SEP1921-84锻件超声波检测详细资料
常用超声波探伤标准要求
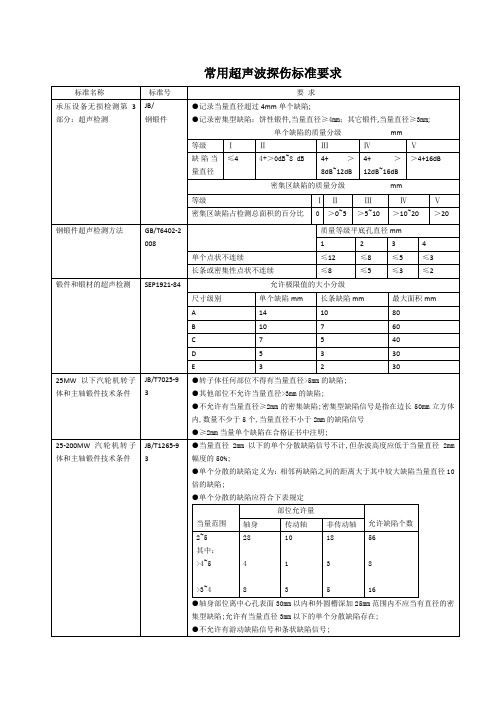
50~200MW汽轮发电机转子锻件技术条件
JB/T1267-93
●不允许有当量直径≥连续性缺陷信号和游动缺陷信号;
●当量直径小于2mm的缺陷不计,允许2~4mm缺陷存在,但相邻两缺陷的距离不小于其中较大缺陷直径的7倍;
●单个分散的缺陷应符合下表规定
允许极限值的大小分级
●不允许有游动信号和条状缺陷信号;
50~200MW汽轮发电机无中心孔转子锻件技术条件
JB/T8706-1998
●当量直径小于mm的缺陷不计,不允许有当量直径等于或大于mm连续缺陷信号和流动缺陷信号;
●在锻件中心φ150 mm范围内,不允许有当量直径大于mm100 MW以下转子锻件,不允许有当量直径大于mm的单个缺陷和大于或等于当量直径mm的密集缺陷信号;
≥3~4
3
1
4
8
总数
15
6
9
30
50MW以下汽轮发电机无中心孔转子锻件技术条件
JB/T 8705-1998
●小于当量直径2 mm的缺陷不计;
●不允许有连续性缺陷信号及游动信号;
●在中心φ150 mm范围内不允许有当量直径大于4 mm的缺陷和大于或等于当量直径mm的密集缺陷信号;
●外圆槽深加25 mm范围内不允许有当量直径大于4 mm的缺陷,其它区域允许有当量直径2~5mm分散的单个缺陷存在,但相邻两个缺陷的距离不小于其较大缺陷直径的5倍;
当量范围
部位允许量
允许缺陷个数
轴身
传动轴
非传动轴
2~5
其中:
>4~5
>3~4
28
4
8
10
1
3
锻件超声波探伤方法简介

锻压
锻造和板料冲压总称为锻压。锻压是对金属坯料施加一外力, 使之产生塑性变形,从而获得具有一定尺寸、形状和内部组 织的毛坯或零件的一种压力加工方法。
锻造能消除金属铸锭中的一些铸造缺陷,使其内部零件和工具 部件,如车床主轴、高速齿轮、曲轴、连杆、锻模、和刀杆 等大都采用锻造制坯。
原材料的缺陷造成的锻件缺陷通常有:
1.表面裂纹:
表面裂纹多发生在轧制棒材和锻制棒材上,一般呈直线 形状,和轧制或锻造的主变形方向一致。造成这种缺陷的原 因很多,例如钢锭内的皮下气泡在轧制时一面沿变形方向伸 长,一面暴露到表面上和向内部深处发展。又如在轧制时, 坯料的表面如被划伤,冷却时将造成应力集中,从而可能沿 划痕开裂等等。这种裂纹若在锻造前不去掉,锻造时便可能 扩展引起 锻件裂纹。
5.亮线(亮区) 亮线是在纵向断口上呈现结晶发亮的有反 射能力的细条线,多数贯穿整个断口,大 多数产生在轴心部分。 亮线主要是由于合金偏析造成的。
轻微的亮线对力学性能影响不大,严重的 亮线将明显降低材料的塑性和韧性。
重量比有一个高的比率。这些元件通常被用在飞机结构中。
锻件的优点有可伸展的长度、可收缩的横截面;可收
缩的长度、可伸展的横截面;可改变的长度、可改变的横
截面。锻件的种类有:自由锻造/手锻、热模锻/精密锻造、
顶锻、滚锻和模锻。
飞机锻件
按重量计算,飞机上有85%左右的的构件是锻件。飞 机发动机的涡轮盘、后轴颈(空心轴)、叶片、机翼的翼 梁, 机身的肋筋板、轮支架、起落架的内外筒体等都是涉 及飞机安全的重要锻件。飞机锻件多用高强度耐磨、耐蚀 的铝合金、钛合金、镍基合金等贵重材料制造。为了节约 材料和节约能源,飞机用锻件大都采用模锻或多向模锻压 力机来生产。 汽车锻按重量计算,汽车上有71.9%的锻件。 一般的汽车由车身、车箱、发动机、前桥、后桥、车架、 变速箱、传动轴、转向系统等15个部件构成汽车锻件的特 点是外形复杂、重量轻、工况条件差、安全度要求高。如 汽车发动机所使用的曲轴、连杆、凸轮轴、前桥所需的前 梁、转向节、后桥使用的半轴、半轴套管、桥箱内的传动 齿轮等等,无一不是有关汽车安全运行的保安关键锻件。
SEP 1921-1984 中文版 锻件和锻材的超声检验
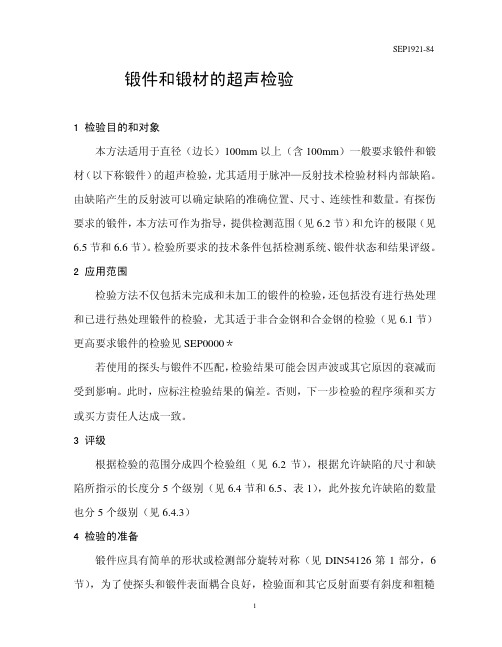
锻件和锻材的超声检验1检验目的和对象本方法适用于直径(边长)100mm以上(含100mm)一般要求锻件和锻材(以下称锻件)的超声检验,尤其适用于脉冲—反射技术检验材料内部缺陷。
由缺陷产生的反射波可以确定缺陷的准确位置、尺寸、连续性和数量。
有探伤要求的锻件,本方法可作为指导,提供检测范围(见6.2节)和允许的极限(见6.5节和6.6节)。
检验所要求的技术条件包括检测系统、锻件状态和结果评级。
2应用范围检验方法不仅包括未完成和未加工的锻件的检验,还包括没有进行热处理和已进行热处理锻件的检验,尤其适于非合金钢和合金钢的检验(见6.1节)更高要求锻件的检验见SEP0000*若使用的探头与锻件不匹配,检验结果可能会因声波或其它原因的衰减而受到影响。
此时,应标注检验结果的偏差。
否则,下一步检验的程序须和买方或买方责任人达成一致。
3评级根据检验的范围分成四个检验组(见6.2节),根据允许缺陷的尺寸和缺陷所指示的长度分5个级别(见6.4节和6.5、表1),此外按允许缺陷的数量也分5个级别(见6.4.3)4检验的准备锻件应具有简单的形状或检测部分旋转对称(见DIN54126第1部分,6节),为了使探头和锻件表面耦合良好,检验面和其它反射面要有斜度和粗糙SEP1921-84度的要求。
对于无氧化铁皮光滑面的检验,只要选择合适的耦合剂,就可以取得良好的检验效果,若表面粗糙度Rq≤20,根据DIN4762的要求应对材料表面进行加工。
若钢材没经过热处理,而锻件声能的衰减仍在允许的偏差极限(或注明极限)内(只要钢适于热处理),为减少声能损失而进行热处理是必要的。
为了检验缺陷所要求的尺寸等级,通过加工和热处理来达到适于检验的结构和表面状态也是必要的。
(表1)5检测系统:5.1检测设备根据脉冲回声技术和回波高度测量关系,带dB幅值控制的校准,超声检测装置应在2dB误差范围内工作。
若在使用的灵敏范围内,则上必显示闸门和饱和度。
检验要求的范围必须调整到与检测装置一致,水平线性应在2%以内。
常用超声波探伤标准要求

常用超声波探伤标准要求
•不允许有当量直径》2mm 的密集缺陷。
(密集型缺陷信号是指在边长 50mm 立方 体内,数量不少于5个,当量直径不小于 2mm 的缺陷信号) • > 2mm 当量单个缺陷在合格证书中注明。
•当量直径2mm 以下的单个分散缺陷信号不计,但杂波高度应低于当量直径 2mm 幅度的50%
•单个分散的缺陷定义为: 相邻两缺陷之间的距离大于其中较大缺陷当量直径 10
倍的缺陷。
•单个分散的缺陷应符合下表规定
•轴身部位离中心孔表面 30mm 以内和外圆槽深加
1.6m m 的密集型缺陷。
允许有当量直径 3mm 以下的单个分散缺陷存在。
•不允许有游动缺陷信号和条状缺陷信号。
标准名称 标准号 承压设备无损检测第 3 JB/T4730.3-
•记录当量直径超过0 4mm 单个缺陷 部分:超声检测 2005 •记录密集型缺陷:饼性锻件,
当量直径》0 4mm 其它锻件,当量直径》0 3mm
钢锻件
单个缺陷的质量分级
mm
等级
密集区缺陷占检测总面积的百分比
I
V
钢锻件超声检测方法 0 > 0~5
> 5~10
>10~20
V > 20
体和主轴锻件技术条件 3
•其他部位不允许当量直径 >3mm 的缺陷
锻件和锻材的超声检测 25MW 以下汽轮机转子 25-200MW 汽轮 机转子 JB/T1265-9 体和主轴锻件技术条件
3。
铸锻件超声波探伤检测方法PPT课件

ቤተ መጻሕፍቲ ባይዱ
• 白点是因钢中含氢量较高时由锻造过程中 残余应力热加工后的相变应力和热应力等 原因产生,是一种细微的氢裂纹,在白点 纵向断口上呈银白色的园点或椭圆形斑点, 故称白点。
• 热处理缺陷:裂纹。由热处理工艺参数 不良引起。
6
• 二、探伤方法概述 • 轴类锻件探伤
①纵波(直探头)可在轴的园周方向和轴端部探 测。
第六章 锻件与铸件超声波探伤
• 第一节 锻件超声波探伤 • 一、锻件加工及常见缺陷: • 加工:由热态钢锭经锻压而成。 • 为改善锻件组织性能,锻后要进行正火,
退火或调质等热处理。 • 缺陷:铸造缺陷:缩孔残余、疏松、夹杂、
裂纹等。
1
整体概况
概况一
点击此处输入 相关文本内容
01
概况二
点击此处输入 相关文本内容
20
• Δ也可用二次底波B1和B2调。工件只有一 个厚度,如某饼型锻件厚300mm,直径很 大,可利用始波T和B1调(但不太准)因T 对零,B1对某刻度,如8格,此时忽略了探 头中引起混响和保护膜引起的延迟,严格 说调好后始波不在零位,而是略后左移。
21
• 双晶直探头: • 可在JB/T4730-2005双晶直探头标准试块上
3
• 疏松是由钢锭凝固时形成的不致密和孔穴, 锻造时锻压比不够未全熔合造成,主要存 在于钢锭中心及头部。铸造引起裂纹主要 是指锻钢件表面上出现的较浅的龟状表面 缺陷也称龟裂,是由于原材料成份不当, 表面状况不好,加热温度和加热时间不合 适等原因产生。
• 锻造缺陷:折叠、白点、裂纹等。
4
• 锻造裂纹可出现在工件中不同位置,可由缩孔残 余在锻造时扩大产生,表面下气泡锻造产生,柱 状晶粗大引起,轴芯晶间裂纹锻造时引起,非金 属夹杂物引起,锻造加热不当引起,锻造变形不 当引起,经锻温度过低等原因引起。
锻件与铸件超声波探伤详细教程(附实例解析)重点讲义资料
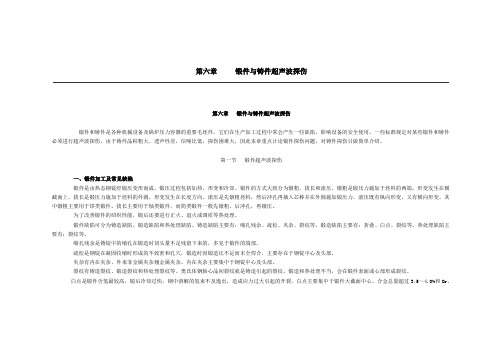
第六章锻件与铸件超声波探伤第六章锻件与铸件超声波探伤锻件和铸件是各种机械设备及锅炉压力容器的重要毛坯件。
它们在生产加工过程中常会产生一些缺陷,影响设备的安全使用。
一些标准规定对某些锻件和铸件必须进行超声波探伤。
由于铸件晶粒粗大、透声性差,信噪比低,探伤困难大,因此本章重点计论锻件探伤问题,对铸件探伤只做简单介绍。
第一节锻件超声波探伤一、锻件加工及常见缺陷锻件是由热态钢锭经锻压变形而成。
锻压过程包括加热、形变和冷却。
锻件的方式大致分为镦粗、拔长和滚压。
镦粗是锻压力施加于坯料的两端,形变发生在横截面上。
拔长是锻压力施加于坯料的外圆,形变发生在长度方向。
滚压是先镦粗坯料,然后冲孔再插入芯棒并在外圆施加锻压力。
滚压既有纵向形变,又有横向形变。
其中镦粗主要用于饼类锻件。
拔长主要用于轴类锻件,而简类锻件一般先镦粗,后冲孔,再镦压。
为了改善锻件的绍织性能,锻后还要进行正火、退火或调质等热处理。
锻件缺陷可分为铸造缺陷、锻造缺陷和热处理缺陷。
铸造缺陷主要有:缩孔残余、疏松、夹杂、裂纹等。
锻造缺陷主要有:折叠、白点、裂纹等。
热处理缺陷主要有:裂纹等。
缩孔残余是铸锭中的缩孔在锻造时切头量不足残留下来的,多见于锻件的端部。
疏松是钢锭在凝固收缩时形成的不致密和孔穴,锻造时因锻造比不足而末全焊合,主要存在于钢锭中心及头部。
夹杂有内在夹杂、外来菲金属夹杂栩金属夹杂。
内在夹杂主要集中于钢锭中心及头部。
裂纹有铸造裂纹、锻造裂纹和热处理裂纹等。
奥氏体钢轴心晶间裂纹就是铸造引起的裂纹。
锻造和热处理不当,会在锻件表面或心部形成裂纹。
白点是锻件含氢最较高,锻后冷却过快,钢中溶解的氢来不及逸出,造成应力过大引起的开裂,白点主要集中于锻件大截面中心。
合金总量超过3.5~4.0%和Cr、Ni、Mn的合金钢大型锻件容易产生白点。
白点在钢中总是成群出现。
二、探伤方法概述按探伤时间分类,锻件探伤可分为原材料探伤和制造过程中的探伤,产品检验及在役检验。
锻件超声波探伤方法简介

原材料的缺陷造成的锻件缺陷通常有:
1.表面裂纹:
表面裂纹多发生在轧制棒材和锻制棒材上,一般呈直线 形状,和轧制或锻造的主变形方向一致。造成这种缺陷的原 因很多,例如钢锭内的皮下气泡在轧制时一面沿变形方向伸 长,一面暴露到表面上和向内部深处发展。又如在轧制时, 坯料的表面如被划伤,冷却时将造成应力集中,从而可能沿 划痕开裂等等。这种裂纹若在锻造前不去掉,锻造时便可能 扩展引起 锻件裂纹。
一、锻件加工及常见缺陷
锻造用的原材料为铸锭、轧材、挤材及锻坯。而轧
材、挤材及锻坯分别是铸锭经轧制、挤压及锻造加 工成的半成品。一般情况下,铸锭的内部缺陷或表 面缺陷的出现有时是不可避免的。例如,内部的成 分与组织偏析等。原材料存在的各种缺陷,不仅会 影响锻件的成形,而且将影响锻件的最终质量。 根据不完全的统计,在航空工业系统中,导致航空 锻件报废的诸多原因中,由于原材料固有缺陷引起 的约占一半左右。因此,千万不可忽视原材料的质 量控制工作。
近场区
干涉:频率相同的两列波叠加,使某些区域的振动加强,某
些区域的振动减弱,而且振动加强的区域和振动减弱的区域 相互隔开。这种现象叫做波的干涉。
近场区:波源附近由于波的干涉而出现一系列声压极大极小
值的区域,称为超声波的近场区。 近场区探伤定量是不利的,处于声压极小值处的较大缺陷回 波可能较低,而处于声压极大值处的较小缺陷回波可能较高, 这样就容易引起误判,甚至漏检,因此应尽可能避免在近场 区探伤定量。
轴类锻件的锻造工艺主要以拔长为主,因而
大部分缺陷的取向与轴线平行,此类缺陷的 探测以纵波直探头从径向探测效果最佳,考 虑到会有其他的分布及取向,因此轴类锻件 探伤,还应辅以直探头轴向和斜探头周向探 测及轴向探测。
常用超声波探伤标准要求[参考资料]
![常用超声波探伤标准要求[参考资料]](https://img.taocdn.com/s3/m/d0e40316af45b307e87197c1.png)
●≥2mm当量单个缺陷在合格证书中注明。
25-200MW汽轮机转子体和主轴锻件技术条件
JB/T1265-93
●当量直径2mm以下的单个分散缺陷信号不计,但杂波高度应低于当量直径2mm幅度的50%。
冶金设备制造通用技术条件(锻钢件超声波探伤方法)
YB/T036.10-1992
●密集缺陷:在钢中距离50mm的范围内,有5个以上大于或等于探伤灵敏度基准的缺陷波,称密集缺陷。
●条状缺陷:当缺陷反射波幅大于或等于探伤灵敏度基准波幅,长度大于或等于30mm的连续性缺陷,称条状缺陷。
标准号
要求
模锻锤和大型机械锻压机用模块技术条件
GB11880-89
●允许存在个别的、分散的、不大于当量直径¢2mm的冶金缺陷。
●在100cm2的面积内,当量直径¢2~¢4 mm的冶金缺陷不超过3个,其中¢3~¢4 mm的冶金缺陷只允许有1个。
●允许有2-4个小于当量直径¢2mm的冶金缺陷的密集区,但每区不得超过10cm3,每区之间距不得小于150mm。
●距中心孔表面75mm以外部位,允许有3个小于当量直径1.6mm的密集缺陷区,但密集区在任何方向的尺寸均应不大于20mm,并且任何两缺陷区间距离应不小于120mm。
●不允许有游动缺陷信号和条状缺陷信号。
50MW以下汽轮发电机转子锻件技术条件
JB/T7026-93
●小于当量直径2mm的缺陷不计。
●不允许有当量直径≥2mm的密集型缺陷密集型缺陷信号,连续性缺陷信号,及游动信号。
●允许有当量直径2~5mm分散的单个缺陷存在,但相邻两个缺陷的距离不小于其较大缺陷直径的5倍,总数量不得超过56个。
- 1、下载文档前请自行甄别文档内容的完整性,平台不提供额外的编辑、内容补充、找答案等附加服务。
- 2、"仅部分预览"的文档,不可在线预览部分如存在完整性等问题,可反馈申请退款(可完整预览的文档不适用该条件!)。
- 3、如文档侵犯您的权益,请联系客服反馈,我们会尽快为您处理(人工客服工作时间:9:00-18:30)。
SEP1921-84锻件和锻材的超声检验
1检验目的和对象
本方法适用于直径(边长)100mm以上(含100mm)一般要求锻件和锻材(以下称锻件)的超声检验,尤其适用于脉冲—反射技术检验材料内部缺陷。
由缺陷产生的反射波可以确定缺陷的准确位置、尺寸、连续性和数量。
有探伤要求的锻件,本方法可作为指导,提供检测范围(见6.2节)和允许的极限(见6.5节和6.6节)。
检验所要求的技术条件包括检测系统、锻件状态和结果评级。
2应用范围
检验方法上仅包括未完成和未加工的锻件的检验,还包括没有进行热处理和已进行热处理锻件的检验,尤其适于非合金钢和合金钢的检验(见6.1节)更高要求锻件的检验见SEP0000*
若使用的探头与锻件上匹配,检验结果可能会因声波或其它原因的衰减而受到影响。
此时,应标注检验结果的偏差。
否则,下一步检验的程序须和买方或买方责任人达成一致。
3评级
根据检验的范围分成四个检验组(见6.2节),根据允许缺陷的尺寸和缺陷所指示的长度分5个级别(见6.4节和6.5、表1),此外按允许缺陷的数量也分5个级别(见6.4.3)
4检验的准备
锻件应具有简单的形状或检测部分旋转对称(见DIN54126第1部分,6节),为了使探头和锻件表面耦合良好,检验面和其它反射面要有斜度和粗糙
SEP1921-84
度的要求。
对于无氧化铁皮光滑面的检验,只要选择合适的耦合剂,就可以取得良好的检验效果,若表面粗糙度Rq≤20,根据DIN4762的要求应对材料表面进行加工。
若钢材没经过热处理,而锻件声能的衰减仍在允许的偏差极限(或注明极限)内(只要钢适于热处理),为减少声能损失而进行热处理是必要的。
为了检验缺陷所要求的尺寸等级,通过加工和热处理来达到适于检验的结构和表面状态也是必要的。
(表1)
5检测系统:
5.1检测设备
根据脉冲回声技术和回波高度测量关系,带dB幅值控制的校准,超声检测装置应在2dB误差范围内工作。
若在使用的灵敏范围内,则上必显示闸门和饱和度。
检验要求的范围必须调整到与检测装置一致,水平线性应在2%以内。
5.2探头
探头标称频率必须与被检验圆盘反射体、声距离长度、声波衰减一致。
一般探头标称频率在1—4MHz,然而只要符合6.5节注明允许的极限值,也可使用其它频率探头。
检验通常使用直探头,然而为检验近表面缺陷和声波难以到达的环或为使缺陷特殊标定锻件部分扇域具有良好的分辨力,通常用TR探头或者斜探头检验。
为了测出圆盘反射体的当量尺寸,应该了解每类探头A VG曲线的制作方法。
SEP1921-84 5.3控制系统
根据DIN54126第1部分,控制系统、探头的调整应与DIN54120要求一致。
5.4耦合剂
耦合剂(也见DIN54126第1部分5.6节)必须对表面具有良好的浸润性,因此(带添加剂的)水、油和胶水都适宜。
调整装置和随后的检验须用同一种耦合剂。
检验加工完毕的锻件,耦合剂上应造成锻件的锈蚀,若有必要,检验后应清除耦合剂,烘干锻件的检测面。
6检测
6.1检测时间
因锻件的可用性与可检验性,预检验应尽早进行,交付检验的锻件通常在没形成夊杂的形状之前进行,然而由于质量原因或加工状态,热处理后检验也非常必要。
6.2检验范围
根据上同要求,锻件检测范围可分成4个检验组。
没有必要考虑机械加工时去除的区域。
检验组1:
直探头检验,在一个或几个最大50mm宽的母线总长度方向的外表面上进行检验(圆在端面上),一般来说声束应该覆盖锻件的核心区域。
例:
棒:轴向一个检验路径
1-84
端面和表面各一个检验路径
轴向4个检测路径
检验组2
直探头检验,在两个或几个最大50mm宽的母线长度或弧线上进行(端面作圆轨迹)。
声束应该覆盖核心区域和锻件大部分的体积。
棒:轴向上互成90º的两个检验路径
端面或表面200mm间距,
2个或几个检验路径
几个或4个轴向路径
检验组3
直探头在两个互相垂直的方向上扫查,同时可用不同类型的探头尽可能地检测锻件的表面,以发现不同类型的缺陷。
-84例:
棒:轴向上至少一半的弧面;
端面检测双方达成一致
饼:整个端面和最小半个
弧面的圆周
整个外表面和一个端面
检验组4
合同中应规定检验的总体积、检验范围和检验使用的探头类型。
注:特殊的检验要求可参照SEP0000
6.3检验步骤
检验根据DIN54126第二部分来进行,根据检验要求的不同,用探头扫查锻件表面。
检验系统按第一次标定点调整和校验,(水平平行表面)或(旋转对称体)按给定的结构图和选定标称频率要有足够的扫查面,至少应做到:
1)因声波衰减或传播声能损失而制作的A VG曲线
2)通过对比试块反射体的反射来调整灵敏度,消除声波衰减和声能损失的影响。
若信噪比(见6.6节)≤6dB,以下内容供需双方须达成一致:记录平底孔直径尺寸(圆反射体)或以dB值表示超过反射体回声的高度,调整灵敏度的
-84
反射体反射回波波高不小于荧光屏满刻度的20%,若达不到要求检验报告中应予以注明。
观察屏幕,探头扫查速度不超过100mm/s。
自动化探伤,探伤速度和脉冲持续时间要相适应,(表1)所示缺陷的尺寸和长度不应漏掉。
用检验组3和检验组4方法进行检验时不应有表面干扰波,每次扫查,探头应有15%的重复覆盖。
6.4显示
6.4.1点状缺陷
探头从不同的方向扫查点状缺陷,接收回声减少的幅值是一致的。
按表1记录可接受的平底孔直径尺寸.
6.4.2连续缺陷
连续缺陷指至少一个扫查方向上幅值减少与其它方向不一致,缺陷的长度按半波高法测量,根据表1记录最大长度的缺陷,同时考虑探头声场特性。
6.4.3数量
记录的数量指在锻件体内超过规定极限以上的缺陷数量或双方约定的区域。
(见6.5节)表2标注从a到e级每个等级的数量。
合同中注明的缺陷数量级和相关尺寸(不同锻件的体积截面长度和面积)。
6.4.4底面回波
若底面回波下降(下降到限定范围内),用不同频率的探头,从不同表面来检验同一区域。
6.5限定偏差(偏差允许极限)
供需双方可按表1直径等级和表2数量等级的要求在可接受的范围内达成
-84一致,不同要求锻件的各个区域也可以按表1直径等级和表2数量等级在接受的范围内供需双方达成一致。
6.6记录极限
若没有其它要求,记录极限与允许极限是同一概念(见6.5节)此时,数量表示的陈述尤为重要,记录极限与允许极限之比最小为6dB,记录极限的信噪比最小也为6dB(见第2节).
7检验报告
检验报告包括以下内容:
a检验件数量
b检验说明
c检验装置和探头类型
d检验件表面状态
e耦合剂
f检验范围
g记录极限与允许极限
h结论
除双方协议的记录极限外,还应描述缺陷的位置、尺寸、状态和数量,根据合同要求,若有必要画出锻件截面图或展开的草图。
此外,在应用检验组3和检验组4还要说明装置的调整方法、声束指向、声束衰减和补偿,若存在分歧须记录在草纸上。
-84
表1允许极限值的大小分级
可靠性限制
尺寸级别单个缺陷mm长条缺陷mm最大面积mm2 A141080
B10760
C7540
D5330
E3230
表2数量级别(见6.4.3节)
数量级别单个缺陷多个缺陷a3216
b168
c84
d42
e21。