陶瓷缺陷分析
陶瓷烧成缺陷及原因分析

陶瓷烧成缺陷及原因分析(一)变形:产品烧成变形是陶瓷行业最常见、最严重的缺陷,如口径歪扭不圆,几何形状有不规则的改变等。
主要原因是装窑方法不当。
如匣钵柱行不正,匣钵底或垫片不平,使窑车运行发生震动,影响到产品的变形。
另外,产品在烧成中坯体预热与升温快时,温差大易发生变形。
烧成温度过高或保温时间太长也会造成大量的变形缺陷。
使用的匣钵高温强度差、或涂料抹不平时也会造成烧成品的变形。
(二)开裂:开裂指制品上有大小不同的裂纹。
其原因是坯体入窑水分太高(大于2%以上),预热升温和冷却太快,导致制品内外收缩不匀。
有的是坯体在装钵前已受到碰撞有内伤。
坯体厚薄不匀,配件(如壶把、咀等)重量过大或粘结不良也会造成制品开裂。
防止的办法是:(1)入窑坯体水分小于2%,车速适当减少冷却量。
(2)装窑时套装操作谨慎,垫片与坯体配方一致。
配件大小、重量与粘接位置恰当。
有的在粘接泥浆中加入10-15%的釉料,可以使咀、把与主体牢固熔接一体,如此可克服开裂缺陷。
(三)起泡:烧制品起泡有坯泡与釉泡两种。
坯泡分为氧化泡与还原泡两种。
氧化泡指坯泡外面覆盖釉层,断面呈灰黑色,多形成于窑内低温部位。
主要是瓷胎与釉料中的分解物未能充分氧化,烧失物未完全排除所致。
予热升温快,氧化分解阶段时间短、氧化结束时窑内温度过低,上下温度差过大。
在坯釉料中,碳酸盐。
硫酸盐及有机杂质含量较多等都是造成产品起泡的主因。
此外时装车密度不当、入窑水份高等原因亦须注意。
还原泡又称过火泡,断而发黄,多发生于高温近喷火口处的制品。
主要由于坯体内硫酸盐与高价铁还原不足,强还原气氛不足及烧成温度过高造成。
釉泡系沉积炭及分解物在釉熔前未能烧尽挥发,气体被阻于釉面层中形成。
若延长釉熔时间或适当平烧即可解决。
(四)阴黄:制品表面发黄或斑状发黄,有的断面也有发黄现象,多出现在高火位处。
主要原因是升温太快,釉熔融过早,还原气氛不足、而使瓷胎中的fe2o3未能还原成feo。
此外,装钵柱太低,窑顶局部产品温度偏高而还原不足也会形成阴黄缺陷。
陶瓷烧制中的常见缺陷及其预防与解决方法

陶瓷烧制中的常见缺陷及其预防与解决方法陶瓷是一种古老而美丽的工艺品,它具有独特的质感和艺术价值。
然而,在陶瓷烧制的过程中,常常会出现一些缺陷,影响了陶瓷制品的质量和美观。
本文将介绍一些常见的陶瓷烧制缺陷,并探讨预防和解决这些问题的方法。
首先,一个常见的缺陷是烧结不均匀。
在陶瓷烧制过程中,由于材料的不均匀性或者烧制温度的不稳定,往往会导致烧结不均匀的问题。
这样的缺陷会使得陶瓷制品表面出现明显的色差或者质地不均匀的现象。
为了预防这个问题,首先需要选择质量均匀的原材料,并严格控制烧制过程中的温度和时间。
此外,可以采用预烧和再烧的方法,使得陶瓷材料在烧制过程中得到更加均匀的加热和冷却。
其次,裂纹是另一个常见的陶瓷烧制缺陷。
裂纹的产生主要是由于烧制过程中的应力不均匀或者材料内部存在缺陷。
为了预防裂纹的产生,可以在烧制过程中适当增加温度的升降速度,减少烧制过程中的应力积累。
此外,可以通过添加一些助烧剂或者改变烧制的工艺参数,来改善陶瓷材料的烧结性能,减少裂纹的产生。
另外,气泡也是陶瓷烧制中常见的缺陷之一。
气泡的产生主要是由于材料中存在气体或者烧制过程中的气体释放不畅。
为了预防气泡的产生,可以在制备陶瓷材料的过程中,采用适当的工艺控制,减少材料中的气体含量。
此外,在烧制过程中,可以采用适当的烧制工艺,提高烧制温度和时间,使得气体能够充分释放。
最后,变形是陶瓷烧制中一个常见而令人头疼的问题。
变形的产生主要是由于材料的烧结收缩性不均匀或者烧制过程中的温度控制不当。
为了解决这个问题,可以在烧制过程中适当调整温度升降速度,减少烧结过程中的应力积累。
此外,可以选择具有较低烧结收缩性的陶瓷材料,或者采用预烧和再烧的方法,来减少变形的发生。
综上所述,陶瓷烧制中的常见缺陷包括烧结不均匀、裂纹、气泡和变形等。
为了预防和解决这些问题,需要从选材、烧制工艺和温度控制等方面进行调整和改进。
只有通过不断的实践和探索,才能够提高陶瓷制品的质量和艺术价值,使其更好地展示出陶瓷这一古老而美丽的工艺品的魅力。
陶瓷|釉面常见缺陷分析处理

陶瓷|釉面常见缺陷分析处理釉面缺陷是釉面砖生产中最让人头疼的问题,施釉工序容易出现的各种缺陷,并从原料、成型、烧成等车间进行问题分析并提出解决措施,希望对大家有所帮一.缺釉缺釉这种缺陷是由于坯体表面的灰尘、油污在施釉前未擦干净;釉浆比重过大使淋釉操作不易掌握造成棱角处缺釉。
解决这种缺陷必须按工艺卡控制好釉浆的工艺性能以方便施釉操作,施釉前将坯体上的灰尘、油污用海绵擦净。
二、厚度不均匀厚度不均匀施釉后如果釉层薄厚不均,会使产品出现色差,影响外观质量。
淋釉、喷釉要按操作标准操作,机械手施釉要调整好操作程序。
无论是淋釉施釉还是机械手施釉,都需要保证釉层厚度的均匀一致。
三、边角出现龟裂边角出现龟裂当喷釉、浸釉、淋釉操作不当时,很容易在制品内边角处出现堆釉,致使釉层过厚,产生小裂,如不处理、烧成后就会滚釉。
这是因为坯体边缘部分较为致密,边角棱角角度较大造成,可通过减少喷水量,釉浆添加盐水等方法解决!四、釉面不平釉面不平釉面不平时,烧成后的釉面难以平整,影响产品的外观质量。
产生的原因:喷嘴雾化不好;釉浆的干燥速度过快,流动性不好或密度太大,施釉操作不熟练。
解决方法是用整形锉修整喷枪的喷嘴,使其雾化好;调整好釉浆的工艺性能;对施釉工加强技术培训。
五.釉滴釉滴这种缺陷是使用机械甩盘甩釉和喷釉的施釉线上最常出现的缺陷。
这种缺陷是由聚集在施釉箱内壁的釉滴掉落在坯体上而产生的。
釉滴产生的原因:釉箱吸尘装置的吸力不足,使釉雰在釉箱内壁聚集或其他设备运行引起釉箱产生振动等。
解决措施:检查施釉箱是否振动;清理吸尘系统,增大吸尘系统吸力。
六.釉料凝块釉料凝块这种缺陷是使用机械甩盘甩釉和喷釉的施釉线上最常出现的缺陷。
釉料凝块产生的原因与釉滴类似,是由施釉箱内壁釉料凝块落到制品上引起的。
产生的原因:1)吸尘系统吸力过大,当釉料受到过大吸力的影响而撞到釉箱壁上,则容易凝结成硬块;2)釉料配方中使用的塑性料过高,如墙地砖使用的底釉,由于其配料中塑性料含量高,因此,更易产生釉料凝块;3)釉箱振动加速了凝块的脱落。
卫生陶瓷缺陷分析

卫生陶瓷缺陷分析着重对其中几种缺陷产生的原因进行分析讨论。
一、变形1、坯料方面①坯料配方不当。
②注浆用的泥浆搭配不合理。
③泥浆成形性能差。
④少于浆速度过慢、中断供浆,会造成坯体塌陷变形。
2、成形及半成品加工方面①注浆模型过干,擦模方法不当;擦模不均匀;模内湿坯收缩不一致,使坯体局部塌陷或局部过早脱模。
②在注浆过程中,由于泥浆表面起皮,或在封闭模型的的漏浆过程中在空腔内产生了负压,形成湿坯塌陷。
③过早脱模,坯体含水率偏高;修坯、粘接操作不当;坯体偏薄或厚薄不一致等。
④模型整体或局部不符合规定要求,失去对坯体的控制作用。
3、烧成方面①装窑方法欠妥。
②烧成制度尤其是烧成温度不合理,烧成温度过高,或局部温度过高等,引起制品变形。
二、裂纹1、原料与坯料方面①原料杂质多,洗、选料不符合要求,有杂质混入坯料。
②坯料配料不准;低可塑性原料用量不当;泥浆细度不合适,过粗或过细;注浆所用泥浆的温度过高。
③泥浆性能不稳定;电解质加入量不当,泥浆过于粘稠;陈腐时间过短;相对密度不合适。
2、成形与半成品加工方面①擦模过程中,用力不均匀或操作方法不当。
②揭模或湿坯脱模过早、过晚。
③模型结构复杂,模型造型或结构本身影响湿坯在模型内均匀地收缩。
④模型对口缝处溢浆,使坯体在对口缝处开裂。
⑤坯体脱模后,在某一部位的重力作用下,使悬空部位接茬处开裂,或某一部位含水率高,受力不均匀,造成坯体开裂。
⑥脱模湿坯与垫托接触部位不相吻合、垫托上有异物,坯体受外力作用而开裂。
⑦修坯粘接时,刀具不锋利,用力不均匀,坯体含水率过高或过低,室内温度高,室外多风等,造成割口与修坯部位开裂。
粘接坯体不实、不牢;各部件与主休含水率不同,收缩不一致,使坯体在干燥时开裂。
⑧打孔眼操作不变,打孔器具不锋利,造成制品眼孔部位开裂。
⑨坯体的底部、凹沟处、漏浆处存浆,或底部模型过干、过湿而造成制品开裂。
⑩坯体在施釉过程中或在存放、搬运、接触等环节不慎磕碰,造成制品开裂。
陶瓷工艺学(3.6)--陶瓷缺陷最终

荞麦地、荞麦点在陶瓷表面上密密麻麻出现微小的黑褐色或褐色斑点,与芥麦面 的黑点极相似,行业内就给这类瓷器取名“荞麦地”、“荞 麦 点”。荞麦地 在 历 朝历 代瓷器都有出现,陶器更多,行业内把它当作一个“鉴古”参考。有的瓷器烧制出 窑 时就带有芥麦点,有的是后来慢慢形成的。根本原内有三点: 一是胎或釉不干净,带有 杂质,这是出窑带 荞 麦 点的主因;二是因修补多次入窑, 环境和新釉不干净所致,也导致 出 现 密 集 养麦点;三是胎质比较 疏 松、釉层不致密的瓷器,经过长时间在自然环境中沾 上杂质或霉菌,形成黑点,这是有的瓷器原来没有荞麦点,后来变荞麦点的主因。
8
陶瓷缺陷—炸纹
炸纹,鸡爪纹——瓷器的损害之一。 炸纹是指器物的颈、 肩或腹部受撞击,瓷器局部出现放射裂纹,有的像鸡爪纹。
9
陶瓷缺陷—毛口
毛 口 ——器物口部损伤缺陷。几边的种面间断瓷缺陷-毛边
毛 边 ——器物口部损伤缺陷。口边的覆釉因伤全部脱落。
11
陶瓷缺陷-釉泡
5
陶瓷缺陷依然存在
崩 、 口 磕 、 足 磕 、 磕 伤 、 磕 边 ——描 述 器 物 破 损 缺 陷 的常用行话,是指器物口际、底足胎釉,由于撞击而出现 大小不等的缺口伤痕。崩是指有碰伤但尚没有出现裂纹。
6
陶瓷缺陷—缺渣
缺 碴 ——瓷器的损害之一,指器物损坏后缺失碎片。
陶瓷缺陷分析
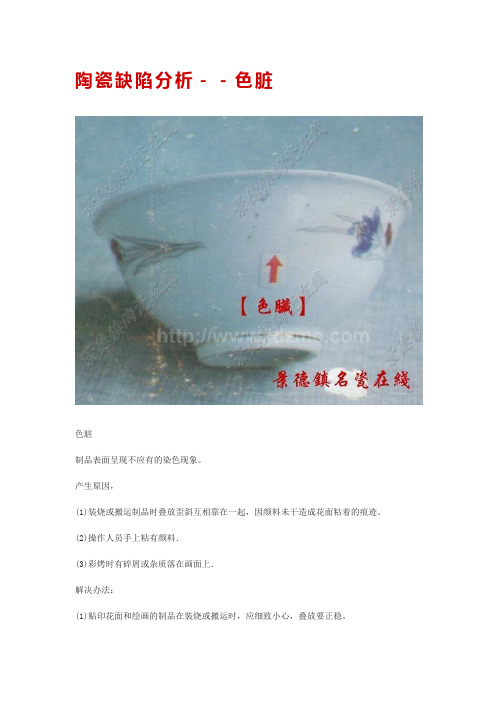
陶瓷缺陷分析--色脏色脏制品表面呈现不应有的染色现象。
产生原因,(1)装烧或搬运制品时叠放歪斜互相靠在一起,因颜料未干造成花面粘着的痕迹。
(2)操作人员手上粘有颜料.(3)彩烤时有碎屑或杂质落在画面上.解决办法:(1)贴印花面和绘画的制品在装烧或搬运时,应细致小心,叠放要正稳。
(2)操作人员工作时手上要保持干净,勿粘颜料。
(3)防止彩烤碎屑、杂质落在画面上。
陶瓷缺陷分析--画面彩色不正画面彩色不正(1)画面缺陷--面面残缺和色泽不正的现象.(2)彩色不正--同一花纹色彩浓淡不匀或由于欠火而产生不光亮的现象。
产生原因:I.釉下装饰(1)分水时,水色、浓淡、厚薄不统一。
(2)施釉时,釉层厚薄不一或画面不干净.(3)花纸上的料没有全部贴坯上,或使用了不符合要求的花纸,以及纸上料色有浓淡不匀的现象。
(4)烧成温度低或烧成气氛不当,使釉面没有充分玻化,花纹色彩不易进出.(5)烧成时由于吸烟或者是欠釉影响产品的呈色效果.2.釉上装饰(1)花纸质量不好或存放时间过长而变质.(2)操作技术不熟练,贴花时未贴妥,而鼓有空气,随着彩烤时温度上升,气泡胀破,导致爆花,或花纸正反面贴错,会造成严重爆花.(3)贴薄膜花纸时,所用酒精配制不当.(4)彩烤时,从色料中或花纸中所产生的气体会对其它产品上的色料发生反应,从而出现呈色不良.(5)所使用的燃料其含硫量过高,使气氛中的二氧化硫与釉料或色料中氧化钙及其它化合物生成硫酸盐,从而使彩色失去光泽。
(6)装烤方式或装载量不当。
(7)彩烤温度过高或过低,使彩色不正。
解决办法:1。
釉下装饰(1)熟悉釉下贴花的操作技术,以及手工工艺,掌握釉下花面的色彩浓淡要求,调好料浆水份.(2)保管好花纸,防止受潮或过干,产生贴花的问题。
(3)掌握釉下贴花产品的施釉厚度,防止过厚或过薄。
(4)制定合理的烧成制度,防止吸烟和烧成气氛不良的现象。
2.釉上装饰(1)妥善保管好花纸,勿使其受潮变质,注意先进厂的先用,保管时间不超过两年,若时间过久将会自然老化变质。
陶瓷生产过程中缺陷及解决

陶瓷生产过程中缺陷及解决色差导致色差的原因也各种各样,原料、坯料加工、成形和烧成等各个环节,控制不好都会产生色差。
两批或两块之间色差1、进厂坯用原料质量波动2、颜料加入量为准确3、球磨细度变化4、色料颗粒大小及级配变化5、白料及色料的比例发生变化6、压制成形7、透明釉施加量发生变化8、烧成制度单块砖上的色差1、无规律的色差:A混料器工作状态不佳,B、白料及色料的颗粒尺寸及颗粒级配相差悬殊2、规律性色差产生这种色差的主要原因是由于推料器安装不当或发生变形等导致它与平台配合不良,喂料时将平台上粉料来回搓细后推入模腔造成。
二、夹层夹层又叫起层、层裂、分层和重皮。
出现夹层现象的根本原因是由于模内粉料中的气体排除不畅造成的。
其影响的因素很多,归结起来为二方面的原因:一、是粉料性能方面的原因,另一个是压机方面的原因1、粉料性能对夹层缺陷的影响①粉料水份对夹层缺陷的影响②陈腐时间对夹层缺陷的影响③粉料颗料级配对夹层缺陷的影响④粉料结块对夹层缺陷的影响⑤粉料表面质量对夹层缺陷的影响2、冲压制度不合理导致夹层缺陷3、模具问题导致夹层缺陷三、变形影响变形的因素很多,如坯体配方、成形、干燥制度等都会导致变形的产生。
对瓷质砖来说,影响最大的还是烧成制度,主要是辊道上下温差设定不合理所致。
烧成对变形的影响1、翘角这种变形的特点是坯体的四角都上翘,长度约为30mm,其余表面是平直或只有少许下凹,这种缺陷发生于窑的中间与两侧。
它是由于烧成后期辊道平面上下温差过大所致。
一般多发生在烧成过程的最后2-5分钟。
解决的办法:①、如果出窑尺寸正确,降低烧成带最后2—3组(箱)辊棒上部的温度(5—10℃或更高,视调试效果确定)并对等升高辊道下面的温度。
②、如果烧成后产品尺寸偏大,则仅升高辊道下面的温度5—10℃度或更多,(视调试效果确定)③、如果烧成后产品尺寸偏小,则仅升高辊道上面的温度5—10℃度或更多,(视调试效果确定)2、角下弯角下弯下好与翘角缺陷相反,它是坯体的四周都下弯,长度约30mm,其余表面是平直或只有少许下凸。
陶瓷烧结内部缺陷

陶瓷烧结内部缺陷
陶瓷烧结内部缺陷是指在陶瓷材料烧结过程中,出现的不完全烧结、气孔、裂纹、包裹物等不良现象。
这些缺陷会降低陶瓷材料的强度、导热性能、气密性等物理性能,严重影响其使用效果。
造成陶瓷烧结内部缺陷的原因有多种,主要包括以下几个方面:
1. 原料质量不过关:原料中含有杂质、颗粒不均匀、颗粒聚集等问题,会导致烧结过程中出现不良缺陷。
2. 烧结温度不适宜:烧结温度过高或过低都容易引起缺陷。
温度过高会导致颗粒烧结不充分,出现气孔和裂纹;温度过低则会导致颗粒无法烧结在一起,形成脆弱的材料。
3. 烧结时间不足:烧结时间不足无法达到完全烧结的效果,会导致内部缺陷。
4. 烧结过程中的气氛不合适:烧结中的气氛对陶瓷材料的质量有很大影响。
若氧气含量过高,会导致氧化反应过剧烈,形成气孔和裂纹;若氢气含量过高,会造成还原反应不充分,使材料质量下降。
为了减少陶瓷烧结内部缺陷的发生,可以采取以下措施:
1. 严格控制原料质量,避免杂质和不均匀颗粒的存在。
2. 控制烧结温度和时间,确保烧结充分而不过度。
3. 优化烧结气氛,使之适应具体陶瓷材料的烧结要求。
4. 加入助烧剂或增稠剂,改善烧结性能,减少缺陷的发生。
5. 增加烧结压力,可以提高瓷体的致密性,减少气孔和裂纹的发生。
- 1、下载文档前请自行甄别文档内容的完整性,平台不提供额外的编辑、内容补充、找答案等附加服务。
- 2、"仅部分预览"的文档,不可在线预览部分如存在完整性等问题,可反馈申请退款(可完整预览的文档不适用该条件!)。
- 3、如文档侵犯您的权益,请联系客服反馈,我们会尽快为您处理(人工客服工作时间:9:00-18:30)。
制品表面呈现不应有的染色现象。
产生原因,
(1)装烧或搬运制品时叠放歪斜互相靠在一起,因颜料未干造成花面粘着的痕迹。
(2)操作人员手上粘有颜料.
(3)彩烤时有碎屑或杂质落在画面上.
解决办法:
(1)贴印花面和绘画的制品在装烧或搬运时,应细致小心,叠放要正稳。
(2)操作人员工作时手上要保持干净,勿粘颜料。
(3)防止彩烤碎屑、杂质落在画面上。
画面彩色不正:
(1)画面缺陷--面面残缺和色泽不正的现象.
(2)彩色不正--同一花纹色彩浓淡不匀或由于欠火而产生不光亮的现象。
产生原因:
I.釉下装饰
(1) 分水时,水色、浓淡、厚薄不统一。
(2) 施釉时,釉层厚薄不一或画面不干净.
(3) 花纸上的料没有全部贴坯上,或使用了不符合要求的花纸,以及纸上料色有浓淡不匀的现象。
(4) 烧成温度低或烧成气氛不当,使釉面没有充分玻化,花纹色彩不易进出.
(5) 烧成时由于吸烟或者是欠釉影响产品的呈色效果.
2.釉上装饰
(1) 花纸质量不好或存放时间过长而变质.
(2) 操作技术不熟练,贴花时未贴妥,而鼓有空气,随着彩烤时温度上升,气泡胀破,导致爆花,或花纸正反面贴错,会造成严重爆花.
(3 )贴薄膜花纸时,所用酒精配制不当.
(4) 彩烤时,从色料中或花纸中所产生的气体会对其它产品上的色料发生反应,从而出现呈色不良.
(5) 所使用的燃料其含硫量过高,使气氛中的二氧化硫与釉料或色料中氧化钙及其它化合物生成硫酸盐,从而使彩色失去光泽。
(6)装烤方式或装载量不当。
(7)彩烤温度过高或过低,使彩色不正。
解决办法:
1。
釉下装饰
(1)熟悉釉下贴花的操作技术,以及手工工艺,掌握釉下花面的色彩浓淡要求,调好料浆水份.
(2)保管好花纸,防止受潮或过干,产生贴花的问题。
(3)掌握釉下贴花产品的施釉厚度,防止过厚或过薄。
(4)制定合理的烧成制度,防止吸烟和烧成气氛不良的现象。
2.釉上装饰
(1)妥善保管好花纸,勿使其受潮变质,注意先进厂的先用,保管时间不超过两年,若时间过久将会自然老化变质。
(2)根据不同季节,气候和薄膜厚薄,配制适宜的酒精溶液.
(3)操作要细心熟练,一次不宜贴粘过多的产品,贴一批及时将气泡、皱纹用纯酒精刮干,
然后再继续进行彩贴。
(4)根据花纸型号,所贴彩件品种,选择适当的空位,适合的彩烤温度,并注意通风。
(5)不使用含硫量过高的燃料。
画线缺陷
用线条装饰的线和边的缺陷:
产生原因:
1.釉下装饰的线条的画线缺陷
(1)坯体变形或是包边形,使打划线条时因坯摆动而易断线.
(2)操作不熟练,手振动或笔画太快、太慢,产生重线或燕尾状线条,虎头蛇尾,浓淡不一.
(3)坯垮边缘沾有不干净的坯粉、灰尘、油污.
(4)氧化钴料液太租,-引起气泡或料刺。
2.釉上装饰的画线缺陷
冲金兰金
(1)金水容器内混有灰尘和水份,以致影响金水的色泽和附着力。
(2)薄膜花纸一般采用聚乙稀膜为基体,它在200℃左右开始熔融,300℃左右即开始分解而放出难闻气体,遇冷又将凝结,由于冷凝后的液体溶化金水能力较强,故一触及金水将造成冲金。
(3)彩烤时产品装得过紧,影响废气的排除,窑内潮湿或燃料含硫量较多,还将造成蒙金、冲金。
(4)产品上有灰尘、油污或粘贴花纸时的余液等,在镶金,画线前未抹掉,则容易造成断金、蒙金和麻点。
(5)金水稀释剂加入量过多或彩烤温度太低造成发兰或紫色.
(6)金水自身浓度不足,画得太薄也引起兰金.
3.流金、炸金
(1)金水稀薄或金笔含金水量过大.
(2)昔通金水用在贴薄膜花纸的产品上,或烤花升温过急。
(3)金水性能不良或金水中溶剂量过大,会引起炸金.
解决办法,
(1)熟练技术撮作,掌握色调性能和浓淡,洗净或擦净将划金线部位的灰尘、油污等杂质。
(2)将青花料中的二氧化二钴色基,改用尖晶石型彩料作为发色基因,这样可大大减少气泡理象.
(3)在镶金或画金时,控制金水中稀释剂的加入量.
(4)彩烤时注童稀装和合理搭配,使产品之间有一定的间距,并在预热带多装排气孔,以利于废气的及时排除,以防冲金、兰金。
(5)严格执行彩烤工艺制度,防止烤花升温过急.
底足粘脏——指底足粘有其它杂质而变色.
产生原因:
(1)制品在运输、加工过程中粘有杂质在底足土,烧成后形成色足.
(2)烤花装烧的托板矽钢片上有铁屑或其它杂质,装烤后制品产生色足。
解决办法:
(1)运输加工工具或台面应打扫干净,防止存有杂质。
(2)矽钢片应涂上一层釉浆,使制品不直接与矽钢片接触。
烤花粘釉
烤花粘釉是烤花过程中制品釉面粘有有色污点及釉面损伤.
产生原因:
主要是制品在装箱、满炉时,制品装得不整齐,或者是由于过份震动,使制品歪斜,互相靠在一起,烧烤花制品上面的颜料粘到另一制品上去,或在700℃一800℃之间,釉面受到损伤。
解决办法
(1)满炉时注意配好筒口,一定要正、直、整齐,不可歪斜.
(2)装箱时注意制品间留有空隙,推箱尽量平稳,减少不必要的震动.
滚迹
在滚压或刀压成形中产生的弧线状痕迹(包括中心凹凸滚头迹、震迹)
产生原因:
(1)泥料含水份偏高或偏低,偏高则容易使坯体成型表面出现滚头迹,如若滚头中心与坯体中心重合,转速比不恰当时还会引起滚头尖,小范围粘泥形成凹陷,偏低则容易产生震迹。
(2)泥料加入量太大,排泥不清或第一轮加泥未加满,二次投泥而使泥料过多,排泥不清,容易出现滚头迹。
(3)重压时间过长、过短,过长则容易出现震迹,过短则因受压次数不够,退刀太快出现滚头迹.
(4)成型时压力不足,或者是滚头脱出模型太突然。
(5)刀片施压时,刀片的工作面受磨损斜度太小.
(6)石膏模与模座不吻合,太紧或太松,或横座的橡胶圈太软.
(7)滚头中心偏移过多造成坯体中心凸起。
(8)滚头中心部份未进行修整易出现凹陷,反之,如修正过度滚头尖唐损和中心长度不够,则易出现凸形。
(9)成型设备质量差,设备零件松动或轴承烧坏也会出现震迹。
解决办法;
(1)严格控制泥条的含水率在工艺指标范围内。
(2)控制泥条的加入量,防止过多过少。
(3)定时检修滚压成型设备.
(4)合理调节滚头夹角和型刀斜度,保证坯体的受压时间.
(5)熟练掌握修模、制模或修制模座的技术工艺要求,一般要修制成倒锥形,模型与模座接触要吻合.
陶瓷缺陷分析--泥渣
泥渣
尚未除净的泥屑、釉屑残留于坯体上造成的缺陷。
产生原因:
(1)压坯时界泥弓或刀片往内装斜,使余泥掉入坯内。
(2)界泥弓或刀片积有泥屎,起刀时掉入坯内。
(3)修磨坯时,泥料或坯粉积在坯体上.
解决办法:
(1)正确安装刀片,避免泥掉入坯内。
(2)经常清理界泥弓架。
(3)捺水时应铲除泥屑、泥渣。
陶瓷缺陷分析--嘴、耳、把接头泥色差
指嘴、耳、把接头泥的色泽与产品本身的色泽不一致。
产生原因:
(1)接头泥配方不当,使用原料不纯。
(2)粘接嘴、耳、涂撩的石灰水过浓,而使接头处呈现不同颜色.
解决办法:
(1)接头泥配方的原料应尽量采用产品本身的泥釉料,以便保持色泽一致。
(2)粘接嘴、耳、把后涂撩的石灰水不宜过浓.。