酸性镀锡光亮剂控制工艺及常见故障处理方法
镀锡故障排除
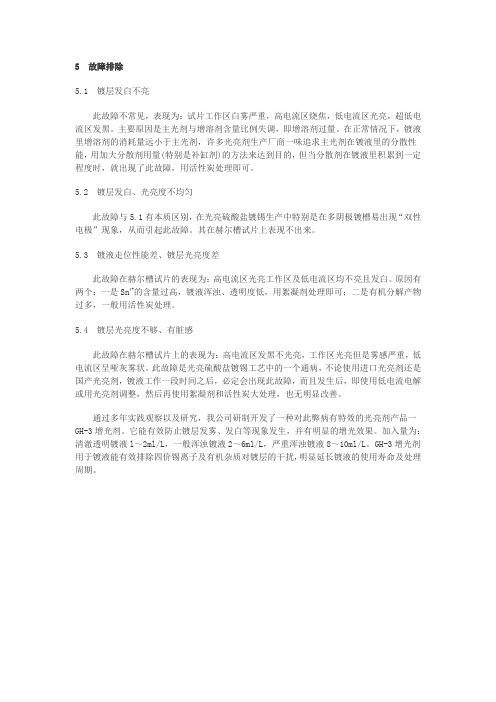
5 故障排除5.1 镀层发白不亮此故障不常见,表现为:试片工作区白雾严重,高电流区烧焦,低电流区光亮,超低电流区发黑。
主要原因是主光剂与增溶剂含量比例失调,即增溶剂过量。
在正常情况下,镀液里增溶剂的消耗量远小于主光剂,许多光亮剂生产厂商一味追求主光剂在镀液里的分散性能,用加大分散剂用量(特别是补缸剂)的方法来达到目的,但当分散剂在镀液里积累到一定程度时,就出现了此故障,用活性炭处理即可。
5.2 镀层发白、光亮度不均匀此故障与5.1有本质区别,在光亮硫酸盐镀锡生产中特别是在多阴极镀槽易出现“双性电极”现象,从而引起此故障。
其在赫尔槽试片上表现不出来。
5.3 镀液走位性能差、镀层光亮度差此故障在赫尔槽试片的表现为:高电流区光亮工作区及低电流区均不亮且发白。
原因有两个:一是Sn4+的含量过高,镀液浑浊、透明度低,用絮凝剂处理即可;二是有机分解产物过多,一般用活性炭处理。
5.4 镀层光亮度不够、有脏感此故障在赫尔槽试片上的表现为:高电流区发黑不光亮,工作区光亮但是雾感严重,低电流区呈哑灰雾状。
此故障是光亮硫酸盐镀锡工艺中的一个通病,不论使用进口光亮剂还是国产光亮剂,镀液工作一段时间之后,必定会出现此故障,而且发生后,即使用低电流电解或用光亮剂调整,然后再使用絮凝剂和活性炭大处理,也无明显改善。
通过多年实践观察以及研究,我公司研制开发了一种对此弊病有特效的光亮剂产品一GH-3增光剂。
它能有效防止镀层发雾、发白等现象发生,并有明显的增光效果。
加入量为:清澈透明镀液l~2ml/L,一般浑浊镀液2~6ml/L,严重浑浊镀液8~10ml/L。
GH-3增光剂用于镀液能有效排除四价锡离子及有机杂质对镀层的干扰,明显延长镀液的使用寿命及处理周期。
光亮镀锡故障处理方法
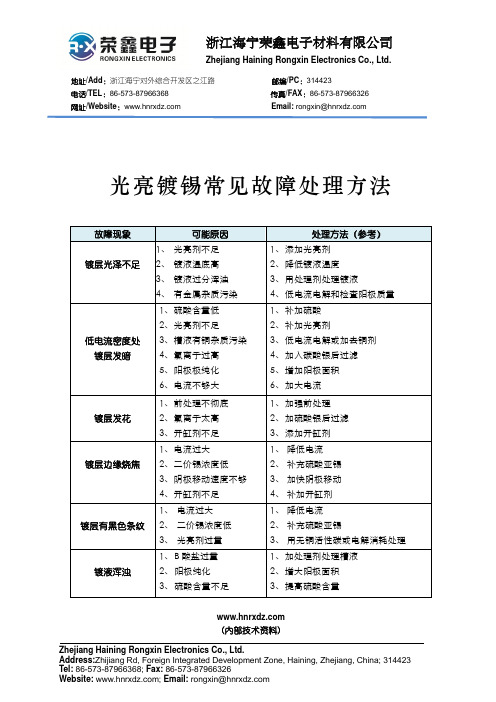
Zhejiang Haining Rongxin Electronics Co., Ltd.Address:Zhijiang Rd, Foreign Integrated Development Zone, Haining, Zhejiang, China; 314423 Tel: 86-573-87966368; Fax: 86-573-87966326Website: ; Email: rongxin@浙江海宁荣鑫电子材料有限公司 Zhejiang Haining Rongxin Electronics Co., Ltd.地址/Add :浙江海宁对外综合开发区之江路 邮编/PC :314423电话/TEL :86-573-87966368 传真/FAX :86-573-87966326 网址/Website : Email: rongxin@光亮镀锡常见故障处理方法(内部技术资料)故障现象可能原因处理方法(参考)镀层光泽不足1、 光亮剂不足2、 镀液温底高3、 镀液过分浑浊4、 有金属杂质污染 1、 添加光亮剂 2、 降低镀液温度 3、 用处理剂处理镀液4、 低电流电解和检查阳极质量低电流密度处 镀层发暗1、 硫酸含量低2、 光亮剂不足3、 槽液有铜杂质污染4、 氯离子过高5、 阳极极纯化6、 电流不够大 1、 补加硫酸 2、 补加光亮剂3、 低电流电解或加去铜剂4、 加入碳酸银后过滤5、 增加阳极面积6、 加大电流 镀层发花1、 前处理不彻底2、 氯离子太高3、 开缸剂不足 1、 加强前处理 2、 加硫酸银后过滤 3、 添加开缸剂镀层边缘烧焦1、 电流过大2、 二价锡浓度低3、 阴极移动速度不够4、 开缸剂不足1、 降低电流2、 补充硫酸亚锡3、 加快阴极移动4、 补加开缸剂镀层有黑色条纹1、 电流过大2、 二价锡浓度低3、 光亮剂过量 1、 降低电流 2、 补充硫酸亚锡3、 用无铜活性碳或电解消耗处理 镀液浑浊1、 B 酸盐过量2、 阳极纯化3、 硫酸含量不足1、 加处理剂处理槽液2、 增大阳极面积3、 提高硫酸含量。
电镀加工:酸性硫酸盐镀锡故障及其处理方法:镀层有白雾
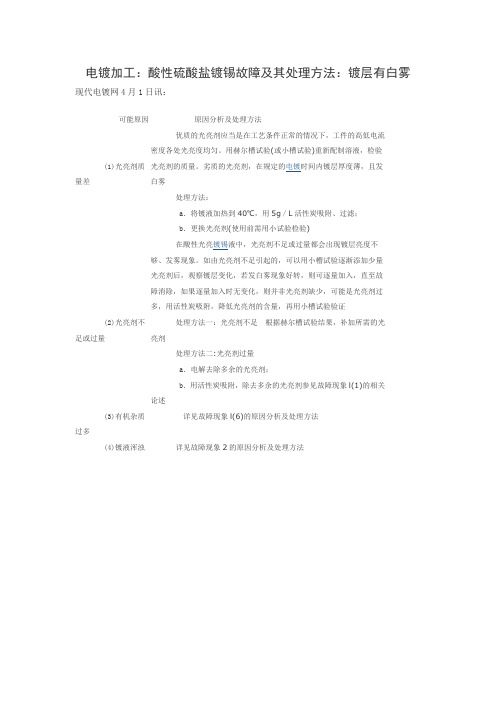
电镀加工:酸性硫酸盐镀锡故障及其处理方法:镀层有白雾现代电镀网4月1日讯:
可能原因原因分析及处理方法
(1)光亮剂质量差
优质的光亮剂应当是在工艺条件正常的情况下,工件的高低电流密度各处光亮度均匀。
用赫尔槽试验(或小槽试验)重新配制溶液,检验光亮剂的质量。
劣质的光亮剂,在规定的电镀时间内镀层厚度薄,且发白雾
处理方法:
a.将镀液加热到40℃,用5g/L活性炭吸附、过滤;
b.更换光亮剂(使用前需用小试验检验)
(2)光亮剂不足或过量
在酸性光亮镀锡液中,光亮剂不足或过量都会出现镀层亮度不够、发雾现象。
如由光亮剂不足引起的,可以用小槽试验逐渐添加少量光亮剂后,观察镀层变化,若发白雾现象好转,则可逐量加入,直至故障消除,如果逐量加入时无变化,则并非光亮剂缺少,可能是光亮剂过多,用活性炭吸附,降低光亮剂的含量,再用小槽试验验证
处理方法一:光亮剂不足根据赫尔槽试验结果,补加所需的光亮剂
处理方法二:光亮剂过量
a.电解去除多余的光亮剂;
b.用活性炭吸附,除去多余的光亮剂参见故障现象l(1)的相关论述
(3)有机杂质
过多
详见故障现象l(6)的原因分析及处理方法
(4)镀液浑浊详见故障现象2的原因分析及处理方法。
浅谈光亮酸性镀铜光亮剂及典型故障处理
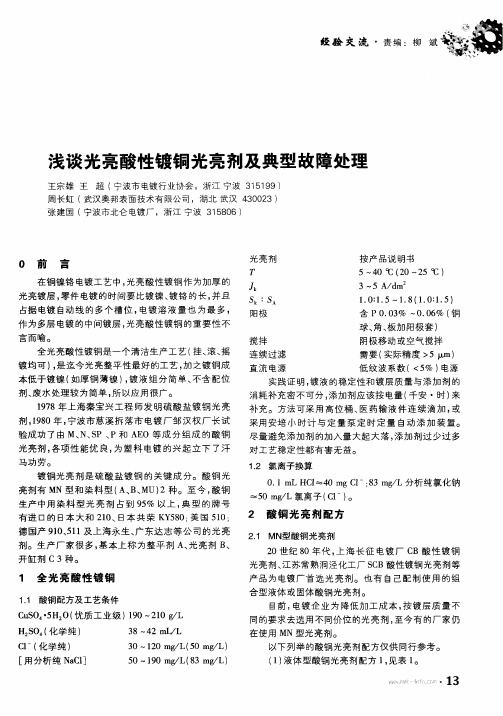
浅谈 光亮酸性镀 铜光亮剂及典型 故障处理
王宗雄 王 超 ( 宁波市 电镀行业协 会 ,浙 江 宁波 3 1 5 1 9 9) 周长虹 ( 武汉奥邦表面技术有 限公司 ,湖北 武汉 4 3 0 0 2 3) 张建国 ( 宁波市北仑 电镀 厂 ,浙江 宁波 3 1 5 8 0 6)
1 全光 亮 酸性 镀 铜
1 . 1 酸铜配方及工艺条件 C u S O 4 ・ 5 H 2 O( 优 质工 业级 ) 1 9 0— 2 1 0 g / L
H 2 S O 4 ( 化 学纯 ) C l 一 ( 化学 纯 ) 3 8— 4 2 m L / L 3 O一1 2 0 m g / L( 5 0 mg / L )
实践 证 明 , 镀 液 的稳定 性和 镀 层质 量 与添 加 剂 的 消耗 补充 密 不可 分 , 添 加剂 应该按 电量 ( 千安 ・ 时) 来
1 9 7 8年上 海秦 宝兴 工 程 师发 明硫 酸 盐镀 铜 光 亮
剂, 1 9 8 0年 , 宁波市 慈 溪拆 落 市 电镀 厂 邹 汉权 厂长 试 验成 功 了由 M、 N、 S P、 P和 A E O 等成 分 组 成 的酸 铜
开缸 剂 C 3种 。
2 0世纪 8 0年 代 , 上 海 长 征 电镀 厂 C B酸 性 镀 铜 光 亮剂 、 江苏 常熟 洞泾 化工 厂 S C B酸性 镀铜 光 亮剂等 产 品为 电镀厂 首 选 光 亮剂 。也 有 自己配 制 使 用 的组 合型 液体 或 固体 酸 铜 光亮剂 。 目前 , 电镀企 业 为 降低 加 工成 本 , 按 镀层 质 量不
光 亮剂 , 各项 性 能 优 良 , 为塑 料 电镀 的兴 起 立 下 了汗
光亮酸性镀铜常见故障分析和排除

光亮酸性镀铜常见故障分析和排除一.杂质的影响和去除1.有机杂质的处理对镀铜液中的光亮剂,通常是采取勤加、少加的原则,避免一次性加入过多的光亮剂。
如果光亮剂加入量过多,或者在镀铜液温度高时光亮剂足量,但在镀铜液冷下来后则光亮剂就显得过量了,这时的光亮剂就起到了有机杂质的影响。
在电镀零件的低电流密度区出现亮与不亮的明显分界,复杂零件的深凹处镀铜层发花,甚至镀层上有铜粉末状析出物等故障。
镀液中的光亮剂(有机杂质)如果稍多可以通过电解的方法消耗,也可以通过加入少量双氧水破坏部分光亮剂,再行调整。
但一次双氧水加入量不宜大于0.ImL/L,且应在强烈搅拌下稀释10倍以上加入。
需要注意的是双氧水对镀液中M、N光亮剂的破坏,可能会造成镀液中整体光亮剂比例的失调。
如果有机杂质过多,这时只能采取停产大处理的方法来除去镀铜液中的有机杂质。
在大处理时应注意:(1)能不加氧化剂只加活性炭吸附即可时,则尽量避免在镀铜液中加氧化剂。
因为加入的氧化剂稍不慎可能未除尽有机杂质,甚至会使后加入的光亮剂再度被破坏,短时间很难调至正常。
(2)双氧水氧化性比高锰酸钾弱,其分解产物为无害的水。
因此,非必要时,仍以加双氧水为好。
若镀铜液中双氧水稍多又急于电镀生产时,可通过加入适量的高锰酸钾来氧化破坏双氧水(此时双氧水成为还原剂),加入量由试验确定。
(3)加入氧化剂破坏镀铜液中有机杂质时,务必加热到55℃~65℃,强烈搅拌0.5h以上,否则一是氧化不彻底,二是残存物除不尽。
因此,必须备有钛质蒸汽管或电加热器用于加热。
(4)一般来讲,大处理要采用优质活性炭,在处理彻底后应补加开缸电镀的光亮剂。
但有时处理并不彻底,则应通过霍耳槽试验来决定添加开缸光亮剂还是加补充剂和加人量的多少。
2.氯离子的处理在光亮硫酸盐镀铜液中,氯离子可以降低镀铜层的应力,提高镀铜层的韧性,同时适量的Cl-离子还能提高镀铜层的光亮度和整平性,使零件的低电流密度区镀层更亮。
但它的含量过高时(≥120mg/L),就会使镀铜层粗糙,产生树枝状条纹并失去光泽等。
酸性光亮镀铜故障处理
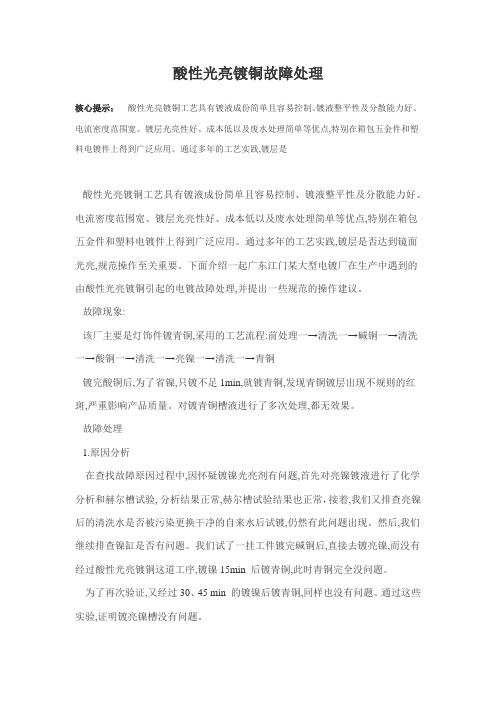
酸性光亮镀铜故障处理核心提示:酸性光亮镀铜工艺具有镀液成份简单且容易控制、镀液整平性及分散能力好、电流密度范围宽、镀层光亮性好、成本低以及废水处理简单等优点,特别在箱包五金件和塑料电镀件上得到广泛应用。
通过多年的工艺实践,镀层是酸性光亮镀铜工艺具有镀液成份简单且容易控制、镀液整平性及分散能力好、电流密度范围宽、镀层光亮性好、成本低以及废水处理简单等优点,特别在箱包五金件和塑料电镀件上得到广泛应用。
通过多年的工艺实践,镀层是否达到镜面光亮,规范操作至关重要。
下面介绍一起广东江门某大型电镀厂在生产中遇到的由酸性光亮镀铜引起的电镀故障处理,并提出一些规范的操作建议。
故障现象:该厂主要是灯饰件镀青铜,采用的工艺流程:前处理一→清洗一→碱铜一→清洗一→酸铜一→清洗一→亮镍一→清洗一→青铜镀完酸铜后,为了省镍,只镀不足1min,就镀青铜,发现青铜镀层出现不规则的红斑,严重影响产品质量。
对镀青铜槽液进行了多次处理,都无效果。
故障处理1.原因分析在查找故障原因过程中,因怀疑镀镍光亮剂有问题,首先对亮镍镀液进行了化学分析和赫尔槽试验, 分析结果正常,赫尔槽试验结果也正常,接着,我们又排查亮镍后的清洗水是否被污染更换干净的自来水后试镀,仍然有此问题出现。
然后,我们继续排查镍缸是否有问题。
我们试了一挂工件镀完碱铜后,直接去镀亮镍,而没有经过酸性光亮镀铜这道工序,镀镍15min 后镀青铜,此时青铜完全没问题。
为了再次验证,又经过30、45 min 的镀镍后镀青铜,同样也没有问题。
通过这些实验,证明镀亮镍槽没有问题。
但问题出现在哪道工序呢?我们又对镀铜进行排查口对酸性光亮镀铜液化学分析和赫尔槽试验,也没有发现什么问题,只不过赫尔槽试片显示添加剂有些过量和水线有些容易发黑而已。
再把酸性光亮镀铜槽后回收水、清洗水都更换,试镀仍然有问题。
最后我们把怀疑的焦点还是回到了酸性光亮镀铜。
对阳极进行了检查,发现表面有一层较厚的黑褐色膜,清洗后,试镀仍然不行。
酸性镀锡光亮剂控制工艺及常见故障处理方法
LHX-920酸性镀锡光亮剂控制工艺及常见故障处理方法青岛南涯电子有限公司电镀TEAM 徐宽文任常忠薛江1.前言LHX-920酸性镀锡光亮剂是由青岛大学用应技术学院谢洪波教授研制的硫酸盐镀锡光亮剂,其使用量少,工艺范围宽,而且能使镀层结晶细致光亮,镀液长期使用稳定不变色,是一种质优价廉的光亮剂。
其性能完全可以替代国外产品。
我公司主要生产弱电轻触开关镀件为铁基体上镀锡。
2000年的时候我们曾使用一种进口光亮剂,但老是出现质量问题,镀液也不稳定,在2003年的时候经过试验选择了LHX-920光亮剂,一直使用至今效果不错。
我们总结了一套适合LHX-920酸性光亮剂的最佳工艺条件及一些常见故障的处理方法,希望与电镀界同仁一起探讨。
2.工艺流程化学除油—酸洗—镀镍—活化—镀锡—中和—烘干3.配方及操作3.1化学除油目的:将粘附在待镀件表面上的油污去除,提高镀层与基体金属的结合力和保持镀液清洁。
工艺:市售一般除油剂温度:50-60℃时间:5-10分钟操作:把待镀件浸入除油液处理5-10分钟,然后用热水清洗(60-70℃)1分钟,再用流水清洗直水呈中性。
3.2酸洗目的:去除镀件表面氧化膜工艺:H2SO4: 3-5%温度:室温时间: 2-3分钟操作:把镀件浸入酸洗液中2-3分钟,注意把氧化膜完全去除。
否则可延长时间。
3.3镀镍目的:提高镀件盐雾试验工艺:NISO4: 250g/lNICL2: 50g/lH3BO3: 50g/l3.4活化目的:溶解镀件表面钝态膜,以保证镀层与基体结合力。
工艺:H2SO4: 5-7%温度:室温时间: 2分钟操作:把镀件浸入活化液中2分钟。
3.5电镀3.5.1镀液成分及工艺条件SnSO4 25-40g/LH2SO4 80-100ml/LLHX-920开缸剂 30-40ml/LLHX-920辅光剂 1-5ml/L温度 5-30℃(最佳10-25℃)电流密度 0.5-1A/dm2过滤连续阳极99.95%纯锡3.5.2 镀液的配制(1)注入3/4的纯水与洁净的镀槽内。
一次酸性硫酸盐镀锡故障处理实例
一次酸性硫酸盐镀锡故障处理实例摘要:酸性硫酸盐镀锡是一种以硫酸和硫酸亚锡为主要成分的常温镀锡工艺,配合光亮剂使用时,具有走位能力好、结晶细致、镀层光亮的特点,应用广泛。
本文结合生产实例,阐述了一种酸性硫酸盐镀锡的故障现象,分析了该故障的原因,提出了该故障的解决方法。
提出了加强工艺管理,定期做好镀液维护,以期避免或减少故障发生。
关键词:酸性硫酸盐镀锡;故障;处理方法一、引言锡具有银白色外观,无毒、柔软,容易进行钎焊,广泛应用电气电子工业、食品工业中。
电镀锡镀液可以分为酸性镀锡和碱性镀锡两大类。
碱性镀锡主要成分为锡酸钠(钾)和氢氧化钠(钾);酸性镀锡主要有硫酸盐型、甲基磺酸盐型、氟硼酸盐型等[1]。
碱性镀锡工艺需要在70~85℃下电镀,不需使用添加剂即可获得哑光的灰色锡镀层,但无法获得光亮镀层;酸性镀锡工艺需要使用光亮剂,可以在室温下获得哑光、半光或全光亮的锡镀层。
硫酸盐镀锡的工艺特点是电流效率高、镀液成分简单、成本低、工艺范围宽、镀后光亮程度高。
这些有点是其他镀锡工艺所不及的。
[2]。
我厂在使用酸性硫酸盐镀锡过程中,出现了一次典型镀液故障:在使用酸性光亮镀锡槽进行T2紫铜套管电镀锡时,发现在工艺要求的电流密度范围内镀出的镀锡层发黄、发白,镀层脆性大且带有流挂状黑色条纹,几乎无法获得合格镀层。
由于无法再进行电镀生产,只能停工处理。
二、故障原因分析导致镀锡层发黄、脆性大、带有黑条纹且难以贮存,可能的原因有镀液受到重金属杂质污染、添加剂失调、四价锡影响等。
为了准确而快速的找到故障原因,及时排除故障恢复生产,立刻到生产现场进行检查,同时取样对镀液进行了赫尔槽试验及化学分析。
(一)生产镀槽试片试验使用试片在生产镀槽上进行电镀实测。
试片采用T2紫铜板,尺寸为100mm×50mm,厚度2mm,单件表面积为1dm2。
取10个试片分为两组,每组5件。
第一组按照工艺下限电流密度电镀,另一组则按照工艺上限电流密度进行电镀,分别观察镀层状态。
光亮酸性镀铜常见故障分析和排除
光亮酸性镀铜常见故障分析和排除一.杂质的影响和去除1.有机杂质的处理对镀铜液中的光亮剂,通常是采取勤加、少加的原则,避免一次性加入过多的光亮剂。
如果光亮剂加入量过多,或者在镀铜液温度高时光亮剂足量,但在镀铜液冷下来后则光亮剂就显得过量了,这时的光亮剂就起到了有机杂质的影响。
在电镀零件的低电流密度区出现亮与不亮的明显分界,复杂零件的深凹处镀铜层发花,甚至镀层上有铜粉末状析出物等故障。
镀液中的光亮剂(有机杂质)如果稍多可以通过电解的方法消耗,也可以通过加入少量双氧水破坏部分光亮剂,再行调整。
但一次双氧水加入量不宜大于0.ImL/L,且应在强烈搅拌下稀释10倍以上加入。
需要注意的是双氧水对镀液中M、N光亮剂的破坏,可能会造成镀液中整体光亮剂比例的失调。
如果有机杂质过多,这时只能采取停产大处理的方法来除去镀铜液中的有机杂质。
在大处理时应注意:(1)能不加氧化剂只加活性炭吸附即可时,则尽量避免在镀铜液中加氧化剂。
因为加入的氧化剂稍不慎可能未除尽有机杂质,甚至会使后加入的光亮剂再度被破坏,短时间很难调至正常。
(2)双氧水氧化性比高锰酸钾弱,其分解产物为无害的水。
因此,非必要时,仍以加双氧水为好。
若镀铜液中双氧水稍多又急于电镀生产时,可通过加入适量的高锰酸钾来氧化破坏双氧水(此时双氧水成为还原剂),加入量由试验确定。
(3)加入氧化剂破坏镀铜液中有机杂质时,务必加热到55℃~65℃,强烈搅拌0.5h以上,否则一是氧化不彻底,二是残存物除不尽。
因此,必须备有钛质蒸汽管或电加热器用于加热。
(4)一般来讲,大处理要采用优质活性炭,在处理彻底后应补加开缸电镀的光亮剂。
但有时处理并不彻底,则应通过霍耳槽试验来决定添加开缸光亮剂还是加补充剂和加人量的多少。
2.氯离子的处理在光亮硫酸盐镀铜液中,氯离子可以降低镀铜层的应力,提高镀铜层的韧性,同时适量的Cl-离子还能提高镀铜层的光亮度和整平性,使零件的低电流密度区镀层更亮。
但它的含量过高时(≥120mg/L),就会使镀铜层粗糙,产生树枝状条纹并失去光泽等。
电镀工艺常见故障和处理方法
Trouble Shooting Indexz电金工艺z碳膜工艺z电铜工艺z图像转移工艺z蚀板工艺z喷锡(热风整平)工艺z线路油墨工艺z电镍工艺z有机保焊膜工艺z压板工艺z沉铜(PTH)工艺z银浆贯孔工艺z电锡工艺z湿绿油工艺一、版权说明关於这个【Trouble Shooting】软件 的版权我想一定是属於 中国PCB技术网 所有,其中如果有同行要直接引用本软件则要与我联系,一般情况下我也希望此软件 在我们同行中广泛传播!但如果要用於商业用途则我们就要认真商量一个方案了!当然这其中的文章版权就是文章和作者和来自 的不同网站!如果我转录的这些文章,相关网站或作者不允许录入到这个软件中,请与我们联系,我们会立即删除并表示道歉!二、注册说明这是一个完全免费的软件,当然我们是想知道这个软件到哪里去了!如果你想要告诉我们,请用这三种方法:1、用EMAIL与我联系。
2、在就是技术网站上留言,并留下EMAIL地址。
3、寄一封书信给我们。
无论何种方法都请写明你的姓名、职业、使用此软件的用途等等。
如果你能对此软件进行一些有建设性的 评价,那我们首先感谢!如果你使用了此软件,觉得对你有一定的帮助,想寄一点钱给我们,那我们非常感激!!三、如何联系我们EMAIL:94TECH@OICQ:9371469网址:三、特别感谢本制程TROUBLE SHOOTING的内容基本上来自己《印制电路工艺》教课书。
此教程为国家信息产业部岗位培训的指定教材。
内容丰富,适用於行业培训。
在此特别感谢!◎ Copyright©2001-2002 ◎ 版权所有©2001-2002 中国PCB技术网◎电镀金工艺◎镀金层常见故障和纠正方法故障可能原因纠正方法低电流区发雾①温度太低②补充剂不足①调整温度到正常值②添加补充剂③有机污染④PH太高③活性炭处理④用酸性调整盐调低PH中电流区发雾,高电流区呈暗褐色①温度太高②阴极电流密度太高③PH太高④补充剂不够⑤搅拌不够⑥有机污染①降低操作温度②降低电流密度③用酸性调整盐调低PH④添加补充剂⑤加强搅拌⑥活性炭过滤高电流区烧焦①金含量不足②PH太高③电流密度太高④镀液比重太低⑤搅拌不够①补充金盐②用酸性调整盐调低PH③调低电流密度④用导电盐提高比重⑤加强搅拌镀层颜色不均匀①金含量不足②比重太低③搅拌不够④镀液被Ni,Cu等污染①补充金盐②用导电盐调高比重③加强搅拌④清除金属离子污染,必要时更换溶液板面金变色(特别是在潮热季节)①镀金层清洗不彻底②镀镍层厚度不够③镀金液被金属或有机物污染④镀镍层纯度不够⑤镀金板存放在有腐蚀性的环境中①加强镀后清洗②镍层厚度不小于2.5微米③加强金镀液净化④加强清除镍镀液的杂质⑤镀金层应远离腐蚀气氛环境保存,其变色层可浸5-15%H2SO4除去镀金板可焊性不好①低应力镍镀层太薄②金层纯度不够③表面被污染,如手印④包装不适当①低应力镍层厚度不小于2.5微米②加强镀金液监控,减少杂质污染③加强清洗和板面清洁④需较长时间存放的印制板,应采用真空包装镀层结合力不好①铜镍间结合力不好②镍金层结合力不好①注意镀镍前铜表面清洁和活化②注意镀金前的镍表面活化③ 镀前清洗处理不良④ 镀镍层应力大③ 加强镀前处理④ 净化镀镍液,通小电流或炭处理◎ Copyright ©2001-2002 ◎ 版权所有©2001-2002 中国PCB技术网 ◎碳膜电路制造技术◎碳膜印制板常见故障及纠正方法序号 故障 产生原因排除方法1碳膜方阻偏高1.网版膜厚太薄2.网目数太大3.碳浆粘度太低4.固化时间太短5.固化抽风不完全6.固化温度低7.网印速度太快1.增大网膜厚度2.降低选择的网目数3.调整碳浆粘度4.延长固化时间5.增大抽风量6.提高固化温度7.降低网印速度 2碳膜图形渗展1.网印碳浆粘度低2.网印时网距太低3.刮板压力太大4.刮板硬度不够1.调整碳浆粘度2.提高网印的网距3.降低刮板压力4.调换刮板硬度3碳膜附着力差1.印碳膜之间板面未处理清洁2.固化不完全3.碳浆过期4.电检时受到冲击5.冲切时受到冲击1.加强板面的清洁处理2.调整固化时间和温度3.更换碳浆4.调整电检时压力5.模具是否在上模开槽4碳膜层针孔1.刮板钝2.网印的网距高3.网版膜厚不均匀4.网印速度快5.碳浆粘度高1.磨刮板的刀口2.调整网距3.调整网版厚度4.降低网印速度5.调整碳浆粘度6.刮板硬度不够 6.更换刮板硬度◎ Copyright©2001-2002 ◎ 版权所有©2001-2002 中国PCB技术网◎酸性电镀铜工艺◎酸性镀铜常见故障及处理故障可能原因纠正方法镀层与基体结合力差镀前处理不良加强和改进镀前处理镀层烧焦①铜浓度太低②阳极电流密度过大③液温太低④阳极过长⑤图形局部导致密度过稀⑥添加剂不足①分析并补充硫酸铜②适当降低电流密度③适当提高液温④阳极就砒阴极知5-7CM⑤加辅助假阴极或降低电流⑥赫尔槽试验并调整镀层粗糙有铜粉①镀液过滤不良②硫酸浓度不够③电流过大④添加剂失调①加强过滤②分析并补充硫酸③适当降低④通过赫尔槽试验调整台阶状镀层氯离子严重不足适当补充局部无镀层①前处理未清洗干净②局部有残膜或有机物①加强镀前处理②加强镀前检查镀层表面发雾有机污染活性炭处理低电流区镀层发暗①硫酸含量低②铜浓度高③金属杂质污染④光亮剂浓度不当或选择不当①分析补充硫酸②分析调整铜浓度③小电流处理④调整光亮剂量或另选品种镀层在麻点、针孔①前处理不干净②镀液有油污③搅拌不够④添加剂不足或润湿剂不足⑤加强镀前处理⑥活性炭处理⑦加强搅拌⑧调正或补充镀层脆性大①光亮剂过多①活性炭处理或通电消耗② 液温过低③ 金属杂质或有机杂质污染② 适当提高液温③ 小电流处理和活性炭处理金属化孔内有空白点① 化学沉铜不完整② 镀液内有悬浮物③ 镀前处理时间太长,蚀掉孔内镀层① 检查化学沉铜工艺操作② 加强过滤③ 改善前处理孔周围发暗(所谓鱼眼状镀层)① 光亮剂过量② 杂质污染引起周围镀层厚度不足③ 搅拌不当① 调整光亮剂② 净化镀液③ 调整搅拌阳极表面呈灰白色 氯离子太多 除去多余氯离子阳极钝化① 阳极面积太小② 阳极黑膜太厚① 增大阳极面积至阴极的2倍② 检查阳极含P是否太多◎ Copyright ©2001-2002 ◎ 版权所有©2001-2002 中国PCB技术网 ◎光化学图像转移(D/F)工艺◎D/F常见故障及处理(1)干膜与覆铜箔板粘贴不牢(2)干膜与基体铜表面之间出现气泡原因解决方法1)干膜储存时间过久,抗蚀剂中溶剂挥发。
- 1、下载文档前请自行甄别文档内容的完整性,平台不提供额外的编辑、内容补充、找答案等附加服务。
- 2、"仅部分预览"的文档,不可在线预览部分如存在完整性等问题,可反馈申请退款(可完整预览的文档不适用该条件!)。
- 3、如文档侵犯您的权益,请联系客服反馈,我们会尽快为您处理(人工客服工作时间:9:00-18:30)。
LHX-920酸性镀锡光亮剂控制工艺及常见故障处理方法
青岛南涯电子有限公司电镀TEAM 徐宽文任常忠薛江
1.前言
LHX-920酸性镀锡光亮剂是由青岛大学用应技术学院谢洪波教授研制的硫酸盐镀锡光亮剂,其使用量少,工艺范围宽,而且能使镀层结晶细致光亮,镀液长期使用稳定不变色,是一种质优价廉的光亮剂。
其性能完全可以替代国外产品。
我公司主要生产弱电轻触开关镀件为铁基体上镀锡。
2000年的时候我们曾使用一种进口光亮剂,但老是出现质量问题,镀液也不稳定,在2003年的时候经过试验选择了LHX-920光亮剂,一直使用至今效果不错。
我们总结了一套适合LHX-920酸性光亮剂的最佳工艺条件及一些常见故障的处理方法,希望与电镀界同仁一起探讨。
2.工艺流程
化学除油—酸洗—镀镍—活化—镀锡—中和—烘干
3.配方及操作
3.1化学除油
目的:将粘附在待镀件表面上的油污去除,提高镀层与基体金属的结合力和保持镀液清洁。
工艺:
市售一般除油剂
温度:50-60℃
时间:5-10分钟
操作:把待镀件浸入除油液处理5-10分钟,然后用热水清洗(60-70℃)1分钟,再用流水清洗直水呈中性。
3.2酸洗
目的:去除镀件表面氧化膜
工艺:
H
2SO
4
: 3-5%
温度:室温
时间: 2-3分钟
操作:把镀件浸入酸洗液中2-3分钟,注意把氧化膜完全去除。
否则可延长时间。
3.3镀镍
目的:提高镀件盐雾试验
工艺:
NISO
4
: 250g/l
NICL
2
: 50g/l
H
3BO
3
: 50g/l
3.4活化
目的:溶解镀件表面钝态膜,以保证镀层与基体结合力。
工艺:
H
2SO
4
: 5-7%
温度:室温
时间: 2分钟
操作:把镀件浸入活化液中2分钟。
3.5电镀
3.5.1镀液成分及工艺条件
SnSO4 25-40g/L
H
2
SO4 80-100ml/L
LHX-920开缸剂 30-40ml/L
LHX-920辅光剂 1-5ml/L
温度 5-30℃(最佳10-25℃)
电流密度 0.5-1A/dm2
过滤连续
阳极99.95%纯锡
3.5.2 镀液的配制
(1)注入3/4的纯水与洁净的镀槽内。
(2)连续不断的搅拌下,慢慢加入所需的硫酸量。
(3)待镀液冷却后,加入SnSO4,并不断搅拌,使其完全溶解。
(4)加入纯水到镀液容量的95%。
(5)加入LHX-920开缸剂和辅光剂
(6)过滤镀液后即可电镀。
3.5.3 LHX-920酸性光亮剂的使用及镀液的维护
镀液配置好以后,如何使用好及维护好镀液是电镀的关键。
LHX-920系列光亮剂主要有开缸剂,辅光剂二种成分组成.LHX-920开缸剂主要有光亮剂,乳化剂,扩散剂,稳定剂组成,主要是稳定镀液,扩大光亮范围,抑制析氢.辅光剂起着提高电流效率,防止镀层氧化的作用,在生产中主要使用开缸剂和辅光剂.生产中要保持这两种成分的比例,温度和电流密度一定要控制在范围内,镀液成分要定期分析,SnSO4`和H2SO4使用中限最好。
六年以来,我们使用该系列光亮剂镀层光亮,结晶细致,镀液始终清澈透明。
为了维护好镀液,镀液要连续过滤,温度尽量控制在20℃以下,每月翻一次槽,把槽底下的镀件清理干净就可以了。
使用六年来,我们从来没有用凝聚剂或活性炭处理过,大大节省了成本。
对于我们的产品,外国客户非常认可。
3.5.4 LHX-920酸性镀锡光亮剂常见故障及纠正方法
工艺:
Na3PO4 50g/l
温度50-60℃
时间 0.5-1分钟
烘干是采用离心甩干机,锡是一种低熔点金属,温度一般控制在80-100℃.
电镀工艺是电镀的关键,光亮剂的选择和使用直接关系到产品质量。
作为电镀工作者一定要不断学习,不断积累经验,加强责任心,创造更高的电镀品质。