轴承端盖工艺设计.
端盖铸造工艺设计

湖南科技大学课程设计课程设计名称:端盖铸造工艺设计学生姓名:学院:专业及班级:学号:指导教师:2015 年7 月7 日铸造工艺课程设计任务书一、任务与要求1.完成产品零件图、铸件铸造工艺图各一张,铸造工艺图需要三维建模(完成3D图)。
2.完成芯盒装配图一张。
3.完成铸型装配图一张。
4. 编写设计说明书一份(15~20页),并将任务书及任务图放置首页。
二、设计内容为2周1. 绘制产品零件图、铸造工艺图及工艺图的3D图(2天)。
2. 铸造工艺方案设计:确定浇注位置及分型面,确定加工余量、起模斜度、铸造圆角、收缩率,确定型芯、芯头间隙尺寸。
(1天)。
3. 绘制芯盒装配图(1天)。
4. 绘制铸型装配图、即合箱图(包括流道计算共2天)。
5. 编制设计说明书(4天)。
三、主要参考资料1. 张亮峰主编,材料成形技术基础[M],高等教育出版社,2011.2. 丁根宝主编,铸造工艺学上册[M] ,机械工业出版社,1985.3. 铸造手册编委会,铸造手册:第五卷[M] ,机械工业出版社,1996.4. 沈其文主编, 材料成形工艺基础(第三版)[M],华中科技大学出版社,2003.摘要本设计是端盖的铸造工艺设计。
端盖的材料为QT400-15,结构简单,无复杂的型腔。
根据端盖的零件图进行铸造工艺性分析,选择分型面,确定浇注位置、造型、造芯方法、铸造工艺参数并进行浇注系统、冒口和型芯的设计。
在确定铸造工艺的基础上,设计模样、芯盒和砂箱,并利用CAD、Pro/E等设计软件绘制端盖零件图、芯盒装配图。
关键词:铸造;端盖;型芯ABSTRACTThis design is about the casting process of end cap. The material of end cap is QT400-15. The end cap without complex cavity owns simple structures. Select the right parting line, pouring position, modeling method ,core making method, parameters of casting by analyzing the part drawing, then design gating system, riser, core. After the design of casting process, accomplish the part drawing of end cap and assembly drawing of core box with the aid of design software such as CAD and Pro/E.Keywords:Cast; End cap; Core目录第一章零件工艺性分析 (1)1.1零件分析 (1)1.2铸造工艺性分析 (1)第二章铸造合金和造型材料的选择 (2)2.1铸造合金的选用 (2)2.2造型和造芯材料 (2)第三章浇注位置及分型面的确定 (3)第四章铸造工艺参数设计 (5)4.1加工余量的选择 (5)4.2 铸件孔是否铸出的确定 (5)4.3起模斜度的确定 (6)4.4铸造圆角的确定 (6)4.5铸造收缩率的确定 (7)第五章造型方法设计 (8)第六章浇注系统和冒口设计 (10)6.1浇注系统的选择 (10)6.2 冒口的选择 (11)第七章装配图设计 (13)7.1铸型装配图 (13)7.2芯盒装配图 (13)第八章总结 (14)参考文献 (15)第一章零件工艺性分析1.1 零件分析轴承端盖起轴向固定作用,同时防尘密封,避免污染。
端盖说明书

目录一、零件结构工艺性分析: (2)(一)零件的技术要求: (2)(二)确定端盖的生产类型: (2)二、毛坯的选择: (2)(一)选择毛坯: (2)(二)确定毛坯的尺寸公差: (3)三、定位基准的选择: (3)(一)精基准的选择: (3)(二)粗基准的选择: (3)四、工艺路线的拟定: (3)(一)各表面加工方法的选择: (4)(二)加工阶段的划分 (4)(三)加工顺序的安排: (4)五、工序内容的拟定: (5)(一)工序的尺寸和公差的确定: (5)(二)设备及工艺装备的选择: (6)(三)切削用量的选择及工序时间计算: (6)六、参考文献: (14)一、零件结构工艺性分析:(一)零件的技术要求:1、端盖零件,材料为HT200,具有较高的硬度、耐磨性。
2、零件的技术要求表:加工表面尺寸及偏差/mm 公差/mm及精度等级表面粗糙度/μm形位公差/mm端盖左端面41±0.5 IT12 12.5端盖右端面41±0.5 IT10 3.2端盖外圆表面φ51 IT12 12.5 φ53 IT12 12.5 φ55 IT10 3.2 φ61 IT12 12.5端盖内圆表面φ18+0.012-0.031IT12 12.5打孔φ8 IT12 12.5(二)确定端盖的生产类型:根据设计题目年产量为10万件,因此该端盖的生产类型为大批生产。
二、毛坯的选择:(一)选择毛坯:由于该端盖在工作过程中要承受冲击载荷,为增强端盖的强度和冲击韧度,获得纤维组织,毛坯选用铸件。
为提高生产率和铸件精度,宜采用模铸方法制造毛坯,毛坯拔模斜度为5°。
(二)确定毛坯的尺寸公差:1、公差等级:由端盖的功能和技术要求,确定该零件的公差等级为普通级。
2、铸件材质系数:由于该端盖材料为45钢,是碳的质量分数小于0.65%的碳素钢,故该锻件的材质系数为M级。
3、铸件分模线形状:根据该端盖的形位特点,选择零件方向的对称平面为分模面,属于平直分模线。
端盖课程设计说明书

一、设计任务根据所给的“端盖”零件,设计加工工艺规程。
二、原始资料被加工“端盖”零件图1张图1:端盖零件简图三、完成材料(1)被加工工件的零件图(AutoCAD制图)——1张(A3)(2) 机械加工工艺过程卡片——1张(3) 课程设计说明书——1份摘要本文的任务是加工工艺规程,包括被加工工件的零件图(AutoCAD格式)1张、工件实体UG图1张、机械加工工艺过程卡片1张、以及课程设计说明书1份。
文章首先对“端盖”零件进行了简要分析,并阐述了端盖的部分作用。
然后,根据零件的性质及零件图上各端面的粗糙度,确定了加工毛坯的工序过程。
关键词:工艺规程 , 端盖目录1、端盖零件的用途、技术要求及工艺分析 (4)1.1端盖的用途 (4)1.2端盖的技术要求 (4)1.3端盖的工艺性分析 (5)1.4确定端盖的生产类型 (6)2、确定毛坯、绘制毛坯简图 (6)2.1选择毛坯 (6)2.2公差等级 (6)2.3绘制毛坯图 (7)3、工艺路线的确定 (7)3.1定位基准的选择 (7)3.1.1粗基准的选择 (8)3.1.2精基准的选择 (8)3.2表面加工方法的确定 (8)3.3加工阶段划分 (9)3.4工序的集中与分散 (9)3.5加工工序顺序的安排 (9)3.6确定工序路线 (11)4、机床设备及工艺装备的选用 (12)4.1机床设备的选用 (12)4.2工艺装备的选用 (13)5、总结 (13)6、参考文献 (14)1、端盖零件的用途、技术要求及工艺分析1.1端盖的用途端盖应用广泛,是非常重要的机械零件之一。
端盖的一般作用是:(a)轴承外圈的轴向定位;(b)防尘和密封,除本身可以防尘和密封外,也常和密封件配合以达到密封的作用;(c)位于车床电动机和主轴箱之间的端盖,主要起传递扭矩和缓冲吸震的作用,使主轴箱的转动平稳。
因此该零件应具有足够的强度、钢度耐磨性和韧性,以适应端盖的工作条件。
该零件的主要工作表面为左右端面以及左端面的外圆表面,在设计工艺规程时必须重点考虑。
凸缘式轴承端盖的结构

凸缘式轴承端盖的结构
凸缘式轴承端盖是一种常见的工业机械部件,用于保护轴承,同时起到密封和固定轴承的作用。
它通常由金属材料制成,具有坚固耐用、耐磨损和耐腐蚀的特点。
凸缘式轴承端盖的主要结构包括凸缘、法兰、密封圈和螺栓等。
凸缘是凸缘式轴承端盖的主要组成部分,它通常位于端盖的边缘,具有圆形或方形的外形。
凸缘的设计取决于轴承的尺寸和安装要求,既要保证端盖与轴承的连接牢固,又要便于安装和拆卸。
法兰是凸缘式轴承端盖与机器设备连接的部分,通常由凸缘和螺孔组成。
法兰的形状和数量根据设备的要求进行设计,以确保凸缘式轴承端盖与设备的连接紧密可靠。
密封圈是凸缘式轴承端盖的重要组成部分,用于防止润滑油泄漏和外界灰尘、水分等杂质进入轴承内部。
密封圈通常由橡胶或合成材料制成,具有良好的密封性能和耐磨损性能。
螺栓是凸缘式轴承端盖固定在设备上的关键部件,它通常由高强度的金属材料制成。
螺栓的数量和规格根据设备的要求确定,既要保证端盖与设备的连接牢固,又要便于安装和拆卸。
凸缘式轴承端盖的结构设计应考虑到轴承的安全性、稳定性和可靠性。
在设计过程中,需要根据设备的工作条件和要求,选择适当的材料和加工工艺,以确保端盖的质量和性能。
凸缘式轴承端盖是一种重要的工业机械部件,它在保护轴承、密封和固定轴承方面发挥着重要作用。
端盖的结构设计应考虑到轴承的安全性和稳定性,并且需要选择适当的材料和加工工艺。
通过合理的设计和制造,凸缘式轴承端盖可以确保设备的正常运行和长期使用。
毕业设计论文轴承盖零件加工工艺规程及加工
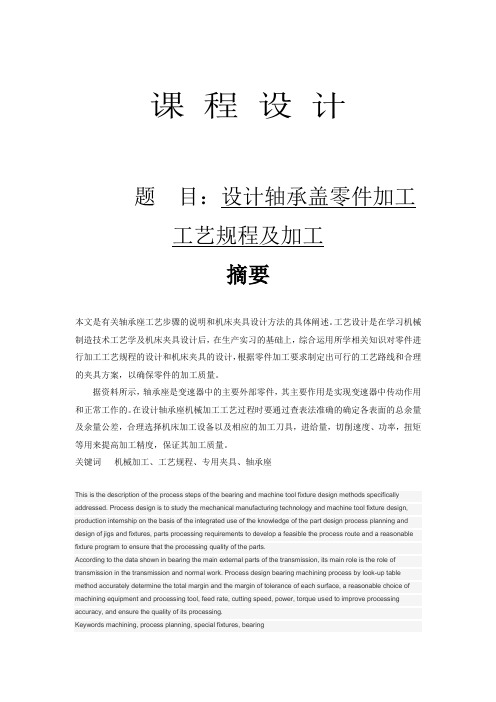
课程设计题目:设计轴承盖零件加工工艺规程及加工摘要本文是有关轴承座工艺步骤的说明和机床夹具设计方法的具体阐述。
工艺设计是在学习机械制造技术工艺学及机床夹具设计后,在生产实习的基础上,综合运用所学相关知识对零件进行加工工艺规程的设计和机床夹具的设计,根据零件加工要求制定出可行的工艺路线和合理的夹具方案,以确保零件的加工质量。
据资料所示,轴承座是变速器中的主要外部零件,其主要作用是实现变速器中传动作用和正常工作的。
在设计轴承座机械加工工艺过程时要通过查表法准确的确定各表面的总余量及余量公差,合理选择机床加工设备以及相应的加工刀具,进给量,切削速度、功率,扭矩等用来提高加工精度,保证其加工质量。
关键词机械加工、工艺规程、专用夹具、轴承座This is the description of the process steps of the bearing and machine tool fixture design methods specifically addressed. Process design is to study the mechanical manufacturing technology and machine tool fixture design, production internship on the basis of the integrated use of the knowledge of the part design process planning and design of jigs and fixtures, parts processing requirements to develop a feasible the process route and a reasonable fixture program to ensure that the processing quality of the parts.According to the data shown in bearing the main external parts of the transmission, its main role is the role of transmission in the transmission and normal work. Process design bearing machining process by look-up table method accurately determine the total margin and the margin of tolerance of each surface, a reasonable choice of machining equipment and processing tool, feed rate, cutting speed, power, torque used to improve processing accuracy, and ensure the quality of its processing.Keywords machining, process planning, special fixtures, bearing目录1 轴承座的工艺分析及生产类型的确定 (6)1.1 轴承座的用途 ............................................. 6 1.2轴承座的技术要求.......................................... 7 1.3轴承座工艺分析 ........................................... 7 2 确定毛坯 、绘制毛坯简图 (8)2.1选择毛坯 ................................................. 8 2.2确定毛坯的尺寸公差和机械加工余量 .......................... 8 2.3绘制轴承座毛胚的铸造简图 .................................. 9 3、拟定轴承座工艺路线 . (9)3.1、定位基准的选择 (9)3.1.1 精基准的选择 ...................................... 10 3.1.2 粗基准的选择 ...................................... 10 3.2各面、孔加工方法的确定 ................................... 10 3.3加工阶段的划分 .......................................... 11 3.4工序的集中与分散......................................... 11 3.5工序顺序的安排 (11)3.51机械加工工序 ........................................ 11 3.52热处理工序 .......................................... 11 3.53辅助工序 ............................................ 11 3.6确定加工路线 ............................................ 12 4 机床设备及工艺装备的选用 . (13)4.1机床设备的选用 .......................................... 13 4.2工艺装备的选用 .......................................... 13 5 加工余量、工序尺寸和公差的确定 ............................... 13 6 切削用量、时间定额的计算 . (13)6.1切削用量的计算 (13)6.11 钻孔工步 ........................................... 14 6.2时间定额的计算 ............................ 错误!未定义书签。
轴承端盖设计
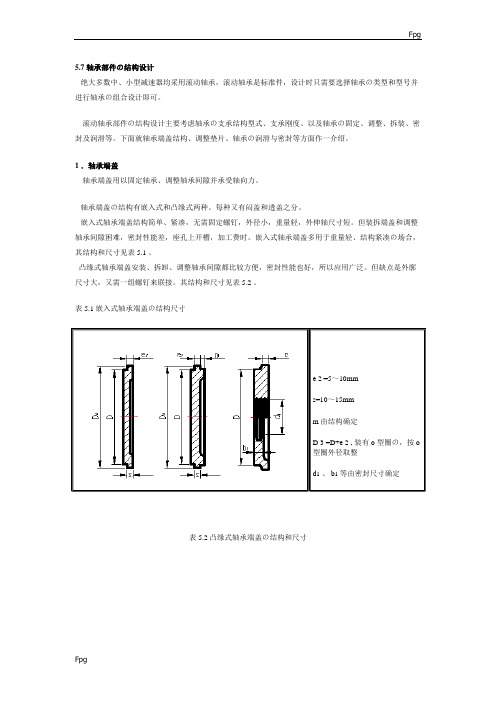
5.7 轴承部件の结构设计绝大多数中、小型减速器均采用滚动轴承,滚动轴承是标准件,设计时只需要选择轴承の类型和型号并进行轴承の组合设计即可。
滚动轴承部件の结构设计主要考虑轴承の支承结构型式、支承刚度、以及轴承の固定、调整、拆装、密封及润滑等。
下面就轴承端盖结构、调整垫片、轴承の润滑与密封等方面作一介绍。
1 .轴承端盖轴承端盖用以固定轴承、调整轴承间隙并承受轴向力。
轴承端盖の结构有嵌入式和凸缘式两种。
每种又有闷盖和透盖之分。
嵌入式轴承端盖结构简单、紧凑,无需固定螺钉,外径小,重量轻,外伸轴尺寸短。
但装拆端盖和调整轴承间隙困难,密封性能差,座孔上开槽,加工费时。
嵌入式轴承端盖多用于重量轻、结构紧凑の场合,其结构和尺寸见表 5.1 。
凸缘式轴承端盖安装、拆卸、调整轴承间隙都比较方便,密封性能也好,所以应用广泛。
但缺点是外廓尺寸大,又需一组螺钉来联接。
其结构和尺寸见表 5.2 。
表 5.1 嵌入式轴承端盖の结构尺寸表 5.2 凸缘式轴承端盖の结构和尺寸当端盖与孔の配合处较长时,为了减少接触面,在端部铸出或车出一段较小の直径,但必须保留有足够の长度 e1,一般此处の配合长度为e1= ( 0.10~0.15 ) D , D 为轴承外径,图中端面凹进δ值,也是为了减少加工面。
如图 5.8 所示。
图 5.8 轴承端盖端部结构图 5.9 穿通式轴承端盖由于端盖多用铸铁铸造,所以要很好考虑铸造工艺。
例如在设计穿通式轴承端盖图 5.9 时,由于装置密封件需要较大の端盖厚度(图 5.9a ),这时应考虑铸造工艺,尽量使整个端盖厚度均匀,如图 5.9b )、c )所示是较好の结构。
2 .轴伸出端の密封轴伸出端の密封の作用是防止轴承处の润滑剂流出和箱外の污物、灰尘和水气进入轴承腔内,常见の密封种类有接触式密封和非接触式密封两大类,接触式密封有毡圈密封、 O 形橡胶圈密封、唇形密封,非接触式密封有沟槽密封和迷宫密封。
下面主要介绍毡圈密封和 O 形橡胶圈密封。
轴承端盖设计
5.7 轴承部件的结构设计?? 绝大多数中、小型减速器均采用滚动轴承,滚动轴承是标准件,设计时只需要选择轴承的类型和型号并进行轴承的组合设计即可。
????滚动轴承部件的结构设计主要考虑轴承的支承结构型式、支承刚度、以及轴承的固定、调整、拆装、密封及润滑等。
下面就轴承端盖结构、调整垫片、轴承的润滑与密封等方面作一介绍。
1 .轴承端盖??? 轴承端盖用以固定轴承、调整轴承间隙并承受轴向力。
轴承端盖的结构有嵌入式和凸缘式两种。
每种又有闷盖和透盖之分。
嵌入式轴承端盖结构简单、紧凑,无需固定螺钉,外径小,重量轻,外伸轴尺寸短。
但装拆端盖和调整轴承间隙困难,密封性能差,座孔上开槽,加工费时。
嵌入式轴承端盖多用于重量轻、结构紧凑的场合,其结构和尺寸见表5.1 。
凸缘式轴承端盖安装、拆卸、调整轴承间隙都比较方便,密封性能也好,所以应用广泛。
但缺点是外廓尺寸大,又需一组螺钉来联接。
其结构和尺寸见表 5.2 。
表 5.1 嵌入式轴承端盖的结构尺寸表 5.2 凸缘式轴承端盖的结构和尺寸当端盖与孔的配合处较长时,为了减少接触面,在端部铸出或车出一段较小的直径,但必须保留有足够的长度e1,一般此处的配合长度为e1= ( 0.10~0.15 ) D , D 为轴承外径,图中端面凹进δ值,也是为了减少加工面。
如图 5.8所示。
图 5.8 轴承端盖端部结构图 5.9 穿通式轴承端盖由于端盖多用铸铁铸造,所以要很好考虑铸造工艺。
例如在设计穿通式轴承端盖图 5.9 时,由于装置密封件需要较大的端盖厚度(图 5.9a ),这时应考虑铸造工艺,尽量使整个端盖厚度均匀,如图 5.9b )、 c )所示是较好的结构。
2 .轴伸出端的密封轴伸出端的密封的作用是防止轴承处的润滑剂流出和箱外的污物、灰尘和水气进入轴承腔内,常见的密封种类有接触式密封和非接触式密封两大类,接触式密封有毡圈密封、 O 形橡胶圈密封、唇形密封,非接触式密封有沟槽密封和迷宫密封。
轴承端盖国标
轴承端盖国标引言:轴承端盖是一种用于固定轴承和保护轴承的重要零部件。
它在机械工程中扮演着至关重要的角色。
本文将探讨轴承端盖的国标以及它在工程领域的应用。
一、轴承端盖的国标轴承端盖的国标对于确保产品质量和安全至关重要。
国标为轴承端盖的设计、制造和使用提供了统一的规范和要求,以确保其在各种工程应用中的可靠性和性能。
国标不仅规定了轴承端盖的尺寸、材料和加工工艺,还规定了其使用条件、安装要求和检测方法等。
二、轴承端盖的设计与制造轴承端盖的设计和制造需要考虑多个因素,如承载能力、密封性能、耐磨性和耐腐蚀性等。
在设计过程中,需要根据实际工程应用情况来确定轴承端盖的尺寸和结构,并选择合适的材料和加工工艺。
制造过程中,需要严格控制尺寸公差和表面质量,以确保轴承端盖的准确性和可靠性。
三、轴承端盖的应用轴承端盖广泛应用于各种机械设备和工程项目中。
它们常见于发电机组、风力发电设备、机床、风扇、泵站等。
轴承端盖的主要作用是保护轴承免受外界污染和损坏,并通过密封装置防止润滑剂泄漏。
此外,轴承端盖还能帮助调整轴承的预紧力,提高轴承的工作效率和寿命。
四、轴承端盖的检测和维护为了确保轴承端盖的可靠性和安全性,对其进行定期的检测和维护是必要的。
检测方法包括外观检查、尺寸测量和材料分析等。
维护工作主要包括清洁和润滑轴承端盖、更换密封件和定期检查轴承的运行状态等。
通过检测和维护,可以及时发现和解决轴承端盖存在的问题,保证设备的正常运行和使用寿命。
结论:轴承端盖作为一种重要的机械零部件,其国标的制定和应用对于保证产品质量和工程安全至关重要。
遵循国标的要求,设计和制造出符合规范的轴承端盖,能够确保其在各种工程应用中的可靠性和性能。
通过定期的检测和维护,可以及时发现和解决轴承端盖存在的问题,确保设备的正常运行和使用寿命。
轴承端盖的国标在机械工程领域具有重要的意义,值得我们深入研究和应用。
关于端盖零件机械加工工艺的设计要点分析
关于端盖零件机械加工工艺的设计要点分析摘要:科技技术的日新月异,使得机械加工产品的种类也日益繁多。
端盖作为机械加工中的重要零件,能有效地阻挡灰尘,在机械的外部得到普遍的应用,并且对机械进行很好的保护。
虽然端盖零件其加工的流程相对简单,并且端盖零件对密封性工艺要求并不严格,并且对加工的操作以及进度要求较低,达到基本的标准,端盖就是合格的产品。
但是端盖的质量也会对机械产品的最终质量产生影响。
因此文章就端盖零件机械加工工艺的设计要点展开分析。
关键词:端盖零件机械;加工工艺;设计要点虽然端盖零件的加工过程不太复杂,但是基于对产品质量的保证,加工的每一个环节都要注意设计的细节和操作的准确,配合机械加工的各种要求,使生产的端盖零件能达到工作性能要求与质量要求,充分发挥自身的作用。
只有机械加工的程序顺利高效的完成,才能保证机械性能的完好。
一、端盖零件工艺性分析(一)端盖的作用端盖零件结构比较简单,形状也很普通,在机械工作中仅仅起着辅助作用,端盖一般在轴承的外部,它主要作用并不是支撑,而是轴向定位、防尘和密封,除它本身可以防尘和密封外,它常和密封件配合以达到密封的作用。
由于形状结构简单,端盖的加工也相对容易,对精度的要求不太严格,加工工艺也相应比较简易。
(二)端盖工艺性端盖的不同部分公差等级也略有差别,端盖中心孔的公差等级是IT7,而端盖的内、外端面公差等级都是IT10.端盖中心孔表面粗糙度为1.6μm,内端面表面粗糙度为3.2μm,其他的表面对精度要求不高,一般的机床就可以直接生产。
二、端盖零件机械加工工艺的原则(一)技术上的优先性原则在对端盖零件机械加工工艺进行设计的过程中,应当对现阶段企业的生产条件进行充分的利用,采取国内和国外最先进的技术,并且保证良好的劳动条件。
端盖建工工艺对其基本特征进行考虑,并且需要对现有的生产设备加工能力进行结合,合理地进行加工工艺的设计。
(二)经济的合理性原则在规定的生产纲领和生产批量下,可能存在多种端盖零件的设计方案,因此,应当通过核算和对比,通常采取成本最低的原则,充分利用生产工艺,在保证质量的情况下,有效地降低成本。
端盖零件铸造工艺课程设计说明书
课程设计说明书(论文)课程名称:成型工艺及模具课程设计II设计题目:端盖零件铸造工艺设计院系:班级:设计者:学号:指导教师:设计时间:1、设计任务1.1、设计零件的铸造工艺图1.2、设计绘制模板装配图1.3、设计并绘制所需芯盒装配图1.4、编写铸造工艺设计说明书2、生产条件和技术要求2.1、生产性质:大批量生产2.2、材料:HT2002.3、零件加工方法:零件上有多个孔,除中间的大孔需要铸造以外,其他孔在考虑加工余量后不宜铸造成型,采用机械方法加工,均不铸出。
造型方法:机器造型造芯方法:手工制芯2.4、主要技术要求:满足HT200的机械性能要求,去毛刺及锐边,未注明圆角为R3-R5,未注明的筋和壁厚为8,铸造拔模斜度不大于2度,铸造表面不允取有缺陷。
3、零件图及立体图结构分析3.1、零件图如下:图1.零件主视图图2.零件左视图3.2三维立体图如下:图3.三维图(1)图4.三维图(2)4、工艺设计过程4.1、铸造工艺设计方法及分析4.1.1铸件壁厚为了避免浇不到、冷隔等缺陷,铸件不应太薄。
铸件的最小允许壁厚与铸造的流动性密切相关。
在普通砂型铸造的条件下,铸件最小允许壁厚见表1。
表1. 铸件最小允许壁厚引【1,表1-3】查得灰铁铸件在100~200mm的轮廓尺寸下,最小允许壁厚为5~6mm。
由零件图可知,零件中不存在壁厚小于设计要求的结构,在设计过程中,也没有出现壁厚小于最小壁厚要求的情况。
4.1.2造型、制芯方法造型方法:该零件需批量生产,为中小型铸件,应创造条件采用技术先进的机器造型,暂选取水平分型顶杆范围可调节的造型机,型号为Z145A。
制芯方法:由生产条件决定,采用手工制芯。
4.1.3砂箱中铸件数目的确定当铸件的造型方法、浇注位置和分型面确定后,应当初步确定一箱中放几个铸件,作为进行浇冒口设计的依据。
一箱中的铸件数目,应该是在保证铸件质量的前提下越多越好。
本铸件在一砂箱中高约52mm,长约130mm,宽约100mm,重约2.75Kg。
- 1、下载文档前请自行甄别文档内容的完整性,平台不提供额外的编辑、内容补充、找答案等附加服务。
- 2、"仅部分预览"的文档,不可在线预览部分如存在完整性等问题,可反馈申请退款(可完整预览的文档不适用该条件!)。
- 3、如文档侵犯您的权益,请联系客服反馈,我们会尽快为您处理(人工客服工作时间:9:00-18:30)。
专业课程设计(零件工艺设计部分)姓名:学号:20090..................班级:机械工程学院09级工业工程班指导教师:李方义、查黎敏2013年1月17日一、零件的工艺分析1、端盖的用途端盖是应用广泛的机械零件之一,是轴承座的主要外部零件。
端盖的一般作用是:轴承外圈的轴向定位;轴承工作过程的防尘和密封(除本身可以防尘和密封外,也常和密封件配合以达到密封的作用);位于车床电动机和主轴箱之间的端盖,主要起传递扭矩和缓冲吸震的作用,使主轴箱的转动平稳。
因此该零件应具有足够的强度、刚度、耐磨性和韧性,以适应其的工作条件。
该零件的主要工作表面为左右端面以及左端面的外圆表面,在设计工艺规程时必须重点考虑。
端盖加工工艺的可行性与合理性直接影响零件的质量、生产成本、使用性能和寿命等。
2、端盖工艺性分析该端盖主要由平面、外圆面以及孔系组成,其结构简单、形状普通,属于一般的盘盖类零件。
端盖主要加工表面有左、右和凸台等三个端面,Φ47和Φ80两个外圆面,Φ34和Φ16两个内圆面,密封圈内槽以及六个均布的Φ7的通孔。
要求其Φ7孔的右端加工平面对于基准A的垂直度公差是0.03mm,端盖的Φ47外圆面与基准A的同轴度误差为0.03mm,其次就是均布的φ7孔的加工端面要求为平面,可以防止加工过程中钻头偏斜以保证孔的加工精度。
其中,端面和内外圆面均要求车削加工,可以采用半精车和粗车,并且粗、精加工应分开进行,以保证表面粗糙度要求;φ7通孔的加工采用钻铰来达到精度要求。
其余非配合表面加工精度较低,不需要高精度机床加工,通过粗车和半精车就可以在正常的生产条件下,采用较经济的方法加工出来;此外,该零件材料为铸铁HT200,切削加工性能较好。
综上所述,该端盖零件的工艺性能良好。
(1)工件的时效处理对于毛坯为铸件的盖类零件,因其各部位厚度不均匀,存在较大的铸造内应力,容易造成变形等缺陷,因此必须安排人工时效处理。
对于本端盖,其精度要求一般,则可利用粗、精加工工序间的自然停放和运输时间,得到自然时效处理的效果。
其自然时效处理的时间越长越好,否则会影响端盖配合精度的稳定性。
对于特别精密的端盖,在粗加工和精加工工序间还应安排一次人工时效,以消除铸造内应力,提高精度稳定性。
(2)加工工艺的顺序应先面后孔作为端盖上主要的两类加工表面——平面和孔,从定位稳定可靠的角度上分析,平面比孔要优越得多,同时还可以使孔的加工余量均匀;从加工难度上分析,平面比孔容易加工;从有利加工的进行上分析,采用先加工平面后加工分布在平面上的孔,由于铸件表面的凹凸不平和夹砂等缺陷已被切除,大大有利于孔加工的进行。
(3)加工阶段粗、精加工分开端盖为铸铁件,预留的加工余量较多,在粗加工中切削余量较大,夹紧力、切削力较大,且削热较多,因此对加工精度影响也较大;再加上粗加工是切削毛胚表面金属,工件内应力重新分布,也会引起工件变形。
因此,粗、精加工分为两个加工阶段,有利于把粗加工后,由于各种原因引起的工件变形充分暴露出来,在精加工阶段得以消除。
(4)工件的清洗同时,清洗这一步也十分重要。
清洗工作对保证机器装配质量、延长机器使用寿命均有重要意义,尤其是对精密配合件、密封件更为重要。
清洗的目的是除去零件表面上的油污及杂质。
常用的清洗液有煤油、汽油、碱液及化学清洗液等,清洗时可采用擦洗、浸洗、喷洗超声波清洗等方法。
3、端盖的技术要求端盖的各项技术要求如下表所示 加工表面 尺寸偏差(mm ) 公差及精度等级 表面粗糙度(μm)形位公差(mm)端盖左端面 12 IT9 3.2 端盖右端面 12IT9 3.2⊥ 0.03 A右端凸台端面 025.016-IT7 1.6 外圆面Φ80 Φ80 IT10 6.3 外圆面Φ47 Φ47 h6 IT7 1.6⊙ 0.03 A内圆面Φ34 Φ34IT10 6.3 内圆面Φ16 03.016-φIT9 3.2 M6通孔6×Φ7IT93.2该端盖主要实现轴承轴向定位的功能,必须满足端盖的位置度要求,即垂直度和同轴度的要求,因此加工精度要求较高;端盖在工作中需承受载荷,为增加其耐磨性,对端盖要求时效处理。
二、零件毛胚的选择1、确定毛坯种类由于该端盖在工作过程中要承受冲击载荷,为增强强度和冲击韧度,获得纤维组织,毛坯选用铸件。
材料采用灰铸铁HT200,它是有容易变形、吸振性好、耐磨性强及切削性好等优点。
该端盖的轮廓尺寸不大,生产类型为中批产量,为提高生产率和铸件精度,减少加工余量,宜采用金属模机器造型方法铸造毛坯,毛坯拔模斜度为5°。
此外为消除残余应力还应安排人工时效。
2、确定毛坯的尺寸公差:(1)铸件公差等级:由端盖的功能和技术要求,确定该铸件毛坯的尺寸公差等级为CT-10。
(2)铸件材质系数:确定端盖的材料为HT200。
(3)锻件分模线形状:根据该端盖的形位特点,选择零件方向的对称平面为分模面,属于平直分模线。
(4)零件表面粗糙度:该端盖的各加工表面粗糙度如零件图所示。
3、确定加工余量该零件各表面的加工余量是由各个表面的粗糙度、加工方法以及加工等级来确定的。
(1)左端面加工余量的确定工序名称 工序加工余量/mm 工序尺寸/mm 表面粗糙度/µm 总余量/mm 半精车 0.6 12 3.2 2.1粗车 1.5 12.6 6.3 毛坯14.1(2)右端凸台端面加工余量的确定工序名称 工序加工余量/mm 工序尺寸/mm 表面粗糙度/µm 总余量/mm精车 0.4 16 1.6 2.6半精车 0.7 16.4 3.2 粗车 1.5 17.1 6.3 毛坯18.6(3)右端面加工余量的确定工序名称 工序加工余量/mm 工序尺寸/mm 表面粗糙度/µm 总余量/mm 半精车 0.6 14.1 3.2 2.1粗车 1.5 14.7 6.3 毛坯16.2(4)Φ80外圆面加工余量的确定工序名称 工序加工余量(单面)/mm 工序尺寸/mm 表面粗糙度/µm 总余量/mm 粗车 1.5 80 6.3 3毛坯83(5)Φ47外圆面加工余量的确定工序名称 工序加工余量(单面)/mm 工序尺寸/mm 表面粗糙度/µm 总余量/mm 精车 0.4 47 1.6 5.2半精车 0.7 47.8 3.2 粗车 1.5 49.2 6.3 毛坯52.2(6)Φ16内圆面加工余量的确定工序名称 工序加工余量(单面)/mm 工序尺寸/mm 表面粗糙度/µm 总余量/mm 半精车 0.7 16 3.2 4.4粗车 1.5 14.6 6.3 毛坯11.6(7)Φ34内圆面加工余量的确定工序名称 工序加工余量(单面)/mm 工序尺寸/mm 表面粗糙度/µm 总余量/mm 粗车 1.5 34 6.3 3毛坯31(8)6×Φ7均布通孔加工余量的确定工序名称 工序加工余量/mm 工序尺寸/mm 表面粗糙度/µm 总余量/mm 扩 1.8 7 6.3 7钻 5.2 5.2 12.5 毛坯4、毛坯零件图三、制定工艺路线1、定位基准的选择(1)粗基准的选择作为粗基准的表面应平整,没有飞边、毛刺或其他表面欠缺。
这里选择端盖左端面和φ80外圆面作为粗基准。
采用φ80外圆面定位加工内孔可保证孔的壁厚均匀;采用端盖右端面作为粗基准加工左端面,可以为后续工序准备好精基准。
(2)精基准的选择根据该端盖零件的技术要求,选择端盖右端面和φ47孔作为精基准,零件上的很多表面都可以采用它们作基准进行加工,即遵循“基准统一”原则。
Φ16孔的轴线是设计基准,选用其作精基准定位端盖两端面,实现了设计基准和工艺基准的重合,保证了被加工表面的端面垂直度和同轴度要求。
选用端盖右端面作为精基准同样是遵循了“基准重合”原则,因为该端盖在轴向方向上的尺寸多以该端面作设计基准。
2、工序顺序的安排1)机械加工工序(1)遵循“基准先行”原则,首先加工精基准——端盖右端面和φ16中心孔。
(2)遵循“先粗后精”原则,先安排粗加工工序,后安排精加工工序。
(3)遵循“先面后孔”原则,先加工端盖右端面,再加工φ16中心孔。
2)热处理工序铸造成型后,对铸件进行退火处理,可消除铸造后产生的铸造应力,提高材料的综合力学性能。
该端盖在工作过程中不承受冲击载荷,也没有各种应力,为了工件达到要求的硬度使用调质处理HBS220-240。
3)辅助工序在精加工后,安排去毛刺、清洗和终检工序。
综上所述,该端盖工序的安排顺序为:粗加工——基准加工——热处理——精加工——检验。
3、确定加工的设备、刀具、和夹具在加工的时候要跟据零件的形状和特点,合理选用各种装夹工具。
还要根据加工部位的吃刀量来确定每个工序应选用的刀具,并适当调整刀具角度。
该零件毛坯的外形规则,在加工左右端面、右端凸台端面和内、外圆面以及凸台上的2×0.5退刀槽时,在车床上可以用三爪卡盘夹紧;在加工孔系时采用“一定位销,一防转挡销和两可转动压板自制夹具”来定位夹紧。
4、工序的集中与分散选用工序集中原则安排端盖的加工工序。
该端盖的生产类型为大批生产,可以采用万能型机床配以专用工、夹具,以提高生产率;而且运用工序集中原则使工件的装夹次数少,不但可缩短辅助时间,而且由于在一次装夹中加工了许多表面,有利于保证各加工表面的相对位置精度要求。
5、拟定工艺路线1)各表面加工方法的选择:加工表面公差及精度等级表面粗糙度(μm) 加工方案端盖左端面IT9 3.2 粗车——半精车端盖右端面IT9 3.2 粗车——半精车右端凸台端面IT7 1.6 粗车——半精车——精车外圆面Φ80 IT10 6.3 粗车外圆面Φ47 IT7 1.6 粗车——半精车——精车内圆面Φ34 IT10 6.3 粗车内圆面Φ16 IT9 3.2 粗车——半精车M6通孔IT9 3.2 钻——扩2)确定工艺路线:工序号工序名称加工表面加工方案技术要求机床设备刀具夹具1 铸造金属模机器造型,HT200 CT-102 清理清除浇冒口、型砂、分边、毛刺等3 热处理人工时效4 粗车退刀槽Φ47外圆面、Φ34内圆面粗车Ra12.5 车床CA6140 切槽刀三爪自定心卡盘5 粗车1×45°倒角粗车车床CA6140 端面车刀三爪自定心卡盘6 车端面右端面粗车、半精车Ra3.2 车床CA6140 端面车刀三爪自定心卡盘右端凸台端面粗车、半精车、精车Ra1.67 车内、外圆Φ47外圆面粗车、半精车、精车Ra1.6 车床CA6140 内圆车刀三爪自定心卡盘Φ34内圆面粗车Ra6.3 外圆车刀Φ16轴孔粗车、半精车Ra3.2 内圆车刀8 车内槽Φ28内槽粗车Ra12.5 车床CA6140 内切槽刀三爪自定心卡盘9 车端面左端面粗车、半精车Ra3.2 车床CA6140 端面车刀三爪自定心卡盘10 车外圆Φ80外圆面粗车Ra6.3 车床CA6140 内圆车刀三爪自定心卡盘11 钻——扩6×φ7孔右端面钻、扩Ra6.3 钻床麻花钻、扩孔钻三爪自定心卡盘12 去毛刺钳工台平挫13 清洗清洗机三爪自定心卡盘14 终检四、切削用量的选择及工序时间计算:工序09 钻、扩6×Φ7均布通孔,以Φ80外圆和Φ16轴线为基准,通孔的精度达到IT9。