电石生产工艺指标控制
电石工艺规程(修改版)..

鄂尔多斯氯碱化工有限公司电石生产工艺规程签发:审核:编制:文件编号:SC/ZD-07分发号:执行单位:氯碱化工分公司执行时间:2015年5月5日鄂尔多斯氯碱化工公司二〇一五年五月五日目录一.产品说明 (2)二.原、辅助材料质量指标 (6)三. 电石生产原理 (7)四.工艺流程简述 (25)五. 工艺控制指标 (25)六. 产品、中间产品及原材料检验要求 (26)一.产品说明1.简介化学名:碳化钙工业名:电石(英文名:Calcium carbide)分子式:CaC2C结构式:CaC分子量:64.102. 电石的物理性质2.1 外观化学纯的碳化钙几乎是无色透明的晶体。
极纯的碳化钙是天蓝色的大晶体,颜色象淬火钢。
工业电石是碳化钙和氧化钙以及其他杂质合成的混合物,根据杂质含量的不同呈黄色或黑色,含碳化钙较高时呈紫色。
电石的新断面具有光泽,吸水后失去光泽呈灰白色。
2.2 密度18℃时,纯电石的相对密度为2.22。
工业电石的密度与其碳化钙的含量关系见表1。
2.3 熔点电石的熔点随电石中碳化钙含量的改变而改变,纯碳化钙的熔点为2300℃。
碳化钙的含量在69%的混合物的熔点最低,为1750℃。
碳化钙的含量继续减少时,熔点反而升高,后降到1800℃,此时混合物中碳化钙含量为35.6%。
在此二个最低熔点(1750~1800℃)之间有一个最大值1980℃,它相当于含碳化钙52.5%的混合物。
随着碳化钙含量继续减少(即低于35.6%)混合物的熔点又升高。
见下图。
影响电石熔点的因素不仅是石灰的含量,氧化铝、氧化硅和氧化镁等杂质也有影响。
2.4 导电性电石能导电,其导电性与电石的纯度和温度有关,碳化钙含量越高,导电性能越好;反之,碳化钙含量越低,导电性能越差。
当碳化钙含量下降到70%~65%间,其导电性能达到最低值,若碳化钙含量继续下降,则其导电性能复又上升,见图2。
3. 电石的化学性质电石的化学性质很活泼,在适当温度下能与许多的气体、液体发生化学反应。
电石厂控制指标
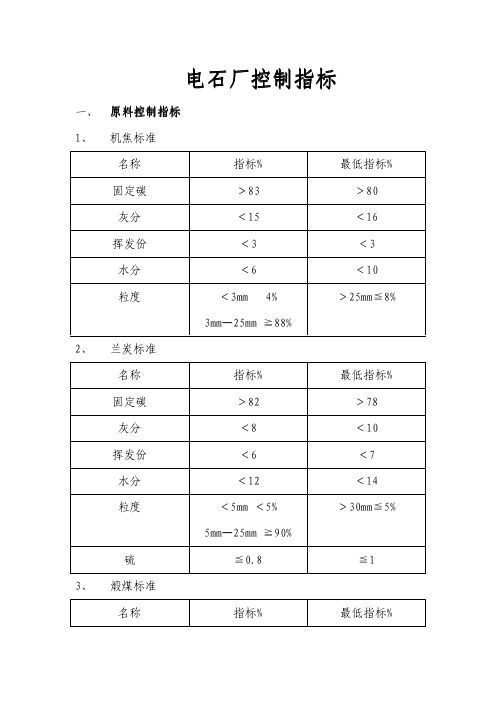
≧270 <5 <5
指标%
最低指标%
固定碳
>84
>84
灰分
<5
<6
挥发份
10——12.5
10——12.5
9、 矿石标准
名称
指标%
最低指标%
碳酸钙
>96
>95
氧化镁
<1
<1
二氧化硅
<1
<1
磷(P)
<0.008
<0.01
硫(S)
<0.1
<0.5
注:此项指标仅对石灰供应厂家不定期抽检
二、 原料入库目测验收标准
名称
外水分
粉末%
粒度
杂质
机焦
到厂不滴水 ≤3mm≤4% ≤25mm 不明显
兰炭
到厂不滴水 ≤5mm≤5% ≤30mm 不明显
煅煤
到厂不滴水 ≤3mm≤5% ≤25mm 不明显
块煤
到厂不滴水 ≤3mm≤1%
不明显
标煤
到厂不滴水 ≤3mm≤5% ≤30mm 不明显
洗标煤
到厂不滴水 ≤3mm≤5% ≤30mm 不明显
>88 <9 <2 <1.5 >25mm≦5%
≦1
指标% >84 <8 <6 <1 <3mm <4% 3mm—30mm ≧90% ≦0.8
最低指标% >80 <9 <7 <1.5
>30mm≦6%
≦1
指标% >90 <3 <6 <3
最低指标% >86 <4 <7 <4
粒度
硫 6、 块煤标准
名称 固定碳 灰分 挥发份 水分 7、 石灰标准 名称 全 CaO 有效 CaO 氧化镁 二氧化硅 粒度
H2S
<0.15
企业标准
电石生产工艺指标控制

生产工艺指标电炉生产工艺指标工艺控制指标.产品产量:150T—235T质量>305L/Kg(热样)炉料配比:石灰:碳素=100:62±2焦炭粒度:3—20mm石灰粒度:5—35mm石灰生过烧≤7%焦炭水份<1%电极压放1—16次/班出炉次数6—8次/班电极最大行程1200mm电极工作长度1.6—1.8m冷却水压力0.25—0.35Mpa冷却水回水温度≤45℃炉压10—50pa电极糊工艺控制指标:原料粒度:50-150mm≥90%炉气净化生产工艺指标工艺控制指标.电石炉炉气压力 10-50Pa炉气量最大4800NM3/h炉气温度 450-600℃除尘器入口温度 220-260℃净气管温度 220-260℃氮气压力 0.40MPa冷却水压力 0.40MPa压缩空气压力 0.60MPa一氧化碳爆炸区间(含5%氧时)上限75%下限12.5%氢气爆炸区间(含5%氧时)上限7.5%下限4.15%炉气爆炸区间(含5%氧时)上限75%下限11-12%除尘器室正常压力 1500-2500Pa除尘器室安全阀开启压力 0.4MPa进净化系统的含尘量: <150g/NM3出除尘器含尘量: <50mg/NM3炉气泄漏率: <0.05%烟尘堆积密度: 0.45t/m3主要设备的操作指标及技术参数除尘器入口温度 220-260℃净气管温度 220-260℃除尘器室正常压力 1500-2500Pa除尘器室安全阀开启压力 0.4MPa原材料或其他材料的质量要求在操作炉气净化到气混烧窑时,必须保持电石炉操作正常,进行氮气置换,检验合格后方可进行炉气使用。
中间品或成品的质量指标控制范围及分析一氧化碳爆炸区间(含5%氧时)上限75%下限12.5%氢气爆炸区间(含5%氧时)上限7.5%下限4.15%炉气爆炸区间(含5%氧时)上限75%下限11-12%2.5 排放物及指标要求一氧化碳排放标准0~62.5mg/m3干燥工艺控制指标生产工艺指标见表1。
电石生产工艺安全控制指导意见
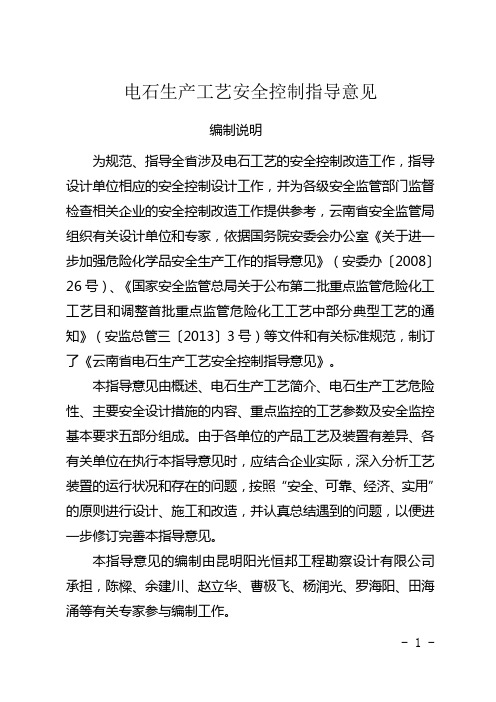
电石生产工艺安全控制指导意见编制说明为规范、指导全省涉及电石工艺的安全控制改造工作,指导设计单位相应的安全控制设计工作,并为各级安全监管部门监督检查相关企业的安全控制改造工作提供参考,云南省安全监管局组织有关设计单位和专家,依据国务院安委会办公室《关于进一步加强危险化学品安全生产工作的指导意见》(安委办〔2008〕26号)、《国家安全监管总局关于公布第二批重点监管危险化工工艺目和调整首批重点监管危险化工工艺中部分典型工艺的通知》(安监总管三〔2013〕3号)等文件和有关标准规范,制订了《云南省电石生产工艺安全控制指导意见》。
本指导意见由概述、电石生产工艺简介、电石生产工艺危险性、主要安全设计措施的内容、重点监控的工艺参数及安全监控基本要求五部分组成。
由于各单位的产品工艺及装置有差异、各有关单位在执行本指导意见时,应结合企业实际,深入分析工艺装置的运行状况和存在的问题,按照“安全、可靠、经济、实用”的原则进行设计、施工和改造,并认真总结遇到的问题,以便进一步修订完善本指导意见。
本指导意见的编制由昆明阳光恒邦工程勘察设计有限公司承担,陈樑、余建川、赵立华、曹极飞、杨润光、罗海阳、田海涌等有关专家参与编制工作。
一、概述电石生产是以石灰和炭素材料(焦炭、兰炭、石油焦、冶金焦、白煤等)为原料,在电石炉内依靠电弧热和电阻热在高温下进行反应生成电石的过程,化学反应式:GaO+3C→CaC2+CO。
开放型电石炉多为人工加料,生产工艺落后,能耗高,“十一五”期间,已经被强制淘汰。
以电石炉结构划分,目前运行的电石炉分为:内燃式和密闭式。
内燃式电石炉是在电石炉上增加了炉盖、自动或半自动的加料系统和除尘器,使得电石生产过程中生成的一氧化碳在炉内燃烧后的烟气,被置于炉上的吸气罩抽出,送至其他装置系统进行热能再利用。
密闭电石炉中的电化学反应在密闭环境中进行,外部的空气不能进入反应电石炉内,反应生成的一氧化碳气体被抽出,经除尘、净化后送至其他装置作为化工原料或燃料使用。
电石厂控制指标
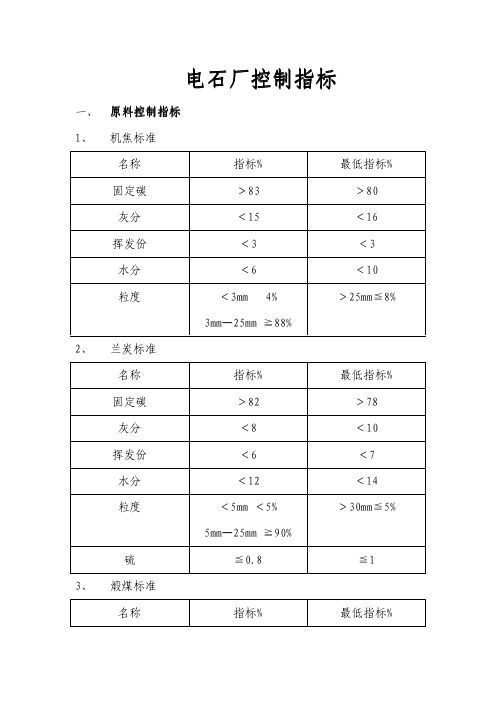
52678
124
120
指标 <120 4——5
指标 142 206 <15 <150 950——1100 580——1000 1.5——2 50——80 750±10 <50
指标 0.15——0.2
2
冷却水回水温度
3ቤተ መጻሕፍቲ ባይዱ
投料次数
4
每炉熔炼时间
八、 电石标准
指标名称
优级品
乙炔发气量
305
PH3
<0.08%
H2S
<0.15
企业标准
305
℃ 次/小时
分钟
一级品 285
<0.08% <0.15
285
<50 4——5
80
合格品 255
<0.08% <0.15
270
容量
一次侧
二次侧
接位
KVA
电压 V 电流 A 电压 V 电流 A
1
160
45105
2
3
12500
154
46863
206
148
48763
4
142
50823
5
35000
137
6
12135
200
133
7
11679
193
8
11314
187
9
10949
181
五、 电极糊加料标准
项目
单位
电极糊投入块度
mm
电极糊柱高度
活性 生烧 过烧 8、 电极糊 名称
<3mm <5% 3mm—25mm ≧90%
≦0.8
>25mm≦5% ≦1
指标% >87 <8 <6 <1
电石用兰炭指标
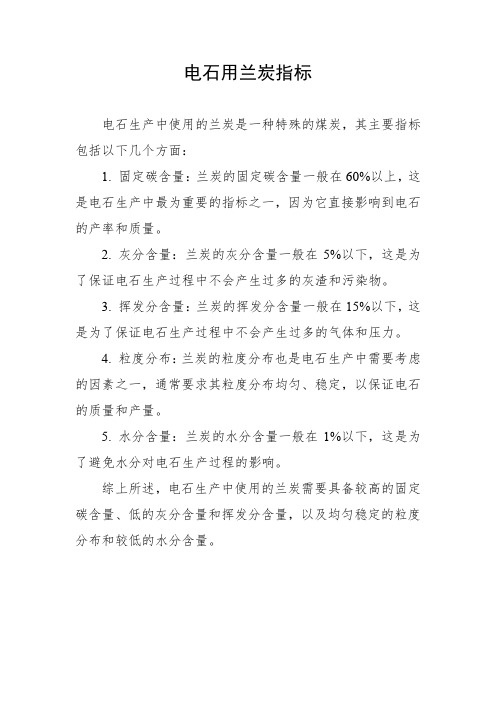
电石用兰炭指标
电石生产中使用的兰炭是一种特殊的煤炭,其主要指标包括以下几个方面:
1. 固定碳含量:兰炭的固定碳含量一般在60%以上,这是电石生产中最为重要的指标之一,因为它直接影响到电石的产率和质量。
2. 灰分含量:兰炭的灰分含量一般在5%以下,这是为了保证电石生产过程中不会产生过多的灰渣和污染物。
3. 挥发分含量:兰炭的挥发分含量一般在15%以下,这是为了保证电石生产过程中不会产生过多的气体和压力。
4. 粒度分布:兰炭的粒度分布也是电石生产中需要考虑的因素之一,通常要求其粒度分布均匀、稳定,以保证电石的质量和产量。
5. 水分含量:兰炭的水分含量一般在1%以下,这是为了避免水分对电石生产过程的影响。
综上所述,电石生产中使用的兰炭需要具备较高的固定碳含量、低的灰分含量和挥发分含量,以及均匀稳定的粒度分布和较低的水分含量。
电石工艺规程(修改版)

鄂尔多斯氯碱化工有限公司电石生产工艺规程签发:审核:编制:文件编号:SC/ZD-07分发号:执行单位:氯碱化工分公司执行时间:2015年5月5日鄂尔多斯氯碱化工公司二〇一五年五月五日目录一.产品说明 (2)二.原、辅助材料质量指标 (6)三. 电石生产原理 (7)四.工艺流程简述 (25)五. 工艺控制指标 (25)六. 产品、中间产品及原材料检验要求 (26)一.产品说明1.简介化学名:碳化钙工业名:电石(英文名:Calcium carbide)分子式:CaC2C结构式:CaC分子量:64.102. 电石的物理性质2.1 外观化学纯的碳化钙几乎是无色透明的晶体。
极纯的碳化钙是天蓝色的大晶体,颜色象淬火钢。
工业电石是碳化钙和氧化钙以及其他杂质合成的混合物,根据杂质含量的不同呈黄色或黑色,含碳化钙较高时呈紫色。
电石的新断面具有光泽,吸水后失去光泽呈灰白色。
2.2 密度18℃时,纯电石的相对密度为2.22。
工业电石的密度与其碳化钙的含量关系见表1。
CaC含量%90 80 70 60 50 40 302密度g/cm3 2.24 2.32 2.40 2.50 2.58 2.66 2.74 2.3 熔点电石的熔点随电石中碳化钙含量的改变而改变,纯碳化钙的熔点为2300℃。
碳化钙的含量在69%的混合物的熔点最低,为1750℃。
碳化钙的含量继续减少时,熔点反而升高,后降到1800℃,此时混合物中碳化钙含量为35.6%。
在此二个最低熔点(1750~1800℃)之间有一个最大值1980℃,它相当于含碳化钙52.5%的混合物。
随着碳化钙含量继续减少(即低于35.6%)混合物的熔点又升高。
见下图。
影响电石熔点的因素不仅是石灰的含量,氧化铝、氧化硅和氧化镁等杂质也有影响。
2.4 导电性电石能导电,其导电性与电石的纯度和温度有关,碳化钙含量越高,导电性能越好;反之,碳化钙含量越低,导电性能越差。
当碳化钙含量下降到70%~65%间,其导电性能达到最低值,若碳化钙含量继续下降,则其导电性能复又上升,见图2。
矿热炉电石生产工艺、入炉深度与电气理论、电流电压控制等参数的探讨

矿热炉电石生产工艺、入炉深度与电气理论、电流电压控制等参数的探讨一、关于电极入炉深度:电石炉电极入炉深度,始终是电石生产行业所关注的的核心话题,电石厂也去过许多电石企业进行学习,同时也对电极入炉深度的问题进行探讨,大部分企业都认为电极入炉深度应控制在1000mm以上,而且作为工艺参数进行严格控制。
但电极入炉1000mm以上的理论依据从何而来?经过查阅电石生产资料与文献,很多都会提及电极入炉,但没有明确具体的数值,仅在资料中发现两处描述: 第一段描述为:炉子主要用电阻熔炼,为此,电极头应保持在炉料面以下1100-1300毫米。
操作过程中,通过经验会得出更精确的数字。
第二段描述为:为了保持炉子工作良好和平稳,电极渗透性良好,并且所有电极都要相同。
这可以通过测量从电极头到炉底的距离来控制,度量应按需要时进行,但至少每隔一天度量一次。
电极头和炉底之间的最佳距离要求为1.1-1.3米,但可按经验确定。
看似两段描述的数据相互矛盾,但仔细推敲,第一段描述中明确指出电极头在炉料面以下1100-1300毫米,电石炉料柱距离炉壳上沿距离为430mm左右,入料深度较入炉深度多430mm,如果料柱烧损,则入料深度与入炉深度的差值会更大。
第二段关于电极入炉的描述,是写在电石炉启动阶段,入炉深度的描述与电石炉实际启动阶段的入炉深度一致。
对于27000KVA电石炉来说,电石炉炉膛深度为2650mm,底部铺300mm碳,底焦上放置启动缸,其高度为1500mm,内部填满焦炭,三相电极正是座在启动缸顶部,所以此时电极入炉850mm,在送电后星接电压较低,为了尽快提高炉底温度,必须将电极下降400mm左右,此时电极端头距炉底1400mm,但随着电石炉负荷的提升,电压、电流会逐渐增大,电极势必会上升,电极上升的程度也要视炉料电阻的大小,根据以往生产过程,一般会上升800mm以上,这也是电石炉启动必须要经历的过程,也就是说在正常生产时,电极入炉会在450mm左右,这里说的入炉深度是以炉壳上沿为基准进行描述的,如考虑料柱高于炉壳上沿及料柱烧损情况,入料深度为880-1300mm,与资料中描述差距不大。
- 1、下载文档前请自行甄别文档内容的完整性,平台不提供额外的编辑、内容补充、找答案等附加服务。
- 2、"仅部分预览"的文档,不可在线预览部分如存在完整性等问题,可反馈申请退款(可完整预览的文档不适用该条件!)。
- 3、如文档侵犯您的权益,请联系客服反馈,我们会尽快为您处理(人工客服工作时间:9:00-18:30)。
生产工艺指标
电炉生产工艺指标
工艺控制指标.
产品产量:150T—235T
质量>305L/Kg(热样)
炉料配比:石灰:碳素=100:62±2
焦炭粒度:3—20mm
石灰粒度:5—35mm
石灰生过烧≤7%
焦炭水份<1%
电极压放1—16次/班
出炉次数6—8次/班
电极最大行程1200mm
电极工作长度1.6—1.8m
冷却水压力0.25—0.35Mpa
冷却水回水温度≤45℃
炉压10—50pa
电极糊工艺控制指标:原料粒度:50-150mm≥90%
炉气净化生产工艺指标
工艺控制指标.
电石炉炉气压力 10-50Pa
炉气量最大4800NM3/h
炉气温度 450-600℃
除尘器入口温度 220-260℃
净气管温度 220-260℃
氮气压力 0.40MPa
冷却水压力 0.40MPa
压缩空气压力 0.60MPa
一氧化碳爆炸区间(含5%氧时)上限75%下限12.5%氢气爆炸区间(含5%氧时)上限7.5%下限4.15%炉气爆炸区间(含5%氧时)上限75%下限11-12%
除尘器室正常压力 1500-2500Pa
除尘器室安全阀开启压力 0.4MPa
进净化系统的含尘量: <150g/NM3
出除尘器含尘量: <50mg/NM3
炉气泄漏率: <0.05%
烟尘堆积密度: 0.45t/m3
主要设备的操作指标及技术参数
除尘器入口温度 220-260℃
净气管温度 220-260℃
除尘器室正常压力 1500-2500Pa
除尘器室安全阀开启压力 0.4MPa
原材料或其他材料的质量要求
在操作炉气净化到气混烧窑时,必须保持电石炉操作正常,进行氮气置换,检验合格后方可进行炉气使用。
中间品或成品的质量指标控制范围及分析
一氧化碳爆炸区间(含5%氧时)上限75%下限12.5%
氢气爆炸区间(含5%氧时)上限7.5%下限4.15%
炉气爆炸区间(含5%氧时)上限75%下限11-12%
2.5 排放物及指标要求
一氧化碳排放标准0~62.5mg/m3
干燥工艺控制指标
生产工艺指标见表1。
表1 工艺制指标
主要设备的操作指标及技术参数。
主要设备操作指标。
主要设备操作指标见表2。
表2 主要设备操作指标
石灰窑生产工艺指标
工艺控制指标.
料位:距料尺零位1米;
助燃风机流量:9000~11000m3/h,风压:14~15Kpa,风温30~50℃
冷却风机流量:6000~7000 m3/h,风压:14~15Kpa,风温30~50℃
增压风机流量:3600~4800 m3/h,风压:14~15Kpa,风温220~250℃
焙烧带温度:900℃~1100℃
废气支管温度:270℃~350℃
窑顶中心废气温度:250℃~350℃
废气总管温度:250℃~300℃
压缩空气压力:0.4~0.8Mpa
氮气压力:0.3~0.5Mpa
冷却水温度:≤20℃,压力:0.3~0.5Mpa
主要设备的操作指标及技术参数
风机轴承座温度≤60℃
电机温度≤70℃
原材料或其他材料的质量要求
石灰石质量指标:
说明:A、来料粒度小于40mm的<5%,大于80mm的<5% ,大于100mm的为0。
B、含泥量<2%。
碳素质量指标
电石炉尾气参数
说明:A、电石炉尾气热值:2500~2800kcal/Nm3。
B、电石炉尾气温度:200~250℃(保证炉气中的焦油不析出)。
C、正常生产状态下到达石灰窑车间总管末端时电石炉尾气压力≥14Kpa。
中间品或成品的质量指标控制范围及分析
石灰窑顶废气经除尘净化后含尘浓度≤50mg/m3
循环水生产工艺指标
工艺控制指标
一体化净水器工艺控制指标:
原水水质:浑浊度≤10000度,PH值为6.5~8.5;进水总管直径DN200mm,进水总管压力为0.2~0.5MPa。
出水量及水质:
装置出水总量≥200 m3/h。
原水浑浊度<3000度时,出水浊度:≤5度。
原水浊度3000~5000度时,出水浊度:≤8度。
凉水塔工艺控制指标:
有效处理量:3300 m3/h,出水温≤33℃,水飘率≤0.002%,噪音:≤75Db,运行电流≤65A,进水温度≤50℃,出水温度≤33℃,进出水温差△t≥17℃。
最高湿球温度29℃。
蜗壳式离心水泵工艺控制指标
热水泵:进口压力为常压,出口压力0.2MPa,流量1450 m3/h。
循环水泵:进口压力为常压,出口压力0.58MPa,流量950 m3/h。
冷却水泵:进口压力为常压,出口压力0.5MPa,流量180 m3/h。
生活水泵:进口压力为常压,出口压力1.05MPa,流量25 m3/h。
造气站生产工艺指标
工艺控制指标.
氮气流量≥540Nm3/min,纯度≥98.5%(V/V),压力≥0.6MPa。
冷却水量≤8 m3/h,进水压力0.2~0.4MPa,进水口温度1~32℃。
氮气露点≤-40℃,压缩空气供气温度≤45℃,压缩空气消耗量≤1300 Nm3/min。
空气流量≥14Nm3/min(20℃,101.325KPa),含油量≤3ppm,排气压力≥0.75MPa(表压),噪声≤75dB,冷却水量≤7 m3/h,进水口压力0.2~0.4MPa,进水口温度1~32℃·
原料指标密闭电石炉的原料指标指的是石灰石的原料指标和还原剂--炭的指标
石灰石
1)质量要求如下:
CaCO3 ≥96%
SiO2 ≤1.0%
Al2O3 ≤1.0%
MgO ≤1.0%
粒度20~60mm
2)炭材质量要求如下:
含固定碳≥82%
灰分<15%
挥发分<1.5%
水分<15%
粒度3~25mm
[导读]碳化钙(CaC2)俗称电石。
工业品呈灰色、黄褐色或黑色,含碳化钙较高的呈紫色。
其新创断面有光泽,在空气中吸收水分呈灰色或灰白色。
能导电,纯
关键词:
碳化钙(CaC2)俗称电石。
工业品呈灰色、黄褐色或黑色,含碳化钙较高的呈紫色。
其新创断面有光泽,在空气中吸收水分呈灰色或灰白色。
能导电,纯度愈高,导电性愈好。
在空气中能吸收水分。
加水分解成乙炔和氢氧化钙。
与氮气作用生成氰氨化钙。
电石是有机合成化学工业的基本原料之一。
是乙炔化工的重要原料。
由电石制取的乙炔广泛应用于金属焊接和切割。
生产方法有氧热法和电热法。
一般多采用电热法生产电石,即生石灰和含碳原料(焦炭、无烟煤或石油焦)在电石炉内,依靠电弧高温熔化反应而生成电石。
生产流程如图所示。
主要生产过程是:原料加工;配料;通过电炉上端的入口或管道将混合料加入电炉内,在开放或密闭的电炉中加热至2000℃左右,依下式反应生成电石:GaO+3C→CaC2+CO。
熔化了的碳化钙从炉底取出后,经冷却、破碎后作为成品包装。
反应中生成的一氧化碳则依电石炉的类型以不同方式排出:在开放炉中,一氧化碳在料面上燃烧,产生的火焰随同粉尘—起向外四散;在半密闭炉中,一氧化碳的一部分被安置于炉上的吸气罩抽出,剩余的部分仍在料面燃烧;在密闭炉中,全部一氧化碳被抽出。
图电石生产工艺流程图。