活塞杆的机械加工工艺规程
活塞杆加工工艺

17.精磨
13.镀后半精磨
12.磨小头
21.磨小头 22.镀后半精磨 23.镀后精磨24.镀后抛光 14.镀后精磨
15.镀后抛光
25.外观检验
16.外观检验
国产加工流程
意大利加工流程
各工序的加工工艺
1、下料:
各工序的加工工艺
1、下料:
★材料领用是关键: 根据生产计划,领取相对应的产品所需原材料的
单,但需注意的问题较多: 1.钢号容易领错误; 2.规格型号容易看错; 3.长度容易出现忽长忽短; 4.端面容易出现斜面大; 5.容易出2、淬前校磨:
活塞杆的加工工艺
因时间关系, 暂讲到这里
活塞杆的加工工艺
谢谢!
活塞杆加工工艺流程
主讲:朱红远
2019年3月
内容说明
活塞杆在减振器的重要性 活塞杆的种类及型号 活塞杆的制作流程 分讲各工序的加工方法,使用设备、 量检具及质量问题点
活塞杆在减振器中的重要性
1.起着联接作用 2.活塞杆失效模式: ⑴.配合尺寸失效时影响装配、异响 ⑵.表面缺陷(划伤、斑点、材料缺陷等)造成的 漏油 ⑶.表面粗糙的不合格,造成漏油 ⑷.活塞杆断裂,后果严重
各工序的加工工艺
使用量具: 下料工序是活塞杆加工工序最简单的工序,控制的尺寸
的也非常单一,就是一个总长; 使用量具就是一个0-500的游标卡尺。 要会使用游标卡尺 使用工装:
剪切模:要定期鉴定(6个月),检查刀块的磨损 程度 磨损后对会加大产品断面的不平整度。
各工序的加工工艺
下料工序的总结: 下料工序是活塞杆加工工序最简单的工序,虽然看似简
⑵、调整定位:根据产品的要求,设定定位装置(最容易出现 因长短定错造成批量报废)
活塞杆加工工艺说明书

活塞杆加工工艺说明书
活塞杆是内燃机中的重要零部件之一,它承受着往复运动时的巨大冲击力和复杂的摩擦力,因此加工工艺的好坏直接影响着活塞杆的使用寿命和性能。
下面将为您介绍活塞杆加工的工艺说明书。
一、材料选择
活塞杆的材料要求比较高,一般选用高品质的合金钢或不锈钢材料,这些材料具有高强度、高耐磨性、高耐腐蚀性和良好的韧性等优点。
二、车削加工
活塞杆的车削加工是其主要的加工工艺之一,其目的是为了保证活塞杆的精度和平滑度。
首先需要在车床上进行粗车,根据活塞杆的尺寸和要求进行车削,要求车削顺序、深度、切削速度和切削深度等参数合理,确保加工精度和表面质量。
三、磨削加工
在车削加工的基础上,还需要进行磨削加工,以提高加工精度和表面平滑度。
磨削工艺一般采用球墨铸铁磨轮,磨削前需进行准备工作,如清洗、校准、结构调整等,以确保磨削的精度和效果。
四、热处理
活塞杆在加工完成后还需要进行热处理,目的是为了消除内部应
力和提高杆的硬度、耐磨性和耐腐蚀性。
热处理方法一般采用淬火加
温处理,加热温度、保温时间、淬火介质和淬火温度等参数需要精确
控制,以确保处理后的活塞杆性能稳定。
五、检验质量
加工完成后的活塞杆需要进行质量检验,检验项目包括尺寸精度、表面平滑度、硬度和耐磨性等指标,以确保产品质量符合标准和要求。
一般采用量具、显微镜、硬度计和摩擦试验机等检测设备进行检验。
在活塞杆加工中,要注意机器设备的维护保养和操作规范,选材、加工和处理要严格按照要求执行,以确保生产出具有优良性能和寿命
长久的活塞杆。
活塞杆的机械加工工艺规程

1.活塞杆的工艺性分析1.1零件图样的分析mm×770mm自身圆度公差为0.005mm。
(1)φ500-025.0mm中心线的同轴度公差为φ0.05mm。
(2)左端M39×2-6g螺纹与活塞杆φ500.0025-mm中心线的同轴度公差为φ0.02mm。
(3)1:20圆锥面轴心线与活塞杆φ500-.0025(4)1:20圆锥面自身圆跳动公差为0.005mm。
(5)1:20圆锥面涂色检查,接触面积不小于80%。
mm×770mm表面渗氮,渗氮层深度0.2~0.3mm,表面硬度62~65HRC。
(6)φ500-025.0材料38CrMoALA是常用的渗氮处理用钢。
1.2零件的工艺分析(1)活塞杆在正常使用中,承受交变载荷作用,φ500mm×770mm处有密封装置往-025.0复摩擦其表面,所以该处要求硬度高又耐磨。
mm×770mm部分经过调质处理和表面渗氮后,芯活塞杆采用38CrMoALA材料,φ500-.0025部硬度为28~32HRC,表面渗氮层深度0.2~0.3mm,表面硬度为62~65HRC。
这样使活塞杆既有一定的韧性,又具有较好的耐磨性。
(2)活塞杆结构比较简单,但长径比很大,属于细长轴类零件,刚性较差,为了保证加工精度,在车削时要粗车、精车分开,而且粗、精车一律使用跟刀架,以减少加工时工件的变形,在加工两端螺纹时要使用中心架。
(3)在选择定位基准时,为了保证零件同轴度公差及各部分的相互位置精度,所有的加工工序均采用两中心孔定位,符合基准统一原则。
(4)磨削外圆表面时,工件易产生让刀、弹性变形,影响活塞杆的精度。
因此,在加工时应修研中心孔,并保证中心孔的清洁,中心孔与顶尖间松紧程度要适宜,并保证良好的润滑。
砂轮一般选择:磨料白刚玉 (WA),粒度60#,硬度中软或中、陶瓷结合剂,另外砂轮宽度应选窄些,以减小径向磨削力,加工时注意磨削用量的选择,尤其磨削深度要小。
活塞杆加工工艺
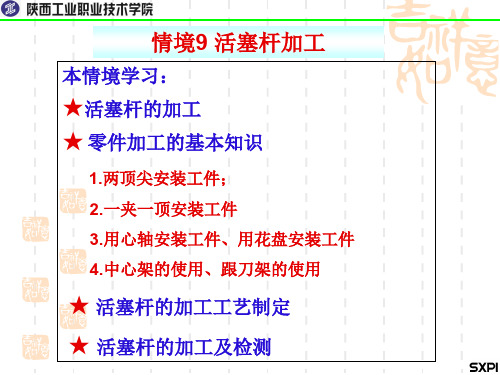
1.开机运行 2.正确安装零件 3.正确安装刀具 4.正确调整机床 5.零件试切 6.打扫机床
视频
9-5 零件的检查
在检验工件之前回答下列问题: •根据图样和检测要求确定所需要的量具和检具 •怎样游标卡尺进行测量 •怎样安装工件
9-6 零件加工的评估总结
1.细长轴加工的特点 2.怎样加紧工件 3.如何选择机床附件 4.加工应该注意的问题
8 用花盘安装工件
图图99.9.9
9-2 零件加工的基础知识
9 在花盘弯板安装工件
图9.10
视频
9-3 零件加工的工序卡
零件工序卡
9-4 零件的加工实施
生产准备:接受工作任务,领取图样,工艺,刀具,工装量具,检查 毛坯的质量
工件加工:能按图样加工出产品,产品应该符合尺寸精度,形位 精度,表面精度要求,能用量具检验质量
图9.3
9-2 零件加工的基础知识
活塞的机械加工工艺规程设计
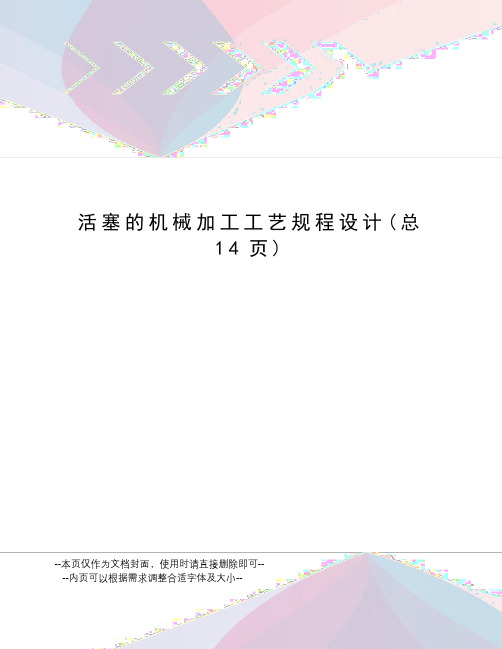
活塞的机械加工工艺规程设计(总14页)--本页仅作为文档封面,使用时请直接删除即可----内页可以根据需求调整合适字体及大小--目录1.零件的分析 (1)零件的作用 (1).零件的工艺分析及其技术要求 (1)2.工艺规程设计 (3). 确定毛坯的制造形式及毛坯尺寸确定的 (3). 基面的选择 (4). 制定工艺路线 (5). 机械加工余量、工序尺寸 (6). 确定切削用量及基本工时 (8)总结 (13)参考文献 (14)1.零件的分析零件的作用活塞是曲柄连杆机构中的重要零件之一,是发动机的心脏,它主要有三个作用。
第一是使发动机作功;第二是密封,它能使发动机内活塞顶以上的空间保持密封,使发动机能连续工作;第三是传热,它能将发动机点燃爆发时的高温传给气缸,再由气缸壁外侧水套内的循环水将热量带走。
.零件的工艺分析及其技术要求图1-1零件图零件的工艺分析1)时效处理是为了消除铸件的内应力,第二次时效处理是为了消除粗加工和铸件残余应力。
以保证加工质量。
2)活塞环槽的加工,分粗加工和精加工,这样可以减少切削力对环形槽尺寸的影响,以保证加工质量。
3)活塞环槽的加工,装夹方法可采用心轴,在批量时可提高生产效率,保证质量。
4)活塞环槽mm 02.008+尺寸检验,采用片塞规进行检查,片塞规分为通端和止端两种。
片塞规具有综合检测功能,即能检查尺寸精度,同时也可以检查环槽两面是否平行,如不平行,片塞规在环槽内不能平滑移动。
5)活塞环侧面与mm 034.0080+Φ轴心线的垂直度检验,可采用心轴装夹工件,再将心轴装夹在两顶尖之间,这时转动心轴,用杠杆百分表测每一环槽的两个侧面,所测读数最大与最小差值,即为垂直度误差。
6)活塞外圆008.0134-Φmm 与034.0080+Φmm 轴心线的同轴度检验,可采用心轴装夹工件,再将心轴装夹在两顶尖之间,这时转动心轴,用百分表测出活塞外圆跳动的读数最大与最小差值,即为同轴度误差。
活塞杆加工工艺流程

活塞杆加工工艺流程
《活塞杆加工工艺流程》
活塞杆是内燃机中的重要零部件,其加工工艺流程对于活塞杆的质量和性能有着至关重要的影响。
在活塞杆的加工过程中,需要经历多道工序和严格的工艺要求。
首先,活塞杆的原材料需要经过初步的加工,包括锻造、热处理等工艺,以保证其材料的均匀性和机械性能的稳定。
接下来,需要进行粗加工,将原材料切割成标准的尺寸,并进行车削等工艺,以确保其外形的精确度。
随后,进行精密加工,包括外圆磨削、内孔加工等工序,以确保活塞杆的尺寸精度和表面粗糙度符合工艺要求。
同时,还需要进行表面处理,例如镀铬、喷涂等工艺,来提高活塞杆的耐磨性和抗腐蚀性能。
在加工过程中,需要严格控制各道工序的工艺参数,包括切削速度、切削深度、刀具选择等,以确保加工质量和效率。
而且,还需要对加工过程中的温度、振动等因素进行监测和控制,以保证活塞杆在加工过程中不会产生裂纹或变形。
总的来说,活塞杆的加工工艺流程需要严格执行,确保每道工序都符合要求,才能生产出高质量的活塞杆产品。
这样不仅能够保证内燃机的性能和可靠性,也能够提高产品的市场竞争力。
活塞杆加工实用工艺要求规范
实用文档xxxx有限公司文件名称:活塞杆加工工艺规范文件编号:GY03-14-2015文件签章有效/受控状态:编制 : 技术工艺科审核:审批:修改记录单版本时间简述A 2015年2月活塞杆加工工艺规范1 引用标准GB/T1800.4-99 孔、轴的极限偏差表 GB/T1801-99 公差配合的选择 GB/T1184-96 形位公差值GB/T1031-95 表面粗糙参数及其数值 厂标等效JB/Z307 GB/T193-81 GB/T196-81 GB/T5786.2-86 GB/T5796.3-86 GB/T6403.5-86 GB/T145-89 GB200-89 GB699-1999 GB908-87 GB/T3-79JB/ZQ0138-80 金属切削加工工艺守则 普通螺纹直径与螺距系列 梯形螺纹基本尺寸 普通螺纹直径与螺距系列 梯形螺纹基本尺寸 砂轮越程槽 中心孔 碳素结构钢 优质碳素结构钢 锻制圆钢和方钢规格普通螺纹的收尾、兼距、退刀槽和倒角单线梯形螺纹的收尾、退刀槽和倒角尺寸2 需用设备(1)100t 开式油压机(2)校直用一组支承滚轮、划针盘、直尺 (3)乙炔氧气加热器 (4)卧式车床C6163,长8m (5)手工交流焊机 (6) 热处理(回火)设备(7) 砂带磨头、外圆磨床、砂盘抛磨头 (8)螺纹检验用环、塞规 3 适用范围本工艺守则适用于加工液压启闭机活塞杆、柱塞杆及部分工业液压缸的活塞杆。
4 活塞杆类型基本有三种4.1 实心活塞杆,见图4.14.2中空型活塞杆由杆头、杆身(无缝管)、杆尾组焊而成,见图4.24.3中空带进油管的活塞杆,见图4.3由杆头、杆身、杆尾及内进油管组焊而成。
将4.2、4.3两种活塞杆称为组合活塞杆图4.1图4.2图4.35 备料及毛坯制作5.1 活塞杆常用材料有45#、35#及40Cr,通常情况下,45#、35#是正火态供货。
具体按设计要求。
5.2毛坯余量的确定选用确定活塞杆坯料余量,应根据其长径比、坯料状态(热轧圆钢,锻圆)通常情况热轧圆钢直径余量6~12mm,长度余量5~10mm。
活塞零件的机械加工工艺规程
活塞零件的机械加工工艺规程活塞是内燃机的重要部件之一,其机械加工工艺规程对于活塞的质量和性能具有重要影响。
下面将从活塞零件的材料选择、加工工艺流程、加工设备和工具选择等方面介绍活塞零件的机械加工工艺规程。
一、材料选择活塞零件的材料通常采用高强度铝合金,如Al-Si-Cu-Mg系列铝合金。
在选择材料时,应考虑到材料的强度、硬度、耐磨性、耐腐蚀性等因素,同时还要考虑到材料的可加工性和成本等因素。
二、加工工艺流程活塞零件的加工工艺流程通常包括以下几个步骤:1. 铸造成型:将铝合金熔化后,通过铸造成型的方式制造出活塞的初步形状。
2. 粗加工:将铸造成型后的活塞进行粗加工,包括车削、铣削、钻孔等工艺,以达到初步的尺寸和形状要求。
3. 热处理:将粗加工后的活塞进行热处理,以提高其强度和硬度等性能。
4. 精加工:将经过热处理的活塞进行精加工,包括车削、磨削、抛光等工艺,以达到最终的尺寸和形状要求。
5. 表面处理:对精加工后的活塞进行表面处理,包括喷涂、阳极氧化等工艺,以提高其耐磨性和耐腐蚀性等性能。
三、加工设备和工具选择1. 车床:活塞的车削加工通常采用数控车床进行,以保证加工精度和效率。
2. 铣床:活塞的铣削加工通常采用数控铣床进行,以保证加工精度和效率。
3. 磨床:活塞的磨削加工通常采用内圆磨床和平面磨床进行,以保证加工精度和表面质量。
4. 刀具:活塞的加工刀具通常采用硬质合金刀具和陶瓷刀具等高硬度刀具,以保证切削效率和切削质量。
总之,活塞零件的机械加工工艺规程对于活塞的质量和性能具有重要影响。
在加工过程中,应根据活塞零件的材料特性和加工要求,选择合适的加工工艺流程、加工设备和工具,以保证活塞的加工质量和性能。
活塞杆加工工艺规范
活塞杆加工工艺规范Newly compiled on November 23, 2020xxxx 有限公司文件名称:活塞杆加工工艺规范 文件编号:GY03-14-2015 文件签章有效/受控状态: 编 制 : 技术工艺科 审 核:审 批:活塞杆加工工艺规范1 引用标准GB/ 孔、轴的极限偏差表 GB/T1801-99 公差配合的选择 GB/T1184-96 形位公差值GB/T1031-95 表面粗糙参数及其数值 厂标等效JB/Z307 GB/T193-81 GB/T196-81 GB/ GB/ GB/ GB/T145-89 金属切削加工工艺守则 普通螺纹直径与螺距系列 梯形螺纹基本尺寸 普通螺纹直径与螺距系列 梯形螺纹基本尺寸 砂轮越程槽 中心孔GB200-89 GB699-1999 GB908-87 GB/T3-79JB/ZQ0138-80 碳素结构钢 优质碳素结构钢 锻制圆钢和方钢规格普通螺纹的收尾、兼距、退刀槽和倒角单线梯形螺纹的收尾、退刀槽和倒角尺寸 2 需用设备(1)100t 开式油压机(2)校直用一组支承滚轮、划针盘、直尺 (3)乙炔氧气加热器 (4)卧式车床C6163,长8m (5)手工交流焊机 (6) 热处理(回火)设备(7) 砂带磨头、外圆磨床、砂盘抛磨头 (8)螺纹检验用环、塞规 3 适用范围本工艺守则适用于加工液压启闭机活塞杆、柱塞杆及部分工业液压缸的活塞杆。
4 活塞杆类型基本有三种实心活塞杆,见图 中空型活塞杆由杆头、杆身(无缝管)、杆尾组焊而成,见图 中空带进油管的活塞杆,见图由杆头、杆身、杆尾及内进油管组焊而成。
将、两种活塞杆称为组合活塞杆图 图 图5 备料及毛坯制作活塞杆常用材料有45#、35#及40Cr ,通常情况下,45#、35#是正火态供货。
具体按设计要求。
毛坯余量的确定选用确定活塞杆坯料余量,应根据其长径比、坯料状态(热轧圆钢,锻圆)通常情况热轧圆钢直径余量6~12mm,长度余量5~10mm。
介绍活塞杆的机械加工工艺
介绍活塞杆的机械加工工艺大家都知道,活塞杆是我们日常应用于气缸运动执行部件中的一个零件,它是支持活塞做功的一个连接部件。
如果我们是在正常的情况下,进行使用活塞杆的话,其活塞杆就可以起到一个承载交变载荷的作用,从而提高配合性质。
因此活塞杆对于加工方面的要求比较高。
那么您知道活塞杆是怎么进行加工的吗?下面佛山欧贝特活塞杆技术人员为大家介绍一下活塞杆的机械加工工艺。
现在就以上的活塞杆图纸为例,来为大家介绍一下活塞杆机械加工工艺:1、下料:佛山欧贝特活塞杆机械加工工艺过程的第一步骤就是下料,需下棒料φ80mm×760mm 。
在下料时需要用到锯床这个工艺设备。
2、锻造:将棒料自由锻成φ62mm×1150mm。
3、热处理:即进行退火,退火是一种金属热处理工艺。
4、划线:划两端中心孔线。
5 、钳工:钻两端中心孔B2.5。
6 、粗车:在粗车时就先夹一端,顶尖顶另一端,然后再将粗车外圆至φ55mm。
7 、粗车:倒头装夹工件时,需顶另一端中心孔,车外圆至φ55mm接工序6加工处。
8 、热处理:在这个热处理中,主要指的是调质处理,我们需要把调质处理28~32HRC。
9、粗车:夹一端,中心架支承另一端,然后切下右端6mm做试片,进行金相组织检查,端面车平,钻中心孔B2.5 。
10、粗车:在倒头装夹工作时,则需要用中心架支撑另一端,车端面,保证总长1090mm,钻中心孔B2.5 。
11、精车:两顶尖装夹工作,车工件右端M39×2-6g,长60mm,直径方向留加工余量1mm,车φ500025.0-mm×770mm时,要使用跟刀架,保证1:20的锥度并留有加工余量1mm 。
12 、精车:倒头两顶尖装夹工件,车另一端(左端)各部及螺纹M39×2-6g,长度100mm,直径方向留加工余量1mm,六方处外径车至φ48mm,并车六方与φ500025.0-mm连接的锥度。
13、磨:主要修研两中心孔。
- 1、下载文档前请自行甄别文档内容的完整性,平台不提供额外的编辑、内容补充、找答案等附加服务。
- 2、"仅部分预览"的文档,不可在线预览部分如存在完整性等问题,可反馈申请退款(可完整预览的文档不适用该条件!)。
- 3、如文档侵犯您的权益,请联系客服反馈,我们会尽快为您处理(人工客服工作时间:9:00-18:30)。
活塞杆的机械加工工艺规程-标准化文件发布号:(9456-EUATWK-MWUB-WUNN-INNUL-DDQTY-KII1.活塞杆的工艺性分析1.1零件图样的分析mm×770mm自身圆度公差为0.005mm。
(1)φ500-025.0mm中心线的同轴度公差为φ0.05mm。
(2)左端M39×2-6g螺纹与活塞杆φ500.0025-mm中心线的同轴度公差为φ0.02mm。
(3)1:20圆锥面轴心线与活塞杆φ500-025.0(4)1:20圆锥面自身圆跳动公差为0.005mm。
(5)1:20圆锥面涂色检查,接触面积不小于80%。
(6)φ500mm×770mm表面渗氮,渗氮层深度0.2~0.3mm,表面硬度62~65HRC。
-.0025材料38CrMoALA是常用的渗氮处理用钢。
1.2零件的工艺分析mm×770mm处有密封装(1)活塞杆在正常使用中,承受交变载荷作用,φ500025-.0置往复摩擦其表面,所以该处要求硬度高又耐磨。
活塞杆采用38CrMoALA材料,φ500mm×770mm部分经过调质处理和表面渗氮-025.0后,芯部硬度为28~32HRC,表面渗氮层深度0.2~0.3mm,表面硬度为62~65HRC。
这样使活塞杆既有一定的韧性,又具有较好的耐磨性。
(2)活塞杆结构比较简单,但长径比很大,属于细长轴类零件,刚性较差,为了保证加工精度,在车削时要粗车、精车分开,而且粗、精车一律使用跟刀架,以减少加工时工件的变形,在加工两端螺纹时要使用中心架。
(3)在选择定位基准时,为了保证零件同轴度公差及各部分的相互位置精度,所有的加工工序均采用两中心孔定位,符合基准统一原则。
(4)磨削外圆表面时,工件易产生让刀、弹性变形,影响活塞杆的精度。
因此,在加工时应修研中心孔,并保证中心孔的清洁,中心孔与顶尖间松紧程度要适宜,并保证良好的润滑。
砂轮一般选择:磨料白刚玉 (WA),粒度60#,硬度中软或中、陶瓷结合剂,另外砂轮宽度应选窄些,以减小径向磨削力,加工时注意磨削用量的选择,尤其磨削深度要小。
mm×770mm外圆和1:20锥度时,两道工序必须分开进行。
在磨(5)在磨削φ500025-.0削1:20锥度时,要先磨削试件,检查试件合格后才能正式磨削工件。
1:20圆锥面的检查,是用标准的1:20环规涂色检查,其接触面应不少于80%。
(6)为了保证活塞杆加工精度的稳定性,在加工的全过程中不允许人工校直。
(7)渗氮处理时,螺纹部分等应采取保护装置进行保护。
1.3审查零件的结构工艺性(1)结构力求简单、对称,横截面尺寸不应该有突然地变化。
(2)应有合理的模面和圆角半径。
(3)38CrMoAlA刚具有良好的锻性和耐磨性。
2.选择毛坯、确定毛坯尺寸、设计毛坯图2.1毛坯的选择因为活塞杆在工作方式是往复运动的形式,为了增加活塞杆的寿命,减小活塞杆的磨损量,因此毛坯选用38CrMoAlA的合金结构钢。
由于生产类型属于成批生产,为了提高生产效率宜采用自由锻方法制造毛坯。
2.2确定毛坯的尺寸公差及机械加工余量(1)公差等级根据零件图各个部分的加工精度要求,锻件的尺寸公差等级为8-12级,加工余量等级为普通级,故取IT=12级。
(2)毛坯基本尺寸由于毛坯的制造方式是自由锻造而成,根据活塞杆零件图的尺寸要求和实际的加工要求,锻造后的尺寸定为:直径62mm、长度1150mm,故查工艺手册,毛坯的尺寸定为:直径80mm、长度760mm。
绘制锻造后零件毛坯图如下:(零件毛坯图)(2)锻造后毛坯加工余量的确定根据上面估算的锻件的质量、形状复杂系数与零件的长度,查表可得单边余量的范围为1.7~2.2mm 。
由于零件为阶梯轴,可以把台阶相差不大的轴的毛坯合成为同一节。
① 对活塞杆1:20的圆锥表面粗糙度0.8µm 的要求,对其加工方案为粗车——精车——粗磨——半精磨——精磨。
查工艺手册得:精磨的加工余量为0.04mm 半精磨的加工余量为0. 06mm,粗磨的加工余量为0.9mm,粗车的加工余量为7mm 。
② 对于活塞杆φ500025.0-mm ×770mm 的外圆表面粗糙度0.4µm 的要求,确定其加工方案为:粗车——精车——粗磨——半精磨——精磨。
由工艺手册查得:精磨的加工余量为0.04mm 半精磨的加工余量为0. 04mm,粗磨的加工余量为0.92mm,精车的加工余量为4mm ,粗车的加工余量为7mm,总的加工余量为12mm 。
精磨后工序的基本尺寸为50,其他各工序的基本尺寸为: 粗车:55+7=62 精车:51+4=55 粗磨:50.08+0.92=51 半粗磨:50.04+0.04=50.08 精磨:50+0.04=50.04 ③对活塞杆两端的螺纹g M 6239-⨯的加工方案都为粗车——精车。
查工艺手册得:粗车的加工余量为7mm,精车的加工余量为15mm ,总的加工余量为22mm 。
3.基准的选择正确选择定位基准是制定机械加工工艺规程和进行夹具设计的关键。
基准的选择是工艺规程设计中的重要问题之一,基准的选择是否合理影响到加工质量,生产率和加工成本。
定位基准的选择合理与否,将直接影响所制定的零件加工工艺规程的质量。
基准选择不当,往往会增加工序,或使工艺路线不合理,或使夹具设计困难,甚至达不到工件的加工精度要求。
定位基准分为粗基准和精基准。
在起使工序中,只能选用未经加工过的毛坯表面作为定位基准,这种基准称为粗基准。
用加工过的表面所作的定位基准称为精基准。
在设计工艺规程的过程中,当根据零件工件图先选择精基准,后选粗基准。
结合整个工艺过程要进行统一考虑,先行工序要为后续工序创造条件。
3.1粗基准的选择粗基准的选择应能保证加工面与非加工面之间的位置精度,合理分配各加工面的余量,为后续工序提供精基准。
所以为了便于定位、装夹和加工,可选轴的外圆表面为定为基准,或用外圆表面和顶尖孔共同作为定为基准。
用外圆表面定位时,因基准面加工和工作装夹都比较方便,一般用卡盘装夹。
为了保证重要表面的粗加工余量小而均匀,应选该表面为粗基准,并且要保证工件加工面与其他不加工表面之间的位置精度。
粗基准采用锻造后的毛坯外圆。
中心孔加工采用三抓自定心卡盘装夹毛坯外圆,车端面、钻中心孔。
一般不能用毛坯外圆装夹两次钻两端中心孔,而应该以毛坯外圆作粗基准,先加工一个端面,钻中心孔,车一端外圆,然后以已车过的外圆作基准,用三抓自定心卡盘装夹,车另一端面,钻中心孔,才能保证两中心孔同轴。
3.2精基准的选择选择精基准时,主要考虑的问题是如何保证零件的加工精度以及安装可靠。
在进行精加工时,应选用已加工表面作为精加工基准。
根据活塞杆的技术要求和装配要求,应选择活塞杆的左右端面和两端面的中心孔作为精基准。
零件上的很多表面都可以以两端面作为基准进行加工。
可避免基准转化误差,也遵循基准统一原则。
两端的中心轴线是设计基准。
选用中心轴线为定为基准,可保证表面最后的加工位置精度,实现了设计基准和工艺基准的重合。
由于两轴面的精加工工序要求余量小且均匀,可利用其自身作为基准。
4.工艺路线的制定制定加工方案的一般原则为:先粗后精,先近后远,先外后内,程序段最少,走刀路线最短以及特殊情况特殊处理。
制定工艺路线要保证加工质量,提高生产效率,降低成本。
根据生产类型是成批生产,零件的几何形状、尺寸精度及位置精度等技术要求,以及加工方法所能达到的经济精度,在生产纲领已4确定的情况下,可以考虑采用专用机床配以专用夹具,并尽量使工序集中来提高生产效率。
除此之外,还应当考虑经济效果,以便使生产成本尽量下降。
4.1划分阶段对精度要求较高的零件,其粗、精加工应该分开,以保证零件的质量。
活塞杆的加工质量要求较高,其中表面粗糙度要求最高为Ra 0.4µm,另外几处圆跳动也有较高的位置精度要求。
精加工方案的确定,将该活塞杆的加工划分为五个阶段:粗车(粗车外圆、端面和钻中心孔等)、精车(精车各处外圆、台阶及次要表面等)、粗磨(粗磨各处外圆)、半精磨、精磨。
4.2工序的集中与分散该活塞杆的生产类型为成批生产,零件的结构复杂程度一般,但有较高的技术要求,可选用工序集中原则安排轴的加工工序。
采用专用机床和部分高生产率专用设备,配用专用夹具,与部分划线法达到精度,以减少工序数目,缩短工艺路线,提高生产效率。
采用工序集中原则,有利于保证各加工面之间的位置精度要求,节省安装工件的时间,减少工件的搬动次数,使生产计划、生产组织工作得到简化,工作装夹次数减少,辅助时间缩短。
4.3加工顺序的安排(1)机械加工工序①按先基准平面后其他的原则:机械加工工艺安排是总是先加工好定位基准面,所以应先安排为后续工序准备好定为基准。
先加工精基准面,转中心孔及车表面的外圆。
②按先粗后精的原则:先安排粗加工工序,后安排精加工工序。
先安排精度要求较高的各主要表面,后安排精加工。
③按先主后次的原则:先加工主要表面,如车外圆各个表面,端面等。
后加工次要表面。
④先外后内,先大后小原则:先加工外圆再以外圆定位加工内孔,加工阶梯外圆时先加工直径较大的后加工直径小的。
⑤次要表面的加工安排:切槽等次要表面的加工通常安排在外圆精车或粗磨之后,精磨外圆之前。
mm×770mm和1:20锥度的加工质量要求较高的表面,安排在后面,并⑥对于φ500025.0在前几道工序中注意形位公差,在加工过程中不断调整、保证其形位公差。
(2)热处理工序的安排在切削加工前宜安排退火处理,其能提高改善轴的硬度,消除毛坯的内应力,改善其切削性能。
在精加工之前进行调质处理,能提高轴的综合性能。
最终热处理安排在半精磨之后精磨加工之前。
其能提高材料强度、表面硬度和耐磨性。
4.4活塞杆工艺路线的确定根据以上的加工工艺过程的分析确定零件的工艺路线如下表所示:5.选择加工设备和工艺装备5.1机床的选择工序1采用锯床工序06.、07、09、10、11、12、16、17采用CW6163车床工序14、15、19、20、23、24采用M1432磨床工序22采用X53K铣床5.2选择夹具该活塞杆的生产纲领是成批生产,所以采用三抓卡盘、双顶尖和铣床专用夹具。
5.3选择刀具在车床上加工的各工序,采用复合中心钻端面车刀和外圆车刀;在铣床上加工的各工序,采用硬质合金铣刀即可保证加工质量。
5.4选择量具和其他加工表面均采用游标卡尺。
对角度尺寸利用专用夹具保证,其他尺寸采用通用量具即可。
6.工序加工余量的确定,工序尺寸及公差的计算(1)活塞杆两端g M 6239-⨯的外圆表面。
其加工路线为粗车——精车。
由工序06、07、11、12组成,据之前查到的加工余量得粗车的加工余量为7mm,精车的加工余量为15mm ,总的加工余量为22mm 。