大型客车车身结构及焊接工艺分析
大型客车车身结构及焊装工艺分析

大型客车车身结构及焊装工艺分析 大型客车车身焊装是大型客车生产中的一个重要环节,车身焊装质量是影响大型客车整体质量优劣的重要因素之一。
针对大型客车车身结构特点及其工艺性,在本文中将重点分析焊装工艺、设备、夹具的特点,总结我国大型客车车身焊装生产现状及与国际水平的差距,希望通过我们共同的努力,能不断改进国产大型客车车身焊装生产工艺,提高车身焊装质量。
大型客车车身结构特点 大型客车车身是由底骨架、左/右侧围骨架、前/后围骨架及顶围骨架等6大片骨架经组焊蒙皮而成,是一骨架蒙皮结构。
根据客车车身承受载荷程度的不同,可把客车车身概括地分为半承载、非承载、全承载式三种类型。
1、半承载式车身 半承载式车身结构特征是车身底架与底盘车架合为一体。
通过在底盘车架上焊接牛腿、纵横梁等车身底架构件,将底盘车架与车身底架进行焊接连接,然后与左/右侧骨架、前/后围骨架及顶骨架组焊成车身六面体。
车身底架与底盘车架共同承载,因此称为半承载式车身。
2、非承载式车身 非承载式车身的底架为独立焊制的,是矩形钢管和型钢焊制的平面体结构,比较单薄。
车身底架与左/右侧骨架、前/后围骨架及顶骨架组焊成车身六面体,漆后的车身要装配到三类底盘上,由底盘车架承载,因此称为非承载式车身。
3、全承载式车身 全承载式车身底架为珩架结构,由矩形钢管和型钢焊制而成,底架与左/右侧骨架、前/后围骨架及顶骨架共同组焊成车身六面体。
漆后的车身采用类似轿车的装配工艺,在车身(底架)上装配发动机、前后桥、传动系等底盘部件,因此客车已无底盘车架痕迹,完全由车身承载,因此称为承载式车身。
三种结构车身的焊装工艺性 1、半承载式车身 半承载式车身是在三类底盘上焊制的,生产中底盘自始至终要经过生产的各个环节,因此在焊装生产中也产生一些工艺问题。
如:由于底盘大大增加了车身质量,使车身在焊装线工序运输中不灵便,人工推运困难,往往需要增加机械化输送机构;此外,由于车身六面体合焊时需要在合装设备中定位底盘,为此合装设备需要设计底盘举升机构用于底盘二次定位,因此增加了合装设备造价。
12m客车车架结构设计及分析
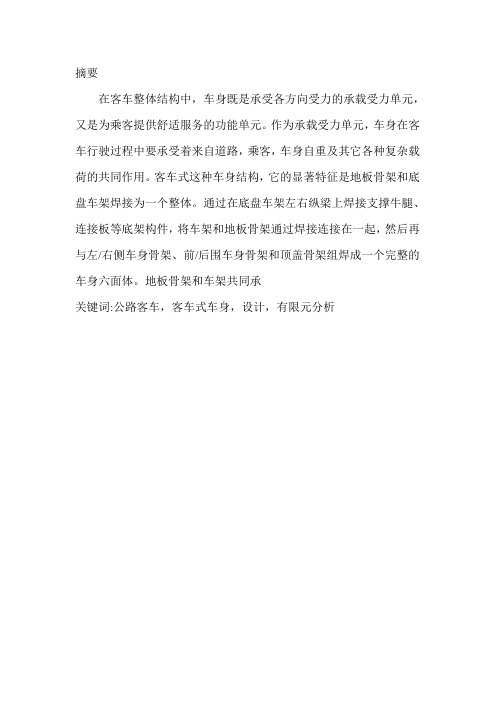
摘要在客车整体结构中,车身既是承受各方向受力的承载受力单元,又是为乘客提供舒适服务的功能单元。
作为承载受力单元,车身在客车行驶过程中要承受着来自道路,乘客,车身自重及其它各种复杂载荷的共同作用。
客车式这种车身结构,它的显著特征是地板骨架和底盘车架焊接为一个整体。
通过在底盘车架左右纵梁上焊接支撑牛腿、连接板等底架构件,将车架和地板骨架通过焊接连接在一起,然后再与左/右侧车身骨架、前/后围车身骨架和顶盖骨架组焊成一个完整的车身六面体。
地板骨架和车架共同承关键词:公路客车,客车式车身,设计,有限元分析AbstractIn the bus structure, the body is bearing unit and functional unit. As bearingunit, body in the passenger car driving to pressure from roads and other variouscomplex load role. Car many important assembly components are body for thecarrier, so the body in the whole bus system occupies very important position, thestrength and stiffness of the direct influence on the bus service life and security.As a functional unit, the body should provide the driver with convenient workingenvironment, for the crew to provide comfortable riding environment, protectthem from bus when exercising vibration, noise, exhaust gas invasion and outside harsh climate; in the traffic accident, reliable body structure and occupant protection system helps to reduce the crew and pedestrian injuries caused by. Inrecent years, with the development of society and the improvement of economicKey Words:analysis Coach bus, Semi-integral body, Design, Finite element目录第1章绪论 (4)1.1研究背景 (4)1.2研究意义 (5)1.3 UG技术的发展概况 (5)1.4客车车身技术的研究现状 (6)1.5本论文的研究内容及目标 (7)第2章车身的总体设计 (8)2.1车身的总体设计方案 (8)2.2车辆布置形式 (9)2.3车身主要尺寸的确定 (9)2.4车辆质量参数的确定 (10)第3章客车车身UG建模 (12)3.1客车式长途客车车身底架建模 (13)3.2左侧骨架总成建模 (18)第四章车身结构有限元分析 (19)4.1车身模型的简化 (19)4.2车辆载荷工况分析 (19)4.2.1水平弯曲工况分析 (19)4.2.2紧急制动工况分析 (22)4.2.3极限扭转工况(右前轮悬空)分析 (24)4.2.4极限扭转工况(左前轮悬空)分析 (25)第5章 (27)论文总结 (27)第1章绪论1.1研究背景中国客车行业从上世纪70年代中期开始起步,经过40年的不断发展和国家汽车产业重点改造,通过引进国外先进技术和合资汽车企业,目前拥有自主研发新车型的能力。
客车车身焊接工艺及焊装质量的控制措施

客车的结构包括车身、底盘、内饰、动力总成和电气设备等,其中车身又分为承载式和非承载式两种。
车身不仅承载部分部件,而且对整车的防水、防尘具有重要作用。
车身包含蒙皮和骨架,主要制造工艺是焊接。
因此,焊接工艺的质量直接影响车身质量和整车性能。
1 客车车身焊接工艺的特点客车作为汽车的一种,在我国划归为商用车范畴,在制造工艺上与乘用车区别较大。
1.1 客车产品结构客车根据用途不同主要分为公路客车和公交客车。
公路车目前较多采用承载式和半承载式车身,公交车多采用非承载式车身。
其中,承载式车身由于要承载大多数部件的重量,地面的振动也会直接传递到车身,因此对底架和车身骨架的焊接质量要求很高,对底架和车身的防腐处理要求也较高。
车身由蒙皮和骨架结合而成,蒙皮多用冷轧钢板、铝板或钢板-增强塑料制成。
骨架大多用型材或冲压件焊成桁架结构。
侧面的蒙皮大多经预张拉后焊于骨架,可以提高车身的强度和刚度,并可减少车身内外板的空腔共振。
1.2 客车车身焊接工艺特点客车作为商用车范畴,在销售上与乘用车区别较大。
销售订单会根据客户的需求对基本型进行修改,如更改发动机,座位种类、数量,空调品牌、车窗结构等。
由于订单主要基于客户的需求,每个订单涉及的车型或多或少都要修改基本型车型图纸,所以客车的制造无法做到大批量生产。
大多数车型都是小批量或个性订制,在生产制造上自动化程度低,人工生产装配占主要比例。
因此,车身焊接生产更是需要大量的焊接工人参与,在焊接工艺的规范上和质量把控上尤为重要。
焊接方式上,多采用CO2气体保护电弧焊和电阻焊。
2 客车车身焊装制造工艺2.1 车身骨架的焊装车身骨架的焊装是骨架从构件到部件再到总成的制造过程。
车身骨架由前后围骨架、左右侧围骨架、顶盖骨架和底架六大片构成,如图1所示。
焊装先从分总成的组焊开始,将散件组焊成六大片分总成。
骨架零件一般由制件车间制作,并运至焊装车间待用。
图1 车身骨架车身骨架只起到支撑、承载作用。
客车制造工艺技术

客车制造工艺技术客车制造工艺技术是指在客车制造过程中所需要运用的一系列技术和工艺方法。
客车作为一种大型交通工具,不仅要求具备良好的外观和性能,更需要在制造过程中保证车辆的质量、安全和耐久性。
本文将从车体制造、焊接工艺和喷漆工艺等方面介绍客车制造的工艺技术。
首先,车体制造是客车制造过程中一项重要的工艺环节。
传统的车体制造通常采用钢板冲压、焊接和组装的方式完成。
现代客车制造中,为了降低车体重量、提高车辆性能,常常使用轻量化材料如铝合金和复合材料。
钢板冲压是将平板钢料通过模具冲压成所需形状,然后再进行折弯和弯曲等工艺,最后通过焊接方法将各零部件连接成一体。
钢板冲压工艺技术的精准性和效率对于车体制造至关重要。
其次,焊接工艺是客车制造过程中的核心技术之一。
焊接是将金属材料通过热的方式进行熔合,实现零部件的连接。
在客车制造中,常用的焊接方法包括手工电弧焊、气体保护焊、激光焊等。
这些焊接方法各有优缺点,选用合适的焊接方法需要根据材料的种类、厚度和组合结构等因素进行综合考虑。
焊接工艺对车体质量和结构强度具有重要影响,必须严格按照规范和标准进行操作。
最后,喷漆工艺是客车制造过程中的一项重要环节。
喷漆不仅是美观的体现,更是对车身进行保护的一道屏障。
客车的喷漆工艺要求颜色均匀、光亮度高、抵抗腐蚀和耐久性好。
喷漆工艺包括表面处理、底漆涂装和面漆涂装等环节。
表面处理是保证涂层附着力和外观质量的关键,底漆涂装是为面漆提供承载和保护作用,而面漆涂装则是最终的外观效果呈现。
喷漆工艺需要严格控制温度、湿度和喷漆厚度等参数,以及遵循环保要求和安全操作规程。
综上所述,客车制造工艺技术是一个综合性强、环节众多的过程。
车体制造、焊接工艺和喷漆工艺都是客车制造中的重要环节,对车辆的外观和性能都有重要影响。
在客车制造过程中,必须严格按照相关规范和标准进行操作,以保证客车质量和安全性。
未来随着技术的不断创新和发展,客车制造工艺技术也将迎来新的突破和进步。
客车车身焊接工艺及焊装质量的控制措施

客车车身焊接工艺及焊装质量的控制措施一、客车车身焊接工艺:客车车身焊接工艺是指在焊接过程中所采用的具体方法和步骤。
正确的焊接工艺可以确保焊接质量,提高车身的强度和耐久性。
常见的客车车身焊接工艺包括下列几种:1. 电弧焊接:电弧焊接是一种常用的焊接方法,通过电弧的热量将焊条和工件熔化并连接起来。
在客车车身的焊接过程中,常使用电弧焊接法进行连接和固定。
2. 气体保护焊接:气体保护焊接是一种在焊接过程中使用保护气体的焊接方法,常使用惰性气体如氩气来保护熔化的金属,防止氧化和污染。
3. 焊接变形控制技术:在客车车身焊接过程中,经常会出现焊接变形的问题,主要是由于热应力引起的。
通过采用适当的焊接变形控制技术,可以有效降低焊接变形的程度。
二、焊装质量的控制措施:1. 选用合适的焊接设备:选择适合的焊接设备是确保焊装质量的首要步骤。
合适的焊接设备可以提供稳定的焊接工艺参数和高质量的焊接效果。
2. 控制焊接材料的质量:焊接材料的质量对焊装质量有很大影响。
在选择焊接材料时,应根据客车车身的材料特性和焊接要求进行选择,并确保焊接材料符合相应的标准和规范。
3. 控制焊接工艺参数:焊接工艺参数是影响焊接质量的重要因素。
通过合理调整焊接电流、电压、焊接速度等参数,可以控制焊接过程中的热量输入和焊接强度,提高焊接质量。
4. 焊接过程监控:焊接过程监控是对焊装质量进行有效控制的重要手段。
通过采用焊接过程监控技术,可以对焊接过程中的温度、应力、变形等进行实时监测和控制,及时发现并修正焊接缺陷。
5. 焊接质量检测:焊接质量的检测是确保焊装质量的重要环节。
采用合适的检测方法和设备,对焊接接头的外观、尺寸、成分和性能等进行全面检测,及时发现焊接缺陷并采取相应的措施进行修正。
6. 定期维护和保养:为保证焊装质量的稳定性和可靠性,需要定期维护和保养焊接设备和工具。
定期对焊接设备进行检修、维护和校准,确保焊接设备的性能和稳定性。
通过正确的焊接工艺和焊装质量的控制措施,可以提高客车车身的焊接质量,确保车身的强度和耐久性,提高客车的安全性和舒适性。
浅析客车车身焊接技术

浅析客车车身焊接技术摘要介绍客车常用的焊接方法,概述了CO2气体保护焊的工艺要求、过程检测及控制措施。
关键词客车;焊接;CO2气体保护焊焊接是客车结构的一种重要的,常用的连接方式。
要保证车身骨架牢固可靠、外观光滑平整,关键在于焊接操作时,要注意焊接方法与材料、焊前准备、焊接要求及参数、焊接过程检测与控制。
1 焊接方法与材料客车常用的焊接方法可分为手工电弧焊、气体保护焊、钨极氩弧焊和电阻焊等;气体保护焊又分为CO2气体保护焊、混合气体保护焊、惰性气体保护焊。
常见的焊接方法与材料及使用范围见表1。
CO2气体保护焊具有高效、节能等优点,是客车车身最常用的焊接方法,下面以CO2气体保护焊为主介绍下焊接工艺。
2 焊前准备2.1 焊接前要对焊接设备工具,材料进行检查:检查焊接设备、辅助设备是否齐全、完好,数字显示稳定、调节灵活、安全可靠等;焊件尺寸及规范是否符合图纸要求及工艺标准;检查焊接材料是否符合工艺要求;焊机及附属设备确保电路、水路、气路和机械装置正常运行。
2.2 焊接前需对焊接位置表面进行清理:清除焊件焊口10~20mm范围内表面的铁锈、油污、水分、灰尘、氧化皮及因手弧焊点表面的焊渣等影响焊接质量的杂质;清除焊件焊口毛刺。
2.3 检查作业环境:CO2焊接区域的风速限制在1.0m/s以下、相对湿度大于90%的环境下;没有挡风措施不能施焊。
3 焊接要求及参数3.1 焊接要求(1)零部件必须经过首件检验符合产品图纸要求后方可批量进行焊接。
(2)多层多道分段焊缝时,每道焊缝之间应错开30~40mm,焊缝收弧不得在拐角急剧转弯处、焊缝交叉处以及焊缝端头等易引起应力集中的地方。
(3)焊件时的定位焊要求:①先点后焊,先对接焊缝后角焊缝,型钢管焊接应先角缝再平缝。
②所用焊条或焊丝与正式焊接所用的焊条或焊丝相同。
③形状对称构件,焊缝应对称排列,交叉焊缝处不应有定位焊,至少远离交叉点50mm。
④保证定位焊强度要求,焊点应尽量短小,距离尽量大;焊缝长度小于400mm定位焊为两点,焊缝长度大于400mm定位焊间距为300mm。
客车车身焊接工艺及焊装质量的控制措施

客车车身焊接工艺及焊装质量的控制措施车身焊接是制造客车的关键工艺之一,焊接质量的好坏直接影响到车身的强度、刚度和安全性能。
为了确保车身焊接的质量,需要采取一系列的控制措施。
下面将详细介绍客车车身焊接工艺及焊装质量的控制措施。
要选择合适的焊接工艺。
客车车身一般采用电弧焊接,常见的有手工电弧焊、气体保护焊和激光焊等。
首先要确定焊接工艺的适用性和效果,选择适合的焊接材料和焊接电流,确保焊接接头的质量。
要控制焊接参数。
焊接参数包括焊接电流、焊接电压、焊接速度和焊接时间等。
不同的焊接接头要根据材料的厚度和接头的形状来确定合适的焊接参数。
要根据焊接规范和工艺要求,确保焊接参数的准确性和一致性。
要保证焊接材料的质量。
焊接材料是保证焊接质量的重要因素之一。
要选择合适的焊条和焊丝,确保其质量符合标准要求。
要储存和保管焊接材料,避免受潮和受污染,保证其使用效果和焊接质量。
要重视焊接设备的维护和保养。
焊接设备的正常运行对焊接质量的稳定性和可靠性有很大影响。
要定期检查焊接设备,确保其正常工作。
要对焊接设备进行维护和保养,保持其良好的状态。
要加强员工的培训和技术指导。
焊接工艺的控制离不开员工的技术水平和操作能力。
要对焊接人员进行培训,提高其焊接技术和操作技能。
并加强技术指导,定期检查和评估员工的焊接质量,及时纠正不良操作和不合格品。
客车车身焊接工艺及焊装质量的控制措施包括选择合适的焊接工艺、控制焊接参数、保证焊接材料的质量、维护焊接设备和加强员工培训等方面。
通过这些措施的综合应用,能够有效提高客车车身焊接的质量和安全性能。
客车车身焊接工艺及焊装质量的控制措施

客车车身焊接工艺及焊装质量的控制措施随着客车产业的不断发展,车身的生产技术和工艺不断提升,焊接工艺也逐步成为客车生产的重要组成部分之一。
客车的车身焊接质量直接影响到车辆的安全性和使用寿命,因此需要一系列的控制措施来确保焊接工艺和焊装质量的达到标准。
一、客车车身焊接工艺的选择合理的焊接工艺是保证焊接质量的基础。
针对不同车身部位、材料以及设计要求,客车生产厂家需要选择适当的焊接工艺,包括手工电弧焊、气体保护焊、等离子弧焊、激光焊等多种形式的焊接工艺。
同时,还需要考虑其他因素,如零部件的材料和结构、焊接成本、焊接设备的性能和质量等。
二、焊接设备的选用和维护高质量的焊接设备是焊接工艺的基础。
客车生产厂家需要选择高质量的焊接设备,并根据不同部位和要求选择不同的焊接设备。
例如,在一些需要高精度的部位,需要使用激光焊接设备。
另外,还需要对设备进行定期的维护和保养,确保其正常运转和稳定性。
三、焊接材料的选择正确的焊接材料也是保证焊接质量的重要因素。
客车生产厂家需要根据焊接部位的材料和性能要求选择合适的焊接材料,并进行严格的质量控制。
例如,在高强度车身焊接中,需要选择与基材相匹配的高强度焊接材料,并进行相应的试验和检测,保证其材料性能和焊接质量。
四、焊接过程中的控制措施在焊接过程中,需要严格控制焊接参数,避免产生缺陷和质量问题。
同时还需要进行定期的焊接试验和检测,避免焊接缺陷和问题的产生。
除此之外,还需要实行全面的质量控制措施,如样板制作、工艺标准化、成品检测等,确保焊接质量符合国家和企业要求。
总之,客车车身的焊接工艺和焊装质量控制需要在各个环节进行严格管理和控制,确保焊接质量达到高水平。
针对不同的部位和要求,应选择合适的焊接工艺、设备和材料,并进行严格的焊接参数控制和质量检测。
而且,客车生产厂家还需要建立完善的质量管理制度和体系,确保焊接质量保证,为用户提供高质量的产品和服务。
- 1、下载文档前请自行甄别文档内容的完整性,平台不提供额外的编辑、内容补充、找答案等附加服务。
- 2、"仅部分预览"的文档,不可在线预览部分如存在完整性等问题,可反馈申请退款(可完整预览的文档不适用该条件!)。
- 3、如文档侵犯您的权益,请联系客服反馈,我们会尽快为您处理(人工客服工作时间:9:00-18:30)。
非承载式车身底架结构较简单,是由各种矩形钢管和型钢焊制的平片式结构。
可采用翻转夹具或卧式固定夹具焊接。
翻转夹具焊接操作方便、节省面积,而且由于是在夹具中完成正反面焊接,因此焊接变形小,但夹具的制造费用较高。
全承载式车身底架为格栅式空间结构,夹具均采用固定式。
为保证与左/ 右侧骨架的装配精度,焊后底架众多的端头需要有淮确的装配尺寸。
生产中采用两种办法加以保证:
一种是提高零件下料尺寸精度和焊装夹具制造精度,焊后辅以少量的手工磨削,使之达到装配精度要求;另一种是采用行走式自动切割机完成此项工艺。
后一种方法生产效率高,但设备投资较大。
□车身六大片骨架组焊是客车车身焊装生产中的关键工序。
该工序不仅决定着客车车身六面体的装配尺寸精度,而且也是制约车身焊装线生产率的咽喉工序。
为提高装配精度及生产效率,国内外先进的客车厂均采用专用合装设备一次完成车身六面体定位组焊成型。
该设备由车身底架定位机构、左/ 右侧骨架夹紧机构、前/ 后围定位机构、顶围吊运装置及动力系统组成。
根据承载车身的运输机构是否从合装设备中间通过,该类设备可分为通过式和非通过式两种。
通过式合装设备的结构相对复杂,其底架定位机构由整体式工艺车和举升机组成。
整体式工艺车是加工精度很高的底架夹紧定位、运输机构,其上面的定位装置可调,可满足不同尺寸的底架定位要求。
整体式工艺车承载着底架进人合装设备初定位后,由举升机将工艺车举起进行二次定位。
当完成车身六面体组焊后,合装设备回位,举升机回落。
若底架结构差别较大,如非承载、半承载、全承载式车身混线生产,可采用不同的工艺车。
因此,通过式合装设备能够满足各种类型大客车车身组焊需要。
缺点是设备投资较大。
非通过式合装设备的底架定位机构是固定在合装设备中间的平台式结构,其与车身底架的接触面大,车身底架受力均衡,因此特别适合于底架刚度差的车身骨架组焊,如非承载式车身组焊。
非通过式合装设备的结构较通过式的简单,因此造价低。
缺点是车型适应性相对较差,如:
不适合半承载式车身组焊;底架高度差别较大时,车身高度方向的装配基
准线(Z/0)调整不便等。
车身骨架合装设备具有一定的生产柔性。
通过在合装设备上同时设计布置几种车「型的夹紧机构(为避免相互千涉,有些可设计成摆动式),可以进行伺系列不同车型混线生产。
此外,合装设备的左/右侧各夹头安装在横向滑槽上,可左右调整,横向滑槽又可沿纵向滑槽上下调整,通过,调整各夹头的位置或更换部分夹头,可以生产更多种车型,但这种调整工作量很大,仅能分期分批生产,不适合混流生产。
2、左/右侧蒙皮及前/后围蒙皮
□左/右侧蒙皮
大型客车左/右侧蒙皮一般采用预应力蒙皮工艺,通过将侧蒙皮钢板张拉到预定长度后焊接到侧骨架上,使钢板内保持一定的残余拉应力。
预应力蒙皮可使蒙皮平整美观,运行鼓噪小,能显著提高车身骨架的刚性和强度。
根据钢板内残余应力形成机理的不同,预应力蒙皮分为热应力蒙皮和拉应力蒙皮两种。
□热应力蒙皮
热应力蒙皮是通过在钢板上通以低电压大电流的电,使钢板发热伸长(电热延伸率约为1%。
),然后迅速焊接在侧骨架上。
冷却后钢板收缩,使之张紧挺直。
热应力蒙皮设备由变压器、工艺架、导电机构组成,其占地面积小,投资
该工艺主要优点是:
钢板受热后沿纵横双向膨胀,冷却后蒙皮内的残余应力为双向应力,可使
车身受力更均衡由于钢板是受热膨胀,可不受车身外形是曲线还是直线的限制;生产柔性好、效率高。
缺点是对工艺要求比较严格,如:
拉伸质量易受人为因素的影响,关闭电源后,焊接操作必须迅速,否则钢板降温过大,延伸率降低,焊后残余应力值过小,影响拉伸效果;控制不当会造成过热引起钢板氧化等。
□拉应力蒙皮
拉应力蒙皮又可分为手工张拉和机械张拉两种
手工张拉是采用夹紧器和丝杠,靠人工的力量拉伸钢板,拉力较小,拉伸后钢板弹性变形
不大,残余拉应力较小,对车身整体刚度及强度提高不大,但对改善蒙皮外观质量、降低鼓噪声仍能取得一定的效果。
机械张力蒙皮是用机械张拉机将钢板拉伸到预定的长度(延伸率为1%。
),再焊接到侧骨架上的工艺方法。
机械张拉机主要由液压系统、电控系统、前/后拉伸架体组成。
该工艺主要优点是拉伸质量稳定、操作方整的缺陷,因此拉伸前对钢板平整度要求不高,可直接采用卷材拉伸;拉伸架体可沿轨道做较大范围的移动,适合不同长度的车身侧蒙皮机械张拉蒙皮因本身工艺条件宽松,适应性强,能最大限度地满足用户的使用要求,已成为国内外大中型客车厂首选的侧蒙皮装配工艺。
考虑侧蒙皮的美观性,侧蒙皮与侧骨架之间的连接一般以电阻点焊为主,
co2 弧焊为辅。
□前/后围蒙皮
大型客车前/ 后围蒙皮件有钢板冲压件和玻璃钢件两种。
钢板冲压件蒙皮一般采用若干块冲压件进行拼焊,这是由于前/后围蒙皮件形状较复杂,外形尺寸又大,若采用大块钢板冲压成型需购置大台面的冲压设备及模具,由于产量所限使得生产成本过高。
焊接工艺采用电阻点焊工艺或co2 弧焊工艺,在蒙皮板搭接处辅以铜钎焊工艺。
co2 弧焊对产品结构适应性强,但焊后工件变形较大,增加了修磨及调整工作量,生产效率低;电阻点焊工艺焊接变形小、生产效率高,但要求蒙皮与骨架要有良好的贴合面,由于前/ 后围蒙皮及骨架结构较复杂、空间曲线度大,对许多设计及加工不十分严格的产品来说这一点很难做到,这也是影响电阻点焊工艺在前/ 后围蒙皮中应用的主要原因。
玻璃钢蒙皮是将整块模压成型的玻璃钢件通过粘接胶贴敷到前/ 后围骨架上,并通过预埋在玻璃钢中的连接角铁与左/ 右侧骨架、顶骨架和底骨架焊接(或螺接)在一起。
采用玻璃钢件可获得整块大曲面度的前/ 后围蒙皮,其造型美观,安装操作方便,劳动强度小,生产效率高,因而在客车生产中用的较普遍。
3、车身焊装线运输方式
大型客车车身焊装线工位间运输方式根据产量的不同,可以采用人工推动、地面链拖动、板式带和滑橇运输系统等几种形式。
人工推动工艺车的运输方式劳动强度较大,但因其组织生产非常灵活,不需要运输设备
投资,在国内客车广中应用很普遍。
地面链输送设备结构简单,易于制造和维修。
缺点是线上各工位需做不同步移动时需要工人钻到车身下脱挂钩,因此组织柔性生产不方便。
由于设备投资少,在较大型客车厂中应用仍比较多。
板式带与地面链相比,不需要工艺车,可省去工艺车回位的麻烦,但投资较大,国内客车厂应用的很少。
滑橇运输系统是大型客车车身焊装线最先进的机械化输送方式,该系统使得工位间纵向和横向转移更加方便灵活,便于工艺布置及生产管理。
系统由PC 机控制,各工位可同步或不同步移动,因此易于组织柔性生产。
其缺点是设备投资大,一般中小型客车厂因资金所限难以采用。
4、焊装工艺流程
传统的大型客车车身焊装工艺流程为:
六大片骨架预制T车身六面体组焊T补焊T焊装各种小件T修磨焊缝、骨架校正、局部补涂底漆T (焊装内蒙皮T)焊装左/右侧蒙皮T焊装前/后围蒙皮T 研装各种门类件T 送涂装车间进行车身面漆。
这种工艺流程的特点是:
在车身焊装过程中,基本不搀加涂装工艺,仅在焊缝处手工补涂快干底漆。
目前国内绝大多数客车厂仍沿用这种工艺流程。
国内少数客车厂通过技术引进对传统的工艺流程进行了改造。
其工艺流程为:
六大片骨架预制T车身六面体组焊T补焊T焊装各种小件T修磨焊缝、骨架校正T骨架整体前处理T (焊装内蒙皮T内蒙皮前处理T)焊装左/右侧蒙皮T 焊装前/后围蒙皮T 研装各种门类件T送涂装车间进行车身面漆。
这种工艺流程的特点是:
车身焊装工艺和涂装工艺相互交叉。
这种混合流程不仅使在骨架焊装生产中破坏的底漆层得到彻底补涂,而且彻底清除了焊接操作过程中工人无意中涂抹在车身上的油污、汗水等污
渍,可显著提高车身防腐蚀性能、提高面漆的附着力。
据有关资料统计,国外大型客车底盘使用寿命为15 年,车身使用寿命仅为
10 年,而国内客车使用寿命更低。
因此,提高车身防腐性能越来越受到重视。
在车身焊装生产环节中间增加前处理生产工艺,是提高车身防腐性能的有效措施。
结束语
综上所述,大型客车车身结构按其承载程度可分为三种类型:
半承载、非承载及全承载式。
三种结构车身对焊装生产工艺的要求略有不同。
掌握客车车身结构和焊装工艺特点,以及国内外在车身焊装工艺、装备及材料方面存在的差距,对搞好客车焊装工艺设计,不断消化吸收国外的先进技术,提高国产大型客车车身焊装质量至关重要。