第三讲刃口尺寸计算2H
第二章冲裁三.凸、凹模刃口尺寸的计算
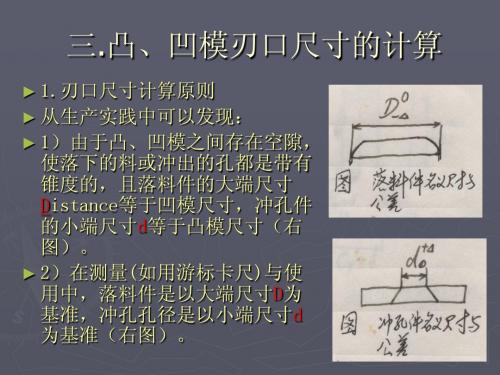
► 清华大学编《机械制图》列出:
标准公差分为IT01、0、1~18共20级, IT01精度最高,IT18精度最低。 例如 轴 Φ 50:IT7公差δ =25μ m(0.025mm) IT9公差δ =62μ m(0.062mm)
► 2.尺寸计算方法
► (1)凸模与凹模分开加工 ► 就是凸、凹模按照各自的图纸分别加工到
; ;
;
4
2
2
4
8
;
8
4
► 最后说明:凸模以凹模为基准配置,保证双面间
隙为Zmin~Zmax=
”。
► ②同理求冲孔件模具刃口尺寸。
► 例题:P19
本例题在教材中省略了重要的说明文字(如“对于 复杂形状工件,凸、凹模应采用配合加工”、“磨 损后会变大的第一类尺寸A”、“磨损后会变小的第 二类尺寸B”、“磨损后不变的第三类尺寸C”)和 中间过程(如公式2-5,2-6,2-7),还要补充 模具图,初学者正式答题时应该注意补充完善。
► (2)凸模与凹模配合加工(配制)
► 就是以凸、凹模中的基准件(落料凹模或
冲孔凸模)作为独立加工对象,按图纸名 义尺寸和公差加工,然后根据基准件的实 际尺寸和形状,采用修配方法加工配制件 (落料凸模或冲孔凹模),修配出单边最 小合理使用间隙。“一把钥匙开一把锁”。 ► 此时基准件图纸上应标注公称尺寸和制造 公差,配制件图纸上只标注公称尺寸,并 注明“按基准件修配单边间隙Zmin/2~ Zmax/2”。
最后尺寸,然后将两者提交装配,为此必 须在凸、凹模图纸上分别标注刃口尺寸和 制造公差δ p(凸模Protruding die)和δ d (凹模Dent die)。优点是:制造周期短、 复制的凸、凹模具有互换性、适于制造标 准件类型的凸、凹模。
第三讲刃口尺寸计算(2H)

5) 尺寸偏差应按“入体”原则标注
落料件上偏差为零,下偏差为负;冲孔件上偏差为正,下 偏差为零。
项目一 冲模制造公差
基本尺寸 ≤18 > 18~20 > 20~80 > 80~120 δp -0.020 -0.020 -0.020 -0.025 δd +0.020 +0.025 +0.020 +0.025 基本尺寸 > 20~180 > 180~260 > 260~500 > 500 δp -0.020 -0.020 -0.040 -0.050 δd +0.040 +0.045 +0.060 +0.070
法只需计算基准件(冲孔时为凸模,落料时为凹模)基本尺寸
及公差,另一件不需标注尺寸,仅注明“相应尺寸按凸模 (或凹模)配作,保证双面间隙在Zmin~Zmax之间”即可。
应用配作法时需先分析凸、凹模刃口尺寸经磨损后的变
化规律,然后可按式(1-27)~(1-29)计算凸、凹模刃口尺寸。
项目一 冲裁模设计
(4) 刃口制造偏差可按工件相应部位公差值的1/4来选取。对于刃口尺寸
磨损后无变化的,制造偏差值可取工件相应部位公差值的1/8并冠以
“ ± ”。
项目一 冲裁模设计
图1-17 孔及冲孔凸模磨损情况
项目一 冲裁模设计
图1-18 落料件及落料凹模磨损情况
项目一 冲裁模设计
任务五
试根据任务书工件尺寸计算模具刃口尺寸
(1-25) (1-26)
{d = 0.4(Zmax - Zmin)
p
dd = 0.6(Zmax - Zmin)
项目一 冲裁模设计 2) 配作法 配作法适用于形状复杂的凸、凹模刃口尺寸计算,先按 零件尺寸和公差计算并制造出凹模或凸模中的一个(基准件), 然后以此为基准再按最小合理间隙配作另一件。因此,配作
刀刃刃口尺寸计算公式
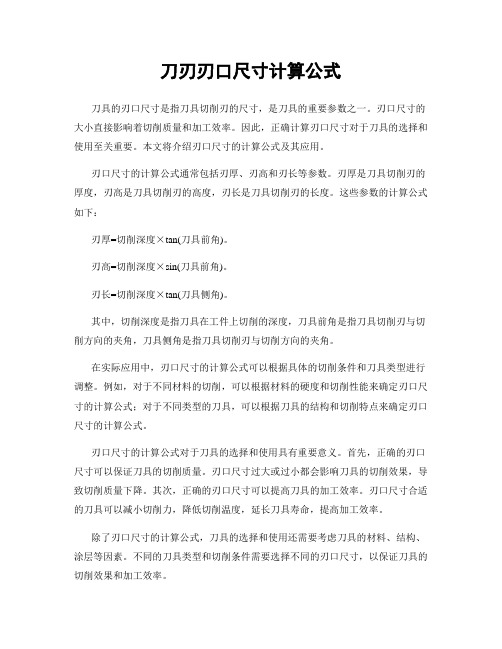
刀刃刃口尺寸计算公式刀具的刃口尺寸是指刀具切削刃的尺寸,是刀具的重要参数之一。
刃口尺寸的大小直接影响着切削质量和加工效率。
因此,正确计算刃口尺寸对于刀具的选择和使用至关重要。
本文将介绍刃口尺寸的计算公式及其应用。
刃口尺寸的计算公式通常包括刃厚、刃高和刃长等参数。
刃厚是刀具切削刃的厚度,刃高是刀具切削刃的高度,刃长是刀具切削刃的长度。
这些参数的计算公式如下:刃厚=切削深度×tan(刀具前角)。
刃高=切削深度×sin(刀具前角)。
刃长=切削深度×tan(刀具侧角)。
其中,切削深度是指刀具在工件上切削的深度,刀具前角是指刀具切削刃与切削方向的夹角,刀具侧角是指刀具切削刃与切削方向的夹角。
在实际应用中,刃口尺寸的计算公式可以根据具体的切削条件和刀具类型进行调整。
例如,对于不同材料的切削,可以根据材料的硬度和切削性能来确定刃口尺寸的计算公式;对于不同类型的刀具,可以根据刀具的结构和切削特点来确定刃口尺寸的计算公式。
刃口尺寸的计算公式对于刀具的选择和使用具有重要意义。
首先,正确的刃口尺寸可以保证刀具的切削质量。
刃口尺寸过大或过小都会影响刀具的切削效果,导致切削质量下降。
其次,正确的刃口尺寸可以提高刀具的加工效率。
刃口尺寸合适的刀具可以减小切削力,降低切削温度,延长刀具寿命,提高加工效率。
除了刃口尺寸的计算公式,刀具的选择和使用还需要考虑刀具的材料、结构、涂层等因素。
不同的刀具类型和切削条件需要选择不同的刃口尺寸,以保证刀具的切削效果和加工效率。
在实际应用中,刃口尺寸的计算可以通过刀具厂家提供的刀具参数表来进行,也可以通过切削力模型和切削仿真软件来进行。
通过这些手段,可以更加准确地确定刃口尺寸,提高刀具的切削效果和加工效率。
总之,刃口尺寸的计算公式是刀具选择和使用的重要参考依据。
正确的刃口尺寸可以保证刀具的切削质量和加工效率,提高加工质量和效率。
因此,刃口尺寸的计算应该引起我们的重视,加强研究和应用。
2-3刃口尺寸计算
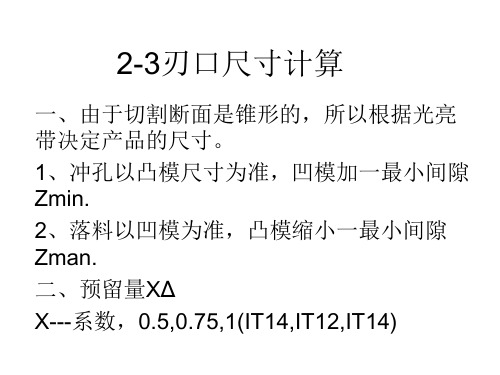
DP = ( Dd − Z
2冲孔:
0 min −δ p
)ቤተ መጻሕፍቲ ባይዱ
= ( Dmax − X∆ − Z
0 min −δ p
)
d p = (d min + X∆) d d = (d p + Z )
0 −δ p
+δ d min 0
= (d min + X∆ + Z
+δ d min 0
三、刃口公差(δp,δd) 1、查表法; 2、IT6---IT7; 3、根据 ︱δp ︱+︱ δd ︱≤Zman-Zmin δp =0.4(Zman-Zmin) δd =0.6(Zman-Zmin) 四、刃口尺寸计算公式
刃口公差采用“入体原则,轴小孔大”,即公差 向有材料的一方偏差。 1、落料:
)
例:计算凸凹模刃口尺寸
• 材料Q235,t=2mm,IT14,X=0.5 • 解: 1、查表:Z=(14~20) ℅t • Zmin=0.14X2=0.28mm • Zmax=0.20X2=0.4mm • Zmax-Zmin=0.4-0.28=0.12mm 2计算δp,δd
δp=0.4(Zmax-Zmin)=0.4x0.12=0.048mm δd=0.6( Zmax-Zmin)=0.6x0.12=0.072mm 3、代入公式计算凸凹模刃口尺寸 ∵是落料,先计算凹模刃口尺寸,凸模 减去Zmin即可。
2-3刃口尺寸计算
一、由于切割断面是锥形的,所以根据光亮 带决定产品的尺寸。 1、冲孔以凸模尺寸为准,凹模加一最小间隙 Zmin. 2、落料以凹模为准,凸模缩小一最小间隙 Zman. 二、预留量X∆ X---系数,0.5,0.75,1(IT14,IT12,IT14)
刃口尺寸计算2.3
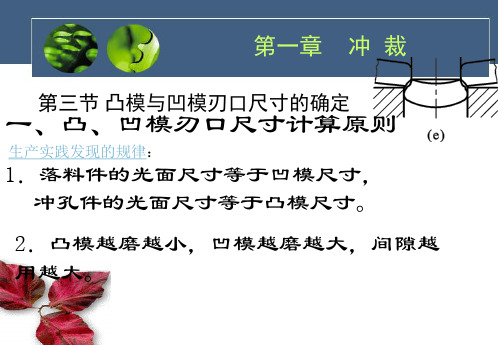
查冲裁初始合理间隙表得:Zmin=0.1 技术要求中说明:凸模刃口尺寸按凹模实际配做,保证最小双面合理 间隙Zmin(0.1mm)
第一章 冲 裁
第一章 冲 裁
= (6.09 + 0.04 )0
+0.012
+ = 6.13 0 0.012
校核: 校核:
δ T + δ A ≤ Z max − Z min
工件精 度IT10 以上 X=1 工件 精度 IT11~ IT13 X=0.75 工件 精度 IT14 X=0.5 也可查 表获得
第一章
冲 裁
第一章 冲 裁
凸、凹模制造公差,可按 取,也可
) − Z min )
IT6~IT7级来选
查表选取,
第一章
冲 裁
第一章
冲 裁
例 t=0.5mm Q235钢. 计算冲 裁凸、 凹模刃 口尺寸 及公差。
第一章 冲 裁
冲制如图所示零件,材料为Q235 钢,料厚t=0.5mm。计算冲裁凸、 凹模刃口尺寸及公差。 解:由图可知,该零件属于无特 殊要求的一般冲孔、落料。
0
校核: 校核: 因此, 因此,可取:
0.016 + 0.025 = 0.04 f 0.02
δ T = 0.4 ⋅ (Z max − Z min ) = 0.4 × 0.02 = 0.008
δ A = 0.6 ⋅ (Z max − Z min ) = 0.6 × 0.02 = 0.012
故:
+ D A = 35.69 0 0.012 mm
a = 80
0 − 0 . 42
mm
b = 40
0 − 0 . 34
mm
c = 35
2.3凹凸模刃口尺寸的计算
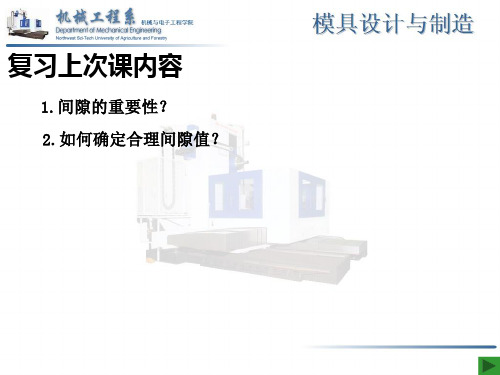
a凹 (80 0.5 0.42 )
1 0.42 4 0
0.105 mm 79 .79 0 mm
0.085 mm 39.750 mm
b凹 ( 40 0.75 0.34 )
c凹 (35 0.75 0.34 )
1 0.34 4 0
1 0.34 4 0
80±0.07 42±0.08
60±0.05
φ 16+0.060 2X? 0
d
解:
① 外型尺寸是按落料计算公式来确定的,即先 确定凹模刃口尺寸,后确定凸模尺寸。 凹模上偏差 d =0.6×(Zmax- Zmin) =0.6×(0.24-0.20) = 0.024 凸模下偏差 p = 0.4×(Zmax- Zmin) =0.4×(0.24-0.20) = 0.016 0 80.07 80尺寸换算=80±0.07 = 0.14 , 1 =0.14 2 =0.10 60尺寸换算=60±0.05 = 60.050 0.10 ,
校核: ≤ Z Z p d max min
0.020 + 0.020 ≤ 0.07 - 0.03 0.04 1(续)
孔距尺寸: Ld =L±=18±0.125×2×0.09 = (18±0.023)mm
0.025 0.025 落料:Dd D x0 (36 0.5 0.62)0 mm 35.690 mm
落料凸、凹模尺寸 a) 落料凹模尺寸 b) 落料凸模尺寸
落料件的光亮带处于大端尺寸,且等于凹模尺寸; 冲孔件的光亮带处于小端尺寸;且等于凸模尺寸。
2.凸模轮廓越磨越小,凹模轮廓越磨越大,结果使间隙越用越大。
冲裁变形过程
计算原则:
1.落料模:先确定凹模刃口尺寸,以凹模为基准,间隙取在凸模 上,即凸模的刃口尺寸=凹模刃口尺寸-最小合理间隙Z 。 冲孔模:先确定凸模刃口尺寸,以凸模为基准,间隙取在凹模 上,凹模的刃口尺寸=凸模刃口尺寸+最小合理间隙Z 。 2.根据冲模在使用过程中的磨损规律:
刃口尺寸的计算
二、凸、凹模刃口尺寸的计算方法(续)
1.按凸模与凹模图样分别加工法(续)
为了保证可能的初始间隙不超过Zmax,即
T A
+Zmin≤Zmax,选取必须满足以下条件: T A ≤ Z max Z min
凸、凹模的制造公差,可按IT6~IT7级来选取,也可 查表2.4.1选取,但需校核。或取
刃口尺寸的计算
一、凸、凹模刃口尺寸计算原则
1.设计落料模先确定凹模刃口尺寸。以凹 模为基准,间隙取在凸模上,即冲裁间隙 通过减小凸模刃口尺寸来取得。 设计冲孔模先确定凸模刃口尺寸。以凸 模为基准,间隙取在凹模上,冲裁间隙通 过增大凹模刃口尺寸来取得。
凸、凹模刃口尺寸计算原则
2.根据冲模在使用过程中的磨损规律,设 计落料模时,凹模基本尺寸应取接近或等 于工件的最小极限尺寸; 设计冲孔模时,凸模基本尺寸则取接近 或等于工件孔的最大极限尺寸。 模具磨损预留量与工件制造精度有关。
A
0 0
DT D A Z min T Dmax x Z min T
(2)冲孔 0 d T d min x T
d A dT Z min 0
1 8
ห้องสมุดไป่ตู้A
d min x Z min 0
A
(3)孔心距
凸、凹模刃口尺寸计算原则
3.冲裁(设计)间隙一般选用最小合理间 隙值(Zmin)。
4.选择模具刃口制造公差时,要考虑工件 精度与模具精度的关系,即要保证工件的 精度要求,又要保证有合理的间隙值。 5.工件尺寸公差与冲模刃口尺寸的制造偏 差原则上都应按“入体”原则标注为单向 公差。但对于磨损后无变化的尺寸,一般 标注双向偏差。
刃口尺寸计算
=(36-0.5×0.62)+0.012=35.69+0.012 × Dp=(Dd-Zmin)-δp =(35.69-0.04)-0.008=35.65-0.008
第三章 冲裁
第四节 凸模与凹模刃口尺寸的确定
冲孔:dp=(dmin+χ∆) – δp 冲孔: =(6+0.75×0.12)-0.008=6.09-0.008 dd=(dp+Zmin) + δp = (6.09+0.04) +0.012=6.13+ 0.012 孔距尺寸: 孔距尺寸: Ld=Lm±∆/8 =18±0.18 /8 ± = (18±0.025)mm ±
第三章 冲裁
第四节 凸模与凹模刃口尺寸的确定
(3)孔心距 Ld=Lm±∆/8 Ld——— 凹模孔心距的尺寸, 凹模孔心距的尺寸, Lm——— 工件孔心距的平均尺寸; 工件孔心距的平均尺寸; ∆——— 冲裁件制造公差; δd = 1/4 ∆ 冲裁件制造公差;
第三章 冲裁ቤተ መጻሕፍቲ ባይዱ
第四节 凸模与凹模刃口尺寸的确定
δd=0.6(Zmax-Zmin) 0.6(
第三章 冲裁
第四节 凸模与凹模刃口尺寸的确定
(1)落料 以凹模为基准件,即先计算凹模的刃口尺寸, 确定凹模的制造偏差。 由于凹模在磨损后尺 寸将变大,即落料件尺寸 会随之增大,为保证凹模 磨损到一定程度仍能冲出 合格零件,落料凹模基本 尺寸应取工件尺寸公差范 围内的较小尺寸。
落料时各部分尺寸与公差分布情况
第三章 冲裁
第四节 凸模与凹模刃口尺寸的确定
落料时刃口尺寸计算公式: 落料时刃口尺寸计算公式: 刃口尺寸计算公式 凹模 Dd=(Dmax-χ∆)+δd 凸模 Dp=(Dd-Zmin)-δp =(D-χ∆-Zmin) - δp Dd、Dp———落料凹、凸模尺寸; 落料凹、 落料凹 凸模尺寸; Dmax———落料件的最大极限尺寸; 落料件的最大极限尺寸; 落料件的最大极限尺寸 ∆——— 冲裁件制造公差; 冲裁件制造公差; 凹模Die 凹模 凸模Protruding model 凸模 Zmin———最小合理间隙; 最小合理间隙; 最小合理间隙 δp、δd———凸、凹模的制造公差,可查有关资料, 凸 凹模的制造公差,可查有关资料,
冲压工艺与模具设计:凸、凹模刃口尺寸计算
落料凹模或冲孔凸模磨损后将会增大的尺寸,相当于简单形状的落料凹 模尺寸
2. 磨损后变小的尺寸
B
(Bmin
x)
0 1
4
冲孔凸模或落料凹模磨损后将会减小的尺寸,相当于简单形状的冲孔凸模 尺寸
3. 磨损后不变的尺寸
C
(C m in
1 2
)
1 8
2.3 凸、凹模刃口尺寸计算
3 用配作加工法的刃口尺寸计算方法
3 用配作加工法的刃口尺寸计算方法
配作法就是先按设计尺寸制出一个基准件(凸模或凹模),然后根据基准 件的实际尺寸再按最小合理间隙配制另一件。 特点:
模具的间隙由配制保证,工艺比较简单,不必校核
T A ≤ Zmax Zmin的条件,并且还可放大基准件的制造公差,
使制造容易。
2.3 凸、凹模刃口尺寸计算
3 用配作加工法的刃口尺寸计算方法 模具刃口尺寸类型
2.3 凸、凹模刃口尺寸计算
3 用配作加工法的刃口尺寸计算方法
图2.24 落料凹模刃口磨损后的变化情况 a)落料件 b)落料凹模刃口轮廓
2.3 凸、凹模刃口尺寸计算
3 用配作加工法的刃口尺寸计算方法
1. 磨损后变大的尺寸
1
A
(
Amax
x)
4 0
14.94,不必标注公差,但要在技术条件中注明:凸模实际刃口尺寸与落料凹
模配制,保证最小双面合理间隙值 Z min 0.10mm
2.3 凸、凹模刃口尺寸计算
3 用配作加工法的刃口尺寸计算方法 落料凹模、凸模的尺寸如图。
落料凸、凹模尺寸 a) 落料凹模尺寸 b) 落料凸模尺寸
如下图零件,材料为D42硅钢板,料厚为0.35mm,用配作加工方法,试 确定落料凸、凹模的刃口尺寸(P103)。
冲裁模刃口尺寸计算
23, 2021
谢谢观赏
You made my day!
我们,还在路上……
§t + §a ≦Z max - Z min 或取 §t = 0.4(Z max-Z min)
§a = 0.6(Z max-Z min) 4.間隙均勻性純靠加工精度保證.
1--1.沖孔:
設工件尺寸為+§d 0
dt = (d + x△) 0
D a = (d t + Z min)+0§a
=
(d
+
ቤተ መጻሕፍቲ ባይዱx△
+Z
特點:在尺寸線箭頭所指的幾何要素中,只有 其中一個要素表面發生磨損,另一個不 存在磨損.
計算方法:其原理與上述計算方法相同.
9、要学生做的事,教职员躬亲共做; 要学生 学的知 识,教 职员躬 亲共学 ;要学 生守的 规则, 教职员 躬亲共 守。20 21/5/23 2021/5/23Sund ay , May 23, 2021 10、阅读一切好书如同和过去最杰出 的人谈 话。202 1/5/232 021/5/2 32021/5/235/2 3/2021 11:03:49 AM 11、一个好的教师,是一个懂得心理 学和教 育学的 人。202 1/5/232 021/5/2 32021/5/23May -2123 -May -21 12、要记住,你不仅是教课的教师, 也是学 生的教 育者, 生活的 导师和 道德的 引路人 。2021/5/23202 1/5/232 021/5/2 3Sunday , May 23, 2021 13、He who seize the right moment, is the right man.谁把握机遇,谁就心想事成。2021/5/23202 1/5/232 021/5/2 32021/5 /235/23 /2021 14、谁要是自己还没有发展培养和教 育好, 他就不 能发展 培养和 教育别 人。202 1年5月 23日星 期日20 21/5/23 2021/5/232021 /5/23 15、一年之计,莫如树谷;十年之计 ,莫如 树木; 终身之 计,莫 如树人 。2021 年5月20 21/5/23 2021/5/232021 /5/235/23/2021 16、提出一个问题往往比解决一个更 重要。 因为解 决问题 也许仅 是一个 数学上 或实验 上的技 能而已 ,而提 出新的 问题, 却需要 有创造 性的想 像力, 而且标 志着科 学的真 正进步 。2021/5/23202 1/5/23 May 17、儿童是中心,教育的措施便围绕 他们而 组织起 来。202 1/5/232 021/5/2 32021/5/23202 1/5/23
- 1、下载文档前请自行甄别文档内容的完整性,平台不提供额外的编辑、内容补充、找答案等附加服务。
- 2、"仅部分预览"的文档,不可在线预览部分如存在完整性等问题,可反馈申请退款(可完整预览的文档不适用该条件!)。
- 3、如文档侵犯您的权益,请联系客服反馈,我们会尽快为您处理(人工客服工作时间:9:00-18:30)。
项目一 冲裁模设计
表1-13 冲裁模初始双面间隙值 Z
材料名称
力学性能
板料厚度 t 0.2 0.5 0.8 1.0
45 T7 、 T8( 退火 ) 65Mn( 退火 )
磷青铜 (硬 ) 铍青铜
HBS ≥ 190 ? b ≥ 600 MPa
Z min 0.025 0.08 0.13 0.17
Z max 0.045
始用间隙 Z
Z min 0.015
Z max 0.035
Z min 0.01
Z max 0.03
0.06
0.08
0.04
0.06
0.10
0.13
0.07
0.10
0.13
0.16
0.10
0.13
H62 、 H68( 软 ) 紫铜 (软 )
L21 ~ LF2 防锈铝 硬铝 LY12( 退火 ) 铜母线、铝母线
加工出凸、凹模,即可保证合理间隙。分别加工法适用于形
状简单(如圆形、矩形)的凸、凹模尺寸的计算,可按式(1-
19)~(1-26)计算凸、凹模刃口尺寸。
(1) 落料:
凹模刃口尺寸
Dd
?
( D max
?
??
)
?
? 0
d
(1-19)
凸模刃口尺寸
(1-20) Dp
?
(Dd
?
Z
min
)
0 ?
?
p
?
(Dmax
?
> 500
δp - 0.020 - 0.020 - 0.040 - 0.050
δd +0.040 +0.045 +0.060 +0.070
项目一 冲裁模设计
2.凸、凹模刃口尺寸计算方法
1) 分别加工法
分别加工法即根据冲裁零件尺寸和凸、凹模的最小间隙
值分别计算出凸模和凹模的尺寸,然后按计算出的尺寸分别
0.66
0.37
0.45
0.75
0.42
0.52
0.92
0.53
0.63
1.29
0.76
0.88
项目一 冲裁模设计
1.3.6 冲裁模凸、凹模刃口尺寸计算规范
1.凸、凹模刃口尺寸计算原则 1) 先确定基准件 落料:以凹模为基准,间隙取在凸模上;冲孔:以凸模 为基准,间隙取在凹模上。 2) 应考虑冲模的磨损规律 落料模:凹模基本尺寸应取接近工件的最小极限尺寸; 冲孔模:凸模基本尺寸应取接近工件的最大极限尺寸。
0.1 0.16 0.20
10 、 15 、 20 钢 硅钢
H62 、 H65( 硬 ) LY12
Q215 、 Q225 钢 08 、 10 、 15 钢
紫铜 (硬 ) 磷青铜、铍青铜 *
H62 、 H68
HBS=140 ~ 190
HBS=70 ~ 140
? b =(400 ~ 600)MPa
? b =(300 ~ 400)MPa
0.38
0.27
0.31
0.20
0.24
0.13
0.17
2.0
0.38
0.42
0.30
0.34
0.22
0.26
0.14
0.18
2.5
0.49
0.55
0.39
0.45
0.29
0.35
0.18
0.24
3.0
0.62
0.68
0.49
0.55
0.36
0.42
0.23
0.29
3.5
0.73
0.81
0.58
0.66
0.43
0.51
0.27
0.35
4.0
0.86
0.94
0.68
0.76
0.50
0.58
0.32
0.40
4.5
1.00
1.08
0.78
0.86
0.58
5.0
1.13
1.23
0.9
1.00
0.65
6.0
1.40
1.50
1.10
1.20
0.82
8.0Leabharlann 2.002.121.60
1.72
1.17
注: 1. Zmin 应视为公称间隙。 2.有 ? 处均系无间隙。
HBS ≤ 70 ? b ≤ 300 MPa
Z min ??
0.025 0.045 0.065
Z max — 0.045 0.075 0.095
1.2
0.21
0.24
0.16
0.19
0.13
0.16
0.075
0.105
1.5
0.27
0.31
0.21
0.25
0.15
0.19
0.10
0.14
1.8
0.34
材料 磷青铜 白铜(Nickel Silver or German Silver)
间隙 (6%~10%)t (6%~10%)t
铝(硬质) 铝(软质) 铝合金(硬质) 铝合金(软质)
铅 高导磁合金(perm alloy)
(6%~10%)t (5%~8%)t (6%~10%)t (6%~10%)t (6%~9%)t (5%~8%)t
项目一 冲裁模设计
模块一 冲裁模具设计
深圳职业技术学院
项目一 冲裁模设计
1.3.5 冲裁间隙选用规范
如图1-16所示,冲裁间隙是指冲裁模的凸模和凹模刃口之间的尺
寸之差。单边间隙用Z/2表示,双边间隙用Z表示。冲裁模双边间隙表示
为
Z?=?Dd-Dp
(1-18)
图1-16 冲裁间隙
项目一 冲裁模设计
项目一 冲裁模设计
表1-14 规则形状冲裁模凸、凹模制造公差
基本尺寸 ≤18
> 18~20 > 20~80 > 80~120
δp - 0.020 - 0.020 - 0.020 - 0.025
δd +0.020 +0.025 +0.020 +0.025
基本尺寸 > 20~180 > 180~260 > 260~500
项目一 冲裁模设计
3) 凸、凹模刃口制造公差应合理 形状简单的刃口制造偏差:按IT6~IT7级或查表1-14选取; 形状复杂的刃口制造偏差:取冲裁件相应部位公差的1/4;对刃 口尺寸磨损后无变化的制造偏差:取冲裁件相应部位公差的1/8 并冠以“±”。
4) 冲裁间隙采用最小合理间隙值(Zmin)
在凸、凹模磨损到一定程度情况下,仍能冲出合格制件。 5) 尺寸偏差应按“入体”原则标注 落料件上偏差为零,下偏差为负;冲孔件上偏差为正,下 偏差为零。
生产实际中,根据材料种类及厚度查表1-12或表1-13确 定合理冲裁间隙。
表1-12 冲裁模初始双面间隙值Z(按材料厚度取值)
材料 纯铁 软钢 硬钢 硅钢片 不锈钢
铜(软质) 铜(硬质) 黄铜(硬质) 黄铜(软质)
间隙 (6%~9%)t (6%~9%)t (8%~12%)t (7%~11%)t (7%~11%)t (6%~10%)t (6%~10%)t (6%~10%)t (6%~10%)t
?Δ ?
Z
min
)
0 ?
?
p
项目一 冲裁模设计
(2) 冲孔:
凸模刃口尺寸
dp
?
(d min
?
?
Δ)
?0 ??
p
(1-22)
凹模刃口尺寸 (3) 孔心距:
dd
?
(dp
?
Z )??d min 0
?
(dmin
?
? Δ?
Z )??d min 0
(1-23)
Δ Ld ? L ? 8
(1-24)
(4) 冲模的制造公差与冲裁间隙之间应满足: