从铜阳极泥中综合回收硒
铜阳极泥脱硒工艺现状和趋势
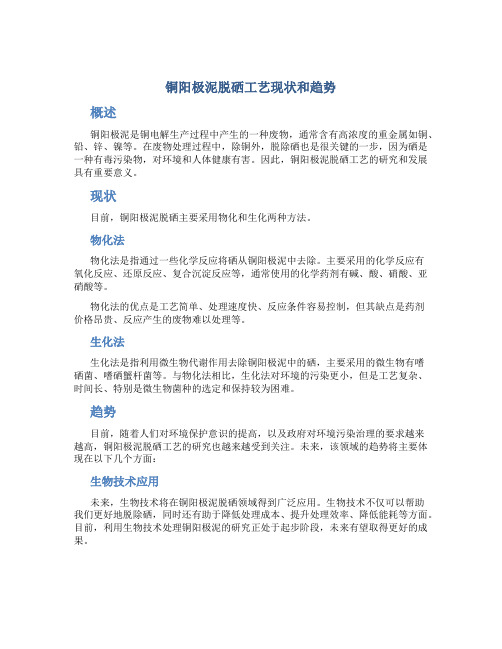
铜阳极泥脱硒工艺现状和趋势概述铜阳极泥是铜电解生产过程中产生的一种废物,通常含有高浓度的重金属如铜、铅、锌、镍等。
在废物处理过程中,除铜外,脱除硒也是很关键的一步,因为硒是一种有毒污染物,对环境和人体健康有害。
因此,铜阳极泥脱硒工艺的研究和发展具有重要意义。
现状目前,铜阳极泥脱硒主要采用物化和生化两种方法。
物化法物化法是指通过一些化学反应将硒从铜阳极泥中去除。
主要采用的化学反应有氧化反应、还原反应、复合沉淀反应等,通常使用的化学药剂有碱、酸、硝酸、亚硝酸等。
物化法的优点是工艺简单、处理速度快、反应条件容易控制,但其缺点是药剂价格昂贵、反应产生的废物难以处理等。
生化法生化法是指利用微生物代谢作用去除铜阳极泥中的硒,主要采用的微生物有嗜硒菌、嗜硒蟹杆菌等。
与物化法相比,生化法对环境的污染更小,但是工艺复杂、时间长、特别是微生物菌种的选定和保持较为困难。
趋势目前,随着人们对环境保护意识的提高,以及政府对环境污染治理的要求越来越高,铜阳极泥脱硒工艺的研究也越来越受到关注。
未来,该领域的趋势将主要体现在以下几个方面:生物技术应用未来,生物技术将在铜阳极泥脱硒领域得到广泛应用。
生物技术不仅可以帮助我们更好地脱除硒,同时还有助于降低处理成本、提升处理效率、降低能耗等方面。
目前,利用生物技术处理铜阳极泥的研究正处于起步阶段,未来有望取得更好的成果。
合理处理废弃物未来,随着科技的发展和环保的重视,铜阳极泥脱硒工艺将逐渐向着绿色、环保、高效、智能的方向发展。
合理处理废弃物,降低对环境的影响,将成为未来铜阳极泥脱硒工艺发展的重要方向之一。
增加循环利用铜阳极泥本身是一种可回收资源,循环利用对于环保和经济发展同样重要。
未来,随着铜阳极泥脱硒工艺的发展,增加循环利用将是该领域的重要发展方向之一。
结论铜阳极泥脱硒工艺在未来将迎来前所未有的发展机遇。
通过对现有工艺的整合和创新,依靠生物技术的进一步发展和合理处理废弃物的实施,以及增加循环利用等措施的推广,我们有望更好地实现铜阳极泥脱硒工艺的环保、高效、绿色发展。
从铜阳极泥处理分铜后液中回收硒和碲
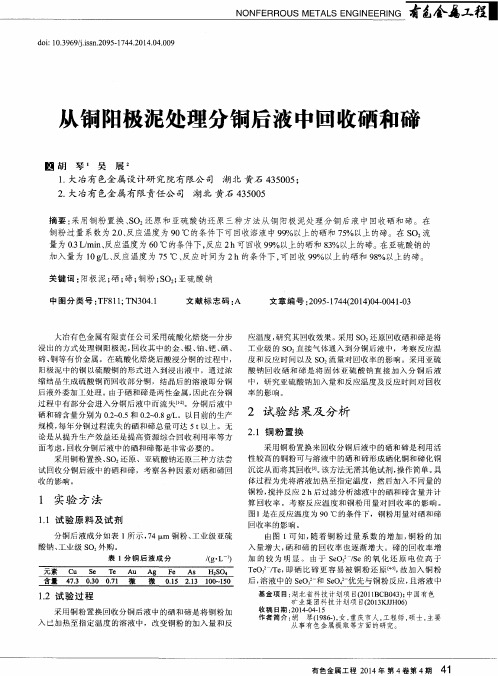
d o i : 1 0 . 3 9 6 9 d . i s s n . 2 0 9 5 — 1 7 4 4 . 2 0 1 4 . 0 4 . 0 0 9
从铜 阳极泥处理 分铜后液 中回收硒和碲
髓 胡 琴 吴 展 1 . 大冶有 色金 属设计研 究院有 限公 司 湖北 黄石 4 3 5 0 0 5 ; 2 . 大冶有 色金 属有 限责任公 司 湖北 黄石 4 3 5 0 0 5
率 的影 响 。
硒和碲含量分别 为 0 . 2 ~ 0 . 5和 0 . 2 ~ 0 . 8 L 。以 目前 的生产 规模 , 每年分铜过 程流失的硒和碲 总量可达 5 t 以上 。无
论 是 从 提 升 生 产 效 益 还 是 提 高 资 源 综 合 回 收 利 用 率 等 方 面考虑 , 回 收 分 铜 后 液 中 的硒 和 碲 都 是 非 常 必 要 的 。 采用铜粉置换 、 S O : 还 原 、 亚硫 酸 钠 还 原 三 种 方 法 尝 试 回 收 分 铜 后 液 中 的硒 和 碲 ,考 察 各 种 因 素对 硒 和 碲 回 收 的影 响 。
摘要: 采用 铜粉 置换 、 S O : 还原和亚硫酸钠 还原三种方 法从 铜 阳极泥处理分铜后 液 中回收硒 和碲。在 铜粉过量 系数为 2 . 0 、 反应温度为 9 0 ℃的条件下可 回收溶液 中 9 9 %以上的硒和 7 5 %以上的碲 。在 S O : 流 量为 0 - 3 L / mi n 、 反应温度为 6 0 ℃的条件下, 反应 2 h可回收 9 9 %以上 的硒和 8 3 %以上的碲。在亚硫酸钠的 加入量为 1 0 g / L、 反应温度为 7 5 ℃、 反应时间为 2 h的条件下 , 可回收 9 9 %以上的硒和 9 8 %以上的碲 。 关键词 : 阳极 泥; 硒; 碲; 铜粉 ; S O 2 ; 亚硫 酸钠
铜阳极泥的氧化焙烧除硒

世上无难事,只要肯攀登
铜阳极泥的氧化焙烧除硒
氧化焙烧一般是在烧重油的小平炉或有烧煤火床的小反射炉、或马弗炉中进行的。
为使阳极泥中的硒尽可能完全氧化,炉膛内阳极泥层的厚度通常不大于100mm,并需进行周期性搅动和维持炉内足够的抽力。
在充分供入空气的条件下,每炉培烧时间为6~8h。
氧化焙烧的目的是为了使大部分硒氧化呈氧化硒(SeO2)挥发,并通过收尘系统(气体洗涤器或湿式电收尘器)予以回收。
当炉温在500℃或低于此温度时,硒化物大部分转化为亚硒酸盐。
2MeSe+3O2 2MeSeO3
炉温上升到650℃或更高时,硒便生成二氧化硒并挥发。
MeSe+O2 Me+SeO2↑
根据氧化焙烧实践,炉温在450~500℃时,硒的挥发率不会高于25%。
但当炉温达650~700℃,并在后期升温到750~800℃时,可以挥发除去阳极泥中90%的硒。
氧化焙烧时,铜生成氧化铜或氧化亚铜。
砷、锑主要生成难挥发的五氧化物,少量生成三氧化物挥发。
碲与硒相似,但前者的氧化速度小,挥发除去不多。
氧化焙烧时,硒的回收率不仅与二氧化硒的挥发率有关,而且也与所用的收尘设备有关。
这是由于焙烧挥发的二氧化硒进入收尘器后,遇水便会溶解而生成可溶性的亚硒酸。
当炉气中所含的(从阳极泥中来的)金属铜粉、没燃烧完的煤粉和二氧化硫及其生成的硫酸以及收尘设备的金属铁等与亚硒酸作用发生的一系列副反应,把亚硒酸还原成金属硒,或生成不溶性的硒化物沉淀,而降低硒的回收率。
且焙烧烟尘中往往导致贵金属的损失。
因此,氧化焙烧法已多。
铜阳极泥中金银及有价金属的回收

前言目前,国内外铜阳极泥处理仍以传统的火法工艺为主,因其操作环境差、污染严重、生产周期长、有价金属得不到综合利用等诸多问题而面临挑战。
此外, 火法工艺对中小企业来说,投资大、设备利用率低、铅害难解决。
工艺流程从铜阳极泥中回收金银及有价金属的工艺流程,见图1。
硫酸化焙烧回收硒在硫酸化焙烧过程中,硒以SeO2 形式挥发,经水吸收生成亚硒酸,而亚硒酸很容易与烟气中的SO2 发生反应,生成粗硒,铜阳极泥经焙烧后,硒的挥发率在98 %以上,产出的粗硒易精镏成精硒〔1~2〕,实现硒的回收。
焙烧后的蒸硒渣含硒约0. 1 %~0. 3 % , 经过焙烧, 阳极泥中的铜转化为可溶性的硫酸铜, 碲则转化为氧化物, 有利于后工序的铜、碲浸出与回收。
低酸浸铜在蒸硒渣中, 加入少量硫酸(或直接用水浸出) 进行低酸分铜, 铜以硫酸铜的形式尽可能地进入溶液, 实现铜与渣的分离。
在实际生产中, 为防止银以硫酸银形式溶出, 分铜时, 须加入足量的NaCl , 使Ag2SO4 全部转化为AgCl 沉入渣中, 避免银的流失。
此外,分铜过程中碲会以硫酸碲形式进入液相,且酸度越高、浸出率越高,为了提高碲的回收率,应控制好反应终点酸度。
一般情况下,控制硫酸终酸为10~14g/ L ,浸出温度80~85 ℃,反应时间3h ,固液比1∶4~5 ,铜的浸出率> 98 %。
过滤后的含铜液经净化处理后,可返电解车间。
为提高电铜质量,该液开路处理,制取碱式碳酸铜,供亚砷酸车间作浸砷剂使用。
碱浸回收碲脱铜后的分铜渣,用NaOH溶液浸溶,其目的是使碲转化为可溶性的亚碲酸钠(Na2O3Te),实现分碲。
金的提取和铋铂钯的回收分碲渣采用硫酸、氯酸钠、氯化钠分金〔2〕。
使物料中的金以HAuCl4 形式溶出,NaCl 的作用在于提供足量的氯离子, 在分金条件下, 铂、钯、铅、铋也会大量浸出。
为消除生产中的铅害, 净化分金液、分金作业终点时, 利用PbCl2 的特性, 采用强制冷却方式使PbCl2 重新回到渣中还原作业后,铋、铂、钯全部进入金还原后液,先加30 %的NaOH 中和还原后液至pH 为0. 5~1. 0 , 改用碳酸钠调pH 值至2. 5~3 , 铋几乎全部发生水解、沉积。
铜阳极泥微波处理回收铜和硒的技术方法

铜阳极泥微波处理回收铜和硒的技术方法一,概述铜阳极泥微波处理回收铜和硒的技术方法是湿法冶金技术方法,特别涉及一种采用微波处理从铜阳极泥中回收铜和硒的方法。
具体是筛去铜阳极泥中颗粒直径大于5mm 的沙粒类杂质,然后加入浓度为 20~500g/L 的硫酸调浆,控制铜阳极泥浆料的重量浓度在1~30%,将铜阳极泥浆料臵于微波炉中,向铜阳极泥浆料中通入或加入氧化剂,调节微波频率为1500~3500MHz,微波加热功率为 120~700w,在常压下浸出反应 1~30min,铜阳极泥中的铜以 CuSO4形式浸出,硒以H2SeO3、 SeSO3等形式浸出。
本发明方法缩短了铜阳极泥的处理时间,加大了处理量,提高了铜和硒的脱除率,使铜阳极泥中其他有价金属走向合理且集中,有利于综合回收,既降低了能耗,又不需要特殊的高压装备,同时具有较快的浸出速度。
二,技术方法基本原理铜阳极泥微波处理回收铜和硒的技术方法属于湿法冶金技术方法,是关于铜阳极泥微波处理回收铜和硒的技术方法,铜在电解精炼时,在直流电作用下阳极上的铜和电位较负的贱金属溶解进入溶液,而正电性金属,如金、银和铂族金属它们在阳极上不进行电化学溶解,而以极细的分散状态落入槽底成为铜阳极泥。
铜阳极泥含有大量的贵金属和稀有元素,是提取贵金属的重要原料。
为了更好地富集稀贵金属元素,并有利于其他有价元素的回收,需要对阳极泥进行预处理,即将阳极泥中影响后续分离工艺显著的非贵金属元素先行解离出来。
铜在铜阳极泥中占有极大的比例,而且它的存在对后续的贵金属分离有重大的影响,因此需要对其进行预处理回收,以降低后续工作的试剂耗量和缩短生产周期。
硒在铜阳极泥中往往与金属等形成稳定的硒化物合金,各种硒化物由于性质十分稳定,使脱硒过程十分困难。
对于铜阳极泥预处理脱铜和收硒,目前国内外采用较多的方法是硫酸盐化焙烧硫酸浸出法、氧化焙烧硫酸浸出法、常压空气搅拌硫酸直接浸出法等。
火法工艺中,焙烧过程存在高能耗、操作环境差以及产生的环境污染等问题,至今仍是一个技术难题;而常压酸浸除铜过程可以不产生二氧化硫,但由于空气氧化法的反应温度不能很高(最高不超过 90℃),因此反应强度较弱、反应时间较长,需要24小时甚至更长时间完成脱铜任务,并且脱铜率和脱硒率低,脱铜率只有60~70% 左右而脱硒率更是小于 30%。
铜阳极泥脱硒工艺现状和趋势

铜阳极泥脱硒工艺现状和趋势前言随着工业的发展,大量的废水被排放到环境中,其中含有大量的重金属和有害物质,严重危害着生态环境和人体健康。
铜阳极泥是一种有毒有害的工业废水,其中的含硒量尤其高,对生态环境和人体健康具有极大的危害。
因此,为有效处理铜阳极泥中的硒元素,降低对环境的污染,铜阳极泥脱硒工艺得到了广泛的关注和研究。
现状目前,铜阳极泥脱硒的主要工艺包括生物法、化学还原法、电化学法等。
下面针对这几种工艺分别进行介绍:生物法生物法是指通过利用在性质和结构上具有还原性的微生物对铜阳极泥进行脱硒的一种方法。
该方法具有成本低、无副产物、可持续等优点,但存在处理周期长、操作难度大、受环境因素干扰等缺点。
化学还原法化学还原法是指利用还原剂将氧化态的H2SeO4还原成无害的H2SeO3的方法。
该方法具有操作简单、处理效果好等优点,但存在还原剂成本高、产生大量的废污水等缺点。
电化学法电化学法是指通过电化学反应对铜阳极泥中的硒元素进行脱除的一种方法。
该方法的处理效率高、处理效果好、无需化学药剂、操作简单等优点,但存在处理时间长、设备成本高、操作技能要求高等缺点。
趋势随着国内外环保法律法规的不断升级,环保和能源领域成为了全球关注的焦点,对于研究铜阳极泥脱硒技术的需求也越来越大。
在未来,铜阳极泥脱硒技术将会趋向于高效、环保、低成本的方向发展。
以下是未来铜阳极泥脱硒技术的几个趋势:先进的电化学技术随着电化学技术的发展,基于电解液动力学、生物产气、反应速率提高等特点,先进的电化学技术将发挥出巨大的作用。
例如,新型的电化学氧化还原处理技术、电化学脱色技术等。
合成新型的功能材料新型功能材料的开发将对铜阳极泥的处理提供更多的选择。
例如,利用铁基材料和微生物相结合可以实现高效、无副产物的脱硒过程等。
智能化技术的应用智能化技术的应用将提高铜阳极泥脱硒的工业化应用水平。
例如,可以开发智能化的电解池技术,实现自动调节和控制电解条件的功能等。
真空蒸馏法从铜阳极泥中回收硒的研究
11 8 7年 , 著名 瑞典 化 学家 J JB r l s 研究 .. e ei 在 z u
黄铁矿 制酸产生 的红 色 酸泥 时 发现 此元 素 , 以希 并
腊月亮 女 神 Sln e e一词 取 名 为 Sl im, e e nu 后来 中文 e
将其译 为硒 。
单 质硒等 , 还可 以与 阳极 泥 中的部 分金 、 形成硒 硒 银
0 2 以下 。 .%
( )采 用离心过 滤 , 2 解决 了漂洗 过程 的水 量 、 时
玻璃 、 陶瓷 、 化工 、 冶金 位等 问题 。 ( )根 据统计结 果表 明 , 3 工艺优 化后 , 直收率 硒
我 国硒 产量近年 来一 直保 持增 长 态势 ,0 3年 20
到 9 .% 。 99
关键词 : 真空蒸馏 ; 阳极泥 ; 铜 提纯 ; 硒
中图 分 类 号 : 4 . T 35 文 献标 识 码 : B
转 入 阳极 泥 。 阳极 泥 中 的硒 的品 位 为 4 ~1% 。 % 2
1 日 J I 舌
硒 在 阳极 泥中与铜 、 以化合 物 的形 式存在 , 银 主要有 A S ( 色 ) C : e 黑色 ) C S ( ge 绿 、us( 、 u e 灰色 ) C A S 、 u g e和
由 8% ~ 6 2 8 %提 高到 9 % 以上 , 2 硒品位 高于 9 % 。 8
产 量为 26t占世界 总产量 的 1%左 右 。但我 国的 9 , 2 自产硒远不 能满足 国 内的需 求 , 每年 需从 日本 、 墨西
哥等 国家进 口大 量 的产 品硒 或 原 料硒 。 目前 , 产 硒 品 主 要 有 工 业 硒 (9 % ) 精 硒 (99 ~ 9 .5 、 9 .% 9.9 ) 9 9 % 和高纯硒 ( 含量 >9 .9 % ) 1 999 。
硒的冶炼用途
硒的冶炼用途
硒是一种半导体元素,主要从铜有色冶炼厂的阳极泥等综合回收。
# L1 j, D9 d& y1 K5 l/ S+ K
1 ^' {, O! l' h1 D+ x二氧化硒是最重要的硒化合物之一,在制药、化工、冶金等许多领域有广泛应用。
其中主要用途之一就是作电解金属锰的添加剂。
尽管其作用机理仍众说纷纭,但大家公认硒化合物提高了氢的超电压,从而使电解过程的电流效率从极低跃升到80%~90%以上,而且对金属锰的晶体结构及沉积形态产生好的影响,并降低了对电解液的净化要求。
* h/ E) q; F: e0 t
7 j! C7 I2 z9 t x/ p" g0 w$ @) x随着国民经济的飞速发展,人们对钢铁的需求日益增长,特别是对低合金钢(如锰钢)的需求大大地带动了对金属锰工业的发展,从而导致对二氧化硒的需求猛增,致使其价格大幅上涨。
由于理论上1吨硒可生产1.4吨以上二氧化硒,且二氧化硒的价格还高于精硒。
因此,利用粗硒生产二氧化硒或进一步精制成纯硒具有重要的经济意义。
回收铜阳极泥中硒的方法
回收铜阳极泥中硒的方法一、方法概要本方法研究回收铜阳极泥中硒的方法技术,其特点是它包括如下工艺步骤:铜阳极泥加铜粉、浓硫酸浆化后送至回转窑焙烧,铜粉在焙烧时生成二氧化硫气体,生成的气体能够起到解决蓬松焙砂、破坏硫酸银、硫酸铅表面张力大问题,从而降低了焙砂粒度,既保证了铜阳极泥中硒的焙烧效果又满足了下道湿法工艺处理的要求;本工艺设备配置简单,尤其适用于复杂含高银、高铅、低铜的铜阳极泥的处理,操作稳定便于控制,资源综合利用率高。
二、基本技术原理本方法属于冶金工艺技术领域,具体地讲是研究回收铜阳极泥中硒的方法,特别适用于复杂含高银、高铅、低铜的铜阳极泥的处理。
目前,铜阳极泥处理主要工艺为,阳极泥经浓硫酸浆化后直接回转窑焙烧,产出适合湿法工艺要求的焙砂;若含银量在 25-30%,铅含量在 20-28% 的铜阳极泥经常规焙烧后产生的焙砂的粒度较大,通常呈块状;硒回收率极低,焙砂质量不能满足湿法处理的要求。
三、主要技术内容本方法的目的是克服上述已有技术的不足,而提供一种回收铜阳极泥中硒的方法,主要解决现有的工艺对银含量 25-30%、铅含量 20-28% 的铜阳极泥硒回收率极低的问题。
本方法的技术方案是:一种回收铜阳极泥中硒的方法,其特殊之处在于它包括如下工艺步骤:a 将浓硫酸加入到反应釜中,浓硫酸与铜阳极泥的液固重量比为 0.8-1.5:1,同时加入适量的铜粉,铜粉加入后使物料中含铜量 10%,开启一次浆化 6h,搅拌料浆成糊状;b 反应完成后,将料浆均匀投入回转窑中进行焙烧,料浆在窑内停留 3-5h,焙砂流入料斗,反应产生的二氧化硫和二氧化硒进入吸收塔进行还原反应,产出粗硒;反应原理:2H2SO4( 浓 )+Cu CuSO4+SO2+2H2O ;SeO2+H2O=H2SeO3 ;H2SeO3+2SO2+H2O=2H2SO4+Se ;c将焙砂加入反应釜内,再加入水、浓硫酸搅拌;在85℃恒温下反应 2h ;过滤后,得到浸出后液和浸出渣;d 浸出后液通过氯化沉银、铁粉置换工艺得到银粉;e 浸出渣通过氯化分金、二氧化硫还原工艺得到金粉。
铜阳极泥的综合回收
银电解精炼的电解液由AgNO3、HNO3的水溶液组 成。电解液含Ag30~150g/L,含HNO32~15g/L ,含Cu40g/L。 为防止阴极析出银的化学溶解和保持电解液 良好的导电性,需往电解液中加入适量的KNO3 、NaNO3。 电解液中银离子浓度的高低,视电流密度及 阳极品位而定。
我国银电解精炼的主要技术条件
银电解阳极泥的处理
银电解精炼产出的阳极泥,占阳极重量的8%左右, 一般含金50% ~70%,含银30% ~40%,还有少量杂质。 银电解阳极泥的处理方法有两种,一种是硝酸分离法 ;一种是进行第二次电解提银。 硝酸分离法是把阳极泥加入硝酸中,银溶解而金不溶解。 此法虽简单,但是耗酸多,银回收麻烦,已不使用。 第二次电解提银,是把第一次电解的阳极泥熔铸成阳极板, 再进行一次电解提银。 二次电解提银可直接在一次电解的电解槽中进行,放 进一部分一次电解的阳极泥铸成的阳极板即可。第一次电 解提银产出的阳极泥成为一次阳极泥(一次黑金粉);第 二次产出的,成为二次阳极泥(二次黑金粉)。阳极泥色 黑,含金多,故称为黑金粉。 二次黑金粉产出率一般为二次阳极中的35%,含Au90%以 上,含Ag6% ~8%,其余为铜杂质。
银的电解精炼
电解精炼是为了得到纯度较高的电解银。 供电解用的银原料,一般要求阳极板中含铜小于5%, 金银总量在95%以上,其中含金量不超过三分之一。 银电解精炼的基本原理 银电解精炼是用阳极泥熔炼所得的金银合金或银合金作 阳极,以银片、不锈钢片或钛片作阴极,以硝酸、硝酸银 的水溶液作电解液,在电解槽中通以直流电,进行电解。 银电解精炼的电解过程: Ag(阴极)∣AgNO3、HNO3、H2O、杂质∣Ag杂质(阳极) 阴极上是主要是银的析出,还有少部分与硝酸的反应。 阳极上,发生银和贱金属杂质氧化溶解反应。
- 1、下载文档前请自行甄别文档内容的完整性,平台不提供额外的编辑、内容补充、找答案等附加服务。
- 2、"仅部分预览"的文档,不可在线预览部分如存在完整性等问题,可反馈申请退款(可完整预览的文档不适用该条件!)。
- 3、如文档侵犯您的权益,请联系客服反馈,我们会尽快为您处理(人工客服工作时间:9:00-18:30)。
从铜阳极泥中综合回收硒马光位201010303136摘要:本文详细讨论了从铜阳极泥中综合回收重有色金属和稀、贵金属的火法———电解,焙烧———湿法及全湿法等主要工艺流程;并简要分析比较了3类流程的技术、经济特点。
关键词:铜阳极泥;综合回收;贵金属;硒1 引言铜阳极泥由阳极铜在电解精炼过程中不溶于电解液的各种物质所组成,其成分及产率主要与铜阳极成分、铸锭质量及电解技术条件有关。
阳极泥产率一般为012~1%,其主要成分(%)为:Cu10~35、Ag1~28、Au011~115、Se2~23、Te015~8、S2~10、Pb1~25、Ni011~15、Sb011~10、As011~5、Bi011~1,铂族金属微量(约70g/t),H2O25~40。
阳极泥中各元素的赋存状态较复杂。
其中以金属状态存在的有铂族金属、金、大部分铜和少量银;硒、碲、大部分银、少量铜和金则以金属硒化物及碲化物形式存在,如Ag2Se、Ag2Te、CuAgSe、Au2Te、AgAuTe 和Cu2Se;还有少量银和铜为AgCl、Cu2S和Cu2O;其余金属则大多数为氧化物、复杂氧化物或砷酸盐、锑酸盐。
因此,阳极泥处理是根据所含各种金属及化合物的物理化学性质,选择适当的化学冶金方法以提取金、银、铜、硒、碲,并附带回收其余重金属和铂族元素。
由于各电解铜厂的阳极泥组成和生产规模不同,各厂处理阳极泥的工艺流程也不同。
但一般均包括下列主要部分:(1)分离回收铜、硒;(2)提取金、银;(3)从有关中间产物中回收其余有色重金属和稀、贵金属;(4)各种粗金属和化合物的精炼、提纯以产出所需纯度的最终产品。
目前国内外应用最多的为火法———电解流程,其次为火法———湿法流程,最近还开始采用全湿法流程。
2 火法———电解流程常用流程一般包括阳极泥硫酸盐化焙烧蒸硒,熔炼回收金、银和贵金属电解精炼3部分。
2.1.1盐化焙烧铜阳极泥和浓硫酸(料、酸比为1∶0175~019)经浆化槽机械搅拌混匀后连续加入回转窑,加料速度决定于炉料含硒量。
窑内温度由进料端的280~300℃逐渐提高至出料端的550~650℃,窑内负压为50~160Pa。
窑中部为铜、镍、硒、碲和部分银的硫酸化反应,窑尾高温区则使生成的SeO2充分挥发。
含有SeO2、SO2和SO3的混合烟气经窑头排气管用真空泵抽入吸收塔。
SeO2被塔内水溶液吸收成为亚硒酸,并被烟气中的SO2还原为含硒9715~9815%的粗硒粉。
后者可提纯至99199%的精硒产品。
烧渣由回转窑出料端排出,送往浸出槽酸浸脱铜,常用浸出温度90℃。
经洗涤过滤后浸出渣送贵铅炉处理。
浸出液送往置换槽,加铜置换沉银,直到用盐酸检验时无明显白色氯化银沉淀为止。
置换沉淀经洗涤过滤,得到的粗银粉含银90%以上,可送往分银炉处理;滤液含铜大于40g/L,则返回铜电解车间。
2.1.2还原熔炼和氧化精炼上述脱铜渣一般含Au016~1%,Ag5~12%,Cu1~2%,送往转炉还原熔炼。
使用苏打和萤石作熔剂,煤粉或焦粉和铁屑作还原剂,在1100~1200℃的熔炼温度下发生造渣及还原反应。
生成的硅酸盐、砷酸盐和锑酸盐即组成稀渣。
稀渣含金、银量少,一般返回铜或铅熔炼系统。
炉料中的PbO、PbSO4及PbS将被碳和铁还原为铅,某些重金属氧化物也同时被还原而形成以铅为主的多元合金(贵铅),而将金、银和铂族元素富集溶解于其中。
随后通风氧化贵铅以除去部分重金属杂质,所得贵铅含Au017~113%、Ag12~20%、Cu3~8%、Pb20~25%、Sb15~20%、Bi013~018和Sn5~6%。
氧化期及还原后期的粘渣含金、银较高,可返回转炉还原熔炼。
转炉烟尘主要由低价砷、锑的氧化物和PbO组成,可用于提取砷、锑。
贵铅送往另一转炉(分银炉),在900~1200℃条件下进行氧化精炼。
贵铅熔化后进行表面吹风氧化,使大量的砷、锑和铅等杂质一部分成为挥发性氧化物进入烟尘,一部分成为非挥发性氧化物进入炉渣。
当炉内合金品位达到75~80%(Au+Ag)时,加入硝酸钠和碳酸钠,使碲迅速氧化形成碲酸钠渣,其含碲量为3~5%。
碲渣用水浸净液和电解提取法制得含Te>98%的电解碲。
除碲后将炉温升至1200℃,继续吹风氧化并加入硝酸钠以除去残余的铜、硒、碲等杂质,使合金品位提高至95%(Au+Ag)以上,即可出炉浇铸成银电解阳极板。
分银炉产出的各种炉渣和烟尘均返回还原熔炼炉处理。
2.1.3精炼2.1.3.1炼用氧化精炼浇铸的粗银板为阳极,外套涤纶隔膜袋,以纯银片、不锈钢板或钛板作阴极,以硝酸银溶液作电解液,在电解槽中通直流电进行电解精炼。
银电解技术条件:电解液组成为Ag80~120g/L,HNO32~5g/L,Cu<50g/L;电流密度为250~300A/m2;电解液温度35~55℃;电解液流量018~2L/分・槽;槽电压115~315V;同极中心距离高达100~150mm,并用玻璃棒或塑料棒在阴、阳极之间不断搅动,以防止阴、阳极间短路。
阴极上析出的银粉沉入槽底不锈钢盘内,定期取出。
目前多用立式电极电解槽,它用硬聚氯乙烯焊成。
槽内用未达到槽底的隔板横向隔成若干小槽,各小槽底部相通,电解液可循环流动。
槽底连通处设有涤纶布制成的带式运输机,专供运出槽内银粉用。
银粉经洗涤、烘干后送往中频感应电炉熔化铸锭,银锭品位为99199%。
金、铂、钯的电极电位都高于银,电解时将不电化学溶解,而以固态形式进入阳极泥,并落入隔膜袋中。
重金属杂质电极电位低于银,电解时与银一起电化学溶解转入溶液,既降低电解液的导电性,又增加硝酸消耗。
其中铅和铋进入电解液后发生水解,呈二氧化铅和碱式硝酸铋沉淀转入阳极泥中;阳极中砷与镉含量通常很少,而影响不大;铜和锑的电极电位与银接近,在电解液中积累到一定程度后会在阳极析出,影响电解银纯度,故需要严格控制。
此外,阳极中硒、碲含量少,常以Ag2Se、Ag2Te、Cu2Se、Cu2Te形式存在,其电化学活性很小,电解时将全部落入阳极泥中。
落入阳极袋内的阳极泥被熔铸成合金板,作为二次银电解精炼的阳极。
二次银电解产生的阳极泥经洗涤、烘干后,即可熔铸成粗金阳极,送往金电解精炼。
2.1.3.2以粗金板(含金约90%)作阳极,外套耐酸布袋;纯金片作为阴极。
电解槽一般用硬塑料制成,槽内电极并联,槽与槽串联。
电解液一般含Au250~350g/L,HCl200~350g/L,可用金阳极隔膜电解造液法配制。
电解液不加热,依靠电解电流可保持50~60℃。
溶液不流动循环,而采用空气连续搅拌。
常用电流密度200~700A/m2,槽电压012~014V。
银在电解时电化学溶解,并与盐酸作用生成AgCl而附着于阳极表面。
当金阳极含银>5%时将形成AgCl薄膜使阳极钝化。
因此在电解过程中除通入直流电以外还需叠加电流强度更大的交流电,进行不对称的脉动电流电解。
这样阳极上将周期地出现正半周期和短暂的负半周期。
在正半周期内发生阳极极化,银溶解形成AgCl膜;在负半周期内发生阴极极化,将有少量紧附电极上的AgCl电化学还原(AgCl+e=Ag+Cl-,ψ0=0122V)。
更为重要的是阳极极性的变化将引起阳极上界面张力的瞬间显著改变(电毛细现象),而使AgCl薄膜松动、脱落。
最好还要定期取出阳极,洗去表面残留的氯化银。
一般交流电与直流电比值为111~115。
此外使用脉动电流还可使歧化反应3AuCl-2ΩAuCl-4+2Au+2Cl-产生的金粉量显著降低,即显著降低阳极泥含金量,提高金电解直收率。
金阳极泥主要含AgCl和Au,取出经洗涤、烘干、还原后熔铸二次银阳极送回银电解。
电解金板经氨水、硝酸分别煮洗和烘干后,送往中频感应电炉熔化铸锭,获得含金>99195%的纯金锭。
金阳极中的杂质一般是银、铜、铅、锌和少量铂族金属。
这些杂质比金的电位低,将电化学溶解进入溶液。
重金属杂质一般含量低,对电解过程影响不大;若铂钯在溶液中大量积累,就可能与金一起在阴极析出。
故一般当电解液中铂族金属含量达10g/L时,就要作为废电解液放出,再用锌粉置换或还原剂(FeSO4、Na2SO3、SO2)还原沉淀回收金;溶液则送去提取铂、钯。
2.1.4的回收和提纯2.1.4.1提纯往还原沉金后的金电解废液中加入沉铂所需理论量115~2倍的工业氯化铵,并在常温下不断搅拌,即生成蛋黄色的(NH4)2・PtCl6沉淀;低价钯不被NH4Cl沉淀而保留于溶液中。
沉铂过程是否完全,可用5%NH4Cl溶液检验。
经长时间沉清、过滤、洗涤沉淀后,氯铂酸铵被灼烧成粗铂;滤液则用于回收钯。
粗铂用王水在加热条件下溶解,并加盐酸赶硝,再加FeSO4以沉淀残余微量金,并过滤。
然后往滤液中加稍过量的NH4Cl,使铂再次沉淀为氯铂酸铵,铂盐用盐酸、氯化铵溶液洗涤。
如此反复溶解沉淀3~5次,即可获得纯氯铂酸铵。
后者烘干后加热至360~400℃,即发生分解反应3(NH4)2PtCl6△3Pt+16HCl+2NH4Cl+2N2↑,而产出纯度为99195~99199%的海绵铂产品。
此外工业上也可使用氧化水解法精炼粗铂。
即往铂溶液中加入溴酸钠,使某些杂质如Ir(Ⅳ)、Fe(Ⅱ)等氧化为高价,再加入NaOH溶液至pH=7~8,即可水解沉淀,彻底除杂。
经一次水解除杂和一次氯化铵沉铂后,即可灼烧氯铂酸铵沉淀而获得品位为9919~99199%的纯铂。
若经多次水解甚至可制得991999%的高纯铂。
2.1.4.2提纯沉铂后的溶液用锌置换即获得金属钯精矿。
钯的提纯可单独或结合应用氯钯酸铵沉淀法和二氧二氨络亚钯法。
其提纯步骤举例如下:(1)粗钯精矿在加热条件下用王水溶解,加盐酸赶硝后加入NH4Cl以沉淀(NH4)2PtCl6,并过滤分离铂沉淀。
(2)滤液用硝酸或Cl2使Pd(Ⅱ)氧化为Pd(Ⅳ),然后用NH4Cl使钯沉淀为(NH4)2PdCl6。
(3)氯钯酸铵经水溶解、氨络合(pH=9)即转化为Pd(NH3)4Cl2溶液,而其它残余铂族元素和贱金属杂质将水解沉淀。
过滤分离后,滤液用盐酸酸化至pH=1,即得Pd(NH3)2Cl2沉淀。
(4)二氯二氨络亚钯用氨水溶解和盐酸酸化再沉淀,如此反复提纯数次。
(5)所得纯Pd(NH3)4Cl2溶液用水合肼或甲酸还原为钯,经洗涤、烘干后即可获得纯度大于99195%的海绵钯。
上述火法———电解流程能有效地分离回收金、银、硒、碲及铂族金属,产品纯度高,金、银、硒的总回收率高达96~98%,因而在国内外获得广泛应用。
但贵金属回收工艺流程较长,返回中间产品多,直收率不高,而且熔炼过程产生有害的烟尘,需专门处理。
对于规模不大的工厂往往不得不在一段时间集中进行贵铅熔炼、精炼及金、银电解精炼过程,显著增长贵金属资金的积压。