转炉少渣炼钢工艺操作(转炉造渣方式)
转炉双渣法炼钢少渣冶炼

3、少渣冶炼的关键技术
▪ 图7和图8分别为氧枪枪位和炉渣FeO含量 对脱磷阶段结束[P]含量的影响,可以看到, 采用较低枪位和高强度供氧,由于熔池搅拌 显著加强,尽管炉渣FeO含量降低至9.5%附 近,脱磷效率非但没有降低,反而有较大幅 度的提高。
第十七页,课件共有50页
2、双渣法少渣冶炼原理
▪ ②终渣碱度高、自由CaO含量高而不外排;排出的前期 渣中自由CaO含量低(前期造的低碱度渣 ),而节省了 CaO用量 ;
▪ ③传统工艺出钢后会有钢水留在炉内,一部分会随炉 渣倒出,而采用少渣冶炼工艺,吹炼终点不倒渣,因 而可以提高钢水收得率。
第十八页,课件共有50页
1、转炉双渣法少渣冶炼现状
▪ 马钢在120t转炉上进行少渣冶炼,用生白云石代替 部分石灰和镁球。
▪ 钢研总院研究对300t转炉的前期渣打水后返回使用, 每炉次加入3~6t返回渣,每炉可节约0.7~1t石灰。
▪ 鞍钢鲅鱼圈研究含磷钢冶炼,不加石灰而只加轻烧白 云石。
第十三页,课件共有50页
2、双渣法少渣冶炼原理
第四页,课件共有50页
1、转炉双渣法少渣冶炼现状
▪ 上个世纪的50--70年代,中国一些转炉钢厂在铁水硅、 磷含量高时,为了降低石灰消耗,减少吹炼过程喷溅, 改善脱磷效果,曾采用过出钢后留渣或“留渣--双渣” 炼钢工艺。后来,随着高炉生产水平提高(铁水硅含量 降低),高磷铁矿石用量减少(铁水磷含量降低),以 及顾忌留渣造成铁水喷溅的安全隐患,留渣或“留渣-双渣”炼钢工艺就不推荐采用了。
第七页,课件共有50页
1、转炉双渣法少渣冶炼现状
▪ 已经发表文章的单位(不完全统计)及生产转炉的 容量:
▪ 首钢京唐300t转炉 ;鞍钢260吨转炉 ;首钢迁安210t转炉; 沙钢180t转炉;酒钢120t转炉;日照120t转炉;马钢120t 转炉 ;莱钢120t转炉;首钢首秦100t转炉;湘钢80t转炉; 首钢长治80t转炉
转炉冶炼工艺

转炉冶炼工艺炼钢就是造渣。
造渣的目的:脱P、减少喷溅、保护炉衬。
造渣制度:确定合适的造渣方式,渣料的加入数量和时间、成渣速度。
渣的特点:一定的碱度、良好的流动性、合适的FeO及MgO、正常泡沫式的熔渣。
单渣法:铁水硅高磷低,或冶炼要求低。
双渣法:铁水硅高磷高,或冶炼要求高。
留渣法:利用终渣的热及FeO,为下炉准备。
成渣的速度:转炉冶炼时间短,快速成渣是非常重要的,石灰的溶解是决定冶炼速度的重要因素。
石灰的溶解:开始吹氧时渣中主要是SIO,MNO,FEO,是酸性渣,加入石灰,石灰溶解速度,可用下面的公式表示J=K(CaO+1.35MgO-1.09SiO2+2.75FeO+1.9MnO-39.1)形成2CAO*SIO2,渣难溶解。
FeO、MnO、MgO可加速石灰溶解,因为可以降低炉渣粘度,破坏2CaO*SiO2的存在。
采用软烧活性石灰、加矿石、萤石及吹氧加速成渣。
成渣的途径:低枪位操作,渣中FeO含量下降很快,磷接近终点时,渣中铁才回升。
适用于低磷铁水,对炉衬寿命有好处。
高枪位操作:渣中FeO含量保持较高水平,碳接近终点时,渣中铁才会下降。
适用于高磷铁水,对炉衬侵蚀严重;FeO高,炉渣泡沫化严重,易产生喷溅。
终点的控制方法:一次拉碳法、增碳法、高拉补吹法。
按出钢要求的终点碳和温度进行吹炼,当达到要求时提枪,操作要求较高。
优点:终点渣FeO低,钢中有害气体少,不加增碳剂,钢水洁净。
氧耗较小,节约增碳剂。
增碳法:所有钢种均将碳吹到0.05%左右,按照钢种加增碳剂。
优点:操作简单,生产率高,易实现自动控制,废钢比高。
高拉补吹:当冶炼中,高碳钢种时终点碳按钢种规格略高一些进行拉碳,待测温取样后按分析结果与规格的差值决定补吹时间。
造渣是转炉炼钢过程中的一个重要内容,渣系的好坏直接关系到炼钢过程能否顺利进行,有时甚至造成溢渣或喷溅,从而降低钢的收得率及粘枪,因此要尽量避免溢渣和喷溅。
技术科安龙飞。
300吨转炉炼钢工艺操作规程

300吨转炉炼钢工艺操作规程一、前期准备工作1.确认炼钢转炉的容量和炉内清洁度,准备好所需的原料和辅助材料。
2.对于炉缸砖、吹氧工艺和氧枪的检查、维护和更换工作要做到位。
3.确认好吹氧的工艺参数和流量。
4.对于所需取样检验的项目和方法进行确认和准备。
5.工作人员进行相关设备的检查、试车和操作培训。
6.开始生产前,进行安全会议,明确操作规程和安全措施。
二、炼钢工艺操作1.转炉预热a.打开转炉排放系统,排除转炉内部的杂质,确保转炉内部干净。
b.将预热氧气引入转炉,预热炉缸砖和炼钢转炉。
2.加入铁水a.逐步将铁水加入转炉,注意加入速度和均匀性。
b.记录加铁时间、数量和铁水成分,以备后续分析。
3.加入废钢和废铁a.根据炼钢配料列表,逐步加入所需的废钢和废铁。
b.注意废钢和废铁的化验报告,确保加入的质量合格。
4.吹氧炼钢a.在加入铁水和废钢后,开始吹氧炼钢。
b.根据设定的工艺参数和流程,控制氧气的流量和时间。
5.取样检验a.在炼钢过程中,定时取样并送至实验室检验。
b.检验项目包括成分、温度、气体成分等。
6.调整炼钢过程a.根据取样结果,及时调整工艺参数,确保炼钢质量。
b.与实验室和现场操作人员密切合作,保证炼钢过程的稳定性和质量。
7.出钢a.在炼钢完成后,开始出钢。
b.出钢的时间、温度和成分要做好记录。
8.清洁转炉a.在炼钢结束后,对转炉内部进行清洁和检查。
b.确保下一次炼钢的顺利进行。
三、结束工作1.整理资料a.对于生产过程和取样检验的数据进行整理和归档。
b.确保质量信息的完整和可追溯性。
2.设备维护a.对于炼钢设备进行维护和保养。
b.准备好下一次炼钢生产的准备工作。
3.安全检查a.进行安全设备和设施的检查和维护。
b.对生产过程中的安全事故和隐患进行总结和处理。
四、注意事项1.在炼钢过程中,操作人员要遵守相关操作规程,确保安全生产。
2.对于炼钢原料和辅助材料要进行认真的检查和保管。
3.炼钢过程中的各项工艺参数和生产数据要详细记录和保存。
转炉炼钢工艺流程
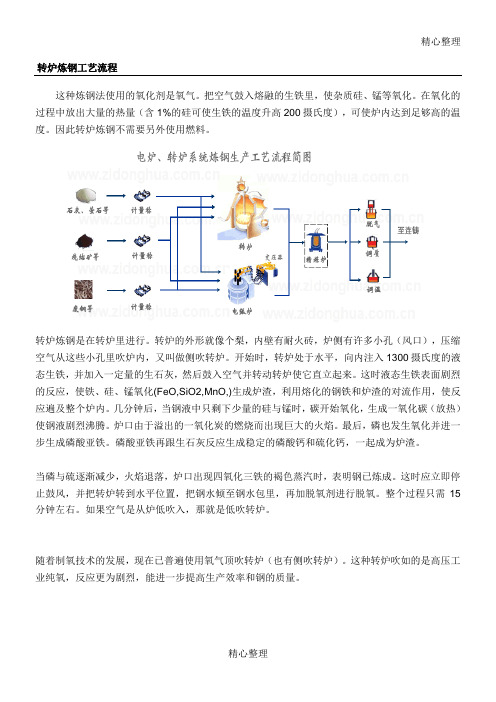
精心整理转炉炼钢工艺流程这种炼钢法使用的氧化剂是氧气。
把空气鼓入熔融的生铁里,使杂质硅、锰等氧化。
在氧化的过程中放出大量的热量(含1%的硅可使生铁的温度升高200摄氏度),可使炉内达到足够高的温度。
因此转炉炼钢不需要另外使用燃料。
摄氏度(放热)15分钟左右。
如果空气是从炉低吹入,那就是低吹转炉。
随着制氧技术的发展,现在已普遍使用氧气顶吹转炉(也有侧吹转炉)。
这种转炉吹如的是高压工业纯氧,反应更为剧烈,能进一步提高生产效率和钢的质量。
转炉一炉钢的基本冶炼过程。
顶吹转炉冶炼一炉钢的操作过程主要由以下六步组成:(1)上炉出钢、倒渣,检查炉衬和倾动设备等并进行必要的修补和修理;(2(3(4(5(6小型转炉为2.5-4.5m3/(t·min);120t以上的转炉一般为2.8-3.6m3/(t·min)。
◆开吹时氧枪枪位采用高枪位,目前是为了早化渣,多去磷,保护炉衬;◆在吹炼过程中适当降低枪位的保证炉渣不“返干”,不喷溅,快速脱碳与脱硫,熔池均匀升温为原则;◆在吹炼末期要降枪,主要目的是熔池钢水成分和温度均匀,加强熔池搅拌,稳定火焰,便于判断终点,同时使降低渣中Fe含量,减少铁损,达到溅渣的要求。
◆当吹炼到所炼钢种要求的终点碳范围时,即停吹,倒炉取样,测定钢水温度,取样快速分析[C]、[S]、[P]的含量,当温度和成分符合要求时,就出钢。
◆当钢水流出总量的四分之一时,向钢包中的脱氧合金化剂,进行脱氧,合金化,由此一炉钢冶炼完毕。
炼钢学概述航天航空、交通运输、农业、国防等许多重要的领域均需要各种类型的大量钢材,我们的日常生活更离不开钢。
总之,钢材仍将是21世纪用途最广的结构材料和最主要功能材料。
炼钢方法(1)最早出现的炼钢方法是1740年出现的坩埚法,它是将生铁和废铁装入由石墨和粘土制成的坩埚内,用火焰加热熔化炉料,之后将熔化的炉料浇成钢锭。
此法几乎无杂质元素的氧化反应。
1856年英国人亨利·贝塞麦发明了酸性空气底吹转炉炼钢法,也称为贝塞麦法,第一次解决了用铁水直接冶炼钢水的难题,从而使炼钢的质量得到提高,但此法要求铁水的硅含量大于0.8%,而且不能脱硫。
转炉双渣法炼钢少渣冶炼

1、转炉双渣法少渣冶炼现状
对于转炉吹炼前期渣的操作控制也进行了研究,
北京科技大学的王新华等在首钢迁安210t转炉上 试验,脱磷阶段采用低碱度(R=1.3~1.5)和低
MgO质量分数(≤7.5%)的渣系,能够形成流动
性良好和适度泡沫化的炉渣,解决了脱磷阶段结
束难以快速足量倒渣和渣中金属铁含量高这两大
3、少渣冶炼的关键技术
图7和图8分别为氧枪枪位和炉渣FeO含量
对脱磷阶段结束[P]含量的影响,可以看到, 采用较低枪位和高强度供氧,由于熔池搅 拌显著加强,尽管炉渣FeO含量降低至 9.5%附近,脱磷效率非但没有降低,反而 有较大幅度的提高。
3、少渣冶炼的关键技术
采用上述高效脱磷工艺,在铁水磷含量为
溅,引发重大安全事故。迁钢公司曾采用加入多
量石灰、白云石或废钢直接冷却对液态炉渣进行 固化的方法,但发现存在以下问题: ①如石灰、白云石加入量多,造成脱磷阶段炉渣 碱度和MgO含量过高,导致倒渣困难;
3、少渣冶炼的关键技术
②如采用废钢对液态渣进行冷却固化,由于废钢
尺寸不均衡,常发生炉内废钢“搭棚”情况,炉 底液态渣不能被充分固化,存在安全隐患。通过
稳定运行。
3、少渣冶炼的关键技术
为了使炉渣具有良好的流动性,还须对MgO含量
进行严格控制。后面的图为210t转炉脱磷阶段结
束时倒渣量与渣中MgO含量的关系,当将MgO含
量控制在7.5%以下时,倒渣量可在8t以上,能够
满足少渣冶炼工艺稳定运行的要求,为此规定对 脱磷阶段炉渣MgO含量按低于7.5%控制。这一 MgO含量控制目标低于常规工艺初期渣的MgO含 量控制目标值,采用后并未发现对炉龄有不利影
③传统工艺出钢后会有钢水留在炉内,一部分会
转炉少渣高效生产(江苏沙钢集团)(1)

沙钢集团
2 . 江苏沙钢集团宏发炼钢生产工艺流程
铁水车
KR脱硫
转炉
LF
RH
外发
销售
精整 室内堆放 轧制
连铸
火焰切割
沙钢集团
3. 江苏沙钢集团宏发炼钢厂转炉少渣工艺
转炉冶炼主要可分为单渣法、双渣法、双联法3种工艺。 单渣法的石灰消耗与铁水初始硅含量关系密切 ,一般在 30kg/t~50kg/t;双渣法冶炼通常在铁水硅含量较高的情况下 采用,转炉辅料消耗较高;双联法虽然能够降低原辅料的消 耗,但是需要额外增加专门用于脱磷的转炉。 沙钢集团宏发炼钢厂转炉的常规冶炼工艺为单渣留渣 法,冶炼超低磷钢种时采用双渣法。常规吹炼工艺的转炉平 均石灰消耗为 26kg/t,吹炼终点总渣量平均为95kg/t,简单 的工艺优化很难进一步降低其石灰消耗。为此,我厂与沙钢 研究院一道共同开发了转炉少渣冶炼工艺。
40 30 20 10 0 0
20
Dolomite,kg/t
Lime,kg/t
15 10 5 0
常规工艺 少渣工艺 试生产
平均22kg/t 平均17kg/t
0.25 0.5 %Si
常规工艺 少渣工艺 试生产
0.75
1
0
0.25
0.5 %Si
0.75
1
沙钢集团
6. 推广应用
0.005 50 50 0.01 100
枪位控制
230 220 210 200
Si<0.25% Si=0.25%--0.4% Si>0.4%
根据铁水成分,我 厂设计了三种枪位 控 制 模 式 :
Si<0.25%低硅模式 Si=0.25%--0.40%中硅 模式 Si>0.40%高硅模式 前期 高枪位吹炼主要 为了快速成渣,利用 前期低温优势最大效 率的去磷。
8-转炉“留渣-双渣”少渣炼钢工艺实践
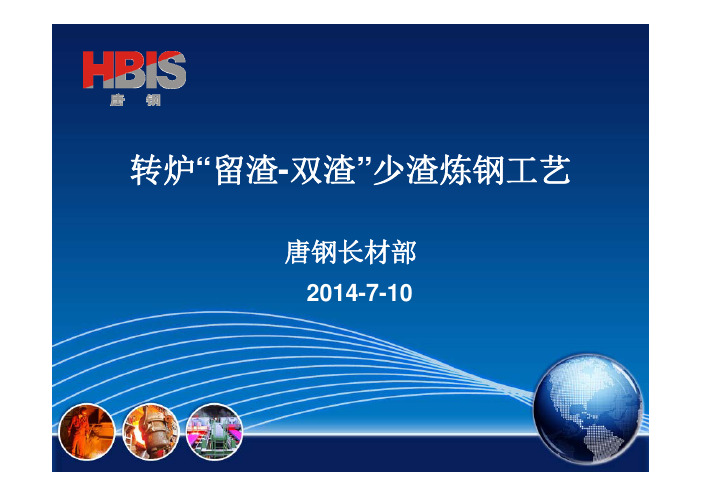
“留渣-双渣”工艺示意图
3.转炉脱磷影响因素
3.脱磷的基本原理
2[P]+5(FeO)+4(CaO)=4CaO·P2O5+5[Fe]
a 4CaO P2 O 5 a a
2 p 5 F eO
Kp
a
4 C aO
% 4CaO P2 O 5 4CaO P O 4 5 4 % P 2 f P2 % F e O 5 F e O % CaO C aO
演变:首钢公司从2011年开始,在首钢首秦和迁钢分别连续试验单
转炉“留渣-双渣”操作,取得较好的效果,目前首钢集团首钢长治, 首钢水钢均推广应用“留渣-双渣”少渣炼钢操作工艺,工艺相对成熟 。
1. 大幅度减少炼钢石灰、白云石等渣料消耗和炼钢渣量; 2. 可以利用出钢后炉渣的物理热,预热废钢; 3. 炼钢终渣含Tfe:15~25%,渣量减少可以降低钢铁料消耗; 4. 双渣倒渣的炉渣主要为脱磷阶段低碱度渣,自由CaO含量低, 可以简化炉渣处理; 5. 常规转炉出钢后留在炉内钢水随炉渣倒出,采用“留渣-少渣”工 艺终点少倒渣、出钢后不倒渣,可以提高钢水收得率。
FeO%
H11Mn2SiA
3A14306-1 3A14306-2 3B14615-1 3B14615-2 3C14935-1 3C14935-2 3A14301-1 3A14301-2 3B14603-1 3B14603-2 3B14612-1 3B14612-1
1 冶炼周期影响
类别 加料 脱磷期 双渣 脱碳期 终点 加废钢 兑铁时间 前期吹炼时间 氮气刹渣 倒渣时间 中后期吹炼 拉碳、补吹时间 等待终点成分 出钢时间 溅渣时间 总冶炼周期 留渣-双渣 1.7 2.4 4.5 2.1 3 8.8 2 1 2.5 2 30 单渣法 1.7 2.2 4.5 / / 8.7 2 1 2.5 2.5 25.1
转炉“留渣+双渣”少渣炼钢工艺实践

转炉“留渣+双渣”少渣炼钢工艺实践李伟东;杨明;何海龙;刘鹏飞;乔冠男【摘要】The key technologies on steelmaking based on the slag reserving and duplex slag process in converter in General Steelmaking Plant of Angang Steel Co., Ltd. are introduced, in-cluding slag reserving and slag solidifying technology, slag fluidity controlling and high efficient dephosphorization technology, fast slagging sufficiently and deslagging technology from molten iron, control technology for slag getting dry and content of FeO in final slag and fast operation technolo-gy based on slag reserving and duplex slag process. After these technologies are used the cost is reduced by 12.19 yuan RMB per ton steel.%介绍了鞍钢股份有限公司炼钢总厂转炉“留渣+双渣”工艺的关键技术,包括留渣及炉渣固化技术、炉渣流动性控制及高效脱磷技术、快速足量放渣及渣铁分离技术、炉渣返干控制及终渣FeO控制技术以及“留渣+双渣”快速生产技术,采用这些技术后,吨钢成本降低12.19元。
【期刊名称】《鞍钢技术》【年(卷),期】2015(000)005【总页数】5页(P41-45)【关键词】转炉;少渣;留渣;双渣;脱磷【作者】李伟东;杨明;何海龙;刘鹏飞;乔冠男【作者单位】鞍钢股份有限公司炼钢总厂,辽宁鞍山114021;鞍钢股份有限公司科技质量部,辽宁鞍山114021;鞍钢股份有限公司炼钢总厂,辽宁鞍山114021;鞍钢股份有限公司炼钢总厂,辽宁鞍山114021;鞍钢股份有限公司炼钢总厂,辽宁鞍山114021【正文语种】中文【中图分类】TF777少渣炼钢是指转炉冶炼总渣量极少化的一种炼钢工艺。
- 1、下载文档前请自行甄别文档内容的完整性,平台不提供额外的编辑、内容补充、找答案等附加服务。
- 2、"仅部分预览"的文档,不可在线预览部分如存在完整性等问题,可反馈申请退款(可完整预览的文档不适用该条件!)。
- 3、如文档侵犯您的权益,请联系客服反馈,我们会尽快为您处理(人工客服工作时间:9:00-18:30)。
2)留渣量较大时,采用精炼返回渣实现炉渣固化;
留渣量较大的情况下,留渣量随循环炉次增加而增加,脱磷期结束倒 渣量在4吨(100吨转炉)左右计算,循环第2炉留渣量在8~9吨左右。留渣
量较大情况下溅渣护炉时间延长至6分钟左右,采用精炼返回渣可以起到
迅速固化炉渣的作用。
• 3)适量加入精炼返回渣
为改善大渣量条件下的炉渣固化效果,缩短溅渣护炉时间,同
少渣炼钢工艺简介
姓名:柴先义
部门:炼钢作业部
日期:2014-5-20
目 录
第1章 少渣炼钢工艺简介
第2章 少渣炼钢工艺操作
第3章 少渣炼钢工艺难点控制
第4章 国内外少渣炼钢效果
炼钢作业部
第1章 少渣炼钢工艺简介
1.1 少渣炼钢工艺简析
铁水“三脱”使传统炼钢工艺发生了显著变化,在铁水预处
理阶段进行脱硅、脱磷和脱硫,使炼钢转炉的主要功能转变为
少钢工艺路线中,后三种炼钢工艺 铁水经过“三脱”预处理后再脱碳炼钢,能够做到少渣 操作 。四种转炉炼钢工艺路线的渣量比较见图1。从图l 可以看出,后三种炼钢工艺的吨钢渣量低于70 kg/t。
1.3 氧气转炉常用的造渣方法
1、单渣法: 在吹炼过程中只造1次渣,中途不倒渣、不扒渣,直到吹炼终点 出钢。单渣操作工艺比较简单,吹炼时间短,劳动条件好,易于实现 自动控制。正常情况下脱磷效率在80%左右,脱硫效率为30%~40%; 第一批渣料是在开吹的同时加入,第二批渣料的加入时间是在硅锰氧 化基本结束,第一批渣料基本化好,碳焰初起时加入。 2、双渣法: 在吹炼中期倒出或扒除1/2~2/3炉渣,然后加入渣料重新造渣的 方法为双渣操作。根据铁水成分和所炼钢种的要求,也可以多次倒炉 倒渣造新渣。在铁水含硅较高,含磷大于0.5%,吹炼优质钢,吹炼中、 高碳钢种时,都可以采用双渣操作。采用双渣操作可以在转炉内保持 最小的渣量,同时又能达到最高的脱磷硫效率。双渣操作脱磷效率在 90%以上,脱硫效率约45%。双渣操作会延长吹炼时间,增加热量损 失,降低金属收得率,不利于自动控制,恶化劳动条件。
3.3炉渣的连续循环控制
1,对炉料加入模式的优化.。在相同倒渣量、总白灰 加入量相同的条件下,提高脱碳期白灰加入量,有利 于提高脱磷期倒渣率、提高脱碳渣的循环利用。
脱磷期白灰加 入量大,容易 造成白灰熔化 不充分,造成 白灰浪费。
所有脱磷期不加 或少加白灰。碱 度控制在 1.8~2.2之间。 终渣碱度控制在 2.8-3.3之间。 脱碳渣热循 环利用 脱磷期白灰消耗 降低 脱磷期白灰加入量由原来的 2/3降低为1/3
采用炉渣固化与安全兑铁的基本原理:将降低炉渣温度,使炉渣液 态变固态,提高炉渣粘度,防止兑铁时铁水与炉渣剧烈反应。 1,炉渣固化采用的技术措施 1)采用溅渣护炉实现炉渣固化; 通常情况下,转炉拉碳倒渣,倒渣后炉内留渣量在5~6吨左右,在该种情 况下,采用溅渣护炉,溅渣时间在3~4分钟可以满足溅渣护炉与固化炉渣的效 果。
作,可以得到流动性良好的炉渣,在获得较好脱磷效果的同时也易
发生喷溅;及时提枪摇炉倒渣,尽可能地多倒富磷渣,防止冶炼后 期回磷。 ②倒掉足够的富磷渣再下枪吹炼,此时要立刻加入第二批料以 防止下枪冶炼时渣中(TFe)过高,产生大喷溅现象。 ③脱碳期采用高—低—低枪位。在吹炼中期,碳激烈氧化, (TFe)被大量消耗,熔渣的矿物组成发生了变化,熔点升高,可能会
12
2.3 技术开发难点
脱碳渣具有高的碱度和比较高的∑(FeO)含量,对铁水具
有去磷和去硫能力,且本身还含有大量的物理热,将该种 炉渣部分/全部留在炉内可以显著加速下一炉初期渣的成渣
过程,提高吹炼前期脱磷率、节省石灰用量和提高炉子的
热效率。但在操作中,必须特别注意防止兑铁水时产生严 重喷溅。
少渣炼钢工艺操作,需特别注重以下方面: 1、液态终渣快速固化 2、脱磷期高效脱磷 3、炉渣连续循环控制
调温和脱碳,同时炼钢渣量减少,形成了少渣炼钢工艺。 国外专家认为,少渣炼钢是在转炉炼钢时,每吨金属料加 入的石灰量低于20 kg,脱碳炉每吨钢水的渣量低于30 kg。值得 指出的是,如果将脱磷转炉每吨金属料产生的20~40 kg脱磷渣 也视为炼钢渣,那么少渣炼钢工艺流程的总渣量约为50-70 kg。 由于少渣炼钢用的铁水硅含量很低,造渣用石灰加入量明显
也能减弱喷溅强度。
4.溅渣护炉时,可加入适量的精炼返回渣,以缩短溅渣护炉时间。
2.2 少渣炼钢工艺的优点:
整个冶炼过程分为脱磷期与脱碳期,具有如下优点。
倒出的脱磷渣中P2O5含量高 渣量少、渣中TFe含量低
——脱磷效率提高
——金属收得率提高 石灰、生烧白云石消耗降低 ——石灰、生烧白云石消耗量降低 少渣炼钢工艺渣量70-80kg/t,普通工艺渣量100120kg/t。少渣炼钢工艺比普通工艺降低35kg/t左右。
第2 章
少渣炼钢操作控制
依据我公司初步设计,将来可能采用的少渣炼钢法为第四种炼钢 工艺的优化,即在同一座转炉上进行铁水脱磷和脱碳炼钢工艺,并将 全部或部分脱碳渣留给下一炉脱磷用,脱磷结束倒出重新造渣,类似
留渣双渣操作。
2.1 冶炼操作控制方法
1、保持有效炉容比,合理控制转炉装入量,控制终渣的R=2.8~ 3.3,MgO=8%~l4%;确保炉底稳定,防止炉底大起大落,保持炉型
20
3、脱磷期结束倒渣量控制
脱磷期结束倒渣量与倒渣时间有一定关系,倒渣时间控 制在3~7分钟时,倒渣量基本在3~4吨以上,随着倒渣时间的 增加,超过7分钟以后,倒渣渣量并没有大幅增加,因此,合 适的倒渣时间应该控制在3~7分钟之间。 脱磷期结束倒渣量在4-7吨左右,连续循环可以持续稳定进 行,脱碳期结束留渣量在10吨左右。倒渣量增加后,炉渣的转炉 终点碱度有所提高。
3.2脱磷期的高效脱磷控制
目标:脱磷期结束磷含量低于0.030%
工艺难点
脱磷期时间短(4~6min)
铁水硅含量高(平均0.52%)
—碱度控制不稳定,渣量大、脱磷难
底吹枪流量低(最高供气强度0.10M3/h.t) —底吹搅拌能力弱,脱磷困难
17
脱磷期快速、深脱磷采用的技术手段有: 1、提高熔池的搅拌强度。 底吹强度低于0.1NM3/mint时,底吹对熔池搅拌力的影 响与顶枪相比相差一个数量级,底吹搅拌力的影响可以忽 略,通过提高矿石加入量,增加渣中FeO含量,提高渣中 [O]来源,增大熔池[C]、[O]反应速度进而提高熔池搅拌强 度。 2、快速去除铁水[Si]含量 当铁水硅含量高于0.2%时,难以发生脱磷反应,冶炼前 期采用大流量供氧、低枪位“硬吹”脱硅工艺,快速深脱 硅,增加脱磷阶段的时间。 3、随着循环炉数的增加,逐渐增大脱碳期渣量。
13
第3章 少渣炼钢工艺难点控制
3.1液态终渣快速固化控制
终渣中含有FeO成分,这种终渣留给下一炉,在兑入铁水时必会发生
以下化学还原反应:(FeO)+[C]=[Fe]+CO;2(FeO)+[C]=2[Fe]+CO2。 若终渣中FeO含量高于25%,还原反应会更激烈,瞬间产生大量的气
体,造成爆发性喷溅事故。
炉渣的连续循环控制
2、炉渣的连续循环控制要求: 脱磷阶段倒渣量在4.0-7.0t (铁水[Si]含量变化影响); 倒渣时间控制在4.0-5.0min; 连续循环3炉以上比例达到50%,最高循环7炉。
平均每炉(8炉)产生渣量7.3吨,该次循环折合吨钢产生渣量 73kg左右。(平均白灰消耗35kg/t)
3 、留渣法
将上炉终渣的一部分或全部留在炉内给下炉使用。终点熔渣的碱度高、
温度高,并且有一定(TFe)含量,留到下一炉有利于初期渣尽早形成,并且 能提高前期去除磷硫的效率,有利于保护炉衬,节省石灰用量。采用留渣 操作时,在兑铁水前要先加石灰或者加废钢稠化冷凝熔渣,当炉内无液体 渣时方可兑入铁水,以避免引发喷溅。 4 、留渣双渣法 将上炉终点渣的一部分或全部留在炉内,然后在吹炼第一期结束时倒 出,重新造渣。留渣双渣法的终渣具有较高的碱度和较高的∑(FeO)含量, 对铁水具有一定的去磷和去硫能力,且本身还含有大量的物理热。将这种 炉渣部分,甚至全部留在炉内,可以显著加速下一炉初期渣的成渣过程, 提高吹炼前期去磷和去硫率,节省石灰用量和提高转炉的热效率。在这种 留渣法中,要特别注意防止兑铁水时产生严重喷溅。
减少,降低了渣料消耗和能耗,提高了金属收得率。同时,因
渣量少,氧的利用效率高,吹炼终点钢水中氧含量低,余锰高, 合金元素收得率较高,从而降低了生产成本。另外,少渣炼钢
工艺终点命中率高,改善了钢水的纯净度,为生产超纯净钢创
造了条件。
1.2 转炉炼钢常见的四种工艺路线
第一种是传统的炼钢工艺,欧美各国的炼钢厂多采用这种模
型的双联法工艺流程为:高炉铁水+铁水预脱硫+转炉脱磷+
转炉脱碳+炉外精炼+连铸。由于受设备和产品的限制,也 有在同一座转炉上进行铁水脱磷和脱碳的操作模式,类似传 统的“双渣法”。
第四种炼钢工艺是对第三种炼钢工艺进行了改进, 与第三种工艺的明显不同是将部分脱碳渣返回脱磷转炉, 脱磷后的铁水进入脱碳转炉脱碳。该工艺是目前渣量最
时为了降低白灰消耗,提高脱磷期冶金效果,进行了回吃返回精炼
渣。溅渣护炉前可加入300kg~500kg/炉的精炼返回渣;溅渣护炉后 加入800kg/炉以上的渣料,优化脱磷期冶金效果。
•
.
精炼返回渣回收应用:成分检验—冷却—破碎—筛分—转炉料 仓。 加入精炼返回渣可以有效降低溅渣护炉时间与炉渣温度, 可以节省白灰消耗300kg以上。 2、溅渣护炉时间与渣量、温度的关系
出现“返干”现象。在处理炉渣“返干”或加速终点渣形成时,不
要加入过量的矿石,或用过高的枪位吹炼,避免(TFe)积聚。
④终点适时降枪,降枪过早熔池碳含量还较高,碳的氧化速度迅速加 快,也会产生大喷;炉役前期炉膛小,同时温度又低,要注意适时降枪, 避免TFe含量过高,引起喷溅。 ⑤吹炼中发生喷溅不能轻易降枪,因为降枪后碳氧反应更加激烈,会 加剧喷溅;应适当提枪迅速压枪,这样可缓和碳氧反应和降低熔池升温速 度,再借助于氧射流的冲击吹开熔渣,有利于气体的排出。 ⑥在炉温很高时,可以在提枪的同时适当加一些石灰稠化熔渣,有时 对抑制喷溅也有些作用,也可加压渣剂减少喷溅。此外,适当降低氧流量