包钢常用铁矿粉烧结基础特性
(完整word版)烧结原料介绍
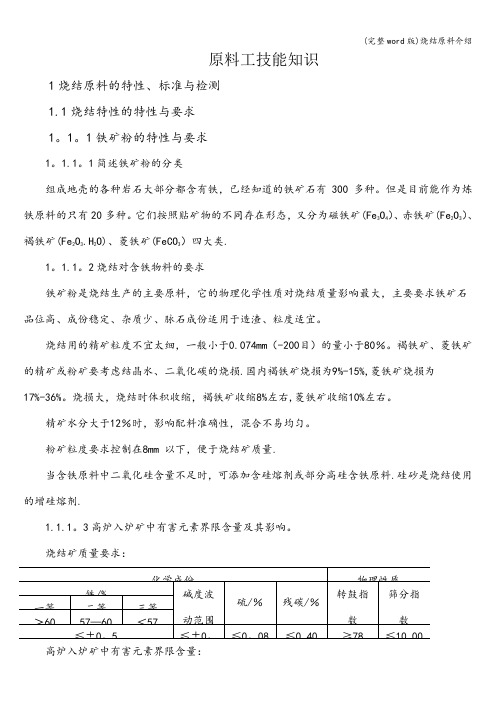
原料工技能知识1烧结原料的特性、标准与检测1.1烧结特性的特性与要求1。
1。
1铁矿粉的特性与要求1。
1.1。
1简述铁矿粉的分类组成地壳的各种岩石大部分都含有铁,已经知道的铁矿石有300多种。
但是目前能作为炼铁原料的只有20多种。
它们按照贴矿物的不同存在形态,又分为磁铁矿(Fe3O4)、赤铁矿(Fe2O3)、褐铁矿(Fe2O3.H2O)、菱铁矿(FeCO3)四大类.1。
1.1。
2烧结对含铁物料的要求铁矿粉是烧结生产的主要原料,它的物理化学性质对烧结质量影响最大,主要要求铁矿石品位高、成份稳定、杂质少、脉石成份适用于造渣、粒度适宜。
烧结用的精矿粒度不宜太细,一般小于0.074mm(-200目)的量小于80%。
褐铁矿、菱铁矿的精矿或粉矿要考虑结晶水、二氧化碳的烧损.国内褐铁矿烧损为9%-15%,菱铁矿烧损为17%-36%。
烧损大,烧结时体积收缩,褐铁矿收缩8%左右,菱铁矿收缩10%左右。
精矿水分大于12%时,影响配料准确性,混合不易均匀。
粉矿粒度要求控制在8mm 以下,便于烧结矿质量.当含铁原料中二氧化硅含量不足时,可添加含硅熔剂或部分高硅含铁原料.硅砂是烧结使用的增硅熔剂.1.1.1。
3高炉入炉矿中有害元素界限含量及其影响。
烧结矿质量要求:高炉入炉矿中有害元素界限含量:1。
1。
2熔剂的特性与要求1。
1.2.1熔剂的分类熔剂可分为碱性熔剂、酸性熔剂和中性熔剂三类。
我国铁矿的脉石多以SiO 2为主,所以普遍使用碱性熔剂。
碱性熔剂即含CaO 和MgO 高的熔剂。
常用的熔剂有:石灰石(CaCO 3)生石灰(CaO )、消石灰(Ca(OH)2)和白云石(主要是CaCO 3和MgCO 3)。
1.1。
2。
2熔剂的要求碱性氧化物含量要高;S 、P 杂质要少;酸性氧化物含(SiO 2+Al 2O 3) 越低越好;粒度和水分适宜。
①有效熔剂性高:即碱性氧化物CaO+MgO 含量要高,而酸性氧化物SiO 2含量要低。
评价熔剂品质的重要标准,是根据烧结矿碱度要求,扣除本身酸性氧化物所消耗的碱性氧化物成分,所剩余的碱性氧化物的含量而确定的。
冶金性能与基础特性

冶金性能与基础特性附1:铁烧结矿、球团矿的冶金性能序号冶金性能名称符号表示概念描述标准1还原度(900℃)RI 还原性指用还原气体从铁矿石中排除与铁相结合的氧的难易程度的一种量度。
2还原速率指数RVI 从还原曲线读出还原达到30%和60%时相对应的还原时间(min)。
我国以3h的还原度指数RI作为考核用指标,还原速率指数RVI作为参考指标。
测定标准为GB/T13241-91“铁矿石还原性的测定方法”。
RI≥72%3低温还原粉化率(500℃)RDI指高炉含铁原料(如烧结矿、块矿、球团矿)在高炉上部较低温度下被煤气还原时,主要由于赤铁矿向磁铁矿转变,体积膨胀,产生应力,从而导致粉化的程度。
低温还原粉化率是烧结矿重要的冶金性能指标之一。
还原粉化指数(RDI)表示还原后的铁矿石通过转鼓试验后的粉化程度,分别用RDI+6.3、RDI+3.15、RDI-0.5表示。
试验结果评定以RDI+3.15的结果为考核指标,RDI+6.3、RDI-0.5只作参考指标。
RDI+3.15≥72%RDI-3.15<28%4荷重还原软化性能T BST BEΔT B反映炉料加入高炉后,炉身下部和炉腰部位透气性的,这一部位悬料和炉腰结厚往往是由于炉料的荷重软化性能不良所造成的,故这一性能对高炉冶炼也显得比较重要。
T BS>1100℃ΔT B=T BE-T BS<150℃5熔融滴落性能ΔT=Td-TsΔPmaxS值铁矿石的熔融滴落性能简称熔滴性能,它是反映铁矿石进入高炉后,在高炉下部熔滴带的性状的,由于这一带的透气阻力占整个高炉阻力损失的60%以上,熔滴带的厚薄不仅影响高炉下部的透气性,它还直接影响脱硫和渗碳反应,从而影响高炉的产质量,因此它是铁矿石最重要的冶金性能。
Ts>1400℃ΔT=Td-Ts<100℃ΔPmax<180×9.8PaS值≤40Kpa·℃6还原膨胀性能RSI 还原膨胀性能是球团矿的重要冶金性能,由于氧化球团的主要矿物组成为Fe203,Fe203还原为Fe304过程中有个晶格转变,即由六方晶体转变为立方晶体,晶格常数由5.42埃增至8.38埃,会产生体积膨胀20%~25%,Fe304还原为Fe0过程中,体积膨胀可为4%~11%。
铁矿粉基础性能及其在烧结优化配矿中的应用
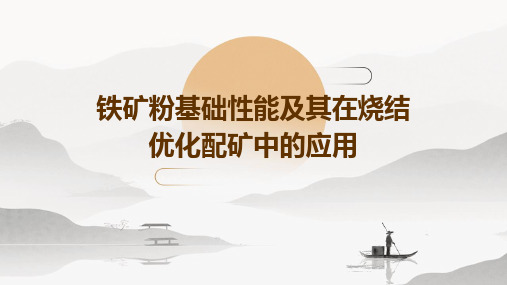
04
铁矿粉在烧结优化配矿中的 研究进展
铁矿粉基础性能的研究进展
铁矿粉的化学成分
随着分析技术的进步,对铁矿粉的化 学成分研究更加深入,尤其是微量元 素的检测和分析,有助于更精确地评 估铁矿粉的质量和潜在价值。
铁矿粉的物理性能
物理性能的研究包括粒度分布、密度 、硬度等,这些因素直接影响铁矿粉 在烧结过程中的反应性和混合性能。
铁矿粉在烧结优化配矿中的理论研究进展
烧结反应动力学
通过建立烧结反应动力学模型,研究 不同成分的铁矿粉在烧结过程中的反 应速率和机理,为优化配矿提供理论 依据。
混合料相组成与性能
研究不同铁矿粉对混合料相组成和性 能的影响,包括液相形成、固相反应 等,有助于揭示铁矿粉在烧结过程中 的作用机制。
铁矿粉在烧结优化配矿中的实践应用进展
铁矿粉基础性能及其在烧结 优化配矿中的应用
目录
• 铁矿粉基础性能 • 铁矿粉在烧结优化配矿中的作用 • 铁矿粉在烧结优化配矿中的实践
应用 • 铁矿粉在烧结优化配矿中的研究
进展 • 结论与展望
01
铁矿粉基础性能
铁矿粉的物理性质
01
02
03
密度
铁矿粉的密度是衡量其质 量的重要指标,密度越大, 单位体积的矿粉质量越大。
有害元素含量
如铅、汞、砷等有害元素 应严格控制其含量,以确 保生铁的安全直接影响烧结 矿的透气性和强度,粒度过小会 导致烧结矿强度降低,过大则会 影响透气性。
粒度分布
理想的粒度分布可以提高烧结矿 的质量和产量,粒度分布过于集 中或分散都不利于烧结。
02
铁矿粉的粒度选择与调整对烧结工艺具有重要影响,合适的粒度分布可以提高烧 结矿的质量和产量。
青钢烧结用铁矿粉基础性能研究

中图分 类号 :TF041
文献标识 码 :A
文章编号 :1004—4620(2016)01—0035—04
一 如 ∞ ∞ %
C一—~ o∞L m n m 舛 L L n L n 鼹
1 前 言
的同化 性 能 、液 相 生 产 特性 、升 温过 程 烧损 和结 晶 水 分解 特 性 、微 观 结 构进 行 试 验研 究 ,以此 为 基 础
青钢烧 结用铁 矿粉基础 性能研 究
杨 小建 ,安秀伟 ,孙宝芳
(青钢集 团银钢炼铁有 限公 司,山东 青 岛 266043)
摘 要 :以青 钢现用的 6种铁矿粉为研究对 象 ,采用微型烧结法试验分析 测试了矿粉的 同化性能 、液 相生 成特性 、烧损和结 晶水 分解特性 、微观结构特性等基础性能。结果表 明,6种铁矿粉 同化性 能和液 相流动性都 较好 ;杨迪粉的烧损值和结晶水
青 钢为 典 型 的沿海 型钢 铁企 业 ,借助 沿 海优 良 港 口的地 域优 势 和交通 运输 优 势 ,着 力发 展 以进 口
探讨 各铁 矿粉 的使 用原 则 ,为 青钢优 化 配矿。结㈣构 及 ㈣ ㈣哪
改善烧 结矿质量 提供技 术支持 。
s— 一L m rL 加 rL rL rL 加 rI
较低 ,结 晶水 含量较 高 ;巴粗粉 SiO 含量介 于纽曼 粉 一 o 0 0 0 4 n 3 ∞ n
业 总成本 。
和超 特 粉 之 间 ,属 于 赤 铁 矿 ,含 有 少 量 K、Na等 元
采用 微 型烧结 法对青 钢 近期使用 的 6种 铁矿 粉
素 ,粒度 较粗 。各种铁矿 粉 的化 学成分见 表 1。 一m 肿 0 m m 肿
收 稿 日期 :2015—09—25 作者 简介 :杨 小建 ,男 ,1980年生 ,2007年毕业 于哈尔滨师范大学地 理科 学专业 。现 为青 岛钢铁 集团银 钢炼铁技术 科烧结 工 艺主管 , 工程师 ,从事烧结配矿及烧结工艺技术工作 。
铁矿粉烧结基础特性的新方法探索

铁矿粉烧结基础特性的新方法探索$杜晓东吴铿朱春恩黄德军徐大安(北京科技大学冶金与生态工程学院)摘要顺应科学研究由“静态”到“动态”的客观发展规律,在铁矿粉与CaO同化反应前 期研究中,充分利用试验所获得的不同信息,由冶金物理化学和冶金传输原理中的基本原理,建立不同信息之间的内在联系,给出表征不同信息总体内涵的同化反应特征数。
拟将该研究的新思路和方法加以应用,确定铁矿粉流动特征数和粘结相强度特征数,进而建立研究铁矿粉烧结基础特性的新方法,为建立铁矿粉性价比的评价体系及烧结配料提出指导性的建议。
关键词铁矿粉烧结基础特性特征数评价体系Exploration of new method for sintering basic characteristicsof iron ore powderDu Xiaodong Wu Keng Zhu Chunen Huang Dejun Xu Daan(University of Science and Technology Beijing)Abstract Following the law of development of scientific research from “static” to “dynamic,,,through assimilation reactions between iron ore powder and CaO, making full use of various information obtained from experiment and physical chemistry and transport principle of metallurgy, the inherent relationship of various information and characteristic number for fully characterizing different phenomenon in sintering were established. And then the fluidity characteristic and intensity of binding phase characteristic can be established through application of this new idea and methods, also the new methods for evaluating the basic sintering characteristic can be established. Moreover, this new method can provide suggestion to the evaluation system for iron ore and ore matching.Keywords iron ore powder sintering basic characteristics characteristic number evaluation sys-国内钢铁产能严重过剩,国家已决定逐年降 低产量。
国外铁矿粉烧结基础特性及优化配矿研究
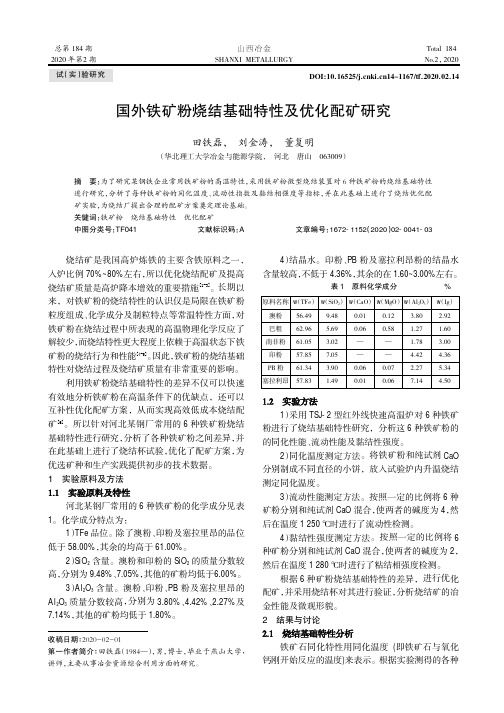
关键词:铁矿粉 烧结基础特性 优化配矿
中图分类号:TF041
文献标识码:A
文章编号:1672-1152(2020)02-0041-03
烧结矿是我国高炉炼铁的主要含铁原料之一, 入炉比例 70%~80%左右,所以优化烧结配矿及提高 烧结矿质量是高炉降本增效的重要措施[1-3]。长期以 来,对铁矿粉的烧结特性的认识仅是局限在铁矿粉 粒度组成、化学成分及制粒特点等常温特性方面,对 铁矿粉在烧结过程中所表现的高温物理化学反应了 解较少,而烧结特性更大程度上依赖于高温状态下铁 矿粉的烧结行为和性能[4-5]。因此,铁矿粉的烧结基础 特性对烧结过程及烧结矿质量有非常重要的影响。
根据 6 种矿粉烧结基础特性的差异,进行优化 配矿,并采用烧结杯对其进行验证,分析烧结矿的冶 金性能及微观形貌。 2 结果与讨论
收稿日期:2020-02-01 第一作者简介:田铁磊(1984—),男,博士,毕业于燕山大学, 讲师,主要从事冶金资源综合利用方面的研究。
铁矿石同化特性用同化温度 (即铁矿石与氧化 钙刚开始反应的温度)来表示。根据实验测得的各种
南非粉、澳粉、巴粗均为赤铁矿,而南非粉同化 能力最强,澳粉、巴粗同化温度相当,主要是因为南 非粉中 SiO2 比较适中,利于铁酸钙的生成,而澳粉 及巴粗中 SiO2 含量过高,将会使 SiO2 与 CaO·Fe2O3 中发生反应,把 Fe2O3 置换出来,生成高熔点硅酸二 钙,抑制铁酸钙的生成,从而使澳粉和巴粗同化性变 差。对于澳粉和巴粗而言,主要是因为巴粗铁矿粉中 MgO 含量较高,促进赤铁矿分解成磁铁矿,不利于铁 酸钙生成,从而相应地提高了同化温度。因此,南非 粉、澳粉、巴粗三种粉同化能力的高低为:南非粉跃澳 粉>巴粗。
铁矿粉烧结过程基础理论
铁矿粉烧结过程基础理论序言:在学习配料技术之前把烧结的基础理论知识和工艺特点温习一遍。
这是学习烧结配料技术的基础,要完全掌握、理解透彻。
铁矿粉烧结是整个钢铁冶炼长流程的首道综合性生产环节,从工艺生产的角度来讲,钢铁冶炼是从铁矿粉烧结开始的,以下简称烧结。
烧结是生产人造富矿的最主要的方法。
(高碱度烧结矿+酸性球团矿是现今我国最流行的高炉冶炼方法。
)将铁精粉(国内磁铁贫矿经过破碎、浮选和磁选)、富矿粉、钢铁冶炼生产中回收的含铁较高的粉末类副产品(高炉和转炉炉尘、轧钢铁皮、高品位钢渣粉等)、熔剂(白云石、菱镁石、石灰石和生石灰等)和燃料(焦粉和无烟煤),按一定比例配料,加水混合制成具有一定粒度的混合料,均匀平铺在烧结台车上,经过点火抽风烧结成块。
再经过破碎、筛分,加工成具有一定强度和粒度组成的人造富矿的过程叫做-烧结。
一、烧结生产的意义1、烧结生产是一种人造富矿的制作方法,这种方法使地壳中大量的低品位铁矿加工成人造富铁矿,用以满足高炉冶炼优质、高产、低耗的冶炼需要。
2、烧结生产中可以应用转炉炉尘、高炉炉尘、轧钢皮、钢渣等钢铁冶炼副产品和硫酸渣等化工副产品,这些废料在烧结过程中得到充分地再利用,做到变废为宝,为企业带来节能环保和降低原料成本的双重效益。
3、烧结生产的烧结矿和天然富矿块相比,更适合高炉冶炼的需要。
主要表现在:成分稳定、粒度适中、低温还原粉化率低、炉内的热强度和整体还原度良好、造渣流动性好。
这些特性使得高炉冶炼更容易调节炉况、稳定生产、提高产量和降低焦比。
4、烧结过程可以除去原燃料中90%以上的硫化物和80%以上的氟化物等钢铁冶炼的有害杂质,大大地简化了后续钢铁冶炼流程中脱硫脱氟等去杂质的工艺,不仅调升了产品质量,而且也极大地降低了钢铁冶炼成本。
二、烧结生产过程1、烧结工艺流程大多数人开始学习烧结工艺的时候,首先学习的就是工艺流程图,我们去某个地方参观或者学习时,也必先熟悉那里的工艺流程图。
铁矿石烧结性能PPT课件
铁矿石烧结性能结果
生成液相粘结周围物料的能力
浸润面积 (%)
800 700 600 500 400 300 200 100
0
哈默斯利 BHP
扬迪矿 卡拉加斯 伊特贝拉 MBR
MMTC 南非矿
铁矿石烧结性能结果
铁矿石烧结性能结果
铁矿石与CaO的反应、生成铁酸钙的性能
50
40
R=1.80
R=2.00
百分比 (%)
30
20
10
0
哈默斯利
BHP
扬迪矿 卡拉加斯 伊特贝拉
MBR
MMTC
不同碱度条件下,进口矿生成能力的比较
南非矿
铁矿石烧结性能结果
铁矿石与CaO的反应、生成铁酸钙的性能
影响铁矿石与CaO的开始反应温度的因素: 铁矿物的种类、结晶水的含量、致密度、
铁矿物以疏松的赤铁矿和褐铁矿为主, 则反应能力较强;而以致密的磁铁矿或 镜铁矿为主,则反应能力较弱。
影响铁矿石与CaO的开始反应
温度的因素:
结晶水的含量
铁矿石与CaO的开始反应温度与结晶水 的含量呈正相关关系。
结晶水含量高,分解后产生大量的气 孔,加大了反应接触面,有利于Ca2+向 矿石的扩散,同时有利于铁矿物离子的 扩散。另一方面,结晶水分解后,铁矿 物的活性增加,均有利于铁矿石与与 CaO的加速进行。
结晶水含量高,烧结过程中要分解,使 得粘结相中可能存在残留气孔,表现出脆弱 的粘结相结构。
影响铁矿石粘结相强度的因素
5.铁矿石的脉石成分
铁矿石的脉石成分Al2O3和SiO2对粘结相 的自身强度的影响有两面性。
冶金性能与基础特性
附1:铁烧结矿、球团矿的冶金性能序号冶金性能名称符号表示概念描述标 准1还原度(900℃)RI还原性指用还原气体从铁矿石中排除与铁相结合的氧的难易程度的一种量度。
2还原速率指数RVI 从还原曲线读出还原达到30%和60%时相对应的还原时间(min)。
我国以3h的还原度指数RI作为考核用指标,还原速率指数RVI作为参考指标。
测定标准为GB/T13241-91“铁矿石还原性的测定方法”。
RI≥72%3低温还原粉化率(500℃)RDI指高炉含铁原料(如烧结矿、块矿、球团矿)在高炉上部较低温度下被煤气还原时,主要由于赤铁矿向磁铁矿转变,体积膨胀,产生应力,从而导致粉化的程度。
低温还原粉化率是烧结矿重要的冶金性能指标之一。
还原粉化指数(RDI)表示还原后的铁矿石通过转鼓试验后的粉化程度,分别用RDI+6.3、RDI+3.15、RDI-0.5表示。
试验结果评定以RDI+3.15的结果为考核指标,RDI+6.3、RDI-0.5只作参考指标。
RDI+3.15≥72%RDI-3.15<28%4荷重还原软化性能T BST BEΔT B反映炉料加入高炉后,炉身下部和炉腰部位透气性的,这一部位悬料和炉腰结厚往往是由于炉料的荷重软化性能不良所造成的,故这一性能对高炉冶炼也显得比较重要。
T BS>1100℃ΔT B=T BE-T BS<150℃5熔融滴落性能ΔT=Td-TsΔPmaxS值铁矿石的熔融滴落性能简称熔滴性能,它是反映铁矿石进入高炉后,在高炉下部熔滴带的性状的,由于这一带的透气阻力占整个高炉阻力损失的60%以上,熔滴带的厚薄不仅影响高炉下部的透气性,它还直接影响脱硫和渗碳反应,从而影响高炉的产质量,因此它是铁矿石最重要的冶金性能。
Ts>1400℃ΔT=Td-Ts<100℃ΔPmax<180×9.8PaS值≤40Kpa·℃6还原膨胀性能RSI 还原膨胀性能是球团矿的重要冶金性能,由于氧化球团的主要矿物组成为Fe203,Fe203还原为Fe304过程中有个晶格转变,即由六方晶体转变为立方晶体,晶格常数由5.42埃增至8.38埃,会产生体积膨胀20%~25%,Fe304还原为Fe0过程中,体积膨胀可为4%~11%。
铁矿粉化学成分对烧结高温基础特性的影响靳加亮王思思
铁矿粉化学成分对烧结高温基础特性的影响靳加亮王思思发布时间:2023-05-30T14:46:58.255Z 来源:《科技新时代》2023年6期作者:靳加亮王思思[导读] 烧结作为矿石冶炼中的重要环节,其烧结质量直接关系到最终矿产的品位。
在烧结过程中,温度是至关重要的因素之一,其直接影响到最终的烧结质量。
因此,文章选用10种铁矿粉作为研究对象,对比烧结高温环境下的同化性、液相流动性、粘结相强度和铁酸钙生成量等烧结特性,以此来分析铁矿粉化学成分对烧结高温基础特性的影响。
天津市新天钢联合特钢有限公司天津市宁河区 301500摘要:烧结作为矿石冶炼中的重要环节,其烧结质量直接关系到最终矿产的品位。
在烧结过程中,温度是至关重要的因素之一,其直接影响到最终的烧结质量。
因此,文章选用10种铁矿粉作为研究对象,对比烧结高温环境下的同化性、液相流动性、粘结相强度和铁酸钙生成量等烧结特性,以此来分析铁矿粉化学成分对烧结高温基础特性的影响。
关键词:铁矿粉化学成分;烧结高温;基础特性;影响近年来,随着冶炼水平的提高和进口铁矿石价格的变化,国内企业为提高烧结矿品位,逐步降低了烧结矿中SiO2的含量。
而随着二氧化硅含量的降低,矿相中硅酸盐含量和液相含量均下降,从而导致烧结矿的冷强度和成品率下降。
因此,寻求提高烧结矿质量的途径显得尤为重要。
1试验原料与方法1.1铁矿粉的化学成分试验所用10种铁矿粉化学成分及烧损见表1。
表1 铁矿粉的主要化学成分(质量分数)及烧损1.2高温基础特性试验方法铁矿粉高温烧结的基本性能包括同化作用、液相流动性、黏结相强度和铁酸钙的生成特性。
2试验结果2.1同化性结果A5和C1的同化温度均高于1300 ° C,低硅矿A1的同化温度为1286 ° C,A2的同化温度最低,优于其他铁矿粉。
2.2液相流动性结果A5镜铁矿的液相流动性小于2.0,A3、A4、A6、B1、C2的液相流动性指数大于4.0,A1的液相流动指数为2.95。
- 1、下载文档前请自行甄别文档内容的完整性,平台不提供额外的编辑、内容补充、找答案等附加服务。
- 2、"仅部分预览"的文档,不可在线预览部分如存在完整性等问题,可反馈申请退款(可完整预览的文档不适用该条件!)。
- 3、如文档侵犯您的权益,请联系客服反馈,我们会尽快为您处理(人工客服工作时间:9:00-18:30)。
包钢常用铁矿粉烧结基础特性
包钢常用铁矿粉烧结是一种重要的冶金工艺,它可以制造出各种形状、性能优异的金属材料。
烧结铁矿粉是指将粒径小于
0.074mm的矿粉经过混合、空气过滤、热处理等工艺步骤,再经过高温烧结成颗粒具有一定的体积和结构的烧结体的工艺过程。
由于烧结铁矿粉具有良好的性能特点,它已经被广泛应用于各种行业,如冶金、建筑、机械制造、电子、化工等行业。
包钢常用铁矿粉烧结具有良好的基础特性。
首先,它具有良好的热稳定性,可以承受极高的温度,即使在高温下也不会轻易熔化,可以长期稳定在高温环境中。
其次,它具有耐腐蚀性,可以在恶劣条件下工作,不容易受到腐蚀,能有效延长使用寿命。
此外,它具有良好的电磁性能,可以有效的抑制电磁波的传播,保护电子设备免受电磁波的损害。
此外,烧结铁矿粉还具有抗压性能强、质量稳定、表面光洁度高、刚度强、热膨胀系数小等特点,因此,它在机械制造、轴承制造、汽车制造、航空航天等行业得到了广泛的应用。
从上述内容可以看出,包钢常用铁矿粉烧结具有良好的基础特性,它的热稳定性、耐腐蚀性、电磁性能、抗压性能强等特点都使它在不同行业得到了广泛的应用。
由于它的优异性能,
不仅可以满足各类工业生产的先进需求,还可以有效提高生产效率。
所以,包钢常用铁矿粉烧结在各类行业中应用量越来越大,是一种非常有用的金属材料。