【精品】液压传动课程设计液压系统设计举例
液压机液压系统设计

攀枝花学院学生课程设计说明书题目:液压传动课程设计——小型液压机液压系统设计学生姓名:学号:所在院系:机电工程学院专业:机械设计制造及其自动化班级:指导教师:职称:攀枝花学院教务处制攀枝花学院本科学生课程设计任务书注:任务书由指导教师填写。
摘要液压机是一种用静压来加工金属、塑料、橡胶、粉末制品的机械,在许多工业部门得到了广泛的应用。
液压传动系统的设计在现代机械的设计工作中占有重要的地位。
液体传动是以液体为工作介质进行能量传递和控制的一种传动系统。
本文利用液压传动的基本原理,拟定出合理的液压传动系统图,再经过必要的计算来确定液压系统的参数,然后按照这些参数来选用液压元件的规格。
确保其实现快速下行、慢速加压、保压、快速回程、停止的工作循环。
关键词:液压机、课程设计、液压传动系统设计AbstractHydraulic machine is a kind of static pressure to the processing of metal, plastic, rubber, the powder product of machinery, in many industrial department a wide range of applications. The design of the hydraulic drive system in modern mechanical design work occupies an important position. Transmission fluid is the liquid medium for the work carried out energy transfer and control of a transmission system.This paper using hydraulic transmission to the basic principle of drawing up a reasonable hydraulic system map ,and then after necessary calculation to determine the liquid pressure system parameters , Then according to the parameters to choose hydraulic components specification. To ensure the realization of the fast down, slow pressure, pressure maintaining, rapid return, stop work cycle.Key words:hydraulic machine, course design, hydraulic transmission system design.目录摘要 (I)Abstract (II)1 任务分析 (1)1.1技术要求 (1)1.2任务分析 (1)2 方案的确定 (2)2.1运动情况分析 (2)3 工况分析 (3)3.1工作负载 (3)3.2 摩擦负载 (3)3.3 惯性负载 (3)3.4 自重 (3)3.5 液压缸在各工作阶段的负载值 (3)4 负载图和速度图 (5)5 液压缸主要参数的确定 (6)5.1 液压缸主要尺寸的确定 (6)5.2 计算在各工作阶段液压缸所需的流量 (6)6 液压系统图 (9)6.1 液压系统图分析 (9)6.2 液压系统原理图 (9)7 液压元件的选择 (11)7.1液压泵的选择 (11)7.2 阀类元件及辅助元件 (11)7.3油箱的容积计算 (12)8 液压系统性能的运算 (13)8.1 压力损失和调定压力的确定 (13)8.2 油液温升的计算 (14)8.3 散热量的计算 (15)结论 (17)参考文献 (18)1 任务分析1.1技术要求设计一台小型液压压力机的液压系统,要求实现快速空程下行—慢速加压—保压—快速回程—停止的工作循环,快速往返速度为V=5.6 m/min,加压速度1V=70mm/min,其往复运动和加速(减速)时间t=0.02s,压制力为320000N,运2动部件总重为40000N,工作行程400mm,(快进380mm,工进20mm),静摩擦系数fs=0.2,动摩擦系数fd=0.1油缸垂直安装,设计该压力机的液压系统传动。
液压传动系统设计计算例题
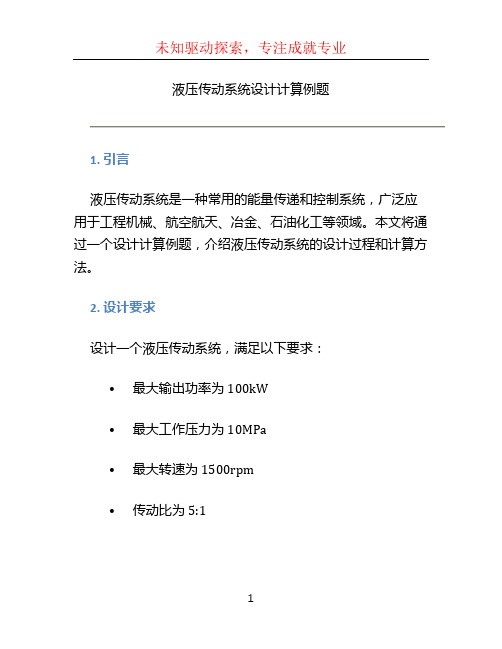
液压传动系统设计计算例题1. 引言液压传动系统是一种常用的能量传递和控制系统,广泛应用于工程机械、航空航天、冶金、石油化工等领域。
本文将通过一个设计计算例题,介绍液压传动系统的设计过程和计算方法。
2. 设计要求设计一个液压传动系统,满足以下要求:•最大输出功率为100kW•最大工作压力为10MPa•最大转速为1500rpm•传动比为5:13. 功率计算根据设计要求,最大输出功率为100kW,转速为1500rpm,可以通过以下公式计算液压机的排量:功率(kW)= 排量(cm^3/rev) × 转速(rpm) × 压力(MPa) × 10^-6由于传动比为5:1,液压泵的排量为液压马达的5倍,因此液压泵的排量为:排量(cm^3/rev) = 功率(kW) / (转速(rpm) × 压力(MPa) × 10^-6 × 5)= 100 / (1500 × 10 × 10^-6 × 5)= 0.133 cm^3/rev4. 泵和马达的选择根据计算结果,液压泵的排量为0.133 cm^3/rev。
在实际中,可以选择一个接近或等于该排量的标准泵来满足需求。
假设我们选择了一台0.15 cm^3/rev的液压泵。
由于传动比为5:1,液压马达的排量为液压泵的1/5,因此液压马达的排量为:排量(cm^3/rev) = 液压泵排量 / 5= 0.15 / 5= 0.03 cm^3/rev同样地,我们可以选择一个接近或等于该排量的标准马达。
5. 油液流量计算油液流量可以通过以下公式计算:流量(L/min) = 排量(cm^3/rev) × 转速(rpm) / 1000液压泵的流量为:流量(L/min) = 0.15 × 1500 / 1000= 0.225 L/min液压马达的流量为:流量(L/min) = 0.03 × 1500 / 1000= 0.045 L/min6. 液压系统元件选择在设计液压传动系统时,除了液压泵和液压马达,还需要选择其他的液压元件,如油箱、油管、阀门等。
液压系统的设计计算举例
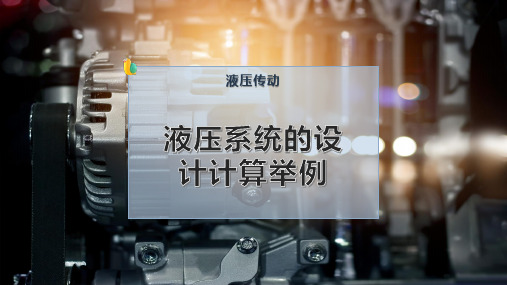
作缸的小腔,即从泵的出口到缸小腔之间的压力损失 Δp = 5.5×105 MPa ,于是小泵出
口压力 pp1 = 21.56×105 MPa (小泵的总效率 η 1 = 0.5 ),大泵出口压力 pp2 =
23.06×105 MPa (大泵的总效率 η 2 = 0.5 )。故电机功率为
P pp1q1 pp2q2 21.56 105 0.167 103 W 23.06 105 0.267 103 W 1 951.5 W
= 0.5 ,大泵出口压力 pp2 = 15.18×105 MPa (大泵的总效率 η 2 = 0.5 )。故电机功率
为
P1
pp1q1 1
pp 2 q2 2
13.68 105 0.167 103 0.5
W 15.18 105 0.267 103 0.5
W
1 267.5 W
(2)工进
小泵的出口压力 pp1 = p1 +Δp1 = 32.19×105 MPa ,大泵卸载,卸载压力取 pp2 =
液压传动
液压系统的设计计算举例
1.1 分析工况及主机工作要求,拟定液压系统方案 1.2 参数设计 1.3 选择元件 1.4 液压系统性能验算
液压系统的设计计算举例
1.1 液分析工况及主机工作要求,拟定液压系统方案
(一) 确定执行元件类型
(二) 确定执行元件的负载、速度变化范围
Fw 18 000 N
1
2
0.5
0.5
综合比较,快退时所需功率最大。据此查产品样本选用Y112M—6型异步电机,
电机功率2.2 kW,额定转速为940 r/min。
(三) 选择液压阀
根据液压阀在系统中的最高工作压力与通过该阀的最大流量,可选出这些元件的 型号及规格。选定的元件列于表中。
液压与气压传动液压系统设计实例
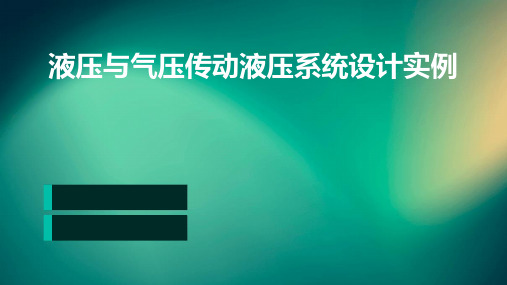
根据系统的工作环境和要求,选择合适的液压介质,如矿 物油、合成油、水等,并确定其清洁度和粘度等参数。
选择合适元件和连接方式
01
选择液压泵和液压马达
根据系统的负载和运动参数,选择合适的液压泵和液压马达,确保其能
够提供足够的流量和压力,并满足系统的效率和精度要求。
02
选择液压缸和阀门
其他常见问题及相应解决方案
气穴现象
产生原因是油液中溶解的气体在低压区析出并形成气泡。解决方案 是减小吸油管路的阻力,避免产生局部低压区。
压力冲击
产生原因是液压阀突然关闭或换向,导致系统内压力急剧变化。解 决方案是在液压阀前设置蓄能器或缓冲装置,吸收压力冲击。
爬行现象
产生原因是液压缸或马达摩擦阻力不均、油液污染等。解决方案是改 善液压缸或马达的润滑条件,使用干净的油液。
关键技术应用
节能环保措施
采用负载敏感技术、电液比例控制技术等 ,提高挖掘机液压系统的控制精度和响应 速度。
通过优化系统设计和选用高效节能元件,降 低挖掘机液压系统的能耗和排放,提高环保 性能。
压力机液压系统性能评估方法论述
评估方法介绍
采用实验测试、仿真分析等方法对压力机 液压系统进行性能评估,获取系统在不同
明确系统的设计目标和约束条件
根据实际需求,明确系统的设计目标,如高效率、 低能耗、高精度等,并考虑成本、空间、重量等 约束条件。
确定系统方案和布局
制定系统原理图
根据设计要求和目标,制定液压系统的原理图,包括液压 缸、液压马达、液压泵、油箱、阀门等元件的连接方式和 控制逻辑。
确定系统布局和安装方式
根据机械设备的结构和空间要求,确定液压系统的布局和 安装方式,包括元件的布置、管路的走向和固定方式等。
液压课程设计--设计一台卧式钻孔组合机床的液压系统

目录0.摘要 (1)1.设计要求 (2)2.负载与运动分析 (2)2.1负载分析 (2)2.2快进、工进和快退时间 (3)2.3液压缸F-t图与v-t图 (3)3.确定液压系统主要参数 (4)3.1初选液压缸工作压力 (4)3.2计算液压缸主要尺寸 (4)3.3绘制液压缸工况图 (5)4.拟定液压系统的工作原理图 (7)4.1拟定液压系统原理图 (7)4.2原理图分析 (8)5.计算和选择液压件 (8)5.1液压泵及其驱动电动机 (8)5.2阀类元件及辅助元件的选 (10)6.液压系统的性能验算 (10)6.1系统压力损失验算 (10)6.2系统发热与温升验算 (11)7.课设总结 (12)0.摘要液压传动技术是机械设备中发展最快的技术之一,特别是近年来与微电子、计算技术结合,使液压技术进入了一个新的发展阶段,机、电、液、气一体是当今机械设备的发展方向。
在数控加工的机械设备中已经广泛引用液压技术。
作为机械制造专业的学生初步学会液压系统的设计,熟悉分析液压系统的工作原理的方法,掌握液压元件的作用与选型是十分必要的。
液压传动在国民经济的各个部门都得到了广泛的应用,但是各部门采用液压传动的出发点不尽相同:例如,工程机械、压力机械采用液压传动的主要原因是取其结构简单、输出力大;航空工业采用液压传动的主要原因取其重量轻、体积小;机床上采用液压传动的主要原因则是取其在工作过程中能无级变速,易于实现自动化,能实现换向频繁的往复运动等优点。
关键词:钻孔组合机床卧式动力滑台液压系统1.设计要求设计一台卧式钻孔组合机床的液压系统,要求完成如下工作循环式:快进→工进→快退→停止。
机床的切削力为25000N ,工作部件的重量为9800N ,快进与快退速度均为7m/min ,工进速度为0.05m/min ,快进行程为150mm ,工进行程40mm ,加速、减速时间要求不大于0.2s ,动力平台采用平导轨,静摩擦系数为0.2,动摩擦系数为0.1 。
液压传动课程设计

【液压传动课程设计说明书设计题目:半自动液压专用铣床液压系统[工程技术系机械设计制造及其自动化4班。
设计者指导教师2016 年 12 月 1 日摘要、液压系统设计计算是液压传动课程设计的主要内容,包括明确设计要求进行工况分析、确定液压系统主要参数、拟定液压系统原理图、计算和选择液压件以及验算液压系统性能等。
现以半自动液压专用铣床液压系统为例,介绍液压系统的设计计算方法。
设计一台多用途大台面液压机液压系统,适用于可塑材料的压制工艺,如冲压、弯曲翻边、落板拉伸等。
要求该机的控制方式:用按钮集中控制,可实现调整,手动和半自动,自动控制。
要求该机的工作压力、压制速度、空载快速下行和减速的行程范围均可根据工艺要求进行调整。
主缸工作循环为:快降、工作行程、保压、回程、空悬。
顶出缸工作循环为:顶出、顶出回程(或浮动压边)。
关键字:液压; 快进; 工进; 快退{前言本课程是机械设计制造及其自动化专业的主要专业基础课和必修课,是在完成《液压与气压传动》课程理论教学以后所进行的重要实践教学环节。
本课程的学习目的在于使学生综合运用《液压与气压传动》课程及其它先修课程的理论知识和生产实际知识,进行液压传动的设计实践,使理论知识和生产实际知识紧密结合起来,从而使这些知识得到进一步的巩固、加深和扩展。
通过设计实际训练,为后续专业课的学习、毕业设计及解决工程问题打下良好的基础。
,(1) 液压传动课程设计是一项全面的设计训练,它不仅可以巩固所学的理论知识,也可以为以后的设计工作打好基础。
在设计过程中必须严肃认真,刻苦钻研,一丝不苟,精益求精。
(2) 液压传动课程设计应在教师指导下独立完成。
教师的指导作用是指明设计思路,启发学生独立思考,解答疑难问题,按设计进度进行阶段审查,学生必须发挥主观能动性,积极思考问题,而不应被动地依赖教师查资料、给数据、定方案。
(3) 设计中要正确处理参考已有资料与创新的关系。
任何设计都不能凭空想象出来,利用已有资料可以避免许多重复工作,加快设计进程,同时也是提高设计质量的保证。
《液压传动》课程教学设计

创新教育科技创新导报 Science and Technology Innovation Herald1441 课程性质、地位与作用我院城市轨道车辆专业主要面向轨道交通车辆生产及轨道交通运营行业企业,培养掌握城市轨道交通车辆的维修、运用、生产及调试技术,具有车辆机械部件装配,电气线路装配、车辆机械及电气故障检测与维修、车辆驾驶等能力,能从事城市轨道车辆维修、驾驶、生产及调试等工作的德、智、体、美等方面全面发展的高素质技能型专门人才。
其面向的就业岗位是轨道车辆电气线路组装、车辆机械部件装配、车辆电气系统调试、车辆售后服务(维修)、城市轨道交通车辆检修工、城市轨道交通车辆运行维护、轨道车辆驾驶、行车调度。
《液压传动》课程是针对车辆机械部件装配、车辆售后服务(维修)、城市轨道交通车辆检修工、城市轨道交通车辆运行维护岗位所开设的一门专业必修基础课程。
本课程所介绍的内容,是学生将来从事机械工程技术人员必须掌握的基础知识。
通过本课程的学习为后续课程通过本课程《城市轨道交通车辆》、《轨道车辆检修》、《轨道车辆装配》的学习奠定基础。
2 教学目标通过本课程的理论教学与实验探索,使学生了解液压传动的原理及组成,熟悉各元件的结构及功能,培养学生安装液压控制回路和分析液压系统功能的能力,具备一定的动手能力,为提高学生的职业能力和可持续性发展打下基础。
2.1 知识目标(1)了解流体力学的基本概念与基本方程。
(2)掌握液压回路的基本工作原理及应用。
(3)掌握液压元件的种类、工作原理、图形符号与功用。
(4)掌握液压传动基本回路的种类及工作原理、应用。
(5)掌握典型液压系统工作原理、系统安装调试和故障诊断的方法。
2.2 能力目标(1)能够正确选用、维护液压元件。
(2)能够安装液压基本控制回路并进行调试。
(3)能够分析液压系统原理,并进行系统与调试。
(4)能判断简单液压回路故障并制定维修方案。
(5)能够分析、排除一般液压系统故障。
机械毕业设计1560液压传动课程设计—全自动方便面压制机液压系统设计
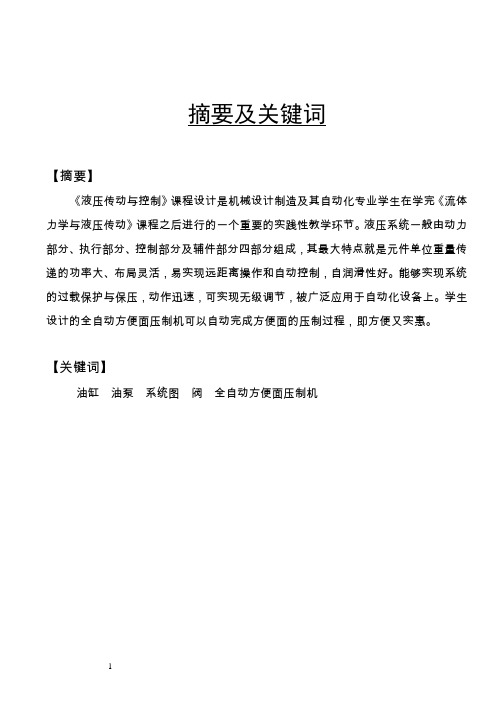
摘要及关键词【摘要】《液压传动与控制》课程设计是机械设计制造及其自动化专业学生在学完《流体力学与液压传动》课程之后进行的一个重要的实践性教学环节。
液压系统一般由动力部分、执行部分、控制部分及辅件部分四部分组成,其最大特点就是元件单位重量传递的功率大、布局灵活,易实现远距离操作和自动控制,自润滑性好。
能够实现系统的过载保护与保压,动作迅速,可实现无级调节,被广泛应用于自动化设备上。
学生设计的全自动方便面压制机可以自动完成方便面的压制过程,即方便又实惠。
【关键词】油缸油泵系统图阀全自动方便面压制机《流体力学与液压传动》课程设计任务书图3-2 型号表示方法液压系统原理图如下图3-3,系统图中有一个齿轮泵,提供动力;一个滤油器;一个压力表,测量油路总压力;两个三位四通电磁换向阀,实现停、通及换向供油;一个二位三通电磁换向阀,实现快进;五个单向阀;四个溢流阀,溢流阀4起溢流阀的作用,保证油泵和回铁1Y A通电,液压缸15活塞上升,到达顶端时,油路继续供油,压力达到压力继电器11的调整值时发信,使电磁铁1Y A断电,3YA通电,液压缸16活塞右行,当到达最右端时,油路压力达到压力继电器13的调整值时发信,使电磁铁3YA断电,4Y A通电,液压缸16活塞左行,当到达最设计体会课程设计是培养学生综合运用所学知识,发现、提出、分析和解决实际问题,锻炼实践能力的重要环节,是对学生实际工作能力的具体训练和考察过程。
回顾起此次课程设计,我感慨颇多。
在整整两个星期的日子里,可以说得是苦多于甜,但是总体来讲,效果还是很好的,不仅巩固了以前所学的知识,还学到了很多在书本上无法学到的知识。
整个设计过程不能说是困难重重,难免会遇到过各种各样的问题,和前两次课程设计相比,力不从心的感觉不再那么强烈,但在设计的过程中还是发现了自己许多不足之处,使自己认识到对以前所学知识理解得不够深刻,掌握得不够牢固,比如说液压元件好多细节没有掌握,以致于错用,对溢流阀的危害没有很深了解,以致于系统图上用了太多的溢流阀,增大了沿程阻力损失,还有原系统图设计过于复杂,在老师的指导下,获得了很大的进步。
- 1、下载文档前请自行甄别文档内容的完整性,平台不提供额外的编辑、内容补充、找答案等附加服务。
- 2、"仅部分预览"的文档,不可在线预览部分如存在完整性等问题,可反馈申请退款(可完整预览的文档不适用该条件!)。
- 3、如文档侵犯您的权益,请联系客服反馈,我们会尽快为您处理(人工客服工作时间:9:00-18:30)。
液压系统设计计算举例液压系统设计计算是液压传动课程设计的主要内容,包括明确设计要求进行工况分析、确定液压系统主要参数、拟定液压系统原理图、计算和选择液压件以及验算液压系统性能等。
现以一台卧式单面多轴钻孔组合机床动力滑台液压系统为例,介绍液压系统的设计计算方法。
1设计要求及工况分析1。
1设计要求要求设计的动力滑台实现的工作循环是:快进工进快退停止。
主要性能参数与性能要求如下:切削阻力F L=30468N;运动部件所受重力G=9800N;快进、快退速度υ1=υ3=0.1m/s,工进速度υ2=0.88×10—3m/s;快进行程L1=100mm,工进行程L2=50mm;往复运动的加速时间Δt=0.2s;动力滑台采用平导轨,静摩擦系数μs=0.2,动摩擦系数μd=0.1。
液压系统执行元件选为液压缸。
1.2负载与运动分析(1)工作负载工作负载即为切削阻力F L =30468N 。
(2)摩擦负载摩擦负载即为导轨的摩擦阻力:静摩擦阻力N 196098002.0s fs =⨯==G F μ动摩擦阻力N 98098001.0d fd =⨯==G F μ(3)惯性负载N 500N 2.01.08.99800i =⨯=∆∆=t g G F υ(4)运动时间快进s1s 1.0101003111=⨯==-υL t工进s 8.56s 1088.0105033222=⨯⨯==--υL t快退s5.1s 1.010)50100(33213=⨯+=+=-υL L t设液压缸的机械效率ηcm =0。
9,得出液压缸在各工作阶段的负载和推力,如表1所列。
表1液压缸各阶段的负载和推力启动加速快进工进反向启动加速快退fsFF=ifdFFF+=fdFF=LfdFFF+=fsFF=ifdFFF+=fdFF=19601480980314481960148098021801650109034942218016501090根据液压缸在上述各阶段内的负载和运动时间,即可绘制出负载循环图F—t和速度循环图υ-t,如图1所示。
2确定液压系统主要参数2.1初选液压缸工作压力所设计的动力滑台在工进时负载最大,在其它工况负载都不太高,参考表2和表3,初选液压缸的工作压力p1=4MPa.2。
2计算液压缸主要尺寸鉴于动力滑台快进和快退速度相等,这里的液压缸可选用单活塞杆式差动液压缸(A1=2A2),快进时液压缸差动连接。
工进时为防止孔钻通时负载突然消失发生前冲现象,液压缸的回油腔应有背压,参考表4选此背压为p2=0。
6MPa。
表2按负载选择工作压力负载/KN <5 5~10 10~20 20~30 30~50 >50工作压力/MPa 〈0.8~11。
5~2 2.5~3 3~4 4~5 ≥5 表3各种机械常用的系统工作压力机械类型机床农业机械小型工程机械建筑机械液压凿岩机液压机大中型挖掘机重型机械起重运输机械磨床组合机床龙门刨床拉床图1 F-t与υ-t图表4执行元件背压力表5按工作压力选取d/D表6按速比要求确定d/D注:1—无杆腔进油时活塞运动速度;υ2—有杆腔进油时活塞运动速度.由式得242621cm 1m 1094m 10)26.04(9.031448)2(-⨯=⨯-⨯=-=p p FA η则活塞直径mm109m 109.0m 10944441==⨯⨯==-ππA D参考表5及表6,得d ≈0。
71D =77mm ,圆整后取标准数值得D =110mm ,d =80mm 。
由此求得液压缸两腔的实际有效面积为242221m 1095m 411.04-⨯=⨯==ππD A 24222222m 107.44m )8.011.0(4)(4-⨯=-⨯=-=ππd D A根据计算出的液压缸的尺寸,可估算出液压缸在工作循环中各阶段的压力、流量和功率,如表7所列,由此绘制的液压缸工况图如图2所示。
表7液压缸在各阶段的压力、流量和功率值cm 2211ηFA p A p =-快进启动2180 —0。
43 ——2121AAPAFp-∆+=121)(υAAq-=qpP1=加速1650 p1+Δp0.77 ——恒速1090 p1+Δp0.66 0。
5 0。
33工进34942 0。
6 3.96 0.84×10—20。
0331221AApFp+=21υAq=qpP1=快退启动2180 —0.49 ——2121AApFp+=32υAq=qpP1=加速1650 0.5 1。
43 ——恒速1090 0。
5 1。
31 0.45 0。
59注:1.Δp为液压缸差动连接时,回油口到进油口之间的压力损失,取Δp=0。
5MPa。
2.快退时,液压缸有杆腔进油,压力为p1,无杆腔回油,压力为p2。
3拟定液压系统原理图3。
1选择基本回路(1)选择调速回路由图2可知,这台机床液压系统功率较小,滑台运动速度低,工作负载为阻力负载且工作中变化小,故可选用进口节流调速回路。
为防止孔钻通时负载突然消失引起运动部件前冲,在回油路上加背压阀。
由于系统选用节流调速方式,系统必然为开式循环系统。
(2)选择油源形式从工况图可以清楚看出,在工作循环内,液压缸要求油源提供快进、快退行程的低压大流量和工进行程的高压小流量的油液。
最大流量与最小流量之比q max/q min=0。
5/(0.84×10—2)≈60;其相应的时间之比(t1+t3)/t2=(1+1。
5)/56。
8=0。
044.这表明在一个工作循环中的大部分时间都处于高压小流量工作。
从提高系统效率、节省能量角度来看,选用单定量泵油源显然是不合理的,为此可选用限压式变量泵或双联叶片泵作为油源。
考虑到前者流量突变时液压冲击较大,工作平稳性差,且后者可双泵同时向液压缸供油实现快速运动,最后确定选用双联叶片泵方案,如图2a所示。
(3)选择快速运动和换向回路本系统已选定液压缸差动连接和双泵供油两种快速运动回路实现快速运动。
考虑到从工进转快退时回油路流量较大,故选用换向时间可调的电液换向阀式换向回路,以减小液压冲击。
由于要实现液压缸差动连接,所以选用三位五通电液换向阀,如图2b所示。
图2液压缸工况图(4)选择速度换接回路由于本系统滑台由快进转为工进时,速度变化大(υ1/υ2=0。
1/(0。
88×10-3)≈114),为减少速度换接时的液压冲击,选用行程阀控制的换接回路,如图2c 所示。
(5)选择调压和卸荷回路在双泵供油的油源形式确定后,调压和卸荷问题都已基本解决.即滑台工进时,高压小流量泵的出口压力由油源中的溢流阀调定,无需另设调压回路。
在滑台工进和停止时,低压大流量泵通过液控顺序阀卸荷,高压小流量泵在滑台停止时虽未卸荷,但功率损失较小,故可不需再设卸荷回路。
3。
2组成液压系统将上面选出的液压基本回路组合在一起,并经修改和完善,就可得到完整的液压系统工作原理图,如图3所示。
在图3中,为了解决滑台工进时进、回油路串通使系统压力无法建立的问题,增设了单向阀6。
为了避免机床停止工作时回路中的油液流回油箱,导致空气进入系统,影响滑台运动的平稳性,图中添置了一个单向阀13.考虑到这台机床用于钻孔(通孔与不通孔)加工,对位置定位精度要求较高,图中增设了一个压力继电器14.当滑台碰上死挡块后,系统压力升高,它发出快退信号,操纵电液换向阀换向。
4计算和选择液压件4。
1确定液压泵的规格和电动机功率(1)计算液压泵的最大工作压力小流量泵在快进和工进时都向液压缸供油,由表7可知,液压缸在工进时工作压力最大,最大工作压力为p 1=3.96MPa ,如在调速阀进口节流调速回路中,选取进油路上的总压力损失∑∆p =0。
6MPa ,考虑到压力继电器的可靠动作要求压差∆p e =0.5MPa ,则小流量泵的最高工作压力估算为()MPa 06.5MPa 5.06.096.3e 11p =++=∆+∆+≥∑p p p p 大流量泵只在快进和快退时向液压缸供油,由表7可见,快退时液压缸的工作压力为p 1=1。
43MPa ,比快进时大。
考虑到快退时进油不通过调速阀,故其进油路压力损失比前者小,现取进油路上的总压力损失∑∆p =0.3MPa ,则大流量泵的最高工作压力估算为图3整理后的液压系统原理图图2选择的基本回路()MPa 73.1MPa 3.043.112p =+=∆+≥∑p p p(2)计算液压泵的流量由表7可知,油源向液压缸输入的最大流量为0。
5×10—3 m 3/s ,若取回路泄漏系数K =1。
1,则两个泵的总流量为L/min 33/s m 1055.0/s m 105.01.133331p =⨯=⨯⨯=≥--Kq q 考虑到溢流阀的最小稳定流量为3L/min ,工进时的流量为0.84×10-5 m 3/s =0.5L/min,则小流量泵的流量最少应为3。
5L/min.(3)确定液压泵的规格和电动机功率根据以上压力和流量数值查阅产品样本,并考虑液压泵存在容积损失,最后确定选取PV2R12—6/33型双联叶片泵。
其小流量泵和大流量泵的排量分别为6mL/r 和33mL/r,当液压泵的转速n p =940r/min 时,其理论流量分别为5.6 L/min 和31L/min ,若取液压泵容积效率ηv =0。
9,则液压泵的实际输出流量为()()L/min33L/min 9.271.5L/min 1000/9.0940331000/9.094062p 1p p =+=⨯⨯+⨯⨯=+=q q q 由于液压缸在快退时输入功率最大,若取液压泵总效率ηp =0。
8,这时液压泵的驱动电动机功率为KW 19.1KW 108.06010331073.1336ppp =⨯⨯⨯⨯⨯=≥-ηq p P 根据此数值查阅产品样本,选用规格相近的Y100L —6型电动机,其额定功率为1.5KW ,额定转速为940r/min.4。
2确定其它元件及辅件(1)确定阀类元件及辅件根据系统的最高工作压力和通过各阀类元件及辅件的实际流量,查阅产品样本,选出的阀类元件和辅件规格如表8所列。
其中,溢流阀9按小流量泵的额定流量选取,调速阀4选用Q —6B 型,其最小稳定流量为0。
03 L/min ,小于本系统工进时的流量0.5L/min 。
表8液压元件规格及型号*注:此为电动机额定转速为940r/min时的流量.(2)确定油管在选定了液压泵后,液压缸在实际快进、工进和快退运动阶段的运动速度、时间以及进入和流出液压缸的流量,与原定数值不同,重新计算的结果如表9所列。
表9各工况实际运动速度、时间和流量表10允许流速推荐值由表9可以看出,液压缸在各阶段的实际运动速度符合设计要求。
根据表9数值,按表10推荐的管道内允许速度取υ=4 m/s ,由式πυqd 4=计算得与液压缸无杆腔和有杆腔相连的油管内径分别为mm2.18mm 10414.360103.624433=⨯⨯⨯⨯⨯==--πυqd mm3.19mm 10414.36010704433=⨯⨯⨯⨯⨯==--πυqd为了统一规格,按产品样本选取所有管子均为内径20mm 、外径28mm 的10号冷拔钢管。