新型低压铸造机简介
第2篇第1章 低压铸造

顶铸式低压铸造机
1-电热加热 保温炉
2-机架 3-供气系统
顶铸式低压铸造机特点: 一台炉上只能放一副铸型,结构简单,操作方 便,但生产效率低,生产结构复杂的铸件需要向 下抽芯时,无法设置抽芯机构。
侧铸式低压铸造机
1-电热反射 式保温炉
2-机架 3-供气系统
侧铸式低压铸造机特点: 铸型和保温炉由升液管连接,一台保温炉可供 两副铸型交替作业,也可同时作业,生产效率 高。装料、撇渣和处理金属液都较方便。这类铸 型的结构复杂。
坩埚材料有一定的高温强度、热稳定性及抗铝液 侵蚀的能力,一般采用合金铸铁或中硅球铁。在 某些特殊情况下,如铁质对某种合金有害、影响 极为严重时,可选用石墨坩埚。
3、密封盖 电阻加热炉的密封盖工作条件差,要求严格,
不但起密封作用,且要承受铸型重量及开合机构 的冲击。因此必须有足够的强度和刚度,在受热 和压力下不变形。通常使用球墨铸铁的密封盖。
陶瓷升液管
1.3.2 铸型开合机构
铸型开合机构有 手动 机械传动 气动传动 液压传动
手动铸型开合机构,其结构简单,但开合力 小,适用于小件生产。
机械传动铸型开合机构,开模力中等,只适用 于两半开模的铸型。
气动传动铸型开合机构,开合动作不平稳,有 冲击,适用于简单小件生产。
液压传动铸型开合机构,开合动作平稳,开合 力大,适用于任何铸型。
—
90
砂型低压 345~374
—
18.5~ — 84~100
铸造
48.7
砂型铸造
—
350~360 —
13
—
砂型低压 铸造
金属型低 压铸造
—
390~395 — 21~24 —
—
440~450 — 17~22 —
低压铸造和高压铸造

低压铸造和高压铸造低压铸造和高压铸造是两种常见的铸造工艺,它们在生产中起着重要的作用。
本文将分别介绍低压铸造和高压铸造的工艺原理、应用领域以及优缺点,以便更好地理解这两种铸造方法。
一、低压铸造低压铸造是一种通过施加低压力来实现铸造的工艺。
在低压铸造中,首先将金属加热至熔化状态,然后将熔融金属注入到模具中。
与传统的铸造工艺相比,低压铸造具有以下特点:1. 工艺原理在低压铸造中,使用一个压力室将金属液体注入到模具中。
通过施加一定的低压力,使金属液体充分填充模具的腔体,并保持一定的压力。
待金属凝固后,通过减小压力,模具可顺利脱模,得到所需的铸件。
2. 应用领域低压铸造适用于生产复杂形状、精度要求较高的零件。
例如,汽车发动机缸体、航空航天部件、工程机械零部件等都可以采用低压铸造工艺。
3. 优缺点低压铸造具有以下优点:首先,铸件的内部结构致密,无气孔,力学性能较好;其次,铸件表面光洁度高,无需二次加工;此外,低压铸造可实现自动化生产,提高生产效率。
然而,低压铸造的设备成本较高,操作要求较严格,对模具的要求较高,且生产周期较长。
二、高压铸造高压铸造是一种通过施加高压力来实现铸造的工艺。
在高压铸造中,金属经过加热熔化后,以较高的压力迅速注入模具中,填充整个腔体。
相比于低压铸造,高压铸造具有以下特点:1. 工艺原理在高压铸造中,金属液体被注入到模具中后,通过施加较高的压力,使其充分充实模具腔体。
随着金属的凝固,压力逐渐减小,直至脱模。
高压铸造一般会使用压铸机进行操作。
2. 应用领域高压铸造广泛应用于汽车、电子、家电等行业的零部件生产。
由于高压铸造能够生产出高精度、高强度的铸件,因此在各个领域都有重要的地位。
3. 优缺点高压铸造具有以下优点:首先,生产效率高,适用于大规模、批量生产;其次,产品精度高,表面光洁度好;此外,高压铸造可使用多种材料,适应性强。
然而,高压铸造设备成本较高,模具制造周期长,且对模具的要求较高。
铝合金低压铸造

7:生产效率高 8:铸件内部有气孔 9:铸件不能热处理强化
低压铸造的原理图
工艺流程
1:熔化工艺流程 2:低压铸造工艺流程 3:模具准备工艺流程(浇注模具) 4:热芯工艺流程 5:壳芯工艺流程 6:冷芯工艺流程 7:震动去芯工艺流程
铝合金熔化工艺流程
2:喷砂机(含喷砂房、除尘器、模具放置小车、压送罐、 喷砂枪)
3:主要作用:用来清理模具表面的过期涂料层及新模具表 面的油污等杂物。
铸造模具(1)
常用铸造模具的分类 1:砂型铸造用模具 2:特种铸造模具 3:精密铸造模具 金属型低压铸造模具 1):金属型低压铸造模具的结构
金属型低压铸造模具一般可分为:上模、下模、侧模、 及抽芯(模具结构中可以没有侧模、抽芯);
件(可以生产200kg以上铸铝件) 7:生产效率比高压铸造低 8:铸件内部没有气孔 9:铸件可以热处理强化
高压铸造 1:压力高,可达到上百兆帕
2:金属液在行腔中的速度快,可达到 60m/s,最高可到120m/s.金属液 对型腔的冲刷大
3:金属液在型腔的流动不平稳 4:型腔只能是金属型(对型腔材料要
求比较高)
铝合金低压铸造
主要内容:
一 :低压铸造介绍: 1:铝合金低压铸造在我国的发展状况; 2:低压铸造的特点; 3:铝合金低压铸造与铝合金压铸的区别;
二:低压铸造 : 1:低压铸造的原理; 2:低压铸造的工艺流程;
三:低压铸造机及主要附属设备的: 1:低压机铸造机; 2:制芯设备; 2.1:冷芯机; 2.2:壳芯机; 2.3:热芯机; 3:振动去芯机; 4:模具预热炉、喷砂机
3:制芯系统(冷芯盒射芯机、三乙胺发生器); 冷芯盒射芯机(含射砂机构、吹气机构与上顶芯机构 一体、开合模机构、下顶芯机构)
铸造设备介绍
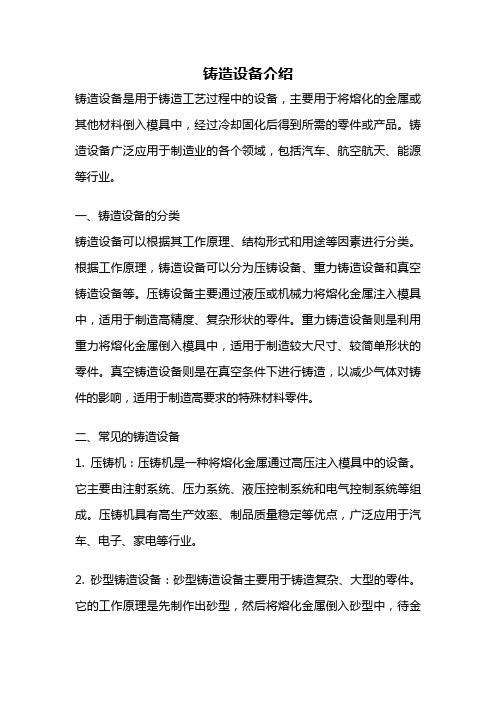
铸造设备介绍铸造设备是用于铸造工艺过程中的设备,主要用于将熔化的金属或其他材料倒入模具中,经过冷却固化后得到所需的零件或产品。
铸造设备广泛应用于制造业的各个领域,包括汽车、航空航天、能源等行业。
一、铸造设备的分类铸造设备可以根据其工作原理、结构形式和用途等因素进行分类。
根据工作原理,铸造设备可以分为压铸设备、重力铸造设备和真空铸造设备等。
压铸设备主要通过液压或机械力将熔化金属注入模具中,适用于制造高精度、复杂形状的零件。
重力铸造设备则是利用重力将熔化金属倒入模具中,适用于制造较大尺寸、较简单形状的零件。
真空铸造设备则是在真空条件下进行铸造,以减少气体对铸件的影响,适用于制造高要求的特殊材料零件。
二、常见的铸造设备1. 压铸机:压铸机是一种将熔化金属通过高压注入模具中的设备。
它主要由注射系统、压力系统、液压控制系统和电气控制系统等组成。
压铸机具有高生产效率、制品质量稳定等优点,广泛应用于汽车、电子、家电等行业。
2. 砂型铸造设备:砂型铸造设备主要用于铸造复杂、大型的零件。
它的工作原理是先制作出砂型,然后将熔化金属倒入砂型中,待金属冷却后取出即可得到所需的铸件。
砂型铸造设备包括砂型制备设备、砂型处理设备和铸造设备等。
3. 低压铸造设备:低压铸造设备主要用于铸造高质量、高精度的零件。
它通过施加一个较低的压力将熔化金属注入模具中,以减少杂质和气泡的产生,从而得到更好的铸件质量。
低压铸造设备适用于制造汽车发动机零件、航空零件等。
4. 连续铸造设备:连续铸造设备主要用于大规模生产连续铸坯的工艺。
它通过将熔化金属连续注入模具中,然后冷却固化得到连续铸坯。
连续铸造设备具有高效、省时、省力等优点,广泛应用于钢铁、有色金属等行业。
三、铸造设备的发展趋势随着科技的不断进步,铸造设备也在不断发展和创新。
目前,一些先进的铸造设备已经采用了自动化、智能化的控制系统,能够实现自动化生产线的操作。
此外,一些新型材料和新工艺也在不断应用于铸造设备中,以提高生产效率和产品质量。
低压铸铝工艺

低压铸铝工艺低压铸铝工艺是一种常见的铸造工艺,广泛应用于汽车、航空航天、电子等行业。
本文将从低压铸铝工艺的原理、特点以及应用领域等方面进行探讨。
一、低压铸铝工艺的原理低压铸铝工艺是指在铸造过程中,通过在铸型上施加一定的压力,使铝液充分填充铸型腔体,并保持一定的压力直至铝液凝固。
其主要原理是利用压力驱动铝液进入铸型,提高铝合金浇注的速度和压实度,从而获得高密度、无缺陷的铸件。
1. 高生产效率:低压铸铝工艺采用自动化生产线,能够实现连续、高效的生产。
同时,由于铝液在铸型中的充填速度较快,可以大大缩短铸件的生产周期。
2. 优良的铸造质量:低压铸铝工艺能够有效控制铝液的充填过程,减少气孔和夹杂等缺陷的产生,从而获得高密度、无缺陷的铸件。
3. 精密铸造能力:低压铸铝工艺能够生产出具有复杂形状和高精度要求的铸件,满足不同行业对于铸件的精密度要求。
4. 节约材料和能源:低压铸铝工艺采用闭模铸造,能够最大限度地减少材料的浪费。
此外,由于铝液在铸型中的充填速度较快,也能够降低能源消耗。
三、低压铸铝工艺的应用领域1. 汽车行业:低压铸铝工艺被广泛应用于汽车发动机缸盖、曲轴箱、传动壳体等零部件的生产。
采用低压铸铝工艺可以大大提高零部件的强度和耐热性能,同时减轻车身重量,提高燃油经济性。
2. 航空航天行业:低压铸铝工艺在航空航天领域的应用也非常广泛,例如飞机发动机零部件、航空电子设备外壳等。
低压铸铝工艺可以生产出轻量化、高强度的铝合金零部件,满足航空航天行业对于零部件强度和重量的要求。
3. 电子行业:低压铸铝工艺在电子行业中主要应用于电子设备外壳的生产。
采用低压铸铝工艺可以生产出外壳表面光洁、无缺陷的铝合金外壳,提高电子设备的质量和性能。
低压铸铝工艺以其高生产效率、优良的铸造质量、精密铸造能力和节约材料能源的特点,在汽车、航空航天、电子等行业得到了广泛应用。
随着科技的不断发展,低压铸铝工艺在未来的应用前景将更加广阔。
铝合金低压铸造
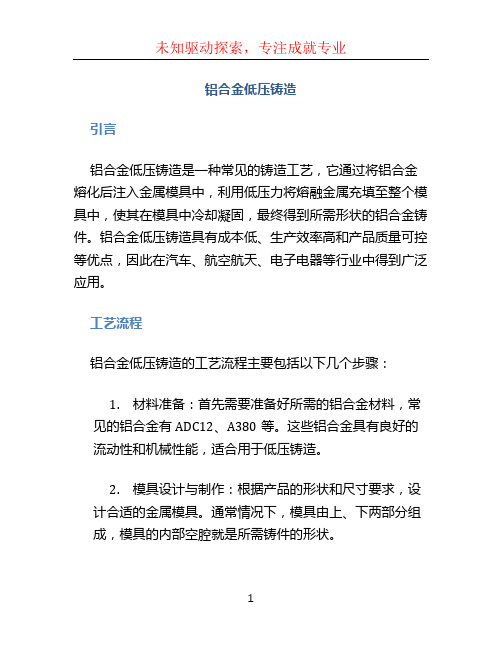
铝合金低压铸造引言铝合金低压铸造是一种常见的铸造工艺,它通过将铝合金熔化后注入金属模具中,利用低压力将熔融金属充填至整个模具中,使其在模具中冷却凝固,最终得到所需形状的铝合金铸件。
铝合金低压铸造具有成本低、生产效率高和产品质量可控等优点,因此在汽车、航空航天、电子电器等行业中得到广泛应用。
工艺流程铝合金低压铸造的工艺流程主要包括以下几个步骤:1.材料准备:首先需要准备好所需的铝合金材料,常见的铝合金有ADC12、A380等。
这些铝合金具有良好的流动性和机械性能,适合用于低压铸造。
2.模具设计与制作:根据产品的形状和尺寸要求,设计合适的金属模具。
通常情况下,模具由上、下两部分组成,模具的内部空腔就是所需铸件的形状。
3.预热模具:在注入熔融铝合金之前,需要先将模具进行预热。
预热模具可以提高铝合金的流动性,减少铸件内部气体的产生。
4.熔炼铝合金:将所需的铝合金材料放入熔炉中熔化,控制适当的熔炼温度和时间,确保铝合金的成分均匀。
5.注入模具:将熔融铝合金通过注射装置注入预热过的模具中。
注入过程中,通过控制低压力,使铝合金充填至整个模具中。
6.冷却凝固:待铝合金充填完毕后,将模具放置在冷却设备中进行冷却凝固。
冷却时间根据铸件的大小和形状而定,通常需要几分钟到几小时不等。
7.脱模与修整:待冷却完全后,可以将铝合金铸件从模具中取出。
由于冷却过程中会产生一些砂痕、气孔等缺陷,所以需要进行修整,使铸件表面平整。
8.检验与包装:对铝合金铸件进行检验,检查尺寸、密度、表面质量等指标是否符合要求。
合格的铸件经过清洁、喷砂等处理后,可以进行包装,准备发货或使用。
工艺优势铝合金低压铸造相较于其他铸造工艺,具有以下优势:•成本低:相比于高压铸造等工艺,低压铸造设备和模具制作成本较低,使用成本也相对较低。
•生产效率高:低压铸造工艺适用于大规模生产,可以快速、连续地生产大量的铝合金铸件。
•产品质量可控:低压铸造过程中,可通过控制合金的温度、压力等参数,使铝合金铸件的尺寸、密度、机械性能等指标更加可控。
低压浇铸原理
低压浇铸原理
低压浇铸(LPDC)是一种常用于铸造的工艺,它利用压力来使熔融金属充满铸型腔室,并通过控制压力的大小来提高产品质量。
低压浇铸的原理可以简单地分为以下几个步骤:
1. 准备铸模和模具:首先,需要制作出铸模和模具,用于形成铸造件的外形。
铸模通常由高强度、耐磨损的材料制成,典型的选择是铸铁或钢。
2. 熔化金属:将所需的金属材料熔化,通常采用熔炉或其他热源将金属加热至其熔点以上,并保持在熔化状态。
3. 铸造准备:在金属熔化的同时,铸模和模具应被加热到适当的温度。
通常,模具需要在铸造开始之前处于预热状态,以避免熔融金属的过早凝固。
4. 压力施加:一旦金属熔化并模具达到适宜温度,将模具移至一个接近金属熔点的位置。
然后,通过施加低压力(通常在2-15巴之间),使熔融金属逐渐充满铸型腔室。
通过控制压力的大小和持续时间,可以实现金属的均匀充填,避免气体气孔、夹杂物等缺陷的产生。
5. 保压和冷却:在金属充填完成后,保持一段时间的压力,以确保金属在凝固过程中保持形状。
同时,通过控制冷却速率,使得金属能够逐渐凝固,并获得理想的微观结构和性能。
6. 铸件取出和后处理:一旦金属完全凝固,即可将铸件从模具中取出,进行后续的清理、修整、加工等工艺步骤,以获得最终的产品。
总的来说,低压浇铸通过施加适度压力和控制冷却过程,能够提高铸造件的密度、表面光洁度和机械性能,是一种重要的铸造工艺。
宁波鸿德天鼎铸造机械 HDTD-800低压铸造机电气 说明书
电气说明书MOD. HDTD-800A安全守则本说明书的编制目的在于提供给客户与机器操作和数据设定系统的使用有关的详细说明。
本说明书随设备一起交付给最终用户:设备操作维修人员必须熟读本说明书并接收HDTD公司培训后才能操作设备;本设备电气部分只能由具有电工操作证书的专业维修人员维修制造商宁波鸿德天鼎铸造机械有限公司地址:宁波集仕港开发区TEL:86-574-88023938FAX 88023978Email:************************目录概述概述与总特点主配电柜本电气设备由一个电气控制柜和一个气动、冷却控制柜组成,防护等级IP54 。
配置有空调和适当 的冷气过滤装置。
所使用的电 器均符合安全与电磁兼容性 的强行标准(EMC)。
在电子设备柜中安装有10 吋彩色显示器、用于控制和监视全过程。
在电子设备控制板上 安装有 西门子PLC,,用于控制动作、压力、冷却、参数管理以及丰富实用的诊断信息。
这套基于PLC和MP操作面板的智能型低压铸造控制,采用世界知名品牌的中型快速PLC 作为低压铸造控制系统核心,一套高可靠高性能的PLC负责协调控制低压铸造的全过程(包括液面加压控制、模具综合冷却控制、液压机械动作控制,所有铸造参数信息和设备状态信息集中管理。
显示操作单元则采用具有数据保存功能的高性能操作面板,能够随时存取、调整和管理大量的铸造参数,无盘无风扇设计在铸造现场可靠性明显优于工控机。
精心设计的PLC和触摸屏软件全部固化基本无须维护,显然软硬件的制造成本和运行成本都比较低。
压力控制执行元件采用自己开发的组合式数字调节阀,克服了一般比例阀的加压速率低、响应速度慢、控制精度低等缺陷。
通过现场使用实践证明该系统是一套先进、智能、高精度和高可靠性的控制系统。
液面加压控制部分是该控制系统的核心内容,在低压铸造设备上具有举足轻重的作用。
本系统采用了智能变参数PID 闭环控制,用高精度压力传感器直接检测炉子压力,加压执行元件采用数字组合快速调节阀岛,与传统的比例阀相比,明显提高了控制精度和加压速度。
低压铸造机工作原理
低压铸造机工作原理低压铸造机是一种常见的铸造设备,它的工作原理非常重要。
本文将详细介绍低压铸造机的工作原理,包括其组成部分和工作过程。
低压铸造机主要由铸造系统、加热系统、液压系统和控制系统组成。
铸造系统包括铸造模具、铸造室和铸造机构,用于制造铸件。
加热系统用来加热金属材料,使其熔化并保持在一定的温度范围内。
液压系统主要用于提供铸造过程中所需的压力和力量,确保铸件的成型质量。
控制系统用于控制整个铸造过程,包括温度、压力和时间的调节。
低压铸造机的工作过程如下:1. 准备工作:首先,将铸造模具安装在铸造机构上,并调整到适当的位置。
然后,将金属材料放入加热炉中进行加热,直到熔化并达到所需的温度。
2. 浇注金属:当金属材料熔化并达到所需温度后,将加热炉移动到铸造机构上方。
然后,打开加热炉的出料口,使熔融金属流入铸造模具中。
在浇注过程中,通过控制液压系统提供的压力,使金属材料以适当的速度和压力进入模具,确保铸件的成型质量。
3. 冷却和固化:在金属材料进入模具后,开始冷却和固化过程。
通过控制系统中的温度和时间参数,确保金属材料在模具中逐渐冷却并固化成所需的形状。
4. 脱模和清理:当铸件完全冷却并固化后,可以打开模具,并将铸件取出。
然后,对铸件进行清理和修整,以去除可能存在的气泡或缺陷,并使其表面光滑。
低压铸造机的工作原理基于物理和化学原理。
通过加热金属材料,使其熔化并保持在适当的温度范围内,可以使金属具有足够的流动性,以便在铸造模具中形成所需的形状。
通过液压系统提供的压力,可以控制金属材料的进入速度和压力,从而确保铸件的成型质量。
控制系统的使用可以精确控制温度、压力和时间等参数,以确保铸件的成型过程达到所需的要求。
低压铸造机是一种重要的铸造设备,其工作原理基于物理和化学原理,通过加热、浇注、冷却和固化等过程,制造出具有一定形状和性能的铸件。
通过合理调节铸造参数和控制系统,可以获得高质量的铸件。
低压铸造机在工业生产中有着广泛的应用,为各行各业提供了可靠的铸造解决方案。
低压铸造机工作原理
低压铸造机工作原理
低压铸造机是一种工业设备,用于制造精密铸件。
它的工作原理如下:
1. 铸件准备:首先,需要准备铸件的模具和铸造材料。
通常,铸件模具由铸造师根据产品需求制作而成,模具内部的空腔形状和尺寸与最终铸件相匹配。
2. 模具装填:模具通常由两部分组成,上模和下模。
上模和下模打开后,铸造材料被放置在其中的空腔中。
这通常是由工人手工完成的。
3. 封模:上模和下模紧密地结合在一起,将铸造材料封在模具中。
这通常是通过机械手臂或液压装置完成的。
4. 吹气:在模具封闭后,开始给模具中的空腔注入气体。
通常使用压缩空气,将气体送入模具的底部。
这样,模具中的铸造材料将受到气体的压力力量,以保持其形状和稳定性。
5. 硬化:在气体压力作用下,铸造材料迅速硬化和冷却,以固定其形状。
在这个阶段,模具内的温度也会逐渐降低。
6. 解模:一旦铸造材料充分硬化,上模和下模会分别打开,从模具中取出制成的铸件。
因为低压铸造机通常具备自动解模的功能,因此此步骤通常由机器自动完成。
7. 去除余料:从模具中取出铸件后,通常还需要进行一些后续
处理。
例如,可以去除多余的铸造材料或修整铸件的表面。
总之,低压铸造机通过在模具中施加一定的气体压力,使铸造材料保持稳定的形状,并通过硬化和冷却固定该形状。
这种铸造工艺常用于制造复杂、高精度的金属铸件,具有高质量和高效率的优势。
- 1、下载文档前请自行甄别文档内容的完整性,平台不提供额外的编辑、内容补充、找答案等附加服务。
- 2、"仅部分预览"的文档,不可在线预览部分如存在完整性等问题,可反馈申请退款(可完整预览的文档不适用该条件!)。
- 3、如文档侵犯您的权益,请联系客服反馈,我们会尽快为您处理(人工客服工作时间:9:00-18:30)。
新型低压铸造机简介
二十世纪六十年代,英国率先采用低压铸造工艺铸造铝合金轮毂,随后以美、德、日等为代表的西方国家开始普遍采用低压铸造工艺生产铝轮毂。
上世纪八十年代我国引进低压铸造设备开始生产汽车铝合金轮毂,并逐步推广,到目前为止,中国已成为世界上铝合金轮毂制造强国,其中大部分轮毂采用传统的低压铸造工艺。
低压铸造铝轮毂普遍采用的是中心浇铸工艺,该工艺最适合轮毂的浇铸成型。
但由于这种工艺补缩通道在中心的特点,使得中心盘和轮辐等部位不能尽快实施强制冷却,造成低压铸造轮毂的轮辐、中心盘部位的机械性能下降,甚至个别轮型达不到汽车厂的质量要求。
尽管很多厂家进行了努力,采取水冷,改进模具设计等工艺,但都难以得到根本的解决。
于是以提高效率、降低成本为目标的各种工艺方法的实验成为传统低压铸造铝轮毂的主要研究方向(例如要求设备动作迅捷快速、模具快装、水冷、水雾冷却等方面)。
今年来日韩等国开始研究使用双边浇的工艺,使得轮毂中心部位的强度大大提高,但相应的也带来一些成型方面、轮辋部位、以及金属利用率低等负面影响。
中国也有一些厂家积极开展了类似的研究,取得一些成功并积累了一定的经验。
我们认为,解决传统低压铸造铝轮毂的固有问题,必须采用打破传统工艺的新型设备和工艺。
双边浇是其中的一个重要的研究方向。
我公司紧跟国内外轮毂成型工艺的最新发展动态,反复研究比较了目前低压铸造设备和工艺的特点,研制出一种最新型的多用途多功能低压铸造机,这种低压铸造机集成了我公司多年的技术成果,适合不同工艺要求,既适用于目前稳定的中心浇铸工艺,有适合新式的双边浇工艺,其中双边浇工艺又适合边模正装的国内和日韩的浇铸方式,又适合欧洲采用的边模返装的双边浇工艺和边模返装的中心浇工艺,同时通过加宽边模支撑板,又适合一机双模的浇铸工艺。
为了进一步提高产品质量及生产效率,降低设备故障率,该设备又集成了大量的新工艺和新配置,无论在OEM工厂还是在零售工厂,该设备都能使工艺人员充分发挥、施展、尝试不同的铸造工艺,从中选取最适合本厂的稳定的轮毂铸造工艺模式高效的组织生产。
欢迎业内同仁惠顾垂询指教。
HDT TD ‐1000S
型多
多功能多用途
途低压铸造机机
模具
模具
具正装,可以
具返装,适合以采用传统的
合欧洲使用过中心浇工艺
过的模具返装,也可以采用
中心浇工艺,用适合正装的
,也适合模具的双边浇工艺
具返装的双边艺 边浇工艺
垂直稳定双边
直升降和平移定。
炉子进出边浇,同时也
液压移进出的保温导轨采用可也适合一机双
压驱动的快速温炉,炉子泄压折叠结构设计双模的生产方
速锁模机构,压后液压泵可计,节省空间式,也适合多
大大减少模可完全泄荷,间。
三升液管多升液管充型
模具更换时间节省能源。
管设计,既适型的特殊产品
间,降低劳动
且垂直升降适合中心浇又品。
动强度
降更加又适合
可选的批
选装的模具局批量生产 局部加热功能
设备能,和模具测温
备增加可靠的温功能,适合
的安全锁机构合新产品的铸构
铸造工艺参数数摸索和复杂产品
新
新型的冷却控
取件手
控制系统,大
手抓取轮毂,
大大提高冷却
降低工人劳动
却效率和产品
动强度
品质量
新型型的炉门结构,可靠且降低低漏风。