PFMEA案例
六步法pfmea案例

六步法pfmea案例全文共四篇示例,供读者参考第一篇示例:案例背景:某家汽车零部件制造公司在生产过程中发现了一个频繁出现的问题:某零部件的尺寸偏差过大,导致装配时无法完全契合,进而影响产品的性能和质量。
为了解决这一问题,公司决定使用六步法PFMEA 进行分析和改进。
步骤一:确定分析范围团队确定了分析的范围为某零部件的生产工艺。
他们明确了问题的具体表现,以及对产品性能和质量的影响。
团队还确定了分析的目的是为了找出可能引起零部件尺寸偏差的潜在故障模式,并制定相应的控制措施。
步骤二:收集相关信息团队开始收集相关信息,包括零部件的设计图纸、生产工艺流程、设备参数、材料性质等。
他们还对生产现场进行实地考察,观察生产过程中的关键环节,并与相关工程师和操作人员进行沟通交流,了解他们对问题的认识和看法。
步骤三:识别潜在故障模式通过分析收集到的信息,团队识别出了可能导致零部件尺寸偏差的潜在故障模式。
包括:材料供应质量不稳定、设备操作不规范、工艺参数设置不当等。
每个故障模式都被赋予一个风险等级,以确定其重要性和优先级。
步骤四:确定故障影响团队分析每个故障模式的影响范围,包括对产品性能、质量、交付时间等方面的影响。
他们还评估了每个故障模式的可能性和频率,以确定其潜在风险。
步骤五:制定改进控制措施基于对故障模式和影响的分析,团队制定了一系列改进控制措施,以降低潜在风险。
加强材料供应商管理、优化生产工艺流程、规范设备操作规程等。
每个控制措施都被赋予一个责任人和执行时间表,以确保实施和落实。
步骤六:跟踪和持续改进团队制定了一个跟踪和持续改进计划,以监控改进控制措施的执行情况和效果。
他们定期对实施情况进行评估和审查,继续识别和解决可能存在的风险和问题,确保质量和性能的持续提升。
通过六步法PFMEA的分析和改进,该汽车零部件制造公司成功解决了零部件尺寸偏差的问题,提高了产品的质量和性能,降低了生产过程中的风险和损失,进一步提升了企业的竞争力和市场地位。
PFMEA培训资料
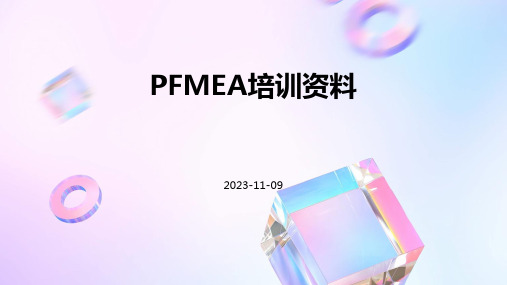
强化风险管理 随着人们对风险管理重视程度的 提高,PFMEA将在未来更加注重 对高风险失效模式的控制和管理 。
扩大应用范围 目前PFMEA主要应用于制造业, 未来可能会扩展到其他领域,如 服务业、医疗保健等。
提供一些实际的PFMEA分析报告案例,以便学员了解 PFMEA分析报告的编写方法和格式,为学员自己编写 PFMEA分析报告提供参考。
感谢您的观看
THANKS
通过服务PFMEA分析,可以识别和评估服 务过程中潜在的故障模式和风险,优化服务 流程,提高客户满意度。
详细描述
服务PFMEA分析是一种在服务设计和实施 阶段对服务过程进行详细分析的质量工具, 通过对服务流程的各个环节进行分析,识别 出潜在的故障模式和风险,评估其对服务过 程的影响程度,制定出有效的改进措施,优 化服务流程,提高客户满意度和忠诚度。
流程分析
总结词
对产品或过程的制造、装配、检测等流程进行详细分析是PFMEA的必要步骤。
详细描述
了解制造、装配、检测等流程中涉及的操作步骤和工艺要求,分析流程中可能出 现的问题和缺陷,以便在后续功能分析和风险分析中针对性地进行预防和改进。
功能分析
总结词
对产品或过程的功能进行分析,明确功能要求和性能指标是 PFMEA的关键步骤。
。
预防措施
预防措施是针对潜在故障模式采增 加防护装置、提高检测频率等。
在PFMEA中,预防措施通常是 在分析阶段确定的,需要综合考 虑设计、制造、使用等多个环节
的风险因素。
改进措施
改进措施是针对已经出现的故 障模式采取的措施,旨在消除 或降低故障的影响。
新版(七步法案例)PFMEA

头下R角偏小 一冲设计不合理 模具制作有偏差 冷墩时光钉直径偏大
5
增加抽风机或空调
2 检查/核对 2
6
要求供应商对模具尺寸进行 中限管理并提供出货检验报
告
3
目视/ 核对/检测
2
6
每隔两个小时对锁紧螺丝紧 固一次
3
检查
2
8
修理模具R角位置
3 检测 2
8
修改一冲相关尺寸
3 检测 2
6
要求供应商对模具尺寸进行 中限管理并提供出货检验报
05 热处理
硬度检测 (维式硬度计)
产品外观及硬度性能符合图纸 目视检测产品外观及仪器检测产品硬度性
要求
能符合图纸要求
电镀后表面发黑
产品从清洗区清除杂质后进入淬火炉进行
渗碳淬火(预热区860℃-60/+20℃,保温
产品表面硬度与芯部硬度需符 区900℃ ±10℃,淬火区 860℃ ±10
合图纸工艺要求:
完成状态
结合经验重新设计一冲模具
2020/3/10 8 2 1 ※ L
完成状态
严格要求模具厂商按我司图纸尺寸制作 2020/3/10 6 2 1
L
我司模具按图纸中限尺寸设计,并要求模具厂 完成状态 商对每批模具进行尺寸检验并提供检验报告到 2020/3/10 7 2 1 ※ L
我司核对
完成状态
要求牙板供应商严格按标准要求设计牙板并提 供检测数据报告
提供检测报告
对
高成
2020/3/10
要求牙板供应商严格按标准要求设计牙板
目视/核 对
董茂文
2020/3/10
将主模模腔尺寸定义在中限并要求供应商 目视/核
PFMEA-失效模式分析

02
失效模式分析
失效模式定义
失效模式定义
01
失效模式是指产品或过程中可能出现的不满足设计意图、技术
要求或操作规范的状或现象。
失效模式分类
02
根据失效的性质和影响程度,失效模式可以分为功能失效、性
能失效、安全失效、适应性失效等类型。
失效模式分析方法
03
失效模式分析方法包括故障树分析、事件树分析、故障模式与
制定改进措施和预防措施
01
根据分析结果,制定针对性的改进措施,以提高产品或过程的 性能、安全性和可靠性。
02
制定预防措施,降低失效模式的发生风险,包括设计优化、工
艺改进、环境控制和使用指导等。
跟踪改进措施和预防措施的实施效果,持续改进,确保产品质
03
量和过程稳定。
04
PFMEA案例分析
案例一:汽车刹车系统PFMEA分析
识别关键特性,确定分析的重点,确 保分析的准确性和有效性。
列出潜在的失效模式
通过头脑风暴、历史数据分析和经验总结等方法,列出可能的失效模式,确保覆盖全面。
对失效模式进行分类和整理,以便后续分析。
分析失效模式的后果
分析失效模式对产品或过程性能、安 全性、可靠性和符合性等方面的影响 。
评估失效模式对客户满意度和生产成 本的影响,以便制定有效的改进措施 。
主观性
在评估失效模式的严重程度、发生频率和检测难度时,可能存在 主观性,导致结果的不一致。
静态性
PFMEA通常在产品开发阶段进行,而后期的更改和改进可能未 被考虑。
PFMEA未来发展方向
人工智能与机器学习应用
利用人工智能和机器学习技术辅助PFMEA分析,提高识别失效模式 的准确性和效率。
PFMEA分析范例
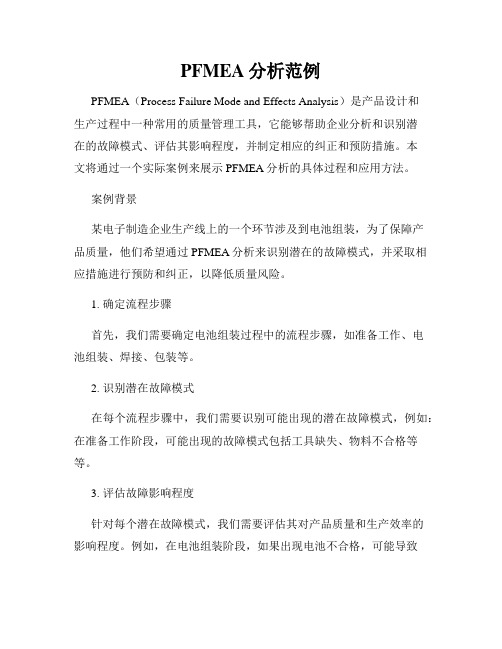
PFMEA分析范例PFMEA(Process Failure Mode and Effects Analysis)是产品设计和生产过程中一种常用的质量管理工具,它能够帮助企业分析和识别潜在的故障模式、评估其影响程度,并制定相应的纠正和预防措施。
本文将通过一个实际案例来展示PFMEA分析的具体过程和应用方法。
案例背景某电子制造企业生产线上的一个环节涉及到电池组装,为了保障产品质量,他们希望通过PFMEA分析来识别潜在的故障模式,并采取相应措施进行预防和纠正,以降低质量风险。
1. 确定流程步骤首先,我们需要确定电池组装过程中的流程步骤,如准备工作、电池组装、焊接、包装等。
2. 识别潜在故障模式在每个流程步骤中,我们需要识别可能出现的潜在故障模式,例如:在准备工作阶段,可能出现的故障模式包括工具缺失、物料不合格等等。
3. 评估故障影响程度针对每个潜在故障模式,我们需要评估其对产品质量和生产效率的影响程度。
例如,在电池组装阶段,如果出现电池不合格,可能导致产品连接不可靠,影响产品性能,同时还会增加后续检测和返工的工作量。
4. 确定风险等级结合故障模式的影响程度,我们可以根据一定的评估标准来确定每个故障模式的风险等级。
例如,可以设定高、中、低三个等级,将电池不合格列为高风险等级。
5. 制定预防和纠正措施对于高风险等级的故障模式,我们需要制定相应的预防和纠正措施,以降低潜在风险。
例如,对于电池不合格的风险,可以建立严格的供应商管理制度,提高物料检测的精度和效率。
6. 实施和跟踪制定好预防和纠正措施后,我们需要将其纳入到生产实践中,并建立相应的跟踪机制,及时评估其实施效果,并根据需要对措施进行调整和改进。
通过以上几个步骤的分析和实施,电子制造企业可以在电池组装过程中减少故障发生的概率,并及时采取纠正措施,以确保产品质量和生产效率的稳定性和可持续性。
总结PFMEA作为一种常用的质量管理工具,可以帮助企业在产品设计和生产过程中识别潜在故障模式,并制定相应的预防和纠正措施。
pfmea优秀案例
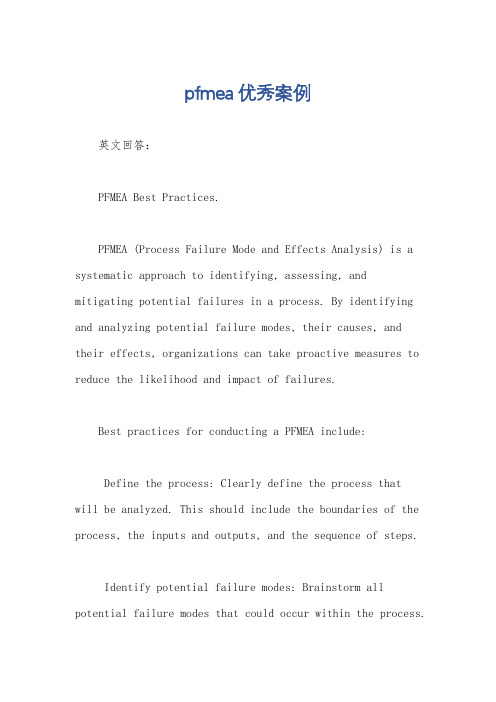
pfmea优秀案例英文回答:PFMEA Best Practices.PFMEA (Process Failure Mode and Effects Analysis) is a systematic approach to identifying, assessing, andmitigating potential failures in a process. By identifying and analyzing potential failure modes, their causes, and their effects, organizations can take proactive measures to reduce the likelihood and impact of failures.Best practices for conducting a PFMEA include:Define the process: Clearly define the process thatwill be analyzed. This should include the boundaries of the process, the inputs and outputs, and the sequence of steps.Identify potential failure modes: Brainstorm all potential failure modes that could occur within the process.This should be done by considering all aspects of the process, including equipment, materials, people, and procedures.Analyze the causes of failure modes: For each failure mode, identify the potential causes. These causes should be specific and actionable.Assess the effects of failure modes: Determine the potential effects of each failure mode. This should include both the immediate effects on the process and the ultimate effects on the customer or end user.Assign risk priority numbers (RPNs): Assign an RPN to each failure mode based on its severity, occurrence, and detectability. The RPN helps prioritize failure modes for mitigation.Develop mitigation strategies: For each failure mode with a high RPN, develop mitigation strategies to reduce the likelihood and impact of the failure. These strategies should be specific and actionable.Implement mitigation strategies: Implement the mitigation strategies that have been developed. This may involve making changes to the process, equipment, materials, people, or procedures.Monitor and evaluate the effectiveness of mitigation strategies: Monitor the effectiveness of the mitigation strategies that have been implemented. This may involve tracking the occurrence of failure modes and assessing the impact of the mitigation strategies.By following these best practices, organizations can improve the effectiveness of their PFMEA process and reduce the likelihood and impact of failures.中文回答:PFMEA优秀案例。
挤出PFMEA第四版实例
挤出PFMEA第四版实例一、本文概述1、PFMEA的定义和重要性PFMEA,即过程失效模式与影响分析,是一种用于评估制造过程中潜在失效模式的工具。
它帮助我们识别、评估和排序潜在的制造过程缺陷,以便在生产之前采取预防措施,从而提高产品质量、降低成本并减少交货期延误。
PFMEA的核心价值在于它能够系统地分析制造过程中的潜在风险,并量化这些风险对最终产品质量的影响。
通过这种方式,我们可以提前发现潜在问题,并在产品设计和制造过程中采取有效的纠正措施。
在汽车制造、电子设备、医疗器械和其他高风险领域,PFMEA已经成为质量管理和持续改进的重要组成部分。
它不仅有助于提高产品质量,还为组织提供了一种实用的工具,以识别和解决潜在的制造过程问题,从而提高生产效率、降低成本并增强市场竞争力。
总之,PFMEA是一种重要的质量管理工具,能够识别和评估制造过程中的潜在失效模式,从而采取预防措施,提高产品质量、降低成本并减少交货期延误。
在未来,随着生产过程日益复杂化和客户需求多样化,PFMEA的重要性将进一步提升。
2、PFMEA的历史和发展PFMEA(Process Flure Mode and Effects Analysis)是一种用于评估和改善制造业过程中潜在失效模式的工具。
自1960年代初期以来,PFMEA已经被广泛应用于各种行业,并且已经成为许多质量和安全标准的要求。
最初的PFMEA方法是在1960年代初期由美国宇航局(NASA)开发的。
当时,NASA正在开发一套新的宇宙飞船系统,他们需要一种可靠的方法来确保制造过程中的质量和安全性。
于是,PFMEA作为一种特殊的故障模式分析方法,能够系统地识别和评估生产过程中潜在的失效模式及其影响。
随着时间的推移,PFMEA逐渐在汽车、电子、医疗和其他制造业中得到广泛应用。
到了1980年代,PFMEA已经成为ISO质量管理体系(ISO 9000)的一部分,并且被广泛接受为行业标准。
新版pfmea七步法案例
新版pfmea七步法案例PFMEA,即“潜在模式与影响分析”,是一种系统性的、定量化的分析方法,用于识别和评估产品或过程潜在的问题和风险,并采取措施控制这些风险。
新版PFMEA七步法是一种基于RPN值(风险优先数)进行优化改进的方法,以下是一个新版PFMEA七步法的案例分析:一、确定相关方和寻找案例在这个案例中,我们将会分析一家假发生产公司的生产过程中的潜在模式与影响。
假发是这个公司的主要产品,主要销售给癌症患者和脱发患者等,因此产品质量要求非常高。
我们将会分析该公司的生产过程,以识别可能存在的问题和风险。
二、制定团队和设立目标我们将会成立一个由生产部门、质量部门和销售部门代表组成的团队,来共同完成这个任务。
我们的目标是找出所有可能存在的问题和风险,并针对每个风险制定控制策略,以降低其风险。
三、绘制流程图和逐步分析我们将会绘制一张该公司假发生产的全程流程图,每一个生产步骤都将会被详细描述。
我们将会对每个生产步骤进行逐步分析,以识别可能存在的问题和风险,包括机器故障、材料缺陷、操作不当等等。
四、评估风险严重程度我们将根据RPN 值来评估每个风险的严重程度。
RPN 值根据三个因素计算出来:发生的概率、可能的影响和检测的能力。
我们将会为每个可能存在的风险计算RPN 值,并按照此数值对每个风险进行排序。
我们将把RPN 值高于100 的所有风险作为紧急问题来对待。
五、确定控制措施和负责人我们将为每个评级高的风险制定控制措施,并确定控制措施的执行者、实施时间和监督人员。
这些措施可能包括调整制造过程、提高质检要求、增加维护保养频率、教育员工如何正确操作、规范化标准工艺等等。
六、执行和跟踪控制措施我们将严格执行控制措施并按时完成项目,同时跟踪每个控制措施的效果和改进情况。
我们将进行定期的审核和改进,以保证控制措施的持续有效性。
七、更新和维护PFMEA表我们将定期更新和维护我们的PFMEA表,并将其作为质量管理的一项重要工具。
PFMEA案例(2[1].2)
工序号及 加工内容
潜在失效 模式
潜在失 效后果
分 类
潜在失效起 因/机理
频 度 O
R P N
现行控 制措施
建议措施
采取措 施
严 重 度
频 度
探 测 度
R P N
P007 装配
内弧板与 其他弧板 不一致
排壳排 链器无 法在炮 箱上锁 紧
8
零件一致性 差,装配基 准不一致
8
3
19 2
装配前 进行检 查
装配前对 零件进行 检查,统 一装配基 准
排壳排链器工艺潜在失效模式及后果(PFMEA)分析(机加)
措施执行结果 工序号及 加工内容
潜在失效 模式
潜在失 效后果
严 重 度 S
分 类
潜在失效起 因/机理
频 度 O
探 测 度 D
R P N
现行控 制措施
建议措施
责任 和目 标完 成日 期
采取措 施
严 重 度
频 度
探 测 度
R P N
P003 钻/ 钻,扩, 铰孔 φ28+0.21 0, φ29+0.21 0。
增加工序 6A,进行 油压机压 装;指定 专门人员 加工;压 装严格压 力和时间。 增加高精 度设备, 定员,定 机,定切 削。
221车间 2004.01
8
2
2
32
P014/镗/ 镗内孔, 保证尺寸 ,形状公 差和表面 粗糙度要 求。
①尺寸及 形置公差 超差。
后续工序 加工余量 不够。
7
G
①机床精度低。 ②切削速度不 匹配。 ③刀、量具使 用不对。
8
3
19 2
工人现 场控制
PFMEA 过程失效模式及后果分析
PFMEA目录简介概念论述原理分析模式及后果分析PFMEA案例分析简介概念论述原理分析模式及后果分析PFMEA案例分析简介过程失效模式及后果分析(Process Failure Mode and Effects Analysis,简称PFMEA)PFMEA是过程失效模式及后果分析的英文简称。
是由负责制造/装配的工程师/小组主要采用的一种分析技术,用以最大限度地保证各种潜在的失效模式及其相关的起因/机理已得到充分的考虑和论述。
概念论述PFMEA是过程失效模式及后果分析(Process Failure Mode and Effects Analysis)的英文简称。
是由负责制造/装配的工程师/小组主要采用的一种分析技术,用以最大限度地保证各种潜在的失效模式及其相关的起因/机理已得到充分的考虑和论述。
失效:在规定条件下(环境、操作、时间),不能完成既定功能或产品参数值和不能维持在规定的上下限之间,以及在工作范围内导致零组件的破裂卡死等损坏现象。
严重度(S):指一给定失效模式最严重的影响后果的级别,是单一的FMEA范围内的相对定级结果。
严重度数值的降低只有通过设计更改或重新设计才能够实现。
频度(O):指某一特定的起因/机理发生的可能发生,描述出现的可能性的级别数具有相对意义,但不是绝对的。
探测度(D):指在零部件离开制造工序或装配之前,利用第二种现行过程控制方法找出失效起因/机理过程缺陷或后序发生的失效模式的可能性的评价指标;或者用第三种过程控制方法找出后序发生的失效模式的可能性的评价指标。
风险优先数(RPN):指严重度数(S)和频度数(O)及不易探测度数(D)三项数字之乘积。
顾客:一般指“最终使用者”,但也可以是随后或下游的制造或装配工序,维修工序或政府法规。
原理分析PFMEA的分析原理PFMEA的分析原理如下表所示,它包括以下几个关键步骤:(1)确定与工艺生产或产品制造过程相关的潜在失效模式与起因;(2)评价失效对产品质量和顾客的潜在影响;(3)找出减少失效发生或失效条件的过程控制变量,并制定纠正和预防措施;(4)编制潜在失效模式分级表,确保严重的失效模式得到优先控制;(5)跟踪控制措施的实施情况,更新失效模式分级表。
- 1、下载文档前请自行甄别文档内容的完整性,平台不提供额外的编辑、内容补充、找答案等附加服务。
- 2、"仅部分预览"的文档,不可在线预览部分如存在完整性等问题,可反馈申请退款(可完整预览的文档不适用该条件!)。
- 3、如文档侵犯您的权益,请联系客服反馈,我们会尽快为您处理(人工客服工作时间:9:00-18:30)。
4 调节注射压力 作业准备验证,适当调整,并 进行工艺监控 清理模具分型面
调节注射温度
产品不合格
1.原料含水分、溶剂或易挥 发物 2.塑料温度太高或受热时间 长,易降聚或分解 3.注射压力太小
3 原料检验 调节注射压力
4.注射柱塞退回太早
7 A 5.模具温度太低
调节注射温度
6.注射速度快
调节注射速度
7.在料筒加料端混入空气
7 56 2 42
天骏2010-10-22 天骏2010-10-22
6
制品质量符合要பைடு நூலகம்求
凹痕、缩水
7
制品质量符合要 求
水纹
产品不合格
1、流道浇口太小
4
2、塑料件太厚或厚薄不均
3、浇口位置不当
4、注射保压时间太短
调节注射保压时间
7 A 5、加料量不夠
加料量控制
6、料筒温度太高
3
注塑成型
产品缺料
影响产品质量、 制造进度
7
影响产品质量、 制造进度
7
影响外观与装 配,使顾客不满 7
意
A 供应商没有严格控制
1、优先使用顾客认可供应商 2 2. 选择有质量保证能力和良 到货验收
好信誉的供应商
3 42
A
检测及对供方的控制手段不 够
2
1.不定期进行供应商审核2.使 用外部认可实验室进行检测
产品型号错误, 顾客不满意
2
C 包装人员粗心
不良品混入,影 响客户使用
5
C 检验人员操作失误
纸箱变形破损
3 C 纸箱堆积太高
顾客不满意
1 C 仓库计数错误
3 检查、更正 3 检验、及时标记 3 检查、更正 3 检查、更正
2 42
1 21
3 18 4 60 3 27 26
生产部 2010-10-22
质管部 2010-10-22
仓库 2010-10-22
仓库 2010-10-22
编制: FMEA 日期(编制)
日期(修订)
范成迎
2010/6/10
措施的效果
责任及目标完成
日期
SO
D
R.
采取之措施 e c e
P.
vc
t
N.
天骏2010-10-22 天骏2010-10-22
4
制品质量符合要 求
产品飞边
5
制品质量符合要 求
气泡
产品不合格
1、注射压力大 2、锁模力不够 3.模具分型面有异物 2 C 4.塑料温度太高 5.模板变形 6.进料口位置不当
过程潜在失效模式及后果分析 (PFMEA)
类型/部件: 车型年:
核心小组:
设计责任: 关键日期:
RPN DETECT
OCCUR CLASS SEV
项目 设计功能/要求
潜在失效模式
潜在失效后果
失效的潜在原因 /机理
现行设计控制防范
现行设计控制探测
建议措施
1 原材料采购
原材料不合格
2 原材料检验
质量不合格流入
2 料筒及喷嘴温度检查 模具温度检查 加料量检查 选择合适设备应能力 调节注射压力 调节注射速度
调节注射时间 检查喷嘴是否通畅
疏通热流道
8 128 布置适当的排气孔 8 128 流道浇口分布选择
FMEA编号: QR7.1.1-34 FMEA编号: PFMEA-122002.000.00.00
页码: 第 页 共 页
1.核对厂家提供的质量证明2. 按批次对原材料进行进货控制 3.实施周期性检验
3
42
1、料筒及喷嘴温度低 2、模具温度太低 3、加料量不够 4、超过设备注射能力 5、注射压力低 6、注射速度慢 A 7、模穴无适当排气孔 8、流道浇口分布不当 9、注射时间短 10、杂物堵塞喷嘴 11、弹簧喷嘴失灵 12、热流道不通
调节料筒温度
7、注射压力太小
调节注射压力
8、注射速度太慢
调节注射速度
产品不合格
1、料筒温度太低 2、注射压力太小 3、模具温度太低 6 B 4、注射速度太慢 5、流道浇口太小
3 调节料筒温度 调节注射压力 调节模具温度 调节注射速度
8 包装 9 最终检验 10 入库存储 11 出货交付
标签贴错 漏检 纸箱受潮变形 数量不准确