价值流管理案例
精益管理 案例

精益管理案例精益管理是一种管理理念,旨在通过最小化浪费和提高价值创造来提高企业的效率和竞争力。
下面我们将通过一个实际案例来介绍精益管理的应用。
某汽车制造公司在生产过程中遇到了一些问题,例如生产周期长、库存积压、生产成本高等。
为了解决这些问题,公司决定引入精益管理理念进行改进。
首先,公司进行价值流分析,找出生产过程中的价值和浪费。
他们发现,在生产过程中存在着很多不必要的等待时间、运输时间和库存积压,这些都是浪费。
于是,他们采取了一系列措施来减少这些浪费,比如优化生产流程、减少库存等。
其次,公司实施了精益生产的方法,包括及时生产、小批量生产和柔性生产。
他们采用了一种叫做“拉动生产”的方式,即根据客户需求来生产,而不是按照预测来生产。
这样不仅减少了库存积压,还能更快地响应客户需求。
另外,公司还注重员工的参与和改进。
他们开展了精益生产的培训,让员工了解精益管理的理念和方法,并鼓励他们提出改进建议。
通过员工的积极参与,公司不断改进生产流程,提高了生产效率。
通过引入精益管理,该汽车制造公司取得了显著的成效。
生产周期大大缩短,库存大幅减少,生产成本也得到了控制。
同时,产品质量和交付周期也得到了提升,客户满意度明显提高。
这个案例充分展示了精益管理在实际中的应用和效果。
通过精益管理,企业能够发现并消除浪费,提高生产效率,降低成本,提升产品质量,从而增强竞争力,实现可持续发展。
总之,精益管理不仅是一种管理工具,更是一种管理理念和文化。
只有将精益管理融入企业的日常运营中,才能真正实现持续改进和提高效率的目标。
希望更多的企业能够认识到精益管理的重要性,积极引入并落实,从而获得持续的竞争优势。
价值管理-价值流图析XXXX 精品
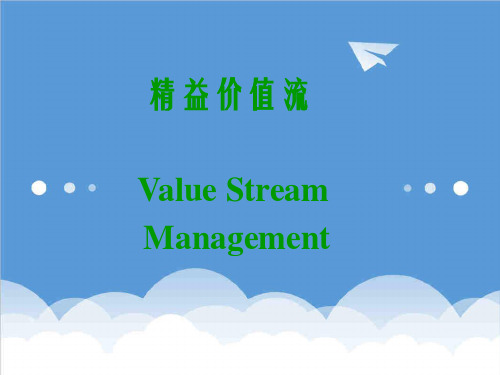
Deliver Courses
Deliver GFP FAB & Deliver
S.E.
ACC (Beale)
ACC & EAFB
S.E. & GFP Sustainment
Procure Spares
Contractor Item Management Spares
TSSP Process
Execution
Provide/Update/Revise Production Tech. Manuals
Deliver Manuals / TCTO’s and Kits
ACC & EAFB
Tech. Manual Sustainment
User Feedback AFTO 22 & DR’s
Definitize d
Funding Provided
Prime Begins Work
Process Architecture
1.0 Direct the Enterprise
2.0 Provide Financial Services & Control
3.0 Provide Internal Services & Facilities
价值流图示:企业图II
Current State Value Stream Map View Global Hawk Program
As Of May 2003
(TIER II)
Alpha Contracting &
Funding Constraints
Suppliers
Key Major Subs:
制造业生产运营管理案例

制造业生产运营管理案例案例背景某制造业公司是一家专门生产汽车零部件的企业。
由于市场竞争激烈,公司面临着薄利多销的压力。
为了提高生产效率、降低成本,公司决定引入先进的生产运营管理方法来改善生产状况。
本文将以该公司为案例,介绍其使用的生产运营管理方法,并分析其效果和经验教训。
生产运营管理方法该公司引入了精益生产(Lean Production)和六西格玛(Six Sigma)的方法来进行生产运营管理。
精益生产精益生产方法是一种通过消除浪费,减少不必要的工序和活动,提高生产效率的管理方法。
该公司在生产过程中使用了价值流图(Value Stream Mapping)来分析整个生产过程中的物料和信息流动情况,找出存在的浪费和瓶颈,并提出改进措施。
通过精益生产的应用,该公司实现了生产过程的流程化和标准化。
他们对每个工序的操作流程进行了详细的标准化,包括了安全操作规范、工作指导书等。
同时,公司通过建立短途运输系统和设立工作站来减少物料的搬运和等待时间,进一步提高生产效率。
六西格玛六西格玛是一种通过分析数据,减少变异,提高质量和效率的管理方法。
该公司使用六西格玛的方法来解决生产中的质量问题和提高产品的质量水平。
该公司首先明确了关键质量指标,并设立了对应的指标体系,通过数据的收集和分析,及时发现生产中的质量问题,并采取相应的改进措施。
同时,公司还开展了六西格玛的培训,提高了员工对质量管理的认识和能力。
效果与经验教训经过精益生产和六西格玛的应用,该公司取得了显著的效果。
首先,在生产效率方面,由于优化了生产过程和流程,消除了瓶颈和浪费,公司的生产效率大大提高。
生产周期缩短,产品的交付时间明显降低,大大提升了客户满意度。
其次,在质量方面,通过六西格玛的方法,公司成功地解决了过去存在的质量问题,产品的一致性和稳定性得到了显著提升。
产品质量的提高进一步增强了公司的竞争力,使其成为了汽车零部件市场的领先企业。
然而,在实施过程中,该公司也遇到了一些经验教训。
企业管理理论中的实践应用案例分享

企业管理理论中的实践应用案例分享在当今竞争激烈的商业环境中,企业管理理论对于企业的成功运营起着至关重要的作用。
然而,理论只有在实践中得到有效应用,才能真正展现其价值。
本文将分享几个不同企业在管理方面的实践应用案例,探讨它们如何运用管理理论来解决实际问题,提升企业绩效。
案例一:某制造业企业的精益生产实践某制造业企业面临着生产效率低下、成本居高不下的问题。
为了改变这一状况,企业引入了精益生产的管理理念。
首先,他们对生产流程进行了深入的价值流分析,识别出了其中的非增值环节和浪费。
例如,发现原材料在仓库中的存储时间过长,导致资金占用和潜在的损耗。
于是,通过优化采购计划和与供应商建立更紧密的合作关系,实现了原材料的及时供应,减少了库存成本。
在生产线上,采用了单件流的生产方式,取代了原来的批量生产模式。
这大大缩短了产品的生产周期,提高了生产效率。
同时,实施了5S 管理,即整理、整顿、清扫、清洁和素养,使工作现场更加整洁、有序,减少了寻找工具和物料的时间浪费。
此外,注重员工的培训和参与。
通过开展定期的精益生产培训课程,让员工理解精益理念,并鼓励他们提出改进建议。
建立了奖励机制,对提出有效改进措施的员工给予表彰和奖励,激发了员工的积极性和创造力。
经过一段时间的精益生产实践,该企业的生产效率显著提高,产品质量得到改善,成本大幅降低,在市场上的竞争力得到了显著提升。
案例二:某科技公司的创新管理实践在快速发展的科技行业,创新是企业生存和发展的关键。
某科技公司为了保持创新能力,采用了一系列创新管理策略。
建立了开放的创新文化。
鼓励员工勇于尝试新的想法,不怕失败。
公司内部经常组织头脑风暴会议,让不同部门的员工聚集在一起,交流思想,碰撞出创新的火花。
在组织架构上,设立了专门的创新团队。
这个团队由跨学科的专家组成,包括技术、设计、市场营销等领域的人才。
他们的任务是探索新的技术趋势和市场需求,为公司的产品研发提供前瞻性的建议。
同时,加强了与外部合作伙伴的合作创新。
精益管理在行政管理部门的应用
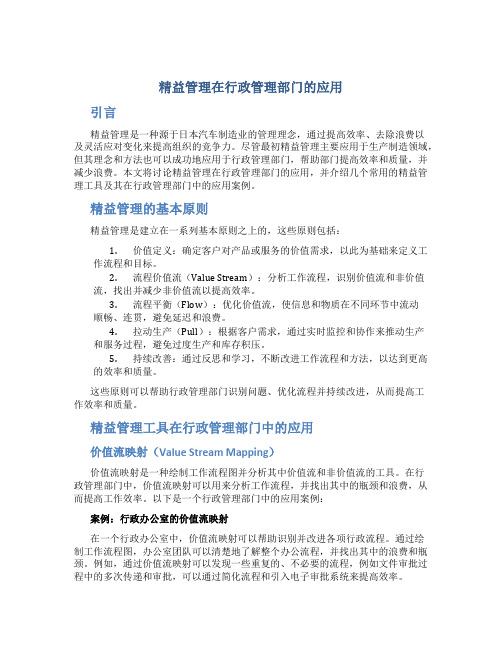
精益管理在行政管理部门的应用引言精益管理是一种源于日本汽车制造业的管理理念,通过提高效率、去除浪费以及灵活应对变化来提高组织的竞争力。
尽管最初精益管理主要应用于生产制造领域,但其理念和方法也可以成功地应用于行政管理部门,帮助部门提高效率和质量,并减少浪费。
本文将讨论精益管理在行政管理部门的应用,并介绍几个常用的精益管理工具及其在行政管理部门中的应用案例。
精益管理的基本原则精益管理是建立在一系列基本原则之上的,这些原则包括:1.价值定义:确定客户对产品或服务的价值需求,以此为基础来定义工作流程和目标。
2.流程价值流(Value Stream):分析工作流程,识别价值流和非价值流,找出并减少非价值流以提高效率。
3.流程平衡(Flow):优化价值流,使信息和物质在不同环节中流动顺畅、连贯,避免延迟和浪费。
4.拉动生产(Pull):根据客户需求,通过实时监控和协作来推动生产和服务过程,避免过度生产和库存积压。
5.持续改善:通过反思和学习,不断改进工作流程和方法,以达到更高的效率和质量。
这些原则可以帮助行政管理部门识别问题、优化流程并持续改进,从而提高工作效率和质量。
精益管理工具在行政管理部门中的应用价值流映射(Value Stream Mapping)价值流映射是一种绘制工作流程图并分析其中价值流和非价值流的工具。
在行政管理部门中,价值流映射可以用来分析工作流程,并找出其中的瓶颈和浪费,从而提高工作效率。
以下是一个行政管理部门中的应用案例:案例:行政办公室的价值流映射在一个行政办公室中,价值流映射可以帮助识别并改进各项行政流程。
通过绘制工作流程图,办公室团队可以清楚地了解整个办公流程,并找出其中的浪费和瓶颈。
例如,通过价值流映射可以发现一些重复的、不必要的流程,例如文件审批过程中的多次传递和审批,可以通过简化流程和引入电子审批系统来提高效率。
5S 应用5S 是一种用于组织工作环境、提高效率和创造舒适工作环境的管理方法。
【价值管理】价值流图常用符号及案例

客户
KITTING
CONVERSION
Machining
Kitting Racks
Welding
Assembly
Packing
Shiiping
供应商 Supplier
Warehouse 仓库
On Demand
Forecast Firm
Order
所在工厂
Forecast 3-mo
Firm Biweekly
Kitting Racks
Welding
Assembly
Packing
Shiiping
供应商 Supplier
Forecast Firm
Order
所在工厂
Forecast 3-mo
Firm Biweekly
客户
Warehouse 仓库
On Demand
Pick List 36 hrs
Loading Plan weekly daily
客户
供应商 Supplier
Warehouse 仓库
Forecast Firm
Order
所在工厂
Forecast 3-mo
Firm Biweekly
客户
供应商 Supplier
Warehouse 仓库
On Demand
Forecast Firm
Order
KITTING
Kitting Racks
所在工厂
客户
KITTING
CONVERSION
Machining
Kitting Racks
Welding
Assembly
Packing
Shiiping
供应商 Supplier
生产线精益管理案例

生产线精益管理案例在一家制造业公司,为了提高生产效率和质量控制,决定引入精益管理。
他们选择了生产线作为试点项目。
首先,该公司通过分析生产线的工作流程,发现了一些浪费和瓶颈。
在此基础上,他们开始对整个生产线进行重新设计,优化各个环节的流程。
通过使用价值流映射工具,他们识别了不必要的物料和工人移动以及无效的等待时间,进一步减少了浪费。
接下来,该公司引入了标准化工作和一体化的工作站,以减少变动和改进交流。
每个工作站都配备了标准化的工具和设备,员工只需按照规定的程序进行操作。
这种标准化的工作方式有助于提高生产线的稳定性和质量一致性。
此外,该公司实施了持续改进的文化。
每周,他们组织了固定的团队会议,讨论生产线上的问题和改进措施。
员工们被鼓励提出自己的观点和改善建议,并与团队一起制定解决方案。
这种开放和协作的工作环境激发了员工的创造力和积极性。
通过引入精益管理,该公司取得了显著的成果。
首先,生产线的工作效率明显提高,生产周期缩短了25%,产量增加了20%。
其次,产品质量得到了很大改善,缺陷率降低了30%以上。
这不仅提高了客户的满意度,也减少了售后服务和退货的成本。
除此之外,该公司还实现了员工参与和团队合作的增强。
员工们更加积极主动地参与到生产过程中,提出了很多有益的改进建议。
他们之间的协作和团队精神大大增强,为公司创造了更好的工作环境和员工满意度。
综上所述,精益管理在该制造业公司的生产线上取得了显著的效果。
通过分析工作流程,优化流程和引入标准化工作,公司提高了生产效率和产品质量。
持续改进的文化和员工参与进一步增强了团队合作和员工满意度。
这个成功案例向其他制造型企业展示了引入精益管理的巨大潜力。
随着全球竞争的加剧,制造业公司面临着提高效率、降低成本、保证质量和提升客户满意度的压力。
精益管理作为一种被广泛应用的管理方法,被许多公司认可为改善生产线效率和质量控制的有效手段。
在这家制造业公司的生产线中,精益管理的实施有助于优化生产流程、减少浪费、提高生产效率和产品质量。
精益管理案例

精益管理案例介绍精益管理是一种以提高效率和降低浪费为目标的管理方法。
它起源于日本的丰田汽车公司,并在全球范围内得到广泛应用。
本文将通过介绍一个精益管理的案例,深入探讨精益管理的原理和实践。
精益管理的原理精益管理的核心原则是通过消除浪费和优化价值流程来提高效率。
它包括以下几个方面的原理:1. 价值流分析精益管理强调对企业的价值流程进行分析,找出其中的浪费和低效环节。
通过剔除不必要的环节和提升价值创造的能力,企业可以实现更高的效率和更快的响应速度。
2. 一体化生产精益管理倡导将不同环节的生产过程进行一体化,以减少生产过程中的等待时间和库存量。
通过优化生产流程和提高生产能力,企业可以更快地响应市场需求。
3. 持续改进精益管理鼓励企业进行持续改进,不断寻找提升效率和降低浪费的方法。
通过设立目标、制定指标和持续监控,企业可以实现持续改进的循环。
精益管理的案例:丰田汽车公司丰田汽车公司是精益管理的典型案例。
丰田在20世纪50年代引入了精益管理的理念,并通过不断改进和优化,成为全球最大的汽车制造商之一。
1. 价值流分析:减少浪费丰田通过对生产流程进行价值流分析,找出其中的浪费和低效环节。
他们发现,传统的生产模式存在着大量的浪费,如等待时间、过度生产和不必要的运输。
为了减少浪费,丰田采取了一系列措施,如精确的生产计划、减少库存和优化运输。
2. 一体化生产:提高效率丰田通过将不同环节的生产过程进行一体化,实现了更高的效率和更快的响应速度。
他们采用了“拉动式生产”模式,即根据市场需求来触发生产,而不是按照预测来进行生产。
这样可以减少库存和等待时间,提高生产效率。
3. 持续改进:追求卓越丰田将持续改进作为企业文化的一部分。
他们鼓励员工提出改进的建议,并通过精益生产系统来管理和监控改进的过程。
丰田还建立了一套完善的培训体系,培养员工的改进意识和能力。
精益管理的效果精益管理的实施可以带来以下几方面的效果:1. 提高效率精益管理通过消除浪费和优化生产流程,可以显著提高企业的效率。