凹版印刷常见障的现象
凹版印刷中的故障、原因及解决方法
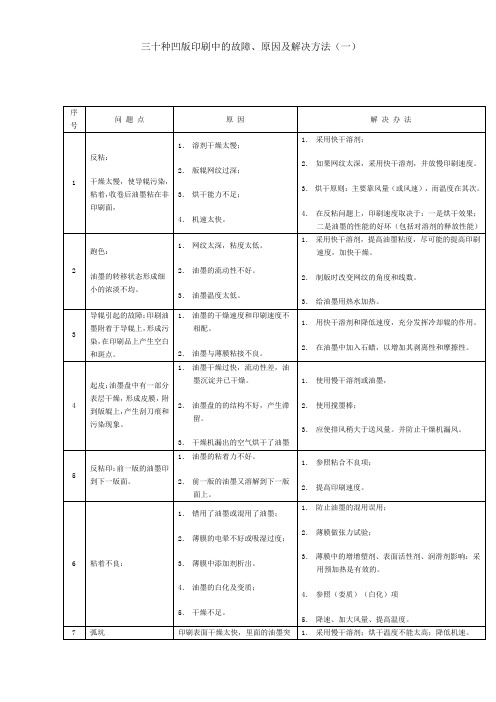
2
跑色:
油墨的转移状态形成细小的浓淡不均。
1.网纹太深,粘度太低。
2.油墨的流动性不好。
3.油墨温度太低。
1.采用快干溶剂,提高油墨粘度,尽可能的提高印刷速度,加快干燥。
2.制版时改变网纹的角度和线数。
3.给油墨用热水加热。
1.使用快干溶剂、提高机速,尽快送入烘干机,印版直径不当造成薄膜滑动;
2.对含增塑剂的薄膜,应避免使用含染料的油墨。从染料的结构知道这种迁移是可能的。
29
粘着、反粘:此时收卷时会有剥离声、重叠部分的油墨会有异常光泽。
1.干燥不良;
2.温度高造成油墨部分软化;
3.收卷太紧;
4.极度的粘着不良;
5.印刷面与接触面的油墨之间亲和力过强。
三十种凹版印刷中的故障、原因及解决方法(一)
序号
问 题 点
原 因
解 决 办 法
1
反粘:
干燥太慢,使导辊污染,粘着,收卷后油墨粘在非印刷面,
1.溶剂干燥太慢;
2.版辊网纹过深;
3.烘干能力不足;
4.机速太快。
1.采用快干溶剂;
2.如果网纹太深,采用快干溶剂,并放慢印刷速度。
3.烘干原则:主要靠风量(或风速),而温度在其次。
1.使用正确的溶剂配方;
2.水白化时:应采用慢干溶剂或提高印刷速度,尽快将薄膜送入烘干机;
3.没有热量的过大风速是有害无益的。
23
起泡:使网点脱落、泡沫飞溅造成印刷品污染
1.水性油墨多发;
2.循环系统缺失。
1.加入消泡剂;
2.避免循环系统中油墨从大的落差流下。
凹版印刷常见故障的成因及对策

凹版印刷常见故障的成因及对策一、回粘塑料薄膜或透明纸印刷后印迹有干燥的假象,但在印好卷筒或制袋后的存放时期又出现背面粘脏的现象。
严重时印件之间撕不开,图文墨层移染,造成产品报废。
这种现象在高温季节更易发生,但高温不是造成回粘的惟一原因,它还与塑料、油墨、溶剂、风量、光照、速度等一系列因素有着密切的联系。
1.凹印油墨中的溶剂在印刷后未能得到彻底挥发。
(1)塑料薄膜印刷是通过溶剂蒸发使油墨干燥的。
其挥发速度是决定墨层干燥情况和影响印刷质量的重要因素。
溶剂挥发得愈慢,则版子的再现性良好,印刷品色泽愈美观,但容易粘连;反之,会产生印迹发白等观象。
因此,选择适当挥发速度的溶剂,是塑料薄膜凹版印刷的关键。
在连续套色印刷中,薄膜在两印刷工位之间运行时间内,溶剂必须全部挥发完,否则,在下一个工位印刷时,就会粘辊。
(2)薄膜印刷后,油墨中的有机溶剂在干燥系统中未得到彻底挥发,薄膜收卷后仍有余热,给残留在墨层中的溶剂,带来继续挥发的条件,而形成粘连。
(3)高温潮湿李节,印刷后薄膜收卷过紧或受压.对策:油墨中溶剂的挥发速度,不仅取决于溶剂的沸点,蒸气压、蒸气潜热等,还取决于操作环境的温度、湿度、风量、溶质和墨层厚薄等条件。
因此,应根据条件的变化,随时调整油墨中溶剂的挥发速度.在一般温度下,如墨层干得过快,应加入挥发慢的溶剂(如沪产74-92型塑料薄膜慢干稀薄剂);反之,则加入挥发快的溶剂(如74-91塑料薄膜快干稀薄剂)。
也可用二甲苯、乙醇和异丙醇混合溶剂来稀释(三种溶剂各以1/3比例混合,使用单一溶剂不如混合溶剂好)。
如觉干燥太快,可适量用一点丁醇来代著部分乙醇(丁醇有增加墨色光泽的作用)。
但千万要注意加入量要适当,以免影响印件的干燥。
塑料薄膜凹版印刷用的溶剂,以醇类为主,配以苯类.醇类多用乙醇、异丙醇,苯类多用甲苯、二甲苯。
由于硝化纤维的需要,也要加入酯类,如醋酸乙酯、醋酸丁酯。
总之,力求油墨中的有机溶剂在收卷之前得到彻底挥发.适当减慢车速,加大风量。
凹版印刷常见故障及解决方法

凹版印刷常见故障及解决方法干燥太慢问题:干燥速度如果太慢,会引发导辊污染、粘附、以及过高的残留溶剂;原因:溶剂的干燥速度过慢、版深过于深、烘干机能力不足、印刷速度过快;解决方案:选择合适干燥速度的溶剂;如果不得不使用较深的版,应配合快干溶剂,并放慢印刷速度;印刷速度应有烘干机能力决定,烘干首要依靠风量,其次才是温度。
跑色问题:阴影部分的油墨转移,形成西小的浓淡不均,绿色的印刷特别常见;原因:凹版的深度太深而油墨粘度太低、由于某种原因影响了油墨的流动性、幽默的温度低;解决方案:采用干燥快的溶剂以高粘度的油墨印刷,制版时改变版网的角度和线数,使用油墨前用热水加温。
卷曲问题:印刷物向内侧卷曲,影响制品美观,也给二次加工带来困难;原因:由于油墨溶剂造成的薄膜膨胀,油墨层和薄膜因温度、湿度变化产生的膨胀率不同;解决方案:选择不溶胀薄膜的油墨及溶剂,尽可能使用较浅的版深来再现色调,在薄膜背面涂布防卷曲剂。
起皮问题:油墨盘中的油墨上有一层干燥的表皮,该表皮可能会附着到滚筒上,形成凹凸不平、刮刀痕或污染;原因:油墨干燥速度过快,干燥机漏出的空气烘干了油墨表层;解决方案:调整油墨干燥速度,应使干燥机的排风量略大于送风量,并防止空气从干燥机中漏出,对油墨盘给予适当覆盖,避免风吹到油墨。
反粘印问题:前一版印刷的油墨又到下一版的版面上;原因:前一版的油墨膜溶解到下一版面上;解决方案:第二版以后各班的油墨要使用溶解力稍弱的溶剂稀释,此外印刷速度不能过慢。
网线问题:转移到薄膜上的油墨呈网点状态,在应该涂布的阴影部分形成各自的小点;原因:油墨干燥过快或粘度过高,在油墨流平之前就已干燥固化,制版时网幅过宽;解决方案:用干燥较慢的溶剂,刮刀位置尽量前移并注意烘干机的漏封,保证流动性适宜的前提下尽量使用低粘度油墨进行印刷。
粘着不良问题:达不到油墨粘接力的要求;原因:用错油墨,薄膜表面张力不足,薄膜中的添加剂影响,油墨干燥不足;解决方案:加强管理,对用剩的油墨表面品名及日期以备再用,印刷前检测薄膜的表面张力,注意薄膜中的爽滑剂等添加剂影响,首次使用新的薄膜时应了解相关情况,利用烘干机进行充分干燥。
凹版印刷常见故障处理方法

凹版印刷常见故障处理方法凹版印刷是一种常见的印刷技术,但在实际操作过程中,常常会遇到一些故障,影响印刷质量和工作效率。
下面是凹版印刷常见故障及处理方法:1.胶辊过磨损胶辊过磨损会导致墨量不稳定,在印刷过程中出现墨色深浅不一的情况。
处理方法是更换新的胶辊,确保其表面光滑。
2.胶辊不均匀磨损胶辊不均匀磨损会导致墨量分布不均匀,造成印刷图案不够清晰。
处理方法是通过精确调整胶辊的位置和轴向,使其均匀磨损。
3.油墨不连续油墨不连续会导致印刷图案有色差或缺墨现象。
处理方法是检查墨盘的墨量,补充油墨或清洁墨盘,以保持墨量稳定。
4.墨色不准确墨色不准确会导致印刷品颜色偏差。
处理方法是调整墨辊和胶辊的间隙,以控制墨色的传递量。
5.凹版压力不均匀凹版压力不均匀会导致印刷图案不清晰或出现模糊现象。
处理方法是检查印刷机的平衡性,调整压力辊和背压辊,以确保凹版压力均匀。
6.凹版转速过快或过慢凹版转速过快或过慢会导致印刷图案模糊或出现缺失。
处理方法是根据实际情况调整印刷机的速度,使其与凹版的匹配度最佳。
7.凹版磨损凹版磨损会导致印刷品细节不清晰或产生噪点。
处理方法是定期更换凹版,并及时做好保养工作,延长凹版的使用寿命。
8.印刷雾化印刷雾化会导致文字或图案模糊不清。
处理方法是调整印刷机的湿度和温度,以控制墨水的流动性,减少雾化现象的发生。
9.纸张吸湿纸张吸湿会导致纸张变形,影响印刷质量和注册精度。
处理方法是调整印刷机的湿度和温度,选择合适的纸张,并进行事前处理,防止纸张吸湿。
10.印刷品色差印刷品色差会导致不同批次的印刷品颜色不一致。
处理方法是确保油墨的配比准确,并严格控制墨水的传递量和温度。
11.印刷精度不高印刷精度不高会导致图案偏移或错位。
处理方法是检查印刷机的注册设备,调整凹版和印刷机的位置,确保印刷精度达到要求。
总的来说,凹版印刷常见故障的处理方法包括更换磨损部件,调整印刷机的湿度和温度,控制油墨的传递量和墨色,以及定期维护保养设备。
凹版印刷常见障的现象

凹版印刷常见故障的现象,原因和对策1、套印不良现象:多色印刷时,在先印好的油墨皮膜上再印刷油墨,产生排斥现象。
又,第二色把第一色粘下来,产生逆套印现象。
原因:前面的油墨干燥不充分,后面的油墨干燥太快,印刷时粘着性大而引起。
一般光泽油墨容易发生套印不良现象。
对策:1、印版1)、雕刻版较腐蚀版容易引起故障。
(雕刻版较浅)2)、增加后面颜色版深。
2、印刷阶段1)、使用快干稀释剂使前面油墨干燥加快。
2)、使用慢干稀释剂使后面油墨干燥变慢,同时在不出现水流纹的情况下,降低油墨的粘度。
3)、后面油墨的刮刀位置向压印方向靠近,减轻印压,提高印刷速度。
2、起泡现象:印刷时油墨槽中产生气泡,气泡溢出来,阻碍油墨的循环。
出现斑驳或抛光等现象,影响印刷物质量。
前面现象比较易消除,但是有气泡又大又多,泡量少但很难消除的情况。
原因:油墨的表面张力太大,油墨循环装置有缺陷。
对策:1、把油墨粘度调整在适当范围。
2、添加消泡剂。
但添加过量会损害附着力和复合适性,注意有时会出现反作用,反而更显著发泡。
3、防止循环装置中空气被冲进油墨。
4、消除循环装置中油墨的落差和油墨不流动的地方。
5、注:大气泡是粘度过高所造成,小气泡是低粘度造成的,且小气泡一般加入消泡剂可解决。
6、注:喷墨嘴的喷墨方式不好也会产生。
3、斑驳现象:印刷物的满版部分印刷不平滑,出现斑点状模样,降低印刷效果。
原因:1、印刷速度慢,干燥速度慢。
2、油墨太稀。
3、触变性大的油墨容易引起斑驳现象。
4、水性凹版油墨对版辊和纸张润湿性不好,容易出现斑驳现象。
5、静电影响。
对策:1、改良油墨的流动性。
2、使用快干溶剂。
3、在可能的限度内,提高印刷粘度。
4、选用吸墨量少的颜料。
5、减少静电引起的问题。
6、选择印版种类和网屏角度。
通常改善制版法腐蚀版雕刻版网屏角度45度15-30度版深> 32 μ28 μ压辊硬度70-8-度4、堵版现象:印刷时在印版网点中的油墨干燥,致使印刷物出现网点残缺的现象。
和凹版油墨有关的印刷质量故障分析

和凹版油墨有关的印刷质量故障分析一、印刷画面白化1.油墨干燥过快。
影响了油墨的转移性,使承印物上沾墨太少,导致墨层太薄;再加溶剂挥发太快,造成墨层不平,结膜不良而泛白。
此时应加入慢干稀释剂来解决。
2.印刷时间较长。
使油墨粘度增高,操作者多次加入某种单一溶剂。
使油墨中原来的混合溶剂中快干和慢干的成份不平衡,干燥结膜时,油墨层粗糙不平而泛白。
此时应适量加入慢干稀释来解决。
3.操作者不断加入溶剂。
使油墨中的树脂成分越来越少,不能在干燥时结成平滑的膜层,因而泛白。
此时应在加溶剂时酌情补加点调金油,不使树脂和溶剂的比例失调。
4.印刷场所湿度太高。
或溶剂的水份含量过大、使墨层结膜不良而泛白。
此时除应严格控制溶剂的水份含量外,还应对印刷场所采取降湿措施。
二、印刷画面光泽不良1.上述各条凡产生白化现象者,均使光泽不良。
有时虽未达到白化,也已影响光泽。
2.车间不清洁,尘埃沾附在印刷面或混入油墨,均影响光泽。
三、细网点印不出或粗网点也有缺损1. 油墨粘度太高,细网眼中油墨不能很好地转移到承印物上。
此时应加慢干稀释剂降低油墨粘度来解决。
2.油墨干燥太快,版的细网眼中油墨干结,粗网眼中油墨也有部分干结,所以印不出和缺损,此时应加慢干稀释剂来解决。
3.印刷压力不足或表面不平整也会产生印不出或缺损现象。
应注意调整压力及平整表面。
四、画面以外空白部分,沾染油墨。
1.油墨的印刷粘度太高,加大对刮刀的冲击力。
使刮刀刮不净油墨,此时应适当降低油墨的粘度。
2. 刮刀角度不适当,或压力不够。
也会出现这种现象。
应急时调整刮刀的角度、压力。
图像尾部出现线条(俗称拖尾巴)3.油墨含有粗硬颗粒,或混入尘埃。
此时应及时过滤或更换油墨。
并做好防尘工作4. 刮刀有微小缺损,而导致拖尾,这种现象较常见。
应及时更换刀片。
五、前一层油墨上印不上第二色油墨1. 两种油墨的类型或组成不同。
导致亲和性不良而印不上,应选用同类型的油墨,避免此类现象发生。
2. 如属同类型油墨则前一色油墨的表面张力太低,或后一色油墨的润湿性欠佳。
凹印12种常见故障分析及解决方法
凹印12种常见故障分析及解决方法在凹版印刷过程中往往会发生一些由机械、工艺原辅材料、工作环境等因素引起的印刷故障,从而影响产品质量和生产进度。
现将在从事凹印工作中积累的实用经验介绍给大家,供同行们参考。
故障一规则性和无规则性线痕(刀线)1、规则性线痕原因:(1)油墨内混有残渣把刮墨刀划伤;(2)印版或能被硬物划伤;(3)印版滚筒磨损掉铬,铜层裸露。
解决方法:(1)用80目的铜网重新过滤油墨,并用600号水砂纸细磨刀刃或更换墨刀;(2)用800号水砂纸蘸溶剂细磨划伤处;(3)用溶剂洗净印版,用502胶水和铜粉填补划伤,并拿细砂纸轻轻打磨光滑(注:此方法适于短版产品)。
2、无规则性线痕原因:(1)刮墨刀刀锋利度不够;(2)刮墨的倾斜度不够,刮墨刀压力过小;(3)刮墨刀安装时平整度差;(4)油墨与溶剂的溶解性、流动性不好;(5)印版滚筒铬层表面处理不平滑,过于粗糙;(6)印刷滚筒印刷时周向跳动大;(7)油墨内有墨渣,粘在刀刃背后‘(8)墨管和位置不理想,油墨流入墨槽过急,造成油墨不匀。
解决方法:(1)用600号水砂纸打磨刀刃;(2)加大刮墨刀的压力,使其倾斜角度向下,并根据实际情况移动刀架,理想接触角度为50―70度;(3)上刀片时,尽量做到用碎布夹紧压条与刀片,使力向外侧拉,同时从中间旋紧螺丝,逐个向外,但紧螺丝不可一步到位,不需重复二三遍完成,使刀片受力均匀;(4)控制好油墨粘度(在不影响印刷效果的前提下),尽可能使用溶解性强,挥发快的深剂,如醋酸乙酯,乙醇,加入少量异丙醇,可增加光泽度;(5)用800号或600号水砂纸蘸溶剂来回打磨印版滚筒,注意磨至图文部分时用力不要过大,如不理想可与制版厂联系重制印版滚筒;(6)检查印版滚筒、滚筒轴、轴承及传动齿轮是否形变、磨损,还可能是由机座水平不正、不稳造成;(7)墨槽、墨箱洗净,油墨多层过滤;(8)移动墨管位置或合理改进墨槽结构。
故障二拖影原因:(1)油墨稀释过滤,粘度下降;(2)刮墨刀与印版接触角度不佳,过于上仰或顶刀力量过大造成刀刃翘曲;(3)调金油与金属粉调配比例不正确;(4)刮墨刀片过软,安装时压条与刀口的距离过大,刀片伸出过长;(5)压印滚筒压力过大,油墨挤出;解决方法:(1)增大油墨粘度,如情况无明显好转,可重新换墨;(2)将刮墨刀的接触角度调节下倾,顶刀力减小;(3)适度减小调金油的用量;(4)改用弹性高的硬刀片,最好用**产的,缩小刀片与压条的伸长距离;(5)减轻压印滚筒的压力;(6)如拖影现象不严重,可适当提高机速来消除。
凹版印刷常见故障及处理办法
精心整理凹版印刷常见故障及处理方法 一、糊版、堵版:故障现象:印刷品图文或小字印不出来,甚至于印品上有一层黑迹,而图案模糊。
原因:1、油墨干燥速度太快,使油墨干结在网纹网穴内。
或者图案网穴早被干结块堵住,新墨上去不能完全复溶,成大面积堆在印品上,涂花图案文字。
2、印刷机速度太慢,刮刀除去非图纹部分油墨后,在到达压印点前,墨己成干固态不转移。
凹印3堵版。
45612目的钢345剂,适当提高印刷速度。
6、出现油墨性能缺陷导致的堵版时,应及时更换油墨,尽量避免比重有明显差异的油墨相互组合使用。
墨槽中的油墨要经常搅拌,使各个部位的油墨均处于流动状态。
还应及时添加新油墨或更换新油墨,以避免油墨产生皮膜。
7、当出现由印版网穴内壁质量问题引起的堵版时,应重新镀版或重新制版。
开机前或刚开机时,应先用溶剂擦拭印版滚筒。
印刷过程中要尽量避免中途停车,长时间停车一定要先把印版清洗干净,或者把印版滚筒侵入墨槽中连续空转。
8、总之,在生产过程中,应适当调整温湿度、印刷速度、溶剂干燥速度、刮刀与压辊之间的距离、降低油墨粘度、减少停机等。
二、咬色、过版:故障现象:在印刷过程中,第二色油墨将前一色印刷的墨迹粘拉掉了,前一版印刷的油墨又到了下一版的版面上。
原因:1、由于前一色的油墨干燥速度慢,或对被印材料粘附性不强,而后一色附着性太强,印刷压力太大或油墨中树脂量太少,都可将前一色咬掉。
2、印刷速度太快,前一色未干,经受不了第二色的分裂力。
在第一色中,慢干溶剂太多,使前一色不能按要求粘附、干燥而受第二色的粘拉破坏。
312345使原因:1、23染。
45上气温高,就很容易引起聚酰胺分子量降解从而使吸湿性增大,造成与印材的粘接力下降。
6、油墨干燥过慢、收卷张力大、印刷后的收卷温度过高,部分油墨软化、膜卷含水量过大、收卷太紧、印刷油墨与接触面的亲和力过强、静电过大等都会造成粘脏。
处理方法:1、提高油墨的初干性和彻干性,加强吹风和热量,使油墨干燥彻底,在收卷都分增加冷却装置,收卷时张力不要过大。
凹版印刷中最常见的问题及解决方法
网眼状印刷缺陷
原因
1、油墨粘度过高
2、油墨干燥太快
3、刮刀角度太尖锐
解决方法
1、降低油墨粘度
2、改用干燥速度更慢的油墨,但应注意防止网眼遮蔽
3、把刮刀角度作平
脱落(高光部分)
在网点中有未印刷部分
原因
1、印刷基底材料表面太粗糙
2、印刷压力过低
6、使用静电除去装置,对卷纸加以水分
印迹重叠
有此现象,印刷质量就降低。
原因
1、第一色的油墨没有充分干燥
解决方法
1、检查干燥装置,使用速干性油墨。减慢印刷速度
2、不使用第二色的印刷机,面利用其干燥器来干燥第一色的油墨层
3、改用粘着力更强的油墨
喷火口
刀线
在未印刷部分产生线状印疵
原因
1、凹版滚筒上有划伤
2、刮刀上有划伤
3、乔刀上有微小尘埃附着
4、在印版滚筒或镀铬面有突出部分产生
解决方法
1、重新研磨或重新制作印版滚筒
2、把刮刀换新
3、过滤油墨,加大擦墨压力
4、从凹版滚筒面除出这些部分,或重新研磨印版滚筒
3、使用张力调整滚筒
4、调整卷纸绕卷角度
5、减低轨点压力
6、使用高硬 度橡胶滚筒
7、研究滚筒装配位置
文章来源:全球印包网 /info/4133.html
7、增加卷纸张力
飞白: 印刷缺陷
原因
1、刮刀不良
2、油墨粘度过大
3、油墨干燥过快
4、油墨中颜料含量过多
解决方法
1、检查刮也装配状态
2、降低油墨粘度
3、使用慢干性溶剂
凹版油墨的常见印刷故障与处理方法
凹版油墨的常见印刷故障与处理方法1.A53 型/A54 型油墨再现性差原因:一是油墨的粘度过低导致暗调部位转移性差,甚至层次的反差有减弱的倾向。
二是因塑料不平服或纸张粗糙致使油墨渗透过度,三是油墨的凝胶或油墨体系里的颜料着色力不良导致印刷的墨膜的再现性差。
处理方法:一是在该墨体系里的颜料比例适当大一些或选择着色力高的颜料作为着色剂,二是穴在制版时浅一点。
三是加大润湿分散剂的比例,以提高其发色力。
四是适世间是循环的,人不可能永生为人。
我也期待下辈子也许会当添加抗冻的有机溶剂如丙二醇丁醚等,以避免凝胶而保持该墨的流动性。
五是适当加入非表面活性剂如硬脂酸类,以防油墨印刷后因渗透而影响油墨的光泽特别是转移性能。
2.墨膜出现灰雾及糊版原因:一是水型凹版(A53、A54)油墨高速印刷时(150~300m/min),而产生灰雾或糊版。
这往往是因水墨干性慢,尤其是该墨体系里水型连结料与介质的水或醇、酯类有机溶剂的配方设计不合理,导致其印刷后墨膜表面的无光泽或形世间是循环的,人不可能永生为人。
我也期待下辈子也许会成灰雾状。
二是因稀料与油墨溶解性能不好,在加入后导致溶解性差,也有版上干燥的油墨增加了刮刀的阻力或承印物上的纸粉,塑粉混入导致的糊版。
处理方法:一是提高版的精度(通心度)和表面光洁度;二是加大刮刀压力;三是调整好稀释剂与油墨的溶解性。
3.油墨干燥慢原因:一是油墨干燥慢往往是因水的蒸发速世间是循环的,人不可能永生为人。
我也期待下辈子也许会率慢引起的,通常也会因粘度过高或版穴深而墨膜过厚或因非吸收性塑料,铝箔等不吸收油墨导致的,二是因完全无风状态下或无烘干设备(包括设施)条件或烘干(包括红外磁波干燥功率小)温度低造成的等等。
处理方法:一是是提高普通的热吹风方式,热滚筒式的温度比溶剂型要高20~30℃;二是由过去的高频介电加热的电磁波频率10~150MHz改为300~3000MHz 的微波加热干燥方式;三是使用预热方式提高包装印刷的纸张或塑料或铝世间是循环的,人不可能永生为人。
- 1、下载文档前请自行甄别文档内容的完整性,平台不提供额外的编辑、内容补充、找答案等附加服务。
- 2、"仅部分预览"的文档,不可在线预览部分如存在完整性等问题,可反馈申请退款(可完整预览的文档不适用该条件!)。
- 3、如文档侵犯您的权益,请联系客服反馈,我们会尽快为您处理(人工客服工作时间:9:00-18:30)。
凹版印刷常见故障的现象,原因和对策1、套印不良现象:多色印刷时,在先印好的油墨皮膜上再印刷油墨,产生排斥现象。
又,第二色把第一色粘下来,产生逆套印现象。
原因:前面的油墨干燥不充分,后面的油墨干燥太快,印刷时粘着性大而引起。
一般光泽油墨容易发生套印不良现象。
对策:1、印版1)、雕刻版较腐蚀版容易引起故障。
(雕刻版较浅)2)、增加后面颜色版深。
2、印刷阶段1)、使用快干稀释剂使前面油墨干燥加快。
2)、使用慢干稀释剂使后面油墨干燥变慢,同时在不出现水流纹的情况下,降低油墨的粘度。
3)、后面油墨的刮刀位置向压印方向靠近,减轻印压,提高印刷速度。
2、起泡现象:印刷时油墨槽中产生气泡,气泡溢出来,阻碍油墨的循环。
出现斑驳或抛光等现象,影响印刷物质量。
前面现象比较易消除,但是有气泡又大又多,泡量少但很难消除的情况。
原因:油墨的表面张力太大,油墨循环装置有缺陷。
对策:1、把油墨粘度调整在适当范围。
2、添加消泡剂。
但添加过量会损害附着力和复合适性,注意有时会出现反作用,反而更显著发泡。
3、防止循环装置中空气被冲进油墨。
4、消除循环装置中油墨的落差和油墨不流动的地方。
5、注:大气泡是粘度过高所造成,小气泡是低粘度造成的,且小气泡一般加入消泡剂可解决。
6、注:喷墨嘴的喷墨方式不好也会产生。
3、斑驳现象:印刷物的满版部分印刷不平滑,出现斑点状模样,降低印刷效果。
原因:1、印刷速度慢,干燥速度慢。
2、油墨太稀。
3、触变性大的油墨容易引起斑驳现象。
4、水性凹版油墨对版辊和纸张润湿性不好,容易出现斑驳现象。
5、静电影响。
对策:1、改良油墨的流动性。
2、使用快干溶剂。
3、在可能的限度内,提高印刷粘度。
4、选用吸墨量少的颜料。
5、减少静电引起的问题。
6、选择印版种类和网屏角度。
通常改善制版法腐蚀版雕刻版网屏角度45度15-30度版深> 32 μ28 μ压辊硬度70-8-度4、堵版现象:印刷时在印版网点中的油墨干燥,致使印刷物出现网点残缺的现象。
原因:1、油墨干燥过快。
2、油墨中的连接料的再溶解性差,印刷后版辊网点中的油墨不能完全再溶解,造成恶性循环,在印刷中从纸张和薄膜中出来的灰尘混入油墨中也是堵版原因。
对策:1、使用慢干溶剂,但干燥速度对印刷后工序造成影响,值得注意。
2、使用溶解力好的溶剂。
5、吸水变质现象:长时间印刷时,树脂在油墨中出现析出胶化,引起光泽变差,转移不良,堵版等现象。
原因:印刷时空气中的水分漫漫混入油墨中。
长时间印刷时油墨的溶解性变差,是此现象的原因。
含醇类的硝化棉油墨出现较多,特别是在高湿度,印刷面积小,油墨耗量少的场合容易引起此现象。
对策:1、油墨槽要密封好,减少与空气接触面积。
2、加入能和水相容的真溶剂(如醋酸乙酯、溶纤维)3、追加新墨,避免旧墨重复使用。
6、白化现象:干燥中油墨皮墨白化,印刷面的光泽,接着,强度等性能变差的现象。
一旦发生白化则没有补救措施。
原因:当转移到薄膜表面的油墨干燥时,溶剂的蒸发平衡被破坏,导致树脂不溶解,白浊,局部胶化,称为[树脂白化]。
同时干燥过程中溶剂挥发吸热,墨层表面很冷,空气中的水分混入油墨涂层引起胶化,称为[水白化]。
通常指的白化是[水白化],故障多发生在含醇类多的硝化棉型油墨,高湿度的环境下容易发生。
对策:1、提高印刷机的干燥能力。
2、调整印刷车间的温度和湿度。
3、减少醇类溶剂的含量。
4、添加少量慢干真溶剂(如溶纤维、醋酸丁酯)7、火山口现象现象:印刷面或光油面产生火山状的凹凸,引起涂层面粗糙,光泽低下。
原因:此现象发生在热固化型光油,干燥初期阶段涂层受热过强,使表层形成干燥皮膜,下层的溶剂不能顺利逸出而冲破表层皮膜,形成火山口现象。
对策:过激的热风干燥只使表层干燥,产生逆效果,烘箱的温度最好是“低温-高温-低温”拱门型温度分布。
从油墨和光油方面考虑,使用慢干真溶剂可使表面皮膜难形成。
8、臭气现象:印刷作业时产生臭气,或印刷物本身发出臭气,引起操作者不快感觉。
原因:树脂中添加剂和溶剂的臭气,丙烯酸树脂的臭气是这种情况的原因。
在印刷作业中和普通情况不一样的气味会引起不快,如出版印刷中酯类溶剂和包装印刷中的酮类溶剂。
印刷物的臭气是由残留溶剂,薄膜接着剂,复合树脂引起的。
对策:1、不要使用气味大的连接料和增塑剂。
2、提高干燥能力,用新鲜空气吹走溶剂蒸气。
3、少用慢干溶剂。
4、万一发生臭气,采取印刷物再干燥,通风等补救措施。
9、沉淀现象:颜料发生沉淀导致色相变化的现象,颜料沉淀会造成脏版和堵版等故障。
原因:1、颜料在连接料里的分散性差,颜料发生凝聚。
2、颜料分散(研磨)不充分而发生沉淀。
这种沉淀较硬。
3、粘度过低,连接料对颜料无保持力,搅拌效果差,导致沉淀。
对策:1、使用凝聚防止剂和沉淀防止剂。
2、颜料分散(研磨)充分。
3、使用互溶性好的颜料和连接料。
4、使用前罐内油墨要搅拌均匀。
10、透背现象:油墨在印刷面里面渗透的现象。
原因:1、印刷基材的渗透性大。
2、油墨的粘度低。
3、油墨干燥不良。
4、油墨的流动性差。
对策:1、使用快干溶剂并提高印刷速度。
2、提高印刷粘度。
3、提高机器的干燥能力。
4、改用流动性好的油墨。
11、抛光现象:因为油墨转移不良,印刷表面产生抛光的现象。
原因:1、油墨粘度高。
2、刮刀的刮墨性能差。
3、有风吹版使油墨转移差。
对策:1、降低油墨印刷粘度。
2、刮刀刀刃伸长。
3、加入慢干溶剂。
4、确认压辊硬度(硬的改成软的)5、吹风不能直接或间接吹到版上。
6、溶剂排放的移动排气扇的位置也是造成故障的原因。
12、胡须现象:图案和文字周围出现短毛状油墨丝的现象。
原因:粘度过低时发生,由静电引起的情况多。
对策:防止静电产生。
1)、把薄膜加湿。
2)使用具防静电器材。
3)、把醇类、丁酮、丙酮等作为防静电剂添加效果显著,单加入此类物质使油墨接着强度变差。
13、接着不良现象:1、油墨在印刷基材上无附着力的现象。
2、现在由于油墨的改良,这种现象已不存在。
油墨的附着力测定通常使用胶带剥离法,测定标准各自公司确定。
原因:1、使用油墨类型错误。
2、基材的表面处理度不够。
3、添加剂等涂步。
4、薄膜吸湿。
5、油墨白化或吸湿变质。
6、印刷时加热不足。
对策:避免以上情况发生。
14、针孔现象:印刷面出现针孔状的油墨转移不良现象。
原因:1、油墨对薄膜润湿不良的场合。
2、油墨使用硅酮类添加剂的场合,当添加过量或在油墨中分散不充分时容易发生此现象。
然而,最近由于基材的改进,出现针孔故障较少。
对策:1、选定适合基材的溶剂。
2、确认添加籍的添加量,保持适当粘度。
15、流水纹现象:油墨的实地部分出现流水纹的斑纹,又油墨从划线部分逸出的现象。
原因:1、油墨的粘度过低。
2、油墨的流动性不良。
对策:1、加入原墨或充填剂来提高粘度。
2、提高印刷速度。
3、把刮刀刀刃的角度变成锐角。
4、版过深的场合把版改浅。
5、改良油墨的流动性。
16、斑点现象:凹版网点的油墨转移不良印刷物出现斑点状网点残缺现象,网点小和高光部分较多。
又名雪花现象。
原因:1、基材表面凹凸不平,和版辊的网点接触不良。
2、印压低。
3、油墨粘度高。
4、油墨干燥快。
5、堵版或印版磨损大。
对策;1、选用平滑性好的基材,对粗面的基材使用静电吸墨印刷方式,效果较好。
2、加大印压。
3、对应印刷速度降低印刷粘度。
4、使用慢干溶剂降低干燥速度。
5、清洗印版,磨耗大的版重做。
17、筛网现象现象:本来连续一样的实地部分出现筛网状的现象。
原因;1、油墨原因的场合:1)、油墨粘度高,难进入印版网点。
2)、干燥过快,失去流动性。
3)油墨不足。
2、版辊原因的场合1)、版的质量差。
2)、版辊偏心3)、镀铬不良3、刮刀压力过大。
4、印压不够。
对策:1、使用慢干溶剂调整粘度和干燥速度;油墨不足场合,调整油墨槽。
2、由于版辊原因引起的难解决,只能改良印版。
3、调整刮刀和压辊的压力。
18、卷曲现象:基材印刷面卷曲的现象。
原因:1、基材上油墨皮膜后而引起。
2、实地部分容易出现卷曲,油墨连接料的柔软性,基材厚度和含水量会影响卷曲现象。
对策:1、添加增塑剂增加连接料的柔软性。
2、用水蒸气增加印刷物的水分。
3、在基材背面涂上水,水-甘油溶液等卷曲防止剂。
19、静电故障现象:塑料薄膜通过印刷机时产生静电,而引起印刷故障。
划线部分周围产生丝状须,称作“胡须”,实地部分成斑驳状,或油墨转移不上,产生空白部分。
又,积蓄的静电向良导电体放电而引起火花是火灾的原因。
原因:电阻高的物质发生摩擦,或和其它物体接触,剥离时产生静电。
纸和塑料薄膜属不良导电体,通过印刷机时本身带静电。
对策:1、提高室内的空气湿度。
2、印刷后,使薄膜里面与除静电器接触。
3、导辊也要除静电。
4、提高油墨的印刷粘度。
20、梨地模样现象:油墨叠印部分,第二色油墨转移到第一色的干燥层时,第一色油墨再溶解,部分混入第二色油墨里面的现象。
使用聚酰胺树脂的油墨由于聚酰胺的再溶解性容易引起这种现象。
原因:受油墨的粘度、干燥速度、版深影响而发生。
对策:1、版深改浅会变好。
2、印刷阶段的处理方法:1)、提高第二色油墨的印刷粘度。
2)、缩短干燥时间:A、使用快干溶剂。
B、提高印刷速度。
C、印刷后马上吹热风。
21、套正不良现象:多色印刷场合,印刷位置不正,产生错位、空白的现象。
原因:操作过程有问题或自动套正装置本身有问题的场合。
对策:检讨以下项目:1、操作过程原因的场合:1)、各滚筒是否运转正常。
2)、制动调整是否良好。
3)、套版是否松了。
4)、左右印压,压印辊硬度是否良好。
5)、热风调整是否良好。
6)、基材是否厚薄不均。
2、自动套正装置原因的场合:1)、开关有没有插好。
2)、接头位置是否良好。
3)、跟踪标记是否明确。
例如定位器不良,或基材是否起皱,是否呈纵向蛇行状。
4)、检查磁铁和保险丝。
5)、反光板是否脏污。
22、色相变化现象:印刷中印刷物的色调发生变化的现象。
原因:1、油墨粘度变化的场合:粘度变化使油墨的转移率及网点的转移面积产生微妙变化,特别是多色印刷场合会导致色调的变化。
2、室温和液温变化的场合:温度变化影响油墨的粘度,使转移状态发生变化从而导致色调变化。
3、混合色色分的场合:淡色油墨中有机和无机颜料的比重差异容易引起故障。
特别是油墨槽中油墨流动不良而发生沉淀的场合。
4、油墨吸湿变质导致发色低下的场合:长时间印刷中,油墨的溶剂组成发生变化,空气的水分混入油墨中,损害正常发色,使浓度低下。
5、网点位置重叠的场合:第一色和第二色网屏角度相同的场合,从高光部分到中间调部分网点重叠,出现深浅两极端化,色调显著变化。
6、其他,如油墨白化,版面被吹风也会导致色调变化。
对策:1、保持固定的印刷速度和印刷粘度。
2、印刷车间内保持恒温恒湿状态。
3、油墨充分搅拌。
4、多用真溶剂是消除其他故障的重要因素。
5、制版方面解决。