(整理)内浮顶储罐施工方案
内浮顶罐施工方案

内浮顶罐施工方案内浮顶罐是一种常用于储存液体的容器,其内浮顶设计可以有效减少液体与空气之间的接触,从而减少蒸发和氧化的可能性。
内浮顶罐施工是一个非常重要的环节,直接影响到罐体的使用效果和安全性。
下面将介绍内浮顶罐的施工方案。
1. 施工前准备工作在进行内浮顶罐的施工前,需要完成以下准备工作:•确定罐体的设计图纸和规格要求;•准备施工所需的材料和工具,包括焊接设备、起重机械等;•对施工现场进行安全检查,确保施工环境符合要求。
2. 罐体组装首先,需要进行罐体的组装工作。
根据设计图纸,将罐体的各个部件进行组装,在组装过程中要确保各部件的连接牢固。
组装完成后,进行外观检查和质量检验,确保罐体符合要求。
3. 焊接工作完成罐体组装后,需要进行焊接工作。
在进行焊接前,首先要对焊接工艺进行检查和确认,选择适合的焊接方法。
然后进行焊接操作,确保焊接接头牢固,焊缝平整。
4. 漏检和压力测试在罐体焊接完成后,需要进行漏检和压力测试。
漏检是为了检查焊接接头是否存在漏洞,需要使用相应的检测设备进行检查。
压力测试是为了检查罐体是否能够承受设计压力,确保罐体安全可靠。
5. 内浮顶安装最后,进行内浮顶的安装工作。
根据设计要求,安装内浮顶及相关设备,需要确保内浮顶安装牢固,能够灵活运作。
安装完成后,进行功能测试,确保内浮顶正常运转。
结语内浮顶罐施工是一个复杂的工程,需要严格按照设计要求和工艺流程来进行。
只有做好施工准备工作,认真进行各项施工工作,才能确保内浮顶罐的质量和安全性。
希望以上介绍的施工方案能够对相关从业人员提供帮助。
大型储罐内浮盘安装施工方案
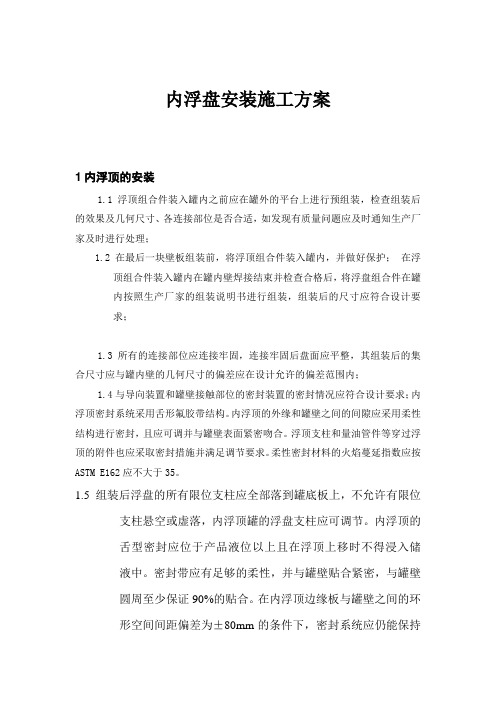
内浮盘安装施工方案1内浮顶的安装1.1 浮顶组合件装入罐内之前应在罐外的平台上进行预组装,检查组装后的效果及几何尺寸、各连接部位是否合适,如发现有质量问题应及时通知生产厂家及时进行处理;1.2 在最后一块壁板组装前,将浮顶组合件装入罐内,并做好保护;在浮顶组合件装入罐内在罐内壁焊接结束并检查合格后,将浮盘组合件在罐内按照生产厂家的组装说明书进行组装,组装后的尺寸应符合设计要求;1.3 所有的连接部位应连接牢固,连接牢固后盘面应平整,其组装后的集合尺寸应与罐内壁的几何尺寸的偏差应在设计允许的偏差范围内;1.4与导向装置和罐壁接触部位的密封装置的密封情况应符合设计要求;内浮顶密封系统采用舌形氟胶带结构。
内浮顶的外缘和罐壁之间的间隙应采用柔性结构进行密封,且应可调并与罐壁表面紧密吻合。
浮顶支柱和量油管件等穿过浮顶的附件也应采取密封措施并满足调节要求。
柔性密封材料的火焰蔓延指数应按ASTM E162应不大于35。
1.5 组装后浮盘的所有限位支柱应全部落到罐底板上,不允许有限位支柱悬空或虚落,内浮顶罐的浮盘支柱应可调节。
内浮顶的舌型密封应位于产品液位以上且在浮顶上移时不得浸入储液中。
密封带应有足够的柔性,并与罐壁贴合紧密,与罐壁圆周至少保证90%的贴合。
在内浮顶边缘板与罐壁之间的环形空间间距偏差为±80mm的条件下,密封系统应仍能保持良好的密封效果。
密封与罐壁件的局部最大允许间隙是6mm。
2附件预制组装2.1抗风圈、加强圈、包边角钢等弧形构件加工成型后,用弧形样板检查,其间隙不得大于2mm。
放在平台上检查,其翘曲变形不得超过构件长度的0.1%,且不得大于4mm。
2.2 热煨成型的构件,不得有过烧、变质现象。
其厚度减薄量不应超过1mm。
2.3罐体的开孔接管,应符合下列要求:2.3.1、开孔接管的中心位置偏差,不得大于10mm;按管外伸长度的允许偏差应为±5mm。
2.3.2、开孔补强板的曲率,应与罐体曲率一致;2.3.3、开孔接管法兰的密封面应平整,不得有焊瘤和划痕,法兰的密封面应与接管的轴线垂直,倾斜不应大于法兰外径的1%,且不得大于3mm,法兰的螺栓孔,应跨中安装。
浮顶罐施工方案

浮顶罐施工方案浮顶罐是一种常用的贮存液体的设备,适用于各种液体贮存。
下面是关于浮顶罐施工方案的介绍。
1. 施工前准备工作:- 选址:根据贮存液体的特性和规模确定浮顶罐的选址位置。
- 土建施工:进行地基平整和混凝土浇筑等土建工作,确保基础稳定。
- 材料准备:准备好浮顶罐所需的材料,包括钢板、焊接材料等。
- 设备准备:准备好施工所需的起重设备、焊接机器等。
2. 浮顶罐施工步骤:- 焊接罐体:将预制的钢板进行焊接,组装成罐体形状。
要注意焊接工艺的合理选择,确保焊接质量。
- 安装浮顶结构:将浮顶罐的浮顶结构安装在罐体上,包括浮顶、桥架、悬臂杆等。
要确保浮顶可以平稳地浮动,并且能够承受所贮存液体的重量。
- 防腐处理:对罐体进行防腐处理,以提高浮顶罐的使用寿命。
- 安装附件:安装浮顶罐的附件,包括液位计、进出口管道等。
- 进行试运行:进行浮顶罐的试运行,检查其运行状态和功能是否正常。
3. 施工注意事项:- 施工环境保护:施工现场要做好环境保护工作,控制噪音、粉尘等污染物的排放。
- 安全防护:施工人员需佩戴好安全防护用具,确保工作安全。
- 质量控制:施工过程中要进行质量控制,确保焊接质量和防腐效果。
- 施工进度控制:进行合理的施工进度控制,保证工期的顺利进行。
总结:浮顶罐的施工方案涉及到选址、土建施工、材料准备、设备准备等多个方面。
在施工过程中需要注意施工环境保护、安全防护、质量控制和施工进度控制等问题。
通过科学合理的施工方案,可以确保浮顶罐的质量和使用寿命,提高贮存液体的安全性和可靠性。
内浮顶储罐施工方案

(六)储罐施工方案1.工程概况中油福州油品码头及库区新建工程共有成品油储罐7具,消防水罐2具,其中柴油罐为3具5000立方米拱顶罐,汽油罐为2具3000立方米和2具5000立方米内浮顶罐,消防水罐为2具1000立方米拱顶罐。
该工程7具罐与预留的一具罐组成了较为紧凑的成品油罐区,便于集中流水施工。
消防水罐则分布于成品油罐区外部。
2.编制依据由中国石油天然气华东勘察设计研究院设计的施工图:2003设-401、1000m拱顶储罐32003设-407、3000m内浮顶储罐32003设-403、5000m内浮顶储罐32003设-405、5000m拱顶储罐3GB128-90《立式圆筒形钢制焊接储罐施工及验收规范》。
SH3530-93《石油化工立式圆筒形钢制储罐施工工艺标准》。
SH3528-93《石油化工钢储罐地基与基础施工及验收规范》。
SHJ22-90《石油化工企业设备与管道涂料防腐蚀设计与施工规范》。
JB4730-94《无损检测》。
据数计设罐储3.)T-301-01~Q235-A21300215.848172T-301-03~2Q235-A500419.817.863T-301-05~3Q235-A500罐719.817.8642Q235-A100罐2-1/11.513.18)4.罐体数据(1)1000立方米拱顶罐罐体数据一览表:(单具总重28850Kg)K量3933Q235-A6000 ××7罐1壁板板1钢2000 )一(16855罐2壁板2000×板钢56Q235-A×6000)二(168 1 3 =6 顶心板板钢δQ235-A 中46404 皮瓜板板钢16 δQ235-A=6Q235-A.F ×75×钢9 角758 326 钢边5 包角Q235-A 10 δ板9 钢=5 板6 垫6800Q235-A=7δ板钢1板底75.施工方法5.1施工方法采用群桅起升倒装法:5.2施工用料:每个罐所需倒链和桅杆如下表所示:3 5000mφ325×8,L=4000mm,22个3 1000m10T 8个倒手动3 3000m10T 16个链3 5000m10T 22个材5.3料验收合当量无质证合质,料选罐储所用的材和附件应具有量格明书进附料材和件行复验。
固定顶、内浮顶储罐施工工艺流程
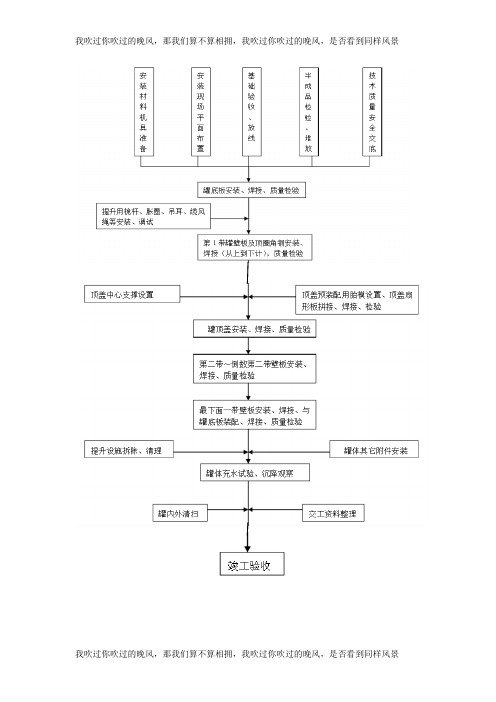
2、不锈钢拱顶罐组焊作业施工工艺流程图
施工准备根底验收中幅板施焊
材料检验存放底板预制
包边角钢组对第一带板组焊
均布立柱或液压提升装置安装撤除中心柱提升各带板
附件安装底板真空试验底板与罐壁组对底圈壁板组对
龟甲缝焊接龟甲缝试漏无损检测
罐体几何尺寸检查梯子平台安装总体验收
封闭人孔总体验收清罐
3、内浮顶储罐施工工艺:
材料验收→放样下料→预制→根底验收→底板组焊及试验检验→最顶层带板
组焊→拱顶组焊→倒数第二层带板组焊→钢结构、梯子平台及附件施工→罐体试验→内浮顶安装→罐体防腐→竣工验收
4、罐室及罐根底施工
施工准备→定位放线→土方开挖〔爆破〕→验槽→砼垫层→罐室环墙根底施工→罐室墙体施工→罐顶簿壳顶板施工→罐室内、外墙抹灰→罐室外墙防水→罐室外侧土方回填→罐室脚手架撤除→钢罐基环梁施工→回填砂沥青砂垫层→根底验收→罐体安装。
储罐组装施工措施方案(内浮顶液压顶升)-通用模版

储罐组装施工措施(适用于内浮顶罐、液压顶升倒装施工)2.1 储罐新建工程量简介新建10000m3拱顶罐2座,储存介质为柴油,钢板厚度有6mm、8mm、10mm、12mm 和14mm五种,材质有Q235-B和16MnR两种,包边角钢为∟125×10,共9圈壁板。
罐体内直径为30m,总高度为19.341m,总重量为222.83t。
2.2 施工工艺流程本工程10000m3拱顶罐拟采用液压顶升倒装工艺法,施工工序如下:2.3 10000m3罐施工措施2.3.1 原材料检验⑴原材料检验:板材及型钢符合设计要求,•人孔、透光孔、通气孔、清扫孔等外购件出厂合格资料齐全。
⑵制造储罐所用的钢板必须逐张进行外观检查,其表面质量应符合GB6654-1996《压力容器用钢板》的规定。
对钢板表面的锈蚀减薄量、划痕深度与钢板实际负偏差之和,当钢板厚度为6~7mm时,允许偏差为-0.6mm;当钢板厚度为8~25mm时,允许偏差为-0.8mm。
⑶所有工程用钢材、半成品、配件、焊材均应按规格、材质分别堆放,下部垫平填实,防止变形损坏,并做好明显标记。
⑷经检验合格的材料,应设专人管理,按限额领料单发放。
对不合格的材料,严禁在工程中使用。
2.3.2 储罐的预制⑴一般规定:① 储罐在预制、组装及检验过程中所使用的样板应符合下列规定:a . 当构件的曲率半径小于或等于12.5m 时,弧形样板的弦长不得小于1.5m ;当曲率半径大于12.5m 时,弧形样板的弦长不得小于2m 。
b . 直线样板的长度不得小于1m 。
c . 测量焊缝角变形的弧形样板,其弦长不得小于1m 。
② 钢板的切割和焊缝的坡口,宜采用机械加工或自动、半自动火焰切割加工;罐顶板和罐底板边缘板的园弧边缘,可采用手工火焰切割加工。
③ 钢板边缘加工面应平滑,不得有夹渣、分层、裂纹及熔渣等缺陷。
火焰切割坡口产生的表面硬化层应磨除。
④ 所有预制构件在保管、运输及现场堆放时,应采取有效措施防止变形、损伤和锈蚀。
储罐组装施工措施方案内浮顶液压顶升-通用模版
储罐组装施工措施(适用于内浮顶罐、液压顶升倒装施工)2.1储罐新建工程量简介新建10000m3拱顶罐2座,储存介质为柴油,钢板厚度有6mm、8mm、10mm、12mm 和14mm五种,材质有Q235-B和16MnR两种,包边角钢为L125X10,共9圈壁板。
罐体内直径为30m,总高度为19.341m,总重量为222.83t。
2.2施工工艺流程本工程10000m3拱顶罐拟采用液压顶升倒装工艺法,施工工序如下:2.310000m3罐施工措施2.3.1原材料检验⑴原材料检验:板材及型钢符合设计要求,-人孔、透光孔、通气孔、清扫孔等外购件出厂合格资料齐全。
⑵ 制造储罐所用的钢板必须逐张进行外观检查,其表面质量应符合GB6654-1996《压力容器用钢板》的规定。
对钢板表面的锈蚀减薄量、划痕深度与钢板实际负偏差之和,当钢板厚度为6〜7mm时,允许偏差为一0.6mm;当钢板厚度为8〜25mm时,允许偏差为一0.8mm。
⑶所有工程用钢材、半成品、配件、焊材均应按规格、材质分别堆放,下部垫平填实,防止变形损坏,并做好明显标记。
⑷ 经检验合格的材料,应设专人管理,按限额领料单发放。
对不合格的材料,严禁在工程中使用。
2.3.2储罐的预制⑴一般规定:① 储罐在预制、组装及检验过程中所使用的样板应符合下列规定:a.当构件的曲率半径小于或等于12.5m时,弧形样板的弦长不得小于1.5m;当曲率半径大于12.5m时,弧形样板的弦长不得小于2m。
b.直线样板的长度不得小于1m。
c.测量焊缝角变形的弧形样板,其弦长不得小于1m。
②钢板的切割和焊缝的坡口,宜采用机械加工或自动、半自动火焰切割加工;罐顶板和罐底板边缘板的园弧边缘,可采用手工火焰切割加工。
③钢板边缘加工面应平滑,不得有夹渣、分层、裂纹及熔渣等缺陷。
火焰切割坡口产生的表面硬化层应磨除。
④所有预制构件在保管、运输及现场堆放时,应采取有效措施防止变形、损伤和锈蚀。
⑵底板的预制:① 绘制底板排板图,根据设计图纸,板材尺寸及标准要求绘制排板图,为补偿焊接收缩,罐底的的排板直径应比设计图样尺寸大0.1〜0.2%。
浮仓内浮顶贮罐施工方案
浮仓内浮顶贮罐施工方案一、前言浮仓(浮式屋顶)内浮顶贮罐是一种常见的储罐形式,广泛应用于石油、化工、食品、饮料等行业。
本文将详细介绍浮仓内浮顶贮罐的施工方案。
二、施工准备工作1.施工组织设计:根据具体施工情况,制定施工组织设计方案,明确负责人和施工人员的职责。
2.打样审批:根据设计图纸和规范要求,制作浮式屋顶和浮顶,进行样板审批。
3.施工图纸和材料准备:根据设计要求,制定施工图纸,并准备好所需材料,如钢材、焊材、涂料等。
4.原材料检验:对所购买的原材料进行检验,确保其质量符合要求。
5.施工设备准备:准备好所需施工设备和机具,如起重机、电动焊机、气瓶等。
6.现场布置:对施工现场进行布置,划定区域,确保施工安全和顺利进行。
三、施工步骤1.钢结构制作:根据设计图纸,制作浮式屋顶的钢结构。
包括制作顶拱构件、校正并焊接顶拱,制作安装导轨等。
2.钢结构安装:将制作好的钢结构进行现场安装,按照设计要求进行组装,并进行调整和校正,确保各构件的精度和平整度。
3.焊接工艺:根据焊接工艺规程,进行钢结构的焊接。
确保焊缝的质量和可靠性。
4.涂装防腐:对已焊接好的钢结构进行涂装和防腐处理,保护其免受腐蚀和氧化。
选用耐酸碱的涂料,确保涂装层的质量。
5.安装浮顶:将制作好的浮顶安装在钢结构之上,并进行调整和校正,确保浮顶与钢结构的接触紧密、平整度良好。
6.导轨安装:安装导轨,确保浮顶的顺畅移动。
7.测量调整:对浮顶进行测量和调整,确保其水平度和平整度满足要求。
8.清洁挂钩:安装清洁挂钩,方便后续清洁维护工作。
9.试运行:对浮仓内浮顶贮罐进行试运行,检查其运行是否正常。
四、安全措施1.施工现场设置警示标志,划定施工区域,保持施工现场的秩序和安全。
2.使用符合规范要求的施工设备和机具,严格按照操作规程进行施工。
3.对施工人员进行安全培训和技术指导,确保其具备相关的安全知识和操作技能。
4.施工期间,严禁酒后上岗和疲劳驾驶,确保施工人员的身体健康和精力充沛。
内浮顶储罐施工方案
上海孚宝港务有限公司储罐区及码头上部设施工程内浮顶储罐施工方案中国化学工程第六建设公司二○○三年四月十七日目录1 编制说明2 编制依据3 施工方法及技术措施3.1 施工程序3.2 预制加工3.3 组装焊接3.4 罐体检验及试验3.5 罐体防腐施工4 劳动力计划5 工机具使用计划6 施工手段用料计划7 质量控制措施8 安全及文明施工1 编制说明上海孚宝港务有限公司储罐区共有内浮顶罐13台,其最大容积为5600m3。
罐体为普通C·S钢板材料,单台最大重量193.6吨,全部采用现场制造,各浮顶罐特性见下表。
2 编制依据2.1 上海孚宝港务有限公司包储顶目初步设计;2.2 《立式圆筒形钢制焊接油罐施工及验收规范》GBJ128-902.3 《现场设备、工业管道焊接工程施工及验收规范》GB50236-982.4 《石油化工立式圆筒形钢制焊接油罐设计规范》SH3064-923 施工方法及技术措施罐体制作采用倒装法施工,即采用先底、顶,后罐壁的方法,具体施工过程和控制措施如下:3.1 施工程序材料验收→放样下料→预制→基础验收→底板组焊及试验检验→最顶层带板组焊→拱顶组焊→倒数第二层带板组焊→钢结构、梯子平台及附件施工→罐体试验→内浮顶安装→罐体防腐→竣工验收。
3.2 基础验收3.2.1 基础表面尺寸要求见表3-1。
3.2.2 以基础中心为圆心,以不同直径作同心圆,将各圆周分成若干等分,在等分点测量基础表面的标高,同一圆周上的测点,其测量标高与计算标高之差不得大于12mm;检查基础表面凹凸度的同心圆直径及测量点数,见表3-2。
基础表面尺寸允许偏差表3-1基础表面凹凸度的同心圆直径及测量点数3.3.1 罐顶板预制3.3.1.1 罐顶下料依据施工图下料,采用氧乙炔焰半自动切割机切割。
罐顶弧形板采用胎具压制加工成形,现场拼装。
因为该板压制后有一定的反弹,该胎具的半径应比拱顶板的弧形半径小20mm。
3.3.1.2 罐顶弧形板每隔1米的距离加压一次,成型后的拱顶板必须用长L=2m的弧形样板检查,不合格的部位需重新压制。
浮顶储罐施工方案
浮顶储罐施工方案一、工程概况与目标本施工方案针对浮顶储罐的建设过程,涵盖了从施工准备到工程验收与交付的全部流程。
本工程旨在安全、高效地建设一座质量稳定、功能完备的浮顶储罐,以满足使用方的存储需求。
二、施工准备工作人员配置:组建专业的施工团队,包括项目经理、技术负责人、安全员、质检员等关键岗位。
材料采购:根据设计要求,采购合格的材料和构配件,并确保其质量和数量满足施工需求。
设备准备:准备必要的施工机械和设备,如挖掘机、吊车、焊接设备等。
现场勘查:对施工现场进行详细勘查,了解地形、地质、气象等条件,为施工提供基础数据。
三、基础施工与验收基础施工:按照设计要求进行基础施工,确保基础平整、稳固。
基础验收:基础施工完成后,进行基础验收,确保基础质量符合设计要求。
四、浮顶储罐安装罐体安装:按照设计图纸和工艺要求,进行罐体的安装工作。
浮顶安装:罐体安装完成后,进行浮顶的安装工作,确保浮顶与罐体连接紧密、密封良好。
五、防腐与保温处理防腐处理:对罐体进行防腐处理,以防止罐体受到腐蚀影响。
保温处理:根据使用需求,对罐体进行保温处理,以减少能源浪费。
六、安全与环保措施安全管理:制定详细的安全管理制度和操作规程,确保施工过程安全可控。
环保措施:采取有效的环保措施,减少施工对环境的影响。
七、质量控制与检验质量控制:建立严格的质量管理体系,确保施工质量符合设计要求。
检验与测试:对施工过程进行全程检验与测试,确保工程质量符合要求。
八、工程验收与交付工程验收:工程完成后,进行全面的工程验收,确保工程质量和使用功能符合设计要求。
交付与使用:工程验收合格后,进行交付使用,并提供必要的技术支持和售后服务。
本施工方案旨在确保浮顶储罐建设过程的安全、高效和质量稳定。
我们将严格按照施工方案进行操作,确保工程顺利完成,并满足使用方的需求。
- 1、下载文档前请自行甄别文档内容的完整性,平台不提供额外的编辑、内容补充、找答案等附加服务。
- 2、"仅部分预览"的文档,不可在线预览部分如存在完整性等问题,可反馈申请退款(可完整预览的文档不适用该条件!)。
- 3、如文档侵犯您的权益,请联系客服反馈,我们会尽快为您处理(人工客服工作时间:9:00-18:30)。
(六)储罐施工方案1.工程概况中油福州油品码头及库区新建工程共有成品油储罐7具,消防水罐2具,其中柴油罐为3具5000立方米拱顶罐,汽油罐为2具3000立方米和2具5000立方米内浮顶罐,消防水罐为2具1000立方米拱顶罐。
该工程7具罐与预留的一具罐组成了较为紧凑的成品油罐区,便于集中流水施工。
消防水罐则分布于成品油罐区外部。
2.编制依据由中国石油天然气华东勘察设计研究院设计的施工图:2003设-401、1000m3拱顶储罐2003设-407、3000m3内浮顶储罐2003设-403、5000m3内浮顶储罐2003设-405、5000m3拱顶储罐GB128-90《立式圆筒形钢制焊接储罐施工及验收规范》。
SH3530-93《石油化工立式圆筒形钢制储罐施工工艺标准》。
SH3528-93《石油化工钢储罐地基与基础施工及验收规范》。
SHJ22-90《石油化工企业设备与管道涂料防腐蚀设计与施工规范》。
JB4730-94《无损检测》。
3.储罐设计数据4.罐体数据(1)1000立方米拱顶罐罐体数据一览表:(单具总重28850Kg)(2)3000立方米内浮顶罐罐体数据一览表:(单具总重76797Kg)(3)5000立方米拱顶罐、内浮顶罐罐体数据一览表:(单具总重119731Kg)5.施工方法5.1施工方法采用群桅起升倒装法:5.2施工用料:每个罐所需倒链和桅杆如下表所示:5.3材料验收储罐所选用的材料和附件,应具有质量合格证明书当无质量合格证明书或质量合格说明书有疑问时,应对材料和附件进行复验。
储罐焊条选用J422、J427电焊条,焊条应具有质量合格说明书。
储罐所选用的钢板,必须逐张进行外观检查,其表面质量应符合现行的相应钢板标准的规定。
钢板表面锈蚀减薄量,划痕深度与钢板实际偏差之和,应符合下表规定。
5.4预制5.4.1罐底预制(1)罐底板预制前应根据实际来料绘制排版图。
并根据图纸放大样,检查无误后方可下料。
(2)罐底的排版直径,宜按设计直径放大0.1-0.2%。
(3)弓形边缘板沿罐底半径方向的最小尺寸,•不得小于700mm。
(4)弓形边缘板的对接接头,宜采用不等间隙,•外侧间隙e1宜为6-7mm,内侧间隙e2宜为8-12mm。
(5)中幅板的宽度不得小于1000mm•,•长度不得小于2000mm。
(6)底板任意相邻焊缝之间的距离,不得小于200mm。
(7)中幅板依图纸采用搭接形式,下料时依据图纸要求适量放大搭接量后进行下料。
(8)罐底板预制完毕后,与基础接触的一面应彻底除锈后涂刷沥青防腐漆,边缘50mm不刷。
5.4.2罐顶预制(1)根据来料实际尺寸,合理排料,进行罐顶板拼接。
(2)加强肋板接长,用对接接头,应加垫板,•且必须完全焊透。
(3)罐顶板与加强助组焊时,•应将罐顶板放置在罐顶板胎具上,画出加强肋板的位置,进行罐顶板,加强肋板的组对,焊接。
(4)罐顶板在焊接径向加强肋板时,一半罐顶板上焊接双道径向加强肋,另外一半不焊接径向加强肋板,安装时,焊接径向加强肋板的一半,沿圆周均布固定,再将不焊接径向加强肋板的一半搭接于前一半上即可。
(5)罐顶板预制完毕后,分别放置于罐顶板胎具上。
(6)顶板下料时,•其径向切割线为一条近似直线的弧线,下料时每角边加宽25mm-50mm后,按直线下料即可,这样可弥补安装时罐顶板中央部分搭接量不足的问题。
5.4.3壁板预制(1)壁板预制前根据实际来料情况应绘制排版图,并应符合下列规定。
(2)各圈壁板的纵向焊缝宜向同一方向逐圈错开,其间距宜为板长的1/3,且不得小于500mm。
(3)底圈壁板的纵向焊缝与罐底边缘板对接缝之间的距离,不得小于200mm。
(4)罐壁开孔接管或开孔接管补强板边缘与罐壁纵向焊缝之间的距离,不得小于200mm,•与环向焊缝之间的距离不得小于100mm。
(5)罐壁最上圈的加强圈的对接接头与壁板纵向焊缝之间的距离,不得小于200mm。
(6)该罐壁板宽度不得小于1000mm,•长度不得小于2000mm。
(7)壁板尺寸的允许偏差,应符合下表规定。
长2m的弧形样板检查,•其间隙不得大于4mm。
5.4.4其它零部件的预制(1)加强圈等弧形构件加工成型后,用弧形样板检查,其间隙不大于2mm,放在平台上检查,其翘曲变形不得超过物件长度的0.1%,且不得大于4mm。
(2)热煨成型的构件,不得有过烧,变形现象,其厚度减溥量不应超过1mm。
(3)部分胎具的预制,见下图。
(4)附件的预制要和上述部分同步。
5.5现场组装5.5.1罐底板组装(1)组装前必须有土建单位提供的基础验收合格通知单。
(2)在基础上放好纵、横十字轴线,边缘板圆周线及中幅板圆周线。
(3)从中心板开始铺设,以中心板为基准,按排版图的编号,在基准板上划好搭接线,向两侧按顺序铺设,以此类推,直至中幅板铺设完毕,再铺设边缘板。
(4)检查罐底板直径及搭接尺寸是否符合设计要求,确认无问题后,将底板临时点焊固定。
5.5.2底板焊接(1)焊接时,应先焊短缝,后焊长缝,•初层焊道应采用分段退焊或跳焊法,在焊接短缝时,宜将长缝的定位焊铲开,用定位板固定中幅板的长缝。
(2)焊接长缝时,由中心开始向两侧分段退焊,焊至距边缘板300mm,停止施焊。
(3)边缘板应先施焊靠外边缘300mm部位的焊缝,对接缝外端宜加引弧板,由罐内中心向外施焊,焊接时宜采用隔缝对称施焊法。
(4)在罐底与罐壁连接的角焊缝焊完后,•边缘板与中幅板之间的收缩缝施焊前,应完成剩余的边缘板对接焊缝的焊接。
(5)收缩缝的第一层焊接,•应采用分段退焊或跳焊法。
(6)罐帽组装(第一圈壁板、包边加强圈、罐顶板总称罐帽)(7)罐帽组装之前,•应将加热器、中心托架、胀圈等运至罐底适当位置放好。
5.5.3顶圈壁板组装焊接在罐底板上划出壁板安装圆周线,焊好内外圆定位板(每米三组),然后用吊车将板吊装至指定位置就位。
利用内外圆定位板将单块圈板下部固定好,圈板上部用无缝钢管(Φ57×5)做好临时支撑。
•全部顶圈壁板围拢后,圈板合围处应为搭接状态(称为封口板),调整好纵缝坡口及圈板上口水平度后,即可进行壁板纵缝焊接。
焊接时,先焊外侧,再进行焊缝内侧砂轮机打磨清根,再焊接焊缝内侧。
最后处理搭接外纵缝,在保证圈板周长准确,上下口周长一致的情况下,画出切割线进行切割。
处理好坡口,进行焊接。
5.5.4包边加强圈组装焊接在顶圈板上口下来500mm处安装胀圈,充分胀圆上口,在顶圈板上画出加强圈的安装线,将包边加强圈进行组对点焊。
全部安装完后,进行焊接。
先焊接对接口,必须开坡口焊接,然后焊接与壁板之间的搭接口。
之后画出罐顶板中心标记。
5.5.5罐顶板组对焊接在罐底中心位置搭设中心托架,上部的托架平面必须用水平尺找平。
并且将等分,画出标记,然后用吊车依次把顶板吊装就位。
吊装时,先将焊有双道径向加强助的一半就位,再吊装另外一半没有径向加强肋的顶板。
为了保证罐顶板弧度,可以用Φ57×5的钢管进行支撑调整。
组装完毕后,进行定位焊。
•然后先焊接内侧焊缝,后焊接外侧焊缝。
外侧径向的长缝,宜采用隔缝对称施焊方法,并由中心向外分段退焊。
罐顶焊接完毕后,即可进行罐顶附件安装。
同时,应对罐顶所有焊缝进行煤油渗透检测。
5.5.6罐壁的组装与焊接5.5.6.1罐壁的组装将第二圈(由上往下)壁板依排版图贴在顶圈壁板外侧,调整纵缝间隙,上口水平度,而后进行纵缝外侧的焊接。
最后一道纵缝应处于搭接状态,称为封口板。
该处用2个倒链上下锁紧,•将另一副胀圈安装至顶圈壁板下口500mm处,把下口胀圆。
•用桅杆倒链将罐帽提升,提升到位后,拉紧锁紧倒链,从离搭接口最远处开始,两组人同时调整环缝并进行点焊。
直至搭接口处,最后进行划线切割,打磨坡口,组对搭接口处的纵缝、环缝,同时检查环缝外上下圈板的周长第五圈下口的周长及整体的垂直度。
5.5.6.2罐壁的焊接先焊接所有纵缝,焊接完毕后,进行环缝焊接。
焊接时先焊外侧,焊工应均匀分布,•同步同向焊接。
外侧焊接完毕后,内侧进行清根打磨,然后均匀分布,同步同向焊接。
焊接完毕后,依照要求进行无损检测。
若发现缺陷超标及时返修,以免减少高空作业。
完全合格后,进行胀圈拆除,安装至第五圈下口上来500mm处,将下口胀圆。
同理进行第三圈、第四圈、第五圈、最后一圈的壁板的组对与焊接。
对于内浮顶储罐,内侧焊缝焊完后应将焊缝余高打磨至与母材齐平。
5.5.6.3罐底与罐壁的焊接罐底与罐壁连接的角焊缝焊接,应先焊内侧,后焊外侧。
焊接时应采用分段退焊法,焊工对称均布,沿同一方向施焊,焊脚高度依图纸要求,并为圆滑过渡。
5.5.6.4罐壁附件的安装根据图纸设计尺寸及开口方位图,进行各种接管的安装,开孔接管的中心位置偏差,不得大于10mm,接管外伸长度的允许偏差应为±5mm,开孔补强圈的曲率,•应与罐体曲率一致,开孔接管法兰的密封面应平整,不得有焊瘤和划痕,法兰的密封面应为接管的轴线垂直,倾斜不应大于法兰外径的1%,且不得大于3mm,法兰的螺栓孔,应跨中安装。
5.5.7内浮顶的组装焊接内浮顶的组装在罐底检查合格后进行。
内浮顶与底层罐壁同心。
内浮顶边缘侧板半径允许偏差为0-10mm。
内浮盘板直接在罐底上铺设,其组装焊接应参照罐底板有关规定执行,局部凹凸度不应大于变形长度的4/1000,且不大于80mm。
5.6检查及验收5.6.1焊缝的外观检查(1)焊缝的表面及热影响区,不得有裂纹、气孔、夹渣和弧坑等缺陷。
(2)焊缝的表面质量及检验方法,应符合下表规定。
注:δ-板厚,L-长度5.6.2焊缝无损检测5.6.2.1罐底板焊缝无损检测罐底板所有焊缝均应真空试漏,试验的负压值应大于等于53KPa•,未发现渗漏为合格,边缘板对接焊缝边缘300mm范围内,当δ<10mm时,每个焊工施焊的焊缝至少抽查一条,按《无损检测》JB4730-94Ⅲ级为合格。
当δ≥10mm时,每条对接缝都必须进行检测,按《无损检测》JB4730-94Ⅲ级为合格。
5.6.2罐壁焊缝无损检测(1)对于纵缝,每一焊工焊接的每种板厚,在最初焊接的3m焊缝的任意部位取300mm进行射线探伤,以后不考虑焊工人数,对每种板厚在每30m•焊缝及其尾数内的任意部位取300mm进行射线探伤。
探伤部位中的25•%应位于丁字焊缝处。
对于底圈壁板上的纵缝,当δ≤10mm时应从每条焊缝取300mm进行射线探伤,取的部位应尽量靠近底板。
当δ≥10mm时,每条纵缝上致少取2处300mm进行射线探伤,其中一张取的部位应靠近底板,同时,该圈壁板的丁字缝应做100%RT 探伤,依据JB4730-94Ⅲ级为合格。
(2)对于环向焊缝,每种板厚(以较薄板为准),在最初焊接的5m 焊缝内任意取300mm进行射线探伤。
•以后对于每种板厚,在每60m•焊缝及其尾数内的任意部位取300mm进行射线探伤,上述检查不考虑焊工人数。