湿法脱硫湍流器及除雾器知识大全
脱硫除雾器

17
(2)除雾器临界烟气流速 在一定烟气流速范围内,除雾器对液滴分离的能力随 烟气流速增加而提高,但是当烟气流速超过一定数值后除 雾能力反而会下降,这一临界烟气流速称为除雾器的临界 烟气流速。 临界点的出现,主要是因为产生了雾沫的二次夹带所 造成的,即分离下来的雾沫,再次融入烟气中,被烟气带 走,其原因是: ①撞在叶片上的液滴由于自身动量过大 而破裂、飞溅;②气流冲刷叶片表面上的液膜,将其卷起、 带走。 为了达到一定的除雾效果,烟气流速非常重要,气流 最高速度不能超过临界速度,最低速度要保证能达到所要 求的最低除雾效率。
28
1.2可能导致结垢的原因
1.2.1设计方面 • 除雾器冲洗水压力不足:除雾器冲洗水压力是指冲洗时入 口母管处的压力, 一般要求大于0. 2Mpa。脱硫系统冲洗 水压力偏小,会使得冲洗效果得不到保证。 • 脱硫系统水平衡有问题:特别是机组低负荷运行时表现得 比较突出。很多设计将设备和轴承冷却、润滑、密封水全 部进入系统, 造成吸收塔高液位影响系统水平衡时, 运行 人员只得停止除雾器冲洗, 以防止吸收塔溢流; • 冲洗压力和流量控制及监测方式不正确:有些系统在除雾 器冲洗门前未设置冲洗水的流量和压力测点, 不能及时监 视和发现阀门内漏及冲洗水压力低, 难以保证冲洗效果。 除雾器差压不准,形同虚设, 起不到监视和报警作用。
23
五、除雾器的常见问题
• 1——除雾器的结垢、堵塞、坍塌
• 2——除雾器的热变形坍塌
24
1、除雾器的结垢堵塞坍塌
严重结垢, 会引起局部堵塞或整体塌陷, 有的 甚至将除雾器底部冲洗水管和支撑梁压断。 此问题主要出现在一级除雾器, 即下部的初级 除雾器, 使得除雾器局部滑动移位,甚至局部脱落。
25
12
湿法脱硫系统培训汇总

大唐长山热电厂1×660MW机组湿法脱硫系统培训教材除灰分场第一课时1 、概述我厂1号机组烟气脱硫设备采用的技术,是中国大唐集团科技工程有限公司从奥地利引进的湿法脱硫技术,其特点是吸收塔采用单回路喷淋塔,有效的避免由于塔内部件较多所产生的结垢堵塞问题,在世界上属先进和成熟的技术。
2、本工程脱硫岛的设计原则脱硫岛的总体设计原则是确保较高的脱硫效率、较高的可用率,并保证安全可靠,并且对锅炉的运行操作无影响。
为此,采用了技术上成熟的工艺,操作上可靠性较高的设备是十分必要的。
我厂1号机组在扩建工程中对脱硫工程提出的设计原则如下:(1)脱硫工艺采用湿式石灰石-石膏湿式烟气脱硫技术,吸收塔采用喷淋塔。
(2)脱硫装置采用一炉一塔,每套脱硫装置的烟气处理能力为一台锅炉BMCR(指锅炉最大连续蒸发量)工况时的烟气量。
脱硫效率设计煤种按不低于95%设计。
(3)脱硫系统设置100%烟气旁路,以保证脱硫装置在任何情况下不影响发电机组的安全运行,旁路烟气挡板从0~100%全开的时间不超过25S。
(4)石灰石浆液制备系统采用外购石灰石块(粒径不大于20mm),由湿式磨机利用工艺水制成吸收浆液。
(5)从热电厂供水系统引接至脱硫工艺水箱,为脱硫工艺系统提供工艺用水。
工艺水补水采用主循环冷却水排水。
(6)脱硫副产品—石膏脱水后含湿量<10%,为综合利用提供条件。
(7)脱硫增压风机按配备一台静叶可调轴流风机考虑。
(8)事故浆液箱设置1台。
(9)脱硫设备年利用小时按5500小时考虑。
(10)FGD系统在质保期内的可用率≥95%。
(11)FGD装置设计服务寿命为30年。
(12)符合我国电力建设的方针政策,贯彻安全、可靠、经济、适用、符合国情的电力建设方针。
(13)烟气脱硫工艺技术成熟、先进、经济合理,有运行业绩。
(14)严格执行有关降低工程造价的要求,优化设计。
(15)脱硫工艺尽可能节约能源和水资源。
2.1 石灰石—石膏湿法脱硫工艺湿法工艺采用的石灰石脱硫吸收剂,价廉易得。
湿式静电除雾器(WESP)在湿法脱硫上的作用
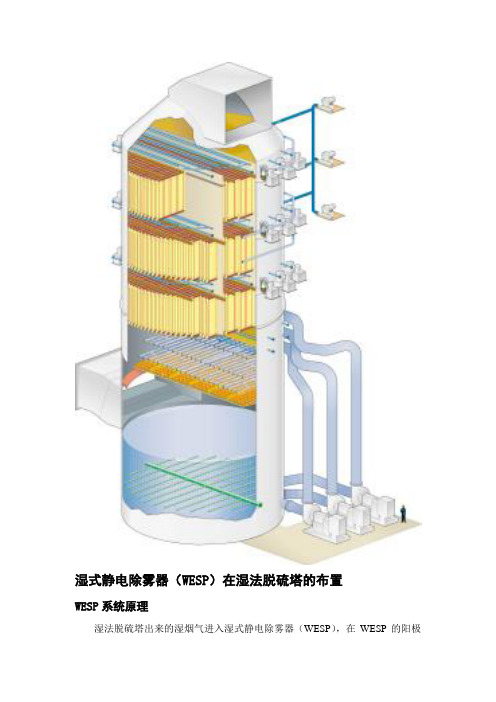
湿式静电除雾器(WESP)在湿法脱硫塔的布置WESP系统原理湿法脱硫塔出来的湿烟气进入湿式静电除雾器(WESP),在WESP的阳极筒和阴极线之间施加数万伏直流高压电,在强电场的作用下,电晕线周围产生电晕层,电晕层中的空气发生雪崩式电离,产生大量的负离子和少量的阳离子,在阳极筒内湿烟气中的微尘(雾)粒子、与放电产生胡正、负离子相碰撞而荷电,荷电后的尘(雾)粒子由于受到高压静电场库仑力的作用,分别向阴、阳极运动;到达两极后,将各自所带的电荷释放掉,尘(雾)粒子就被阴、阳极所收集,靠重力自流向下而与气体分离;部分的尘(雾)粒本身则由于其固有的黏性而附着在阳极板(筒)和阴极线上,通过冲洗的方法清除。
WESP装置结构(1)WESP本体WESP本体采用圆形结构,规格为Φ9.2m×10.7m,上部设有烟气导流板和气体分布板,下部设有液体收集槽,总高度约14m(含盖顶及下部收集槽)。
外壳体为碳钢衬玻璃鳞片。
WESP的出口烟道设置在本体侧面,直接接现有的垂直净烟道,降低了烟气的阻力;而且也能防止净化后的烟气二次带水。
收集的液体自流进入浆液箱,靠水泵打回吸收塔。
(2)阳极装置阳极装置包括沉淀极、支撑梁、冲洗水管、支撑梁。
阳极筒(也称沉淀极)采用先进的导体玻璃钢材质、导电性能好、易冲洗等优点。
阳极膜上、下端由支撑管支撑、张紧,其中上部的支撑管兼作冲洗水管,通过该冲洗水管可实现阳极膜6个面的在线冲洗,以保证阳极膜不结垢。
阳极膜上下的四层支撑管分别由四道支撑梁进行支撑。
阳极膜上部支撑梁固定于塔壁上,下部的支撑梁通过两端的调节机构来调节其高度,以实现对阳极膜的张紧。
沉淀极采用玻璃钢蜂窝状结构。
蜂窝状结构较圆管结构截面面积利用率高,玻璃钢材质具有导电性能好、使用寿命长等优点。
(3)阴极装置阴极装置包括阴极线、上下部吊挂装置、绝缘箱。
每个阳极孔中心布置有一条阴极线,采用芒刺型、铅锑合金材质,阴极线固定于上下框架上,框架通过绝缘箱支撑。
石灰石湿法烟气脱硫主要设备介绍

石灰石湿法烟气脱硫主要设备介绍石灰石浆液循环系统是该脱硫工艺的关键设备,它包括搅拌器、泵和沉淀设备等,用于制备和输送石灰石浆液。
石灰石浆液中的Ca(OH)2在反应塔中与烟气中的二氧化硫进行反应生成硫酸钙,完成脱硫过程。
而石膏产生系统则用于处理产生的废料,将其转化为石膏并进行回收利用。
吸收塔是石灰石湿法烟气脱硫工艺中的核心设备,用于接触烟气和石灰石浆液并将二氧化硫吸收下来。
吸收塔通常采用填料或喷淋装置来增加接触面积,从而提高脱硫效率。
另外,氧化风机也是不可或缺的设备,用于通过吸收塔将烟气送出并进行处理后排放。
总的来说,石灰石湿法烟气脱硫主要设备包括石灰石浆液循环系统、石膏产生系统、吸收塔和氧化风机。
这些设备相互配合,共同完成烟气脱硫的工艺,从而降低二氧化硫排放,保护环境。
石灰石湿法烟气脱硫是一种成熟的烟气脱硫工艺,其主要设备包括石灰石浆液循环系统、石膏产生系统、吸收塔和氧化风机。
这些设备在石灰石湿法脱硫工艺中起着至关重要的作用,下面我们将对这些设备的工作原理和特点进行更详细地介绍。
首先是石灰石浆液循环系统,这个系统主要由搅拌器、泵和沉淀设备组成。
石灰石浆液是石灰石颗粒在水中的悬浮液体,它是湿法脱硫工艺中的脱硫剂。
搅拌器主要用于搅拌水和石灰石颗粒,使其形成均匀的浆液;泵则负责将石灰石浆液输送至吸收塔,实现脱硫反应;沉淀设备用于过滤和回收产生的石膏。
石灰石浆液循环系统的核心在于悬浮的石灰石颗粒能够提供充足的反应表面积,使得二氧化硫与石灰石浆液充分接触,从而实现二氧化硫的吸收和脱硫反应。
此外,该系统还需要设备对石膏浆液进行过滤和脱水处理,以实现石膏的回收和再利用。
其次是石膏产生系统,它主要用于处理生产过程中产生的废料,将其转化为石膏并进行回收。
石膏是一种优质的建筑材料,可用于生产石膏板、石膏线等建筑材料,并且还可以作为肥料、吸附剂、填充剂等材料进行深加工利用。
因此,石膏产生系统的设计和运行对于副产品的回收利用至关重要。
湿式除尘脱硫器物理和化学方法介绍

湿式除尘脱硫器物理和化学方法介绍
湿法脱硫设备系统是我公司根据用户实际情况专业设计的标准化脱硫设备工艺,从而对气体进行系统的脱硫设备、再生、熔硫。
脱硫设备采用物理、化学相结合,脱硫处理技术塔具有设备可长期运行、连续脱硫设备、无二次污染而且有副产品硫磺、处理气量大、脱硫设备精度高等优点,整个脱硫设备、再生、熔硫、处理工艺还有高效简单、管理方便、运行费用低等优点。
湿法脱硫设备原理
湿法脱硫设备可以归纳分为物理吸收法、化学吸收法和氧化法三种。
物理和化学方法在硫化氢再处理问题,氧化法是以碱性溶液为吸收剂,并加入载氧体为催化剂,吸收H2S,并将其氧化成单质硫,湿法氧化法是把脱硫设备剂溶解在水中,液体进入设备,与气体混合,气体中的硫化氢(H2S),与液体产生氧化反应,生成单质硫吸收硫化氢的液体有氢氧化钠、氢氧化钙、硫酸钠、硫酸亚铁等。
目前,成熟的氧化脱硫设备法即采用889脱硫设备剂进行脱硫设备,在正常工艺条件下,脱硫设备效率可达99.6%以上。
分为高塔再生和再生槽再生两种配套设备,两种设备各具特点。
我公司可根据用户实际情况,进行设计制造,确保达到用户实际效果需求。
因工艺较复杂,材质要求较高,需要的辅助设备较多,所以设备造价较高,但有副产品,没二次污染等特点。
湿法脱硫设备特点
(1)备可长期不停的运行,连续进行脱硫设备酸。
(2)用PH值来保持脱硫设备效率,运行费用低。
(3)工艺复杂需要专人值守。
(4)设备需保养。
(5)适用于气量大、硫含量高、脱硫设备精度高的气体。
湿法脱硫技术

湿法脱硫技术湿法脱硫技术是一种环保的烟气脱硫方法,它广泛应用于工业和电力行业,用于减少大气中的二氧化硫排放,降低空气污染。
本文将从湿法脱硫技术的原理、工艺和应用等方面进行详细介绍。
一、湿法脱硫技术的原理湿法脱硫技术是利用溶液中的碱性物质与二氧化硫发生化学反应,将二氧化硫转化为可溶于水中的硫酸盐。
主要的反应方程式为:SO2 + Ca(OH)2 → CaSO3 + H2O湿法脱硫技术有两种主要方式,分别是石灰石石膏法和海水脱硫法。
石灰石石膏法是将石灰石干燥研磨成粉末后与烟气中的二氧化硫反应,产生石膏,而海水脱硫法则是通过将海水喷洒到烟气中,利用海水中的碱性物质进行反应。
二、湿法脱硫技术的工艺湿法脱硫技术主要包括烟气净化系统和废水处理系统两部分。
烟气净化系统主要由除尘器、喷射塔和循环泵等设备组成。
烟气通过除尘器进行初步的净化,去除其中的颗粒物和粉尘。
之后,烟气进入喷射塔,喷洒石灰石水浆或海水,与二氧化硫发生反应,形成硫酸盐溶液。
最后,循环泵将硫酸盐溶液回收,净化后再次喷洒到烟气中,循环利用。
废水处理系统用于处理湿法脱硫过程中产生的废水。
废水中含有大量的硫酸盐和其他污染物,需要进行化学处理和沉淀处理,以降低污染物的浓度,使其达到排放标准。
三、湿法脱硫技术的应用湿法脱硫技术被广泛应用于工业和电力行业的烟气净化中,主要用于减少二氧化硫的排放量,保护环境。
以下是湿法脱硫技术在不同领域的应用举例:1. 电力行业:湿法脱硫技术被广泛应用于火电厂和燃煤发电厂中,用于减少烟气中的二氧化硫排放,降低大气污染。
2. 钢铁行业:湿法脱硫技术可以应用于钢铁生产中的高炉和转炉烟气脱硫,减少二氧化硫的排放,减轻对大气环境的污染。
3. 化工行业:湿法脱硫技术可以用于化工厂废气的治理,降低二氧化硫的排放,保护周边的环境质量。
4. 石油行业:湿法脱硫技术可以应用于炼油厂中,减少烟气中的硫化氢等有害气体的排放,改善工作环境。
总之,湿法脱硫技术是一种重要的烟气脱硫方法,具有广泛的应用前景。
除雾器知识大讲堂
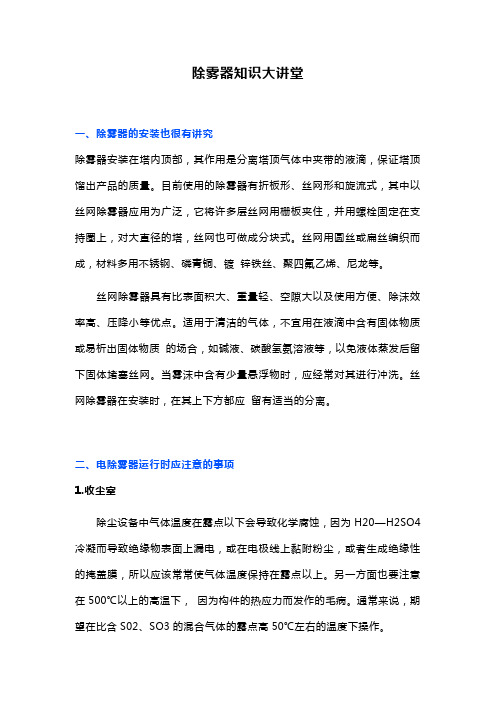
除雾器知识大讲堂一、除雾器的安装也很有讲究除雾器安装在塔内顶部,其作用是分离塔顶气体中夹带的液滴,保证塔顶馏出产品的质量。
目前使用的除雾器有折板形、丝网形和旋流式,其中以丝网除雾器应用为广泛,它将许多层丝网用栅板夹住,并用螺栓固定在支持圈上,对大直径的塔,丝网也可做成分块式。
丝网用圆丝或扁丝编织而成,材料多用不锈钢、磷青铜、镀锌铁丝、聚四氟乙烯、尼龙等。
丝网除雾器具有比表面积大、重量轻、空隙大以及使用方便、除沫效率高、压降小等优点。
适用于清洁的气体,不宜用在液滴中含有固体物质或易析出固体物质的场合,如碱液、碳酸氢氨溶液等,以免液体蒸发后留下固体堵塞丝网。
当雾沫中含有少量悬浮物时,应经常对其进行冲洗。
丝网除雾器在安装时,在其上下方都应留有适当的分离。
二、电除雾器运行时应注意的事项1.收尘室除尘设备中气体温度在露点以下会导致化学腐蚀,因为H20—H2SO4冷凝而导致绝缘物表面上漏电,或在电极线上黏附粉尘,或者生成绝缘性的掩盖膜,所以应该常常使气体温度保持在露点以上。
另一方面也要注意在500℃以上的高温下,因为构件的热应力而发作的毛病。
通常来说,期望在比含S02、SO3的混合气体的露点高50℃左右的温度下操作。
2.电源设备为使电除雾器高效工作,期望常常加上尽可能高的电压。
所以,对导电部分和大地的绝缘,支承物的构造,以及资料等应当予以特别注意。
如有水分、粉尘附着在绝缘瓷瓶表面上,或混入电除雾器的绝缘油中,电气绝缘就会明显恶化,使有用电压下降。
经过完全打扫的绝缘瓷瓶用1000V 兆欧计测量其绝缘电阻大致上是无限大,至少应以20Mn以上作为基准。
绝缘瓷瓶应该依据运用状况、环境来决议其定时打扫周期。
此外,应把绝缘瓷瓶放在箱内并送入热风避免遭到湿气体和粉尘的影响。
晶闸管整流的场合,温度对其工作特性和寿数有影响,所以有必要注意晶闸管周围温度的上升情况。
晶闸管整流器收藏在贮槽内,因为常常受绝缘油等的冷却,所以没有温度上升的问题,但是要注意吸湿呼吸器等的污染。
湿法脱硫学习
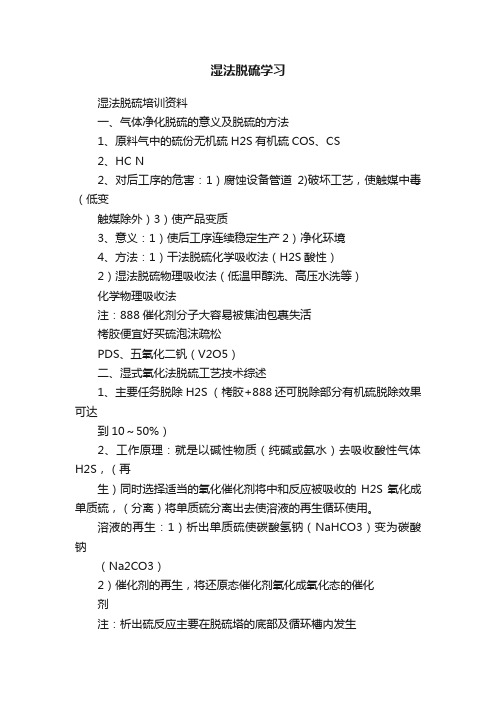
湿法脱硫学习湿法脱硫培训资料一、气体净化脱硫的意义及脱硫的方法1、原料气中的硫份无机硫H2S有机硫COS、CS2、HC N2、对后工序的危害:1)腐蚀设备管道2)破坏工艺,使触媒中毒(低变触媒除外)3)使产品变质3、意义:1)使后工序连续稳定生产2)净化环境4、方法:1)干法脱硫化学吸收法(H2S酸性)2)湿法脱硫物理吸收法(低温甲醇洗、高压水洗等)化学物理吸收法注:888催化剂分子大容易被焦油包裹失活栲胶便宜好买硫泡沫疏松PDS、五氧化二钒(V2O5)二、湿式氧化法脱硫工艺技术综述1、主要任务脱除H2S (栲胶+888还可脱除部分有机硫脱除效果可达到10~50%)2、工作原理:就是以碱性物质(纯碱或氨水)去吸收酸性气体H2S,(再生)同时选择适当的氧化催化剂将中和反应被吸收的H2S氧化成单质硫,(分离)将单质硫分离出去使溶液的再生循环使用。
溶液的再生:1)析出单质硫使碳酸氢钠(NaHCO3)变为碳酸钠(Na2CO3)2)催化剂的再生,将还原态催化剂氧化成氧化态的催化剂注:析出硫反应主要在脱硫塔的底部及循环槽内发生催化剂的好坏取决于催化剂的载氧能力3、湿法脱硫工艺技术特点(吸收、再生、回收三大环节)湿式氧化法脱硫其实质上就是一种伴有氧化反应的湿式中和反应过程第一步、中和反应碱液吸收H2S第二步、采用载氧体催化剂进行催化氧化还原反应,把负二价硫氧化成单质硫第三部、加入空气氧化失活的催化剂使其得到再生,同时将单质硫分离出去Na2CO3+H2S→NaHS+NaHCO32NaHS+O2→2NaOH+S↓三、我厂湿法脱硫工艺流程简介1、气体回炉煤气焦炉气→罗茨风机→1#脱硫塔→2#脱硫塔→甲醇气柜火炬2、溶液流程溶液配制槽→栲胶配置槽→→溶液储槽→溶液泵→再生塔1#2#催化剂活化槽→液封槽脱硫塔1#2#3、硫泡沫流程再生塔顶部→再生塔扩大部分→硫泡沫槽→离心机母液循环槽槽←地槽硫膏外销4、工艺流程特点1)采用湿式氧化法(碱式)双塔串联2级吸收2)催化剂为复式多元催化剂(栲胶+PDS+888)3)高塔鼓风再生工艺4)设计能力处理气量41300m3/h 余量20%设计压力300㎜H2O脱除H2S能力入口5.6g/m3出口20mg/m3四、湿法脱硫主要控制指标1)入口H2S含量5.6g/m32)出口H2S含量20mg/m33)入口焦油含量30mg/m34)入口苯含量≤400-700 mg/m35)萘含量<50 mg/m36)焦炉气压力>6KPa7)焦炉气入口温度25-40℃8)溶液组分总碱度0.4-0.6mol/L(20-30g/L)Na2CO3含量4-6g/LNaHCO3 含量14-26g/l栲胶含量2.5g/L (加PDS时1.0-1.5 g/L)V2O5含量0.5-0.8g/LPDS(888) 含量30ppm(复合使用时10-15ppm)9、溶液循环量750-850m3/h 单塔10、空气含量1000-1700 m3/h 单塔11、再生溶液温度30-40℃12、悬浮硫<0.5g/L 不得超过1.0 g/L13、副盐含量Na2S2O2 Na2SO4 NaCNS(硫氰酸钠)总量<250g/m314、PH值 8.2-8.815、点位栲胶 -180~230mvPDS 888 -150~-210mv几项主要指标的确定1)溶液循环量确定依据①吸收液气比﹥12L/m3②喷淋密度38-48m3/m3.h2)空气量的确定依据①1 H2S需要1.57m3空气实际比例为5-15倍②吹风强度 40-70 60-130m3/m3.h3)再生温度35-42℃>45℃副反应增长速度直线上升<30℃再生速度减慢,再生不完全吸收:增加压力,降低温度有利于吸收4)PH值(总碱度)8.2-8.8(20-30g/L)①NaHCO4/Na2CO4比4-6倍②脱硫催化剂的要求5)点位-150~-210mv观察再生效果,过高引起过度氧化副反应增多点位过高悬浮硫多Na2S2O3多(Na2S2O3硫代硫酸钠)2Na2S2O3+O2→2 Na2SO4+2S↓6)悬浮硫越低越好﹤150g/L 不得超过1.0过高会引起塔的堵塞6)副盐﹤150g/L HC n 0.5~1.5g/m3副盐多不但影响H2S的平衡分压而且由于它们在溶液中的累积降低了有效组分的浓度,且从溶液中的析出,破坏工艺生产条件增加原料碱的消耗降低硫膏的产量。
- 1、下载文档前请自行甄别文档内容的完整性,平台不提供额外的编辑、内容补充、找答案等附加服务。
- 2、"仅部分预览"的文档,不可在线预览部分如存在完整性等问题,可反馈申请退款(可完整预览的文档不适用该条件!)。
- 3、如文档侵犯您的权益,请联系客服反馈,我们会尽快为您处理(人工客服工作时间:9:00-18:30)。
谢谢观赏
离心分离下的液滴脱除 经过加速器加速后的气流高速旋转 向上运动,气流中的细小雾滴、尘颗 粒在离心力作用下与气体分离,向筒 体表面方向运动。而高速旋转运动的 气流迫使被截留的液滴在筒体壁面形 成一个旋转运动的液膜层。从气体分 离的细小雾滴、微尘颗粒在与液膜层 接触后被捕悉,实现细小雾滴与微尘 颗粒从烟气中的脱除。 多级分离器实现对不同粒径液滴的 捕悉 气体旋转流速越大,离心分离效果 越佳,捕悉液滴量越大,形成的液膜 厚度越大,运行阻力越大,越容易发 生二次雾滴的生成;因此采用多级分 离器,分别在不同流速下对雾滴进行 脱除,保证较低运行阻力下的高效除 尘效果。
• 4运行方式
• 4.1 管束除尘器三小时冲洗一次,每一分区冲洗一分钟; • 4.2 管束式除尘装置连续2h运行阻力大于设计压力时,将 单个冲洗水门冲洗时间调节至3分钟,压力恢复正常之后 按原冲洗时间执行; • 4.3 当除尘器冲洗停止运行6h以上时,除尘器冲洗水恢复 运行后,第一次运行冲洗时间延长为3分钟; • 4.4 引风机停止且喷淋层退出运行后,管束装置冲洗水要 加强冲洗后方能退出,停运前冲洗水冲洗时间变更为3分 钟,所有冲洗单元完毕后,管束式除尘器停止运行; • 4.5 定期检查冲洗水管道上的过滤器滤网是否堵塞、是否 破损,若有破损,务必及时更换新的滤网,以免造成管束 冲洗喷嘴的堵塞;
湿法脱硫湍流器及除雾器知识大全
2017.8.15
1.湍流器相关介绍
• 1.1湍流子及湍流层
• 1.2湍流器原理: • 基于多相紊流掺混的强传质机理和气体动力学原理开发的 的旋汇耦合装置产生气液旋转翻覆湍流空间,气液固三相 充分接触,迅速完成传质过程,从而实现了气体高效净化。
• 1.3湍流器安装位置及作用
三相反应的传质速度,使反应更容易进行,有效的提高了 脱硫效率。
• 1.4湍流器工作示意图
• 1.5 湍流塔技术优势
1.5.1均气效果好 塔内烟气和浆液分布不均容易造成烟气短路形成盲区,这也是造成 脱硫效率低和运行成本高的重要原因。安装旋汇耦合装置的脱硫塔, CFD模拟显示均气效果比一般空塔提高15-30%,脱硫装置能在比较经 济、稳定的状态下运行。 1.5.2传质效率高 传质速率是决定脱硫效率的关键指标,而旋汇耦合装置改变进塔气 体的流动状态(由层流状态改变成湍流状态),降低气液膜阻力,增 加液气接触面积,从而提高气液传质速率。 1.5.3降温速度快 从湍流器端面进入的烟气,与浆液通过旋流和汇流的耦合、旋转、 翻覆形成湍流度很大的气液传质体系,烟气温度迅速下降,有利于塔 内气液充分反应。 1.5.4适应性强 适用于不同的工艺和工况,由于良好的均气效果,受气量大小影响 较小,系统稳定性强;受进塔烟气二氧化硫含量变化影响小,脱硫效 率高,适用于不同煤种,对于高硫煤效果更明显。 1.5.5能耗低 增加液气比能提高脱硫效率,但液气比增加的同时也使浆液循环泵 电耗相应增加。采用旋汇耦合专利技术的湍流塔在低的液气比时能保 证较高的脱硫效率,尽管湍流器会增加一部分阻力,但整体系统能耗 会降低,据统计,比同类技术节约电能8%--10%。
• 湍流器安装在吸收塔入口干湿界面和第一层喷淋层之间, 在湍流器平面设置有若干湍流子通过湍流器大梁和吸收塔
本体进行固定,在湍流平面不同位置安装有大小和角度不
相同的湍流子,在原烟气进入吸收塔并通过湍流器时,烟 气和逆流而下的循环浆液混合并进行反应,湍流器的安装
和使用有效的避免了烟气短路现象,并改变了气、液、固
• 3 主要性能保证值
• (1)吸收塔进口SO2浓度3500 mg/Nm3(标干, 6% O2), 吸收塔出口SO2浓度≤25 mg/Nm3(标干, 6% O2);吸收 塔出口NOx排放浓度≤40 mg/Nm3(NOx以NO2计,标干, 6% O2);吸收塔进口粉尘含量≤50 mg/Nm3(标干, 6% O2),吸收塔出口粉尘含量≤5mg/Nm3(标干, 6% O2)。
•1.6管束式除尘装置——结构及原理
1、结构 管束筒体 —内筒壁面光洁,筒体垂直,断面圆滑,无 偏心。 分离器 —实现不同粒径的雾滴在烟气中的分离。 导流环 —控制气流出口状态,防止捕悉液滴被二次 夹带。
•
2ቤተ መጻሕፍቲ ባይዱ原理
使用环境的特点 管束式除尘装置的使用环境是含有大量液滴 的饱和净烟气,特点是雾滴量大,雾滴粒径分 布范围广,由浆液液滴、凝结液滴和尘颗粒组 成;除尘主要是脱除浆液液滴和尘颗粒。 细小液滴与颗粒的凝聚 大量的细小液滴与颗粒在高速运动条件下碰 撞机率大幅增加,易于凝聚、聚集成为大颗粒, 从而实现从气相的分离。 大液滴和液膜的捕悉 除尘器筒壁面的液膜会捕悉接触到其表面 的细小液滴,尤其是在增速器和分离器叶片的 表面的过厚液膜,会在高速气流的作用下发生 “散水”现象,大量的大液滴从叶片表面被抛 洒出来,在叶片上部形成了大液滴组成的液滴 层,穿过液滴层的细小液滴被捕悉,大液滴变 大后跌落回叶片表面,重新变成大液滴,实现 对细小雾滴的捕悉。