齿轮的参数和啮合条件
齿轮的参数与计算
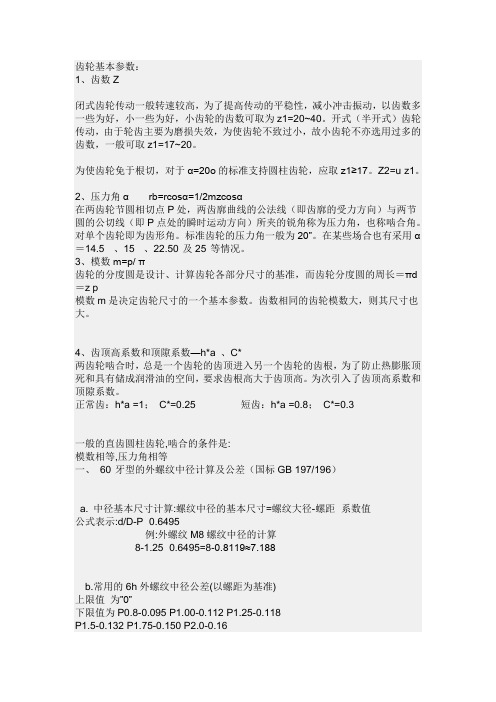
齿轮基本参数:1、齿数Z闭式齿轮传动一般转速较高,为了提高传动的平稳性,减小冲击振动,以齿数多一些为好,小一些为好,小齿轮的齿数可取为z1=20~40。
开式(半开式)齿轮传动,由于轮齿主要为磨损失效,为使齿轮不致过小,故小齿轮不亦选用过多的齿数,一般可取z1=17~20。
为使齿轮免于根切,对于α=20o的标准支持圆柱齿轮,应取z1≥17。
Z2=u·z1。
2、压力角α rb=rcosα=1/2mzcosα在两齿轮节圆相切点P处,两齿廓曲线的公法线(即齿廓的受力方向)与两节圆的公切线(即P点处的瞬时运动方向)所夹的锐角称为压力角,也称啮合角。
对单个齿轮即为齿形角。
标准齿轮的压力角一般为20‖。
在某些场合也有采用α=14.5°、15°、22.50°及25°等情况。
3、模数m=p/ π齿轮的分度圆是设计、计算齿轮各部分尺寸的基准,而齿轮分度圆的周长=πd =z p模数m是决定齿轮尺寸的一个基本参数。
齿数相同的齿轮模数大,则其尺寸也大。
4、齿顶高系数和顶隙系数—h*a 、C*两齿轮啮合时,总是一个齿轮的齿顶进入另一个齿轮的齿根,为了防止热膨胀顶死和具有储成润滑油的空间,要求齿根高大于齿顶高。
为次引入了齿顶高系数和顶隙系数。
正常齿:h*a =1;C*=0.25 短齿:h*a =0.8;C*=0.3一般的直齿圆柱齿轮,啮合的条件是:模数相等,压力角相等一、60°牙型的外螺纹中径计算及公差(国标GB 197/196)a. 中径基本尺寸计算:螺纹中径的基本尺寸=螺纹大径-螺距×系数值公式表示:d/D-P×0.6495例:外螺纹M8螺纹中径的计算8-1.25×0.6495=8-0.8119≈7.188b.常用的6h外螺纹中径公差(以螺距为基准)上限值为‖0‖下限值为P0.8-0.095 P1.00-0.112 P1.25-0.118P1.5-0.132 P1.75-0.150 P2.0-0.16P2.5-0.17上限计算公式即基本尺寸,下限值计算公式d2-hes-Td2即中径基本尺寸-偏差-公差M8的6h级中径公差值:上限值7.188 下限值:7.188-0.118=7.07C常用的6g级外螺纹中径基本偏差: (以螺距为基准)P 0.80-0.024 P 1.00-0.026 P1.25-0.028 P1.5-0.032P1.75-0.034 P2-0.038 P2.5-0.042上限值计算公式d2-ges即基本尺寸-偏差下限值计算公式d2-ges-Td2即基本尺寸-偏差-公差例M8的6g级中径公差值:上限值7.188-0.028=7.16下限值:7.188-0.028-0.118=7.042注:①以上的螺纹公差是以粗牙为准,对细牙的螺纹公差相应有些变化,但均只是公差变大,所以按此控制不会越出规范界限,故在上述中未一一标出.②螺纹的光杆坯径尺寸在生产实际中根据设计要求的精度和螺纹加工设备的挤压力的不同而相应比设计螺纹中径尺寸加大0.04—0.08之间,为螺纹光杆坯径值,例我们公司的M8外螺纹6g级的螺纹光杆坯径实在7.08—7.13即在此范围.③考虑到生产过程的需要外螺纹在实际生产的未进行热处理和表面处理的中径控制下限应尽量保持在6h级为准二、60°内螺纹中径计算及公差(GB 197 /196)a. 6H级螺纹中径公差(以螺距为基准)上限值:P0.8+0.125 P1.00+0.150 P1.25+0.16 P1.5+0.180P1.25+0.00 P2.0+0.212 P2.5+0.224下限值为‖0‖,上限值计算公式2+TD2即基本尺寸+公差例:M8-6H内螺纹中径为:7.188+0.160=7.348 上限值:7.188为下限值b. 内螺纹的中径基本尺寸计算公式与外螺纹相同即D2=D-P×0.6495即内螺纹中径螺纹大径-螺距×系数值c. 6G级螺纹中径基本偏差E1(以螺距为基准)P0.8+0.024 P1.00+0.026 P1.25+0.028 P1.5+0.032P1.75+0.034 P1.00+0.026 P2.5+0.042例:M8 6G级内螺纹中径上限值:7.188+0.026+0.16=7.374下限值:7.188+0.026=7.214上限值公式2+GE1+TD2即中径基本尺寸+偏差+公差下限值公式2+GE1即中径尺寸+偏差三、外螺纹大径的计算及公差(GB 197/196)a. 外螺纹的6h大径上限值即螺纹直径值例M8为φ8.00上限值公差为‖0‖b. 外螺纹的6h级大径下限值公差(以螺距为基准)P0.8-0.15 P1.00-0.18 P1.25-0.212 P1.5-0.236 P1.75-0.265P2.0-0.28 P2.5-0.335大径下限计算公式:d-Td 即螺纹大径基本尺寸-公差例:M8外螺纹6h大径尺寸:上限为φ8,下限为φ8-0.212=φ7.788c. 外螺纹6g级大径的计算与公差6g级外螺纹的基准偏差(以螺距为基准)P0.8-0.024 P1.00-0.026 P1.25-0.028 P1.5-0.032 P1.25-0.024 P1.75 –0.034 P2.0-0.038 P2.5-0.042上限计算公式d-ges 即螺纹大径基本尺寸-基准偏差下限计算公式d-ges-Td 即螺纹大径基本尺寸-基准偏差-公差例: M8 外螺纹6g级大径上限值φ8-0.028=φ7.972下限值φ8-0.028-0.212=φ7.76注:①螺纹的大径是由螺纹光杆坯径及搓丝板/滚丝轮的牙型磨损程度来决定的,而且其数值在同样毛坯及螺纹加工工具的基础上与螺纹中径成反比出现即中径小则大径大,反之中径大则大径小.②对需进行热处理和表面处理等加工的零件,考虑到加工过程的关系实际生产时应将螺纹大径控制在6h级的下限值加0.04mm以上,如M8的外螺纹在搓(滚)丝的大径应保证在φ7.83以上和7.95以下为宜.四、内螺纹小径的计算与公差a. 内螺纹小径的基本尺寸计算(D1)径基本尺寸=内螺纹基本尺寸-螺距×系数例:内螺纹M8的小径基本尺寸8-1.25×1.0825=6.646875≈6.647b. 内螺纹6H级的小径公差(以螺距为基准)及小径值计算P0.8 +0. 2 P1.0 +0. 236 P1.25 +0.265 P1.5 +0.3 P1.75 +0.335P2.0 +0.375 P2.5 +0.48内螺纹6H级的下限偏差公式D1+HE1即内螺纹小径基本尺寸+偏差注:6H级的下偏值为―0‖内螺纹6H级的上限值计算公式=D1+HE1+TD1即内螺纹小径基本尺寸+偏差+公差例:6H级M8内螺纹小径的上限值6.647+0=6.6476H级M8内螺纹小径的下限值6.647+0+0.265=6.912c. 内螺纹6G级的小径基本偏差(以螺距为基准)及小径值计算P0.8 +0.024 P1.0 +0.026 P1.25 +0.028 P1.5 +0.032 P1.75 +0.034P2.0 +0.038 P2.5 +0.042内螺纹6G级的小径下限值公式=D1+GE1即内螺纹基本尺寸+偏差例: 6G级M8内螺纹小径的下限值6.647+0.028=6.6756G级M8内螺纹小径的上限值公式D1+GE1+TD1即内螺纹基本尺寸+偏差+公差例: 6G级M8内螺纹小径的上限值是6.647+0.028+0.265=6.94注:①内螺纹的牙高直接关系到内螺纹的承载力矩的大小,故在毛坯生产中应尽量在其6H级上限值以内②在内螺纹的加工过程中,内螺纹小径越小会给加工具——丝锥的使用效益有所影响.从使用的角度讲是小径越小越好,但综合考虑时一般采用小径的在中限至上限值之间,如果是铸铁或铝件时应采用小径的下限值至中限值之间③内螺纹6G级的小径在毛坯生产中可按6H级执行,其精度等级主要考虑螺纹中径的镀层,故只在螺纹加工时考虑丝锥的中径尺寸而不必考虑光孔的小径。
齿轮与齿条配合参数

齿轮与齿条配合参数(最新版)目录1.齿轮与齿条的概述2.齿轮与齿条的配合参数3.齿轮与齿条配合参数的选择4.齿轮与齿条配合的应用实例正文一、齿轮与齿条的概述齿轮与齿条是一种常见的机械传动装置,广泛应用于各种工业设备、机床和自动化生产线等领域。
齿轮通常是圆柱形的,表面有齿,可以与齿条的齿相互啮合,从而实现转动与直线运动的传递。
二、齿轮与齿条的配合参数齿轮与齿条的配合参数主要包括以下三个方面:1.模数:齿轮的齿高与π的比值,用来表示齿轮的大小。
模数越大,齿轮的齿越大,传动扭矩越大,但齿轮的精度也越低。
2.压力角:齿轮齿面的夹角,通常取 20°、25°或 30°。
压力角的选择影响齿轮的强度、传动效率和磨损性能。
3.齿数:齿轮上的齿的数量。
齿数越多,齿轮的传动精度越高,但齿轮的结构越复杂,加工难度越大。
三、齿轮与齿条配合参数的选择齿轮与齿条配合参数的选择应根据实际工况和传动要求进行,主要考虑以下因素:1.传动扭矩:根据传动设备的负荷和转动速度,计算出需要的传动扭矩,从而选择合适的齿轮模数和齿数。
2.传动精度:根据传动设备的定位精度和速度要求,选择合适的齿轮压力角和齿数。
3.工况条件:考虑环境温度、湿度、润滑条件等因素,选择合适的齿轮材料和制造工艺。
四、齿轮与齿条配合的应用实例齿轮与齿条配合在各种工业设备中都有广泛应用,例如:1.机床:齿轮与齿条配合可以实现机床的刀具快速移动和精确定位,提高加工效率和精度。
2.自动生产线:齿轮与齿条配合可以实现生产线上的物料传送和生产线的同步运行,提高生产效率。
3.工程车辆:齿轮与齿条配合可以实现车辆的转向、变速等功能,保证车辆的稳定行驶。
总之,齿轮与齿条配合参数的选择和应用对机械传动的性能和效果至关重要。
齿轮基本参数
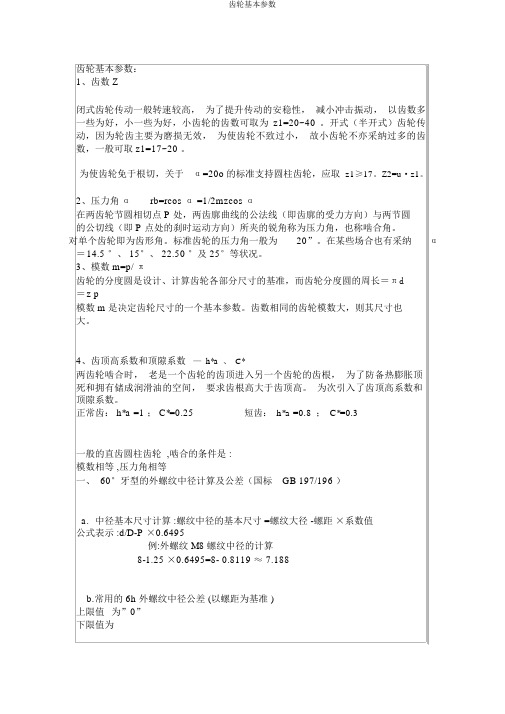
齿轮基本参数:1、齿数 Z闭式齿轮传动一般转速较高,为了提升传动的安稳性,减小冲击振动,以齿数多一些为好,小一些为好,小齿轮的齿数可取为z1=20~40 。
开式(半开式)齿轮传动,因为轮齿主要为磨损无效,为使齿轮不致过小,故小齿轮不亦采纳过多的齿数,一般可取 z1=17~20 。
为使齿轮免于根切,关于α=20o的标准支持圆柱齿轮,应取z1≥17。
Z2=u·z1。
2、压力角αrb=rcos α =1/2mzcos α在两齿轮节圆相切点 P 处,两齿廓曲线的公法线(即齿廓的受力方向)与两节圆的公切线(即 P 点处的刹时运动方向)所夹的锐角称为压力角,也称啮合角。
对单个齿轮即为齿形角。
标准齿轮的压力角一般为20”。
在某些场合也有采纳α=14.5 °、 15°、 22.50 °及 25°等状况。
3、模数 m=p/ π齿轮的分度圆是设计、计算齿轮各部分尺寸的基准,而齿轮分度圆的周长=πd=z p模数 m 是决定齿轮尺寸的一个基本参数。
齿数相同的齿轮模数大,则其尺寸也大。
4、齿顶高系数和顶隙系数—h*a、C*两齿轮啮合时,老是一个齿轮的齿顶进入另一个齿轮的齿根,为了防备热膨胀顶死和拥有储成润滑油的空间,要求齿根高大于齿顶高。
为次引入了齿顶高系数和顶隙系数。
正常齿: h*a =1 ; C*=0.25短齿:h*a =0.8;C*=0.3一般的直齿圆柱齿轮 ,啮合的条件是 :模数相等 ,压力角相等一、 60°牙型的外螺纹中径计算及公差(国标GB 197/196 )a.中径基本尺寸计算 :螺纹中径的基本尺寸 =螺纹大径 -螺距×系数值公式表示 :d/D-P ×0.6495例:外螺纹 M8 螺纹中径的计算8-1.25 ×0.6495=8- 0.8119 ≈ 7.188b.常用的 6h 外螺纹中径公差 (以螺距为基准 )上限值为”0”下限值为上限计算公式即基本尺寸,下限值计算公式d2-hes-Td2 即中径基本尺寸 -误差 -公差M8 的 6h 级中径公差值:上限值7.188 下限值 :7.188-0.118=7.07C 常用的 6g 级外螺纹中径基本误差 : (以螺距为基准 )上限值计算公式d2-ges 即基本尺寸 -误差下限值计算公式d2-ges-Td2 即基本尺寸 -误差 -公差例 M8 的 6g 级中径公差值 :上限值 7.188-0.028=7.16下限值 :7.188-0.028-0.118=7.042注 :①以上的螺纹公差是以粗牙为准 ,对细牙的螺纹公差相应有些变化 ,但均不过公差变大 ,因此按此控制不会越出规范界线 ,故在上述中未一一标出 .②螺纹的光杆坯径尺寸在生产实质中依据设计要求的精度和螺纹加工设施的挤压力的不一样而相应比设计螺纹中径尺寸加大 0.04 —0.08 之间 ,为螺纹光杆坯径值 , 例我们企业的 M8 外螺纹 6g 级的螺纹光杆坯径实在 7.08 —7.13 即在此范围 .③考虑到生产过程的需要外螺纹在实质生产的未进行热办理和表面办理的中径控制下限应尽量保持在 6h 级为准二、 60°内螺纹中径计算及公差 (GB 197 /196)a. 6H 级螺纹中径公差 (以螺距为基准 )上限值 :P0.8+0.125 P1.00+0.150 P1.25+0.16 P1.5+0.180P1.25+0.00 P2.0+0.212 P2.5+0.224下限值为”0”,上限值计算公式2+TD2 即基本尺寸 +公差例 :M8-6H 内螺纹中径为 :7.188+0.160=7.348上限值:7.188为下限值b. 内螺纹的中径基本尺寸计算公式与外螺纹相同即 D2=D-P×0.6495 即内螺纹中径螺纹大径 -螺距×系数值c. 6G 级螺纹中径基本误差E1( 以螺距为基准 )P0.8+0.024 P1.00+0.026 P1.25+0.028 P1.5+0.032P1.75+0.034 P1.00+0.026 P2.5+0.042例:M8 6G 级内螺纹中径上限值 :7.188+0.026+0.16=7.374下限值 :7.188+0.026=7.214上限值公式 2+GE1+TD2 即中径基本尺寸 +误差 +公差下限值公式 2+GE1 即中径尺寸 +误差三、外螺纹大径的计算及公差(GB 197/196)a. 外螺纹的 6h 大径上限值即螺纹直径值例M8为φ8.00上限值公差为” 0”b.外螺纹的 6h 级大径下限值公差 (以螺距为基准大径下限计算公式 :d-Td 即螺纹大径基本尺寸 -公差例:M8 外螺纹 6h 大径尺寸 :上限为φ 8,下限为φ8-0.212= φ 7.788c.外螺纹 6g 级大径的计算与公差 6g级外螺纹的基准误差 (以螺距为基准 )P0.8-0.024 P1.00-0.026 P1.25-0.028 P1.5-0.032 P1.25-0.024 P1.75–0.034上限计算公式d-ges 即螺纹大径基本尺寸 -基准误差下限计算公式d-ges -Td 即螺纹大径基本尺寸 -基准误差 -公差例: M8 外螺纹 6g 级大径上限值φ8-0.028= φ 7.972下限值φ8-0.028- 0.212= φ 7.76注 :①螺纹的大径是由螺纹光杆坯径及搓丝板 /滚丝轮的牙型磨损程度来决定的 ,并且其数值在相同毛坯及螺纹加工工具的基础上与螺纹中径成反比出现即中径小则大径大 ,反之中径大则大径小 .②对需进行热办理和表面办理等加工的部件 ,考虑到加工过程的关系实质生产时应将螺纹大径控制在 6h 级的下限值加 0.04mm 以上 ,如 M8 的外螺纹在搓 (滚)丝的大径应保证在φ7.83以上和 7.95 以下为宜 .四、内螺纹小径的计算与公差a. 内螺纹小径的基本尺寸计算(D1)径基本尺寸 =内螺纹基本尺寸 -螺距×系数例:内螺纹 M8 的小径基本尺寸 8- 1.25 × 1.0825=6.646875 ≈ 6.647 b.内螺纹 6H 级的小径公差 (以螺距为基准 )及小径值计算P0.8 +0. 2 P1.0 +0. 236 P1.25 +0.265 P1.5 +0.3 P1.75 +0.335P2.0 +0.375 P2.5 +0.48内螺纹 6H 级的下限误差公式D1+HE1 即内螺纹小径基本尺寸 +误差注 :6H 级的下偏值为“0”内螺纹 6H 级的上限值计算公式 =D1+HE1+TD1 即内螺纹小径基本尺寸 +误差 + 公差例:6H 级 M8 内螺纹小径的上限值 6.647+0=6.6476H 级 M8 内螺纹小径的下限值 6.647+0+0.265=6.912c.内螺纹 6G 级的小径基本误差 (以螺距为基准 )及小径值计算P0.8 +0.024 P1.0 +0.026 P1.25 +0.028 P1.5 +0.032 P1.75 +0.034P2.0 +0.038 P2.5 +0.042内螺纹 6G 级的小径下限值公式 =D1+GE1 即内螺纹基本尺寸 +误差例: 6G 级 M8 内螺纹小径的下限值 6.647+0.028=6.6756G 级 M8 内螺纹小径的上限值公式 D1+GE1+TD1 即内螺纹基本尺寸 +误差 + 公差例: 6G 级 M8 内螺纹小径的上限值是 6.647+0.028+0.265=6.94注 :①内螺纹的牙高直接关系到内螺纹的承载力矩的大小 ,故在毛坯生产中应尽量在其6H 级上限值之内②在内螺的加工程中 ,内螺小径越小会加工具——的使用效益有所影响 .从使用的角度是小径越小越好 ,但合考一般采纳小径的在中限至上限之 ,假如是或件采纳小径的下限至中限之③内螺 6G 的小径在毛坯生中可按 6H 行 ,其精度等主要考螺中径的 ,故只在螺加工考的中径尺寸而不用考光孔的小径。
齿轮基本参数知识

齿轮基本参数知识1、齿数Z闭式齿轮传动一般转速较高,为了提高传动的平稳性,减小冲击振动,以齿数多一些为好,小一些为好,小齿轮的齿数可取为z1=20~40。
开式(半开式)齿轮传动,由于轮齿主要为磨损失效,为使齿轮不致过小,故小齿轮不亦选用过多的齿数,一般可取z1=17~20。
为使齿轮免于根切,对于α=20o的标准支持圆柱齿轮,应取z1≥17。
Z2=u·z1。
2、压力角αrb=rcosα=1/2mzcosα在两齿轮节圆相切点P处,两齿廓曲线的公法线(即齿廓的受力方向)与两节圆的公切线(即P点处的瞬时运动方向)所夹的锐角称为压力角,也称啮合角。
对单个齿轮即为齿形角。
标准齿轮的压力角一般为20”。
在某些场合也有采用α=14.5° 、15° 、22.50°及25°等情况。
3、模数m=p/ π齿轮的分度圆是设计、计算齿轮各部分尺寸的基准,而齿轮分度圆的周长=πd=z p模数m是决定齿轮尺寸的一个基本参数。
齿数相同的齿轮模数大,则其尺寸也大。
4、齿顶高系数和顶隙系数—h*a 、C*两齿轮啮合时,总是一个齿轮的齿顶进入另一个齿轮的齿根,为了防止热膨胀顶死和具有储成润滑油的空间,要求齿根高大于齿顶高。
为次引入了齿顶高系数和顶隙系数。
正常齿:h*a =1; C*=0.25 短齿:h*a =0.8; C*=0.3一般的直齿圆柱齿轮,啮合的条件是:模数相等,压力角相等齿轮的直径计算方法:齿顶圆直径=(齿数+2)*模数分度圆直径=齿数*模数齿根圆直径=齿顶圆直径-4.5模数比如:M4 32齿齿顶圆直径=(32+2)*4=136mm 分度圆直径=32*4=128mm齿根圆直径=136-4.5*4=118mm 7M 12齿就是(12+2)*7=98mm。
标准渐开线直齿圆柱齿轮的正确啮合条件

标准渐开线直齿圆柱齿轮的正确啮合条件
1. 模数选择合适: 在确定齿轮传动比和转速需求的基础上,选择适当的模数。
模数的选择应能保证齿轮的牙根强度满足要求。
2. 齿数的选择: 根据传动比和齿轮模数,计算出齿轮的齿数。
齿数的选择要满足齿轮副的啮合条件,确保齿轮啮合时的角度斜率误差小于规定范围。
3. 正确的啮合距离: 通过计算齿轮的分度圆直径和齿数,确定啮合距离。
啮合距离是保证齿轮齿形正确的重要参数。
4. 角啮合条件: 确保两个齿轮的法向力和切向力不超过公差范围,从而保证齿轮在啮合时能够正常工作。
5. 齿轮的啮合过渡曲线: 在齿轮的啮合曲线上,应设定适当的过渡曲线,以减小啮合冲击和噪音,并提高齿轮传动的平稳性。
6. 啮合啮合角选择: 根据齿轮的齿数和分度圆直径,确定适当的啮合角,以确保齿轮啮合位置正确。
7. 齿轮材料选择: 根据工作负荷和要求的使用寿命,选择适当的材料,以保证齿轮的强度和耐磨性。
请注意以上条件仅作为一般标准参考,实际设计应结合具体要求、应用环境和工作条件进行。
齿轮的参数基本介绍
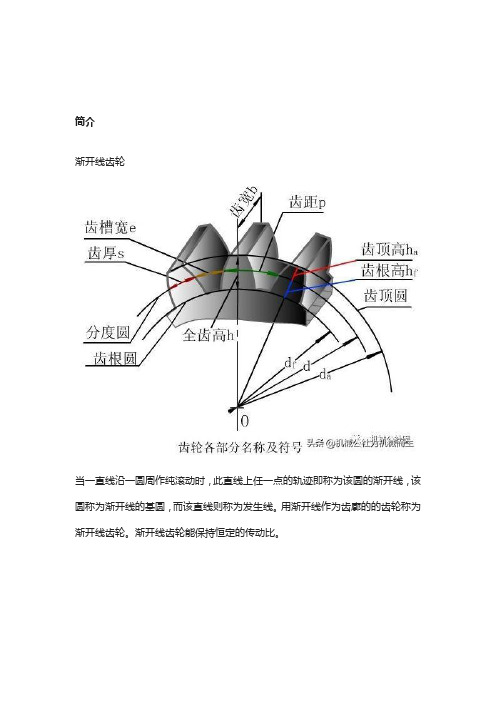
简介渐开线齿轮当一直线沿一圆周作纯滚动时,此直线上任一点的轨迹即称为该圆的渐开线,该圆称为渐开线的基圆,而该直线则称为发生线。
用渐开线作为齿廓的的齿轮称为渐开线齿轮。
渐开线齿轮能保持恒定的传动比。
AK: 渐开线rb: 基圆n-n:发生线压力角渐开线上任一点法向压力的方向线(即渐开线在该点的法线)和该点速度方向之间的夹角称为该点的压力角。
下面左图中,αk即为渐开线上K点的压力角。
由图可知:cosαk=ON/OK=rb/Rk。
下面右图中,压力角是半径线与齿形的切线间的夹角,α为压力角,因为α‘=α,所以α‘也是压力角渐开线上各点压力角不等。
基圆上压力角为零,齿顶圆上压力角最大。
通常所说的齿轮压力角指的是分度圆上的压力角,以α表示,并规定分度圆上的压力角的标准值,称为标准压力角,我国取α=20°。
齿轮各部分名称和基本参数端面──垂直于齿轮轴线的平面法面──垂直于轮齿齿线的平面齿线──齿面与分度圆柱面的交线基圆──形成渐开线的发生线在其上作纯滚动的圆齿宽b ──轮齿沿轴向的尺寸基准齿条──依其标准齿轮规格所切削出来之齿条称为基准齿条节圆(Pitch Circle) ──两齿轮连心线上咬合接触点各齿轮上留下轨迹称为节圆节径(Pitch Diameter) ──节圆直径分度圆──在齿顶圆和齿根圆之间,规定一直径为d的圆,作为计算齿轮各部分尺寸的基准,这个圆称为分度圆。
分度圆的大小是由齿距和齿数决定的。
分度圆周长dπ=mz,d= pz/π齿轮各部分的名称和基本参数1、分度圆:齿轮上作为齿轮尺寸基准的圆,用d表示2、齿距:相邻两齿同侧齿廓间的分度圆弧长,用p表示3、模数:齿距P与π的比值,用m表示4、压力角:渐开线齿廓上与分度圆交点处的压力角a,国家标准压力角为20度5、齿顶高:由分度圆到齿顶圆的径向高度,用ha表示6、顶隙:两齿轮装配后,两啮合齿沿径向留下的空隙距离,用C表示7、齿根高:由分度圆到齿根圆的径向高度,用hf表示8、全齿高:由齿顶圆到齿根圆的径向高度,用h表示★直齿圆柱齿轮正确的啮合条件:模数相等压力角相等标准直齿圆柱齿轮尺寸计算公式表名称符号计算公式齿距pP=mπ齿厚ss=mπ/2槽宽ee=mπ/2齿顶高haha = ha※m齿根高hfhf =( ha※+ C※)m全齿高hh =(2 ha※+ C※)m分度圆直径dd=mz齿顶圆直径dada=d±2 ha齿根圆直径dfdf=d±2 hf基圆直径dbdb=dcosa=mzcosa 中心距aa=m(Z2±Z1)/2齿数和齿面齿数:从基准面看下去,若顺时针测量,则齿或槽定义齿/槽号为1,2…,Z为总齿数。
齿轮基本参数
齿轮基本参数齿轮基本参数:1、齿数Z闭式齿轮传动一般转速较高,为了提高传动的平稳性,减小冲击振动,以齿数多一些为好,小一些为好,小齿轮的齿数可取为z1=20~40。
开式(半开式)齿轮传动,由于轮齿主要为磨损失效,为使齿轮不致过小,故小齿轮不亦选用过多的齿数,一般可取z1=17~20。
为使齿轮免于根切,对于α=20o的标准支持圆柱齿轮,应取z1≥17。
Z2=u·z1。
2、压力角α rb=rcosα=1/2mzcosα在两齿轮节圆相切点P处,两齿廓曲线的公法线(即齿廓的受力方向)与两节圆的公切线(即P点处的瞬时运动方向)所夹的锐角称为压力角,也称啮合角。
对单个齿轮即为齿形角。
标准齿轮的压力角一般为20”。
在某些场合也有采用α=14.5°、15°、22.50°及25°等情况。
3、模数m=p/ π齿轮的分度圆是设计、计算齿轮各部分尺寸的基准,而齿轮分度圆的周长=πd =z p模数m是决定齿轮尺寸的一个基本参数。
齿数相同的齿轮模数大,则其尺寸也大。
4、齿顶高系数和顶隙系数—h*a 、C*两齿轮啮合时,总是一个齿轮的齿顶进入另一个齿轮的齿根,为了防止热膨胀顶死和具有储成润滑油的空间,要求齿根高大于齿顶高。
为次引入了齿顶高系数和顶隙系数。
正常齿:h*a =1;C*=0.25 短齿:h*a =0.8;C*=0.3一般的直齿圆柱齿轮,啮合的条件是:模数相等,压力角相等一、60°牙型的外螺纹中径计算及公差(国标GB 197/196)a. 中径基本尺寸计算:螺纹中径的基本尺寸=螺纹大径-螺距×系数值公式表示:d/D-P×0.6495例:外螺纹M8螺纹中径的计算8-1.25×0.6495=8-0.8119≈7.188b.常用的6h外螺纹中径公差(以螺距为基准)上限值为”0”下限值为P0.8-0.095 P1.00-0.112 P1.25-0.118P1.5-0.132 P1.75-0.150 P2.0-0.16P2.5-0.17上限计算公式即基本尺寸,下限值计算公式d2-hes-Td2即中径基本尺寸-偏差-公差M8的6h级中径公差值:上限值7.188 下限值:7.188-0.118=7.07C常用的6g级外螺纹中径基本偏差: (以螺距为基准)P 0.80-0.024 P 1.00-0.026 P1.25-0.028 P1.5-0.032P1.75-0.034 P2-0.038 P2.5-0.042上限值计算公式d2-ges即基本尺寸-偏差下限值计算公式d2-ges-Td2即基本尺寸-偏差-公差例M8的6g级中径公差值:上限值7.188-0.028=7.16下限值:7.188-0.028-0.118=7.042注:①以上的螺纹公差是以粗牙为准,对细牙的螺纹公差相应有些变化,但均只是公差变大,所以按此控制不会越出规范界限,故在上述中未一一标出.②螺纹的光杆坯径尺寸在生产实际中根据设计要求的精度和螺纹加工设备的挤压力的不同而相应比设计螺纹中径尺寸加大0.04—0.08之间,为螺纹光杆坯径值,例我们公司的M8外螺纹6g级的螺纹光杆坯径实在7.08—7.13即在此范围.③考虑到生产过程的需要外螺纹在实际生产的未进行热处理和表面处理的中径控制下限应尽量保持在6h级为准二、60°内螺纹中径计算及公差(GB 197 /196)a. 6H级螺纹中径公差(以螺距为基准)上限值:P0.8+0.125 P1.00+0.150 P1.25+0.16 P1.5+0.180P1.25+0.00 P2.0+0.212 P2.5+0.224下限值为”0”,上限值计算公式2+TD2即基本尺寸+公差例:M8-6H内螺纹中径为:7.188+0.160=7.348 上限值:7.188为下限值b. 内螺纹的中径基本尺寸计算公式与外螺纹相同即D2=D-P×0.6495即内螺纹中径螺纹大径-螺距×系数值c. 6G级螺纹中径基本偏差E1(以螺距为基准)P0.8+0.024 P1.00+0.026 P1.25+0.028 P1.5+0.032P1.75+0.034 P1.00+0.026 P2.5+0.042例:M8 6G级内螺纹中径上限值:7.188+0.026+0.16=7.374下限值:7.188+0.026=7.214上限值公式2+GE1+TD2即中径基本尺寸+偏差+公差下限值公式2+GE1即中径尺寸+偏差三、外螺纹大径的计算及公差(GB 197/196)a. 外螺纹的6h大径上限值即螺纹直径值例M8为φ8.00上限值公差为”0”b. 外螺纹的6h级大径下限值公差(以螺距为基准)P0.8-0.15 P1.00-0.18 P1.25-0.212 P1.5-0.236 P1.75-0.265P2.0-0.28 P2.5-0.335大径下限计算公式:d-Td 即螺纹大径基本尺寸-公差例:M8外螺纹6h大径尺寸:上限为φ8,下限为φ8-0.212=φ7.788c. 外螺纹6g级大径的计算与公差6g级外螺纹的基准偏差(以螺距为基准)P0.8-0.024 P1.00-0.026 P1.25-0.028 P1.5-0.032 P1.25-0.024 P1.75 –0.034 P2.0-0.038 P2.5-0.042上限计算公式d-ges 即螺纹大径基本尺寸-基准偏差下限计算公式d-ges-Td 即螺纹大径基本尺寸-基准偏差-公差例: M8 外螺纹6g级大径上限值φ8-0.028=φ7.972下限值φ8-0.028-0.212=φ7.76注:①螺纹的大径是由螺纹光杆坯径及搓丝板/滚丝轮的牙型磨损程度来决定的,而且其数值在同样毛坯及螺纹加工工具的基础上与螺纹中径成反比出现即中径小则大径大,反之中径大则大径小.②对需进行热处理和表面处理等加工的零件,考虑到加工过程的关系实际生产时应将螺纹大径控制在6h级的下限值加0.04mm以上,如M8的外螺纹在搓(滚)丝的大径应保证在φ7.83以上和7.95以下为宜.四、内螺纹小径的计算与公差a. 内螺纹小径的基本尺寸计算(D1)径基本尺寸=内螺纹基本尺寸-螺距×系数例:内螺纹M8的小径基本尺寸8-1.25×1.0825=6.646875≈6.647b. 内螺纹6H级的小径公差(以螺距为基准)及小径值计算P0.8 +0. 2 P1.0 +0. 236 P1.25 +0.265 P1.5 +0.3 P1.75 +0.335P2.0 +0.375 P2.5 +0.48内螺纹6H级的下限偏差公式D1+HE1即内螺纹小径基本尺寸+偏差注:6H级的下偏值为“0”内螺纹6H级的上限值计算公式=D1+HE1+TD1即内螺纹小径基本尺寸+偏差+公差例:6H级M8内螺纹小径的上限值6.647+0=6.6476H级M8内螺纹小径的下限值6.647+0+0.265=6.912c. 内螺纹6G级的小径基本偏差(以螺距为基准)及小径值计算P0.8 +0.024 P1.0 +0.026 P1.25 +0.028 P1.5 +0.032 P1.75 +0.034P2.0 +0.038 P2.5 +0.042内螺纹6G级的小径下限值公式=D1+GE1即内螺纹基本尺寸+偏差例: 6G级M8内螺纹小径的下限值6.647+0.028=6.6756G级M8内螺纹小径的上限值公式D1+GE1+TD1即内螺纹基本尺寸+偏差+公差例: 6G级M8内螺纹小径的上限值是6.647+0.028+0.265=6.94注:①内螺纹的牙高直接关系到内螺纹的承载力矩的大小,故在毛坯生产中应尽量在其6H级上限值以内②在内螺纹的加工过程中,内螺纹小径越小会给加工具——丝锥的使用效益有所影响.从使用的角度讲是小径越小越好,但综合考虑时一般采用小径的在中限至上限值之间,如果是铸铁或铝件时应采用小径的下限值至中限值之间③内螺纹6G级的小径在毛坯生产中可按6H级执行,其精度等级主要考虑螺纹中径的镀层,故只在螺纹加工时考虑丝锥的中径尺寸而不必考虑光孔的小径。
齿轮啮合的基本条件公式
齿轮啮合的基本条件公式
1. 齿轮正确啮合条件。
- 对于标准安装的渐开线齿轮,正确啮合条件是两轮的模数和压力角分别相等。
- 设齿轮1的模数为m_1,压力角为α_1;齿轮2的模数为m_2,压力角为α_2,则正确啮合条件公式为:
- m_1 = m_2=m(模数相等)
- α_1=α_2 = α(压力角相等),对于标准齿轮,α = 20^∘。
2. 连续传动条件。
- 齿轮连续传动的条件是重合度varepsilon≥slant1。
- 重合度varepsilon的计算公式为varepsilon=(1)/(2π)[z_1(tanα_a1-tanα') +
z_2(tanα_a2-tanα')],其中z_1、z_2分别为两齿轮的齿数,α_a1、α_a2分别为两齿轮齿顶圆压力角,α'为啮合角。
- 齿顶圆压力角α_a的计算公式为cosα_a=(r_b)/(r_a),其中r_b为基圆半径,r_a为齿顶圆半径。
对于标准齿轮,r_b = rcosα(r为分度圆半径),r_a=r + h_a^*m (h_a^*为齿顶高系数,对于标准齿轮h_a^*=1)。
标准直齿圆柱齿轮正确啮合条件
标准直齿圆柱齿轮正确啮合条件标准直齿圆柱齿轮是机械传动中常见的一种齿轮,其正确的啮合条件对于齿轮传动系统的正常运行至关重要。
在实际应用中,如果齿轮的啮合条件不符合标准,将会导致齿轮传动系统产生噪音、振动、磨损加剧等问题,严重影响机械传动的工作效率和寿命。
因此,了解标准直齿圆柱齿轮的正确啮合条件对于工程师和技术人员来说至关重要。
首先,标准直齿圆柱齿轮的正确啮合条件包括齿轮的模数、齿数、齿面硬度、啮合角等方面。
在设计和制造齿轮时,必须严格按照标准规范进行,确保齿轮的各项参数符合要求。
其中,齿轮的模数是指齿轮的齿数和直径的比值,它决定了齿轮的尺寸和传动比。
合适的模数能够保证齿轮的强度和传动效率,避免因齿轮尺寸过大或过小而导致的啮合问题。
其次,齿轮的齿数也是影响其正确啮合条件的重要因素之一。
齿数的选择应该考虑到传动比、工作条件、传动精度等因素,以确保齿轮在工作时具有良好的传动性能和稳定性。
此外,齿面硬度对于齿轮的正确啮合条件也至关重要,适当的齿面硬度能够提高齿轮的耐磨性和使用寿命,减少齿轮的磨损和损伤。
最后,啮合角是影响齿轮正确啮合条件的重要参数之一。
啮合角的选择应该考虑到齿轮的传动比、工作条件、噪音和振动等因素,以确保齿轮在工作时具有良好的传动性能和稳定性。
合适的啮合角能够减小齿轮的啮合冲击和噪音,提高齿轮传动的效率和平稳性。
总的来说,标准直齿圆柱齿轮的正确啮合条件是一个综合性的问题,需要考虑到齿轮的各项参数和工作条件。
只有严格按照标准规范进行设计和制造,并合理选择齿轮的各项参数,才能确保齿轮在工作时具有良好的传动性能和稳定性,避免因啮合条件不符合标准而导致的问题。
因此,工程师和技术人员在设计和选择标准直齿圆柱齿轮时,务必要充分了解和掌握其正确啮合条件,以确保齿轮传动系统的正常运行和可靠性。
齿轮基本参数
你设计的这个齿轮基本参数为:1、模数m=22、齿数z=103、分度圆直径D=mz=2*10=20mm4、齿根圆直径D2=D-2.5*m=20-2.5*2=15mm5、齿顶圆直径D1=D+2*m=20+2*2=24mm6、压力角α=20度(这是标准值)7、分度圆弦齿厚S=3.1286mm(查手册,再根据手册上的参数乘以模数)8、分度圆弦齿高h=2.1232mm(查手册,再根据手册上的参数乘以模数)你的参数大部分都对,就是“分度圆弦齿厚”不对,需要查手册,加计算,同时要查出“分度圆弦齿高”压力角,也称啮合角。
从这定义就可以推断:如果压力角小的话,齿轮的承载能小就会减小,如果偏大的话机械效率就会降低很多。
所以一般都约定压力角在20度。
其它特殊情况下也有采用其它压力角的,只是比较小见齿轮压力角渐开线及渐开线齿轮当一直线沿一圆周作纯滚动时,此直线上任一点的轨迹即称为该圆的渐开线,该圆称为渐开线的基圆,而该直线则称为发生线。
图1如图1:AK——渐开线基圆,rbn-n:发生线θK:渐开线AK段的展角用渐开线作为齿廓的的齿轮称为渐开线齿轮。
渐开线齿轮能保持恒定的传动比。
渐开线上任一点法向压力的方向线(即渐开线在该点的法线)和该点速度方向之间的夹角称为该点的压力角。
显然,图2中的图2αk即为渐开线上K点的压力角。
由图可知:cosαk=ON/O K=rb/Rk参考文献:[2] 卢玉明.机械设计基础.高等教育出版社,1998蜗轮蜗杆蜗轮蜗杆蜗轮蜗杆(Worm)[编辑本段]蜗轮及蜗杆机构一、用途:蜗轮蜗杆机构常用来传递两交错轴之间的运动和动力。
蜗轮与蜗杆在其中间平面内相当于齿轮与齿条,蜗杆又与螺杆形状相似。
二、基本参数:模数m、压力角、蜗杆直径系数q、导程角、蜗杆头数、蜗轮齿数、齿顶高系数(取1)及顶隙系数(取0.2)。
其中,模数m和压力角是指蜗杆轴面的模数和压力角,亦即蜗轮端面的模数和压力角,且均为标准值;蜗杆直径系数q为蜗杆分度圆直径与其模数m的比值。
- 1、下载文档前请自行甄别文档内容的完整性,平台不提供额外的编辑、内容补充、找答案等附加服务。
- 2、"仅部分预览"的文档,不可在线预览部分如存在完整性等问题,可反馈申请退款(可完整预览的文档不适用该条件!)。
- 3、如文档侵犯您的权益,请联系客服反馈,我们会尽快为您处理(人工客服工作时间:9:00-18:30)。
自动卸螺纹模具设计初级教程
BY WELLDESIGN17.Nov,04
前言:
塑胶产品螺纹分外螺纹和内螺纹两种,精度不高的外螺纹一般用哈夫块成型,而内螺纹则大多需要卸螺纹装置。
今天简单介绍内螺纹脱模方法,重点介绍齿轮的计算和选择。
一、卸螺纹装置分类
1、按动作方式分
①螺纹型芯转动,推板推动产品脱离;
②螺纹型芯转动同时后退,产品自然脱离。
2、按驱动方式分
①油缸+齿条
②油马达/电机+链条
③齿条+锥度齿轮
④来福线螺母
二、设计步骤
图)
①“D”——螺纹外径
②“P”——螺纹牙距
③“L”——螺纹牙长
④螺纹规格/方向/头数
⑤型腔数量
2、确定螺纹型芯转动圈数
U=L/P + Us
U ……螺纹型芯转动圈数
Us……安全系数,为保证完全旋出螺纹所加余量,一般取0.25~1
3、确定齿轮模数、齿数和传动比
模数决定齿轮的齿厚,齿数决定齿轮的外径,传动比决定啮合齿轮的转速。
在此之前有必要讲一下齿轮的参数和啮合条件。
三、齿轮的参数和啮合条件
模具的卸螺纹机构中大多应用的是直齿圆柱齿轮,而且一般都是渐开线直齿圆柱齿轮,因此下面就以渐开线直齿圆柱齿轮为研究对象。
1、齿轮传动的基本要求
①要求瞬时传动比恒定不变
②要求有足够的承载能力和较长的使用寿命
2、直齿圆柱齿轮啮合基本定律
两齿轮廓不论在何处接触,过接触点所作的两啮合齿轮的公法线,必须与两轮连心线相交于一点“C”,这样才能保证齿轮的瞬时传动比不变。
将所有“C”点连起来就成了2个外切圆,称之为分度圆,分度圆圆心距即齿轮圆心距。
详见下图
3、渐开线直齿圆柱齿轮参数
分度圆直径------“d”表示
分度圆周长--------“S”表示
齿轮齿距--------“p”表示
齿轮齿厚--------“sk”表示
齿轮齿槽宽--------“ek”表示
齿轮齿数--------“z”表示
齿轮模数--------“m”表示
齿轮压力角--------“ɑ”表示
齿轮传动比--------“i”表示
齿轮中心距--------“l”表示
4、计算公式如下:
①齿距 = 齿厚 + 齿槽宽即:p = sk + ek
②模数的由来
因为S = Z x P = π x d
d = P / π x Z
π是无理数,为计算方便,将P / π规定为常数,即模数,用m 表示,故有公式如下:d = m ×Z.
即:分度圆直径等于模数乘以齿数。
我国规定模数有2个系列,优先采用第一系列。
模数第一系列:1、1.25、1.5、 2、2.5、3、4、5、6 8 、10…
模数第二系列:1.75、2.25、2.75、3.25、3.5、4.5、5.5、7…
③压力角
我国规定:分度圆处的压力角为标准压力角,其值20°。
④传动比
当模数一定时,传动比就等于齿数比,即 i = Z1 / Z 2
⑤中心距
当齿数确定时,中心距I = (Z1+Z2) / 2 * m
5、齿轮啮合条件
模数和压力角相同的齿轮都可以正确啮合。
四、现在回到二、3,怎样在实际应用中确定齿轮的模数、齿数和传动比。
1.齿数
当传动中心距一定时,齿数越多,传动越平稳,噪音越低。
但齿数多,模数就小,齿厚也小,致使其弯曲强度降低,因此在满足齿轮弯曲强度条件下,尽量取较多的齿数和较小的模数。
为避免干涉,齿数一般取Z≥17,螺纹型芯的齿数尽可能少,但最少不少于14齿,且最好取偶数。
2.模数
工业用齿轮模数一般取m≥2。
英制齿轮采用径节制,径节齿轮把齿数z与分度圆直径d之比定为径节,以”P”表示,即
p = Z / d , 1 / in
径节与模数的换算公式为
m = 25.4 / p , mm
3.传动比
传动比在高速重载或开式传动情况下选择质数,目的为避免失效集中在几个齿上。
传动比还与选择哪种驱动方式有关系,比如用齿条+锥度齿或来福线螺母这两种驱动时,因传动受行程限制,须大一点,一般取1≤i≤4;当选择用油缸或电机时,因传动无限制,既可以结构紧凑点节省空间,又有利于降低马达瞬间启动力,还可以减慢螺纹型芯旋转速度,一般取0.25≤i≤1。
五、卸螺纹机构其它配件
1.轴承选择
①深沟球轴承------主要承受径向负荷也可承受一定轴向负荷
②圆锥滚子轴承------可以同时承受径向和轴向负荷
③推力球平面轴承------只承受轴向负荷
2.链轮选择
链轮参数有:p-----节距
d-----分度圆直径
z-----链轮齿数
链轮分度圆计算公式:d = p / sin(180゜/ z )
节距为标准值,如下:8 , 9.525 , 12.7 , 15.875 , 19.05 , 25.4 , 31.75 , 38.1 ,
44.45 , 50.8…
六、附录
附录包括模具结构实例和HASCO标准件目录。
实例1
实例2。