MRB特采作业管理办法
MRB作业办法

5.1特采处置方式
5.1.1会议决定通过对物料进行特采时。
5.1.2IQC对特采物料贴上特采物料标签,并在标签上注明特采原因,及使用条件。并发出《材
料不良通知单》给供应商分析改善。
5.1.3货仓在发特采物料给给生产时,必须在发料单上写明原因,使用条件。
5.1.4生产在领用特采物料上线时,必须通知工程和品管并依据工程的特采物料加工规范进行
加工。
5.1.5品管IPQC对特采物料上线需作特别追踪,一旦发生不良或异常,即通知停线,以免造成报废。
5.2返工处理方式
5.2.1会议决定通过对物料进行返工时。
5.2.2在第一时间通知供应商过来返工,若供应商未到我司处理,则由我司人员进行挑选,按14元/小时的单价,向供应商扣除返工工时费用。
5.2.3由IQC发出《材料不良通知单》要求供应商分析改善。
1.0目的
界定不良或可疑问题物料的处理方式,以免误用,造成品质问Байду номын сангаас。
2.0范围
适用于物料不良而无法判定处理方式。
3.0定义
MRB:(Material Review Board)物料评审委员会。
4.0权责
4.1成员构成:IQC+PMC+工程+采购
4.1.1IQC:将REJ之物料检验单立即交PMC并立即发出CAR。
4.1.2PMC:
a.填上材料上线日期。
b.依据材料紧急程度,决定是否召开MRB会议。如果是,则通知相关人员开会;如果不是,则将单据退还IQC,由IQC办理退货事宜。
4.1.3工程:做相关之实验,以作为WAIVE(特采)或其它决定依据。
4.1.4参与讨论执行MRB之结论(如向厂商扣款及要求及时补货等)。
MRB管理规定

1.0目的为了清晰MRB的工作流程,明确各相关部门的工作职责,提高MRB的运作质量和效率,确保不合格来料及成品得到快速处理。
2.0范围适用于品质中心IQC对外购/外协加工来料检验不合格的物料,及QA检验不合格的成品。
3.0定义MRB(materials review board):物料审核委员会,MRB组成成员:PMC/QC/采购部/工程部/QA/市场部/装配车间。
4.0 IQC来料不合格MRB流程/职责:作业指导书文件编号:QCIN06002-A.2 文件状态MRB管理规定页码:第 2 页,共 4 页生效日期: 2013-5-20制定:审核: 批准:序号职责流程流程细则相关文件相关记录4.4 MRB 4.4综合MRB意见,对不合格物料的《普通物料检验报告》给出综合判定意见。
4.4.1若不合格物料不急用,则退货处理。
4.4.2若不合格物料急用,则由MRB评估商讨对不合格物料做出挑选、返工、让步接受、退货处理等解决方案。
4.5 采购部供应商品质中心IQC4.5采购部与供应商沟通结果为不合格物料由供应商返工/挑选,则供应商需到亿龙对不合格物料进行挑选/返工处理,完成后良品合格入仓,不良品由IQC出《物料退料报告》退供应商处理。
《物料退料报告》4.6 采购部供应商4.6采购部与供应商沟通结果为由亿龙代替供应商对不合格物料进行挑选/返工。
4.6.1亿龙挑选后,良品投入使用,不良品由IQC出《物料退料报告》退应商处理。
《物料退料报告》4.7 品质中心IQC装配车间4.7亿龙派人挑选/返工不合格物料所产生的费用,由相应供应商支付,由IQC根据装配车间给出的挑选/返工费用,出具相应挑选/返工的《供应商扣款通知单》。
《供应商扣款流程》《供应商扣款通知单》4.8 MRB 4.8由MRB商讨决定不合格物料判定结果为AOD条件/让步接受。
4.8.1若涉及到降价/扣款接受,则由IQC出具相应降价/扣款的《供应商扣款通知单》。
MRB作业指引(基础性通用)-干货

MRB作业指引文件编号:版本:A/0 MRB作业指引制定部门: ****部制订日期: ***年**月**日正文页数: 4页附件页数: 2页文件修订履历1.目的:根据《不合格品处理程序》的定义,针对重大异常/或者涉及到需要过程评估、相关部门评审的不符合事件/或者涉及到PMC紧急需求的事件而成立MRB小组,并定义MRB小组会议方式对相关事件进行及时、有效的处理,使做出合理的、可行的、不影响客户需求的最佳决定。
2.范围:可适用于原材料来料、仓库物料/半成品/成品、客户投诉/反馈事件/售后事件的处理,以及其他整个生产运营过程涉及到需要各相关部门共同评估、评审的事件。
3.定义:3.1 MRB: Material Review Board 材料审查委员会3.2 8D: 8Discipline Working Sheet 8D Report3.3 MRB小组成员组成:由PMC、采购、业务、生产、工程、品质、研发、仓储组成,并由组织者负责召集相关部门进行MRB会议。
4.职责:4.1.IQC: 负责原材料进料抽样检查和品质标准判定,标识隔离不符合品;物料重大异常/或涉及到过程评估、各部门评审的异常事件的提报;4.2.SQE: 负责供应商原材料质量问题的处理推进,反馈成效追踪及必要时对厂商稽查;供应商原材料质量问题导致产线额外工时的确认,并最终确认工时的正确性,并附上工时记录表于MRB报告/或者来料物料异常通知单,进而跟进工时转嫁和妥当处理;组织生产过程因物料质量问题导致的重大异常的MRB会议召集,协助PQE推进受影响产品的应急围堵处理;4.3.IPQC:负责制程中原材料/半成品/成品异常CAR处理推进和标识隔离不符合品,反馈成效追踪;搜集详细信息并提报过程重大异常/或涉及到过程评估、各部门评审的异常事件于组长及以上;4.4.FQC/OQC: 负责成品抽样检查和品质标准判定工作过程异常品的CAR和标识隔离不符合品,成效追踪和反馈,搜集详细信息并提报FQC/OQC处重大异常/或涉及到过程评估、各部门评审的异常事件于组长及以上;4.5.PQE:负责过程中重大异常/或涉及到过程评估、各部门评审的异常事件的处理推进,主导非原材料质量问题导致的MRB会议,并协助因原材料质量问题导致的MRB会议的正常进行和妥善处理;对于异常成品出货部分,协同工程/研发进行成品可靠性、风险评估等工作;督促MRB的有效执行;4.6.CQE:负责客户投诉/反馈事件/售后事件的MRB召开,具体处理根据客诉流程执行(ER-QP-04 客户投诉处理程序);4.7.PE:负责重大异常/或者涉及到需要过程评估、相关部门评审的不符合事件的过程评估(工艺角度进行评估),并协助研发进行产品可靠性评估;对于异常成品出货部分,协同品质/研发进行成品可靠性、风险评估等工作;主导应急围堵措施、纠正和预防措施的制定;当锁定并明确为原材料问题时,转交给到SQE;由SQE推进供应商处理,并反馈供应商8D结果;4.8.研发:负责重大异常/或者涉及到需要过程评估、相关部门评审的不符合事件的产品评估(可靠性、风险性角度进行评估)。
MRB作业管理办法

MRB作业管理办法1.背景介绍MRB指的是Material Review Board,即物料评审委员会。
在制造业中,MRB作为一个重要的管理机构,负责处理各类物料和工件的问题,确保产品质量和工程流程正常进行。
为了更好地规范和管理MRB的工作,制定MRB作业管理办法是非常必要的。
2.目的和范围MRB作业管理办法的目的在于明确MRB的职责和权限,并规范MRB的工作流程,确保评审过程的公正性和有效性。
该管理办法适用于所有涉及物料评审的部门和人员。
3.职责和权限3.1 MRB的职责包括但不限于以下内容:- 对于出现的物料问题或相关突发事件进行评审,并及时做出处理决策;- 确定问题物料的分类和处理方式,如报废、维修、退货等;- 监督和协调相关部门进行问题物料的处置,并跟踪处理结果;- 提出改善建议和措施,减少问题物料的发生。
3.2 MRB的权限包括但不限于以下内容:- 对物料问题进行评审,决定是否需要进行总体评审;- 根据评审结果,决定是否进行进一步的物料测试、分析和验证;- 对于问题物料的处置方式,如报废、维修等,有决策权;- 对评审结果进行审批,并监督相关部门执行。
4.工作流程4.1 问题发现和报告- 员工或部门发现物料问题,立即向MRB提交问题报告;- 问题报告中需要包括物料的具体问题描述、影响范围和后果等信息。
4.2 评审和处理决策- MRB收到问题报告后,立即召开评审会议,对问题进行评审和讨论;- 根据评审结果,MRB决定是否需要进行总体评审,并做出处理决策。
4.3 总体评审- MRB组织相关部门的代表参与总体评审;- 总体评审主要针对重大问题或涉及多个部门的问题进行综合评估。
4.4 处理措施和执行- MRB根据评审结果和总体评审结论,决定问题物料的处置方式;- MRB指定相关部门负责问题物料的处置,并监督处理措施的执行;- 处置方式可能包括报废、维修、退货等。
4.5 改善建议和措施- MRB根据问题的发生和处理情况,提出改善建议和措施;- MRB与相关部门合作,推动改善措施的实施,并定期评估改善效果。
MRB作业办法
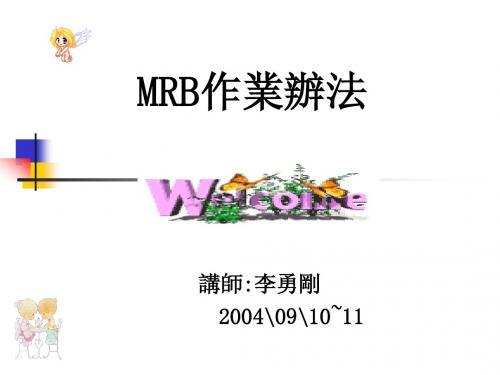
MRB的成員可包括:企划﹑品工﹑制工﹑產工﹑采購, 其中企划負責 MRB 每月召開具體時間的確定﹑各單 位 MRB 成員(包括代理人)的統計及臨時 MRB 會議的 通知.
當 IQC 驗貨發現不良時,由IQC人員依 <<進料品質異常處理 作業規范>> 開立<<原材料不良通知單>>通知采購根據物料 需求狀況及不良狀況判定(直接判定退貨之情況除外)確定是 否進行MRB會議,如果需要則由企划召集相關MRB成員進行 MRB評審決定不合格物料最終處理方式由品保主管核准并記 錄于<<原材料不良通知單>>,如果處理結果為‘’特采‘’, 則由采購單位填寫<<特采申請單>>申請特采, <<特采申請單 >>必需經品保主管審核,廠長批准同意.
MRB作業辦法
講師:李勇剛 2004\09\10~11
目 的
界定 MRB 的權責及要求,以便對外購件 (包括原物料)的不良及時制定有效之處 理對策,以利生產順利進行.
范 圍
IQC 驗貨不良(包括供應商通知不良), 產線外購件不良,倉庫儲存之呆滯外購物 料的處置及后續的矯正措施的監督均適 用之.
權 責
IQC﹕ 判定外購件不良.依據異常之狀況,積極 與供應商聯 絡對品質異常采取矯正及預 防措施,以防止再發生. 企划: 召集相關單位召開 MRB 會議,及時確定物料異常之 處理方案.
品工/制工/產工: 參與物料異常之處理方案.
采購: 配合物料異常處理及供應商矯正及預防措施 實施狀況跟催.
產線發現外購件不良,由品管單位開立<<原材料不良通 知單>>,發現儲存物料不良時由企划開立<<原材料不良 通知單>>通知采購依4.2規定作業. 采購應報告物料之需求狀況,同時﹑品工﹑制工﹑產工 應對物料不良狀況進行判定,并將會簽意見填寫于會簽 單位核定欄.
MRB特采作业管理办法
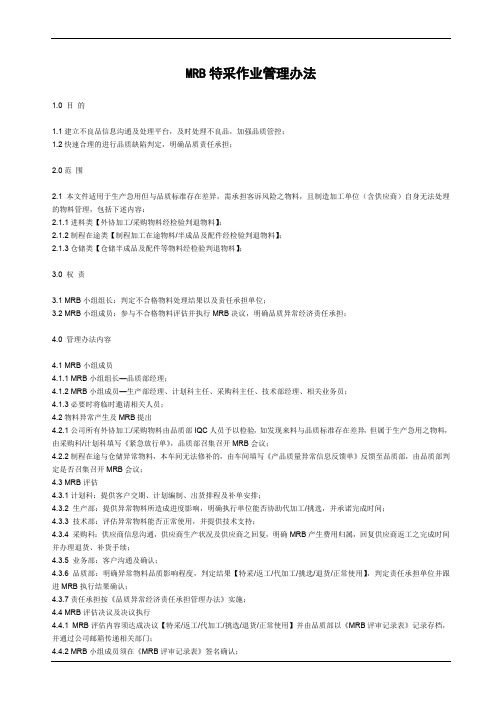
MRB特采作业管理办法1.0 目的1.1建立不良品信息沟通及处理平台,及时处理不良品,加强品质管控;1.2快速合理的进行品质缺陷判定,明确品质责任承担;2.0范围2.1 本文件适用于生产急用但与品质标准存在差异,需承担客诉风险之物料,且制造加工单位(含供应商)自身无法处理的物料管理,包括下述内容:2.1.1进料类【外协加工/采购物料经检验判退物料】;2.1.2制程在途类【制程加工在途物料/半成品及配件经检验判退物料】;2.1.3仓储类【仓储半成品及配件等物料经检验判退物料】;3.0 权责3.1 MRB小组组长:判定不合格物料处理结果以及责任承担单位;3.2 MRB小组成员:参与不合格物料评估并执行MRB决议,明确品质异常经济责任承担;4.0 管理办法内容4.1 MRB小组成员4.1.1 MRB小组组长—品质部经理;4.1.2 MRB小组成员—生产部经理、计划科主任、采购科主任、技术部经理、相关业务员;4.1.3必要时将临时邀请相关人员;4.2物料异常产生及MRB提出4.2.1公司所有外协加工/采购物料由品质部IQC人员予以检验,如发现来料与品质标准存在差异,但属于生产急用之物料,由采购科/计划科填写《紧急放行单》,品质部召集召开MRB会议;4.2.2制程在途与仓储异常物料,本车间无法修补的,由车间填写《产品质量异常信息反馈单》反馈至品质部,由品质部判定是否召集召开MRB会议;4.3 MRB评估4.3.1计划科:提供客户交期、计划编制、出货排程及补单安排;4.3.2 生产部:提供异常物料所造成进度影响,明确执行单位能否协助代加工/挑选,并承诺完成时间;4.3.3 技术部:评估异常物料能否正常使用,并提供技术支持;4.3.4 采购科:供应商信息沟通,供应商生产状况及供应商之回复,明确MRB产生费用归属,回复供应商返工之完成时间并办理退货、补货手续;4.3.5 业务部:客户沟通及确认;4.3.6 品质部:明确异常物料品质影响程度,判定结果【特采/返工/代加工/挑选/退货/正常使用】,判定责任承担单位并跟进MRB执行结果确认;4.3.7责任承担按《品质异常经济责任承担管理办法》实施;4.4 MRB评估决议及决议执行4.4.1 MRB评估内容须达成决议【特采/返工/代加工/挑选/退货/正常使用】并由品质部以《MRB评审记录表》记录存档,并通过公司邮箱传递相关部门;4.4.2 MRB小组成员须在《MRB评审记录表》签名确认;4.4.3 属生产部协助供应商代加工/挑选,则由生产部记录耗损的成本【工时/材料】,并填写《返修耗时/耗料记录表》上报采购科/财务部门;4.4.4 属品质部MRB全检执行挑选或代加工的(包括本厂制程产生的不良),由品质部负责将MRB产生费用及责任进行划分,并填写《返修耗时/耗料记录表》上报采购科/财务部,财务部执行扣款;4.5 MRB执行结果监督及确认4.5.1 品质部对MRB决议执行之结果予以监督,并判定是否符合要求;4.6 MRB全检组成人员4.6.1品质部品检科下属检验人员为主要实施人员;4.6.2 生产执行车间属MRB临时实施人员;4.7 实施4.7.1《MRB作业管理办法》自颁发日起实施;5.0 附件5.1《产品质量异常信息反馈单》;5.2《MRB评审记录表》;5.3《返修耗时/耗料记录表》;5.4《紧急放行单》;5.5《品质异常经济责任承担管理办法》;。
MRB作业规范
5.5.5制造在送验使用筛选或重工材料生产的成品时,须在【送验单】上注明成品上零件料号及不良现象,FQC在收到该批成品时,须对该位置的材料做重点检查。并在报表中进行记录,以利追溯。
6.7供货商重工管制规范9
7.表单9
7.1不良材料处理单9
7.2 REJ标签9
7.3 MRB异常单追踪记录表9
7.4HOLD标签9
7.5进料批退标签9
8.附件9
8.1附件一MRB作业流程9
1.目的
当原物料出现品质问题时,经材料审查会议决议,提供及时有效之解决对策以达到既能配合紧急生产和出货的需求,又能保证预期的品质需求。
5.4.1经MRB最终裁定为特采的不合批材料,由IQC填写【REJ标签】,注明MRB单号、不良现象及处理方式后,贴于该异常批材料的外包装上。
5.4.2如材料为进料时特采,由仓库入良品仓。
5.4.3如材料为上线后特采,由制造直接使用,制造在使用贴有特采标识的材料时,制造须对该批材料做特别管控,以追踪其上线后品质。
2.范围
本公司所有原物料不符合品质要求者均适用本办法。
3.权责
3.1物控单位:客供料、代检料之MRB会议召集,提供物料库存状况及进度需求,及与客户端协调换料(客供料、代检料)。
3.2采购单位:自购料之MRB会议召集,Charge来料损失费用之执行,退料或换货处理,从物料交期角度给出处理意见(自购料部分)。
5.6退货
5.6.1经MRB最终裁定为退货后,由IQC在来料的外包装箱上贴【REJ标签】,并注明退货,由物料室及仓库将批退材料退入不良品仓。
MRB作业指引
三阶文件/MRB作业指引1.目的
对不合格进行判定、统计分析、查找原因以利于持续改善。
2.范围
对进料检验、过程检验、最终检验及客户退货的不合格品的判定均适用。
3. 定义
3.1 MRB: 物料评审小姐
3.2 UAI:特采放行让步接受
4. 内容
4.1判定标准:参照《FQA检查作业指引》及客户的特殊要求。
4.2报废处理流程图
不良品申请报废MRB初判
所属部门确认
MRB判定报废摆放区
可返工,返修或UAI
相应部门
4.3 MRB负责人把每天的报废板分工序放入相应部门的报废暂存箱内,由部门
主管或领班每天确认。
4.4成型前工序判定的报废板必须在“流程卡”上注明准确的报废数量及确认人,
每张“流程卡”包装出货后由MRB负责人核对报废数量是否准确,确认无误后把“流程卡”交生产统计员。
4.5判定可返工的板必须作返工登记,并在规定时间内追回,判定可返修的板退
回相关部门。
4.6判定可以UAI出货的板必须填写《UAI单》,《UAI单》需品质部主管级以
三阶文件/MRB作业指引上人员审批后方可有效。
5. 记录及总结报告
5.1《MRB申请单》必须详细填清生产型号、报废数量、报废原因、产生工序,报废需部门负责人认可签名。
5.2每周对各工序报废统计一次出品质周报,每月对各工序统计一次出品质月
报。
5.3每月(周)召开一次品质月(周)会,对本月(周)出现的主要不良讨论分
析并制定相应对策。
6 记录与表单
6.1《报废申请单》
6.2 《MRB统计表》。
MRB作业管理办法
MRB作业管理办法第一章总则1.1 目的本作业管理办法的目的是为了规范和有效管理MRB(Maintenance Review Board)作业,保障飞机维修和维护工作的高质量和安全性。
1.2 适用范围本作业管理办法适用于所有相关部门和人员,包括但不限于航空公司的维修工程师、飞机制造商的技术支持人员、航空维修公司的维修人员等。
第二章 MRB作业流程2.1 作业申请所有的MRB作业必须按照规定的流程进行申请。
申请人应提供详细的背景信息、问题描述以及所需资源和时间等。
2.2 作业评估和分配作业申请提交后,由MRB主管或指定的负责人对申请进行评估,并根据作业的性质和紧急程度进行优先级划分和分配。
2.3 作业执行作业执行包括问题分析、解决方案的制定与评估、实施和验证等环节。
作业执行人员应按照规定的要求和流程进行操作,并记录相关的数据和信息。
2.4 作业审查作业执行完成后,应进行作业审查。
审查过程中,应对作业的合规性、质量和安全性进行评估,并记录审查结果和意见。
2.5 作业关闭和文档存档作业审查通过后,作业应进行关闭,并将相关文档进行存档。
存档的文档应按照规定的要求进行整理、归类和保存,以备将来参考和审查。
第三章作业管理要求3.1 作业规范所有的MRB作业必须按照相关的技术规范和标准进行操作。
作业执行人员应严格遵守规范,确保操作的准确性和可靠性。
3.2 问题分析与解决方案对于作业中出现的问题,应进行全面细致的分析,并提出合理可行的解决方案。
解决方案应考虑技术、经济和安全等方面的因素,并经过评估和验证确认后方可实施。
3.3 数据管理作业过程中产生的数据和信息应进行有效的管理和记录。
相关人员应确保数据的准确性和完整性,并妥善保存数据以供参考和汇总分析。
3.4 作业报告每个MRB作业应编写相应的作业报告。
作业报告应包括作业的目的、过程、结果和评估等内容,并按照规定的格式进行编写和提交。
第四章质量控制与改进4.1 质量控制MRB作业的质量控制是保障作业质量的重要环节。
MRB管理规范
安徽易特流焊割发展有限公司MRB管理规范文 件 编 号版本/修改状态页 次 第 页 共 页一、目的:为了防止紧急物料的误用,防止不符合预期的物料或成品产生非预期的后果,特制定本规范二、适用范围:公司所有成品、半成品的生产,包括整机生产、部件生产、来料预装处理、PCBA生产等。
本规定适用于IQC对外购物料或外协加工物料及IPQC/QA对物料或产品检验结果为不合格时。
三、术语和定义:MRB(materials review board):物料审核委员会类别 申请部门 参与评审部门 评审人外协、外购原材料不良评审 采购部/生产部采购部 采购部负责人品质部 品质部负责人生产部 生产部负责人验证中心 验证中心负责人半成品、成品不良评审 生产部品质部 品质部负责人生产部 生产部负责人验证中心 验证中心负责人技术部 技术部负责人市场部 市场部负责人机要办 总经理四、职责和权限:1、市场部:对于不符合客户要求的产品,根据各部门给出的建议,从交期等方面评估物料或产品特采可能产生的后果,评估货期、市场状况并同客户沟通,确定客户对不合格物料/产品是否可接收,并给出本部门的意见或建议2、生产部:2.1根据生产排期、物料的库存状况,从生产加工的角度评估物料或产品处置可能造成的影响,对不合格物料或产品做出拒收、让步放行、返工等的建议或意见2.2当不合格物料涉及到需要生产车间加工或拣用时,生产部需参与评审,并提供加工或拣用场所及安排人员,并对挑选出的不合格品进行标识、隔离及后续处理3、采购部:根据与供应商沟通协商的意见及物料的交货周期,从原材料交期等方面评估物料处理对生产和客户交期等的影响,对不合格物料做出拒收、让步接收(降价或扣取供应商加工/挑选使用的费用)等处理的意见或建议4、品质部:根据既往品质状况评估来料不良缺陷对产品装配影响程度,从品质的角度评估物料的处理对生产、检验和客户使用等方面的影响,做出可否投入生产使用的初步判断,并提出拒收、让步接收、返工等的处理建议或意见5、技术部:从设计研发、可靠性等方面考虑对生产、检验、客户使用等方面的影响,并提出处理建议或意见6、验证中心:6.1当不合格物料涉及到需要增加加工工艺或提供拣用夹具时,并给出物料加工工艺或夹具制做方案;6.2当不合格物料涉及到需要验证中心技术支持时,从生产加工工艺、可靠性等角度提出处理建议或意见7.机要办:根据各评审部门综合意见,裁定MRB的最终处置决定五、管理流程:。
- 1、下载文档前请自行甄别文档内容的完整性,平台不提供额外的编辑、内容补充、找答案等附加服务。
- 2、"仅部分预览"的文档,不可在线预览部分如存在完整性等问题,可反馈申请退款(可完整预览的文档不适用该条件!)。
- 3、如文档侵犯您的权益,请联系客服反馈,我们会尽快为您处理(人工客服工作时间:9:00-18:30)。
MRB特采作业管理办法
1.0 目的
1.1建立不良品信息沟通及处理平台,及时处理不良品,加强品质管控;
1.2快速合理的进行品质缺陷判定,明确品质责任承担;
2.0范围
2.1 本文件适用于生产急用但与品质标准存在差异,需承担客诉风险之物料,且制造加工单位(含供应商)自身无法处理
的物料管理,包括下述内容:
2.1.1进料类【外协加工/采购物料经检验判退物料】;
2.1.2制程在途类【制程加工在途物料/半成品及配件经检验判退物料】;
2.1.3仓储类【仓储半成品及配件等物料经检验判退物料】;
3.0 权责
3.1 MRB小组组长:判定不合格物料处理结果以及责任承担单位;
3.2 MRB小组成员:参与不合格物料评估并执行MRB决议,明确品质异常经济责任承担;
4.0 管理办法内容
4.1 MRB小组成员
4.1.1 MRB小组组长—品质部经理;
4.1.2 MRB小组成员—生产部经理、计划科主任、采购科主任、技术部经理、相关业务员;
4.1.3必要时将临时邀请相关人员;
4.2物料异常产生及MRB提出
4.2.1公司所有外协加工/采购物料由品质部IQC人员予以检验,如发现来料与品质标准存在差异,但属于生产急用之物料,由采购科/计划科填写《紧急放行单》,品质部召集召开MRB会议;
4.2.2制程在途与仓储异常物料,本车间无法修补的,由车间填写《产品质量异常信息反馈单》反馈至品质部,由品质部判
定是否召集召开MRB会议;
4.3 MRB评估
4.3.1计划科:提供客户交期、计划编制、出货排程及补单安排;
4.3.2 生产部:提供异常物料所造成进度影响,明确执行单位能否协助代加工/挑选,并承诺完成时间;
4.3.3 技术部:评估异常物料能否正常使用,并提供技术支持;
4.3.4 采购科:供应商信息沟通,供应商生产状况及供应商之回复,明确MRB产生费用归属,回复供应商返工之完成时间并办理退货、补货手续;
4.3.5 业务部:客户沟通及确认;
4.3.6 品质部:明确异常物料品质影响程度,判定结果【特采/返工/代加工/挑选/退货/正常使用】,判定责任承担单位并跟进MRB执行结果确认;
4.3.7责任承担按《品质异常经济责任承担管理办法》实施;
4.4 MRB评估决议及决议执行
4.4.1 MRB评估内容须达成决议【特采/返工/代加工/挑选/退货/正常使用】并由品质部以《MRB评审记录表》记录存档,并通过公司邮箱传递相关部门;
4.4.2 MRB小组成员须在《MRB评审记录表》签名确认;
4.4.3 属生产部协助供应商代加工/挑选,则由生产部记录耗损的成本【工时/材料】,并填写《返修耗时/耗料记录表》上报采购科/财务部门;
4.4.4 属品质部MRB全检执行挑选或代加工的(包括本厂制程产生的不良),由品质部负责将MRB产生费用及责任进行划分,并填写《返修耗时/耗料记录表》上报采购科/财务部,财务部执行扣款;
4.5 MRB执行结果监督及确认
4.5.1 品质部对MRB决议执行之结果予以监督,并判定是否符合要求;
4.6 MRB全检组成人员
4.6.1品质部品检科下属检验人员为主要实施人员;
4.6.2 生产执行车间属MRB临时实施人员;
4.7 实施
4.7.1《MRB作业管理办法》自颁发日起实施;
5.0 附件
5.1《产品质量异常信息反馈单》;
5.2《MRB评审记录表》;
5.3《返修耗时/耗料记录表》;
5.4《紧急放行单》;
5.5《品质异常经济责任承担管理办法》;。