DFMEA(设计失效模式与效应分析)-20121123
设计失效模式及效应分析(DFMEA)

6
Development of a Design FMEA 设计FMEA的开始 设计 的开始
First Step of DFMEA: IDENTIFY DESIGN INTEND 第一步 : 确定设计意图 “Listing of what design is expected to do and what is expected not to do” “列出设计期望做什么和不期望做什么?
FMEA Date (Orig.) ______(Rev.)____ehicle(s)____________________
7
8 Core Team__________________________________________________________________________________________________________________________
Subsystem Level
Frame Function: –Provides stable attachment for seat support Potential Failure Mode(s) Structural failure seat support Excessive deflection of seat support Function: –Provides pleasing appearance Potential Failure Modes(s) Finish (shine)deteriorates Paint chips
Component Level Upper Frame
设计失效模式分析(DFMEA)

设计失效模式分析(DFMEA)预览说明:预览图片所展示的格式为文档的源格式展示,下载源文件没有水印,内容可编辑和复制1. 目的确定与产品相关的设计过程潜在的失效模式,确定设计过程中失效的起因,确定减少失效发生或找出失效条件的过程控制变量并编制潜在失效模式分级表,为采取预防措施提供对策。
2. 适用范围本程序适用于新产品设计、产品设计变更时的样品试验阶段的FMEA 分析。
3. 职责3.1 项目组:负责设计潜在失效模式和后果分析的工作主导,DFMEA 的制定;3.2 APQP跨功能小组:负责设计失效模式和后果分析(DFMEA )结果的评估;3.3 各职能部门:负责各失效模式和后果分析相关工作配合和对策的实施;3.4管理者代表:负责设计失效模式和后果分析(DFMEA )结果的批准。
4. 定义4.1 DFMEA :设计潜在失效模式和后果分析(Design Failure Mode and Effecting Analysis )是指设计人员采用的一门分析技术,在最大范围内保证充分考虑失效模式及其后果、起因和机理,DFMEA 以最严密的形式总结了设计技术人员进行产品设计时的指导思想。
4.2 APQP小组:由总经理指定的公司内部从事新产品设计和更改的跨功能组织。
4.3严重度(S):是潜在失效模式对下序组件、子系统、系统或顾客影响后果的严重程度的评价指标。
4.4频度(0):是指某一特定的具体的失效起因/机理发生的可能性/频率。
4.5探测度(D):DFMEA是指在零部件、子系统或系统投产之前,现行过程控制方法找出失效起因/机理(设计薄弱部份)的能力的评价指标,PFMEA是指在零部件离开制造工序或装配工位之前,现行过程方法找出失效起因/机理(过程薄弱部份)的可能性的评价指标。
5. 流程图:设计失效模式和后果分析(DFMEA )流程图参见(附件一)6. 作业程序和内容6.1实施DFMEA的时机6.1.1在设计阶段图面设计之前项目组负责主导DFMEA小组实施DFMEA,并且在产品图样完成之前全部完成。
(DFMEA)汽车行业设计失效模式分析
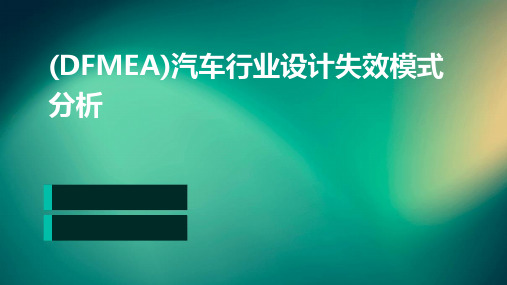
性能下降
随着使用时间的增加,发动机性能可能会逐渐下 降,导致汽车动力不足、加速缓慢等问题。这可 能是由于发动机内部零件磨损、燃油系统堵塞或 点火系统故障等原因引起的。
振动过大
发动机振动过大可能会对车辆的舒适性和稳定性 产生不良影响,同时也会增加零部件的磨损和疲 劳破坏。振动过大的原因可能包括发动机平衡性 差、零部件松动或损坏等。
不断更新表格,以反 映产品设计的更改和 改进。
确保表格内容完整、 准确,为后续分析提 供基础数据。
绘制设计流程图
01 详细绘制产品设计的流程图,包括各个组件的相 互关系和作用。
02 明确各个设计阶段的输入和输出,以便更好地理 解设计的整体流程。
03 分析流程图,找出可能存在的设计缺陷和失效模 式。
优化方法
采用先进的优化算法和仿真技术,对设计方案进行多目标优化。
优化过程
充分考虑制造工艺、材料特性等因素,确保优化方案的可行性。
提高制造质量
制造工艺
采用先进的制造工艺,提高零部件和整车的制造 精度和质量。
质量控制
建立严格的质量控制体系,确保每个环节的制造 质量符合要求。
质量检测
采用多种质量检测手段,如无损检测、功能检测 等,确保产品合格率。
03
基于影响评估,为每个故障模式制定相应的改进措施
和优先级。
03 汽车行业中的设计失效模 式
发动机系统
总结词
发动机系统是汽车的核心部分,其设计失效模式 主要表现在性能下降、过热、振动过大等方面。
过热
发动机过热是常见的失效模式之一,可能导致拉 缸、润滑油变质等严重后果。过热的原因可能包 括冷却系统故障、发动机负荷过大、散热器堵塞 等。
传动系统
(DFMEA)汽车行业设计失效模式分析

4
文档仅供参考,如有不当之处,请联系本人改正。
三、绘制功能框图(方块图)
方框图最好地展示了部件与部件之间的物理和物流关系。功能框图指出 了在设计范围内部件与子系统之间的相互关系,这种关系包括:信息流、 能量、力和流体;
5
文档仅供参考,如有不当之处,请联系本人改正。
闪光灯方块图
定温度、压力、湿度范围、设计寿命)相关的信息 (度量/测量变量)。如果该项目有多种功能,且 有不同的失效模式,应把所有的功能单独列出。
8
文档仅供参考,如有不当之处,请联系本人改正。
六、列出潜在失效模式
潜在失效模式所谓潜在失效模式是指部件、子系统或系统有可能会 未达到或不能实现项目/功能栏中所描述的预期功能的情况(如 预期功能失效)。这种潜在的失效模式可能会是更高一级的子系 统或系统的潜在失效模式的起因或者是更低一级的部件的潜在失 效模式的影响后果。
对于特定的项目及其功能,列出每一个潜在的失效模式。前提是这 种失效可能发生,但不一定发生。推荐将对以往TGW(运行出 错)研究、疑虑、报告和小组头脑风暴结果的回顾作为起点。
只可能出现在特定的运行条件下(如热、冷、干燥、粉尘等)和特 定的使用条件下(如超过平均里程、不平的路面、仅在城市内行 驶等)的潜在失效模式应予以考虑。
不符合法规
14
文档仅供参考,如有不当之处,请联系本人改正。
八、评估严重度(S)
严重度是一给定失效模式最严重的影响后果的级别。严重 度是单一的FMEA范围内的相对定级结果。严重度数值的 降低只有通过改变设计才能够实现。严重度应以表2为导 则进行估算:
小组应对评定准则和分级规则达成一致意见,尽管个别产品分析可做修改。 (见表2) 注:不推荐修改确定为9和10的严重度数值。严重度数值定级为1的失效模式 不应进行进一步的分析。 注:有时,高的严重度定级可以通过修改设计,使之补偿或减轻失效的严重 度结果来予以减小。例如,“瘪胎”可以减轻突然爆胎的严重度,“安全带” 可以减轻车辆碰撞的严重程度。
生产件批准(PPAP)之设计失效模式及后果分析(DFMEA)
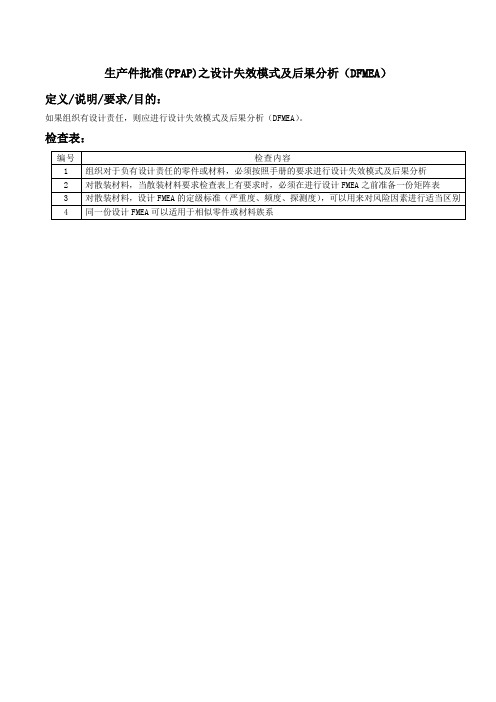
对散装材料,设计FMEA的定级标准(严重度、频度、探测度),可以用来对风险因素进行适当区别
4
同一份设计FMEA可以适用于相似零件或材料族系
生产件批准(PPAP)之设计失效模式及后果分析(DFMEA)
定义/说明/要求/目的:
如果组织有设计责任,则应进行设计失效模式及后果分析(DFMEA)。
检查表:
编号
检查内容
1
组织对于负有设计责任的零件或材料,必须按照手册的要求进行设计失效模式及后果分析
2
对散装材料,当散装材料要求检查表上有要求时,必须在进行设计FMEA之前准备一份矩阵表
DFMEA(Design Failure Mode and Effects Analysis,设计失效模式及后果分析)

DFMEA出自 MBA智库百科(/)DFMEA(Design Failure Mode and Effects Analysis,设计失效模式及后果分析)目录[隐藏]• 1 什么是DFMEA• 2 DFMEA基本原则• 3 DFMEA与PFMEA的关系• 4 形式和格式(Forms and Formats)• 5 我们应在何时进行设计失效模式及后果分析?• 6 我们应在什么时间进行设计失效模式及后果分析?•7 我们应在什么时间进行设计失效模式及后果分析?•8 我们应在什么时间进行设计失效模式及后果分析?•9 由谁进行设计失效模式及后果分析?•10 怎样进行设计失效模式及后果分析?•11 怎样进行设计失效模式及后果分析?•12 怎样进行设计失效模式及后果分析?•13 怎样进行设计失效模式及后果分析?•14 DFMEA的案例分析[1]o14.1 实施DFMEA存在的困难o14.2 实施DFMEA的准备工作o14.3 实施DFMEA的流程•15 相关条目•16 参考文献[编辑]什么是DFMEADFMEA是指设计阶段的潜在失效模式分析,是从设计阶段把握产品质量预防的一种手段,是如何在设计研发阶段保证产品在正式生产过程中交付客户过程中如何满足产品质量的一种控制工具。
因为同类型产品的相似性的特点,所以的DFMEA阶段经常后借鉴以前量产过或正在生产中的产品相关设计上的优缺点评估后再针对新产品进行的改进与改善。
[编辑]DFMEA基本原则DFMEA是在最初生产阶段之前,确定潜在的或已知的故障模式,并提供进一步纠正措施的一种规范化分析方法;通常是通过部件、子系统/部件、系统/组件等一系列步骤来完成的。
最初生产阶段是明确为用户生产产品或提供服务的阶段,该阶段的定义非常重要,在该阶段开始之前对设计的修改和更正都不会引起严重的后果,而之后对设计的任何变更都可能造成产品成本的大幅提高。
DFMEA应当由一个以设计责任工程师为组长的跨职能小组来进行,这个小组的成员不仅应当包括可能对设计产生影响的各个部门的代表,还要包括外部顾客或内部顾客在内。
DFMEA范文

DFMEA范文DFMEA(Design Failure Mode and Effects Analysis),即设计失效模式与效果分析,是一种系统性的设计分析方法,通常用于评估新产品或过程的潜在失效模式及其影响。
DFMEA可以帮助设计团队在产品设计的早期阶段发现和解决可能存在的问题,以减少产品在实际使用中可能发生的故障和事故。
本文将介绍DFMEA的基本概念、步骤、工具和应用,并探讨其在产品设计和开发过程中的重要性。
1.基本概念DFMEA是一种系统性、逐步的分析方法,用于识别由于设计缺陷而导致的潜在失效模式及其可能的影响。
通过对产品的各个组成部分进行分解,将可能的失效模式、失效原因和失效影响进行系统性的识别和评估。
DFMEA通常包括以下几个关键要素:-失效模式:即产品或系统可能出现的失效形式,例如断裂、磨损、过热等。
-失效原因:导致失效模式发生的根本原因,如材料选择不当、设计缺陷等。
-失效影响:失效对产品性能、安全性、可靠性等方面的影响,以及可能造成的后果。
2.步骤-确定分析范围:确定分析的产品或系统范围,明确团队成员和参与方。
-组织团队:组建跨职能团队,包括设计工程师、制造专家、质量工程师等,以确保全面分析。
-识别失效模式:对产品的各个组成部分进行分解,识别可能的失效模式。
-识别失效原因:确定导致每个失效模式发生的潜在原因。
-评估失效影响:评估每种失效模式对产品性能、安全性、可靠性等方面可能造成的影响。
-制定改进措施:针对每种失效模式和原因,制定相应的改进措施和控制计划。
3.工具-鱼骨图:用于识别失效模式和原因之间的关联。
-五为法则:用于深入分析可能的失效原因和影响。
-优先级排序:根据失效模式的严重性、发生频率和探测难度,确定优先处理的失效模式。
4.应用-风险管理:通过分析产品的潜在失效模式和影响,可以及早发现并解决问题,减少产品在实际使用中的风险。
-质量改进:通过设定合理的控制计划和改进措施,可以提高产品的质量和可靠性。
DFMEA失效模式与效应分析

N
所有RPN小
於規定值
Y FTA 分析
DFMEA報告
N 設計審查 Y 記錄保存
設計FMEA表
(2)系統
(2)子系統
(2)零組件: (2) . 設計責任: (3)
車型/年份: (5) . 生效日期:
核心小組:
(8) .
FMEA編號:
(1)
頁 次:
of
. 準備者 :
(4)
FMEA日期(制訂) (7) (修訂) (7) .
國際間采用FMEA之狀況
1.ISO9004 8.5節FMEA作為設計審查之要項 。
2.CE標志,以FMEA作為安全分析方法。 3.ISO14000,以FMEA作為重大環境影響面
分析與改進方法。 4.QS9000以FMEA 作為設計與制程失效分
析方法。
設計FMEA之目的
1.幫助設計需求與設計方案的評估。 2.幫助初始設計對制造和裝配的需求。 3.在設計發展階段,增加失效模式和系統效應分析的次數。 4.提供另一項分析資訊,幫助設計驗證之規劃。 5.根據對顧客需求的影響性,列出失效模式的排序,並按序改
‧不適當的維護作業。
‧金屬疲勞。
‧缺之環境保護。
‧裝備欠流暢。
‧錯誤的算法。
‧腐蝕
‧超過壓力‧
設計FMEA填寫說明
(15)發生度 參考下列各因素,決定發生度等級值(1~10): 1.相似零件或子系統的過去服務歷史資料和相關經驗? 2.零件、上一階零件或分系統是否滯銷? 3.上一階零件或分系統改變程度的大小? 4.零件與上一階零件,基本上是否有差異? 5.零件是否為全新的產品? 6.零件使用條件是否改變? 7.作業環境是否改變? 8.是否運用工程分析去預估,應用此零件之發生度?
- 1、下载文档前请自行甄别文档内容的完整性,平台不提供额外的编辑、内容补充、找答案等附加服务。
- 2、"仅部分预览"的文档,不可在线预览部分如存在完整性等问题,可反馈申请退款(可完整预览的文档不适用该条件!)。
- 3、如文档侵犯您的权益,请联系客服反馈,我们会尽快为您处理(人工客服工作时间:9:00-18:30)。
※ RPN(風險順序數):計算並記錄糾正後的RPN值的結果。
14
設計FMEA分析步驟
15
設計FMEA嚴重度評估標準
16
設計FMEA發生率評估標準
17
設計FMEA難檢度評估標準
18
設計FMEA改善對策提出時機
The timing to provide solution / 提出改善對策之時機
以利追蹤
※ Planning Stage(設計階段):填上依據目前所進行分析標的物所處之開發階段 ※ Design Responsibility (設計責任):填入負責的設計與開發之工程師全名
※ Prepared By(編制者):填入負責編制DFMEA的工程師的姓名
※ Part Name/Program(系統、子系統或零部件的名稱及編號):填入適當的分析級別並
12
設計FMEA分析表說明(Ⅲ)
※ POTENTIAL CAUSE(S) / MECHANISM(S) OF FAILURE(失效的潛在原因或機理) :填入每一
個失效模式的所有可以想到的失效原因或失效機理。
※ DESIGN CONTROLS(現行設計管制):填入已經完成或承諾要完成的預防措施、設計確認
DFMEA(設計失效模式與效應分析)
Design Failure Mode and Effect Analysis
1
什麽是FMEA ?
※
FMEA是一種系統方法,使用制式表格及問題解決
方法以確認潛在失效模式及其效應,並評估其嚴重度、 發生度、難檢度(探測/偵測)及目前管制方法,從而計算
風險優先指數(RPN),最後採取進一步改善方法,如此
持續進行,以達防患失效模式及效應發生於未然
2
FMEA 分類
※
設計(DESIGN FMEA) : 為防止和消除相關製品或設計的失敗點
※
製程(PROCESS FMEA) : 為防止和消除相關製品或其他工序的失敗點
3
何謂設計FMEA
?
※ 設計的潛在FMEA 是一種分析技術,係由負責設計的工程師或
小組使用,在儘可能的範圍內用來確保所有潛在的失效模式及其原 因均已納入考量並予以處理。
<100
二. S, O, D任一>8
三. S × D >35
19
設計FMEA展開
※ 計算關鍵指數RPN = (S) × (O) × (D)
注意事項: 1. 關鍵指數RPN = 嚴重度× 發生率× 難檢度 2. RPN數值範圍應該在1 ~ 1000之間 3. 數值用於設計重點之排序RPN≧100 or嚴重度≧9,需即刻改善(可 依 客戶需求or專案討論決定) ※ 策劃建議改善措施 注意事項: 1. 對RPN值最高之重點項目,策劃改善措施 2. 若失效原因尚未釐清前,建議改善措施要靠統計的實驗設計手法來 決定 3. 應採取可以量化效益的正面改善行動 4. 任何建議措施盡量以降低評價等級的內容順序為:嚴重度、發生率 及難檢度。������ 5. 參考之改善行動方式:(不侷限於此) 實驗設計法 修改設計 修正測試計劃 修改材料規格
20
建議措施(Ⅰ)
嚴重度 發生度 難檢度
※ 只有透過設計和/或製程修改,方能降低嚴重度評價等級,
而目前大部份的建議措施只有降低發生率與難檢度,如:安全 氣囊設計、斷電電池設計
※ 降低嚴重度的建議行動,如:試驗設計、修改試驗計畫、
修改設計、修改材料性能要求等
Hale Waihona Puke 21建議措施(Ⅱ)
嚴重度 發生度 難檢度
※ 最終成品及其所有相關的系統、子系統及零組件,都應納入評
估,FMEA是設計小組想法之摘錄(包括依據經驗有可能失效事項之 分析)。
※ 根據潛在失效模式對顧客的影響程度,列出優先順序來,並據
以建立設計、改善、開發及驗收測試或分析之優先順序系統。
4
設計FMEA 實施時機 ※ 下列條件發生時則必頇實施DFMEA分析:
※ 如果要降低發生的機率,必頇修訂製程和/或設計。
還要運用統計方法,執行以行動導向的製程研究,連 同適當的資訊回饋,以持續段改善及預防缺點發生
22
建議措施(Ⅲ)
嚴重度 發生度 難檢度
※ 較佳降低難檢度的方法,是使用防錯法。一般來說,提高偵測控制來達到
品質的改善,是不經濟且效益不大。增加品管檢驗頻率不是有效的預防/矯 正措施,且僅能暫時為之,且應以永久性的預防/矯正措施為本。某些狀況, 對特定的零件作設計變更,可能有助於偵測。變更現行管制系統,也可能提 昇其偵測能力。必頇強調的主要是預防不良( 意即:降低發生率) 而不是偵測 不良。例如:寧可用統計製程管制而不是隨機品質檢查或相關的檢驗
23
Thanks!
24
11
設計FMEA分析表說明(Ⅱ)
※ Design Item & Function/Requirements(設計項目和功能需求) :
填入被分析項目的名稱和編號。
※ Potential Failure Mode(潛在失效模式):對於一個特定項目及其功能,列出每一個
潛在的失效模式。
※ Potential Effects(s) of Failure(潛在失效後果):填入功能上之失效模式的效果或指為
顧客感受到的失效模式對功能的影響。
※ 嚴重度:填入評估潛在失效後果的嚴重程度等級,其評定準則和分級分為1—10級。 ※ SCC(CLASSICICATION, 管制項目) :針對RPN≥100 、嚴重度數(S)≥9 以及當產品和/
或過程歸類為關鍵特性,標識/註明那些可能需要附加的設計或程序控制的部件、子 系統或系統的產品特殊特性,其使用之標誌符號(*)參考關鍵特性管制程序。
※ 有關環境方面資料
產品使用條件、工作環境條件、與其他系統之介面關係、人機介面
7
設計FMEA小組成員
8
設計FMEA分析表
設計FMEA範例
9
怎樣獲得設計FMEA template
10
設計FMEA分析表說明(Ⅰ)
※ FMEA 編號:填入FMEA號碼(目前以產出此Report的年份、月與日當作其編輯),
‧新產品開發(L3)與設計改良(L2)時 ‧新製程導入時 ‧客戶要求時
‧重大品質異常發生時
‧追蹤產品驗證時所發生的的失效
5
組成設計FMEA團隊 ※ 在設計FMEA 團隊中,組成人員含硬體及系統之設計工程師
團隊, 故由負責設計、製造、品保、可靠度、業務、物料、測 試工程師、以及 其它之專業工程師組成團隊。
一.RPN=S*O*D ≧100
Description Must to provide soultion / 頇提出改善對策。 Should not to provide solution / 可不採取改善對策。 If the severity ranking equals 9 or above, must to provide solution / 若嚴重度大於9(含)時,必頇提出改善對策。
/驗證或其他活動。
※ OCC(發生度):描述發生度級別數著重在描述可能性的級別數之相對意義,而不是絕
對具體的數值,發生度數的取值與失效率範圍有關,但並不反應實際出現的可能性。
※ DET(難檢度):指與設計控制中所列的最佳探測控制相關聯的等級數。 ※ RPN(風險順序數):是嚴重度數(S)和發生度數(O)及難檢度數(D)三項數字之
填入被分析的系統、子系統或零部件的名稱及編號
※ Product Name/Model(產品名稱或型號):填入所分析的設計將要應用和/或影響的產
品名稱或型號(如有已知的話)
※ Date(Orig.) :填入初次預定完成FMEA日期,該日期應為設計階段即應完成不應超過
進入DVT階段日期
※ Date(Rev.) :填入更新報告日期
※ 現階段應至少要求RD內部(含機構與各支援單位)、製造單位
需要參與。
6
設計FMEA資料收集 ※ 有關產品設計方面資料
產品功能、工作原理、運行及工程程序、結構形式、其組成的零組件特性、材質
※ 有關製造工藝方面資料
加工過程、組裝過程、方法、檢驗及測試方式
※ 有關使用維修方面資料
使用情形與過程、工作條件、操作人員情況、每項維修所需時間、維修紀錄
填入每一項建議措施的責任組織的名稱和個人的姓名以及目標完成的日期。
※ ACTIONS TAKEN(採取的措施):填入在措施實施之後實際措施的簡要說明(但必頇)
以及生效日期。
※ SEV(嚴重度)/OCC(發生度)/ DET(難檢度):當確定了預防/糾正措施以後,重新估算
並記錄糾正後的嚴重度、發生度和難檢度值。
乘積。
※ RECOMMENDED ACTION(S) (建議措施) :按RPN值排出次序後,針對高嚴重度((S)≥9
或依顧客規定要求)、高RPN值(RPN≥100或依顧客規定要求)和小組指定的其他項目進行
預防/糾正措施的改善動作。
13
設計FMEA分析表說明(Ⅳ)
※ RESPONSIBILITY AND TARGET COMPLETION DATE(建議措施的責任與目標完成日期):