纱线的强力与强力不匀
整经时纱线的张力对织造工序和织物质量的影响

书山有路勤为径;学海无涯苦作舟
整经时纱线的张力对织造工序和织物质量的影响
整经时纱线的张力对织造工序和织物的质量有重要影响。
整经时要求单纱与片纱张力尽量均匀一致。
张力过大,纱线会过分伸长,强力与弹性会有损失;张力过小,会使经轴或织轴卷绕不平整。
张力不匀,会造成织造时开口不清,会影响织物的外观质量及布面平整度。
影响整经张力的因素:整经张力由单纱退绕张力、张力装置引起的张力、导纱机件磨擦所引起的张力。
1.单纱退绕绕力:
筒子退绕时,纱线会形成气圈,气圈的回转速度与表面的磨擦状况,会
影响退绕张力的大小。
(1)筒子短片段退绕时张力的变化:
(2)整只筒子纱退绕时张力变化:
2.张力装置产生的张力:
一般情况退绕张力很小,不能满足经轴卷绕密度和良好成形要求,需采
用附加张力装置,使纱线具有必要张力。
筒子架上张力装置的作用原理分累加法和倍积法两大类。
(1)垫圈式张力装置:
(2)双柱压力盘式张力装置
(3)无柱双张力盘张力装置
(4)单盘无柱式、压辊式和双罗拉式(Hacoba)
3.导纱距离对退绕张力的影响:
整经时的导纱距离指筒管顶部在导纱瓷眼间距,当导纱距离不同,纱线
的平均张力发生变化。
专注下一代成长,为了孩子。
纱线品质评定
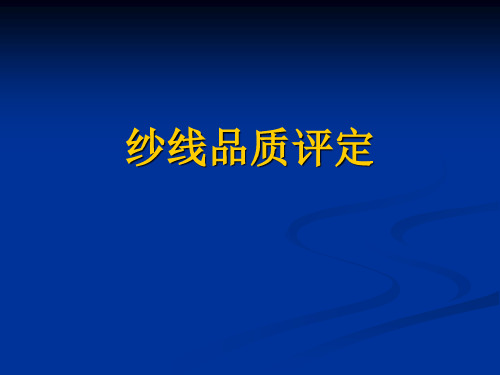
棉纱的评等项目
单纱断裂强力变异系数 百米质量变异系数 条干均匀度 1克棉纱内棉结粒数 1克棉纱内棉结、杂质总粒数共5项 保证条件(前提):单纱的断裂强度和百
米质量偏差。
棉纱品质评定的评定方法
1)棉纱的评等按质量指标分为优等、一等、 二等,低于二等作为三等。5个评等项目分 别评等。
2)当单纱的断裂强度和百米质量偏差超出 允许范围时,在单纱断裂强力变异系数和 百米质量变异系数原评等的基础上顺降一 个等别,如2项都超出范围时,只顺降一次, 降至二等为止。
百米质量变异系数和百米质量偏差的检验
1)摇取缕纱:据细纱机开台数,共拔取30个纱管, 在周长为1m的纱框式缕纱测长仪上,每只管纱摇 取一缕纱(张力为0.5 cN/tex),共30缕,每缕长 100m,摇好后将纱头尾接好,接头长度不超过 1cm。
2)逐缕称重:将30缕纱在电子天平上逐缕称重, 精确至0.01g。
纱线品质评定
目的要求
通过实验,要求掌握棉纱品质评定的 依据和试验方法,对给定的纱线按规 定的品质要求,通过检验,定出等级。
基本知识
1. 纱线的品质评定就是对纱线按照规定的品质 要求,通过检验定出等级,作为厂、销商贸进行 纱线品质考核及实行优质优价的依据。
2. 品质评定必须依据一定的标准,我国的标准 分为国家标准、行业标准、地方标准和企业标准, 其中适合纺织行业的有国家标准和行业标准。国 家标准是由国家标准化组织经法定化程序制定、 发布的标准;行业标准是由行业标准化组织制定, 由国家主管部门批准、发布的标准,它适用于纺 织行业的各个专业。标准的内容包括:产品品种 规格、技术要求、试验方法、检验规则、包装、 标志等。
3)测定回潮率:将30缕纱称其总重,用烘箱法测 其干重。
纱线各项物理性指标

纱线各项物理性指标一、百米干重量:指100m纱线的干燥重量。
如21s纱的百米干重量为二、重量偏差:指为确保纱线的支数不变,所规定的单位长度的纱线重量偏差范围。
例如:某21s纱线的重量偏差为±2%,是否合理(1)百米干定量=号数÷÷10 (2)号数=由两公式我们可求得20s、21s、22s的百米干定量分别为、、再由21s的百米干定量计算±2%的偏差值得、,没有超出一个支数,所以它是合理的。
三﹑重量CV(%):衡量每段纱线的重量不匀率,又称支数的变异系数。
四、条干CV(%):指纱线主体的粗细、重量均匀度。
1. CV值学名变异系数,又称标准差率。
是衡量资料中各观测值变异程度的一个统计量。
其作用是反映单位均值上的离散程度,常用在两个或多个总体均值不等的离散程度比较上。
若两个总体的均值相等,则比较标准差系数与比较标准差是等价的。
2. 标准差也称均方差。
标准差反映的是一组数据的离散程度,平均数相同的,标准差未必相同。
3. 例如:A:45、55、65、75、85、95 平均数:70 标准差:B:67、68、69、70、71、72 平均数:70 标准差:可以看出B的离散程度小于A。
上例是两组数据平均数相同情况下的,用均方差表示即可。
如果平均数不同,则要用CV值来表示其变异程度。
五、断裂强力、断裂强度与断裂强力变异系数CV(%)。
1. 断裂强力:指纱线所能承受的最大拉伸外力。
单位为N(牛)。
测试速度为5m/min。
2. 断裂强度:每特克斯所能承受的最大拉伸外力。
单位为N/tex。
特克斯即纱线的号数。
3. 断裂强力变异系数CV(%):纱线的强力不匀率。
六﹑纱疵:粗节+50%、细节﹣50%、棉结+200%1. 粗节+50%:纱线直径超过纱线主体50%的部分。
单位:个/km。
2. 细节﹣50%:纱线直径小于纱线主体50%的部分。
单位:个/km。
3. 棉结:是由纤维、未成熟棉或僵棉,因轧工质量不良或纺纱过程中处理不善集结而成。
如何改善和降低毛纱线条干不匀率
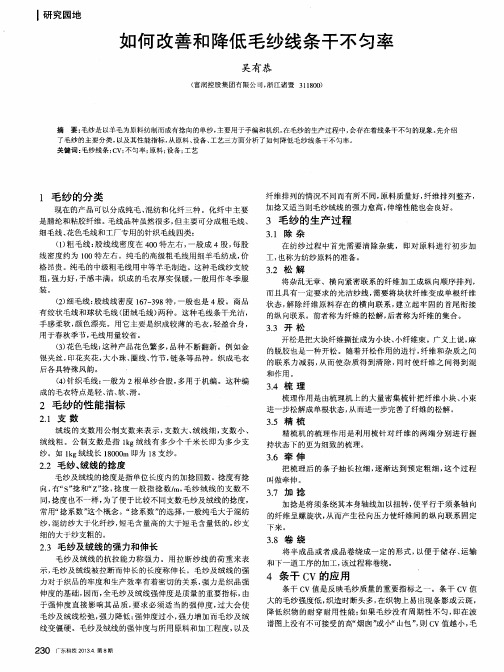
2 毛纱的性能指标
2.1 支 数 绒线 的支数用 公制支数 来表示 ,支数大 、绒 线细 ,支数小 、
绒 线 粗 。 公 制 支 数 是 指 1 绒 线 有 多 少 个 千 米 长 即 为 多 少 支 纱 。如 lkg绒 线 长 18000m 即 为 18支 纱 。
2.2 毛纱 、绒线 的捻 度
将半成 品或者成 品卷绕成 一定 的形 式,以便于储 存 、运输 和 下 一 道 工 序 的 加 工 ,该 过 程 称 卷 绕 。
4 条干 CV的应用
条干 CV值是反映毛纱质量 的重要指标之 一 。条干 CV值 大 的毛纱强度低 ,织造时断头多 ,在织物上易 出现条影或 云斑 , 降低 织 物 的 耐 穿 耐 用 性 能 ;如 果 毛 纱 没 有 周 期 性 不 匀 ,即 在 波 谱 图上没有不可接受的高“烟 囱”或小“山包”,则 CV值 越小 ,毛
2-3 毛纱 及绒 线 的强力 和伸 长
毛纱及绒 线的抗拉 能力称强力 。用 拉断 纱线 的荷 重来表 示,毛纱及绒 线被 拉断而伸 长的长度称伸长 。毛纱及绒线 的强 力 对 于 织 品的 牢 度 和 生 产 效 率 有 着 密 切 的关 系 ,强 力 是 织 品强 伸度的基础 ,因而 ,全毛纱及绒线强伸度是质量 的重要指 标,由 于强伸度直接 影响其 品质 ,要求必须适 当 的强伸度 ,过大会使 毛纱及绒线松弛 ,强力降低 ;强伸度过小 ,强力增加而毛纱及绒 线变僵硬 。毛纱及绒线 的强伸度与所用 原料和加 工程 度,以及
项目三纱线质量检验

• 1.线密度特数Nt(tex)俗称号数,是指1000米长的纱线在 公定回潮率时的重量克数。是法定计量单位。其计算式如 下:
•
特数:Nt=Gk/L×1000
•
标准重量 Gk=G0(1+wk%)
•
对于棉纱:Wk=8.5%
采用绞纱称重法测试
• 特数的换算关系:1tex=10 dtex;
1tex=1000 mtex;
• 股线细度表示法
– 特数制: 单纱特数合股数 ,如:14tex 2
•
单纱特数相加 如: 16tex+18tex
– 支数制:单纱支数/合股数,如26/2
•
单纱支数倒数和的倒数
– 复丝细度表示法:
•
复丝总旦数/单丝根数, 如150D/48F
.股线细度的表达 用单纱细度和单纱根数n的组合来表达。
(1)特数制 当组成股线的单纱细度相同时,则股线细度
纱线试样总干重 (1 纱线试样总长度
Wk
)
1000
(tex)
纱线试样总干重量=每缕纱干重量×纱线试样缕数。
纱线试样总长度=每缕纱长度×纱线试样缕数。
2.纱线的线密度偏差
N t
Nta Nt
Nt
100%
n
3.重量变异系数CV=
1 X
(Xi X )2
i 1
n 1
(二)、纱线细度不匀率
1、纱线的细度偏差 是指由于纺纱工艺、设备和纺纱操作等 原因,使实际生产出的纱线的细度与设计的纱线细度会有 一定的偏差,根据纱线采用的细度指标不同而异,分别为 重量偏差(也称线密度特数偏差)、旦数偏差和支数偏差。 纱线的细度偏差一般用重量偏差 Nt来表示。
成纱强力的影响因素及改进措施

成纱强力的影响要素及改良举措要使织物拥有必定的强力和坚牢度,一定使纱线拥有必定的强力,纱线强力是评论纱线质量的重要指标。
表示纱线强力的指标可分为绝对强力和相对强力两大类。
绝对强力是指纱线受外力直接拉伸到断裂时所需要的力,也叫断裂强力。
用牛顿(N)或厘牛(CN)表示..。
纱线断裂的原由:纱线断裂是由一部分纤维断裂、一部分纤维滑脱。
也就是断面纤维滑脱根数减少、断面处单根纤维强力低、不匀率大;纱中纤维之所以滑脱,主假如因为纤维长度短、短绒齐集,纤维卷曲少、纤维柔度差、纤维之间抱协力差。
影响成纱的强力要素:1原料性能、如长度、的线密度、断裂长度等;2、纺纱工艺过程对影响性能影响程度;3、成纱构造,如纤维的挺直平行及在纱线的摆列散布状况,纱线的捻度大小等;4、成纱均匀度,如重量不匀率和条干不匀率以及捻度不匀率等。
因为断裂老是在最纤弱处发生。
提升成纱强力主要应从合理选择原料、减少混淆差别、提升前纺半制质量量、改良半制品与成纱构造、提升细纱条干以及合理选择捻系数等方面着手。
纱线强力也是一个系统工程,重要的是解决强力衰环。
解决强力衰环,看拟简单,实质是比较难做到的一件事。
涵盖方面太广。
一句话:细节决定成败!1/7原纱的强力特点包含均匀强力、强力不匀率、均匀伸长及伸长不匀率。
一般经纱均匀强力在15cN/tex,强力CV%在9%~10%左右,纬纱均匀强力12cN/tex,强力CV%9%~10%左右。
均匀断裂伸长,一般都控制在2%之内。
喷气织机停台的重要强力指标是强力衰环即最低强力,一般以为纱线细度仅为正常纱的40%时,这类细节弱环必定惹起断头,造成停台,假如强力衰环在4cN/tex,伸长率低于2%,必定会造成断头。
其强力衰环除了细节疵点占61%之外,其余弱捻、接头不良,含杂粗节等也会造成经纬间停台,约占39%。
原纱上的细节主要有三类:一种短绒细节,一种是粗细节结头处,另一种长细节或多个短细节连在一起的都会惹起断头。
纱线质量标准

第一章 纱线质量标准
第一节 棉纱质量标准
作为售纱和企业下道工序输入的半制品,本 白棉纱的检验分等,一般按国家技术监督局 发布的GB/T398-93执行。由于未再制定新的 标准,因此,国内多数厂家只用此标准评定 纱线等级,而更多是用乌斯特公报来衡量纱 线质量。
一、国内有六项指标 1 单强 2 Nhomakorabea强不匀 3 条干:Uster条干、黑板条干 4 重量不匀率 5 重量偏差 6 纱疵点:10万米纱疵、 黑板条干纱疵
1、普梳棉纱技术要求(参见书上表) 2、精梳棉纱技术要求(参见书上表) 二、Uster的2001公报 参见书上公报统计。
第二节
毛纱线质量标准
一般毛纱线均作为企业内部的半制品加以考核,没有国 家标准,只有行业标准或地方企业标准。 一般以物理指标分等,外观疵点分级, 分等指标有: ①特数偏差;②重量不匀;③捻度不匀; ④平均强力不小于CN(断裂长度);⑤低档纤维含量; ⑥含油率;⑦染色牢度。 其中⑤⑥⑦三项指标是在售纱时考虑 分级指标有:①纱疵 ②大肚纱 用黑板条干或uster条干 粗纺、精纺参见书上表。
第三节 苎麻纱质量标准
部颁标准 FZ/T32002-92 以纱的内在质量:强力及不匀、重量不 匀、重量偏差定等。 以纱的外观质量:条干均匀度、粗细节、 麻粒定级。 股线:以单纱强力及不匀、重量偏差定 等,以粗节定级。 数据参见书上表。
第四节 绢丝质量标准
部颁标准FZ/T42002-97 桑蚕绢丝指标: ①断裂长度; ②支数不匀; ③条干不匀; ④洁净度; ⑤千米疵点数;⑥支数偏差; ⑦强力不匀; ⑧断裂伸长度; ⑨捻度偏差率;⑩捻度不匀率。 其中:②③⑤对织物外观有影响 ③④⑤用黑板观察
成纱强力影响因素及提高措施

成纱强力影响因素及提高措施胡振龙赵卫华(东营市宏远纺织有限公司)纱线强力是评价纱线质量的重要指标,有绝对强力和相对强力之分。
影响成纱强力的主要因素有:原料性能(纤维长度、细度、单纤维强力等)、纺纱工艺、成纱结构(纤维伸直度、平行度、排列分布、纱线捻度等)、成纱均匀度(条干不匀率、捻度不匀率)等。
因此提高成纱强力要从合理选择原料、改善须条结构、提高成纱条干、合理选择捻系数等方面入手。
1 原料与成纱强力的关系1.1 纤维长度及整齐度与成纱强力的关系纤维长度长,整齐度好、短纤维少,则成纱光洁,强力高,见表1。
表1纤维长度及整齐度与成纱强力的关系1.2 纤维线密度与成纱强力的关系在其它条件相同的条件下,纤维的线密度小,成纱截面内纤维根数多,分布均匀,成纱条干均匀,纤维间接触面积大,摩擦力大,纱线在拉伸断裂时,滑脱纤维的根数将会减少,纱线强力就高。
1.3 单纤维断裂长度与成纱强力的关系单纤维断裂长度大,则成纱强力高。
单纤维强力差时,在纺纱过程中易断裂而形成短绒,被搓揉成结粒,恶化成纱条干,从而使成纱强力降低。
1.4 棉纤维性能与成纱强力的关系表棉纤维主要指标与成纱强力的关系见表2。
表2 棉纤维主要指标与成纱强力的关系2 纺纱工艺对成纱强力的影响2.1 清梳工艺在保证原料充分开松的情况下,尽可能避免猛烈打击,避免损伤纤维、增加短绒。
保证各种成分混合均匀,提高各单机运转效率,在保证前后供应的条件下,单机运转效率越高越好,尽量达到98%以上。
开清工序各单机要优化工艺参数,做到薄喂快给、柔和开松,以梳代打,合理减少打击点。
做到棉结、杂质、短绒兼顾。
实践中证明:开清工序的总除杂效率,在原棉含杂率小于1.5%时应保持在30-40%;原棉含杂率在1.5-2%之间时应保持在40-50%;原棉含杂率大于2.0%时应保持在40-60%,最基本的要求是要保证筵棉含杂率不高于1.0%。
确定了开清工序的总除杂效率后,要合理分配各单机的除杂率,控制棉结和短绒增长率。
- 1、下载文档前请自行甄别文档内容的完整性,平台不提供额外的编辑、内容补充、找答案等附加服务。
- 2、"仅部分预览"的文档,不可在线预览部分如存在完整性等问题,可反馈申请退款(可完整预览的文档不适用该条件!)。
- 3、如文档侵犯您的权益,请联系客服反馈,我们会尽快为您处理(人工客服工作时间:9:00-18:30)。
提高纤维长度,使纤维长度L> 2LC; 提高纱线中纤维间的抱合力和摩擦力。
3 影响成纱强力的因素
(1)原料性能; (2)纺纱工艺过程对纤维性能的影
响程度; (3)成纱结构; (4)成纱均匀度。
第二节 提高成纱强力
1 原料选配对成纱强力的影响
入细纱之前得到充分混合。
2.2 细纱工艺与成纱强力
2.2.1 细纱牵伸工艺对成纱强 力影响
提高成纱强力,细纱的牵伸 工艺应重点放在提高细纱均 匀度上,细纱条干不匀↑,则 强力↓,强力不匀率↑ 。
2.2.2 纱线结构和捻度与纱线强力
加捻程度对纱线性能的影响
有利因素:
纤维间的摩擦力增加,纱线由于纤维间滑脱而 断裂的可能性减少。
图2 混纺纱中1、2两 种纤维的拉伸曲线
(2)第二种混纺情况
拉伸的第一阶段是伸长能力较小的纤维先 断,此时,混纺纱承受的拉伸外力F1为:
(2)第二种混纺情况
紧接着到第二阶段,纤维2承担外力直至断裂,这时 混纺纱承担的外力F2为: F2 n2P2
式中:P2——纤维2的断裂强力。
当纤维2的含量比较小时: n1P1 n2P2 n2P2
加捻使纱线在长度方向的强力不均匀性降低。
不利因素 :
纤维对纱线轴向的分力减小,从而使纱线的强 力降低。
纱线加捻过程中使纤维承受了预负荷,外层纤 维比内层承受了更多的预负荷,预负荷的增加 使纱线承受外力的能力降低,加之内外层负荷 分配不匀,表现为纱线强力的下降。
在捻系数达到临界捻系数之前,有利因素起主导地位,随着捻系数的增加成纱强力增加,捻系数超过 临界捻系数之后,不利因素起主导作用,随着捻系数的增加,纱线强度反而下降。
纱线中纤维滑脱的原因
纤维长度短; 短绒积聚; 纤维卷曲; 纤维柔软度差; 纤维之间抱合力差。
2 纱线拉伸断裂过程
纱线强力P的计算公式:P=Q+F
P—纱线强力;Q—全部断裂纤维所构成的部分强力 ;F—全部滑脱纤维所构成的部分强力。
对于同一原料的纱线来说,应该设法提高Q,减少 F,即增加纱线断裂时断裂纤维的根数,减少滑脱 纤维根数,即提高纤维强力利用系数。
1.1 纤维长度及其整齐度与成纱强力
纤维长度比较短时,长度的增加对成纱 强力提高比较显著;当纤维长度足够长 时,长度对强力的影响就不很明显;
纤维长度整齐度越好,成纱强力越高 纤维长度越长,整齐度越好,成纱强力越高
1 原料选配对成纱强力的影响
1.2 纤维线密度与成纱强力
一般情况下,在纺纱特数相同的情况下,纺纱所用的纤维细 度越细,成纱强力越高;
2.1.2 合理制定并、粗工艺,提高半 制品均匀度
并条应配置合理的牵伸形式和牵伸工艺 ,以保证在牵伸过程中对纤维运动的控 制,才能保证良好的条干均匀度。
适当提高粗纱工序相对湿度、缩小牵伸 隔距,可稳定纤维运动,对提高条干均 匀度有利。且回潮率高时,牵伸后纤维 间内应力易于消失,能维持伸直平行的 状态。
则混纺纱的强力: P n1P1 n2P2
由于P1>P2,所以随着n2的增加,纱线的强力降低 当纤维2的含量比较大时: n1P1 n2P2 n2P2
则混纺纱的强力: P n2P2 可以看出,随着n2的增加,纱线的强力增加。
Hale Waihona Puke (2)第二种混纺情况以上分析可得出,混纺
纱的强力有可能出现比
强力小的纤维的纯纺纱
的强力还要小的情况。
如图所示曲线会出现小
凹点。
图3 混纺纱强力与混纺比的关系曲线
1.4 混纺纱各组分的强力和伸长对纱线强力的 影响
(3)当混纺在一起的 两种纤维的断裂伸长 率相差较大,且纤维1 断裂时的强力小于纤 维2在纱线中受到的拉 伸力,两种纤维的拉 伸曲线如图所示:
图4 混纺纱中1、2两 种纤维的拉伸曲线
3 车间温湿度与纱线强力
纤维吸湿后,物理机械性能会发生变化
棉纤维吸湿后横切面膨胀,刚度↓ ,塑性变形↑ ,纤维变的 柔软,容易变形;
回潮率↑ ,纤维表面摩擦系数↑ ,纤维间的抱合力和摩擦力 ↑ ,纱线强力↑;
回潮率↑,静电排斥现象↓,纤维间的抱合力和均匀性↑,纱 线强力↑。
所以,在纱条回潮率适当偏高的情况下进行纺纱,不 但能提高纱线的强力,而且能改善细纱条干和外观。
滑脱长度(LC)
2 纱线拉伸断裂过程
纱线的拉伸断裂过程
外层纤维首先逐步滑脱或断裂
外层纤维中小于2LC的短纤维首先被 抽拔滑脱,然后大于2LC的长纤维逐 步断裂。
由外向内第二层纤维滑脱或断裂 如此直至纱线完全解体
2 纱线拉伸断裂过程
纱线中纤维断裂的原因
断面纤维根数少; 单根纤维强力低; 断面处单根纤维强力不匀率大。
假设混纺纱中只有1、2两种纤维;纱线的断裂只 是由于纤维断裂而无滑脱;混纺纱中纤维混合均 匀;两种纤维线密度相同。在此假设下,混纺纱 的强力有三种情况。
(1)当两种纤维断裂伸长相同而强力不同时
当拉伸到伸长为1、2纤维的断裂伸长时,两种纤 维同时断裂,混纺纱的强力P为下式所示:
图1 混纺纱中1、2两 种纤维的拉伸曲线
(2)第三种混纺情况
拉伸的第一阶段是拉伸到伸长为纤维1的断 裂伸长时,纤维1首先断裂,此时混纺纱承 受的拉伸外力F1为:
(2)第三种混纺情况
紧接着到第二阶段,纤维2承担外力直至断裂,这时 混纺纱承担的外力F2为: F2 n2P2
式中:P2——纤维2的断裂强力。
当纤维2的含量比较小时: n1P1 n2P2 n2P2
梳棉机的机后还应加强短绒的排除,保证良好的漏底状态, 选用较合理的给棉板形式与工作面长度等。
2.1.1 合理配置清梳工艺,充分开松 ,减少短绒与棉杂
实践证明,减少梳棉机刺辊部分短纤维生成 并加大后车肚排除,锡林与盖板工作区采用 “紧隔距,强分梳”的工艺原则时,能充分 发挥分梳效能,并起到排除结杂与短绒的效 果,对提高成纱强力有利。
2.1.1 合理配置清梳工艺,充分开松,减少短绒与 结杂
开清棉工艺的制定要本着提高各机开松效率,防止过 猛打击,以免损伤纤维并减少棉结杂质;
梳棉工序应充分梳理,排除短绒和结杂,并注意减少 对纤维损伤。
对于刺辊速度的考虑,在满足对纤维作用齿数的条件下,刺 辊速度偏低掌握为宜,以利于减少纤维损伤、达到提高成纱 强力的目的。
1.3 断裂强度变异系数
反映纱线强力不匀率的指标,用均方差系数即CV值表 示。
2 纱线拉伸断裂过程
纱线断裂是由一部分纤维断裂或滑脱引起 的
当纤维间摩擦力>纤维的断裂强力时,则纱线 被拉伸时,这部分纤维只能被拉断;
当纤维间摩擦力<纤维的断裂强力时,则纱线 被拉伸时,这部分纤维将从纱中抽拔出来而 成为滑脱纤维。
纤维细度对细特纱的强力影响要比粗特纱大; 但应注意,成熟度差的纤维,虽然线密度较细,但因单纤维
强力低,用这种纤维纺纱时,强力反而降低; 棉纤维的线密度不匀率对成纱强力的影响也很大。
1.3 纤维断裂长度、单纤维强力与成纱强力
纤维断裂长度大、单纤维强力高,成纱强力就高。
1.4 混纺纱各组分的强力和伸长对纱线强力的 影响
由于P2>P1,所以随着n2的增加,纱线的强力增大 ,即随着混纺纱中强力大的纤维混纺比的增加, 混纺纱的强力提高。
1.4 混纺纱各组分的强力和伸长对纱线强力的 影响
(2)当混纺在一起的 两种纤维断裂伸长率 相差较大,且纤维1断 裂时的强力大于纤维2 ,在纱线受到拉伸力 作用时,两种纤维的 拉伸曲线如图所示:
成纱强力随粗纱短片段不匀率的增加而 降低,因此要降低粗纱的短片段不匀, 以提高成纱强力。
2.1.2 合理制定并、粗工艺,提高半 制品均匀度
改善粗纱的短片段不匀,应严格控制末并 条的重量,降低台差、眼(头)差,减少 因纤维条重量差异形成的粗纱卷绕伸长锭 差,合理控制粗纱伸长率。粗纱工序除控 制温湿度外,粗纱卷绕张力应适当,但卷 绕密度不能过小。
则混纺纱的强力: P n1P1 n2P2
由于P1<P2,所以随着n2的增加,纱线的强力增加 当纤维2的含量比较大时: n1P1 n2P2 n2P2
则混纺纱的强力: P n2P2 可以看出,随着n2的增加,混纺纱的强力增加。
2 纺纱工艺对成纱强力的影响
2.1 前纺工艺与成纱强力
第五章 纱线的强力与强力 不匀
第一节 纱线强力的基本 概念
1 纱线强力的基本指标
1.1 绝对强力(即断裂强力) 1.2 相对强力
1.2.1 断裂强度
单位粗细(或面积)纱线上所能承受的最大负荷
1.2.2 单纱断裂长度
握持单纱一端,使其下垂,当下垂总长因纱线自身重力把纱 线沿握持点拉断时,这个长度就称断裂长度。
纱线的百米重量CV值是影响管纱强力的重 要因素。
一般细纱重量不匀率稳定在2%以内,才能 避免突发性的CV值超过标准。
但有时单纱强力不匀率较高,而百米重量 CV值无表现,这是由于出现“突发强力” 纱段,往往只有0.5m左右,这就要求降低 细纱长片段不匀的同时,也要降低0.5m左 右的片段不匀。
3 混纺纱线片段间的纤维混合不匀对强力不匀的影响
粗纱捻系数应根据不同产品的质量特点合 理设计。
2.1.3 提高原料混合均匀度
减少原料差异率、增强前纺对原料的混合作用,是提 高成纱强力的必要条件。
提高原料混合均匀度,主要应做好以下几方面工作:
减少混用原料的形状差异,特别要减少纤维线密度、 长度、初始模量的差异以及包装密度和尺寸差异;
增强梳前工序的混合效果; 提高梳棉机梳理作用,增加单纤维之间的混合机会。 适当增加精梳、并条工序的并合数,使原料成分在进
混纺纱的强力除取决于各成分纤维的强力外,还取 决于各成分纤维断裂伸长率的差异。
由于各成分纤维断裂的不同时性,使混纺纱的强力并不等 于各成分纯纺纱强力的加权平均值,而总是低很多。