PFMEA 卡扣注塑件
注塑成型PFMEA完整版
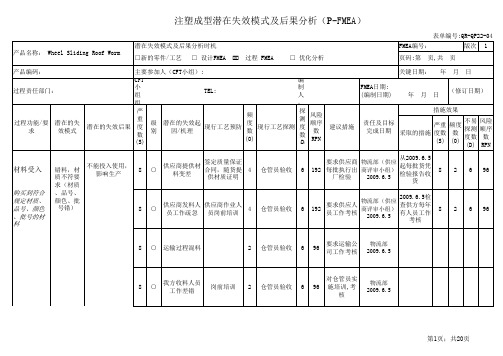
2
24
要求供应商 每批提供
SGS
物流部和销售 部2009.6.5
包装破损
原料漏出,少数致 生产少数
6
●
仓管员搬运方 法不当
岗前培训
2
仓管员目视
6
对仓管员实 72 施培训,考
核
生产部 2009.6.5
进货检验
(检查验证采 购的物料是 否符合采购
原料来料 料品不能使用,耽
错误
误生产
6
●
供应商送货错 依采购订单品
用协议
2
供方委外测试
2
24
进行供应商 物流部和销售 定期审核 部2009.6.5
6
SC ●
没有明确环境 建立环境物质 物质限量要求 过程管理体系
2
体系审核、管 理评审
2
24
进行供应商 物流部和销售 定期审核 部2009.6.5
6
SC ●
未向供应商索 取环境物质含 量的测试报告
建立SGS报告 清单
2
定期审核,确 认
材质不符
影响产品生产,不 能使用
第3页;共20页
严
过程功能/要 求
潜在的失 效模式
潜在的失效后果
重 度 数
材质不符
影响产品生产,不 (S) 能使用
7
级 别
潜在的失效起 因/机理
频
现行工艺预防
度 数
现行工艺探测
(O)
探 测 度 数 (D)
风险 顺序 数 RPN
○
供应商送货错 误
供应商依据采 购单送货
注塑成型潜在失效模式及后果分析(P-FMEA)
产品名称: Wheel Sliding Roof Worm
注塑件过程失效模式及后果分析表模板(PFMEA)

6
包装破损
零件污染,客户投 诉
5
产品碰伤砸伤 客户投诉
6
装箱时确认不足 货物堆积过高
搬运不规范
2
无
3
试验后制定合理堆 积标准
2
无
100目测 100目测 100目测
5 60 5 75 4 48
标签贴错 发错货,客户投诉 5
标签与实物未核对 2
无
100目测
4 40
产品数量不正确
客户投诉
6
80-出货检验
关键尺寸超差
第 1 页,共 2 页
注塑件过程失效模式及后果分析表模板(PFMEA)
零件号
设计责任部门
FMEA 编号
零件名称
关键日期
编制人
车型/年份
系统/子系统/部件
编制日期
核心小组
序号
过程
潜在的失效模式
严 潜在的失效后果 重
度
级 别
潜在的失效原因/机理
频 度 数
现行预防性设计控 制
现行探测性设计控 制
探 测 度
5 60 5 75
建议措施
责任人和目标 完成日期
无
采取的措施
严频探 R 重度测 P 度数度 N
无
无
无
无
不同产品分区放置, 并做好标识
6
2 5 60
无
对纸箱进行固定 6 2 5 60
无
无
无
无
无
不同产品分区放置, 并做好标识
6
2 5 60
无
对纸箱进行固定 6 2 5 60
无
40-原材料烘料
烘料时间不对 烘料温度不对
表面料花 色差
注塑产品PFMEA表

FME A 编产品名称/Product:J ETTA 内框过程职责第页关键日期编制人:刘红FMEA (原2014.5.8控制预防Control and Prevention 发生度Occur 控制探测Control and Detection 探测度Dete 采取的措施/完成日期Measures/C 严重度S 发生度O 探测度D RPN 10 原料采购及时延期影响生产5没合理安排库存设最低库存,及时跟踪2按月订单量的一半设最低库存330包装破包影响产品外观7运输过程损坏专人验收6全检142颗粒大小均匀颗粒连并、偏大影响注塑加工6供应商生产造成抽检2两包/批44810-2 原料入库指定位置,批次分开批次混放发料时混发2作业员未按规定分区,加强管理4专人检查32410-3 配料先进先出混料影响产品品质稳定6作业员未按规定加强员工培训、管理,做好原料标识3专人发放原料,建立原料台账236设定温度过高材料结块6F 作业员疏忽现场放置作业指导书3每小时检查1~2次236设定温度过低材料干燥不充分6F作业员疏忽现场放置作业指导书3每小时检查1~2次47220-2 模具安装安全碰擦、伤害人员受伤、耽误生产6作业员疏忽加强培训、严格按安全作业标准操作2现场管控,季度考核224调试工艺时间长耽误生产进度4工艺员业务水平不够加强培训3月度考核336外观尺寸不合格返工或报废5F 工艺调整不合理制作工艺表,并及时更新,检验员及时跟进5做好首件确认37520-4 注塑成型稳定产品容易出现缺陷报废产品多,产量不够3设备不稳定加强设备保养3设备保养维修记录32720-5 取产品、修边、自检无缩痕、无明显熔接痕、无变形、缺料、拉丝、卡爪断裂缺陷产品容易混进包装返工5F作业员疏忽、质量意识不强定期对员工进行培训、做好标准样品参考5自检记录、月度考核375外观符合要求(如上)缺陷产品容易漏检返工、客诉、退货7F 检验员抽检比率太小或漏抽严格按标准要求每箱抽取两个4产品入库检验记录384尺寸合格尺寸偏差报废7F工艺不合理做好首件确认4加强巡检力度384包装箱无损坏使用不合格纸箱产品损坏、客户退货6作业员疏忽加强作业员培训、管理3按作业指导书操作236数量准确多装或少装客诉、退货6作业员疏忽加强作业员培训、管理4电子称复检372搬运过程损坏客诉、退货6作业员野蛮搬运加强作业员培训、管理3专人负责354码放太高产品损坏、纸箱损坏4作业员不按规定实施作业加强作业员培训、管理3专人负责检查112RPN 建 议 措施Suggestio n Measure 职责和目标完成日期Duties and target completion干燥温度85±5°快速、合理20-1 原料干燥20-3 工艺调试30 检验40 包装50 入库失效潜在原因Potential causes of failure 现行过程 Current Process 实施结果Results of theimplementation 过程Process步骤Step 功能要求Request 分类Clas sify 轻拿轻放、最高堆放5层潜在失效模式Potential FailureMode失效潜在影响The potential impact of failure 严重度Seve rity 10-1 检验 注塑产品PFMEA表潜在失效模式与影响分析Failure mode and effects analysis(过程FMEA/Process FMEA )车型年/项目/Model year/Project:JETTA 1.4T 核心小组/Core Group:项目小组。
塑胶产品易开裂物料 PFMEA 模板-(1

清理完成后技术员对清理工 作确认,用无尘布擦拭,无 脏污即可(详见换料作业指
导书进行作业) 技术员开机前对材料进行核 对确认是否按照规范做业。
技术员对加料人员设定的干 燥温度及时间进行确认,选
用设备进行确认.
材料在炮筒停留时间适 当,生产出外观、功能 合格的产品
成型机台与实际零件重量不匹 配,导致材料降解
7 材料在炮筒停留时间过长
成型周期设置不合理,导致生产 7 材料在炮筒停留时间过长 周期过长,导致材料降解
生产设备性能稳定可 靠,产品一致性好,支 持批量生产
螺杆磨损造成储料不稳定或驱动 曲臂磨损造成锁模不稳定,机台 稳定性差,产品一致性不好,可 能出现小概率的不良品
8
注塑机台维护不到位
模温符合理、正确,生 实测多点模温偏低,导致熔接线 8 实测模具温度不够高,致零件内
产出外观、功能合格的 位置强度下降、开裂
应力偏大
产品
注塑压力合理、正确, 注塑压力过大,使产品内应力大 8 注塑压力过大
生产出外观、功能合格
的产品
速度过快会导致材料温度上升而 8 小浇口情况下,注塑速度过快
5
设备维护不到位
生产前5模样品需废弃, 生产前10模内注塑机参数还不稳 5 生产过程控制不完善
10模后注塑趋于稳定, 定,产品一致性不好,不良率高
产品一致性好
8 零件清洗工艺缺失、或不彻底 金属镶件有油污,跟塑胶材料不
兼容
清洗外观、油污的溶剂跟塑胶材 8 清洗剂选择错误 料不兼容
8 模具上模前保养不规范 顶针油、润滑油等模具用油接触
过大,导致材料降解;背压过 小,导致熔胶内气体量过大,材 料易局部降解,产品易产生气 泡,开裂。
注塑PFMEA范本
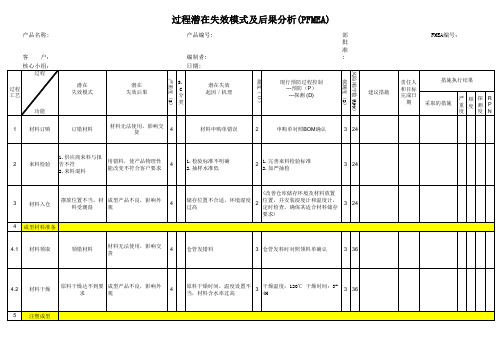
1.制作参数参 照表;提高调 机员的技术水
平 2.经常性清洗 及更换模具配
件
7
2
3 42
5.3 首件确认
外观不良 产品尺寸超差
客户投诉,退货
4
客户投诉,退货
5
2
2 16
未按成型工艺参数表设定
按成型工艺参数表重新设定参数
2
3 30
产品名称:
客 户: 核心小组:
过程 过程 工艺
功能
6 生产自检
潜在 失效模式
类
现行预防过程控制 ---预防(P) ---探测 (D)
过程责任部门:注塑 部 批 准 :
FMEA编号:
建议措施
责任人 和目标 完成日
期
措施执行结果
采取的措施
严频探 R 重度测 P 度 度N
客户投诉,退货
4
产品包装不合理
3
检讨包装书,并修正
3 36
产品名称:
客 户: 核心小组:
过程 过程 工艺
功能
1 材料订购
潜在 失效模式
订错材料
风险顺序数(RPN) 探测度(D)
频度(O)
严重度(S)
过程潜在失效模式及后果分析(PFMEA)
产品编号:
潜在 失效后果
编制者: 日期:
S. C 分
潜在失效 起因/机理
类
现行预防过程控制 ---预防(P) ---探测 (D)
3.锁模力不够,料温过高, 注射压力过大,保压时间过
长,保压压力过大 4.模温过低,注射速度过 3
快,注射压力过大 5.注射速度过快,注射压力
过大 6.保压时间不合理,注射压
力不合理(第二段) 7.原材料中含有一定阻燃
PFMEA 塑料件

用错料,使产品物理性 能改变不符合客户要求
4
1.检验标准不明确 2.抽样水准低
2
1.完善来料检验标准 2.加严抽检
3 24
3
材料入仓
摆放位置不当,材 成型产品不良,影响外 料受潮湿 观
4
(改善仓库储存环境及材料放置 储存位置不合适,环境湿度 位置,并安装湿度计和温度计, 2 过高 定时检查,确保其适合材料储存 要求)
4
产品箱数太多,运输时未将 2 其固定
产品箱数较多时,用保护膜打好 绷带固定好的后再拉货入仓,防 止途中倒塌
3 24
产品外观不良 10 OQC 出货检验 少数,标签错误
客户投诉,退货
4
入库途中损伤,前工序漏检 2
退回生产返工,补货
3 24
客户投诉,补货
4
前工序粗心出错
2
退回生产返工,补货
3 24
11
确认人
表单编号:QR-QA-40-A
过程潜在失效模式及后果分析(PFMEA)
产品名称: 客 户: 核心小组:XXXX
过程 严重度(S) 频度(O) 探测度(D) 过程 工艺 功能 1 材料订购 订错材料 材料无法使用,影响交 货 4 材料申购单错误 2 申购单对照BOM确认 潜在 失效模式 潜在 失效后果 S. C 分 类 潜在失效 起因/机理 现行预防过程控制 ---预防(P) ---探测 (D)
4
技术员操作失误
2 重新对准射嘴
3 24
过程潜在失效模式及后果分析(PFMEA)
产品名称: 客 户: 核心小组:XXXX
过程 严重度(S) 频度(O) 探测度(D) 过程 工艺 功能 潜在 失效模式 潜在 失效后果 S. C 分 类 潜在失效 起因/机理 现行预防过程控制 ---预防(P) ---探测 (D)
大灯饰圈注塑PFMEA

潜在的失效模式及后果分析(过程 FMEA)FMEA编号:GY00001757项目名称:大灯饰圈过程责任部门:生产部编制人:张豪FMEA日期(编制):2001.4.20车型年/车辆类型:轿车关键日期:2001.5FMEA日期(修订):2013.6.10页码:第页共页潜在的失效模式及后果分析(过程 FMEA)FMEA编号:GY00001757项目名称:大灯饰圈过程责任部门:生产部编制人:张豪FMEA日期(编制):2001.4.20车型年/车辆类型:轿车关键日期:2001.5FMEA日期(修订):2013.6.10页码:第页共页潜在的失效模式及后果分析(过程 FMEA)FMEA编号:GY00001757项目名称:大灯饰圈过程责任部门:生产部编制人:张豪FMEA日期(编制):2001.4.20车型年/车辆类型:轿车关键日期:2001.5FMEA日期(修订):2013.6.10页码:第页共页潜在的失效模式及后果分析(过程 FMEA)FMEA编号:GY00001757项目名称:大灯饰圈过程责任部门:生产部编制人:张豪FMEA日期(编制):2001.4.20车型年/车辆类型:轿车关键日期:2001.5FMEA日期(修订):2013.6.10页码:第页共页潜在的失效模式及后果分析(过程 FMEA)FMEA编号:GY00001757项目名称:大灯饰圈过程责任部门:生产部编制人:张豪FMEA日期(编制):2001.4.20车型年/车辆类型:轿车关键日期:2001.5FMEA日期(修订):2013.6.10页码:第页共页潜在的失效模式及后果分析(过程 FMEA)FMEA编号:GY00001757项目名称:大灯饰圈过程责任部门:生产部编制人:张豪FMEA日期(编制):2001.4.20车型年/车辆类型:轿车关键日期:2001.5FMEA日期(修订):2013.6.10页码:第页共页。
注塑产品_PFMEA案例

共 4页 编制
最初编 制日期
FMEA 编号
201
FMEA 版本号
A
电话号码
FMEA 最新 更改日期
过程
要求
潜在失效模式 潜在的失效后果
严
重 等 潜在的失效原因/
度级
机理
S
控制预防
产品表面缩水
产品外观不合格 顾客抱怨
产品尺寸偏大 与相关零件不匹配,
或偏小
使顾客不满意
4、注塑成型
通过注塑机和模 产品表面烧焦 具成型生产出颜 色、外观、尺寸 、性能合格的产
2
《成型条件表》每班 次点检
4
48
2/16
编号: 总成
零件名称/零件号/工 序名称
产品编号:
CFT小组成 员:
分总成
潜在的失效模式及后果分析-PFMEA
零件
设 计/ 过 程 责 任 部 门
制 造 部
关键日期:(要求PFMEA编制完成日及预计生产开始日期)
Hale Waihona Puke PFMEA编制预定完成日:
预计生产开始日:8
9/16
2013-01
A/0
措施结果 R
ODP N
10/16
2013-01
A/0
措施结果 R
ODP N
11/16
2013-01
A/0
措施结果 R
ODP N
12/16
2013-01
A/0
措施结果 R
ODP N
13/16
2013-01
A/0
措施结果 R
ODP N
14/16
2013-01
A/0
不正确
作业
7
- 1、下载文档前请自行甄别文档内容的完整性,平台不提供额外的编辑、内容补充、找答案等附加服务。
- 2、"仅部分预览"的文档,不可在线预览部分如存在完整性等问题,可反馈申请退款(可完整预览的文档不适用该条件!)。
- 3、如文档侵犯您的权益,请联系客服反馈,我们会尽快为您处理(人工客服工作时间:9:00-18:30)。
过程 FMEA
总成
零件名称/零件号/ 工序名称
分总成
卡扣/001/注塑 车型/年份
主要参加成员
零件
设 计 / 过 程 责 任 部 门
产品工程部
关 键
共 2 页 第 页
编 制
FMEA 编号 电话号码
最
FMEA 最新
初
更改日期
严
频
设计和工艺性 能要求
潜在失效模式
潜在的失效后 重 等 潜在的失效原因/ 度
关键控制特性:KCC
施结果
R P N
注:安全/符合关键产品特性:○ 配合/功能关键产品特性:◇
关键控制特性:KCC
施结果
R P N
注:安全/符合关键产品特性:○ 配合/功能关键产品特性:◇
关键控制特性:KCC
施结果
R P N
注:安全/符合关键产品特性:○ 配合/功能关键产品特性:◇
关键控制特性:KCC
设计 FMEA
过程 FMEA
总成
零件名称/零件号/ 工序名称
分总成
卡扣/001/注塑 车型/年份
主要参加成员
零件
设 计 / 过 程 责 任 部 门
产品工程部
关 键
共 2 页 第 页
编 制
FMEA 编号 电话号码
最
FMEA 最新
初
更改日期
设计和工艺性 能要求
潜在失效模式
严
频
潜在的失效后 重 等 潜在的失效原因/ 度
6
材料牌号不正确
次的材料报告并对每
包装破损
2 批次材料委外做试验
材料测试报告
2 24
无
检查包装外观
从仓库将原材 料送到车间
材料不正确
产品性能达不 到预定要求 6
操作工疏忽 1
注塑工艺卡片 1 6
无
注:安全/符合关键产品特性:○ 配合/功能关键产品特性:◇
关键控制特性:KCC
文件号:
潜在的失效模式及后果分析
2
开机前5分钟对每个模 具型腔进行首检
注塑工艺卡片
2 24
无
成品检验
产品断裂等现象
产品报废、顾 客抱怨
7
2
每班1次每次4只进行 测试
测试报告
2 28
无
注:安全/符合关键产品特性:○ 配合/功能关键产品特性:◇
关键控制特性:KCC
文件号:
潜在的失效模式及后果分析
设计 FMEA
过程 FMEA
总成
零件名称/零件号/ 工序名称
文件号:
潜在的失效模式及后果分析
设计 FMEA
过程 FMEA
总成
零件名称/零件号/ 工序名称
分总成
卡扣/001/注塑 车型/年份
主要参加成员
零件
设 计 / 过 程 责 任 部 门
产品工程部
关 键
共 2 页 第 页
编 制
FMEA 编号 电话号码
最
FMEA 最新
初
更改日期
设计和工艺性 能要求
潜在失效模式
分总成
卡扣/001/注塑 车型/年份
主要参加成员
零件
设 计 / 过 程 责 任 部 门
产品工程部
关 键
共 2 页 第 页
编 制
FMEA 编号 电话号码
最
FMEA 最新
初
更改日期
设计和工艺性 能要求
潜在失效模式
严
频
潜在的失效后 重 等 潜在的失效原因/ 度
果
度级
机理
数
S
O
现行过程控制预防
现行过程控制探
严
频
潜在的失效后 重 等 潜在的失效原因/ 度
果
度级
机理
数
S
O
现行过程控制预防
现行过程控制探
探 测 度
R P
测
DN
建议措施
措施结果
责任目标/
完成日期
采取的 措施
SOD
原材料采购 材料不正确 产品不能入库 5
采购单不正确 2 采购前检查采购单
2 20
无
要求供应商提供每批
原材料入厂检 验
材料不正确
产品性能达不 到预定要求
探 测 度
R P
测
DN
建议措施
措施结果
责任目标/
完成日期
采取的 措施
SOD
包装
包装不牢、漏包 散包、顾客不
、破损等
满意
5
没有按包装操作 指导书进行操作
1
对产品首件进行确认
15
无
运到仓库 产品发生磕碰 产品被损坏 5
按包装操作指导书进 按《出厂检验》
1
行转运
进行抽查
15
无
注:安全/符合关键产品特性:○ 配合/功能关键产品特性:◇
施结果
R P N
注:安全/符合关键产品特性:○ 配合/功能关键产品特性:◇
关键控制特性:KCC
按照注塑工艺卡 片进行检查并记 录 每班两次过程
检验
2
14
无
按照注塑工艺卡
修边
影响外观 4 产品有飞边和毛
刺、缺口
操作工失误
2
对产品首件进行确认
片进行检查并记 录 每班两次过程
1
8
无
检验
注:安全/符合关键产品特性:○ 配合/功能关键产品特性:◇
关键控制特性:KCC
文件号:
潜在的失效模式及后果分析
设计 FMEA
果
度级
机理
数
S
O
现行过程控制预防
现行过程控制探
探 测 度
R P
测
DN
建议措施
措施结果
责任目标/
完成日期
采取的 措施
SOD
注塑
产品注塑成型后
有缩孔、裂纹、 产品性能降 变形、缺料等现 低,顾客抱怨
7
象
1、注塑机的工艺 参数设置的不正 确2、没有按操指
导书进行操作
1
检查注塑工艺卡片工 艺参数
开机前5分钟需对每个 模具型腔进行首检并 对产品首件进行确认
果
度级机理数现行过 Nhomakorabea控制预防
产品有飞边和毛
S
O
修边
刺、缺口
影响与其它部 件的装配
3
模具有磨损 2 对产品首件进行确认
现行过程控制探
探 测 度
R P
测
DN
模具操作指导书 进行模具验证
2 12
建议措施 无
措施结果
责任目标/
完成日期
采取的 措施
SOD
尺寸不符
产品使用性能 下降
6
注塑机的工艺参 数设置不合理