SMP-P-G012-00物料平衡及产品收率管理规程
GMP体系文件物料平衡管理规程

目的:建立一个物料平衡的工作标准,掌握生产过程中物料平衡,进行严格的收率控制,防止发生差错和出现混药现象。
范围:产品生产过程中的各个关键工序
责任人:岗位操作人员、车间管理人员、质量保证部、生产制造部。
内容:
1、在每个关键工序计算收率,进行物料平衡是避免或及时发现差错与混药的有效方法之一,因此,每个品种关键生产工序的批生产记录(批包装记录)都必须明确规定物料平衡的计算方法,以及根据验证结果确定收率范围。
2、物料平衡计算的基本要求
2.1 物料平衡计算公式:物料平衡=(产出量+尾料量)/(总投入量)× 100%
产出量:生产过程中实际产出量,不包括收集的废品量,生产中取得样品量(检品),丢弃的不合格物料。
尾料量:生产过程中产生的药头数量等。
总投入量:生产过程实际投入的数量。
2.2 在生产过程中如有跑料现象,应及时通知车间管理人员及质量保证部质量监督员,并详细记录跑料过程及数量。
跑料量也应计入物料平衡中,加在实际范围之内。
3、物料平衡计算单位
3.1 固体以重量计算。
3.2 液体以体积或重量计算。
4、数据处理
4.1 凡物料平衡在规定范围之内,经质监员审核,可以递交下道工序。
4.2 凡物料平衡高于或低于合格范围,应立即贴“待查”标志,不能递交下道工序,并填写偏差通知单,通知车间管理人员及质监员按“生产过程偏差处理管理规程”进行调查处理,并如实记录。
4.3 质量保证部会同生产制造部定期对各工序收率及产品的总体物料平衡进行
核算,并进行回顾性验证,为工艺改进、技术革新及技术文件的修订提供参考。
SMP-SC-011 物料平衡及产率管理规程

无。
6变更历史
版本号01:新建文件,2015年5月1日起开始执行。
7附录
无。
4.4物料平衡的评价
4.4.1标准随工艺变化而变化,因此应处于动态管理之中。制剂室可以根据产品质量总结回顾评价既定标准的合理性,必要时进行适当的调整。
4.4.2当生产工艺、可能随之变化,质量管理部应负责组织评价各种工艺变化对物料平衡标准所带来影响的合理性,必要时应进行验证。
(2)分装操作的物料平衡
计算方法:物料平衡=(至贴签量 平均装量+损耗量)/至分装量 100%
限度:100%
(3)贴签操作的物料平衡
计算方法:实际产量=入库量+取样量
物料平衡=(实际产量+损耗量)/至贴签量 100%
限度:100%
4.2产率
计算方法:产率=实际产量/理论产量 100%
限度:95%~105%(普通制剂);90~110%(中药制剂)
4.3物料平衡的审核
4.3.1凡物料平衡在合格范围之内,经生产负责人检查确认后,可以递交下道工序。
4.3.2若物料平衡超出了合格范围,不能递交下道工序。要通知相关管理人员进行评估与调查,并详细记录,具体执行《偏差管理规程》。
4.3.3在进行批放行审核时应对各工序物料平衡情况进行审核,作为评价产品是否合格的重要指标之一。
4.1.2物料平衡的计算
每个工序必须进行物料平衡,药品生产过程中的物料平衡如有显著误差,必须进行调查,确认是否存在潜在质量风险,因此,物料平衡标准也是产品质量的检验性指标。
(1)配制操作的物料平衡
计算方法:物料平衡=(至分装量+取样量+损耗量)/总投料量 100%
限度:95%~105%(普通制剂);90~110%(中药制剂)
SMP-SC-WL010-00物料平衡管理规程
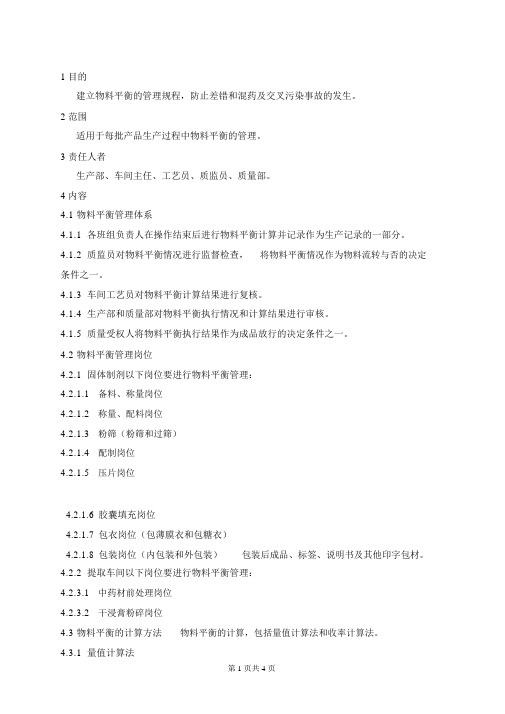
1目的建立物料平衡的管理规程,防止差错和混药及交叉污染事故的发生。
2范围适用于每批产品生产过程中物料平衡的管理。
3责任人者生产部、车间主任、工艺员、质监员、质量部。
4内容4.1 物料平衡管理体系4.1.1 各班组负责人在操作结束后进行物料平衡计算并记录作为生产记录的一部分。
4.1.2 质监员对物料平衡情况进行监督检查,将物料平衡情况作为物料流转与否的决定条件之一。
4.1.3 车间工艺员对物料平衡计算结果进行复核。
4.1.4 生产部和质量部对物料平衡执行情况和计算结果进行审核。
4.1.5 质量受权人将物料平衡执行结果作为成品放行的决定条件之一。
4.2 物料平衡管理岗位4.2.1 固体制剂以下岗位要进行物料平衡管理:4.2.1.1备料、称量岗位4.2.1.2称量、配料岗位4.2.1.3粉筛(粉筛和过筛)4.2.1.4配制岗位4.2.1.5压片岗位4.2.1.6胶囊填充岗位4.2.1.7包衣岗位(包薄膜衣和包糖衣)4.2.1.8包装岗位(内包装和外包装)包装后成品、标签、说明书及其他印字包材。
4.2.2 提取车间以下岗位要进行物料平衡管理:4.2.3.1中药材前处理岗位4.2.3.2干浸膏粉碎岗位4.3 物料平衡的计算方法物料平衡的计算,包括量值计算法和收率计算法。
理论数(实际投入量)=产成品数+残次品数4.3.2 收率计算法平衡收率=实际值 / 理论值× 100%理论值为实际投入物料量。
实际值为生产过程中实际产出量包括本岗位正品产出量、废品量、零散品量、生产中取样(留样)量。
4.3.3 在生产过程中如有跑料、散装后跌落在地上的物料,要及时通知车间工艺员及车间质监员,详细记录损失数量及事故过程,其损失数计入残次品数之内进行计算。
4.3.4 上工序移交下来的有效物料并经复核的数量,计入下工序计算收率的理论值。
4.3.5 理论投入数与实际产出数二者的正负误差要控制在允许范围内。
4.3.6允许偏差范围根据各产品的特性及加工部位的不同分别制定各岗位平衡允许偏差范围。
【精】GMP物料平衡与收率3
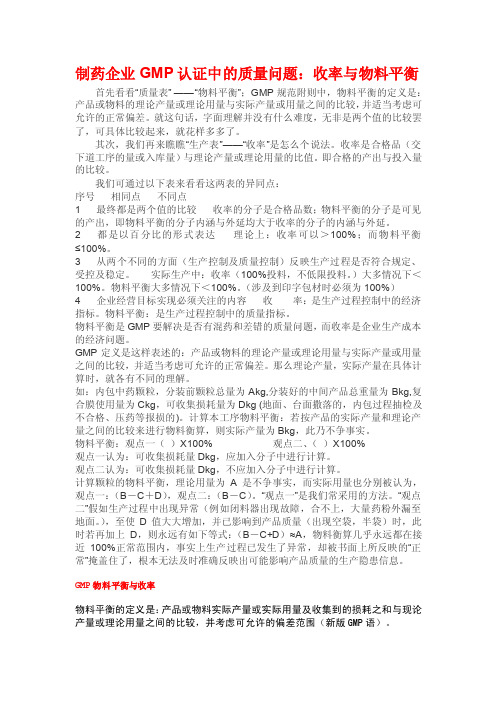
制药企业GMP认证中的质量问题:收率与物料平衡首先看看“质量表” ——“物料平衡”;GMP规范附则中,物料平衡的定义是:产品或物料的理论产量或理论用量与实际产量或用量之间的比较,并适当考虑可允许的正常偏差。
就这句话,字面理解并没有什么难度,无非是两个值的比较罢了,可具体比较起来,就花样多多了。
其次,我们再来瞧瞧“生产表”——“收率”是怎么个说法。
收率是合格品(交下道工序的量或入库量)与理论产量或理论用量的比值。
即合格的产出与投入量的比较。
我们可通过以下表来看看这两表的异同点:序号相同点不同点1 最终都是两个值的比较收率的分子是合格品数;物料平衡的分子是可见的产出,即物料平衡的分子内涵与外延均大于收率的分子的内涵与外延。
2 都是以百分比的形式表达理论上:收率可以>100%;而物料平衡≤100%。
3 从两个不同的方面(生产控制及质量控制)反映生产过程是否符合规定、受控及稳定。
实际生产中:收率(100%投料,不低限投料。
)大多情况下<100%。
物料平衡大多情况下<100%。
(涉及到印字包材时必须为100%)4 企业经营目标实现必须关注的内容收率:是生产过程控制中的经济指标。
物料平衡:是生产过程控制中的质量指标。
物料平衡是GMP要解决是否有混药和差错的质量问题,而收率是企业生产成本的经济问题。
GMP定义是这样表述的:产品或物料的理论产量或理论用量与实际产量或用量之间的比较,并适当考虑可允许的正常偏差。
那么理论产量,实际产量在具体计算时,就各有不同的理解。
如:内包中药颗粒,分装前颗粒总量为Akg,分装好的中间产品总重量为Bkg,复合膜使用量为Ckg,可收集损耗量为Dkg (地面、台面撒落的,内包过程抽检及不合格、压药等报损的)。
计算本工序物料平衡:若按产品的实际产量和理论产量之间的比较来进行物料衡算,则实际产量为Bkg,此乃不争事实。
物料平衡:观点一()X100%观点二、()X100%观点一认为:可收集损耗量Dkg,应加入分子中进行计算。
物料平衡的标准管理规程

物料平衡的标准管理规程一、目的:建立物料平衡的标准管理规程,防止发生差错。
二、适用范围:适用于每批产品生产过程中物料平衡的管理。
三、责任者:生产技术部负责人、操作工人、质量监督员。
四、正文:1 在关键工序计算收率,进行物料平衡是避免或及时发现差错的有效方法。
2 收率计算的基本方法:2.1 收率计算收率=实际值/理论值×100%其中:理论值:为按照所用的原料(包装材料)量,在生产中无任何损失或差错的情况下得出的最大数量;实际值:为生产过程中实际产出量包括本工序正品产出量。
2.2 在生产过程中如有跑料、散装后跌落在地上的物料,应及时通知组长及品管监督员,详细记录损失数量及事故过程,其损失数加在实际值之内进行计算。
2.3上工序移交下来的有效物料并经复核的数量,为下工序计算收率的理论值。
2.4各工序物料平衡计算具体方法:2.4.1 过筛打粉预处理:检查与复核原物料品名、数量、以及其质量情况。
每一个物料,打粉过筛后称重量,并将上述每一种物料经打粉后的损耗率记录在工艺原始记录上。
计算:物料损耗率=(打粉过筛前总重-打粉过筛后总重)/打粉过筛前总重×100%2.4.2制颗粒:检查与复核领入原物料的品名、批号、数量以及质量情况,如发现有异常情况,及时报告品管监督员同意后退回中间站。
颗粒制好后,称重量、抽样测含量,必要时可增加测水分。
2.4.2.1 计算总收率:预处理后物料总重量及制粘合剂的固体料(不含配粘合剂所用的液体溶媒)之和为理论值,颗粒干燥后总重量及捕尘器中废料和收集的残料之和为实际值,颗粒总收率=实际干颗粒共重/(本批配料后的总共重量+外加辅料)×100%颗粒损耗率=(制料前总重-实际干颗粒共重)/制粒前总重×100%2.4.2.2 损耗率太大或有问题时,必须查明原因,如检查工序内地面上积粉等可收集部分称重后,再复核计算是否相符,要求将损耗率降低。
如果损耗率是负值,很可能颗粒中水分太高。
物料平衡的管理规程
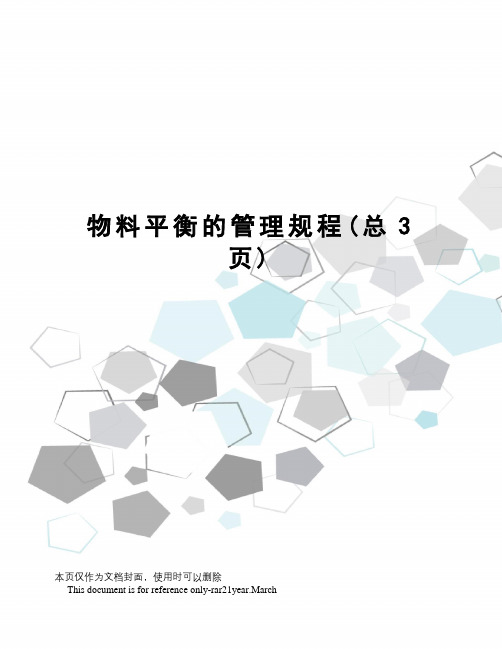
物料平衡的管理规程(总3页)本页仅作为文档封面,使用时可以删除This document is for reference only-rar21year.March建立物料平衡的管理规程。
建立物料平衡的审核标准,掌握生产过程中物料收率变化,防止差错和混药。
2 范围适用于每个批次产品生产过程的关键工序都要进行物料平衡的计算及偏差处理。
3 职责生产技术部部长、生产车间主任、工艺员、操作工,QA监控员。
岗位操作人员负责本岗位平衡的计算,并对计算结果进行判断;生产车间主任负责批平衡收率的计算,工艺员负责各岗位平衡收率的审核及对出现偏差进行分析和说明;QA负责批生产平衡的审核。
4 内容4.1 物料平衡是产品或物料实际产量或实际用量及收集到的损耗之和与理论产量或理论用量之间的比较,并考虑可允许的偏差范围。
4.2 物料平衡的计算是为了防止物料误用和非正常流失4.3 每个品种各关键生产工序的批生产记录(批包装记录)都必须明确规定平衡的计算方法,以及根据验证结果和生产实际确定的平衡限度范围。
4.4 物料平衡计算:产出量+废品量+剩余量物料平衡=×100%(99-100%)投入量投入量:领料的净量。
产出量:为生产过程中实际产出量,包括合格产品和不合格产品。
废品量:过程抛撒受污染后收集的扫地料及检测后不能再使用的产品或料粉。
4.5 物料平衡计算单位:4.5.1 中间产品、成品:中间体采用重量单位(kg);说明书、包装袋、包装盒、包装箱等,分别采用“张”、“只”、“套”、“个”计算。
4.6 结果处理:4.6.1 凡物料平衡在规定平衡限度范围之内,经质量部QA检查确认后,产品可以递交下工序。
4.6.2 凡物料平衡超出规定平衡限度范围的,应立即贴示“待验”标志,产品不得递交下工序,操作工应及时填写《偏差通知单》,通知生产车间主任及QA监控员按《生产过程偏差处理管理规程》中有关偏差处理程序进行调查,采取处理措施,并详细记录。
GMP物料平衡管理规程

页码:文件编号:生效日期: 再版日期:第1页/共2页SMP-PM-01003-1标准管理规程STANDARD MANAGEMENT PROCEDURESubject题目:物料平衡管理规程Issued by颁发部门:质量部Written by起草人:Date日期:Dept. Head Approval 部门主管审核:Date日期:QA Director Approval QA 主管审核:Date日期:Approved by批准:Date日期:Dispense分发:总经理、质量部、生产部、商务部、行政人事部1.目的建立物料平衡的管理规程,严格物料管理,防止物料流失,控制成品率;防止差错和混药事故的发生。
2.适用范围适用于每批产品生产过程中物料平衡的管理。
3.责任者生产部、各生产车间、商务部、质量部相关人员。
4.内容4.1.在每个关键工序计算收率、进行物料平衡,是避免和及时发现差错与混料的有效方法之一。
因此,每个品种各关键生产工序的批生产记录(批包装记录)都必须明确规定收率的计算方法,以及根据验证结果确定的收率合格范围。
4.2.收率计算的基本要求:4.2.1.收率计算:实际值收率=─────────×100%理论值其中:理论值:按照所用的原料(包装材料)量,在生产中无任何损失或差错的情况下得出的最大数量。
实际值:生产过程中实际产出量,包括:本工序产出量、生产中取得样品量(检品)4.2.2.在生产过程中如有跑料现象和可见损耗,应及时通知车间管理人员及QA部门QA检查员,并详细记录跑料可见损耗过程及数量。
跑料和可见损耗数量也应计入物料平衡之中,加在实际值的范围之内。
页码:文件编号:生效日期: 再版日期:第2页/共2页SMP-PM-01003-1标准管理规程STANDARD MANAGEMENT PROCEDURESubject题目:物料平衡管理规程Issued by颁发部门:质量部4.2.3.如若实际收率在规定的收率范围内,即视为物料平衡合格,一般收率应在97%-101%之间。
GMP质量体系010物料平衡管理规程

物料平衡管理规程
1. 目的:建立物料平衡管理规程,防止差错和混淆。
2 范围:生产车间的关键工序。
3 责任:操作工、过程监控员、车间负责人、质量负责人、生产负责人对本规程的实
施负责。
4 内容:
4.1 物料平衡是指产品或物料的理论产量或理论用量与实际产量或用量之间的比较,并
适当考虑可允许的正常偏差。
4.2 每批产品生产结束后,由车间对物料进行平衡计算,及时发现差错与混药。
4.2.1 物料平衡的计算:
%100⨯=
理论值
实际值
物料平衡
注:实际值:为生产中实际产出量。
包括本工序产出量(合格品);收集的废品量;
生产中的样品量(检品、留样观察品)。
理论值:按照生产指令所用的原料、包装材料量,在生产过程中无任何损失
或差错的情况下得出的理论数量。
4.3 需要进行物料平衡计算的主要工序;见下表:
物料平衡表:
4.4 数据的处理:
4.4.1 物料平衡率高于或低于合格范围,不能递交下工序,通知过程监控员及质量部有关
人员进行调查,采取处理措施,并详细记录。
4.4.2 质量负责人对各工序物料平衡进行检查,为工艺改进、技术标准文件的修订提供参
考。
- 1、下载文档前请自行甄别文档内容的完整性,平台不提供额外的编辑、内容补充、找答案等附加服务。
- 2、"仅部分预览"的文档,不可在线预览部分如存在完整性等问题,可反馈申请退款(可完整预览的文档不适用该条件!)。
- 3、如文档侵犯您的权益,请联系客服反馈,我们会尽快为您处理(人工客服工作时间:9:00-18:30)。
1.目的:
建立一个标准的物料平衡及产品收率管理规程,防止生产浪费和质量事故的产生,及时掌握生产过程中收率的变化情况以加强生产过程的管理。
2.依据:
国家食品药品监督管理局《药品生产质量管理规范》(1998年修订)
3.适用范围:
各工序生产结束后的物料平衡及成品的收率计算。
4.责任:
各岗位操作人员对本岗位的物料进行核算,生产管理人员对每批成品的收率进行计算,QA人员对本规程的实施进行监督。
5.内容:
5.1.每个工序必须进行物料平衡,避免或及时发现差错与混药的发生。
若平衡
率超出工艺规定的范围,应进行偏差调查。
5.1.1.原辅料的平衡率计算公式为:生产后物料数量/生产前物料数量×100%。
5.1.1.1.生产前物料数量:物料投入的总量,如粉碎过筛工序即为粉碎前称量的
物料总重。
5.1.1.2.生产后物料数量:产出量、收集的废品量、剩余量、取样量等生产后能
计量的物料数量。
如中间过程的取样量少,不影响物料的平衡时,可以
忽略不计。
5.1.1.3.如生产过程进行了分装,产出量、取样量与投料量的单位不一致时,应
进行换算,用产出量乘以换算系数进行计算,如平均装量,平均板重等。
文件名称物料平衡及产品收率管理规程文件编码SMP-P-G012-00 5.1.1.4.由于有收集不到的废品量,以及平均装量的局限性,因此物料平衡有一
定的范围,平衡率的范围在工艺规程中明确规定。
5.2.成品收率的计算:(成品数量+取样量)/投料量×100%,计算时,必须将
相关单位进行换算。
5.3.每批产品应在生产作业完成后,作物料平衡检查。
做物料平衡的岗位有:
粉碎岗位、称量配料岗位、总混岗位、压片岗位、胶囊充填岗位、包装岗位、分装岗位等。
6.培训:
6.1.培训时间:0.5小时
6.2.培训部门:生产部
6.3.受训人员:生产部全体人员、QA检查员。