , 给 抗 力 F 、 深 抗 力 F 、 切 削 力 进 x切 v主 用 的方法 有 以下几 种 : z 21为增 加装 夹 接 触 面 ,尽 量 采用 开 缝 F 都会 随刀 具 前角 的增 大而减 小 。这是 因为 . 套筒( 见图 2 或特制软卡爪 ( 图 3 装夹零 前角增大 ,剪切角 巾随之增大 ,切削变形减 ) 见 ) 变形系数 ∈ 减小, 切屑沿前刀面流出时的 件 , 夹紧 力均 匀 分布 在工 件 上 , 少 因夹 紧 小 , 使 减 摩 擦 力减 小 , 因此切 削力 显著 减小 。 引起 的变形 。
典型小薄壁套类零件的加工

尽 可 能增大 刀杆截 面积 ,减少 刀具 的悬伸 长度 等 。 ( 3 ) 受力 变 形 :因工 件 壁 薄 ,在 夹 紧力 的作 用
3 4 磊
参 磊 工 。 冷 加 工
工 艺
下容 易产 生 变 形 ,从 而 影 响 工 件 的 尺 寸 精 度 和 形 状
布 的导气 孑 L 作 用 到 弹性 橡 胶 套 上 ,由弹 性 橡 胶 套 的 变形把 工件 夹 紧。夹 爪 定 位 孔 是 当 夹具 与 机 床 安 装
T 劬 岬 。 I 工 艺
典型小薄壁套类零件的加工
山 东省 泰 安 市 高 级 技 工 学校 ( 2 7 1 0 0 0 ) 焦 长 玉
小 薄壁 套 类 零 件 在 仪 表 、办 公 以及 其 他 小 型设 备 中应 用广 泛 。其 加 工难 度 大 ,主 要 原 因是 在 装 夹 和 机加 工过 程 中容 易 产 生 多 种 变 形 。本 文 对 其 变 形
减 小切 削 热 的措 施 :减 小 切 削 力 ,车 削 时 需 注 意控 制 切 削 温 度 的 升 高 ,首 先 通 过 减 小 切 削 变 形 ( 切削 力 )来 减少切 削热 的产 生 ,同时增 大刀 尖部 分
( G B / T 1 2 2 0 ) 不 锈 钢 ,难 切 削 。 内径 尺 寸 为 & 1 0~ &1 2mm,公差 只有 0 . 0 1—0 . 0 2 mm。外 径 为 + 1 4一 &1 4 . 3 mm,公 差只 有 0 . 0 2 mm。两端 内孑 L 对 称 ,各 有
好 后配 作 的。
精度 。若用 自动 定 心 卡 盘 装 夹 薄 壁 件 ,零 件 在 三 个 卡爪 夹 紧力 的作 用 下 ,产 生 变 形 ,造 成 零 件 的 网度
薄壁类零件的车削工艺分析

薄壁类零件的车削工艺分析段立波一.引言薄壁类零件指的是零件壁厚与它的径向、轴向尺寸相比较, 相差悬殊, 一般为几十倍甚至上百倍的金属材料的零件,具有节省材料、结构简单等特点。
薄壁类零件已广泛地应用于各类石油机械部件。
但是薄壁类零件的车削加工是比较棘手的,具体的原因是因为薄壁类零件自身刚性差、强度弱,在车削加工中极容易变形,很难保证零件的加工质量。
如何提高薄壁类零件的加工精度是机械加工行业关心的话题。
二.薄壁类零件车削过程中常出现的问题、原因及解决办法我们在车削加工过程中,经常会碰到一些薄壁零件的加工。
如轴套薄壁件(图1),环类薄壁件(图2),盘类薄壁件(图3)。
本文详细分析了薄壁类零件的加工特点、防止变形的装夹方法、车刀材料、切削参数的选择及车刀几何角度。
进行了大量的实验,为以后更好地加工薄壁类零件,保证加工质量,提供了理论依据。
图1轴套薄壁件图2环类薄壁件图3盘类薄壁件1.薄壁类零件的加工特点1.1因零件壁薄,在使用通用夹具装夹时,在夹压力的作用下极易产生变形,而夹紧力不够零件又容易松动,从而影响零件的尺寸精度和形状精度。
如图4所示,当采用三爪卡盘夹紧零件时,在夹紧力的作用下,零件会微微变成三角形,车削后得到的是一个圆柱体。
但松开卡爪,取下零件后,由于零件弹性,又恢复成弧形三角形。
这时若用千分尺测量时,各个方向直径相同,但零件已变形不是圆柱体了,这种变形现象我们称之为等直径变形。
图4三爪卡盘装夹1.2因零件较薄,加工时的切削发热会引起零件变形,从而使零件尺寸难以控制。
对于膨胀系数较大的金属薄壁零件,如在一次安装中连续完成半精车和精车,由切削热引起零件的热变形,会对其尺寸精度产生极大影响,有时甚至会使零件卡死在芯轴类的夹具上。
1.3薄壁类零件加工内孔中,一般采用单刃镗刀加工,此时,当零件较长时,如果刀具参数及切削用量处理不当,将造成排屑困难,影响加工质量,损伤刀具。
1.4由于切削力和夹紧力的影响,零件会产生变形或振动,尺寸精度和表面粗糙度不易控制。
薄壁套类零件车削加工方法

薄壁套类零件车削加工方法摘要:工业中广泛使用薄壁件,但是由于其加工工艺性差,在切削力、残余应力、切削热、夹紧力等因素影响下,薄壁件易发生加工变形,不易控制加工精度和提高加工效率。
本文对薄壁件加工过程中引起变形的因素进行了分析,通过改变工件的压紧方式和定位基准,设计制作工装并加工验证,得出加工薄壁件的合理工艺安排,顺利解决了工件变形问题,保证了加工质量,提高了加工效率。
关键词:薄壁套类零件车工夹具设计装夹方法一、前言航空工业中广泛使用薄壁结构零件。
薄壁零件由于其刚性好、强度高、相对重量较轻等优点,使得薄壁零件在社会中的运用越来越广泛。
薄壁零件主要是指零件的壁厚小于2mm的零件。
它们在机械加工工业中占有较大比例,薄壁套类零件因其具有重量轻、节约材料和结构紧凑等特点,广泛应用于航空领域。
此类零件结构复杂,刚度较低,加工余量大,并有很多的形位公差要求,加工中极易发生变形和切削振动,让刀现象严重,装夹和定位较困难,一直以来都是加工难点。
二、结构分析此项套类零件是用来支承旋转轴及轴承,该类零件的主要表面是内孔和外圆,其主要技术要求是内孔及外圆的尺寸以及圆度要求;内外圆之间的同轴度要求;孔轴线与端面的垂直度要求。
薄壁套类零件壁厚很薄,径向刚度很弱,在加工过程中受切削力、切削热及夹紧力等因素的影响,极易变形,导致以上各项技术要求难以保证。
针对这些问题,本文对薄壁套类零件加工过程中装夹方法做了初步的探讨。
我厂生产某项车削加工薄壁套类后盖零件,首次投入400件,生产类型为大批量。
此项零件壁厚仅为0.7mm,最薄的地方为0.5mm。
三、初次加工存在的问题我们对首批加工情况进行调查、分析和研究,投入400件,超差品181件,报废19件,合格率仅为50%。
按照原来的加工方法,先镗右端内腔及环槽,再调头车削左端圆台,夹持零件右端外圆时零件已经变形,然后用和圆台同样大小的圆环将零件小端面压紧在芯轴上,接触面小,在加工过程中旋转,零件跳动量大,装夹不牢靠。
(整理)薄壁零件车削加工方法探讨

薄壁零件车削加工方法探讨1. 薄壁零件的加工特点1.1 薄壁零件不能承受较大的径向力,用通用夹具安装困难。
1.2 薄壁零件的刚性差,在夹紧力的作用下,极易产生变形,常态下工件的弹性复原,会影响工件的尺寸精度和形状精度。
1.3 工件受切削热的影响,尺寸精度不易控制。
1.4 由于切削力的影响,工件易产生变形或振动,尺寸精度和表面粗糙度不易控制。
1.5 薄壁零件刚性差,不能采用较大的切削用量,生产效率低。
因此合理的选择装夹方法,加工方法,切削用量,减少振动及充分冷却和检测都是保证加工薄壁零件的关键。
2. 薄壁零件的装夹方法2.1 通用软爪定位装夹,选择正确的夹紧力作用点,使夹紧力作用在工件刚性较好的部位,适用于形状和尺寸公差要求不严的零件加工优点:装卸方便长度可定位,看承受较大切削力。
缺点:零件定位点较集中,零件加紧后变形较严重。
2.2 大面积扇形软爪装夹:采用扇形软爪的三爪卡盘,按与加工零件的装夹面动配合的要求,加工出卡爪的工作面,增大与零件的接触面积。
优点:增大夹紧力的作用面积,使工件支持面增大,夹紧力均匀分布在工作面上,可加大切削用量,不易产生变形。
缺点:扇形软爪不易加工。
2.3 芯棒装夹2.3.1 采用椎体芯轴装夹,将零件直接套在椎体芯轴加工。
2.3.2 采用圆柱芯轴装夹,将零件装在芯轴上采用轴线压紧。
减小零件径向变形。
优点:装卸零件方便,能保证较高的同心度,技术要求。
缺点:零件内孔被芯轴划伤。
2.4 磁力吸盘装夹:采用磁力吸盘将零件吸附在吸盘上,这时零件只受轴向力,而径向不受力。
优点:可一次较高零件内外圆。
缺点:零件找正比较麻烦,应用范围小。
3. 薄壁零件较高方法的选择3.1 先粗后精先粗加工出零件的外圆和内孔,外圆和内孔均匀留0.5 —0.8 毫米余量,端面单边留0.25 —0.3 毫米余量,然后选择适当的装夹方法,将零件精加工到图纸尺寸要求。
3.2 先内后外先加工内孔,以为孔较外圆难加工,易产生变形。
薄壁零件加工装夹方法及车削加工技巧
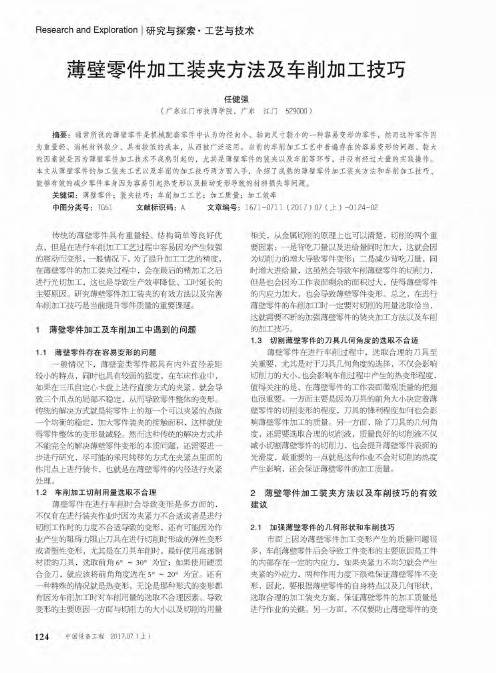
薄壁零件加工装夹方法及车削加工技巧任健强(广东江门市技师学院,广东江门529000)摘要:通常所说的薄壁零件是机械配套零件中认为的径向小、轴向尺寸较小的一种容易变形的零件,然而这种零件因 为重量轻、消耗材料较少、具有较低的成本,从而被广泛运用。
当前的车削加工工艺中普遍存在的容易变形的问题、较大 的因素就是因为薄壁零件加工技术不成熟引起的,尤其是薄壁零件的装夹以及车削等环节,并没有经过大量的实践操作。
本文从薄壁零件的加工装夹工艺以及车削的加工技巧两方面入手,介绍了成熟的薄壁零件加工装夹方法和车削加工技巧、能够有效的减少零件本身因为容易引起热变形以及振动变形导致的材料损失等问题。
关键词:薄壁零件;装夹技巧;车削加工工艺;加工质量;加工效率中图分类号:TG51 文献标识码:A 文章编号:1671-071 1(2017) 07 (上)-0124-02 Research and Exploration|研究与探索•工艺与技术传统的薄壁零件具有重量轻、结构简单等良好优 点,但是在进行车削加工工艺过程中容易因为产生较强 的震动而变形,一般情况下,为了提升加工工艺的精度,在薄壁零件的加工装夹过程中,会在最后的精加工之后 进行光切加工,这也是导致生产效率降低、工时延长的 主要原因。
研究薄壁零件加工装夹的有效方法以及完善 车削加工技巧是当前提升零件质量的重要课题。
1薄壁零件加工及车削加工中遇到的问题1.1薄壁零件存在容易变形的问题一般情况下,薄壁套类零件都具有内外直径差距 较小的特点,同时也具有较弱的强度,在车床作业中,如果在三爪自定心卡盘上进行直接方式的夹紧,就会导 致三个爪点的局部不稳定,从而导致零件整体的变形。
传统的解决方式就是将零件上的每一个可以夹紧的点做 一个均衡的稳定,加大零件装夹的接触面积,这样就使 得零件整体的变形量减轻。
然而这种传统的解决方式并 不能完全的解决薄壁零件变形的本质问题,还需要进一 步进行研究,尽可能的采用转移的方式在夹紧点里面的 作用点上进行装卡,也就是在薄壁零件的内径进行夹紧 处理。
数控车床加工薄壁零件的工艺及参数选择

数控车床加工薄壁零件的工艺及参数选择摘要:薄壁类零件本身的结构相对薄弱,加工难度较大,并且在目前数控机床操作环节,对于操作人员而言,最难的问题就是对薄壁零件的加工。
因此在设计过程中采取工装夹具等来分析具体电气设备中的支护件结构,然后利用数控车床进行加工,判断影响其加工精度的相关因素,以优化设计来促进后续加工工作顺利开展。
同时,也需注重后续加工质量的保障措施,提升薄壁类零件的加工精度。
关键词:数控车床;加工薄壁零件;工艺;参数选择引言对于在车削上具有薄壁结构的某些零件,由于零件的薄壁,在夹紧力作用下容易变形,从而影响零件的尺寸精度和形状精度。
在排程中,虽然存在工件和精加工,但工件和精加工通常是分开进行的,首先执行完整的工件加工,然后在精加工之后完成工件加工。
由于切削馀量大、切削力大、变形大,在加工过程中不一定能完全消除过度切削力所造成的变形。
由于前后厚度不同,尺寸很差,很难满足工艺要求如果在编程时合理安排毛坯和精加工路径以及合理分配加工馀量,可以解决零件变形问题的一些不良刚度。
一、薄壁零件简述薄壁零件是由厚度和内径曲率比小于5%的薄板和加强筋组成的轻元件,它们使用少量材料并产生低质量的产品。
薄壁零件的结构本身相对紧凑,硬度和刚度不足,易于在生产过程中变形和修复,这影响了薄壁零件的方向,但也影响了薄壁零件的使用效果。
薄壁零件具有特殊的尺寸和形状,即使是特殊材料,最常用的薄壁加工材料也是钛合金和复合材料,它们是在不同的生产场景和场景中制造的。
从分析薄壁零件的加工和工艺角度来看,薄壁零件的最终加工效果反映了加工等级,薄壁零件通常应用于高精度领域,加工等级直接影响下一个装配产品的质量。
从车削过程的角度来看,夹具的切削量和材料以及几何参数会影响薄壁加工的质量。
二、影响薄壁零件质量的因素分析(一)切割方式的选择切割薄壁零件时,必须选择适当的切割方法以避免影响零件过程的质量。
因此,结合薄壁零件的实际要求,应选择科学的加工方法来提高零件的切削精度。
薄壁零件的加工工艺和夹具设计

摘要:本文系统设计了薄壁零件的数控车削加工工艺。
通过探讨薄壁零件在加工中存在的易变形、零件尺寸精度、位置精度及表面粗糙度不易保证等技术问题,对加工难点进行分析,给出了加工工艺路线和加工方案,通过优化、完善夹具设计和切削参数,防止了薄壁零件加工变形、保证了较好的尺寸精度和位置精度,从而有效解决薄壁零件的车削加工难题。
由于薄壁零件刚性差、强度弱,在加工中极易变形,是零件的形位公差增大,不易保证零件的加工质量。
因此对薄壁零件的装夹,切削加工过程中刀具的合理选用及切削量的选择,提出了严格要求。
在普通车床上加工形状较复杂、有一定精度要求、且需要多把刀具进行加工的批量零件时,不仅需要频繁换刀和装夹,花费大量的人力和时间,而且加工出来的零件质量取决于加工人员的技术水平, 产品质量得不到充分的保证。
而运用数控车床,结合传统的加工工艺,不但能大大缩短加工时间、提高加工精度,而且成品率高、产品质量稳定。
所以,在运用数控机床加工过程中为保证被加工薄壁件的必要的精度,有同轴度要求的内外圆柱面或有垂直度要求的外圆与端面,尽可能在一次装夹中完成;需要编制其加工路线、合理的选择个阶段的加工参数并编写高质量的数控加工程序。
为完全保证零件的形位公差需要设计其装夹的夹具,为此,对零件图纸、零件加工及时效处理等方面都认真地进行了分析和研究。
图1-1由图1-1可看出,?64mm的外圆对?60mm的内孔的同轴度,?64的外圆的圆度和表面质量以及内孔尺寸精度的加工是该薄壁零件最主要的加工难点。
因为该零件刚性差、强度弱,在加工中极易变形,表面质量、垂直度及同轴度难以保证。
镗削内孔时应一次装夹中加工出来,以保证该零件的尺寸精度。
针对薄壁零件壁薄、刚性差、易变形的特点,可设计该薄壁零件专用夹具装夹,以保证零件的尺寸精度和形位公差达到图纸技术要求。
这些加工难点的存在,使得加工过程中刀具选择、加工工艺路线安排、工艺装夹方式确定等对于该零件是否合格非常关键。
- 1、下载文档前请自行甄别文档内容的完整性,平台不提供额外的编辑、内容补充、找答案等附加服务。
- 2、"仅部分预览"的文档,不可在线预览部分如存在完整性等问题,可反馈申请退款(可完整预览的文档不适用该条件!)。
- 3、如文档侵犯您的权益,请联系客服反馈,我们会尽快为您处理(人工客服工作时间:9:00-18:30)。
薄壁套类零件车削加工方法
摘要:工业中广泛使用薄壁件,但是由于其加工工艺性差,在切削力、残余应力、切削热、夹紧力等因素影响下,薄壁件易发生加工变形,不易控制加工精度和提高加工效率。
本文对薄壁件加工过程中引起变形的因素进行了分析,通过改变工件的压紧方式和定位基准,设计制作工装并加工验证,得出加工薄壁件的合理工艺安排,顺利解决了工件变形问题,保证了加工质量,提高了加工效率。
关键词:薄壁套类零件车工夹具设计装夹方法
一、前言
航空工业中广泛使用薄壁结构零件。
薄壁零件由于其刚性好、强度高、相对重量较轻等优点,使得薄壁零件在社会中的运用越来越广泛。
薄壁零件主要是指零件的壁厚小于2mm的零件。
它们在机械加工工业中占有较大比例,薄壁套类零件因其具有重量轻、节约材料和结构紧凑等特点,广泛应用于航空领域。
此类零件结构复杂,刚度较低,加工余量大,并有很多的形位公差要求,加工中极易发生变形和切削振动,让刀现象严重,装夹和定位较困难,一直以来都是加工难点。
二、结构分析
此项套类零件是用来支承旋转轴及轴承,该类零件的主要表面是内孔和外圆,其主要技术要求是内孔及外圆的尺寸以及圆度要求;内外圆之间的同轴度要求;孔轴线与端面的垂直度要求。
薄壁
套类零件壁厚很薄,径向刚度很弱,在加工过程中受切削力、切削热及夹紧力等因素的影响,极易变形,导致以上各项技术要求难以保证。
针对这些问题,本文对薄壁套类零件加工过程中装夹方法做了初步的探讨。
我厂生产某项车削加工薄壁套类后盖零件,首次投入400件,生产类型为大批量。
此项零件壁厚仅为0.7mm,最薄的地方为0.5mm。
三、初次加工存在的问题
我们对首批加工情况进行调查、分析和研究,投入400件,超差品181件,报废19件,合格率仅为50%。
按照原来的加工方法,先镗右端内腔及环槽,再调头车削左端圆台,夹持零件右端外圆时零件已经变形,然后用和圆台同样大小的圆环将零件小端面压紧在芯轴上,接触面小,在加工过程中旋转,零件跳动量大,装夹不牢靠。
一部分零件端面压伤,还有外圆加工成椭圆,同轴度、垂直度无法满足要求。
四、装夹方法的改进
(一)薄壁套类零件的加工分析
对于薄壁零件的加工,如果采用普通装夹方法,会产生很大的变形,无法保证加工精度。
薄壁零件加工,改进装夹方式,根据零件的结构特点制定合适、有效的装夹措施:
①采用工艺夹头装夹车削时在坯料上预留一定的夹持长度,在工件完成内孔、外圆及端面的加工后切掉,单边留余量0.5mm,然后去应力时效。
这样不但防止了工件产生太大变形,而且保证了内
孔、外圆及端面间的位置精度。
②通过增加夹压点或夹压面积减小零件的变形或使变形均匀化。
将零件的每一个点的夹紧力保持均衡,就是增大零件的装夹接触面,就能有效的减少零件的变形量。
采用软爪来装夹工件,既简单,又经济,是一种方便有效的装夹方式。
③增设辅助支承,以增强工件的刚性。
变径向夹紧为轴向夹紧,使夹紧力作用在刚度较大的轴向,避免了径向发生大的变形。
(二)车工夹具结构设计
外圆留较大的余量,采用软爪装夹外圆,先加工内孔、圆台和一个环槽端面;圆环与工件内腔壁充分接触,从而把零件撑紧,消除了径向间隙,提高了定位精度,这时零件与夹具组成一个刚性整体,再用软爪夹紧零件外圆加工左端面圆台和环槽时就不会发生变形了,利用压紧工艺凸台来固定工件,既改变了夹紧力对工件变形的影响,又起到支撑作用和吸附作用,对防止、抑制切削过程中的切削振动很有帮助;在第三道工序中采用如图6所示的夹具装夹工件加工外圆。
该夹具的芯轴上装上此前使用的圆环,拧动螺母,使其向左移动时,圆环给工件一个轴向力,在芯轴上加工出槽让位,轴向力推动工件紧紧接触芯轴端面,而芯轴外圆和端面是一次加工出来的,垂直度高,然后车削外圆台阶和端面。
该夹具使夹紧力作用在工件的左端面上,增大了接触面,减小了工件因变形而产生的加工误差,很好地保证了内外圆的同轴度要求和内孔与端面的垂直度要求。
五、使用效果
第二批投入200件,全部合格。
通过实际切削加工表明,用新设计的夹具装夹,零件变形较小,零件的同轴度、垂直度及各项尺寸的要求都能够得以保证。
刀具几何参数及切削用量的选择也较为合理,工件的各项要求均有明显的提高。
该夹具成功解决了薄壁套类零件在加工过程中容易变形的难题,降低了此类零件的废品率,提高了生产效率。