8MN板框式模锻液压机本体设计
80MN双柱斜置式快锻液压机机架有限元分析

2太 原 重 型 机 械 集 团 有 限 公 司 技 术 中心 , . 山西 太 原 0 0 2 3 0 4)
摘 要 : 用 P oE 软 件 建 立 了 8 MN 双 柱 斜 置 式 快锻 液 压 机 机 架 的 三 维 全 接 触 实 体 模 型 , ANS 利 r/ 0 以 YS软 件 作 为 有 限 元 分 析 工 具 , 对 机 架 施 加 预 应 力 , 施 加 极 限工 作 载 荷 , 到 主 要 部 件 应 力 和 位 移 分 布 图 , 对 先 再 得 并
双 柱 斜 置 式 预 应 力 机 架 由上 横 梁 、立 柱 、 下 横 梁 、 杆 、 紧 螺 母 、 压 缸 组 成 。用 P oE软 件 建 立 拉 预 液 r/ 了 机 架 的 三 维 实 体 模 型 , 为 了简 化 模 型 ,减 少 计 算
缸 的 顶 部 和 下 横 梁 与 工 作 台接 触 的 面 上 。
机 架 各 部 件 之 问存 在 多 处 接 触 ,在 ANS YS
分 析 中 采 用 面 一面 接 触
压 机 的优化设 计 , 结 构合 理 , 构尺 寸轻 巧 。在我 其 机
国 , 于设计 方法 落后 , 内厂商难 以同发 达 国家在 由 国 激烈 的市场上 竞争 。 传 统 的锻造 压机 的主导 机型 一直是 三 梁 四柱式
横 梁 与 拉 杆 的 接 触 位 置 也 有 较 大 应 力 ,都 在 材 料 性
能 的允许范 围之 内 。 生 较大应 力 的原 因是 : 局部 产 ① 变 形 较 大 , 生 应 力 集 中 ; 由 于 模 型 较 大 , 元 划 产 ② 单
分 过 大 , 算 不 够 精 确 。施 加 极 限 工 作 载 荷 后 , 柱 计 立
800MN大型模锻液压机极限设计制造技术创新

800M N大型模锻液压机极限设计制造技术创新曾祥东,杨固川,张华,于江,胡孟君,陈文( 中国第二重型机械集团公司重型机械设计研究院,四川成都610052)摘要: 简述800 M N大型模锻液压机上巨大尺寸、重要零件的极限设计制造,特别是机架C形板、主工作缸、活动横梁中梁等的极限设计技术以及在铸造、锻造、焊接方面的极限制造技术。
设计过程中对C形板进行优化设计,使过渡圆角处的最大应力由原来的456M Pa降为237.1M Pa; 对主工作缸的局部进行设计优化,使进液孔内壁的最大主应力和等效应力分别降低到192和217M Pa,应力值降低幅度超过40%。
经过国家科技重大专项课题组联合技术攻关,成功解决了大尺寸重要零件极限设计制造关键技术的难题。
关键词: 模锻液压机; 极限设计; 极限制造D O I: 10.13330/j.iss n.1000-3940.2014.02.019中图分类号: TH163文献标识码: A文章编号: 1000-3940( 2014) 02-0096-06C r e a t io n of li m i t d esig n and manu f a c t u r i n g t ec hn i qu e fo rclose-d ie fo r gi n g h y d r au lic p r ess of 800 M NZ en g Xian g d o n g,Yan g Guchuan,Z han g Hua,Yu Jian g,Hu M en g jun,C hen Wen ( T he Hea vy M achiner y Desi g n andResearch Institute,China Nati o nal Er z h o n g Gr o up C o〃,Chen g du610052,China )A b s t r a c t: T he limit desi g n and manu f acturin g technique of imp o rtant parts w ith lar g e si z es in the800 M N cl o se-die fo r g in g h y draulic press w as described brie f l y,especiall y the limit desi g n techn o l ogy of the“C”shaped plate in f rame,the main c y linder and the c o unter beam of m ov in g cr o sshead,and the limit manu f acture of castin g,fo r g in g and w eldin g〃 T he ma x imum stress at the f illet radius of“C”shaped plate w as reduced f r o m456t o 237.1 M Pa thr o u g h the o ptimi z ati o n desi g n〃 T he ma x imum principal stress and the equi v alent stress of liquid in- let h o le in the main wo rkin g c y linder w ere reduced t o 192and217M Pa respecti v el y b y a l o cal o ptimi z ati o n desi g n,and the stresses w ere decreased b y m o re than40%〃 T hr o u g h j o int technical research of the nati o nal science and techn o l ogy maj o r special pr o ject g r o up,the ke y technical pr o blems of limit desi g n and manu f acture ab o ut imp o rtant parts w ith lar g e si z es w ere success f ull y res o l v ed〃K ey wo r d s: cl o se-die fo r g in g press; limit desi g n; limit manu f acture我国自主设计制造的、世界最大的800 M N ( 8 万吨) 大型模锻油压机,是国家科技重大专项课题,压机于2013年4月在中国二重投产。
液压机

主要焊接结构件的设计1、液压机的本体液压机的本体分为铸造结构、焊接结构以及铸焊混合结构。
近代由于焊接技术的进步,液压机本体采用焊接结构的已很普遍,焊接结构对单件小批量生产的企业非常合适。
焊接结构的优点是:制造工艺灵活、方便、结构重量轻、外形美观、制造成本低,铸造结构有其自身的特点,对某些使用工艺是很合适的,因此目前焊接结构还是不能完全代替铸造结构的。
液压机的主要焊接结构件是指上横梁(CROWN)、滑块(SLIDE)、底座(BED)、立柱(UPRIGHT)、移动工作台(MOVING BOLSTER)等。
这些焊接构件的结构设计不应是铸造结构模式的简单变化,不同用途,公称力大小不同,外形尺寸不同的液压机的焊接构件也不能简单地采用一种结构模式,整体焊接框架不能简单地按组合框架的模式简单的变形。
但任何一个具体的结构设计必须按实际的情况考虑问题,所以下面介绍的原则必须结合具体的设计创造性的灵活运用。
焊接结构设计的另一个重要问题是焊接接头的设计。
焊接构件中,甚么部位采用全焊透接头,甚么部位采用不焊透接头,甚么接头开坡口,甚么接头不开坡口,坡口应该是甚么型式和大小等。
因此研究液压机结构件的设计对提高设计水平、设计质量、降低成本是很有意义的。
本资料的目的是研究这些问题,提出一些设计原则或总结一些经验,用来指导设计。
2、关于焊接接头焊接接头必须保证连接部位的强度,接头的形式及大小必须适应当代焊接技术并满足施焊的要求。
现代工艺一般都采用气保焊,焊接接头与接头部位的受力状况,与板厚有关。
接头的设计应该是在满足受力的前提下尽量简单,尽量的小。
这样才能减少变形,降低成本。
理论上对T型接头的研究证明,三分之一钝边的坡口的焊接接头即和被焊板等强度,下面提出的C方式接头就是根据这个理论并参照日本小松株式会社压力机溶接基准制订的。
对接焊缝及要求受力处则要求采用下面提出的D方式接头。
一般联系筋板采用A方式接头的不开坡口的角焊缝。
焊接接头及其坡口型式见表一。
模锻液压机

•
三台齐造,10万吨级航空工业重 点装备总投资40亿元以上工程期 2008年2012年
• 2008年10月16日下午,与中国大飞机工程配套的巨型模锻液压机项目――苏州昆仑优秀制作 技巧设施有限公司正式定居江苏昆山周市镇。该公司将结合清华大学等机构,整合各方资源, 设计制作世界最大的10万吨巨型模锻液压机,这一项目将转变世界航天航空业巨型锻件出产 布局。据普查,一个通例的飞机项目可直接带领600家企业的进展,间接带领2500余家企业进 展。苏州昆仑公司施行的10万吨巨型模锻液压机,是大飞机项目成型制作起伏架等重点部件 的制作装备,将为周市镇打造优秀设施制作业产业基地,引进航空、航天工业产业链上的其 余企业奠基坚实根基。 眼前中国曾经动工上马的8万吨以上级模锻压机最少有3台,离别位于昆山、阎良、德阳, 可分离合作上海、西安、成都等地的航空航天产业。这标记中国设备制作业总体水准进一步 晋级,完成了中国锻造产品从高端产品向世界顶级产品的横亘,重点巨型锻件受制于外国的 时代完全完结,成为中国国民经济尤其是设施制作业和保全国度平安不可缺乏的主要战略设 施。 更令人轰动的是,清华大学曾经研发布16万吨模锻液压机,只因眼前我国制作业尚不必要如 此之大的模锻液压机,一旦国度必要,即可出图制作。16万吨是俄罗斯7.5万吨压机的2倍多, 是美国4.5万吨的3.5倍多。惊人的数字,中国必将成为世界锻压业新的霸主。 黑龙江省齐齐哈尔市中国第一重型机械集体于2006岁尾修建出15000级自由锻造液压机。
新中国前期建成的九套巨型成套 设施
• 新中国前期建成的九套巨型成套设施为我国冶金工业作出了 主要奉献,这九套巨型成套设施是:1973年投产的30000吨模锻水 压机,1971年投产的12500吨有色金属卧式挤压水压机,1972年投 产的辊宽2800毫米热轧铝板轧机和辊宽2800毫米冷轧铝板轧 机,1971年投产直径80-200毫米系列钢管冷轧机和直径2-80毫米 系列钢管冷轧机,1971年投产辊宽2300毫米冷轧合金薄板轧机, 1984年4月装配运用辊宽700毫米二十辊极薄带钢轧机,1965年投 产10000吨油压机,后因改善了工件的材质和原资料,用1000吨模 仿样机所替换,九套巨型成套装备的设计制作,有力地增援了国 防创建,促使了重型机械制作技巧水准的增高,使重型机械进展 进去了自行设计制作巨型成套装备的新阶段,一同也带领了各辅 机、电气、仪表制作业的进展。
关于8轴钻组合机床液压系统设计_百度文库解读

8轴钻组合机床液压系统设计摘要本文首先介绍了应用在组合机床上的液压系统的工作过程。
介绍了液压技术的发展现状和趋势。
详细了解了液压技术在我国的发展情况和被应用的状况。
仔细地阐述了设计液压系统的过程及步骤:液压系统的原理图的绘制、液压参数的计算(其中详尽地列出了所有的计算公式和过程)、液压站总装图的绘制以及零件图的绘制。
设计出了液压系统的原理图,并对它作出详细的阐述,简要说明了液压的工作原理,具有高效、节能的作用。
设计使液压技术向高压、高速、大功率、高效率、低噪声和高度集成话等方向发展,有广泛的应用前景和实际意义。
This article first introduced the application on the aggregate machine-tool hydraulic system work process. Briefed the hydraulic pressure technology development present situation and the tendency. Has understood the hydraulic pressure technology in detail in our country's development situation and by the application condition. Carefully elaborated the design hydraulic system process and the step. Hydraulic system schematic diagram plan, Hydraulic pressure parameter computation (Has listed all formula and process exhaustively,Hydraulic pressure station final assemly drawing plan as well as detail drawing plan.Designed the hydraulic system schematic diagram. And makes the detailed elaboration to it.Briefing hydraulic pressure principle of work. Has highly effective. Energy conservation function. The design causes the hydraulic pressure technology to the high pressure, high speed, high efficiency, high efficiency and the low noise and integrates directions and so on. Speech to develop highly has the widespread application prospect and the practical significance.目录第1章绪论1.1 组合机床41.3 液压技术 (4)1.4 液压技术在国外的发展趋势………………………………1.5 液压技术在我国的发展趋势 (6)第2章液压系统设计 (1)2.1明确液压系统设计要求 (11)2.2零件图的工艺分析 (1)2.3液压系统设计步骤 (5)2.4工况分析62.5选择液压元辅件 (17)2.6验算液压系统技术性能 (26)第三章液压泵站的设计 (29)3.1液压泵站的介绍 (29)3.2 液压泵站的设计过程 (29)第4章结论 (30)致谢辞 (31)参考文献 (32)第1章绪论当今世界,机械技术一日千里,为我们所处的时代加上了飞翔的翅膀,机械技术的产生和飞速发展改变了整个人类的生活和思维方式,为人类文明的进程作出了卓越的贡献,液压技术为机械行业做出了很大的贡献。
大型自由锻造液压机车间工艺设计分析
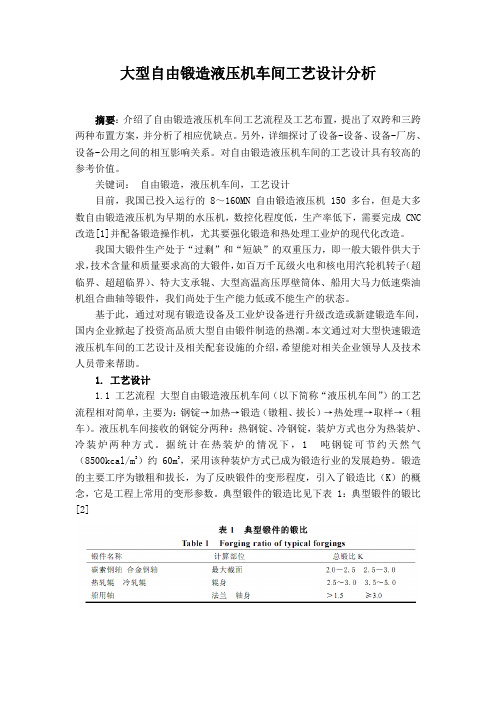
大型自由锻造液压机车间工艺设计分析摘要:介绍了自由锻造液压机车间工艺流程及工艺布置,提出了双跨和三跨两种布置方案,并分析了相应优缺点。
另外,详细探讨了设备-设备、设备-厂房、设备-公用之间的相互影响关系。
对自由锻造液压机车间的工艺设计具有较高的参考价值。
关键词:自由锻造,液压机车间,工艺设计目前,我国已投入运行的 8~160MN 自由锻造液压机 150 多台,但是大多数自由锻造液压机为早期的水压机,数控化程度低,生产率低下,需要完成 CNC 改造[1]并配备锻造操作机,尤其要强化锻造和热处理工业炉的现代化改造。
我国大锻件生产处于“过剩”和“短缺”的双重压力,即一般大锻件供大于求,技术含量和质量要求高的大锻件,如百万千瓦级火电和核电用汽轮机转子(超临界、超超临界)、特大支承辊、大型高温高压厚壁筒体、船用大马力低速柴油机组合曲轴等锻件,我们尚处于生产能力低或不能生产的状态。
基于此,通过对现有锻造设备及工业炉设备进行升级改造或新建锻造车间,国内企业掀起了投资高品质大型自由锻件制造的热潮。
本文通过对大型快速锻造液压机车间的工艺设计及相关配套设施的介绍,希望能对相关企业领导人及技术人员带来帮助。
1. 工艺设计1.1 工艺流程大型自由锻造液压机车间(以下简称“液压机车间”)的工艺流程相对简单,主要为:钢锭→加热→锻造(镦粗、拔长)→热处理→取样→(粗车)。
液压机车间接收的钢锭分两种:热钢锭、冷钢锭,装炉方式也分为热装炉、冷装炉两种方式。
据统计在热装炉的情况下,1 吨钢锭可节约天然气(8500kcal/m3)约60m3,采用该种装炉方式已成为锻造行业的发展趋势。
锻造的主要工序为镦粗和拔长,为了反映锻件的变形程度,引入了锻造比(K)的概念,它是工程上常用的变形参数。
典型锻件的锻造比见下表 1:典型锻件的锻比[2]大锻件形体尺寸大,缺陷多,内应力大,温度分布不均匀,结晶、相变复杂,内部热扩散及氢气扩散困难。
所以,冷却和热处理方式多,周期长、工艺过程复杂[2] 。
80MN热模锻压力机控制系统设计
80MN热模锻压力机控制系统设计热模锻压力机是借助模具实现金属热成型的锻压设备。
它广泛应用于汽车、拖拉机、机车、石化、军工等行业,是进行大批量、高精度模锻件生产的首选设备。
它可以进行镦粗、预锻、终锻、切边、冲孔等工序。
热模锻压力机的用途非常广泛,在热模锻压力机上可以完成开式模锻、闭式模锻、挤压等各种型材的热模锻工艺。
在热模锻压力机上进行锻造的典型零件有:(1)通过镦粗形式成型的锻件,如法兰盘和齿轮毛坯等。
(2)通过挤压方式成型的锻件如一些筒型零件。
(3)通过预先引伸方式成型的锻件,如汽车发动机的曲轴、前梁等。
1 热模锻压力机工作原理热模锻压力机主要由压平机的主机本体、辅助设备、液压系统、润滑系统、气动系统和电气控制系统组成。
压力机本体采用整体实心铸造机身,“X”型滑块导轨,双点支撑结构,具有刚性好、导向精度高、抗偏载能力强等特点。
主电机拖动小飞轮旋转,小飞轮通过皮带传动带动大飞轮,与大飞轮同轴的小齿轮与大齿轮啮合,而大齿轮最终为滑块提供动力,为了增加惯性,所以大齿轮的尺寸非常大,以保证有足够的惯性。
当电机经过四级启动1/ 8电阻启动完毕后,此时转速达到额定转速,通过离合器与制动器的配合,使滑块上下运动,滑块从上死点运动至下死点再回到上死点为一个工作循环,上死点也就是滑块的上极限位,下死点既为滑块下极限位。
压力机滑块有两种工作方式:调整与单次,调整工作方式时,滑块可以点动的停在任何位置;单次工作方式时,踩下脚踏开关,滑块完成一个工作循环。
由于机械构造的原因,润滑对热模锻压力机尤为重要,在压机本体上有多处干油及稀油润滑监测点和温度监测点,如:曲轴干油润滑、高速轴稀油润滑、曲轴温度等,这些监测点将开关量信号传入PLC控制系统,实时反映各个监测点的状态,以防止润滑不到位导致机械设备损坏。
2 工艺流程该热模锻压力机采用KUKA机械手上料,棒料经过传送带进入中频加热炉进行加热,当温度达到900℃左右时,棒料从加热炉中送出,此时上料机械手抓起热棒料送入压力机第一个工位,机械手撤出等待锻压,压力机滑块向下动作时,滑块动力是靠电机的带动,在上下模具接触到之后,也就是到达下死点后,滑块是靠惯性向上动作,在向上运行的过程中,上下顶料器顶出,将工件顶出模具。
多向模锻液压机设计
摘要本设计为中小型多向模锻液压机,最大工作负载设计为8MN。
主机主要由上梁、导柱、工作台、移动横梁、主缸、顶出缸,水平梁,水平缸等组成。
本文重点介绍了机械及液压系统的设计。
通过具体的参数计算及工况分析,制定总体的控制方案。
为解决缸快进时供油不足的问题,顶部设置补油油箱进行补油。
缸的速度换接与安全行程限制通过行程开关来控制;为了保证工件的成型质量,液压系统中设置保压回路,通过保压使工件稳定成型;为了防止产生液压冲击,系统中设有泄压回路,确保设备安全稳定的工作。
此外,对重要液压元件进行了结构、外形、工艺设计,对部分液压元件进行了合理的选型.控制系统的设计,它包括PLC的选型与程序设计。
关键词:多向模锻液压机, 机械设计,液压系统,可编逻辑控制器ABSTRACTThis paper design for the multi-forging of hydraulic , the mainframe’s largest work load design for 8000KN. Mainframe mainly by the beam、guided、worktable、mobile beams、master cylinder、level cylinder、cylinder head out of components etc. This paper focuses on the machine and hydraulic system design. Through analyzing specific parameters and hydraulic mechanic situation , to formulate a master control project. To solve the cylinder express entered the shortage of oil supply in the top of the mainframe installed oil tank. Cylinder for the speed of access restrictions and security through the limit switch to control switches.To ensure the quality of the work-piece molding, the hydraulic system equipped with packing loop through packing work-piece stability molding; To prevent hydraulic shocks, pressure relief system with a loop to ensure that this equipment can be a safe and stable work. In addition, the paper hydraulic station on the overall layout of the key components of the hydraulic structure、shape、process、technique for a specific design.the design of control system ,this part include choose the type of PLC and design the program.Keywords: Multi-forging of hydraulic machine, Design of machinary, Hydraulic System, Programmable Logic Controller目录1绪论 (1)1.1液压机行业概要 (1)1.2多向模锻的优缺点及发展方向 (3)2.机械总体设计 (4)2.1多向模锻压机主要技术参数 (4)2.2多向模锻液压机的基本工作原理 (4)2.3 总体布局方案的拟定 (5)2.4液压机设计 (6)2.5立柱设计 (15)2.6上横梁设计 (16)2.7下横梁工作台的设计 (17)2.8活动横梁设计 (19)2.9水平梁的设计 (19)3.液压系统设计 (20)3.1 液压机主缸工况分析 (20)3.2 液压机水平缸工况分析 (21)3.3 液压机顶出缸工况分析 (21)3.4 液压系统方案的设计 (22)3.5液压系统控制过程分析 (23)3.6液压系统的计算和选择液压元件 (24)4 .PLC控制系统设计 (31)4.1传感器的选择 (31)4.2位置检测装置 (31)4.3控制系统PLC的选型及控制原理 (32)4.4 PLC种类及型号选择 (32)4.5 PLC程序设计 (33)参考文献 (36)致谢 (37)1绪论1.1液压机行业概要液压机发展史,1795年,英国人Bramah取得了第一个手动液压机的专利,但真正的液压机的发展历史不到200年。
锻造液压机.
北京重型机器厂
5MN双柱下拉式 锻造液压机,拔 长2t以下的碳素 钢锭,镦粗1t以 下的碳素钢锭, 温度范围狭窄的 高强耐热合金钢。 8MN快锻液压机 拔长钢锭5t,镦 粗2.5t,最大环 件1550/1200, 饼件1100
厚度公差:+2mm。
3、整装式锻造液 压机
(二)、其他结构形式的锻造液压机及 其 技术参数 1、缸动式锻造液压机 特点:1)移动部分质量轻,惯性小, 消耗驱动功少。
北京重机厂 刚性固定改浮动接触,延长寿命,总长缩短
3、横向移砧装置 液压驱动,三、四套砧子。 中心线与移 动工作台互 成一定角度 或90度。
4、砧库 两种 存放3-4套砧子 横向移砧装置上只放两套
5、上砧快换与旋转装置
6、旋转台 圆盘形件,代替下砧 碟形弹簧上浮
7、氧化皮收集器
公害,磨损,划伤工作表面
第六节
锻造液压机
一、 锻造液压机的结构与技术参数
自由锻造液压机。上下砧、简单通用工具。3.15~150MN,几 十千克到三百吨坯料、钢锭。 翻动、送进。过去桥式起重机、转链、套筒。自由锻造操作 机,计算机控制,液压机与操作机联动。
(一)、最常见锻造操作机的本体结构形式及其技术参数
三种:单臂式、下拉式、整装式 1、单臂式锻造液压机
多用于公称压力较大 日本三菱50MN液压机 每侧立柱5 根拉杆,直径 200~250mm
按顺序 螺母旋入拉杆,支撑套,预紧缸 螺母旋入拉杆,手动高压泵。 1600x10E5Pa。30min。
(三)、Байду номын сангаас造液压机的工作能力
公称压 力/MN
拔长最 大钢锭/t 镦粗最 大钢锭/t
5.0
2 1
8.0
80MN双柱式预应力结构快速锻造液压机的设计研发
8 MN双柱 式预应 力 0 结构快 速锻造液压机 的设计研发
张 亦 工 。 陈 峰
( . 原 重 工 股 份 有 限公 司 技 术 中 心 , 1太 山西 太 原 0 0 2 3 0 4; 2济 南 铸 造 锻 压 机 械 研 究 所 有 限 公 司 , . 山东 济 南 2 0 2 ) 5 0 2
收稿 日期 :0 1 0 — 8 2 1-22
液 压 机 结 构 、 动 方 式 和 控 制 技 术 的 创 新 。 根 本 上 传 从
作者简介 : 张亦 工(90 )男 , 16一 , 高级工程师 , 事锻压设备及 其生产 从
工艺的设计研究管理
改 善 了 锻 造 车 间 的 劳 动 环 境 和 作 业 条 件 , 实 现 了锻
.-
太重 屎工
.
I
I
1
一
E
一 一
向结 构 ,使 内侧 导 板 能 够 自动 贴 合 产 生 横 向变 形 后
的 立 柱 , 效 提 高 了 导 向精 度 。 有 22 “ 人 4 ” 造 操 作 环 境 . 宜 1锻 =
口[ = 0
耐磨 导 板 , 活 动横 梁提 供 坚 固 、 性 的导 向平 面 。 为 刚
F辛
一
l
r — 辛气
q
与传 统 圆导套 相 比 , 面导 板接 触 面积 大 , 向面 压 平 导 低 , 向 间 隙 可 调 , 换 方 便 。 活 动 横 梁 具 有 超 长 导 导 更
. 1
7 结 束 语
【 徐 灏. 2 】 机械设计手册第 5 M . ; 卷[ ] 北京 机械工业 出版社 ,9 8 19 .
- 1、下载文档前请自行甄别文档内容的完整性,平台不提供额外的编辑、内容补充、找答案等附加服务。
- 2、"仅部分预览"的文档,不可在线预览部分如存在完整性等问题,可反馈申请退款(可完整预览的文档不适用该条件!)。
- 3、如文档侵犯您的权益,请联系客服反馈,我们会尽快为您处理(人工客服工作时间:9:00-18:30)。
本科毕业设计(论文)8MN板框式模锻液压机本体设计燕山大学本科毕业设计(论文)8MN板框式模锻液压机本体设计学院(系):机械工程学院____________年级专业:__________ 2010级_____________学生姓名:_______________________________指导教师:_______________________________答辩日期:2014 年月日 ________________燕山大学毕业设计(论文)任务书学院:机械工程学院系级教学单位:塑性成形系摘要大型模锻件制造水平的高低与航空航天、核电、船舶、军工等行业的发展存在着直接的联系并产生深远的影响。
为了满足对大型锻件日益增长的需求,用于其生产的主要设备—大型模锻液压机的研究、开发就显得更加迫切。
模锻液压机本体结构多种多样,其中,板框组合式结构可以很好的解决大型压机高承载引起的一系列问题,所以国内外大型模锻液压机广泛采用此结构。
目前大型板框式模锻液压机板框结构形式主要有三类:①框架由多层横板和竖板联成②框架由多层整片“ O'形钢板相互叠加通过预紧而成③框架由多层带钩头的钢板组合成。
液压机框架由多层带“ C”形钩头钢板组合成可以节省材料,降低成本,而且还能够解决加工、制造、安装、运输等问题,减少应力集中现象出现,提高了机架的强度,明显优于其它结构。
在设计过程中,根据液压机的主要技术参数算出主工作缸、穿孔缸、回程缸、平衡缸、上梁板、下横梁、活动横梁、“ C”形板、大拉杆、上下夹紧梁和上十字键等的主要尺寸。
液压缸作为液压机的关键部件,必须拥有足够的强度或刚度,所以必须通过校核计算,确定液压缸最终尺寸,并且利用UG 软件,建立了横梁、夹紧梁,上十字键和整体框架等零部件的实体模型,以Marc有限元软件作为分析工具,对主要受力零部件进行了三维有限元计算,对其结构的合理性和应力集中情况进行了分析,最终完成设计。
关键词:模锻,液压机,本体,板框式,建模,有限元,分析AbstractThe level of large forging manufacturing there is a direct link with aerospace, nuclear power, shipbuilding, war industry and other industries development and have a profound impact. In order to meet the increasing demand for large forgings, used for the production of large forging hydraulic press which is the main equipment research, development, becomes more urgent. Die forging hydraulic press frame structure is varied, among them, plate and frame composite structure can solve a series of problems caused by the large press high bearing well, so the domestic and foreign large forging hydraulic press widespread adoption of the structure. So far, the plate and frame structure of a large plate and frame type die forging hydraulic press mainly has three categories:(1) framework by multi-layer rung and got behind vertical plate (2) framework by multilayer entire "O" shape steel overlay each other by preloaded into (3) framework by multilayer belt hook plate combined into. Hydraulic press frame by "C" shaped hook and multi-layer steel plate combination can save materials, reduce cost, but also can solve the problem of processing, manufacture, installation, transportation and so on, to reduce stress concentration phenomenon, improve the strength of the chassis, is superior to other structures.In the design process, according to the main technical parameters to calculate the primary work cylinder of hydraulic press, punch, the return cylinder and balance cylinder, the beams, activity "C" shape plate, bar, upper and lower clamping beam and the main dimensions of the cross key, etc. Hydraulic cylinder as the key components of hydraulic press, must have sufficient strength and rigidity, so must pass the check calculation, determine the hydraulic cylinder size, and by using UG software, set up the beam, the clamping beam, cross key parts such as entity model and the overall framework, with finite element software Marc as analysis tool, the main stress components of the three-dimensional finite element calculation, the structure of rationality and stress concentration was analyzed, and the final design.Keywords: die forging hydraulic press, ontology, plate and frame type, modeling, finite element,analysis第1 章绪论1.1 课题背景为了满足电力、船舶、航空、航天和国防工业对大型锻件日益增长的需求,大型模锻液压机的开发、研究是不可避免的而且十分迫切的。
早在上世纪中叶,法国、前苏联和美国等先进制造国家就投建并应用于生产中一大批4 万吨级以上的大型模锻液压机,极大程度的带动了本国的航空、汽车等制造业,当时生产的大批优质锻件至今仍在使用而且性能良好。
到上世纪末前苏联和美国设计制造的压力机比例达到世界总量的七成左右,前苏联发展液压机技术较早,于1959 年设计制造的两台7.5 万吨大型模锻液压机一直沿用至今。
我国模锻液压机研究起步较早,后来由于各种原因研究工作搁置下来。
我国8 万吨模锻液压机顺利投产标志着我国已经步入锻造大国行列。
通过8MN板框式模锻液压机的设计、研究可以初步的掌握模锻液压机的结构和工作原理,解决出现的问题进一步优化设计过程,为以后大型、巨型模锻液压机的设计制造做好技术储备。
此外,通过完成此设计过程来巩固学过的知识,提高自己的能力。
1.1.1 综述本课题国内外研究动态模锻液压机主要应用领域为电力、船舶、航空航天行业, 大型模锻液压机是我国大型锻件在模锻过程中的重要设备, 过去我们国家没有大型压力机,致使一些锻件不得不依靠进口,这始终束缚着我国航空、航天、汽车、兵器等行业的发展。
现阶段而言,我国8万吨模锻液压机顺利投产使我国成为世界拥有数量最多、吨位最大重型模锻锻压设备的国家,但是从设备构成、等级、技术水平和所生产的锻压件的品种、精度、工艺水平方面与国外比,我们还有一些差距。
早在上世纪八十年代林秀安,聂绍珉对钢板组合机架做过研究;聂绍珉、金淼和吴生富等对全预紧机架整体性能进行了分析;我校黄学玲也通过工程算法对650MN液压机预紧机架进行受力分析并制作一台1:10样机安装在实验室;现阶段,国内对800MN模锻液压机的研究最多,早在2005年,我们学校的田会然、张庆等就对其本体结构进行了设计与分析;2010 年,杨固川、于江等人对大型模锻液压机机架结构进行了分析研究;中国第二重型机械集团公司通过对设计、研究以及国内外已建成液压机性能分析比较得出:采用C形板机架结构建造出800MN莫锻液压机;而国外,早在1959年前苏联建造的750MN莫锻液压机即为板框组合式结构;美国建造的450MN莫锻液压机采用立柱以“ T”形钩头板作为主要受力构件的结构;法国的650MN多向模锻液压机则以“ C”形钩头板为主要受力构件。
目前已投产的大型板框式莫锻液压机板框结构形式简介1.1.1.1 液压机框架由多层横板和竖板联成前苏联建造的750MN莫锻液压机就是这类结构(见图1),它是用多层的横板和竖板通过螺栓、键和销联接成整体的框架来承受液压机的公称压力[6]。
这种结构形式能够使得大型、巨型液压机的加工、输送和组装方便简单容易实现,然而由于它由多层横板和竖板构成整体,联接部位繁多,构成复杂,联接形式不单一,而且联接部位应力集中现象十分显著,大大的降低了机器框架的强度和承载压力的能力[7-10],也在一定程度上浪费了制造机架的材料增加了成本。
1.1.1.2液压机框架由多层整片“ O'形钢板相互叠加通过预紧而成由多层整片的“ O”形钢板叠加构成基本框架,以螺栓紧固联接构成一个整体。