PLC如何应用到轧钢生产线中
PLC在钢铁冶金企业电气自动化控制中的应用

PLC在钢铁冶金企业电气自动化控制中的应用钢铁冶金企业是一个电力、机械和自动化密集度较高的行业,而PLC(Programmable Logic Controller,可编程逻辑控制器)在这个行业的电气自动化控制中扮演着非常重要的角色。
下面将详细介绍PLC在钢铁冶金企业电气自动化控制中的应用。
PLC在钢铁冶金企业中常用于控制和监测生产线的运行。
通过PLC,可以实现对生产线各个设备的控制和监测,例如炼铁炉、炼钢炉、连铸机等设备的开启、停止、自动控温、速度控制等。
PLC可以根据工艺流程的要求,编写相应的控制程序,确保生产线能够按照需要进行工作,同时实现对各个设备运行状态的监测和报警功能,确保生产的安全和稳定。
PLC还可以用于实现钢铁冶金企业的数据采集和远程监控。
通过与传感器和仪表的连接,PLC可以采集各种生产过程中的数据,如温度、压力、流量等参数。
这些数据可以实时传输到上位机,进行数据分析和处理,为企业的生产决策提供依据。
通过PLC可以实现对生产过程的远程监控,监测设备的运行状态,及时调整和处理异常情况,提高生产的效率和质量。
PLC还可以用于实现钢铁冶金企业的能源管理和节能控制。
钢铁冶金企业消耗的能源较大,节能成为企业的重要任务。
通过PLC,可以对各个设备进行能源消耗的监测和控制,实现能源的优化配置和节约利用。
通过对生产过程的监测和数据分析,可以找出能源消耗较大的环节,进行合理调整和控制,降低能源消耗,并且可以实现对能源的实时监测和统计,为企业的能源管理提供支持。
PLC还可以用于实现钢铁冶金企业的安全控制和报警。
钢铁冶金企业往往存在一些危险环境,如高温、高压、有毒气体等,对工人的安全有较大的威胁。
通过PLC,可以实现对这些危险环境的监测和控制,当危险情况发生时,PLC可以自动发出报警信号,并采取相应的安全措施,确保工人的安全。
PLC在钢铁冶金企业电气自动化控制中具有非常重要的应用价值。
它可以用于控制和监测生产线的运行、实现数据采集和远程监控、实现能源管理和节能控制、以及实现安全控制和报警等功能,提高企业的生产效率和质量,降低能源消耗,保障工人的安全,对钢铁冶金企业的发展具有重要意义。
PLC在钢铁冶金企业电气自动化控制中的应用

PLC在钢铁冶金企业电气自动化控制中的应用PLC是一种专门用于工业控制系统的电子设备,它采用可编程的逻辑控制器,能够根据预设的程序自动执行各种控制操作。
在钢铁冶金生产过程中,PLC可以实现自动化控制的各种功能,包括物料输送、温度控制、测量与检测、安全保护和故障诊断等。
下面就针对这些功能来具体分析PLC在钢铁冶金企业中的应用。
PLC在钢铁冶金企业中的物料输送控制方面发挥着重要作用。
在钢铁冶金生产过程中,原材料、中间产品和成品需要通过输送设备进行运输。
PLC可以通过对输送设备的控制,实现物料的自动化输送,提高生产效率和降低人力成本。
通过PLC控制,可以实现物料输送过程中的自动刹车、速度调节、方向控制等功能,确保物料输送过程的安全和稳定。
PLC在温度控制方面也具有重要作用。
钢铁冶金生产过程中,需要对物料和设备进行精确的温度控制,以确保生产过程的正常进行。
PLC可以通过连接温度传感器和执行器,实现对温度信号的采集和控制。
PLC还可以根据预设的温度控制程序,对加热、冷却设备进行自动控制,确保温度稳定在设定范围内,提高产品质量和生产效率。
PLC在安全保护和故障诊断方面也能够发挥重要作用。
钢铁冶金生产过程中存在各种安全隐患和设备故障问题,需要及时进行处理和解决,以确保生产安全和设备正常运行。
PLC可以通过连接安全传感器和执行器,实现对生产过程中的安全隐患的实时监测和预警。
PLC还可以通过连接故障诊断设备,实现对设备故障的实时诊断和报警。
通过PLC控制,可以实现对生产过程中的安全隐患和设备故障问题的及时处理,确保生产安全和设备正常运行。
PLC在钢铁冶金企业电气自动化控制中的应用非常广泛,可以实现物料输送、温度控制、测量与检测、安全保护和故障诊断等各种功能。
通过PLC控制,可以实现生产过程的自动化和智能化,提高生产效率和产品质量,降低生产成本和人力成本,确保生产安全和设备正常运行。
钢铁冶金企业在电气自动化控制系统的建设和应用中,需要充分重视PLC的应用,发挥其重要作用。
浅谈PLC系统在轧钢产线自动控制中的应用
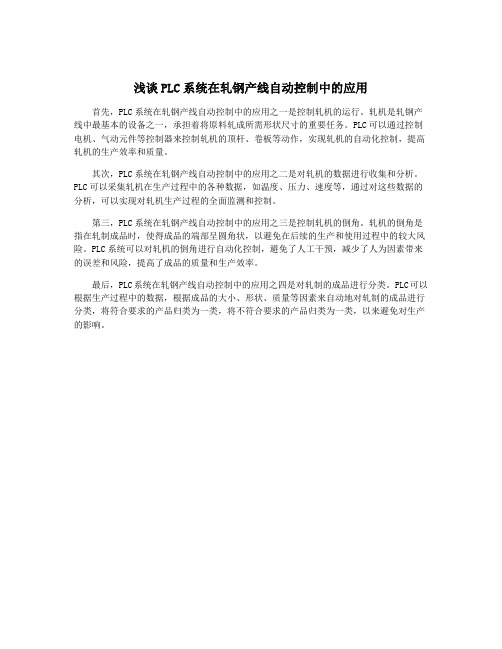
浅谈PLC系统在轧钢产线自动控制中的应用
首先,PLC系统在轧钢产线自动控制中的应用之一是控制轧机的运行。
轧机是轧钢产线中最基本的设备之一,承担着将原料轧成所需形状尺寸的重要任务。
PLC可以通过控制电机、气动元件等控制器来控制轧机的顶杆、卷板等动作,实现轧机的自动化控制,提高轧机的生产效率和质量。
其次,PLC系统在轧钢产线自动控制中的应用之二是对轧机的数据进行收集和分析。
PLC可以采集轧机在生产过程中的各种数据,如温度、压力、速度等,通过对这些数据的分析,可以实现对轧机生产过程的全面监测和控制。
第三,PLC系统在轧钢产线自动控制中的应用之三是控制轧机的倒角。
轧机的倒角是指在轧制成品时,使得成品的端部呈圆角状,以避免在后续的生产和使用过程中的较大风险。
PLC系统可以对轧机的倒角进行自动化控制,避免了人工干预,减少了人为因素带来的误差和风险,提高了成品的质量和生产效率。
最后,PLC系统在轧钢产线自动控制中的应用之四是对轧制的成品进行分类。
PLC可以根据生产过程中的数据,根据成品的大小、形状、质量等因素来自动地对轧制的成品进行分类,将符合要求的产品归类为一类,将不符合要求的产品归类为一类,以来避免对生产的影响。
PLC在轧钢生产线的应用
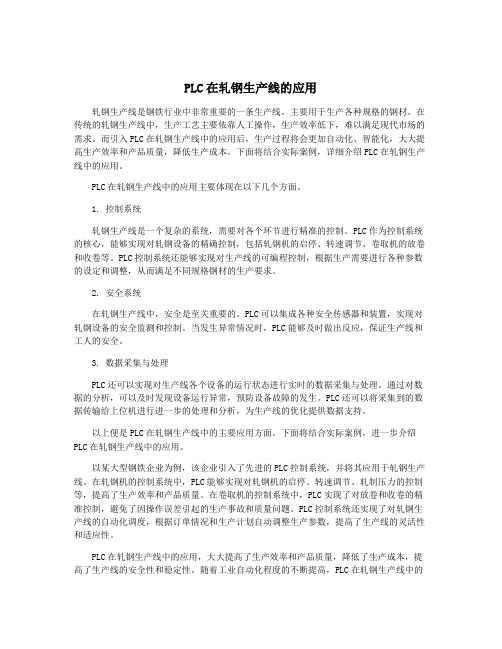
PLC在轧钢生产线的应用轧钢生产线是钢铁行业中非常重要的一条生产线,主要用于生产各种规格的钢材。
在传统的轧钢生产线中,生产工艺主要依靠人工操作,生产效率低下,难以满足现代市场的需求。
而引入PLC在轧钢生产线中的应用后,生产过程将会更加自动化、智能化,大大提高生产效率和产品质量,降低生产成本。
下面将结合实际案例,详细介绍PLC在轧钢生产线中的应用。
PLC在轧钢生产线中的应用主要体现在以下几个方面。
1. 控制系统轧钢生产线是一个复杂的系统,需要对各个环节进行精准的控制。
PLC作为控制系统的核心,能够实现对轧钢设备的精确控制,包括轧钢机的启停、转速调节、卷取机的放卷和收卷等。
PLC控制系统还能够实现对生产线的可编程控制,根据生产需要进行各种参数的设定和调整,从而满足不同规格钢材的生产要求。
2. 安全系统在轧钢生产线中,安全是至关重要的。
PLC可以集成各种安全传感器和装置,实现对轧钢设备的安全监测和控制。
当发生异常情况时,PLC能够及时做出反应,保证生产线和工人的安全。
3. 数据采集与处理PLC还可以实现对生产线各个设备的运行状态进行实时的数据采集与处理。
通过对数据的分析,可以及时发现设备运行异常,预防设备故障的发生。
PLC还可以将采集到的数据传输给上位机进行进一步的处理和分析,为生产线的优化提供数据支持。
以上便是PLC在轧钢生产线中的主要应用方面。
下面将结合实际案例,进一步介绍PLC在轧钢生产线中的应用。
以某大型钢铁企业为例,该企业引入了先进的PLC控制系统,并将其应用于轧钢生产线。
在轧钢机的控制系统中,PLC能够实现对轧钢机的启停、转速调节、轧制压力的控制等,提高了生产效率和产品质量。
在卷取机的控制系统中,PLC实现了对放卷和收卷的精准控制,避免了因操作误差引起的生产事故和质量问题。
PLC控制系统还实现了对轧钢生产线的自动化调度,根据订单情况和生产计划自动调整生产参数,提高了生产线的灵活性和适应性。
PLC在轧钢生产线的应用

PLC在轧钢生产线的应用
PLC(可编程逻辑控制器)在轧钢生产线中广泛应用,主要用于自动化控制和监视整个生产过程。
下面将详细介绍PLC在轧钢生产线中的应用。
在轧钢生产线的初轧段,PLC用于控制和监视各种设备的操作。
PLC可以控制主驱动电机的开关和速度,以确保轧制辊正常运转。
它还可以监测轧辊的温度、压力和振动,及时发现异常并做出相应的处理。
在轧钢生产线的中间轧段,PLC起到了非常重要的作用。
它可以利用传感器实时监测钢坯的宽度、厚度和重量等参数,并通过PLC进行数据处理和分析。
当钢坯不符合规定要求时,PLC可以自动调整轧辊的位置和压力,以确保产出的产品符合标准。
这大大提高了生产效率和产品质量。
在轧钢生产线的精轧段,PLC在控制和监视冷却系统方面发挥重要作用。
PLC可以实时监测冷却水的温度和流量,并控制冷却水的供给量。
当冷却水温度过高或流量异常时,PLC会发出警报并自动关闭冷却水的供给。
PLC还可以控制辊道的速度和冷却时间,以确保轧制后的产品具有理想的硬度和表面质量。
在轧钢生产线的尾段,PLC用于控制钢坯的切割和堆垛操作。
PLC可以根据产品规格和长度要求,自动调整切割刀的位置和速度。
它还可以控制堆垛机器人的动作和坯料的堆垛方式,使得堆垛过程更加高效和精确。
PLC在轧钢生产线中的应用具有多样性和重要性。
它可以实现自动化控制和监视整个生产过程,提高生产效率和产品质量。
随着技术的不断进步,PLC在轧钢生产线中的应用将进一步发展和完善。
PLC在轧钢生产线的应用
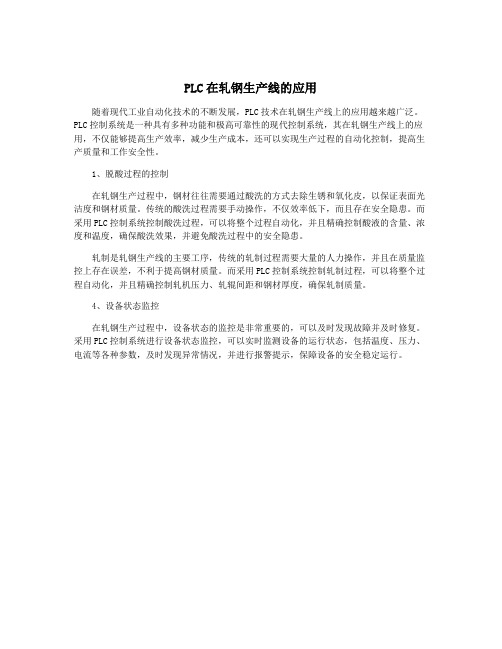
PLC在轧钢生产线的应用
随着现代工业自动化技术的不断发展,PLC技术在轧钢生产线上的应用越来越广泛。
PLC控制系统是一种具有多种功能和极高可靠性的现代控制系统,其在轧钢生产线上的应用,不仅能够提高生产效率,减少生产成本,还可以实现生产过程的自动化控制,提高生产质量和工作安全性。
1、脱酸过程的控制
在轧钢生产过程中,钢材往往需要通过酸洗的方式去除生锈和氧化皮,以保证表面光洁度和钢材质量。
传统的酸洗过程需要手动操作,不仅效率低下,而且存在安全隐患。
而采用PLC控制系统控制酸洗过程,可以将整个过程自动化,并且精确控制酸液的含量、浓度和温度,确保酸洗效果,并避免酸洗过程中的安全隐患。
轧制是轧钢生产线的主要工序,传统的轧制过程需要大量的人力操作,并且在质量监控上存在误差,不利于提高钢材质量。
而采用PLC控制系统控制轧制过程,可以将整个过程自动化,并且精确控制轧机压力、轧辊间距和钢材厚度,确保轧制质量。
4、设备状态监控
在轧钢生产过程中,设备状态的监控是非常重要的,可以及时发现故障并及时修复。
采用PLC控制系统进行设备状态监控,可以实时监测设备的运行状态,包括温度、压力、电流等各种参数,及时发现异常情况,并进行报警提示,保障设备的安全稳定运行。
PLC在轧钢生产线的应用
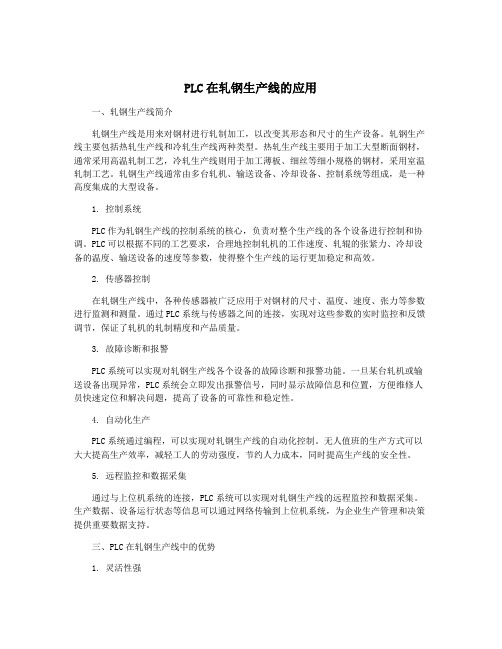
PLC在轧钢生产线的应用一、轧钢生产线简介轧钢生产线是用来对钢材进行轧制加工,以改变其形态和尺寸的生产设备。
轧钢生产线主要包括热轧生产线和冷轧生产线两种类型。
热轧生产线主要用于加工大型断面钢材,通常采用高温轧制工艺,冷轧生产线则用于加工薄板、细丝等细小规格的钢材,采用室温轧制工艺。
轧钢生产线通常由多台轧机、输送设备、冷却设备、控制系统等组成,是一种高度集成的大型设备。
1. 控制系统PLC作为轧钢生产线的控制系统的核心,负责对整个生产线的各个设备进行控制和协调。
PLC可以根据不同的工艺要求,合理地控制轧机的工作速度、轧辊的张紧力、冷却设备的温度、输送设备的速度等参数,使得整个生产线的运行更加稳定和高效。
2. 传感器控制在轧钢生产线中,各种传感器被广泛应用于对钢材的尺寸、温度、速度、张力等参数进行监测和测量。
通过PLC系统与传感器之间的连接,实现对这些参数的实时监控和反馈调节,保证了轧机的轧制精度和产品质量。
3. 故障诊断和报警PLC系统可以实现对轧钢生产线各个设备的故障诊断和报警功能。
一旦某台轧机或输送设备出现异常,PLC系统会立即发出报警信号,同时显示故障信息和位置,方便维修人员快速定位和解决问题,提高了设备的可靠性和稳定性。
4. 自动化生产PLC系统通过编程,可以实现对轧钢生产线的自动化控制。
无人值班的生产方式可以大大提高生产效率,减轻工人的劳动强度,节约人力成本,同时提高生产线的安全性。
5. 远程监控和数据采集通过与上位机系统的连接,PLC系统可以实现对轧钢生产线的远程监控和数据采集。
生产数据、设备运行状态等信息可以通过网络传输到上位机系统,为企业生产管理和决策提供重要数据支持。
三、PLC在轧钢生产线中的优势1. 灵活性强PLC系统的编程灵活,可以根据不同的生产要求和工艺参数进行调整,适应不同规格和品种的钢材生产。
2. 稳定可靠PLC系统具有高度集成的特点,能够对设备和生产过程进行全面控制和监控,保证了轧钢生产线的稳定运行。
浅谈PLC系统在轧钢产线自动控制中的应用

浅谈PLC系统在轧钢产线自动控制中的应用1. 引言1.1 PLC系统的定义可编程逻辑控制器(PLC)是一种用于工业控制系统的特殊计算机,其主要功能是监控输入信号并根据程序控制输出设备。
PLC系统通过接收来自传感器或开关的输入信号,经过内部程序处理后控制执行器或电机等输出设备的工作,实现对工业设备或生产过程的自动控制。
PLC系统具有可编程、高可靠性、灵活性强、开放式架构等特点,因而被广泛应用于各类自动化控制系统中,包括轧钢产线。
PLC系统的设计基于逻辑控制原理,通过在PLC的编程软件中设定各个输入信号与输出设备之间的逻辑关系,实现对产线各个部分的精确控制。
PLC系统可以根据生产需求随时修改程序,使得轧钢产线可以快速适应不同工艺参数或生产规格的变化。
PLC系统还可以实现监控和数据记录功能,帮助运营人员及时了解产线运行状态,提高生产效率和质量控制水平。
1.2 轧钢产线自动控制的重要性轧钢产线自动控制的重要性在于提高生产效率、保障产品质量、减少人工操作、降低生产成本,提高生产线的稳定性和可靠性。
通过PLC系统实现轧钢产线的自动控制,可以将生产过程中的各种数据实时监测和控制,自动进行调节和处理,避免了人为因素对生产造成的干扰,提高了生产线的运行效率和产品质量稳定性。
而且PLC系统能够根据不同需求自动调整生产参数,实现生产线的智能化管理,可以更好地适应市场需求的变化和产品新旧的更新迭代。
轧钢产线自动控制的重要性不仅体现在提高生产效率和产品质量的方面,同时也在于提升企业的竞争力,实现经济效益的最大化。
通过PLC系统在轧钢产线中的应用,可以有效提高生产线的工作效率,降低生产成本,同时也可以实现生产过程的智能化和自动化,为轧钢产线的发展注入新的活力和动力。
2. 正文2.1 PLC系统在轧钢产线中的应用介绍PLC系统在轧钢产线中的应用主要包括控制轧机的启停、速度调节、张力控制、轧辊调整等功能。
通过PLC系统可以实现对整个轧钢过程的实时监测和控制,实现自动化生产。
- 1、下载文档前请自行甄别文档内容的完整性,平台不提供额外的编辑、内容补充、找答案等附加服务。
- 2、"仅部分预览"的文档,不可在线预览部分如存在完整性等问题,可反馈申请退款(可完整预览的文档不适用该条件!)。
- 3、如文档侵犯您的权益,请联系客服反馈,我们会尽快为您处理(人工客服工作时间:9:00-18:30)。
PLC在轧钢生产线监控系统中的 应用
画面的开发方法
1)监控画面的开发方法 实时监控系统上机应用软件的开发建立在组态软件的基础之上, 是工业控制系统软件开发的一个方向。当计算机硬件有了飞速发展之 后,各种应用领域对软件提出了更高的要求。 2)组态软件 wincc软件基于PLC硬件,运行在Windows平台上的一种组态软 件,该组态主要是应用程序的集成开发环境,软件开发者在这个环境 中完成界面的设计,变量的定义等工作,它具有先进完善的图形生成 功能;同时具有数据报警,趋势曲线,过程记录,安全防范等重要功能, 组态显示画面是软件的是实时运行环境,用于显示画面开发系统中建 立的图形画面,并负责软件与PLC之间的数据交换,实时更新变量的 数值。
监控画面的设计
1)wincc在轧钢监控系统中的工艺流程 根据相关案例分析统计得出,在目前的生产工艺中,wincc在轧 钢生产监控系统中的应用包含了六辊可逆冷轧机组、推拉式酸洗线、 罩式退火炉、平整机、拉弯矫直和联合剪,主要装备为全液压压下、 液压AGC自动控制、机组全数字直流供电。 2)应用特点 工艺特点:(1)控制周期快; (2)控制功能多; (3)控制功能之间存在较强的耦合。 作为过程生产方和维护方来说,性能优异的过程监测系统是实现 优化过程控制的重要条件。所以要求基于以太网的监测操作系统必须 具有下面的基本特点:可靠性;灵活性;开放性;可维护性。
通信服务阶段
在此阶段,PLC与一些智能模块通信、响 应编程器键入的命令,更新编程器的显示内容 等,当PLC处于停状态时,只进行内容处理和 通信操作等内容。
输入处理阶段
输入处理也叫输入采样。在此阶段顺序读 取所有输入端子的通断状态,并将所读取的信 息存到输入映像寄存器中,此时,输入映像寄 存器被刷新。
PLC如何应用到轧钢生产线中
整理者:机械580
可编程控制器概述
可编程控制器也就是我们普遍说的PLC,它是以转化工业生产模 式为主设计的,采用了可编程控制储存器、计算器,以保证数据的科 学、高效运行,并且能够实现顺序控制、逻辑运算、定时操作等指令, 通过模拟信号和数字信号相结合来进行系统管理,这种系统的应用克 服了传统手工机电操作的限制,也避免了传统设备线路复杂、可靠性 低、功耗高以及灵活性差的缺陷,充分利用了微电子技术和信息技术 的优点,全面实现了工业生产的自动化、综合化和现代化需求。
可编程控制器在轧钢生产线中的应用
可编程控制器在轧钢生产线中的 应用原理
系统组成 在目前我国的轧钢生产器中的可编程控制系统中,整个系统组成 都是以开放性集散控制系统为主,是通过操作人员、操作站、CPU机 架以及通道共同组成的。 在整个管理系统中,整个系统包含了软件系统和应用软件两个不 同组成部分,其中系统软件主要是以中央处理器和位处理器为主的, 它包含了微型处理器、存储器以及语言执行器三部分,而应用软件则 包含了读写存储器、语言编程器、程序设计器等。
程序处理阶段
按先上后下,先左后右的步序,对梯形图 程序进行逐句扫描并根据采样到输入映像寄存 器中的结果进行逻辑运算,运算结果再存入有 关映像寄存器中。但遇到程序跳转指令,则根 据跳转条件是否满足来决定程序的跳转地址。
输出刷新阶段
程序处理完毕后,将所有输出映象寄存器 中各点的状态,转存到输出锁存器中,再通过 输出端驱动外部负载。
工作原LC有运行模式和停止模 式。其中运行模式:分为内部处理、通信操作、 输入处理、程序执行、输出处理五个阶段。 停止模式 当处于停止工作模式时,PLC只进行内部 处理和通信服务等内容。
在生产线中的应用过程
内部处理阶段 在此阶段,PLC检查CPU模块的硬件是否 正常,复位监视定时器,以及完成一些其它内 部工作。