干油集中润滑系统配管简介
川润双线干油集中润滑系统的安装调试说明101125

双线干油集中润滑系统的安装、调试要领书一、润滑系统简介双线干油集中润滑系统主要由三大部分组成:泵站、分配器及终端阀、管路。
泵站定时输出高压油脂,经双线管道送至各个分配器,双线分配器将油脂定量排向给脂管,最终到达轴承等润滑点。
二、施工流程图安装准备工作↓↓泵站设备安装分配器、终端阀安装↓↓管道预安装↓管道清洗↓系统充脂↓试运转调试三、安装准备工作良好的准备工作是顺利施工的关键3.1根据系统图、清单、说明书等了解润滑系统的构成、设备功能及数量、安装尺寸、联接尺寸等,并与现场实际情况核对。
若有差错或缺件要及时补救。
3.2确定泵站、分配器、配管位置,尽量避开温度太高或太低之处,避免与其它设备管线互相干涉,还要使泵站到管路末端尽可能短。
3.3安排好施工工序,避免与主机或其它设备的安装相互干扰,造成窝工、返工。
3.4合理调整人员、施工用设备及能源。
安装工必须懂得润滑设备及各类管接头、管路的安装,至少有一次以上的全过程安装经验。
四、管接头的型式及安装4.1管接头的型式双线干油润滑系统用管接头有插入焊接式、焊接式、锥密封焊接式、卡套式四大类,有二种主要用途:(1)用于管子对管子的连接,如直通(活接头)、直角、三通等。
此外另有高压胶管接头用于活动部分的连接,A型配焊接式;(2)用于管子对设备的连接,如:端直通、端直角等,其端部螺纹要拧入设备的螺孔4.2端直通(直角管接头)同设备的联接安装(1)该类接头端部螺纹主要有公制M(如M18×1.5)、管螺纹G(如G3/8)、锥管螺纹R(如R3/8)三种;(2)在公制M、管螺纹G情况下,螺根处必须套入组合垫圈(或铜垫圈)后再旋入设备,直至垫圈被压紧;(3)在锥管螺纹R情况下,头部螺纹应缠绕密封节,从根部往前缠约1圈半,顶端制1~2牙,方向与螺纹坚固回转方向相反。
对小于R3/8的,用1/2胶带宽度缠绕,然后旋入设备。
4.3插入焊接式管接头安装(1)按需要长度用锯床或切割机等机具切断管子,但绝对不允许用火焰切割或砂轮切割;(2)除去管端内外圆毛刺、金属切屑及污垢;(3)除去管接头的防锈剂及污垢;(4)将管子插入管接头孔内到底;(5)校正位置后点焊,检查与相关件的尺寸位置符合要求后,用氩弧焊将管子与管接头焊牢。
干油集中润滑系统

干油集中润滑系统安装调试维护说明书干油集中润滑系统主要由电动(手动)润滑泵、液压换向阀、双(单)线分配器、干油过滤器、各类管接头、无缝钢管、铜管、软管和各类管夹等组成。
在干油集中润滑系统中,安装和调试对整个润滑系统的正常使用起到非常重要的作用,所以要求安装人员必须对润滑系统中各个设备做到正确的安装,在调试过程中按使用说明书进行正确的使用,切不可蛮干,以下对润滑系统中常用设备的安装和调试逐一进行说明:一、电动润滑泵的安装、调试、维护安装:1、润滑泵应垂直安装和固定在便于维修及灰尘较少的地方,并注意环境温度是否适合泵的工作温度范围。
2、润滑泵应安装在润滑系统的中心位置,这样系统管道较短,压力降可保持在最低限度,以保证泵产生足以克服润滑点背压的压力。
3、电动机旋转方向按转向标牌方向接线。
4、必须使用干净的润滑脂。
因为含有杂质的润滑脂往往是润滑泵和系统产生故障的主要原因,充填润滑脂时必须使用专用加油泵,通过加油口加入。
泵在首次充填润滑脂前,最好先加些润滑油,因为润滑油流动作好,会充满所有的部位,有利于排除空气。
如有的润滑部位不能使用润滑油,那么润滑泵必须运转至无空气存在的润滑脂从管道末端排出为止。
5、为了防止润滑脂进入压力表,在首次启动润滑泵前,要拆下带有压力表的接头和弯管,然后启动润滑泵,直至润滑脂从接头处排出为止,然后重新装上弯管并使之紧固,在弯管内注满润滑油,最后装上带有压力表的接头。
维护和保养:1、过滤网:过滤网要经常清洗,必要时还需用汽油或煤油清洗。
2、限压阀:可以从0调到40MPa任意调节,调节螺钉右旋可把压力调高,左旋则调低,限压阀的设定压力不能超过泵的最大工作压力,出厂时已调至30MPa。
3、保险片:由于某些故障原因而系统中的压力达到50MPa时,保险片破裂,润滑脂从管中溢出。
在新的保险片装入前,首先要查明系统超压的原因并排除故障。
调换保险片时须把凸面朝上,且须放入2片,如保险片装反,泵会因压力超过允许值而遭到损坏。
润滑脂(干油)集中润滑系统

润滑脂(干油)集中润滑系统一、润滑脂(干油)集中润滑系统的结构原理所谓“干油”,就是润滑脂;目前常用的干油集中润滑系统都是开式的,即润滑脂在润滑点消耗掉,不返回油桶。
典型的智能式干油集中润滑系统由电动油脂泵、加油泵、过滤器、分配器、控制柜、管路附件组成(见下图),其油路采用一个电磁换向阀控制一个润滑点的方式,管路布置和工作原理简单,故障判断和处理相对于使用单线或双线分配器容易;缺点是分配器体积较大。
该系统的突出特点是将传统的集中润滑与现代高新技术相结合,采用PLC对系统进行自动控制,并可实现计算机远程监控。
控制柜中的PLC是该系统的核心,它控制系统实现:按设定的循环间隔时间,启动系统,各电磁换向阀依次得电动作,逐点给油;通过设定各电磁换向阀得电时间,控制各点给油量;电磁换向阀得电时,流量传感器检测油流信号并反馈,通过指示灯或在监控电脑画面上显示;系统高、低压、油位低自动保护及报警;系统运行和故障记录功能。
采用计算机远程监控,则更可凸显系统控制和维护方便的高科技特点。
系统适用于上百个给油点的大型机械设备或生产线的集中润滑,并可与单线式集中润滑系统相结合使用。
与这些优点对应的是:系统的维护对电气人员、系统的使用对系统管理人员素质要求较高;系统的价格较高。
二、润滑脂(干油)集中润滑系统的优点智能干油集中润滑系统可根据设备工作状态,现场环境温度不同条件及设备润滑部位的不同要求,准确、定时、定量、可靠的满足各种润滑要求。
以维克森VICSEN-MX型集中润滑系统为例,该系统采用递进式工作方式,泵设计成可间歇或持续工作,这样可以按照不同的需要来编辑运行程序,一个直联的减速电机驱动泵内凸轮工作,可以同时驱动3个外置泵单元。
每个泵单元都配有溢流过压保护阀防止超压损坏。
可设置1-200个润滑点,能够准确及时地推送油脂到各个润滑点,还可以显著提高设备寿命,更加节省润滑脂的用量,多个润滑点可以采用统一的一个集中润滑系统,不仅可以大幅度的降低运营成本,而且维护起来也更加简单。
干油润滑维护手册

目录1.系统用途及性能1.1概述1.2系统组成及性能1.3润滑原理及配管2.润滑泵站操作说明2.1手动2.2自动2.3持续3.集中润滑系统安装、维护、操作说明3.1管道和支管3.2管道连接3.3给油器3.4压差开关3.5压力表安装3.6接头安装3.7系统试运转3.8润滑剂种类和润滑次数3.9电气操作•双线集中润滑系统的故障检查5 .设备储存6 .易损件清单1 .系统用途及性能1.1 概述 此干油集中润滑系统为双线终端式系统。
供“340连轧管机组从穿孔机区到冷床 区设备近2700点的润滑,共有12个站区,其中有11个站区需要进行干油集中润滑, 每个站区一套干油润滑系统,其中包括:G1穿孔机入口区干油集中润滑系统(共107 点,不含穿孔机主机上润滑点)、G2穿孔机出口区干油集中润滑系统(共118点,不 含SMS 顶头更换装置上润滑点)、G3穿孔机区干油集中润滑系统(共120点,不含 穿孔机主机上润滑点)、G4芯棒冷却区干油集中润滑系统(共286点)、G5芯棒循环 区干油集中润滑系统(共207点)、G6连轧机区干油集中润滑系统(共144点)、G7 连轧脱管机区干油集中润滑系统(共106点)、G8炉前运输设备区干油集中润滑系统 (共375点)、G9定径机区干油集中润滑系统(共124点)、G10-1#冷床区干油集中 润滑系统(共465点)和G11-2#冷床区干油集中润滑系统(共638点)。
而G12为 限动齿条干油喷射润滑系统,其设备全部由用户自备。
此系统共设有三种润滑周期,第一种润滑周期为6小时,G1、G2、G4、G5、G7、 G8、G9、G10和G11均为此周期的集中润滑系统;第二种润滑周期为30分钟,G3 即为此周期的集中润滑系统;第三种润滑周期为2小时,G6即为此周期的润滑系统。
已经设定的润滑周期时间,用户可视设备运行需要作相应的调整和变更,以达到满 意的润滑效果。
1.2 系统组成及性能每个站区的干油集中润滑系统均由干油润滑站、电器控制箱、主管及支管11 12路、管接头、分配器及压差开关和压力表组成。
干油集中润滑系统
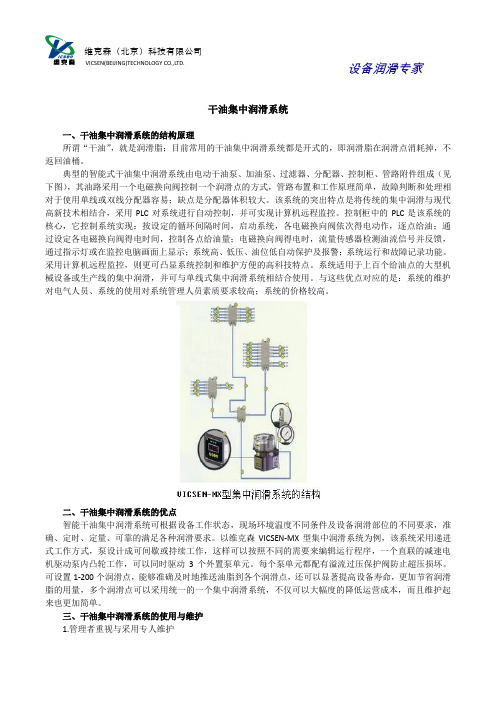
干油集中润滑系统一、干油集中润滑系统的结构原理所谓“干油”,就是润滑脂;目前常用的干油集中润滑系统都是开式的,即润滑脂在润滑点消耗掉,不返回油桶。
典型的智能式干油集中润滑系统由电动干油泵、加油泵、过滤器、分配器、控制柜、管路附件组成(见下图),其油路采用一个电磁换向阀控制一个润滑点的方式,管路布置和工作原理简单,故障判断和处理相对于使用单线或双线分配器容易;缺点是分配器体积较大。
该系统的突出特点是将传统的集中润滑与现代高新技术相结合,采用PLC对系统进行自动控制,并可实现计算机远程监控。
控制柜中的PLC是该系统的核心,它控制系统实现:按设定的循环间隔时间,启动系统,各电磁换向阀依次得电动作,逐点给油;通过设定各电磁换向阀得电时间,控制各点给油量;电磁换向阀得电时,流量传感器检测油流信号并反馈,通过指示灯或在监控电脑画面上显示;系统高、低压、油位低自动保护及报警;系统运行和故障记录功能。
采用计算机远程监控,则更可凸显系统控制和维护方便的高科技特点。
系统适用于上百个给油点的大型机械设备或生产线的集中润滑,并可与单线式集中润滑系统相结合使用。
与这些优点对应的是:系统的维护对电气人员、系统的使用对系统管理人员素质要求较高;系统的价格较高。
二、干油集中润滑系统的优点智能干油集中润滑系统可根据设备工作状态,现场环境温度不同条件及设备润滑部位的不同要求,准确、定时、定量、可靠的满足各种润滑要求。
以维克森VICSEN-MX型集中润滑系统为例,该系统采用递进式工作方式,泵设计成可间歇或持续工作,这样可以按照不同的需要来编辑运行程序,一个直联的减速电机驱动泵内凸轮工作,可以同时驱动3个外置泵单元。
每个泵单元都配有溢流过压保护阀防止超压损坏。
可设置1-200个润滑点,能够准确及时地推送油脂到各个润滑点,还可以显著提高设备寿命,更加节省润滑脂的用量,多个润滑点可以采用统一的一个集中润滑系统,不仅可以大幅度的降低运营成本,而且维护起来也更加简单。
干油集中润滑系统配管简介
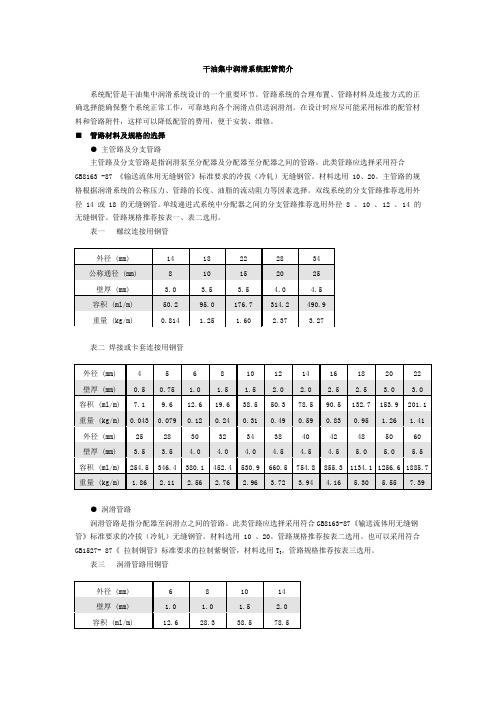
干油集中润滑系统配管简介系统配管是干油集中润滑系统设计的一个重要环节。
管路系统的合理布置、管路材料及连接方式的正确选择能确保整个系统正常工作,可靠地向各个润滑点供送润滑剂。
在设计时应尽可能采用标准的配管材料和管路附件,这样可以降低配管的费用,便于安装、维修。
■管路材料及规格的选择●主管路及分支管路主管路及分支管路是指润滑泵至分配器及分配器至分配器之间的管路。
此类管路应选择采用符合GB8163 -87 《输送流体用无缝钢管》标准要求的冷拔(冷轧)无缝钢管。
材料选用 10、20。
主管路的规格根据润滑系统的公称压力、管路的长度、油脂的流动阻力等因素选择。
双线系统的分支管路推荐选用外径 14 或 18 的无缝钢管。
单线递进式系统中分配器之间的分支管路推荐选用外径 8 、 10 、 12 、 14 的无缝钢管。
管路规格推荐按表一、表二选用。
表一螺纹连接用钢管表二焊接或卡套连接用钢管●润滑管路润滑管路是指分配器至润滑点之间的管路。
此类管路应选择采用符合GB8163-87《输送流体用无缝钢管》标准要求的冷拔(冷轧)无缝钢管。
材料选用 10 、20。
管路规格推荐按表二选用。
也可以采用符合GB1527- 87《拉制铜管》标准要求的拉制紫铜管,材料选用T3。
管路规格推荐按表三选用。
表三润滑管路用铜管●运动部分用管路系统中机器移动、转动部件之间所用的分支管路、润滑管路推荐采用 Q/YT330-98《高压胶管总成》中所列的高压软管。
■管路连接方式的选择●主管路及分支管路(1)推荐选用焊接式或锥密封连接形式。
对于管子外径不大于 18 的管路也可以选用卡套式连接。
(2)螺纹连接式管路只能用于公称压力不大于 2OMPa 的系统。
●润滑管路推荐选用卡套式连接方式。
用钢管时选用卡套式管接头,用铜管时选用铜管用接头。
■管路设计安装中的注意事项(1)对于腐蚀性环境,管路材料应选用符合 GB2270-80《不锈钢无缝钢管》标准要求的冷拔(冷轧)不锈钢无缝钢管。
双线干油集中润滑系统的安装
3.4合理调整人员、施工用设备及能源。
安装工必须懂得润滑设备及各类管接头、管路的安装,至少有一次以上的全过程安装经验。
4、管接头的型式及安装4.1管接头的型式双线干油润滑系统用管接头有插入焊接式、焊接式、锥密封焊接式、卡套式四大类,有二种主要用途:(1)用于管子对管子的连接,如直通(活接头)、直角、三通等,此外另有高压胶管接头用于活动部份的连接,A型配焊接式;(2)用于管子对设备的连接,如:端直通、端直角等,其端部螺纹要拧入设备的螺孔上。
4.2端直通(直角管接头)同设备的联接安装(1)该类接头端部螺纹主要有公制M(如M18×1.5)、管螺纹G(如G3/8)、锥管螺纹R(如R3/8)三种;(2)在公制M、管螺纹G情况下,螺根处必须套入组合垫圈(或铜垫圈)后再旋入设备,直至垫圈被压紧;(3)在锥管螺纹R情况下,头部螺纹应缠绕密封节,从根部往前缠约1圈半,顶端制1~2牙,方向与螺纹坚固回转方向相反。
对小于R3/8的,用1/2胶带宽度缠绕,然后旋入设备。
4.3插入焊接式管接头安装(1)按需要长度用锯床或切割机等机具切断管子,但绝对不允许用火焰切割或砂轮切割;(2)除去管端内外圆毛刺、金属切屑及污垢;(3)除去管接头的防锈剂及污垢;(4)将管子插入管接头孔内到底;(5)校正位置后点焊,检查与相关件的尺寸位置符合要求后,用氩弧焊将管子与管接头焊牢。
4.4焊接式及锥密封焊接式管接头安装(1)按4.3条(1)(2)(3)方法切管、除屑、清洗,并暂时取下管接头内O型密封圈;(2)将管子口对准接管贴平,校正位置后点焊,检查与相关件的尺寸、位置符合要求后,用氩弧焊将对接口焊牢;(3)管道清洗后正式安装时,放入O型密封圈;(4)安装后,慢慢拧紧螺母,直至管子不能动时,再拧紧螺母2/3~4/3圈。
4.5卡套式管接头安装(1)按4.3条(1)(2)(3)方法切管、除屑、清洗,同时还要保证管子圆度;(2)将螺母、卡套先后套入管子,卡套前端刃口(小径端)距管子口至少3mm,然后将管子插入接头体内锥孔,顶到为止;(3)慢慢拧紧螺母,同时转动管子直至不动时,再拧紧螺母2/3~4/3圈;(4)拆开检查卡套是否切入管子,位置是否正确。
干油润滑系统说明书
目录1.滑系统说明书2.润滑系统图3.电控柜使用和维修4.泵站及其原理图5.电控原理图(一)6.电控原理图(二)7.电控原理图(三)8.电控柜外形图9.电控柜内部元件图10.电控柜JD1和JD2端子排接线图11.泵站端子接线图无料钟炉顶集中式干油润滑系统一、系统构成系统由2个不同的润滑周期组成。
通过2个自动二位四通阀来分别单独驱动2个润滑周期;●4小时润滑周期(包括上密阀、料流阀、柱塞阀、及均压阀、放散阀)●45分钟润滑周期(包括溜槽传动齿轮、行星齿轮箱、下密封阀)干油润滑系统按双管线原则工作,基本组成如下;●润滑泵—主泵和备用泵。
●两位四通换向阀—直流电机控制的两位四通换向阀把泵提供的润滑油送入与干油分配器连接的主管中。
●干油分配器—输送一定设定量润滑油到润滑点,这与通过输送管到相应润滑点的背压无关。
●终端压力开关—其压力已设定好,此压力开关将使泵停机,其在预定时间结束后启动两位四通换向阀使其换向。
输送到干油分配器2组相反出口的润滑点的润滑油量可以满足不同润滑需求量。
另外,可以通过更多的支管及连接更多的干油分配器来扩大系统。
只要泵的压力和润滑油输出量允许这样做。
通过装在同一润滑系统内不同润滑周期的几个换向阀可以随意地把系统分成几个支系统。
1.1带干油箱的集中润滑泵站泵站装有以下安全装置1.1.1电液压力开关压力开关的目的是:当压力到达预定的最大压力时断开润滑泵的电机驱动,从而保护泵和电机。
压力开关在预设压力(160—400bar)断开泵的电机。
(目前定为250bar)1.1.2压力表用于目测工作压力。
1.1.3过滤器阻止杂质进入主管路1.1.4安全阀如果电液压力开关失效,安全阀作为最后防线可保护泵不受太高的压力而损坏,安全阀的设定压力为410bar且是防堵塞的1.1.5液位控制机构30升的油箱的高低液位控制是借助于随动板及限位开关完成的。
它将油箱的油位正常和低油位的信号反馈到电控柜以及油箱旁的指示灯(红色灯表示油位低)(但我们只采用了油箱的低油位报警控制功能)油箱的液位被检测,如果达到了报警下线则发出报警信号,泵将被断开。
干油润滑系统介绍
干油润滑系统介绍干油润滑系统介绍000重要提醒:系统检测到您的帐号可能存在被盗风险,请尽快查看风险提示,并立即修改密码。
| 关闭网易博客安全提醒:系统检测到您当前密码的安全性较低,为了您的账号安全,建议您适时修改密码立即修改 | 关闭工作原理单线式集中润滑系统由泵站输出润滑脂,通过一级(母)分配器由一路输油变成多路出油。
这些多路出油再由二级(子)分配器分成更多的分支油路;根据需要还可以增加三级(孙)分配器,这样便组成单线递进式油路,可以向数百个润滑点供送润滑脂。
特点1、供油主管道只需一根,配管简单,费用低;2、对活动部分的润滑点可实施供油;3、对处于机构紧凑、环境恶劣、部位重要的润滑点可实现自动加油,以提高加油的可靠性;4、只要系统在工作,每个润滑点都能获得预定的给脂量,油脂不会浪费;5、在全部润滑点中,只要有任一处堵塞,通过各种形式的发讯器即能报警,所以只要监视一台母分配器的动作,就可实现对全系统的监视。
1、电动润滑泵方式电控柜内有计数器和计时器,其中计数器是与同一级分配器上行程开关相关联的。
当一级分配器完成一个分油循环,分配器的柱塞便接触行程开关一次,计数器计入一个数。
当计数器上达到规定的计数次数时,指定电动润滑泵停止或二位二通电磁阀闭合。
经过设定的时间间隔后系统重新开始工作(电机运转或二位二通电磁阀打开)。
电控柜内的计时器是用来设定单位时间内输入系统的油脂量。
当设定的单位时间内计数器计入的数值未达到设定值时,电控柜自动报警。
另外系统管道中压力超过额定压力的限制值时也会自动报警。
二位二通电磁阀用来切断或打开主管道的通路。
如系统润滑点较多,采用并联式集中润滑,则二位二通电磁阀在系统中的作用更为突出,每个并联支路必须配备一台二位二通电磁阀。
该系统配管费用较低,且能满足每个润滑点所需的润滑脂的数量,同时能实现定时、定量,无一遗漏地向每个润滑点供送清洁润滑脂。
①电动润滑泵;②电动加油泵;③干油过滤器;④二位二通电磁阀;⑤行程开关;⑥主分配器;⑦子分配器;⑧孙分配器;⑨电控柜2、手动润滑泵方式手动润滑泵给油时,母递进分配器中的运动指示器每运动一次,该系统对每个润滑点给油一次。
润滑脂(干油)集中润滑系统
润滑脂(于油)集中润滑系统特点:(1)供脂量精确,避免不必要的浪费;(2)供脂时间准确,防止摩擦副润滑不足;(3)自动化程度高,可节省人力和减轻劳动强度;{4)系统工作可靠性高,可避免漏加润滑脂造成的摩擦功耗增加和设备磨损破坏;(5)设备投资较大.润滑脂润滑特点:粘着性强、润滑持续时间长、流动性差、无法循环使用。
要求:定时间,定消耗量补充.足够的润滑脂,保持良好的润滑状态:避免过量而造成浪费,污染.必须保证:定时、定量供脂.第一节干油集中润滑系统的组成和工作原理干油集中润滑系统组成:一般由润滑脂泵(于油泵),润滑脂过滤器,压力表、换向装置、输脂主管、给油器,输脂支管等组成,一、双线非顺序式干油集中润滑系统(1)双线非顺序式给油器工作原理给油器工作原理如下:Ⅱ管高压一进入给油器配油腔下腔一推动配油柱塞3向上移动一配油腔下腔与下通道接通,将上通道与出脂口A接通一H管经配油腔下腔一下通道进人压油腔下腔一推动压油柱塞2向上移动一将压油腔上腔的润滑脂经上通道、出脂口A送人连接A口的摩擦副支管.供脂主管压力每交替变化一次,即完成一次供脂动作.供脂量由压油腔的直径和压油柱塞的行程决定.指示杆6与压油柱塞2为刚性连接,通过调节螺丝8在护罩7上的位置,可以改变指示杆6的行程,从而改变压油柱塞2的行程,而达到改变供脂量,在护罩7通过视窗观察指示杆6的运动情况,判定给油器的工作情况。
(2)手动干油站工作原理手动于油站由人工驱动的柱塞式油泵,换向阀,储脂筒,压力计、单向阀、过滤器和手摇柄等组成。
、工作原理如下:干油站的手摇柄与小齿轮1联接,摇动手摇柄一小齿轮带动齿条柱塞2左右往复运动。
柱塞2向左运动,单向阀3关闭,压力脂将左腔的单向阀4顶开,润滑脂在柱塞的压迫下经过换向阀6,进人主脂管Ⅱ.当所有的给油器工作完毕后,随着柱塞式油泵不断工作主腊管Ⅱ内的压力迅速升高,通过压力表可观察到主脂管Ⅱ内66压力值。
当主脂管Ⅱ内的压力达到定值时,表明所有的给油器工作完毕,一次供脂过程已经结束。
- 1、下载文档前请自行甄别文档内容的完整性,平台不提供额外的编辑、内容补充、找答案等附加服务。
- 2、"仅部分预览"的文档,不可在线预览部分如存在完整性等问题,可反馈申请退款(可完整预览的文档不适用该条件!)。
- 3、如文档侵犯您的权益,请联系客服反馈,我们会尽快为您处理(人工客服工作时间:9:00-18:30)。
干油集中润滑系统配管简介
系统配管是干油集中润滑系统设计的一个重要环节。
管路系统的合理布置、管路材料及连接方式的正确选择能确保整个系统正常工作,可靠地向各个润滑点供送润滑剂。
在设计时应尽可能采用标准的配管材料和管路附件,这样可以降低配管的费用,便于安装、维修。
■管路材料及规格的选择
●主管路及分支管路
主管路及分支管路是指润滑泵至分配器及分配器至分配器之间的管路。
此类管路应选择采用符合
GB8163 -87 《输送流体用无缝钢管》标准要求的冷拔(冷轧)无缝钢管。
材料选用 10、20。
主管路的规格根据润滑系统的公称压力、管路的长度、油脂的流动阻力等因素选择。
双线系统的分支管路推荐选用外径 14 或 18 的无缝钢管。
单线递进式系统中分配器之间的分支管路推荐选用外径 8 、 10 、 12 、 14 的无缝钢管。
管路规格推荐按表一、表二选用。
表一螺纹连接用钢管
表二焊接或卡套连接用钢管
●润滑管路
润滑管路是指分配器至润滑点之间的管路。
此类管路应选择采用符合GB8163-87《输送流体用无缝钢管》标准要求的冷拔(冷轧)无缝钢管。
材料选用 10 、20。
管路规格推荐按表二选用。
也可以采用符合GB1527- 87《拉制铜管》标准要求的拉制紫铜管,材料选用T3。
管路规格推荐按表三选用。
表三润滑管路用铜管
●运动部分用管路
系统中机器移动、转动部件之间所用的分支管路、润滑管路推荐采用 Q/YT330-98《高压胶管总成》中所列的高压软管。
■管路连接方式的选择
●主管路及分支管路
(1)推荐选用焊接式或锥密封连接形式。
对于管子外径不大于 18 的管路也可以选用卡
套式连接。
(2)螺纹连接式管路只能用于公称压力不
大于 2OMPa 的系统。
●润滑管路
推荐选用卡套式连接方式。
用钢管时选用卡
套式管接头,用铜管时选用铜管用接头。
■管路设计安装中的注意事项
(1)对于腐蚀性环境,管路材料应选用符合 GB2270-80《不锈钢无缝钢管》标准要求的冷拔(冷轧)不锈钢无缝钢管。
(2)管子内必须清洁,不允许有氧化皮、锈斑等杂质。
采用卡套式连接的管路组装前管子要进行表面处理。
采用焊接式连接的管路,焊接后再进行表面处理。
(3)要用切管器切割管子,不要用锯子锯,以免产生铁屑。
(4)弯管时尽量采用冷弯,避免热弯,防止产生氧化皮。
(5)管路布置应尽量避开温度太高或太低的地方。
高温将造成油脂老化变质,低温将增大油脂的流动阻力。
(6)管路应布置在被润滑的设备或墙壁上,用管夹固定。
应布置在没有机械干涉,便于观察及维修的地方。