问题分析八步法
8D:解决问题的八大步骤

D1: ESTABLISH THE TEAM (成立小组)
• 1.让客户认为我们非常地重视他们所反应 的问题 • 2. • 3.G8D 要求要有成员的职称及联络分机 • 4.所有成员共同承担责任及后果, 但不要单 兵作业, 也不要写 Paperwork
31
成员包括:
●最高指导员(CHAMPION)
2
8D的本质: 问题解决程序
当我们观察到 或发现………时 这现象是否正常 跟标准或目标比较的差 异(偏离程度) 其差异是否不该在 为什么会发生异常 ?
现
象
确认并定义问题 WHAT, WHEN, WHERE, WHO, WHY, HOW, HOW MUCH
例如: 人员出勤率93%
问
题
分析原因 WHY
12
%
异常
Quality Improvement
v } ² £ ¨ ¤
Quality Control
Quality Control
É ¶ ® ¡
13
二、如何挖掘问题?
14
把问题想象成一座冰山
现象
现在
看得到的, 可感觉 , 可测量
why
问题
why
紧急处理
真因
一次因 (近因)
why
治标对策 (暂时)
• 答1:因为机器超载, 保 险丝烧断了 • 答2: 因为轴承的润滑 不足 • 答3: 因为润滑帮浦失 灵了 • 答4: 因为帮浦的轮轴 耗损了 • 答5: 因为杂质跑到里 面去了
21
5 Why的分布层次
现象
为什么机器停了? 现在 为什么机器会超载? 为什么轴承会润滑不足? 为什么润滑帮浦会失灵?
– 一般为主管阶层,对小组的进度有 监督, 支持及决策决定权力.
分析和解决问题的八个基本步骤

骤作者: 日期:分析和解决问题的八个基本步骤1 •组成一个问题解决小组。
通常问题解决小组来自问题相关部门人员。
有时会有更高的主管参与,他们的参与有两方面的原因,一是给予更专业的指导,二是阻止各部门相互推卸责任,使问题解决的更快。
2•问题描述。
很多时候,我们见到一些公司在解决问题的时候,由于大家似乎对问题都知道是怎么回事了,于是在讨论解决的时候,直接进入了寻找解决问题的方法和改善措施。
这是一个不好的做法。
即使团队成员都知道问题发生的经过,但我们在讨论时,仍然需要将问题的发生现象,按照一定的基本原则(比如4M2S人、机、聊、法、系统、地点)做仔细的描述。
这样描述的目的有三个,一个让每个成员更清楚问题的来龙去脉,用科学的思维思考问题发生的现象,二是将问题按照三现(现场,现实,现物)的原则来描述,避免各个成员在思考改善措施时岀现主观性偏差。
通常很多公司都规定描述按照一定的原则,比如4M2S等。
在问题描述里面,还需要注意几点:一是确定问题的影响范围和程度;二是要确定问题发生的频次,如果是产品质量问题,则是要确定发生率;三是要确定问题的主体,即发生的主体是什么,是一个零件呢,还是一批材料,或者是某个人,要记录这些主体的详细信息,如物料号,批次等。
3•解决问题的暂定对策。
很多问题发生,影响会非常大,而问题也很复杂,一时很难找出真正原因是什么。
这个时候,我们要做的事情就是立刻采取一个措施阻止问题的继续扩大或者让问题暂时解决。
待下一步在来仔细分析,查找问题根源,做出根源对策。
通常暂定对策的可行性需要全体团队做仔细的分析,这里主要考虑的就是对客户、员工、公司的影响如何。
比如如果当已经卖到市场的汽车被发现有潜在问题,那么汽车公司要做的第一件事、也是暂定对策,就是召回市场的现有车辆。
再比如,如果当工厂内发生了零部件不良,暂定对策就可能是先更换零部件,寻找一批质量合格的暂时先使用;也可能由于没有合格的零部件,让供应追加一些检查项目,立刻生产出一批合格的紧急送到工厂生产。
解决问题的8步法

■作成实施计划书
把已经设计好的(想好的)对策总结到实施计划书上。 (1) 对策项目能否达成活动目标(是否有联系) (2) 对策数目多吗。(是否能完成。多的话多少才合适) (3) 用5W1H具体地实施
◆设定目标值时考虑方法的例子◆
A公司 B公司 X公司 目标值
現状
趋势
目标值
A
B
C
D
E
1.选定课题
2.充分理解现况
3.制定目标值
4.要素分析 7.确认効果
8.总结、标准化
5.设计对策
6.实施对策
■步骤2 充分理解现况
对各种特性的变化或倾向进行的区分和调查
◆方块图例◆
(个) 20 个 16 12 数 8 4 0 规 格
4.分析主因 7.确认效果 8.总结、标准化
( 3 ) 设定改善的「目标值」
(根据提出的主题,决定改善到何种程度) 「目标值」按以下三个方面来表现。 ● 管理特性
● 目标值
● 限期
对于目标值,我们当然还不知道是否能达到。 但这不是能与不能的问题,而是按照「必须达到」的要求所定的值。 所以有必要最初就决定。
是要找到引起结果偏差的原因。
追求原因的原理是找到要素然后进行分析。通过这样做能尽快找到要素。要 素分析可以用另外一种说法就是叫竭尽全力找要素。
这个步骤是问题解決活动中最重要的程序。如果能准确抓住真正要素、 那对下一个对策的步骤是有直接效果的。 (1)找出要素(调查发生偏差的条件) 利用特性要因图,调查出要素。 特性要素图就是把对特性(结果)有影响的要素系统地调查,查找出偏差的原 因。
解决问题八步法
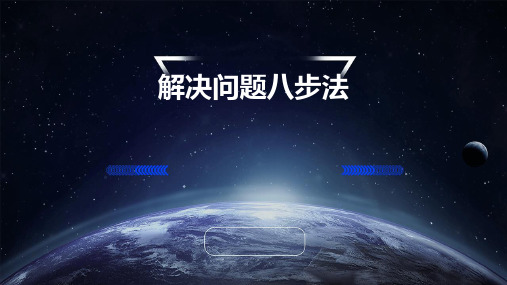
03
对解决方案实施后的长期效果进行监测,了解解决方案的持久
性和稳定性。
分析解决方案的优缺点
分析解决方案的优势
分析解决方案的优点和长处,了解其在解决问题中的贡献。
识别解决方案的不足
识别解决方案的缺点和不足之处,为改进和完善提供依据。
对比其他方案
将当前解决方案与其他备选方案进行对比,了解其相对优劣。
总结解决方案的经验教训
决策制定
根据综合评估和权衡结果,制定最 终的解决方案。
04
实施解决方案
制定实施计划
明确目标
在制定实施计划之前,要明确问 题的解决目标,确保计划与目标
保持一致。
制定详细步骤
根据问题的性质和实际情况,制 定具体的实施步骤,包括任务分
配、时间安排、资源需求等。
考虑风险和挑战
在制定计划时,要充分考虑可能 遇到的风险和挑战,并制定应对
策略。
分配资源
人力
根据实施计划的需求,合理分配人力资源,明确 每个人的职责和任务。
物力
确保所需的设备和物资得到及时供应,以满足实 施计划的需求。
财力
根据实施计划的需求,合理安排预算,确保计划 的顺利实施。
监控实施过程
定期检查进度
按照实施计划,定期检查任务的完成情况,确保计划按期进行。
调整计划
根据实际情况,对实施计划进行必要的调整,以适应变化的需求和 条件。
反馈与改进
在实施过程中,及时收集反馈信息,对存在的问题进行改进,以提 高实施效果。
05
检查效果
评估解决方案的效果
评估解决方案的可行性
01
评估解决方案在实际应用中的可行性,包括技术、资源、时间
等方面的考虑。
问题分析与解决的八步骤D程序

第五步:短期對策(暫時對策) 矯正措施 客人庫存品 路上的成品
Delta成品倉之庫存品
WIP(在線品) 材料倉庫之材料
第六步:長期(永久) 預防措施 -------從根本上杜絕不良再發生 *設計變更
*治工具防呆
*增加測試或組裝站等 第七步:成效追蹤(QA部) (改善前,後對比) 第八步:報告人 & 核准 & 效果驗證
問題分析與解決的八步驟8D程序
By: LISA QI
一. 8個步驟(問題分析處理步驟) D1. 改善主題選定與目標設定 Improvement subject &Target setup D2.問題定義及執行及驗證暫時防堵措施
problem definition
D3.現狀分析 Fact & Data finding analysis D4. 實施真因分析與驗證真因 Root cause analysis and verification
二.CAR 8D 介紹 第一步驟: 不良描述 a. 不良現象 b. 不良數
c. 抽樣數
d. 不良率 e. 提出者
第二步驟: 不良原因分析小組成員:
MFG,TE,IE,ME,QC or VQA,ENG,RMA等
強調團隊合作 第三步驟:Root Cause(根因分析) 第四步驟:不良品外流原因調查 (檢討品質體系,不良品一路過關斬將留出去, 哪裡有管理漏洞)
D5. 列出選定及驗證永久對策 Permanent corrective action D6.執行永久對策及效果確認 Verification of effectiveness
D7.防止再發及標準化
Recurrence prevention & Standardization D8.認知與殘餘潛在問題 Recognition & remaining Potential problem
质量管理工具之问题解决八步法-8D

D(8 Disciplines)即问题解决8步法,最早是福特公司使用的经典质量问题分析手法,对于解决工厂中存在的问题是一个很有用的工具,尤其在面对重大不良时,它能建立一个体系,让整个团队共享信息,并引导团队提供解决问题的方法。
工作中,你有没有过这样的感触:1 .XX现象已经反映了好几天了,怎么不见有人反馈呢?2 . XX事件解决方法大家都知道,可是没有人愿意解决,我也一直推不动。
3 . 这个不良现象到底是什么,为什么现在查到的和当时得知的不一样呢?4 . 都已经让XX部门全检了,怎么又发现不良了呢?5 . 这个不良一直反复发生,XX部门根本解决不掉!6 . XX不良记得已经解决了呀,怎么还在发生呢?7 . 原来XX SBU以前处理过这个问题,我们去看看他们怎么处理的。
8 . 每天都在被各种各样的异常翻来覆去的折腾,根本没有时间好好整理报告!8D方法由8个步骤和1个准备步骤组成,客观地确定、定义和解决问题并防止相似问题的再次发生。
8D方法应用流程▲D1组建问题解决团队8D原名就是叫团队导向问题解决步骤,8D小组需要由具备产品及制程知识,能支配时间且拥有职权及技能的人士组成,必须指定一名8D团队组长。
不具备以上条件的8D是失败的8D,它没法在你需要资源解决问题时提供帮助。
若一个体系出现了质量异常,绝非单一部门职能失效,否则整个体系需要重新进行完善。
8D团队的角色构成▲8D负责人:作为8D项目支持者的身份参与8D项目。
没有负责人的签字8D报告不能进行关闭审批。
8D组长:负责8D全过程的进行直至问题解决、8D项目关闭。
8D组员:在组长的协调下利用自身知识与技能参与8D问题的解决。
确定团队成员应注意的问题:团队人数:4~10人组长的选择:部门经理指定本部门人员或亲自担任组员的选择原则:与问题相关且具备相关的资源、能力D1的常见性错误:选择的8D团队成员对涉及问题没有相关知识或认识;只有一两个人实施8D过程。
解决问题八步法

解决问题八步法只要能很好地完成这八步,您就是最优秀的管理者,至少应该到知名企业的总经理职位了。
我们平常所见到的大多数管理者,其实只做到了第四步。
在管理中,要牢记以下四点,您将会受益终身:数字化理解、结构性思维、分解任务的能力、制定业务策略的能力。
步骤一描述问题1、清楚地描述什么时间,什么地点,什么人,发生了什么事,不要加入个人的主观意见;2、问题穷尽,不怕问题多,不怕内容细,就怕发现不了问题。
步骤二找出问题成因1、深入问题现场,调研问题成因,用“5个为什么”不断地追问,追问到根源,必须详细记录问题的相关人,时间,地点和数量;2、一切用数据化来理解分析,找出问题发生的真正成因,无法量化的问题,可以用经验信息判断。
步骤三根据问题的成因找出解决问题的措施1、站在客户、经营者、上级领导或对方的角度思考问题,做出问题――对应的具体解决方案,变成一件件非常具体的事项;2、拿着方案召集所有相关者进行认真讨论分析,采纳合理的建议,进行优化整合。
步骤四完善标准与流程将所有分散的具体解决方案对应到相应业务流程中,整合成一套完整的业务策略和解决方案。
步骤五设计执行的工具、制度1、设计出可执行的流程、动作、和标准、并制定一一对应的表格工具;2、制定出激励与处罚机制;步骤六设计培训内容1、方案优化后制作图文并茂的课件进行培训、确定授课人、培训对象、时间、地点;2、培训完成后考试,根据考试结果、对培训课件、培训方式进行优化。
步骤七设计检核工具、检核流程1、制定检核流程,明确检查人、检查内容、标准、频率、被检查的对象与事物、检查反馈的交付物;2、收集业务相关者执行过程中的问题反馈对方案细节进行优化、方案优化与调整的内容进行通告与培训、形成循环。
步骤八分析业务策略的效益分析业务策略的执行情况、是否达到预期的目标、不断的用数据来优化业务。
PDCA解决问题八步法

---------------------------------------------------------------最新资料推荐------------------------------------------------------PDCA解决问题八步法PDCA解决问题八步法部门 Division 版本号 Version轿车一厂总装二车间T-P-CP1-4T-P-CP1-401 2016-03-141更新日期 Date1/ 30目录01 学习PDCA的目的? 1.1 PDCA简单概述 ? 1.2 PDCA是推动团队成长和持续改进的有力工具 ? 1.3 PDCA循环是解决问题和决策的基本技能 ? 1.4 PDCA循环可以增强工作的计划性 ? 1.5 PDCA循环是管理的基础,可以提升例行工作水平02 PDCA详解? 2.1 PDCA 的解释及来源? 2.2 PDCA的四阶段? 2.3 PDCA八步骤详解 ? 2.4 PDCA 三特点五要素轿车一厂总装二车间T-P-CP1-42---------------------------------------------------------------最新资料推荐------------------------------------------------------ 一、学习PDCA的目的? 1.1 PDCA简单概述? PDCA,是高度概括的持续提升的方法论,是通用的管理方法。
实践证明它是崇尚持续改善的企业必备的思维和行动方式。
这个工具适用性很强,可以用来解决各种各样的问题,简单易懂、容易上手,是拥有基本读写能力的人都可以做的事情。
? 详细讲解PDCA的目的:训练员工理解和掌握PDCA管理循环,从而把PDCA的方法论通过不同层级人员参加的各类改善行为的锻炼,形成全员共同的思维模式,落实于日常的各项工作中。
? 总装车间到处都有改进,到处都有问题解决,“促进问题的解决是每一位员工最基本的职业素养”,学会并熟练运用PDCA整套问题解决的思维流程去正确地做事,才能“运筹于帷幄之中,决胜于千里之外”,才能持续深化我们的知识和技能从而成长为合格的员工。
- 1、下载文档前请自行甄别文档内容的完整性,平台不提供额外的编辑、内容补充、找答案等附加服务。
- 2、"仅部分预览"的文档,不可在线预览部分如存在完整性等问题,可反馈申请退款(可完整预览的文档不适用该条件!)。
- 3、如文档侵犯您的权益,请联系客服反馈,我们会尽快为您处理(人工客服工作时间:9:00-18:30)。
- 44 46 48 44 47
观测月日 观测时间 789
34 21 09 778 45 32 19 11 11 10 47 35 21 232 57 45 30 10 10 9 01 48 33 433 11 58 44 10 10 11 14 01 46 332
47 47 45
85-1-1 PM2:00 10 11
ENVIRONMENT 环境
MAN 人
METHOD 方法
4M1E
MACHINE 机器
MATERIAL 物料
44、、鱼鱼骨骨图图
原因1
原因2
结果
原因3
原因4
55、、55WWHHYY
丰田汽车公司前副社长大野耐一先生曾举了一个例子来找出停机的真 正原因。
有一次,大野耐一发现生产线上的机器总是停转,虽然修过多次但仍 不见好转。于是,大野耐一与工人进行了以下的问答: 一问:为什么机器人停了?---保险丝就断了 一问:为什么保险丝烧断了---线路过载 一问:为什么线路会过载---轴承损坏且卡住了 一问:为什么轴承会损坏 ---轴承润滑不够 一问:为什么轴承润滑不够---机器人的油泵送油不足 一问:为什么机器人的油泵送油不足---油泵的进油口被堵塞了 一问:为什么油泵的进油口被堵塞---油里混进了金属屑 一问:为什么油里混进了金属屑---油泵的进油口未安装过滤器
四四句句话话
问题描述需要标准化、具体化、数字化;
案例:错误与正确描述问题的习惯
错误的习惯
文文字字
明天\上午
经常\总是 好几次 大概\可能
转变
报告
正确的习惯
数数字字
上午8:45
89.3% 230片 5次/月 报表
3、正确描述问题的工具-5W2H
((11)) WWHHYY————为为什什么么??为为什什么么要要这这么么做做??理理由由何何在在??原原因因是是什什么么?? ((22)) WWHHAATT————是是什什么么??目目的的是是什什么么??做做什什么么工工作作?? ((33)) WWHHEERREE————何何处处??在在哪哪里里做做??从从哪哪里里入入手手?? ((44)) WWHHEENN————何何时时??什什么么时时间间完完成成??什什么么时时机机最最适适宜宜?? ((55)) WWHHOO————谁谁??由由谁谁来来承承担担??谁谁来来完完成成??谁谁负负责责?? ((66)) HHOOWW————怎怎么么做做??如如何何提提高高效效率率??如如何何实实施施??方方法法怎怎样样?? ((77)) HHOOWW MMUUCCHH————多多少少??做做到到什什么么程程度度??数数量量如如何何??质质量量水水平平如如何何?? 费费用用产产出出如如何何??
中1
方
个) 向
操
作
0个
注:材料、成品不包括在标准中间在库数内 无自动加工 各机械都没有自动装卸装置
工艺老化标准在制品举例
转圈时间 = 120 秒
在制品WIP=
节拍时间 TT = 25秒
A
M
M
= 在制品 WIP
特殊工艺流 程转盘
A
A = 自动
M = 手动
标准在制品 =
M
原料RM
M
成品 FG
件 units
25
32 500 300 846
7秒 25秒
30
35 - - 788
5秒 30秒
编制时间: 年 月 日 作成:
例 护罩、油泵加工生产线
编制日期
2009年9月16日 作成:
生产线名 品号 品名
MH-0221 J537-1600 罩、油泵
标准作业 组合票
分解编号 必需数 T.T
1/1 560pcs/日
合
31
计
自动机时间 完成时间 分 28秒 分 33秒
交换刃具 个数 时间
600 120
加工 能力 (78 8)
831
备注图示时间 手作业 自动机........
5秒 28秒
25
28 600 120 978 3秒 25秒
19
24 500 300 1121 5秒 19秒
21
27 500 300 1000 6秒 21秒
54 43 89 05 53 11 10 08 56 33 19 07 11 11 23 10 43 32 20 9 10 34 23 23
48 49
分解号
观测者 要素作 业时间
7
1/1
张某某
着眼点(准 备时间)
算出
11
Step6
2
9
决定/核准
3 Step7
9
3 CT=44
Step5
决定
例 护罩、油泵加工生产线
工序能力表 品号 3537-1600
单位
姓名
生产线名 MH-0221
品名 罩、油泵
2-23系
张三
序 工序名 机 基本时间
号称
号
手作业时
间
1 基准面 LS0 分 5秒
切削
23
2 端面切 LS0
3
削
24
3 钻 10 DR
5
孔
o85
4 钻 5孔 DR
6
086
5 钻 20 DR
7
孔
060
6 清洗
CL0
5
34
品质方面
•加工品质问题少 •精度偏差小
遵守标准作业可以保证品质也决定数量、成本
2、标准作业的三要素
标准作业三要素
标
作
准
业
工
顺
时
序
(T.T)
标 准 手 持 量
用最小限度的作业人员和在制品进行的 所有工序之间的同步生产
3、标准作业三件套
标准作业三件套
标
工
序 能
准
标
作
准
业
作
力
组
业
表
合
票
票
5、确定标准作业的步骤
CT 分解号
6
49
49
1/1
重点(KPI) 量化的要求 流程
SOP三要素
十、防错技术
断根原理 对称原理 自动原理 顺序原理 互锁(保险)原理
隔离原理
层别原理
复制原理
警告原理 缓和原理
•• 傻傻瓜瓜插插头头 •• 照照相相机机快快门门防防错错装装置置 •• 空空调调的的红红飘飘带带 •• 螺螺栓栓是是否否紧紧到到位位 •• 检检查查表表 •• 拆拆装装螺螺栓栓
逆物流方向操作
有自动加工时
无自动加工时
有工件老化、降 温、干燥或自动 检测设备时 两个相邻的作业 者之前要增加一 个标准中间在库 即拉动超市
0个(机械 外) 1个(机械 外) 1个(机器 中) 0个
根据需要
看板管理
自动加工
2个
逆 (机械 方 中/前 向 各1 操 个)
作 1个
(加工
前1
个)
1个
(机械 顺
生产线名 MH0221
品号 品名
3537-1600 罩、油泵
例 标准作业票
作业内容 从 取材料
编制日期 2009年9月16日 作成:
到 放置成品
瓶颈
CL034
完成品 ⑧ ⑦ 材料 ① ②
不包括标准手持
LS023
DR060
DR01/5
④ 1/100 DR085
LS024
品质检查 安全标记 标准手持 标准手持数 TT
案例:正确利用描述问题的工具-5W2H
内容 WHAT WHERE
WHEN WHO HOW MUCH HOW WHY
是什么? 间隙是9+1MM A生产线B工位
下午上班0.5小时 张三
不良率95% 下道工序无法加工
操作问题
不是什么? 间隙没问题
×其它工位
其它时段也有发生 其它人
良品只有5%
—— 图纸问题
(1)现状把握
P
(2)要因解析
(3)设定目标
(4)确立计划
(5)对策树立
D
(6)实施对策
C
(7)效果确认
A
(8)标准化
重新构筑
PDCA
改善循环
★.问题描述
1、问题描述的现状
• 模糊而不够精确 • 想当然而不习惯还原真像 • 标准不统一或经常变化
2、正确描述问题的习惯
• 先说过程,不说原因; • 说自己,不说别人; • 要精确,不要模糊; • 要事实,不要感觉;
最后将这台机器加装了过滤器,停机的问题得以根本解决。
小结
1.问题描述需要标准化、具体化、数字化; 2.对问题进行排序,用全局的观念去解决; 3.用5W2H分析问题 4.对问题产生的原因排序,找出关键因素; 5.现场问题需要现场、现状、现物分析。
八、标准作业
1、标准作业概要
定义
以人的动作为中 心,把工序集中 起来,以没有 MUDA的操作顺序 有效的进行生产 的方法。
顺序原理
汽车 范例
没有 踩住 煞车 时不 能启 动。
互锁原理
当你 放开 手柄 时, 割草 机立 即停
止
冲压机双手按钮
隔离原理
范例
层别原理
范例
目视/警告方法
不同颜色
标签检查
消防自动喷洒
清单检查
警报
范例
安
鸡
全
蛋
安
气
托
全
囊
盘
帽
防
静
防
电
静
橡
电
胶
工
指
鞋
训 练 Tra ini ng