连铸坯与钢锭质量对比
模铸在大钢锭及特殊钢生产方面的比较优势
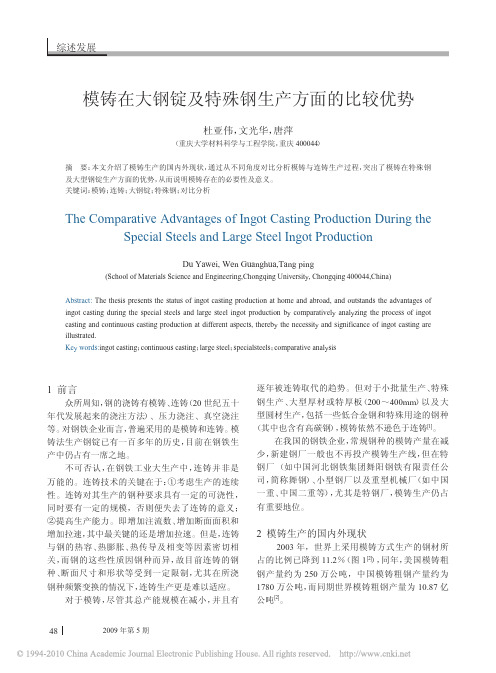
1前言众所周知,钢的浇铸有模铸、连铸(20世纪五十年代发展起来的浇注方法)、压力浇注、真空浇注等。
对钢铁企业而言,普遍采用的是模铸和连铸。
模铸法生产钢锭已有一百多年的历史,目前在钢铁生产中仍占有一席之地。
不可否认,在钢铁工业大生产中,连铸并非是万能的。
连铸技术的关键在于:①考虑生产的连续性。
连铸对其生产的钢种要求具有一定的可浇性,同时要有一定的规模,否则便失去了连铸的意义;②提高生产能力。
即增加注流数、增加断面面积和增加拉速,其中最关键的还是增加拉速。
但是,连铸与钢的热容、热膨胀、热传导及相变等因素密切相关,而钢的这些性质因钢种而异,故目前连铸的钢种、断面尺寸和形状等受到一定限制,尤其在所浇钢种频繁变换的情况下,连铸生产更是难以适应。
对于模铸,尽管其总产能规模在减小,并且有逐年被连铸取代的趋势。
但对于小批量生产、特殊钢生产、大型厚材或特厚板(200~400mm)以及大型圆材生产,包括一些低合金钢和特殊用途的钢种(其中也含有高碳钢),模铸依然不逊色于连铸[1]。
在我国的钢铁企业,常规钢种的模铸产量在减少,新建钢厂一般也不再投产模铸生产线,但在特钢厂(如中国河北钢铁集团舞阳钢铁有限责任公司,简称舞钢)、小型钢厂以及重型机械厂(如中国一重、中国二重等),尤其是特钢厂,模铸生产仍占有重要地位。
2模铸生产的国内外现状2003年,世界上采用模铸方式生产的钢材所占的比例已降到11.2%(图1[2]),同年,美国模铸粗钢产量约为250万公吨,中国模铸粗钢产量约为1780万公吨,而同期世界模铸粗钢产量为10.87亿公吨[2]。
模铸在大钢锭及特殊钢生产方面的比较优势杜亚伟,文光华,唐萍(重庆大学材料科学与工程学院,重庆400044)摘要:本文介绍了模铸生产的国内外现状,通过从不同角度对比分析模铸与连铸生产过程,突出了模铸在特殊钢及大型钢锭生产方面的优势,从而说明模铸存在的必要性及意义。
关键词:模铸;连铸;大钢锭;特殊钢;对比分析The Comparative Advantages of Ingot Casting Production During the Special Steels and Large Steel Ingot ProductionDu Yawei,Wen Guanghua,Tang ping(School of Materials Science and Engineering,Chongqing University,Chongqing400044,China)Abstract:The thesis presents the status of ingot casting production at home and abroad,and outstands the advantages of ingot casting during the special steels and large steel ingot production by comparatively analyzing the process of ingot casting and continuous casting production at different aspects,thereby the necessity and significance of ingot casting are illustrated.Key words:ingot casting;continuous casting;large steel;specialsteels;comparative analysis近年来,随着钢铁工业的不断发展,世界连铸钢的比例也在不断攀升,截至2007年,全世界连铸比高于97%的国家有25个,其中高于99%的有15个(100%的有7个)[3]。
连铸坯质量及控制方法

连铸坯质量及控制方法1、连铸坯质量的含义是什么?最终产品质量决定于所供给的铸坯质量。
从广义来说,所谓连铸坯质量是指得到合格产品所允许的铸坯缺陷的严重程度。
它的含义是:——铸坯纯净度(夹杂物数量、形态、分布、气体等)。
——铸坯表面缺陷(裂纹、夹渣、气孔等)。
——铸坯内部缺陷(裂纹、偏析、夹杂等)。
铸坯纯净度主要决定于钢水进入结晶器之前处理过程。
也就是说要把钢水搞“干净”些,必须在钢水进入结晶器之前各工序下功夫,如冶炼及合金化过程控制、选择合适的炉外精炼、中间包冶金、保护浇注等。
铸坯的表面缺陷主要决定于钢水在结晶器的凝固过程。
它是与结晶器坯壳形成、结晶器液面波动、浸入式水口设计、保护渣性能有关的。
必须控制影响表面质量各参数在目标值以内,以生产无缺陷铸坯,这是热送和直接扎制的前提。
铸坯的内部缺陷主要决定于在二次冷却区铸坯冷却过程和铸坯支撑系统。
合理的二次冷却水分布、支承辊的对中、防止铸坯鼓肚等是提高铸坯内部质量的前担。
因此,为了获得良好的铸坯质量,可以根据钢种和产品的不同要求,在连铸的不同阶段如钢包、中间包、结晶器和二次冷却区采用不同的工艺技术,对铸坯质量进行有效控制。
2、提高连铸钢种的纯净度有哪些措施?纯净度是指钢中非金属夹杂物的数量、形态和分布。
要根据钢种和产品质量,把钢中夹杂物降到所要求的水平,应从以下五方面着手:——尽可能降低钢中[O]含量;——防止钢水与空气作用;——减少钢水与耐火材料的相互作用;——减少渣子卷入钢水内;——改善钢水流动性促进钢水中夹杂物上浮。
从工艺操作上,应采取以下措施:(1)无渣出钢:转炉采用挡渣球(或挡渣锥),防止钢渣大量下到钢包。
(2)钢包精炼:根据钢种选择合适的精炼方法,以均匀温度、微调成分、降低氧含量、去除气体夹杂物等。
(3)无氧化浇注:钢水经钢包精炼处理后,钢中总氧含量可由130ppm下降到20ppm以下。
如钢包→中间包注流不保护或保护不良,则中间包钢水中总氧量又上升到60~100ppm范围,恢复到接近炉外精炼前的水平,使炉外精炼的效果前功尽弃。
连铸坯质量解析(共20张PPT)
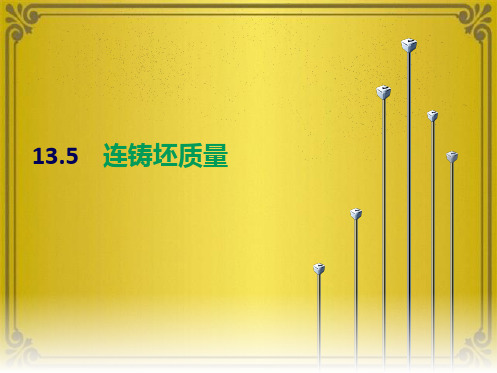
(2)二,冷区如采果用平夹稳杂的热物冷细却,小矫,直呈时铸球坯形的表,面弥温度散要分高于布质,点沉对淀钢温度质或量高的于γ影--α。响比集中存在要小些;当夹杂物大,
Your company slogan
13.5.2 连铸坯表面质量
13.5.2.1 表面裂纹
表面裂纹就其出现的方向和部位,可以分为面部纵裂纹.角部纵裂纹与横裂纹,星状 裂纹等。
纵向裂纹在板坯多出现宽面的中间部位.方坯多出现在棱角处。表面纵裂纹直接影响钢材质量。
若铸坯表面存在深度为,长度为300mm的裂纹,轧成板材后就会形成1125mm的分 层缺陷。严重的裂纹深度达10mm以上,将造成漏钢事故或废品。
(从4)表选1。用3—性大5能所于良列好5数的0据保μ可m 护以渣看的;出大,富型集夹溶杂质元物素往的母往液伴流动有是裂加剧纹中出心偏现析.的造重要成原连因。铸坯低倍结构不合格,板材分层,并
2 连铸坯表面质量 (4)选用性能良好的保护渣;
中2 间连包损铸使坏坯用表冷双面层轧质渣量钢覆盖板剂的,隔表绝面空气等,,避免对钢钢液的危二害次很氧化大。。夹杂物的大小形态和分布对钢质量的影响也不同
来看,锰-硅盐系夹杂物的外观颗粒大而浅,Al2O3系夹杂物细小而深。若不清除,会造成成品表面缺陷
,增加制品的废品率。夹渣的导热性低于钢,致使夹渣处坯壳生长缓慢,凝固壳薄弱,往往是拉漏的起因, 一般渣子的熔点高易形成表面夹渣。
敞开浇铸时,由于二次氧化.结晶器表面有浮渣。浮渣的熔点和流动性以及钢液的浸润性均与浮渣的组成
连铸坯质量对轧钢生产的影响

连铸坯质量对轧钢生产的影响
在钢铁行业生产系统中,炼钢与轧钢作为上下工序是息息相关的,从生产组织到工艺技术要求再到成本利润,只有轧钢提质降耗轧出合格的产品才能画上圆满的句号。
连铸坯质量问题主要表现在以下几个方面:1、连铸坯的纯净度:夹杂物数量、分布程度等;2、表面缺陷:角裂、纵裂、横裂、夹渣、脱方、鼓肚、凹坑、断面切割流渣等;3、内部缺陷:中间裂纹、中心偏析、内生夹杂、外来夹杂、疏松、缩孔等;4、化学成分:不稳定、不均匀等。
由于连铸坯经常性的存在以上缺陷,对轧钢生产带来很多生产事故,导致轧钢生产综合效益降低。
对作业率、成材率、合格率的提高、成品性能的稳定、成本消耗、员工的劳动强度等带来的一系列的影响。
为了更好地实现高效、快捷、均衡、顺行的生产模式,创造良好的整体效益,炼钢与轧钢就要双向挖潜提标。
首先炼钢方面要严控工艺技术要求,实实在在地提高连铸坯的质量。
其次炼钢技术管理人员、质检人员要本着下道工序为上帝的宗旨严把质量关。
再次要与轧钢系统做好联系沟通、及时跟踪、及时整改、及时优化创新,这样我们的水平才能提高,我们的整体效益才能做好。
小方坯质量的特点
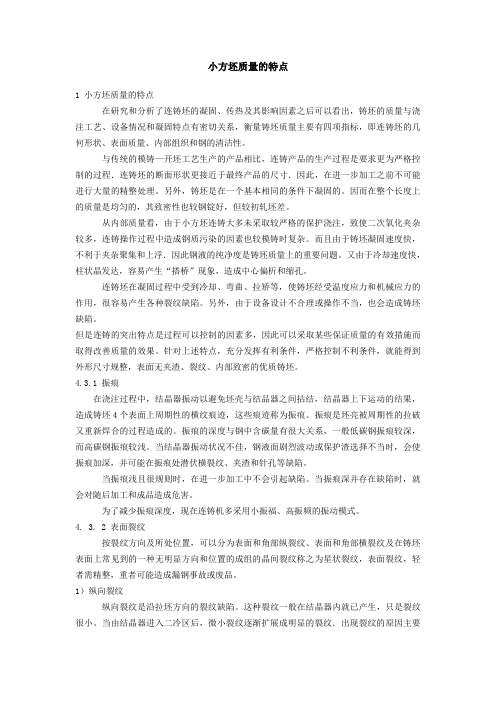
小方坯质量的特点1 小方坯质量的特点在研究和分析了连铸坯的凝固、传热及其影响因素之后可以看出,铸坯的质量与浇注工艺、设备情况和凝固特点有密切关系,衡量铸坯质量主要有四项指标,即连铸坯的几何形状、表面质量、内部组织和钢的清洁性。
与传统的模铸—开坯工艺生产的产品相比,连铸产品的生产过程是要求更为严格控制的过程.连铸坯的断面形状更接近于最终产品的尺寸.因此,在进一步加工之前不可能进行大量的精整处理。
另外,铸坯是在一个基本相同的条件下凝固的。
因而在整个长度上的质量是均匀的,其致密性也较钢锭好,但较初轧坯差。
从内部质量看,由于小方坯连铸大多未采取较严格的保护浇注,致使二次氧化夹杂较多,连铸操作过程中造成钢质污染的因素也较模铸时复杂。
而且由于铸坯凝固速度快,不利于夹杂聚集和上浮.因此钢液的纯净度是铸坯质量上的重要问题。
又由于冷却速度快,柱状晶发达,容易产生“搭桥”现象,造成中心偏析和缩孔。
连铸坯在凝固过程中受到冷却、弯曲、拉矫等,使铸坯经受温度应力和机械应力的作用,很容易产生各种裂纹缺陷。
另外,由于设备设计不合理或操作不当,也会造成铸坯缺陷。
但是连铸的突出特点是过程可以控制的因素多,因此可以采取某些保证质量的有效措施而取得改善质量的效果。
针对上述特点,充分发挥有利条件,严格控制不利条件,就能得到外形尺寸规整,表面无夹渣、裂纹、内部致密的优质铸坯。
4.3.1 振痕在浇注过程中,结晶器振动以避免坯壳与结品器之间拈结,结晶器上下运动的结果,造成铸坯4个表面上周期性的横纹痕迹,这些痕迹称为振痕。
振痕是坯亮被周期性的拉破又重新焊合的过程造成的。
振痕的深度与钢中含碳量有很大关系,一般低碳钢振痕较深,而高碳钢振痕较浅。
当结晶器振动状况不佳,钢液面剧烈波动或保护渣选择不当时,会使振痕加深,并可能在振痕处潜伏横裂纹、夹渣和针孔等缺陷。
当振痕浅且很规则时,在进一步加工中不会引起缺陷。
当振痕深并存在缺陷时,就会对随后加工和成品造成危害。
连铸小方坯的凝固组织和内部主要缺陷总结
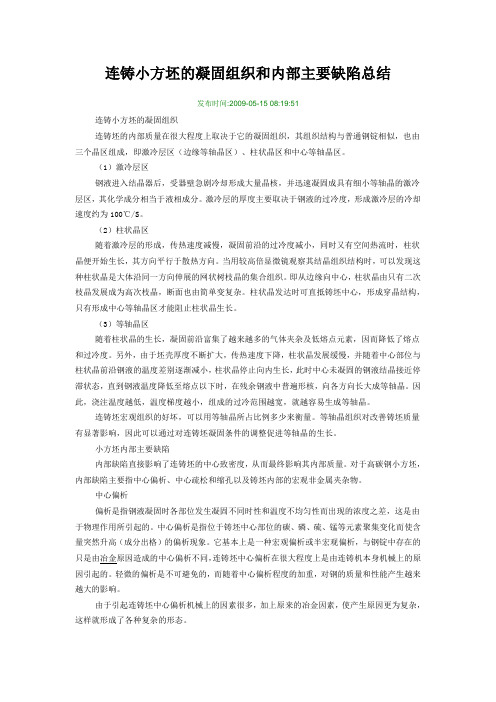
连铸小方坯的凝固组织和内部主要缺陷总结发布时间:2009-05-15 08:19:51连铸小方坯的凝固组织连铸坯的内部质量在很大程度上取决于它的凝固组织,其组织结构与普通钢锭相似,也由三个晶区组成,即激冷层区(边缘等轴晶区)、柱状晶区和中心等轴晶区。
(1)激冷层区钢液进入结晶器后,受器壁急剧冷却形成大量晶核,并迅速凝固成具有细小等轴晶的激冷层区,其化学成分相当于液相成分。
激冷层的厚度主要取决于钢液的过冷度,形成激冷层的冷却速度约为100℃/S。
(2)柱状晶区随着激冷层的形成,传热速度减慢,凝固前沿的过冷度减小,同时又有空间热流时,柱状晶便开始生长,其方向平行于散热方向。
当用较高倍显微镜观察其结晶组织结构时,可以发现这种柱状晶是大体沿同一方向伸展的网状树枝晶的集合组织。
即从边缘向中心,柱状晶由只有二次枝晶发展成为高次枝晶,断面也由简单变复杂。
柱状晶发达时可直抵铸坯中心,形成穿晶结构,只有形成中心等轴晶区才能阻止柱状晶生长。
(3)等轴晶区随着柱状晶的生长,凝固前沿富集了越来越多的气体夹杂及低熔点元素,因而降低了熔点和过冷度。
另外,由于坯壳厚度不断扩大,传热速度下降,柱状晶发展缓慢,并随着中心部位与柱状晶前沿钢液的温度差别逐渐减小,柱状晶停止向内生长,此时中心未凝固的钢液结晶接近停滞状态,直到钢液温度降低至熔点以下时,在残余钢液中普遍形核,向各方向长大成等轴晶。
因此,浇注温度越低,温度梯度越小,组成的过冷范围越宽,就越容易生成等轴晶。
连铸坯宏观组织的好坏,可以用等轴晶所占比例多少来衡量。
等轴晶组织对改善铸坯质量有显著影响,因此可以通过对连铸坯凝固条件的调整促进等轴晶的生长。
小方坯内部主要缺陷内部缺陷直接影响了连铸坯的中心致密度,从而最终影响其内部质量。
对于高碳钢小方坯,内部缺陷主要指中心偏析、中心疏松和缩孔以及铸坯内部的宏观非金属夹杂物。
中心偏析偏析是指钢液凝固时各部位发生凝固不同时性和温度不均匀性而出现的浓度之差,这是由于物理作用所引起的。
冶金质量分析
1.反应速度通常可用下式表示: ,n 、c 、K 分别为反应级数、反应物浓度及速率常数,其K 与温度有关.2. ,A 、E 分别代表常数及活化能,它有决定反应机理和预测反应速度的功能。
3.反应速度理论:碰撞理论和绝对反应速度理论①碰撞理论 根据气体动力学理论,对均相来说,任何反应的产生,必须满足以下的两个条件:1)分子与分子之间的碰撞2)碰撞时分子处在能起反应的状态。
碰撞频率Z 随温度增加的关系式为Z 正比T1/2。
而真正对速度贡献大的是那些具有高于平均能量的分子,即活化分子。
并不是所有碰撞的分子都能发生反应,所以起反应的分子必须要获得额外的、高出平均水平的能量E ,对此发生反应的最小平均动能称为活化能,当活化能越低,活化分子越多,反应速度就越快。
这个因素是实际导致反应发生的碰撞分额,称为“有效”碰撞。
②绝对反应速度理论 绝对反应速度理论又称活化络合物理论或过渡态理论,仍设分子发生碰撞,但排斥速度是碰撞的函数。
反应速度是由活化络合物过渡态的分解速度给定的。
更适合于处理钢铁冶金中的反应。
基本原理 1)活化络合物可像对待任何其他化学物质那样来对待,并与各反应物处于平衡状态,它的寿命很短。
2)活化络合物分解成两种产物的反应速度为通用速度,与反应物的性质和活化络合物的形态无关。
4. 炉渣在冶金过程中的作用①炉渣的有利方面(对熔炼过程的正常进行,提高合金质量,改进技术经济指标等都有很大的影响。
)1)炉渣直接参加化学反应,控制合金元素的氧化与还原,并去除合金中硫磷等有害杂质。
2)炉渣对合金熔体有保护作用。
3)电弧炉、平炉从上部加热熔池,在此过程中,炉渣是传热介质,同时还有保温作用。
4)电渣重熔精炼炉渣还可作为电阻发热体并具有渣洗过滤金属的作用。
②炉渣的不利方面 1)炉渣能浸蚀炉衬,降低炉衬寿命。
2)炉渣夹有金属小珠粒及未还原的金属氧化物,降低金属的回收率。
5.分解压力在炼钢中的应用 :①判断熔池中物质的反应方向。
连铸常见质量缺陷
连铸常见质量缺陷1 连铸工艺流程大包钢水→回转台→中间包→结晶器→二冷室→拉矫机→脱坯辊→中间辊道→夹持辊→火切机→切割平台→翻钢机→冷床→移坯车→(打号)铸坯集积2 常见质量事故的原因及处理连铸过程只是一个保持过程,不可能修正炼钢及设备的问题,因此才有了“炼钢是基础,设备是保证,连铸为中心”。
影响铸坯缺陷的因素归纳为三个方面:①钢水条件:脱氧情况、碳含量、锰硅比、锰硫比和杂质元素含量等。
②操作工艺:钢水温度、拉速、保护浇注方式、冷却水量及分布、钢水吹氩搅拌、喂丝等。
③设备状况:结晶器和二次冷却装置等主要在线设备的运行状况。
最终产品质量决定于所提供的铸坯质量。
根据产品用途的不同,提供合格质量的铸坏,这是生产中所考虑的主要目标之—。
从广义来说,所谓铸坯质量是得到合格产品所允许的铸坯缺陷的严重程度。
所谓铸坯质量的含义是指:铸坯的纯净度(夹杂物含量、形态、分布)、铸坯表面缺陷(裂纹、来渣、皮下气泡等)、铸坯内部缺陷(裂纹、偏析等)。
铸坯的纯净度主要决定于钢水进入结晶器之前的处理过程,也就是说要把钢水搞“干净”些,必须在钢水进入结晶器之前各工序下功夫,如选择合适的炉外精炼,钢包----中间包---结晶器的保护浇注等。
铸坯的表面缺陷主要决定于钢水在结晶器的凝固过程。
它是与结晶器内坯壳的形成、结晶器振动、保扩渣性能、浸入式水口设计及钢液面稳定性等因素有关的,必须严格控制影响表面质量的各参数在合理的目际值以内,生产无缺陷的铸坯,这是热送和直接轧制的前提。
铸坯内部质量主要决定于铸坏在二冷区的凝固冷却过程和铸坯的支撑系统的精度。
合理的二冷水量分布、支承辊的严格对中、防止铸坯鼓肚变形等,是提高内部质量的关键。
因此为了获得良好的铸坯质量。
我们可以根据钢种和产品不同要求,在连铸的不同阶段如钢包、中间包、结晶器、二冷区采用不同的工艺技术,对铸坯质量进行有效的控制,以消除铸坏缺陷或把缺陷降低到不影响产品质量所允许的范围内。
连铸坯质量控制
连铸坯质量控制迟景灏(重庆大学连铸技术研究所)对连铸坯质量控制的目的是使铸机产量高、质量好、缺陷少、收得率高,最终达到高效益。
为此,必须具备以下四项技术:*高水平的冶炼技术;*先进的连铸机的设备;*先进的连铸工艺和操作技术;*科学的管理。
1、连铸坯质量及结构特点1.1 连铸坯质量特点(与模锭相比较)*连铸坯组织致密,晶粒细;*连铸坯化学成份比模锭均匀;*宏观偏析程度比模锭小;*夹杂物总量比模锭低。
1.2 连铸坯结构特点连铸坯内部结构与普通小钢锭结构基本相似,它是由三个结晶区组成的,见图1。
图1.铸坯低倍组织结构*激冷层——由细小等轴晶组成的,其厚度2~4mm,而且成份均匀(是所浇钢液的平均成份)*柱状晶区或树枝晶区;*中心粗大等轴晶区;上述三个结晶区受许多因素的影响,如过热度、钢水的成份,特别是碳的含量,铸坯断面尺寸(传热方式)、浇注速度及冷却条件等。
1.3 铸坯结构几个名词1.3.1 内部结构——指的是用硫印或酸浸的方法,在铸坯横断面或纵断面上显示出的内部组织结构,通过它可以观察铸坯内部激冷层,柱状晶、中心等晶、内部偏析、疏松、缩孔、裂纹及硫化物分布情况。
1.3.2 宏观结构1.3.3微观结构2、连铸坯质量通常衡量铸坯质量标准如下:*连铸坯几何形状质量;*连铸坯表面质量;*连铸坯内部质量;*连铸坯洁净程度。
连铸坯缺陷分类:连铸坯上可见到多种多样的缺陷,其缺陷因机型、断面尺寸、断面形状、钢种及操作条件不同而异。
2.1 连铸坯的几何形状质量连铸坯几何形状缺陷不仅是铸坯外观形状问题,还与铸坯表面裂纹、内部裂纹等密切相关。
形状缺陷的种类随铸坯形状和大小而异,常见的几何形状缺陷有鼓肚、菱变、凹陷及梯形缺陷。
2.1.1 铸坯形状缺陷类型*铸坯鼓肚缺陷,见图2图2.板坯鼓肚缺陷1—中心裂纹,2—中间裂纹,3—近角内裂纹,4—三角区裂纹*铸坯菱变或脱方缺陷,见图3。
图3.方坯菱变或脱方*梯形坯,见图4图4.梯形坯*表面凹陷2.1.2 铸坯形状缺陷产生原因及防止措施2.1.2.1 铸坯鼓肚,是由于浇注温度高,拉速快,足辊和夹持辊开口度选择不当、夹持辊弯曲及零段水和一段水冷却强度弱等原因引起的,还与钢种有关。
钢坯的缺陷对轧制产生的影响
钢坯的缺陷对轧制产生的影响1.初轧坯的特点初轧坯时以钢锭为原料,经均热,开坯轧制而成的。
因此,初轧坯具有规格范围广,钢种多的特点。
钢锭经过压缩比为20-30,轧成的初轧坯压缩比大,从而改善了组织。
但轧制不能消除钢锭表面缺陷,也不能消除偏析,缩孔等内部缺陷。
初轧坯的表面质量及内在质量主要取决与钢锭的原始状况。
初轧坯在生产中发生烧损并要切头,切尾,因此初轧坯金属收得率比连铸坯低10%左右。
2.连铸坯的特点连铸坯是用钢水直接浇注拉矫而成的。
连铸坯工艺较模铸坯减少了钢锭再加热与开坯后的切头切尾,金属收得率高,能源消耗少。
就此而言,它具有初轧坯不可相比的优点。
但由于连铸小方坯质量不易保证,小规格的连铸方坯不易生产,有些钢种(尤其是沸腾钢和某些合金钢)还不能生产。
因此,高速线材厂还不能全部采用连铸小方坯作为生产线材的坯料。
国外为了扩大连铸坯的钢种,改善坯料质量,有的厂家先铸出300mm以上的大方坯,再经过连轧机轧成线材轧机需要的小方坯。
3.锻坯的特点由于产品的要求,需要组织的特殊性,以及一些军工、精密合金要求的小批量精品合同,需要锻造,锻坯一般坯小,同时要求脱碳层严格,主要钢坯缺陷其来源可分成两类:炼钢和铸锭造成的缺陷及初轧开坯轧钢造成的缺陷。
从缺陷所在的部位又可分表面缺陷及内部缺陷两种。
表面缺陷主要有:结疤、裂纹、拉裂、、牙痕、折叠、划痕、压痕、凹陷、角不满、弯曲(见弯曲度)、炸裂、剪切缺陷、清理不良、劈裂、尺寸超差等;内部缺陷夹杂(见非金属夹杂)、缩孔残余(见缩孔)、气囊、气泡、气孔、内裂、尾孔表面缺陷裂缝:冶炼成分,开坯时的加热,轧制都有可能造成钢坯裂缝,多见于轴承钢,弹簧钢等高碳钢初轧坯,连铸坯也可见此类缺陷。
在开坯的轧制中裂缝被放大成裂口,轧制到成品会形成折叠和裂纹的缺陷,裂缝直接影响钢材的后续生产。
蓝裂:钢坯部分修磨过重导致局部过热,组织改变,失效后由于应力作用导致钢坯表面开裂,多见于轴承钢。
一般要求蓝裂部分切除。