过程确认控制程序
质量管理体系文件:生产过程控制程序
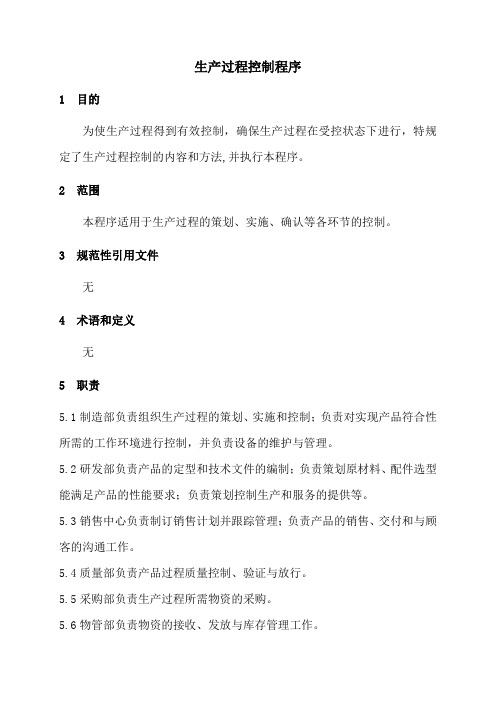
生产过程控制程序1目的为使生产过程得到有效控制,确保生产过程在受控状态下进行,特规定了生产过程控制的内容和方法,并执行本程序。
2范围本程序适用于生产过程的策划、实施、确认等各环节的控制。
3规范性引用文件无4术语和定义无5职责5.1制造部负责组织生产过程的策划、实施和控制;负责对实现产品符合性所需的工作环境进行控制,并负责设备的维护与管理。
5.2研发部负责产品的定型和技术文件的编制;负责策划原材料、配件选型能满足产品的性能要求;负责策划控制生产和服务的提供等。
5.3销售中心负责制订销售计划并跟踪管理;负责产品的销售、交付和与顾客的沟通工作。
5.4质量部负责产品过程质量控制、验证与放行。
5.5采购部负责生产过程所需物资的采购。
5.6物管部负责物资的接收、发放与库存管理工作。
5.7综合管理部负责组织人员培训工作。
6工作程序6.1生产过程策划6.1.1销售中心负责根据公司的年度销售目标、客户订单意向、市场预测等资料和信息,制订月销售计划;研发部负责根据销售计划确定产品的所有配置,编制技术文件,策划控制生产和服务的提供;质量部根据技术文件提出质量控制要求;生管员负责根据销售计划和产品清单制定《月生产计划》;制造部负责依据《月生产计划》对产品制造过程进行策划,综合平衡生产能力,制定排产计划,并组织过程的实施。
6.1.2根据生产过程的特点,应在受控条件下进行生产和服务提供。
适用时,受控条件应包括:a)在工作现场能够获得作业指导书、工艺规范等相关指导文件,规定做什么、怎么做、做到什么程度。
b)为产品和服务的符合性提供证据,所配备使用监视和测量资源(设备、人员、软件和信息资料等)数量、性能、测量范围以及使用方法等应满足监视和测量要求,其特性或能力与被监视和测量的产品和服务特性相适应。
c)在作业指导书中明确工序监视和测量点及验收标准,确保过程和结果符合要求。
d)控制基础设施和环境,设备的实际状况和各种参数能力适用于特定对象和场所,保持适宜的工作环境。
HSF关键过程识别和控制程序

HSF关键过程识别和控制程序HSF关键过程识别和控制程序1.0目的明确HSF关键过程的识别、确认和控制办法,证实这些工序实现所策划的能力,确保生产和过程的有效性。
2.0适用范围适用于公司大范围内HSF关键过程的识别、确认和控制。
3.0职责3.1技术部、品质部、采购部、制箔部、制液部、物管组负责HSF 关键过程的识别和确认;3.2技术部负责HSF关键过程的控制方法与准则;3.3制箔部、制液部、品质部负责HSF关键工序设备和对应人员资格的鉴定;3.4行政部负责组织对HSF关键过程人员的培训及资格鉴定;3.5技术部、品质部、采购部负责对供应商HSF关联工作的督导与跟踪;3.6市场部负责与客户间沟通HSF要求相关工作;3.7相关部门人员负责填写记录并保存。
4.0定义HSF关键过程:指影响实现产品HSF质量特性值和质量要求的过程和阶段。
5.0 HSF关键过程的识别与范围5.1HSF关键过程的识别5.1.1过程的识别原则:直接或间接对产品造成禁用环境物质污染的过程或活动都属关键过程的识别对象,广义的过程包括外部供应商、客户的生产活动及公司内部的生产活动。
5.1.2本公司识别HSF关键过程为采购、生产、包装、储存过程,并以进料、制液、制箔、分切、物管组等生产过程为管控对象,设立质量控制活动。
5.1.3原辅材料的风险度分类识别5.1.3.1 A类高度风险物料:物料直接与产品有关系,是产品的组成部分,又分两类:a)直接物料,如:阴极铜;b)需参与生产成为产品的组成部分的非直接物料,如:硫酸锌、硫酸镍、纤维素等;5.1.3.2 B类中等风险物料:与产品间接的有关系,但不是产品的组成部分,又分两类:a)化学品,如:硫酸、胶原蛋白等;b)需与产品一起交客户的包装材料,如缠绕膜、纸管、胶带等;5.1.3.3 C类低风险物料:与产品有接触,不是产品的组成部分的工具、制具,如:生产机组轴辊、分切刀片、手套等。
5.1.4对厂内和厂外既定HSF不合格品的管控,严格执行《环境物质管控程序》、。
验证确认控制程序

1、目的对公司所开展的质量活动中所涉及的验证和确认进行控制,以保证验证和确认过程在受控状态中进行,判定验证和确认的结论是否符合要求。
2、范围适用于对公司的设施设备、工艺过程和方法所开展的验证、确认活动。
3、职责3.1 质量部对法规、标准要求识别后,根据实际情况提出需进行相关的验证、确认活动,并组织与其相对应验证、确认小组;3.2 质量部负责组织验证、确认方案的编写,如公司内部无能力编写验证、确认方案,可委托公司外方编写验证、确认方案;3.3 验证、确认方案中确定的实施部门负责验证、确认活动的实施;3.4 验证、确认小组对外方验证确认结果进行复核;3.4 验证、确认小组对结果进行分析并编写出验证、确认报告;3.6 质量部经理负责验证、确认方案和报告的审核;3.7 验证、确认小组组长负责验证、确认方案和报告的批准。
4、工作程序4.1定义4.1.1 验证:证明任何操作规程、生产工艺或系统能达到预期结果而展开的一系列有计划、文件化活动。
验证是建立一个书面的证据,保证用一个既定的过程来始终如一地生产出符合预先确定质量特性的产品。
4.1.2 确认:证明厂房、设施、设备能正确运行并可达到预期结果的一系列有计划、文件化活动。
4.2 对于公司厂房、设施、设备的确认:质量部负责组织验证、确认小组对公司外方的确认结果进行复核后,外方的确认报告由质量部经理审核和验证、确认小组组长批准。
4.3 质量部根据法规、标准要求和公司实际的工艺过程、检查方法等识别出是否需开展的验证、确认活动。
公司其它部门在实际作业过程中如需对本部门的质量活动进行验证、确认,可委托质量部编制验证、确认方案。
4.4 确定需进行验证、确认活动后,质量部负责起草验证、确认方案。
原则上验证方案包括以下内容:1)概述;2)验证依据;3)验证目的;4)验证范围和实施时间;5)验证小组和职责;6)验证具体步骤;7)偏差的处理;8)再验证周期;9)相关记录。
4.5 验证、确认小组组长组织验证小组成员对验证、确认方案进行讨论、提出修改意见后形成验证、确认终稿,方案的终稿由质量部经理审核、验证小组组长批准。
ISO13485:2016软件确认控制程序精选全文完整版

1、目的确保质量管理体系过程中和医疗器械产品的软件各功能满足预期用途,特编制本程序文件。
2、范围适用于本公司所有医疗器械软件。
3、职责3.1 工程部:按公司的程序要求进行软件的设计和开发,进行软件验证、集成和软件维护,软件的生产周期评估。
3.2 品管部:负责软件使用前的确认。
3.3 采购部:负责软件变更后的确认。
4、定义4.1 医疗器械软件:旨在包括在被开发的医疗器械内的已开发的软件相同,或者预期本身用作医疗器械而开发的软件。
4.2 软件的安全性级别:制造商应按照软件系统引起的危害对于患者、操作者或其他人员的可能影响,赋于每个软件系统一个软件安全性级别(A、B 或C) 。
A级:不可能对健康有伤害或损坏。
B级:可能有不严重的伤害。
C级:可能死亡或严重伤害。
4.3 黑盒测试:将系统(软件和硬件)看作不能打开的黑盒,在不考虑系统内部结构和特性的情况下,测试者只依靠系统需求说明书,从可能的输入条件和输出条件中确定测试数据,也就是根据系统的功能或外部特性,设计测试用例(例如功能测试)。
4.4 白盒测试:即结构测试或逻辑驱动测试。
这种测试允许测试者考虑系统的内部结构,并根据系统内部结构设计测试用例,而不考虑系统的功能。
4.5 版本:某一配置项的已标识了的实例。
注:软件产品某版本的修改产生了一个新版本,但要求软件配置管理活动。
5、内容5.1软件的分类根据软件的作用方式不同,软件分类及定义见下表:5.2 软件的生存周期工程部负责软件的生存周期的评估,对软件进行确认。
软件应在初次使用前进行确认,适当时,在这类软件的变更后或应用时进行确认。
软件确认和再确认有关的特定方法和活动应与软件应用相关的风险相一致,包括对产品符合规范能力的影响。
5.3 软件测试工程部制定软件的测试方法,规范软件测试的主要方式和方法。
5.3.1 测试的分类a. 软件项各模块的单元测试;b. 软件组装测试;c. 软件确认测试;5.3.2 测试方案的策划测试方案的策划应包括以下内容:a. 单元测试计划、软件组装测试计划;b. 软件验收确认测试计划;c. 测试用例设计;d. 测试环境和工具;e. 测试结果的判定准则;f. 测试的组织和人员安排;g. 用户文档5.3.3 工程部按照软件测试方案的要求,在各软件模块、软件项和软件系统设计实现过程各阶段进行软件测试。
需确认工艺过程控制程序(含表格)

需确认工艺过程控制程序(YY/T0287-2017 idt ISO13485-2016)1.目的为了进一步规范本公司生产过程中需确认过程,确保工艺过程控制有效。
2.范围适用于本公司生产过程中的焊接、电镀、喷塑等工艺过程。
3.职责生产部负责公司需确认工艺过程控制工作。
质检部负责对过程的质量检验工作。
采购部负责对外发单位的资质审查和能力、技术等评审。
4.参考资料不合格品控制程序纠正/预防措施控制程序文件控制程序采购控制程序供应商控制程序GB/T19001-2016 idt ISO9001-2015质量管理体系要求YY/T0287-2017 idt ISO13485-2016医疗器械质量管理体系用于法规的要求YY/T0316-2016医疗器械风险管理对医疗器械的应用医疗器械生产质量管理规范(总局公告2014年第64号)(2015年3月1日起施行)医疗器械生产质量管理规范附录无菌医疗器械(2015年第101号)(2015年10月1日起实施)医疗器械生产质量管理规范无菌医疗器械现场检查指导原则(食药监械监〔2015〕218号附件2)(2015年9月25日发布实施)5.作业程序5.1定义产品质量不能通过后续的监视或测量加以验证的工序;对形成的产品是否合格,不易或不能经济地进行验证的过程。
5.1.1生产部确定工艺过程所需的机器设备,设备的操作规程,工艺作业指导书等,确保设备安装到位、并正确运行,及设备的维修保养等。
5.1.2质检部确定工艺过程的检验规程及检验方式,确认过程中实施过程所需的任何特殊控制和条件需要监视的过程参数等。
5.1.3人事部对人员操作资格和操作水平进行确定。
5.1.4确认的内容应包括或涉及以下内容:A、产品的详细说明;B、工艺的技术参数;C、试运行数据;D、性能鉴定的全部记录;E、进行性能鉴定时所有仪表、记录仪表等经过校准的证明;F、复审和重新确认的规定;G、确认方案;H、所用程序的文件资料;I、所用人员的培训手册与记录;J、文件化操作规程,包括过程控制范围;K、维护与校准程序;5.2初次/每年至少一次由生产部组织相关人员对的资质、设备的认可和人员资格的鉴定以及工艺方法、工艺参数的合理性进行确认。
生产过程控制程序(标准版)
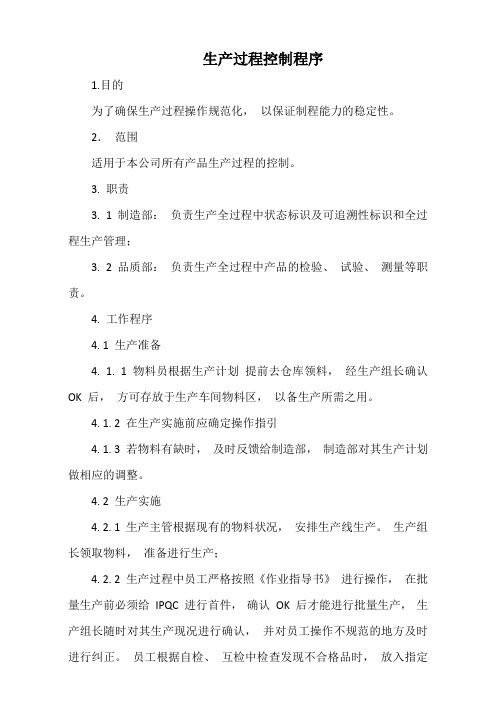
生产过程控制程序1.目的为了确保生产过程操作规范化,以保证制程能力的稳定性。
2.范围适用于本公司所有产品生产过程的控制。
3. 职责3. 1 制造部:负责生产全过程中状态标识及可追溯性标识和全过程生产管理;3. 2 品质部:负责生产全过程中产品的检验、试验、测量等职责。
4. 工作程序4. 1 生产准备4. 1. 1 物料员根据生产计划提前去仓库领料,经生产组长确认OK 后,方可存放于生产车间物料区,以备生产所需之用。
4. 1. 2 在生产实施前应确定操作指引4. 1. 3 若物料有缺时,及时反馈给制造部,制造部对其生产计划做相应的调整。
4. 2 生产实施4. 2. 1 生产主管根据现有的物料状况,安排生产线生产。
生产组长领取物料,准备进行生产;4. 2. 2 生产过程中员工严格按照《作业指导书》进行操作,在批量生产前必须给IPQC 进行首件,确认OK 后才能进行批量生产,生产组长随时对其生产现况进行确认,并对员工操作不规范的地方及时进行纠正。
员工根据自检、互检中检查发现不合格品时,放入指定的不合格品盒内。
4. 2. 3 各项作业工序完成后,由包装人员按作业指导书进行包装确认、称重、打单入库;4. 2. 4 若生产过程中出现重大异常时,发现者应及时的通知组长或线长进行确认,不能消除异常时,组长或线长应马上通知主管。
4. 2. 5 在生产异常处理后,必须由IPQC 重新进行首件确认OK,才可进行再生产。
4. 3 人员控制工作人员须具备岗位说明规定的任职资格,具备一定的知识和技能,以满足岗位的要求。
在职员工要持续进行质量管理体系、操作技能、相关制度规范等知识的培训,培训依据《人力资源管理控制程序》执行,培训合格后颁发上岗证。
4. 4 设备管理4. 4. 1 生产设备的管理制造部门每天检查生产设备的运行情况,按保养计划实施保养, 异常情况及时报告对生产设备进行维修,确保其处于正常运转状态。
4. 4. 2 生产使用检测设备的管理现场所使用的检测设备由制造部负责日常的维护,有异常情况应及时报告品管中心,检测设备的计量管理由品管中心统一管理,依据《监视和测量资源控制程序》执行。
生产过程控制程序含流程图

1.0目的
为了使生产过程始终处于良好的受控状态,并对于生产异常状况,加以预防改善,从而使产品符合规定的要求并不断提高产品质量。
2.0范围
适用于本公司所有产品的生产过程。
3.0定义:
3.1关键工序: 对最终产品的性能、寿命、可靠性及经济性等方面有直接影响的工序;产品质量特性形成的工序;工艺难度大,质量不稳定或问题发生较多的工序。
3.2特殊工序:该工序的产品质量不能通过检验和试验完全验证;该工序的产品质量需经过破坏性实验或采用复杂、昂贵的方法才能测得;该工序的产品质量特性无法测量,或不合格的质量特性要在产品使用后才能显示出来。
4.0职责
4.1 生产部——负责生产计划的编制、生产过程控制、生产现场5S管理,生产安全管理、设备保养及维护;负责人员配置及协助技能培训。
负责组织生产过程的再确认。
4.2 技术中心——提供产品图纸、等生产过程需要的技术资料与技术支持;负责工艺装备的设计与提高;负责生产过程的再确认的技术中心分确认;负责生产过程的技术问题的处理。
负责新产品试制的跟踪。
4.3 工艺部——工艺作业指导书
4.4 品管部——负责生产过程的采购件、半成品、成品的检验及质量控制;负责生产过程的再确认的质量确认。
4.5. 采购部——负责按时按质按量采购生产所需物料;负责保管、收发生产所需的各种物料;
4.6 人事部——组织人力资源招聘及技能培训。
4.7 各车间——负责按生产作业计划组织本车间生产;负责车间安全、设备、5S管理;负责生产过程中的异常问题的报告及处理。
附录1:。
产品和过程确认管理程序(含表格)

产品和过程确认管理程序(IATF16949-2016)1 目的对新产品和新过程以及批产产品和批产生产线(过程)进行确认,证实产品和过程能够满足规定的使用要求或已知的预期用途的要求且稳定受控。
2 适用范围2.1 适用于公司及外协的产品和过程确认。
2.2 如下发生更改时,需进行重新确认:2.2.1 新品(油品);2.2.2 关键工艺参数更改(调合/灌装设备、调合温度、调合时间、溶胶温度、溶胶时间、调合加料顺序、过滤设置)2.2.3 油品设计更改(DFMEA更改、关键原材料更改-复合添加剂、增粘剂、基础油等级降低);2.2.4 生产产地变更;2.2.5 供应新品(包材、外购新品)。
3 职责3.1 技术研发中心负责组织产品和过程确认,并下达确认实施计划;负责向顾客提交PPAP申请批准资料。
3.2 生产部根据确认计划组织试生产;负责生产设备状态、工艺、人员资格等确认。
3.3 调度中心负责包材产品确认。
3.4 各部门负责按项目提出申请和开展工作。
4 引用文件4.1 《产品质量先期策划控制程序》5 术语和定义5.1 确认项目、申请部门、周期时间项目新品(油品)关键工艺参数更改设计更改(油品)生产场所变更供应新品确认时机批产前批产时批产时批产前批产前申请部门项目组长生产部技术研发中心生产部供应部组织部门技术研发中心技术研发中心技术研发中心技术研发中心技术研发中心6 工作流程产品和过程确认工作流程图、产品和过程确认工作流程说明职责岗位流程作业指导书、记录等项目组长、生产部、技术研发中心、供应部技术研发中心生产部6.16.26.3确认实施计划下达生产计划设计更改关键工艺参数更改生产场所变更新品(油品)供应新品提出确认申请制订、下达确认实施计划技术研发中心生产部调度中心供应部技术研发中心各职责部门技术研发中心6.46.56.66.7生产计划工艺文件状态确认报告工装状态确认报告工艺验证报告测量系统分析报告过程能力分析报告生产设备状态确认报告操作人员资质确认报告工作环境、定置管理确认报告全项目检验报告产品确认试验报告制造现场过程确认问题报告整改计划产品和过程确认报告工作环境、定置管理确认生产线设备状态操作人员资质确认产品确认整改计划确认报告现场过程确认工艺文件状态、工装状态确测量系统分析、过程能力分析技术研发中心6.8产品和过程确认工作流程说明序号流程块工作标准期量标准6.1 提出确认申请6.1.1如符合以下任何一个更改时,需进行重新确认,则由职责部门按上述5.1“确认项目、申请部门、周期时间”表格内容执行。
- 1、下载文档前请自行甄别文档内容的完整性,平台不提供额外的编辑、内容补充、找答案等附加服务。
- 2、"仅部分预览"的文档,不可在线预览部分如存在完整性等问题,可反馈申请退款(可完整预览的文档不适用该条件!)。
- 3、如文档侵犯您的权益,请联系客服反馈,我们会尽快为您处理(人工客服工作时间:9:00-18:30)。
1.0目的
对特殊过程确认进行有效控制,确保此过程达到预期的要求,保证产品质量。
2.0范围
适用于本公司所有特殊过程的控制。
3.0职责
3.1研发部,生产部,负责识别出生产过程中的特殊过程;
3.2质量部,负责组织实施过程确认活动,生产部等相关部门配合;
4.0工作程序
4.1定义
4.1.1特殊过程
当生产和服务提供过程的输出不能由后续的监视或测量加以验证,包括在产品使用或服务已交付之后问题才显现出来的过程。
4.1.2过程确认
获得某一过程持续产生满足预先规定要求的结果或产品的客观证据。
过程确认包括安装鉴定(IQ)、运行鉴定(OQ)和性能鉴定(PQ);
4.1.3安装鉴定(IQ)
依据客观事实确定所有涉及到加工设备和辅助系统安装的关键方面符合已确定的规范要求,同时恰当地考虑了设备供应商所推荐的有关要求;
4.1.4运行鉴定(OQ)
依据客观事实确定所有过程控制限度、操作标准要求,过程输出满足预先设定的要求;
4.1.5性能鉴定(PQ)
依据客观事实确定在预先设定条件下过程输出持续稳定满足预先设定要求。
4.2过程确认的策划
4.2.1识别需要进行确认的过程
4.2.1.1对每一个生产或服务提供的过程或其子过程,应明确描述其过程参数和期望的过程输出。
由使用该过程的部门进行分析;
a)该生产或者服务提供的产品是否可以采用随后的监控或测量进行有效验证,如不能进行有
效验证,则该过程需要进行确认;
b)对可以进行有效验证的过程应考虑,对其进行独立验证是否充分排除了不可接受的风险,以
及验证成本是否可以接受,如存在不可接受风险或验证成本不可接受,则给过程需要进行确认。
4.2.1.2当引入一种新的过程,或生产和服务提供过程发生重大变更时,应由生产或服务提供部门重新进行评价,确定该过程是否有必要进行过程确认;
4.2.1.3用于生产和服务提供的过程控制软件均需要进行确认;
4.2.1.4对识别出来的特殊过程,建立《特殊过程清单》。
4.2.2过程确认的活动和计划
4.2.2.1过程确认活动
过程确认活动包括对特定过程评价计划的制定和评价阶段的实施,记录信息的收集和阐述。
这些活动通常包括以下几个阶段:
a)设备规范的评审与批准;
b)所使用设备的初始鉴定和必要服务的提供,也称为安装鉴定(IQ);
c)证明过程输出可接收的结果,并建立过程参数的限度(需要考虑最恶劣的情况),也称为运
行鉴定(OQ);
d)保持过程输出持续稳定,也称为性能鉴定;
4.2.2.2由生产部负责组织制定《过程确认方案》。
《过程确认方案》应包括:
a) 过程参数的准确性和误差,包括使用设备的安装;
b)操作者的技能、能力和知识的要求;
c)所有过程控制的准确性,包括环境参数;
d)适当时,过程和设备的鉴定;
e)对未满足这些准则的过程参数的处理和可接收的准则;
f)需要进行重新确认的条件;
g)确定参与过程确认的人员,组成过程确认小组;
h)确定过程确认的方案和过程确认的方法;
4.2.2.3 过程确认方法应考虑下列因素:
a)评价的过程;
b)过程的输出(或生产的产品);
c)验证项目和测量接收准则;
d)过程确认的范围和区间;
e)被确认过程涉及到人员和设备;
f)过程所使用的设备及其质量要求;
g)操作者及其技能要求;
h)对过程的完整描述;
i)与产品部件、生产物料等相关的有关规格指标;
j)在过程确认活动中影响过程操作的任何特定控制或条件;
k)监控的过程参数,监测的控制方法;
l)被监控的产品特性及其监测方法;
m)评估产品的任何主观准则;
n) 确定可测量和主观观察项的差异评分等级;
o)数据收集和分析所采用的统计方法;
p)生产设备维护和维修的影响;
q)设定过程确认准则;
r)对安装鉴定、运行鉴定和性能鉴定,基于产品/过程要求;
s)确定验证/测量项目;
t)确定如何进行验证/测量;
u)确定验证/测量的频次,既考虑到统计意义;
v)确定何时进行验证/测量;
w)确定接收/拒绝准则;
x)确定文件记录要求。
4.3过程确认
4.3.1安装鉴定
安装确认需考虑以因素:
a) 设备设计特性;
b)安装条件;
c)校准、防护性维护保养、清洁日程;
d)安全特性;
e)随机文件、操作手册、随机图示等;
f)软件文档;
g)备件清单;
1.1.1环境条件(洁净要求、温度要求、湿度要求等);
1.1.2设备生产商提供的证明文件,经评估可作为安装鉴定的依据
1.1.3运行鉴定
运行鉴定应考虑日常操作中调整的范围,以及最恶劣情况,以保证过程的输出在日常操作中均能够满足确定的要求;运行鉴定应考虑下列因素:
a)过程控制的极限(时间、温度、压力、线速度、设定条件等);
b)软件参数;
c)原材料特性;
d)过程操作程序;
e)材料处理要求;
f)过程变更控制;
g)培训;
h)瞬时稳定性和过程能力(纬度影响或控制特性);
i)潜在失效模式,操作水平,最恶劣条件(FMEA分析,故障树分析);
j)采用统计评估技术,如:回归试验建立关键参数、设定统计试验优化过程。
1.1.4性能鉴定
性能鉴定是为了验证过程在正常条件下的持续稳定能力;性能鉴定应考虑下列因素:
a)实际输出、过程参数,以及确定相应操作程序;
b)确认过程输出是否可接收;
c)保证确认过程能力;
d)过程重复性、过程长期稳定性。
e)在性能鉴定中,应分析过程及其输出的数据,确定过程输出的正常变化范围。
f)作为运行鉴定和性能鉴定的一部分,应确定过程持续监控和维护的要求。
应对过程及其输出的数据进行分析,识别任何可以控制因素引起的变异。
基于过程特性及其敏感性,导致变异的可控因素包括:温度、湿度、电源稳定性、震动、环境污染、水处理的纯度、外界光源影响、人为因素、材料变异、设备磨损等,应采取适当的措施控制这些因素。
4.3.4生产过程软件的确认
生产过程中使用的软件,如特殊过程中关键设备中的软件、自动化生产的控制软件、追溯系统等,在使用前应经过确认,具体的确认依据《软件管理控制程序》执行。
4.3.5过程确认报告
作为过程确认的输出,应形成《过程确认报告》。
《过程确认报告》应概述和提及过程确认方案和过程确认结果,应对过程确认做出明确结论。
《过程确认报告》由过程确认小组负责起
草,项目负责人审核,管理者代表批准。
4.4保持已确认过程的有效性
4.4.1已确认过程的监控
生产和服务提供过程所在部门应监控过程趋势,以确保过程在已经确认的参数范围之内运行。
当监控数据表明过程质量特性出现偏离,生产和服务提供过程所在部门应启动调查分析,采取必要的纠正和预防措施,并重新确认过程的有效性。
4.4.2过程的再确认
当发生操作程序、设备、人员变化时,由生产和服务提供工程所在部门评估这些变化对过程的影响程度,确定是否需要对过程进行再确认;
对已经识别的需要进行确认的过程,每间隔一年,需要再对过程进行再确认。
再确认需要通过操作确认和实效确认,确认过程的有效性;当发生下列情况下,应进行过程再确认:a)过程的变化可能影响质量或者过程确认的有效性;
b)过程监控数据表明在质量方面有明显的不良趋势;
c)产品设计导致过程发生变化;
d)生产场所的变化;
e)过程应用程序发生变化。
对过程再确认应予以评估和记录。
评估包括:过程输出质量特性的历史数据、过程变化、产品变化、外部要求的变化(法规或标准),以及其他情况。
过程再确认不需要重复过程初始确认的所有步骤。
当采购了新设备时,有必要进行安装确认(IQ),需要对原操作确认未覆盖的操作进行运行确认(OQ),依据新设备对过程的影响进行相应的性能确认(PQ)。
5.0相关文件
5.1 《软件管理控制程序》
6.0相关记录
6.1《过程确认方案》QR-MD-031
6.2《过程确认报告》QR-MD-032。