从铜阳极泥中回收硒_碲新技术
【CN110042246A】一种高碲银硒渣短流程回收硒的方法【专利】

(19)中华人民共和国国家知识产权局(12)发明专利申请(10)申请公布号 (43)申请公布日 (21)申请号 201910335008.6(22)申请日 2019.04.24(71)申请人 紫金矿业集团股份有限公司地址 364200 福建省龙岩市上杭县紫金路1号紫金大厦 申请人 紫金铜业有限公司(72)发明人 陈杭 衷水平 吴星琳 郑佳翔 张焕然 王俊娥 罗仁昆 李涛 (74)专利代理机构 北京科亿知识产权代理事务所(普通合伙) 11350代理人 汤东凤(51)Int.Cl.C22B 7/00(2006.01)C22B 11/02(2006.01)C22B 15/00(2006.01)C01B 19/00(2006.01)
(54)发明名称一种高碲银硒渣短流程回收硒的方法(57)摘要本发明公开了一种高碲银硒渣短流程回收硒的方法,包括如下步骤:S1、将高碲银硒渣置于真空蒸馏炉内,在20-100Pa、300-350℃条件下进行真空蒸馏2-3h,产出粗硒和含银、铜、碲的底渣;S2、将步骤S1中得到的粗硒置于硒氧化炉中,在氧气流量6-10m3/h、温度500-570℃的条件下反应3h,得到二氧化硒和含碲底渣。本发明通过真空蒸馏的方法,简单、快速、节能、高效地将硒从银、碲、铜中分离并进行硒的提纯,最终得到二氧化硒。
权利要求书1页 说明书3页 附图1页
CN 110042246 A2019.07.23
CN 110042246 A1.一种高碲银硒渣短流程回收硒的方法,其特征在于,包括如下步骤:S1、将高碲银硒渣置于真空蒸馏炉内,在20-100Pa、300-350℃条件下进行真空蒸馏2-3h,产出粗硒和含银、铜、碲的底渣;S2、将步骤S1中得到的粗硒置于硒氧化炉中,在氧气流量6-10m3/h、温度500-570℃的条件下反应3h,得到二氧化硒和含碲底渣。2.根据权利要求1所述的方法,其特征在于,还包括如下步骤:将步骤S1得到的含银、铜、碲的底渣返回铜阳极泥处理工艺。3.根据权利要求1所述的方法,其特征在于,还包括如下步骤:步骤S2得到的含碲底渣返回铜阳极泥处理工艺。
铜阳极泥处理工艺的研究进展

温 度 7 q 时 间 15 。在此 工 艺条件 下 铋 、 脱 除率 5c .h 锑
分别 达 8 % 、4 以上 。 5 7% 对 于含铋 比较 多 的 阳极 泥 , 少 华 报 道 的脱 胡
金属。
处 理铜 阳极 泥工 艺投 产 , 法 工艺 由 于金 、 直 收率 湿 银
高 生成 周期 短 等优 点 而获 得 迅 速 发 展 。近 年 来 , 国
1 1 锑 、 、 的脱 除 。 铋 砷
铜 阳极 泥物相 分 析结果 表 明 , 、 9 铋 锑 0% 以上是
内外 对铜 阳极泥处 理 工 艺 不 断 地 进 行 了工 艺改 革 和 设备 改革 。对铜 阳极 泥 处 理 工 艺 的 进 一 步研 究 主要
金 、 的一个 主要 来 源 。同时 , 阳极泥 中还 富含 铂 、 银 铜
还含有少量 的其 它杂质 , c ,n S 2A2 3C O 如 o Z ,i , 1 ,a O O
等 “ 。阳极 泥可 被用 作提取 s ,eA , g 铂 族 ] eT , u A 及
金属 的原 料 , 时它 也 被认 为是 含 A ,b B 及 易 溶 同 sS , i
中图分类号 : F 1 . T 1 13 文献标识码 : A 文章编号 :0 1 2 7 2 0 )2— 0 2—0 10 —17 (0 8 1 0 3 7
Ag 5 ~ 1 9, Au 0.0 ~ 5, Pt 5 0 ~ 0.0 5,Pd 00
0 写 言 {
中圉 已探 明的金 、 矿产 资 源 中 , 生金 资源 约 银 伴
阳极泥处理工艺

铜陵有色金属集团公司50万吨阳极泥处理选择流程的主要依据是阳极泥的化学成分和生产规模的大小。
目前,国内外阳极泥处理工艺主要有三大类:一是全湿法工艺流程,以美国Outfort公司为代表。
流程为“铜阳极泥一加压浸出铜、碲一氯化浸出硒、金一碱浸分铅一氨浸分银一金银电解”;二是以湿法为主,火法、湿法相结合的(半)湿法工艺流程,为国内目前大多数厂家所采用。
主干流程为“铜阳极泥一硫酸化焙烧蒸硒一稀酸分铜一氯化分金一亚钠分银一金银电解”;三是以火法为主,湿法,火法相结合的火法流程,以波立登公司和奥托昆普公司为代表,主干流程为“铜阳极泥一加压浸出铜、碲一火法熔炼、吹炼一银电解一银阳极泥处理金”,在熔炼、吹炼的设备上,波立登公司仅用1台卡尔多炉来完成,奥托昆普公司则为选用贵铅熔炼炉和转炉两台炉子来完成。
湿法处理铜阳极泥工艺流程如图1所示。
铜阳极泥经预处理脱铜产低铜泥,低铜泥进入回转窑中进行硫酸化焙烧蒸硒,硒蒸气被水吸收还原产粗硒;蒸硒渣低酸分铜,预处理液和分铜液合并,用碱中和产出碱式碳酸铜;碱式碳酸铜返回铜系统;分铜渣碱浸分碲;分碲液用硫酸中和产铅碲渣、分碲渣氯化分金,分金液用二氧化硫还原产粗金粉;分金渣用亚硫酸钠分银;分银液用甲醛还原产粗银粉;分银渣含少量金银可销售至铅冶炼厂回收铅、锡和少量的金银;粗金粉、粗银粉分别电解产电金、电银。
此阳极泥处理工艺中,分碲工序在上述原料成分的情况下,由于碲含量较低,经济上无利可图,所以不回收。
年处理2500t阳极泥亚硫酸钠 1200甲醛 125碳酸钠 704.69硝酸 l1.33硫酸 3500盐酸 3.1氢氧化钠 2200液体二氧化硫 200水 143000氢氧化钙 63电 15638 103/(kwh)氯化钠 700蒸汽 31820综合能耗方面-每吨干阳极泥(半)湿法约为2.9t标准煤,而波立登法约为1.5t标准煤。
从以上的方案比较中可以看出:(半)湿从以上的方案比较中可以看出:(半)湿法流程的优点是工艺成熟,有价元素综合回收好,返料少、循环负荷小,无烟气和烟尘的污染,环境保护及车间工业卫生好,相对投资省。
含铜污泥中铜的资源化回收技术

含铜污泥中铜的资源化回收技术含铜污泥是指在生产工艺中产生的含有较高铜含量的固体废弃物。
由于铜是一种宝贵的有色金属资源,因此对于含铜污泥的资源化回收技术的研究具有重要的意义。
本文将介绍几种常用的含铜污泥资源化回收技术。
1.铜溶解浸出技术铜溶解浸出技术是目前最常用的含铜污泥资源化回收技术之一、该技术通过浸出剂将含铜污泥中的铜溶解出来,然后进行分离和提纯。
常用的浸出剂有酸性浸出剂和氨液浸出剂。
通过控制浸出剂的浓度、温度、pH值等因素,可以实现高效的铜溶解浸出。
2.电解法电解法是另一种常用的含铜污泥资源化回收技术。
该技术将含铜污泥作为阳极,通过电解液中的铜离子向阳极迁移并沉积,实现铜的回收。
电解法具有回收纯度高、操作简便等优点。
但是,电解法相对来说比较耗能,且设备成本较高。
3.沉浸浸出法沉浸浸出法是一种较为简单的含铜污泥资源化回收技术。
该技术通过将含铜污泥浸泡在适当的浸出剂中,使铜溶解出来。
常用的浸出剂有酸性溶液、氨液等。
与铜溶解浸出技术相比,沉浸浸出法操作简单、设备成本低,但回收铜的效率相对较低。
4.熔融法熔融法是一种将含铜污泥直接加热至熔融状态,然后将铜分离出来的资源化回收技术。
该技术适用于铜含量较高的污泥,通过高温熔融可以将铜从污泥中分离出来。
熔融法可以实现较高的回收率,但是设备成本较高,处理过程较为复杂。
除了上述几种常用的含铜污泥资源化回收技术外,还有一些新兴的技术被用于回收铜。
如生物浸出法利用微生物的作用将铜从含铜污泥中溶解出来,生物还原法通过微生物的还原作用将铜从氧化态还原为金属态,以便进行回收等。
这些新兴的技术在环保性、资源利用效率、经济性等方面具有独特的优势,对于含铜污泥的资源化回收具有重要的意义。
在实际应用中,不同的含铜污泥资源化回收技术可以根据污泥的特性和工艺要求进行选择。
由于不同技术存在着各自的优缺点,因此在实际应用中应该综合考虑各方面因素,确定最适合的回收技术,并通过工艺改进和优化提高回收率和经济效益。
二氧化硫还原沉金后液回收硒碲及捕集铂钯

二氧化硫还原沉金后液回收硒碲及捕集铂钯方法研究概述:通过 SO2 直接还原回收硒碲和捕集铂钯的方法研究,以沉金后液为原料。
采用 X 射线衍射仪(XRD)和扫描电镜(SEM) 对还原产物的物相、微观形貌进行表征,结果表明:当反应温度为 85 ℃,SO2 流量为 0.2 L/min,反应时间为 4 h,H + 浓度为 3.3 mol/L 和 Cl −浓度为 0.72 mol/L 时,Se 和 T e 回收率分别为 99.5%和 96.64%,Pt 和 Pd 回收率均到了 100%,所得黑色还原产物中硒、碲、铂和钯的质量分数分别为 28.06%、52.3%、0.084%和 0.588%。
产物中硒和碲均以单质态形式存在,其形貌为球状体和柱状体。
铜阳极泥是电解精炼粗铜时所产生的不溶物,它的产率一般为电解铜产量的 0.2%~1.0%,因其中含有大量的贵金属和稀有元素而成为提取稀贵金属的重要原料。
目前,国内采用湿法流程处理铜阳极泥的工厂已达 40%以上。
铜阳极泥经预处理脱铜(硒碲)之后,采用亚硫酸钠或氨水浸出银、氯酸钠浸出金工艺分别得到分银液和分金液,分银液用水合肼或甲醛还原得到银粉,分金液用亚硫酸钠或草酸还原得到金粉和沉金后液。
沉金后液含有大量的硒碲铂钯,目前一般在沉金后液中加入锌粉置换铂钯得到铂钯精矿,其工艺简单,操作方便;但是,锌粉置换法得到的铂钯精矿中铂钯含量低,回收铂钯时损失大,造成硒碲流失,锌粉用量大,生产成本高。
此外,有报道采用铜粉或铜片置换沉淀溶液中的硒碲,不过沉淀物中的硒和碲是以硒化铜和碲化铜的形式存在,不利于后续硒碲分离,延长了工艺流程。
本研究采用 SO2 直接还原沉金后液回收硒碲和捕集铂钯,该处理工艺使硒和碲得到回收,所得还原产物硒碲品位高,有利于硒碲分离回收;另外,铂、钯等贵金属得到完全回收并高度富集,为含稀贵金属溶液的有效综合利用提供一条可行途径。
1 实验1.1 实验步骤实验取某铜冶炼厂草酸还原分金液得到的沉金后液,其成分如表 1 所列。
从复杂碲铜物料中回收碲的工艺研究
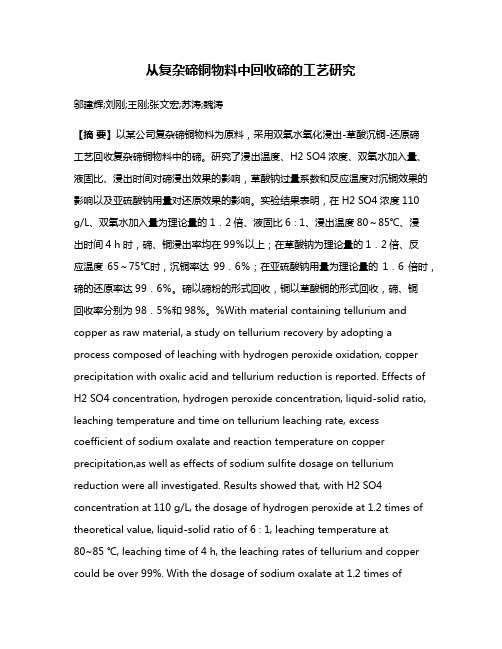
从复杂碲铜物料中回收碲的工艺研究邬建辉;刘刚;王刚;张文宏;苏涛;魏涛【摘要】以某公司复杂碲铜物料为原料,采用双氧水氧化浸出-草酸沉铜-还原碲工艺回收复杂碲铜物料中的碲。
研究了浸出温度、H2 SO4浓度、双氧水加入量、液固比、浸出时间对碲浸出效果的影响,草酸钠过量系数和反应温度对沉铜效果的影响以及亚硫酸钠用量对还原效果的影响。
实验结果表明,在H2 SO4浓度110g/L、双氧水加入量为理论量的1.2倍、液固比6∶1、浸出温度80~85℃、浸出时间4 h时,碲、铜浸出率均在99%以上;在草酸钠为理论量的1.2倍、反应温度65~75℃时,沉铜率达99.6%;在亚硫酸钠用量为理论量的1.6倍时,碲的还原率达99.6%。
碲以碲粉的形式回收,铜以草酸铜的形式回收,碲、铜回收率分别为98.5%和98%。
%With material containing tellurium and copper as raw material, a study on tellurium recovery by adopting a process composed of leaching with hydrogen peroxide oxidation, copper precipitation with oxalic acid and tellurium reduction is reported. Effects of H2 SO4 concentration, hydrogen peroxide concentration, liquid-solid ratio, leaching temperature and time on tellurium leaching rate, excess coefficient of sodium oxalate and reaction temperature on copper precipitation,as well as effects of sodium sulfite dosage on tellurium reduction were all investigated. Results showed that, with H2 SO4 concentration at 110 g/L, the dosage of hydrogen peroxide at 1.2 times of theoretical value, liquid-solid ratio of 6∶1, leaching temperature at80~85 ℃, leaching time of 4 h, the leaching rates of tellurium and copper could be over 99%. With the dosage of sodium oxalate at 1.2 times oftheoretical val ue and reaction temperature at 65~75 ℃, copper precipitation rate reached 99. 6%. With the dosage of sodium sulfite at 1. 6 times of theoretical value, the reduction rate of tellurium could be up to 99.6%. Tellurium was recovered in the form of powder and copper was recovered as copper oxalate, with corresponding recoveries of 98.5% and 98%.【期刊名称】《矿冶工程》【年(卷),期】2014(000)004【总页数】4页(P104-107)【关键词】碲铜物料;氧化酸浸;碲;铜【作者】邬建辉;刘刚;王刚;张文宏;苏涛;魏涛【作者单位】中南大学冶金与环境学院,湖南长沙410083;中南大学冶金与环境学院,湖南长沙410083;中南大学冶金与环境学院,湖南长沙410083;中南大学冶金与环境学院,湖南长沙410083;中南大学冶金与环境学院,湖南长沙410083;中南大学冶金与环境学院,湖南长沙410083【正文语种】中文【中图分类】TF803.2我国稀散金属资源非常丰富,其中碲的储量处于世界第3 位。
铜阳极泥的焙烧-湿法冶金流程
世上无难事,只要肯攀登铜阳极泥的焙烧-湿法冶金流程阳极泥的湿法冶金,具有环境污染小,贵金属分散损失少,易于实现机械化和自动化作业,效率高,成本低等诸优点,尤其用于阳极泥产量多的大中型工厂,经济效率更为显著,而成为大中工厂今日处理阳极的主要流程。
此外,氰化法、硫脲法等,也被有些工厂用来处理阳极泥生产过程中的某些中间产品。
80 年代以来,全湿法和半湿法处理铜阳极泥的工业流程已在我国大多数工厂广泛应用。
它们主要包括铜阳极泥的预先硫酸盐化或氧化焙烧,然后进行湿法分步处理以提取金银,并综合回收有价金属。
下面列举的三个有代表性的铜阳极泥处理工业流程,都是经过许多生产厂家和研究部门长期探索的基础上综合和发展而来的。
一、铜阳极泥的蒸硒和湿法-电解法流程此法是贵溪、富春江、武汉、铜陵二冶等厂采用的工业流程。
阳极泥首先经硫酸盐化焙烧蒸硒,并从炉气中用稀硫酸液吸收和通入SO2 还原回收粗硒。
蒸硒渣经稀硫酸加热并鼓风搅拌浸出脱铜,浸液返回铜电解。
脱铜渣采用氨浸分银,并用水含肼从浸液中还原出粗银送电解。
分银渣进行碳酸钠硅化并用稀硝酸浸出除铅,并向铅液中加适量硫酸(不使过剩)使生成PbSO4 沉淀,滤液返回再浸铅。
除铅渣使用HCl、NaCl 和CaOCl 浸出金,并通SO2 还原为粗金送电解。
最终渣返回铜火法冶炼。
二、铜阳极泥的硫酸盐化焙烧和湿法-沉淀法流程本流程为烟台冶炼厂等所采用。
硫酸盐化焙烧分别采用高温和低温法。
当阳极泥含硒较高时,在600~650℃焙烧和蒸硒4h,并从烟气中吸收和还原为粗硒;而含硒量低时,则在300℃焙烧2h。
焙烧原料与硫酸的配比为1∶1。
焙烧。
铜阳极泥富集贵金属的方法试验
铜阳极泥富集贵金属的方法试验一,概述在铜冶炼工艺过程中,生产出来的冰铜是一种中间产品,冰铜经过阳极炉或转炉冶炼,得到另外的铜冶炼的中间产品粗铜,铜冶炼企业通常处理粗铜的方法是采用电解方法,通过粗铜电解,得到电解铜,既阴极铜,在粗铜电解过程中大量的杂质元素,有价金属,如:铜、铅、锡、金、银、铂、钯、硒、碲等贵金属和稀有金属,都以铜电解阳极泥的形式沉淀富集,本方法试验是属于有色金属的湿法冶金,试验原料是一种高杂质铜阳极泥预处理富集贵金属的方法。
步骤是向沥干水分后的铜阳极泥中加入硫酸调浆,置于微波反应炉中,进行微波酸浸5~30min,然后进行固液分离,得到微波酸浸渣和微波酸浸液,向微波酸浸渣中加入稀硫酸调浆,在通入氧气压力为0.8~1.2MPa条件下,将微波酸浸浆料置于高压反应釜中进行加压酸浸4~6h,得到加压酸浸渣和加压酸浸液,从加压酸浸渣中回收金和银,从加压酸浸液中回收镍。
本发明的技术方案同时提高了杂质铜阳极泥中的铜、硒、碲和镍浸出回收率,缩短了铜阳极泥的处理时间,提高了铜阳极泥的处理量,使贵金属走向合理且集中,有利于综合回收。
二、方法试验来源本方法试验是有色金属的湿法冶金,试验原料是广东某铜冶炼企业电解产出的一种高杂质铜阳极泥,粗铜电解精炼过程中,在直流电作用下阳极上的铜和电位较负的贱金属溶解进入溶液,而正电性金属,如金、银和铂族金属它们在阳极上不进行电化学溶解,而以极细的分散状态落入槽底形成铜阳极泥。
铜阳极泥中含有大量的贵金属、铂族金属和稀有元素,是提取稀贵金属的重要原料。
为了有效提取铜阳极泥的稀贵金属,并有利于其他有价元素的回收,需要对阳极泥进行预处理,预处理过程的目的是尽可能脱除铜、硒、碲、镍等金属并使贵金属得到富集,然后再用火法或湿法的方法进行回收金、银和铂族金属。
铜、硒、碲、镍等元素在铜阳极泥中占有极大的比例,而且它的存在对后续的贵金属分离有重大的影响,因此需要对其进行预处理回收,以降低后续工作的试剂耗量和缩短生产周期。
铜阳极泥处理研究现状
铜阳极泥处理研究现状孔祥峰1,2,3,邓聚海1,2,3(1.昆明理工大学 真空冶金国家工程实验室,云南 昆明 650093;2.昆明理工大学 云南省有色金属真空冶金重点实验室,云南 昆明 650093;3.昆明理工大学 省部共建复杂有色金属资源清洁利用国家重点实验室,云南 昆明 650093)摘 要:简述了国内外阳极泥火法处理工艺:传统火法工艺、卡尔多炉工艺、半湿法工艺、卡尔多炉工艺以及全湿法工艺,通过对工艺流程、主要杂质元素走向、金属回收率及主要存在问题进行比较,对铜阳极泥处理工艺的选择提出建议,并对未来发展方向作出展望。
关键词:铜阳极泥;三联吹炼;选冶联合法;卡尔多炉法中图分类号:P694 文献标识码:A 文章编号:1002-5065(2019)19-0169-2Research Status of Copper Anode Sludge TreatmentKONG Xiang-feng1,2,3, DENG Ju-hai1,2,3(1. Kunming University of Science and Technology Vacuum Metallurgy National Engineering Laboratory,Kunming 650093,China;2. Kunming University of Science and Technology Yunnan Key Laboratory of Nonferrous Metals Vacuum Metallurgy,Kunming 650093,China;3. Kunming University of Science and Technology, Ministry of Science and Technology, State Key Laboratory for Clean Utilization of Complex Nonferrous Metal Resources,Kunming 650093,China)Abstract: The anode mud fire treatment process at home and abroad is briefly described: traditional fire process, Karl multi-furnace process, semi-wet process, Karl multi-furnace process and all-wet process, through the process flow, main impurity element orientation, metal The recovery rate and main problems are compared, suggestions are made for the selection of copper anode mud treatment process, and the future development direction is prospected.Keywords: copper anode mud; triple blowing; combined metallurgy method; Caldo furnace method铜阳极泥是粗铜电解精炼产生的副产物,质量一般约为阳极板的0.2%~1.0%。
浅谈提高铜阳极泥中硒回收率的几点建议
铜 阳 极 泥 化 学 成 分 ( 量 分 数 ) P 5 一 质 : b2 %
3 5% 、 5% 、Bi5% 一 1 Cu 0. 0% 、S 4% 一 1. e 0. 2% 、
Te % 一8 。 2 %
阳极泥与浓硫酸混合 ( 酸料 比 = . ~ . : ) 1 1 14 1 ,
1 引 言
硒是一种典型的半 导体元素 , 广泛应用于静 电 复印、 电子、 玻璃 、 钢铁 、 陶瓷、 冶金、 化工及医药工业 方面。硒在 自然界 中不单独存在, 常与金属矿物 , 尤
其是 铜 的硫化 物共 生 ( 主要 伴 生 在黄 铜 矿 、 铜 矿 、 斑 黄铁 矿 中 ) 含 量 很 低 。铜 、 及镍 电 解 阳 极 泥 是 且 铅
(cec n ehooyD vlp et eat n fB C,B ii 7 00 C i ) Si eadTc nlg ee m n D pr t NM n o me o ayn 39 0, hn a
Ab ta t Dec b stec p e n d dfo h ai r cpe f h c v r f ee im , rc s ,ito u e oi sr c : s r e h o p ra o emu rm teb scp n ilso er o eyo lnu p o es nrd c dt m— i i t e s
亚硒酸被炉气 中的 s O 还原为单质硒 :
H2 e S O3+2S O2+ H2 = S 0 e+ 2H2 e S O4
沉 淀物 经过 滤 、 涤 和干 燥 , 到 粗 灰 硒 , 收 洗 得 吸
液中尚含有一定量的硒 , 可进一步还原从中回收硒。
2 2 阳极泥 的成 分 .
- 1、下载文档前请自行甄别文档内容的完整性,平台不提供额外的编辑、内容补充、找答案等附加服务。
- 2、"仅部分预览"的文档,不可在线预览部分如存在完整性等问题,可反馈申请退款(可完整预览的文档不适用该条件!)。
- 3、如文档侵犯您的权益,请联系客服反馈,我们会尽快为您处理(人工客服工作时间:9:00-18:30)。
从铜阳极泥中回收硒、碲新技术
梁刚舒万艮蔡艳荣郑诗礼
(中南工业大学化学系,长沙410083)
提出了从铜阳极泥中回收硒、碲的新技术:以H2O2作氧化剂,在弱酸性溶液中氧化硒和碲,固液分离后调节pH分离硒和碲,在盐酸酸化下用Na2SO3还原硒和碲。
硒和碲回收率分别为99%和98%,纯度均可达99%。
关键词:硒碲回收铜阳极泥
1前言
从铜电解阳极泥中回收提纯硒、碲的方法较多,有苛性碱氧化加压浸出[1]、氧化焙烧高温浸出[2]、低温氧化焙烧、稀硫酸浸出等[3,4],硒、碲还原大都采用二氧化硫还原、铜还原的方法[5,6]。
由于采取预先焙烧氧化的方法,存在设备较复杂,动力设备维修费用高,二氧化硫气体对人体和环境危害较大,硒、碲回收率和纯度不高等缺点。
经小型试验和工业试验改进了现有工艺,提高了硒、碲的回收率和纯度,降低了生产成本。
2试验
211原料
试验原料为大冶金属公司电解铜阳极泥,其化学成分见表1。
表1铜阳极泥化学成分
元素Au Ag Cu Se Te Pb As 成分/%0.912.0823.4 6.7 3.1 4.3 1.19
212方法
21211硫酸预浸除铜
铜阳极泥中铜含量高对硒、碲和贵金属回收不利。
必须首先对阳极泥进行预处理。
采用3mol/L H2SO4浸出,浸出温度40e,时间2h,使阳极泥中铜含量降至1%~3%,碲和银部分浸出。
银可加入氯化钠或盐酸优先沉淀回收,碲可用铜粉还原。
21212硒、碲氧化
在pH=3~4的H2SO4和NaCl体系中加入10%H2O2(理论计算量的200%),温度75e,氧化时间6h,将硒、碲氧化成亚硒酸盐和亚碲酸盐,贵金属留于渣中,然后固液分离。
21213硒、碲分离
用10%NaOH调至pH6,使碲形成亚碲酸盐沉淀物,过滤分离硒、碲。
21214硒、碲还原
将亚硒酸钠溶液以3mol/L H Cl酸化
第21卷第4期稀有金属1997年7月
后,用Na2SO3溶液还原成元素硒。
沉淀的硒用水淋洗并干燥。
碲酸沉淀物用011mol/L H Cl和H2SO4溶解,过滤分离后用4mol/L H Cl 酸化,再用Na2SO3溶液还原成元素碲。
沉淀的碲用水淋洗并干燥。
3结果和讨论
311预浸出时硫酸浓度和温度对金属浸出率的影响
改变硫酸浓度,固定条件:浸出温度40e、固液比1B3、浸出时间2h;改变浸出温度,固定条件:硫酸3mol/L、固液比1B3、浸出时间2h。
试验结果见表2、3。
表2硫酸浓度对浸出率的影响
硫酸浓度c mol/L
浸出液成分/mg#ml-1浸出率/%
Ag Au Se T e Cu Ag Au Se T e Cu
4 1.88<0.0050.180.9174.21 4.67<0.20.838.9395.1 3 1.87<0.0050.070.7173.68 4.65<0.20.28 6.9094.
5 2 1.02<0.0050.010.3060.93 2.65<0.20.05 2.8578.1
表3浸出温度对浸出率的影响
浸出温度t
e
浸出液成分/mg#ml-1浸出率/%
Ag Au Se T e Cu Ag Au Se T e Cu
30 1.81<0.0050.020.7067.91 4.58<0.20.08 6.8387.1 40 1.87<0.0050.070.7173.68 4.63<0.20.28 6.9094.5 50 2.38<0.0050.170.9174.93 5.90<0.20.648.7396.1 80 5.47<0.005 2.40 1.7876.9513.61<0.28.717.398.7
由表2看出,随着硫酸浓度增大,铜、硒、碲和银浸出率都增大。
为了减少硒的损失,选择硫酸浓度3mol/ L,此时铜浸出率9415%,硒浸出率0128%,阳极泥中铜含量降至214%,物料量减少到53%。
由表3看出,温度高于40e,铜浸出率增加较小,而硒、碲和银浸出率增加较大。
故选择浸出温度40e,此时铜浸出率9415%、硒浸出率0128%。
液固比和浸出时间对铜、硒、碲和银浸出率影响不大。
选择在硫酸浓度3mol/L、浸出温度40e、固液比1B3和浸出时间2h条件下进行综合验证试验,获得铜浸出率为9417%,银、硒和碲浸出率分别为4155%、0127%和4175%,基本上达到了除铜和预先部分回收银和碲的目的。
312硒、碲氧化时pH对浸出率的影响改变pH值,固定其它条件:浸出温度75e、浸出时间6h、在硫酸和氯化钠体系中添加10%H2O2(理论量的200%)溶液作氧化剂。
试验结果见表4。
由表可知,在pH=3时硒、碲浸出率为100%,而贵金属则留在渣中,实现了分离的目的。
313pH对硒和碲分离的影响
用10%NaOH溶液调节pH。
pH值对硒和碲分离的影响见表5。
由表可知:在pH=6时硒、碲浓度比为542,达到较
255
4期梁刚等从铜阳极泥中回收硒、碲新技术
表4 pH 对硒和碲浸出率的影响
pH 浸出液成分/mg #m l -1浸出率/%
S e T e Pb S e Te Pb 1113.430.1 1.46101100 1.82113.030.30.1410010.10.173113.031.30.031001040.064112.829.4<0.00510096.1<0.015119.710.2<0.00510333.5<0.016
113.0
0.2
<0.005
100
0.7
<0.01
表5 pH 对硒和碲分离的影响
pH 硒浓度c Se mg/ml 碲浓度c Te mg/ml S e/Te 4.5112.629.4 3.85111.510.210.95.5110.7 1.861.56
108.4
0.2
542
好的分离。
314 盐酸浓度对硒、碲还原率的影响
变化盐酸酸化浓度,固定其它条件:Na 2SO 3溶液(理论值的150%)、还原温度25e 、还原时间2h 。
试验结果见图1。
由图可知,盐酸浓度为3mol/L 时硒还原率为100%;浓度为4mol/L 碲还原率100%。
故硒和碲还原的最佳盐酸浓度分别为3mol/L 和4mol/L。
图1 盐酸浓度对硒、碲还原率的影响
4 结 论
11采用硫酸预浸出除铜,使阳极泥中铜含量降至1%~3%,物料量减少
50%~60%,对下一步贵金属回收有利,既能缩小设备规模,又能减少材料消耗和降低成本。
21用H 2O 2在弱酸性体系中氧化硒和碲,避免了氧化焙烧工序,缩短工艺流程和生产周期,有利于提高金属的回收率。
31在盐酸酸化条件下使用Na 2SO 3溶液代替二氧化硫气体进行还原,易于控制和减少环境污染,硒和碲的回收率可分别达到99%和98%,纯度均为99%。
金和银损失少于011%。
5 参考文献
1 INCO.Ltd.U.S.Patent 4163046,
1978.
2 Sumitomo M etal M ining Co.Ltd.Jpn.Ko kao T okkyo Koho JP.5773179.
3 夏徽君1贵金属,1993,14(3):611
4 陈昌禄,冯学良1第四届全国金银选冶学术会议论文集,郑州,1993:1601
5 Haffman J E.有色冶炼,1990,18(5):291
6 Hyv ar inen Olli,Lindr oos L eo and Yllo Erkki.T he Journal of the M iner als,M etals and M aterial Society ,1989,41(7):42.
(1996年10月21日收稿)
256 稀 有 金 属
21卷。