TPM培训材料资料
TPM_培训资料

TPM_培训资料TPM 培训资料一、TPM 简介TPM 即全员生产维护(Total Productive Maintenance),是一种以提高设备综合效率为目标,以全系统的预防维修为过程,全体人员参与为基础的设备保养和维修管理体系。
TPM 的核心目标是通过消除设备故障、降低维修成本、提高生产效率和产品质量,从而实现企业的可持续发展。
它强调的不仅仅是设备的维护和保养,更是一种全员参与、持续改进的管理理念。
二、TPM 的发展历程TPM 起源于 20 世纪 50 年代的美国,当时被称为“事后维修”。
到了20 世纪 60 年代,日本引进了这一理念,并结合自身的实际情况进行了改进和发展,形成了具有日本特色的 TPM 管理模式。
在 20 世纪 70 年代,TPM 开始在日本企业中广泛推广和应用,并取得了显著的成效。
随后,TPM 逐渐传播到世界各地,成为众多企业提升设备管理水平和生产效率的重要手段。
三、TPM 的八大支柱1、自主保全自主保全是指操作人员对自己操作的设备进行日常的清扫、点检、加油、紧固等保养工作。
通过自主保全,操作人员能够更加熟悉设备的性能和运行状况,及时发现并解决问题,从而提高设备的可靠性和稳定性。
2、计划保全计划保全是指由专业的维修人员根据设备的运行状况和故障规律,制定科学合理的维修计划,并按照计划进行定期的维修和保养工作。
计划保全能够有效地预防设备故障的发生,延长设备的使用寿命。
3、个别改善个别改善是指针对设备存在的问题和薄弱环节,组织专门的团队进行深入的分析和研究,制定切实可行的改善方案,并加以实施。
个别改善能够快速有效地解决设备的重大问题,提高设备的性能和效率。
4、品质保全品质保全是指通过设备的维护和保养,确保产品的质量稳定。
它要求在设备的设计、制造、安装、调试、使用和维护等各个环节,都要充分考虑到产品质量的要求,采取有效的措施防止质量问题的发生。
5、初期管理初期管理是指对设备的规划、设计、选型、购置、安装、调试等前期工作进行有效的管理。
TPM培训资料
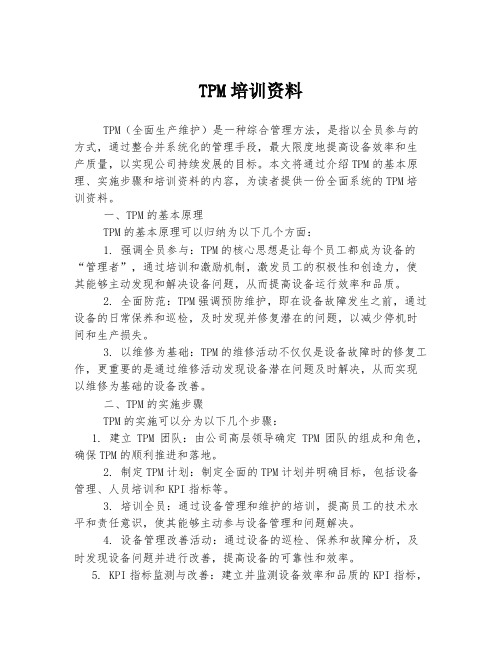
TPM培训资料TPM(全面生产维护)是一种综合管理方法,是指以全员参与的方式,通过整合并系统化的管理手段,最大限度地提高设备效率和生产质量,以实现公司持续发展的目标。
本文将通过介绍TPM的基本原理、实施步骤和培训资料的内容,为读者提供一份全面系统的TPM培训资料。
一、TPM的基本原理TPM的基本原理可以归纳为以下几个方面:1. 强调全员参与:TPM的核心思想是让每个员工都成为设备的“管理者”,通过培训和激励机制,激发员工的积极性和创造力,使其能够主动发现和解决设备问题,从而提高设备运行效率和品质。
2. 全面防范:TPM强调预防维护,即在设备故障发生之前,通过设备的日常保养和巡检,及时发现并修复潜在的问题,以减少停机时间和生产损失。
3. 以维修为基础:TPM的维修活动不仅仅是设备故障时的修复工作,更重要的是通过维修活动发现设备潜在问题及时解决,从而实现以维修为基础的设备改善。
二、TPM的实施步骤TPM的实施可以分为以下几个步骤:1. 建立TPM团队:由公司高层领导确定TPM团队的组成和角色,确保TPM的顺利推进和落地。
2. 制定TPM计划:制定全面的TPM计划并明确目标,包括设备管理、人员培训和KPI指标等。
3. 培训全员:通过设备管理和维护的培训,提高员工的技术水平和责任意识,使其能够主动参与设备管理和问题解决。
4. 设备管理改善活动:通过设备的巡检、保养和故障分析,及时发现设备问题并进行改善,提高设备的可靠性和效率。
5. KPI指标监测与改善:建立并监测设备效率和品质的KPI指标,通过持续改善活动,达到KPI指标的要求。
6. TPM标准化工作:通过制定并执行TPM的标准化工作流程,实现全员参与、持续改善和可持续发展的目标。
三、TPM培训资料的内容1. TPM的基本概念和原理:介绍TPM的基本概念和原理,以及TPM对企业发展的重要性和价值。
2. TPM的实施步骤和方法:详细介绍TPM的实施步骤和方法,并提供实际案例和操作指南,帮助员工理解并掌握TPM的实施技巧。
TPM培训资料课件(2024)
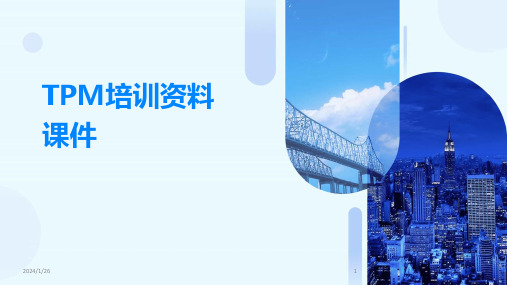
明确推进小组职责
成立专门的推进小组,负 责TPM的具体实施工作, 包括制定计划、组织培训 、监督实施等。
明确员工职责
员工应积极参与TPM的实 施,按照计划和要求完成 相关工作,提出改进建议 。
15
完善相关制度和流程
完善设备管理制度
建立设备管理制度,明确设备的采购 、使用、维护、报废等管理流程,确 保设备的正常运行和维护。
液压故障
由于液压系统油液污染、泄漏 、压力不足等原因引起的故障 ,如液压泵损坏、油缸漏油等 。
其他故障
包括由于人为操作不当、环境 因素(如温度、湿度)变化等
原因引起的故障。
12
2024/1/26
03
CATALOGUE
TPM实施策略与步骤
13
制定TPM推进计划
2024/1/26
确定TPM推进目标和时间表
建立考核体系
将评估指标纳入考核体系,制定相应的考核标准和奖惩措施。
2024/1/26
26
定期进行自查和互查活动
1 2
制定自查计划
确定自查的周期、参与人员、检查内容等。
开展自查活动
按照计划进行自查,记录检查结果,发现问题及 时整改。
3
实施互查机制
鼓励员工之间进行互查,相互监督,共同提高。
2024/1/26
01
明确TPM推进的短期和长期目标,以及实现这些目标的时间表
。
制定详细的推进计划
02
根据目标和时间表,制定具体的推进计划,包括推进的步骤、
责任人、完成时间等。
评估资源需求
03
对推进计划所需的资源进行评估,包括人力、物力、财力等,
确保资源的合理配置。
TPM培训资料
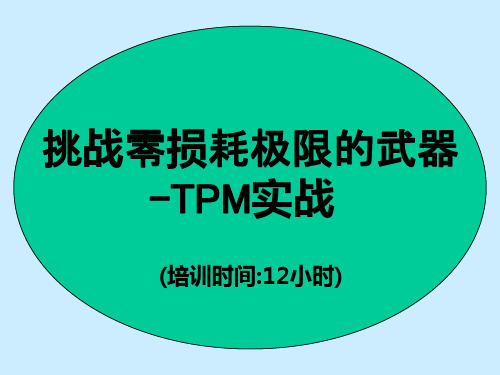
TPM 三 大 思 想
TPM三大思想
(核心-预防哲学)
预防哲学
四大零化目标
零不良 零灾害 零故障 零浪费
全员参与
TPM 预 防 哲 学
预防哲学
设备预防保全 ↓
延长设备寿命\减少设备浪费
日常预防
↓
防止故障 日常设备保全(给油\清扫等)
例行检查 ↓
测定故障
(定期检查\诊断技术)
提前处理
↓
维修故障 (提前对策\设备预防保全)
TPM 四大心脏模式特色
■ 简单易行,见效快 ■ 各个心脏相对独立,互相促进,反复循环
自主保养 寻找问题 提案改善
品质保全 课题改善
第二讲 主要内容回顾
○ TPM定义、起源和发展 ○ TPM 两大基石与八大支柱 ○ TPM三大思想 ○ TPM四大目标 ○ TPM两大效果 ○ TPM四大心脏模式
第二讲 课堂讨论题
某公司TPM活动推进效果图
有形效果
P-生产效率
人均生产台数 增加了45%
设备综合效率 增加了1.3倍
Q-品质
不良率
减少了15%
合格率
保持为98%
C-成本
制造成本 降低了29%
物料成本 降低了15%
D-交期
交期达到率为99%
S-安全
工伤事故为0
M-员工面貌 提案件数翻了6倍
无形效果
-自主管理意识增加了 -相互埋怨情绪逐步减少了 -现场油污和灰尘很难看到,现场 整洁有序
全 改
质 保
养养 善养 善善善 全
5S 活 动
小集团活动
TPM 八 大 支 柱
活动支柱
要点
-教育活动放在TPM活动各支柱首位,首要解决的是培
TPM培训资料

彻底 清 扫并 检查 针对污染 源 采 取 措 施 并 改 善 制 定 暂时性 的 标准 全 员设备的 检查和 保 养 自 主 保 全 的 开始 工 作 位 置 上 的 组织和 完 善 自 发的 设备管 理
5S
难点问题对策/实施
基 础 阶 段
制定点检标准 员工培训/点检实施 自主保全工作开始 目视化管理/优化项目
T P M
全员生产保全
(Total Productive Maintenance)
总 目 录
1. 企业生存的要求 2. 设备效率 3. PM (自主保全)说明 4. TPM(全员自主保全)说明
企业生存的要求
产出的产品 > 投
(服务/环境/情报)
入
(人/材料/设备)
方法1
方法2
大量增加设备投资
不花钱或少花
管理标准化/改善活动自主实施
实 施 阶 段
三、 TPM说明
目 录:
1.TPM定义 2.TPM发展史 3.TPM特点 4.TPM活动形式 5.TPM活动成果 6.TPM工作范畴/内容 7.TPM之树 8.TPM重新组合
1、TPM的定义
TPM(Total Productive
目 标
TPM说明
Maintenance)---全 员预防保全
2、TPM发展史
1960年前后
TPM说明
1980年以后 全面生产维护 TPM: Total Productive Maintenance 全员参加型的保养 生产维修(PM) Productive Maintenance 综合上述维护方法,系统的 维护方案
1960年前后
1955年前后
维修预防(MP) MaintenancePrevention 设计不发生故障的设备,设备 FMEA
TPM培训资料
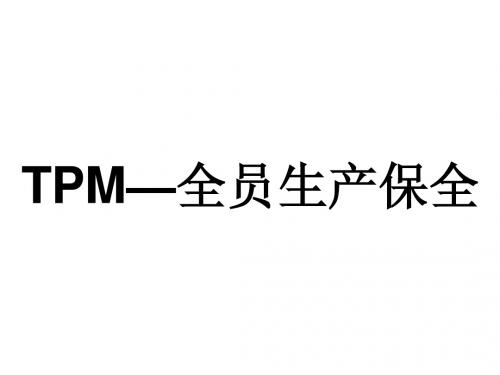
设备的点检润滑管理
• 定期点检 2.1对于厂控设备除实行日常点检外,班组长还 要对其进行定期机能调查。 2.2对重要关键设备、事故多发设备、刚投入生 产的设备要重点关注,对其余设备要有计划进行 点检。 2.3定期点检的检查方法是利用自己的感觉,并 配备一定的检查仪器,对设备的性能进行综合检 查。 2.4定期点检时应填写设备定期点检表与设备检 修报表
提高设备效率 纵向:从高层到一线员工, 维护(保全) MAINTENANCE 维护(保全) 提高人的效率 横向:所有部门 提高管理效率 纵横: 小集团活动 提升品质 推进无人化
TPM(Total productive maintenance)= 全员生产保全 maintenance)
设备的基本条件和使用条件
改 善 表
改 善 前 改 善 后
问题现象及影响: 问题现象及影响: 干油站墙壁脱落严重, 干油站墙壁脱落严重,设备运 行环境差! 行环境差!
发现日期: 发现日期:11.20 发现人: 发现人: 完成日期: 完成日期:11.30
改善内容及效果: 改善内容及效果: 解决日期: 解决日期:11.30 墙壁重新粉刷,变得干净美观。 墙壁重新粉刷,变得干净美观。 解决人: 解决人: 确认人: 确认人:
清扫点检 : 产品及设备各部品的污染
由磨损引起的部品劣化 由摩擦引起的部品精密度低下 由污染累积而引起的功能低下
组装安装条件 : 组装公差、水平度、变形,...
紧固 : 部品组装精密度的问题
连接部品的松动、变形 由振动、冲击等引起的精密度低下 由热膨胀系数差异而引起的松动、变形 动作条件 : 电压、压力、真空度、反应速度,...
发现日期: 发现日期:11.25 发现人: 发现人: 完成日期: 完成日期:12.7
TPM培训资料
饲料生产与工程项目职能线
饲料生产与工程项目职能线
步骤 0 : 准备阶段
1 : 政策准备
2 : 制定工作计划
3 : 制定考核指标(KPI) 4 : 了解设备各部件及使用方法 5 : 准备清理工具 6 : 成立各部门TPM小组 7 : 设备责任到人 8 : 了解设备有哪些不安全区域 9 : 准备阶段的资金准备和奖励措施
5S是什么
形成习惯,提 高整体素质。
整理
区分要物与不 要物,将不要 物处理掉。
素养
保持前3个S, 制度化,规范 化。
5S
整顿 清扫
将要物规范放 置,使寻找时 间为零。
清洁
使工作环境变 得无灰尘、干 净整洁。
饲料生产与工程项目职能线
为什么要推行5S
对客户方而言:改善客户的印象
※5S能节省空间,提升企业形象,降低成本,提升效率。
TPM活动的三大要素
-板(现况板、活动板、信息传递板)-硬件软件的方法论 -物(现场、现物、现象)-实事求是的三现主义 -人(从工人到最高经营者)-以人为本的三者主义
饲料生产与工程项目职能线
TPM 内容 ——八大支柱 TPM 的八大支柱
世界级水平
自主保全
早期管理
预防维护
教育培训
质量管理
安全、健 康、环保 事务管理 5S基础
TPM 的 发 展 史
TPM历程
韩国
80-90再发展
中国
20世纪90年代 中期导入
美国
50-60发展
日本
60-70发展为TPM
饲料生产与工程项目职能线
◆ 中国企业实施TPM情况 海尔、海信
饲料生产与工程项目职能线
TPM培训资料
TPM培训资料【维护TPM原则的培训资料】TPM(全称为Total Productive Maintenance,即全面生产维护),是一种旨在改善生产设备效率和维持生产设备状态的管理方法。
其核心理念是通过减少生产过程中的停机时间和故障,实现生产线的稳定运行并提高生产效率。
本文将为大家介绍TPM的基本原则以及实施TPM 的方法,并提供一些关于TPM培训的资料。
一、TPM的基本原则1.设备运行时长的最大化:TPM的目标是通过减少停机时间和故障,最大程度地提高设备的运行时长。
实现这一目标的主要方法包括设备的良好维护管理、防止故障发生和及时处理故障。
2.全员参与:TPM的实施需要全公司员工的积极参与和配合。
不仅是设备操作人员,还包括设备维护人员、管理人员和支持人员。
通过全员参与,可以深入了解设备运行情况和存在的问题,并共同制定解决方案。
3.预防性维护:TPM强调对设备进行预防性维护,即在设备出现故障之前,通过定期检查和保养,预防故障的发生。
预防性维护的目的是提前发现潜在问题,避免设备故障带来的生产停滞。
4.终身学习:TPM强调员工的终身学习和技能提升。
通过持续的培训和学习,员工可以不断提高自己的专业知识和技能,更好地适应设备和生产工艺的变化,并为持续改进提供支持。
二、TPM的培训资料1.培训大纲:在进行TPM培训时,可以先制定一个培训大纲,明确培训的内容、目标和时间安排。
培训大纲可以帮助培训者更好地组织培训过程,确保培训的有效性。
2.培训材料:为了支持培训的进行,可以准备一些相关的培训材料,如PPT、培训手册、案例分析等。
这些材料可以帮助培训者向学员传达TPM的基本概念、原则和实施方法,并且可以提供一些实际案例进行讨论和分析。
3.培训案例:为了使学员更好地理解和应用TPM的原则和方法,可以准备一些与实际生产相关的培训案例。
通过分析和讨论这些案例,学员可以了解TPM的实际应用和效果,并掌握解决实际问题的方法。
TPM培训资料
• “清扫就是点检”、“点检在于发现设备的不正常”,这是自主保全的 两个基础,也是改善现场体质的基础。一旦初期清扫阶段的活动半途而 废,后面的活动必将事倍功半甚至完全失效。
设备清扫的部位及初期清扫的要点
设备清扫的部位
2、从原因来看: 故障是人“ 故”意引起的“ 障”
故障的类型 1、功能停止型故障 2、功能下降型故障
B、零故障的思想基础: 1)设备的故障是人为造成的; 2)人的思维及行动改变后,设备就能实现零故障; 3)要从“ 设备会产生故障”的观念转变为 “ 设备本身不会产生故
障”;
4)“ 能实现零故障”。 C、实现零故障的对策: 1) 具备基本条件: 清扫、加油、紧固是防止劣化得三要素,也是设备运行的基本条件。
总的来说,清扫就是要切实通过设备及周围环境的整理、整顿、清扫,找出 不良(微缺陷、发生源、不要物等)存在并决定日常目力所及范围内的处 置及改善,来实现以下目标:
• 通过整理、整顿、清扫,将陈年污垢除去,创造一个整洁的工作场所;
• 改善造成灰尘、脏污的源头并改善周围劣化的环境;
• 通过整理、整顿、清扫,使设备潜在的缺陷、异常显性化,并恢复其机能;
源头对策:对污染源、采取了有效的防范措施,对清扫、点检困难点进行改善或 改进; 专项工具:对设备清扫或现场改善起作用的工具,要求小集团每月至少开发一个;
• 彻底清扫设备的各个角落,切身体验“清扫就是点检”,做到“自己的设 备自己维护”;
• 按照计划推进整理、整顿、清扫,提高全员的管理水平,形成一个“能遵 守已决定事项”的工作氛围。
• 一定要找出不正常现象
• 清扫是为了点检设备的健康状态,所以活动的要点就是找出设备不正常现 象。所谓不正常现象,是指“已发生的不正常现象”和“可能发生的不正 常现象”两种情形。
TPM培训资料
TPM的概念1、设备维修体制简介①事后维修----BM(Breakdown Maintenance)这是最早期的维修方式,即出了故障再修,不坏不修。
②预防维修--PM(Preventive Maintanance)这是以检查为基础的维修,利用状态监测和故障诊断技术对设备进行预测,有针对性地对故障隐患加以排除,从而避免和减少停机损失,分定期维修和预知维修两种方式。
③改善维修--CM(Corrective Maintanance)改善维修是不断地利用先进的工艺方法和技术,改正设备的某些缺陷和先天不足,提高设备的先进性、可靠性及维修性,提高设备的利用率。
④维修预防--MP(Maintenance Prevention)维修预防实际就是可维修性设计,提倡在设计阶段就认真考虑设备的可靠性和维修性问题。
从设计、生产上提高设备素质,从根本上防止故障和事故的发生,减少和避免维修。
⑤生产维修--PM(Productive Maintenance)是一种以生产为中心,为生产服务的一种维修体制。
它包含了以上四种维修方式的具体内容。
对不重要的设备仍然实行事后维修,对重要设备则实行预防维修,同时在修理中对设备进行改善维修,设备选型或自行开发设备时则注重设备的维修性(维修预防)。
2、什么叫TPM?(Total Productive Maintenance)2.1 什么是TPM?TPM的意思就是是“全员生产维修”,这是日本人在70年代提出的,是一种全员参与的生产维修方式,其主要点就在“生产维修”及“全员参与”上。
通过建立一个全系统员工参与的生产维修活动,使设备性能达到最优。
TPM的提出是建立在美国的生产维修体制的基础上,同时也吸收了英国设备综合工程学、中国鞍钢宪法中里群众参与管理的思想。
在非日本国家,由于国情不同,对TPM的理解是:利用包括操作者在内的生产维修活动,提高设备的全面性能。
2.2 TPEM:Total Productive Equipment Management就是全面生产设备管理。
- 1、下载文档前请自行甄别文档内容的完整性,平台不提供额外的编辑、内容补充、找答案等附加服务。
- 2、"仅部分预览"的文档,不可在线预览部分如存在完整性等问题,可反馈申请退款(可完整预览的文档不适用该条件!)。
- 3、如文档侵犯您的权益,请联系客服反馈,我们会尽快为您处理(人工客服工作时间:9:00-18:30)。
TPM 如何为精益服务
• TPM 提高设备效率 – 减少投资 – 提高现有资产效率
• TPM 取保零停机和高可靠性 – 允许短期计划和小批量 – 确保生产顺畅
• TPM 提高质量 – 制程更可靠 – 充分减少不良
• TPM 强调 – 操作员技能 – 设备和周围环境表现 – 全员参与和责任心
OPERATOR
SHIFT
DATE
MACH
AVAILABILITY CODE TIME
COMMENTS
A. Total Available Time: B. Planned downtime: C. Net Available Tim(eA: - B)
min. min. min.
D. Total Downtime:
H. Ideal Cycle Time:
(min / part)
J. Performance Efficiency:
(H x G divided by E X 100)
qty. %
QUALITY RATE K. Total Defects: (Rejects and Scrap) L. Quality Rate:
TPM Services
TPM 帮助消除浪费
• 时间和精力的浪费是由于: – 停机 – 速度慢 – 质量差
• 资产的浪费是由于: – 低OEE – 需要额外的设备和人手
• 浪费是由于: – 大批量生产 – 大量安全库存
TPM Services
典型的TPM 结果
• 可操作性上升 25% • 维护成本降 30% 到 50% • 库存降低 50% 到 75% • 停机的人力损失减少 50% • 报废减少 70% • 产能提高 25-40% • 生产力提高 50%
Auburn, IN
Three Rivers, MI
Jackson AMD,rkshop
六种损失对设备可生产时间的 影响
8 小时
总机器可用时间
设备可用性角 度衡量
总可操作时间
6小时
停机损失
剩余操作时间
4.8小时
生产效率角度衡 量
速度损失
最终可操作时间 不良损失
• TPM 活动要求组织内所有成员的参与,从最 高管理者到一线工人,是跨部门的活动,要求 所有的职能领域的参与;
• TPM活动通过紧密的跨部门团队合作来达成提 高设备总效率的目的。
作用
– ①减少设备停机损失, 提高可预知运行时间
– ②减少不良 – ③减少设备相关其他损
失 – ④减少制造过程中的其
他损失
旧习惯 我操作 – 你维修
TPM 习惯 人人都有维护设备的
责任
故障:人为引起的障碍
TPM 有助于提高主人翁责任感
维护良好的设备可以给我们
• 维护良好的设备可以保质保量的生产 • 缺乏维护的设备产量低质量差 • 坏的设备做不出任何产品
设备缺乏维护是因为:
• 设备缺乏维护
– 维护部的问题 – 操作员的问题
MTTR - Mean Time To Repair 平均修复时间
需要采用各种方法掌握设备的 真实状况
Total Productive Manufacturing
全员生产性维护
TPM 定义
• TPM 是设备管理的一种全新理念,通过全员参 与设备的管理来实现设备效率的最大化。
• TPM 致力于构建人和设备之间的最佳关系;并 涵盖设备整个生命周期
生产效率……………………… 95%
质量合格率…………………….99.9% OEE = .90 X .95 X .999 = 85%
TPM Services
美国工厂 平均水平
30-45% OEE
55-70%
损失
隐藏的工厂
最大产
85% OEE 15%
损失
能
世界级
TPM Services
OEE
如何计算OEE
(G - K divided by G X 100)
%
OVERALL EQUIPMENT EFFECTIVENESS
M. Overall Equipment Effectiveness:
M = (F X J X L X 100)
%
Cycle Meter Reading Number:
Part Number
TPM 活动的目标
1. 优化设备状况,提高设备有效性 2. 开发针对设备整个生命周期的维护计划 3. 开发出相关标准和检查表 4. 提高操作员和维修人员技能 5. 系统的提高工作环境 6. 全员参与提高大家团队精神 7. 练习目标管理的过程
• 所有设备都应该像最好的时候一样运行 • 设备只有当技术淘汰时才会被更换 • TPM 活动包含寻找并消除所有小的停机
Cycle Time
Shift Start
Shift End
CYCLE TIME AVERAGING WORKSHEET
Qty. Run
Total Time
Re je cts
OEE 帮助我们找到隐藏的工厂. OEE 帮助我们找到改善的机会 不要放在一边 – 要真正用起来
其他维护相关的指标
MTBF - Mean Time Between Failure 平均停机间隔时间
3.2 小时
质量角度衡 量
设备停机 换型和调整 等待和微小停机 速度减缓
制程不良 开机不良或换型不良
OEE MEASURES TPM “Actual Machine Performance Data”
= OEE
设备有效性 X 生产效率 X
质量
世界级工厂 OEE目标
设备有效性…………………….90%
设备有效性 X 生产效率 X 质量结果
停机 换型 & 调整 其他
等待 & 微小停机 速度减缓
制程不良 开机或换型不良
提醒: OEE 衡量制造过程中的 六种损失
• 停机 • 换型及调整 • 等待和微小停机 • 速度减缓 • 制程不良 • 开机,换型,调整不良
OVERALL EQUIPMENT EFFECTIVENESS FORM
min.
D. Tot E. Operating Time: F. Equipment Availability:
(C - D) (E divided by C X 100)
min. %
PERFORMANCE EFFICIENCY
G. Total Parts Run:
(Good and Bad Parts)