硅橡胶配方以硫化工艺
硅橡胶工艺流程
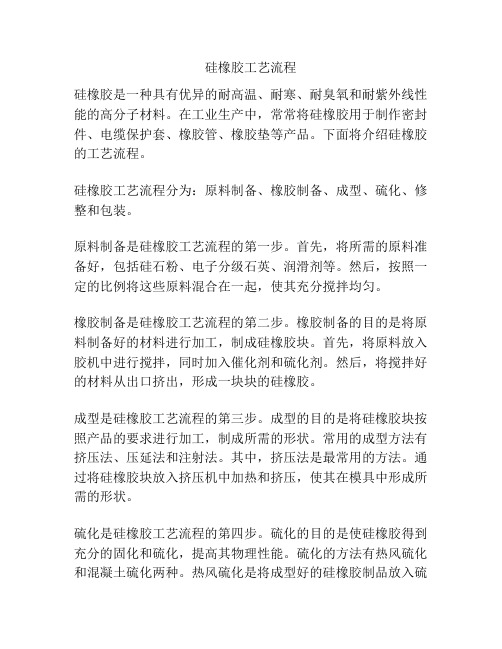
硅橡胶工艺流程硅橡胶是一种具有优异的耐高温、耐寒、耐臭氧和耐紫外线性能的高分子材料。
在工业生产中,常常将硅橡胶用于制作密封件、电缆保护套、橡胶管、橡胶垫等产品。
下面将介绍硅橡胶的工艺流程。
硅橡胶工艺流程分为:原料制备、橡胶制备、成型、硫化、修整和包装。
原料制备是硅橡胶工艺流程的第一步。
首先,将所需的原料准备好,包括硅石粉、电子分级石英、润滑剂等。
然后,按照一定的比例将这些原料混合在一起,使其充分搅拌均匀。
橡胶制备是硅橡胶工艺流程的第二步。
橡胶制备的目的是将原料制备好的材料进行加工,制成硅橡胶块。
首先,将原料放入胶机中进行搅拌,同时加入催化剂和硫化剂。
然后,将搅拌好的材料从出口挤出,形成一块块的硅橡胶。
成型是硅橡胶工艺流程的第三步。
成型的目的是将硅橡胶块按照产品的要求进行加工,制成所需的形状。
常用的成型方法有挤压法、压延法和注射法。
其中,挤压法是最常用的方法。
通过将硅橡胶块放入挤压机中加热和挤压,使其在模具中形成所需的形状。
硫化是硅橡胶工艺流程的第四步。
硫化的目的是使硅橡胶得到充分的固化和硫化,提高其物理性能。
硫化的方法有热风硫化和混凝土硫化两种。
热风硫化是将成型好的硅橡胶制品放入硫化炉中进行加热硫化。
混凝土硫化是将硅橡胶制品放入硫化罐中,然后在高压和高温条件下进行硫化。
修整是硅橡胶工艺流程的第五步。
修整的目的是将硫化好的硅橡胶制品进行修整和整形,使其达到产品的使用要求。
常用的修整方法有切割、磨光和清洗等。
通过这些方法,将硅橡胶制品进行修整和整形,使其外观平整、光滑。
包装是硅橡胶工艺流程的最后一步。
包装的目的是对修整好的硅橡胶制品进行包装、标识和运输。
常用的包装方法有装箱、拆装和贴标等。
通过这些方法,将硅橡胶制品进行包装,使其达到出厂标准。
以上是硅橡胶的工艺流程。
通过原料制备、橡胶制备、成型、硫化、修整和包装等步骤,能够将硅橡胶加工成所需的产品。
硅橡胶因其优异的性能,在各个行业中都有广泛的应用。
硅胶热硫化粘接工艺

硅胶热硫化粘接工艺
硅胶热硫化粘接是一种常见的粘接工艺,通常用于连接硅橡胶等材料。
下面是硅胶热硫化粘接的基本工艺流程:
1.材料准备:准备需要粘接的硅胶材料和相应的硅胶粘接剂。
确保表面清洁,并根据需要进行必要的处理,如打磨、去脏、去油等。
2.涂胶:将硅胶粘接剂均匀涂抹在需要粘接的表面上。
使用刷子、滚筒或喷枪等工具,确保涂层均匀且覆盖到需要粘接的整个表面。
3.预处理:根据硅胶粘接剂的要求,可能需要在涂胶后进行预处理步骤,如等待一定时间使其干燥或部分固化。
4.加热:将已涂抹粘接剂的硅胶部件置于加热设备中进行加热。
加热的温度和时间根据粘接剂的要求而定,一般处于硅胶的热硫化温度范围内。
5.压接:在加热过程中,将需要粘接的硅胶部件压合在一起,确保粘接剂在高温下充分润湿并与硅胶材料结合。
使用适当的压力,确保接触良好并消除气泡。
6.冷却:在压接后,让硅胶部件自然冷却至室温。
在此过程中,粘接剂会继续硫化,形成牢固的连接。
7.后处理:根据需要,可以对粘接部位进行修整和后处理,如去除多余的粘接剂、表面处理等。
需要注意的是,每种硅胶粘接剂的具体工艺参数可能会有所不
同,因此在操作前应该详细阅读粘接剂的技术说明书,并按照其要求进行操作。
此外,安全操作也是十分重要的,特别是在涉及加热和化学品使用时应采取适当的防护措施。
硅橡胶的成分
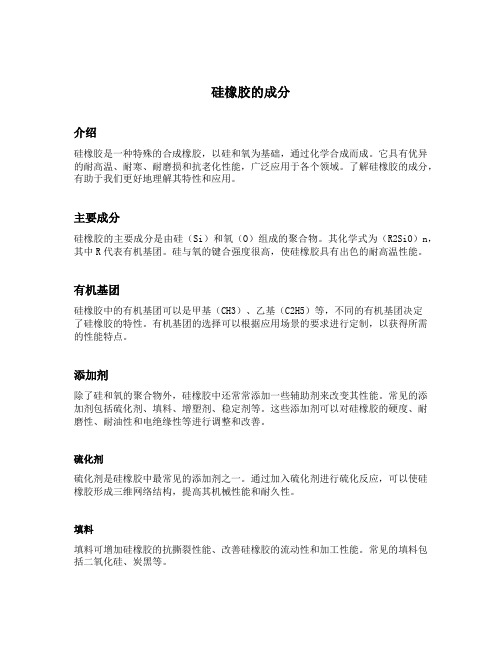
硅橡胶的成分介绍硅橡胶是一种特殊的合成橡胶,以硅和氧为基础,通过化学合成而成。
它具有优异的耐高温、耐寒、耐磨损和抗老化性能,广泛应用于各个领域。
了解硅橡胶的成分,有助于我们更好地理解其特性和应用。
主要成分硅橡胶的主要成分是由硅(Si)和氧(O)组成的聚合物。
其化学式为(R2SiO)n,其中R代表有机基团。
硅与氧的键合强度很高,使硅橡胶具有出色的耐高温性能。
有机基团硅橡胶中的有机基团可以是甲基(CH3)、乙基(C2H5)等,不同的有机基团决定了硅橡胶的特性。
有机基团的选择可以根据应用场景的要求进行定制,以获得所需的性能特点。
添加剂除了硅和氧的聚合物外,硅橡胶中还常常添加一些辅助剂来改变其性能。
常见的添加剂包括硫化剂、填料、增塑剂、稳定剂等。
这些添加剂可以对硅橡胶的硬度、耐磨性、耐油性和电绝缘性等进行调整和改善。
硫化剂硫化剂是硅橡胶中最常见的添加剂之一。
通过加入硫化剂进行硫化反应,可以使硅橡胶形成三维网络结构,提高其机械性能和耐久性。
填料填料可增加硅橡胶的抗撕裂性能、改善硅橡胶的流动性和加工性能。
常见的填料包括二氧化硅、炭黑等。
增塑剂可以使硅橡胶变得更加柔软和可塑,提高其可加工性。
稳定剂稳定剂可以抑制硅橡胶在加工和使用过程中的老化和劣化,延长硅橡胶的寿命。
加工方法硅橡胶的成分确定后,需要进行相应的加工方法以获得所需的形状和性能。
1.混炼:将硅橡胶和各种添加剂进行混合,通常使用开炼机进行混炼,以确保添加剂均匀分散。
2.成型:混炼后的硅橡胶将被送入成型机中,通过挤出、压延、注塑等方式,制成所需形状的硅橡胶制品。
3.硫化:成型后的硅橡胶制品需经过硫化反应,通常在高温下进行,以形成硬硫化层,提高其耐热性和耐寒性。
应用领域硅橡胶由于其独特的性能,被广泛应用于各个领域。
汽车行业硅橡胶在汽车行业中被用于制造密封件、隔音件、悬挂部件等。
其耐高温和耐磨性能使得硅橡胶可以在各种恶劣的工作环境中长期稳定运行。
医疗器械硅橡胶是许多医疗器械的关键组成部分,如医用导管、人工心脏瓣膜等。
硅橡胶种类、配方、生产工艺及用途

硅橡胶种类、配方、生产工艺及用途(共8页)--本页仅作为文档封面,使用时请直接删除即可----内页可以根据需求调整合适字体及大小--硅橡胶种类、配方、生产工艺及用途摘要:硅橡胶是一种兼具无机和有机性质的高分子弹性材料,其分子主链由硅原子和氧原子交替组成(—Si—O—Si—),侧链是与硅原子相连接的碳氢或取代碳氢有机基团,这种基团可以是甲基、不饱和乙烯基(摩尔分数一般不超过01005)或其它有机基团,这种低不饱和度的分子结构使硅橡胶具有优良的耐热老化性和耐候老化性,耐紫外线和臭氧侵蚀。
分子链的柔韧性大,分子链之间的相互作用力弱,这些结构特征使硫化胶柔软而富有弹性,但物理性能较差。
关键词:硅橡胶、热硫化型橡胶、工艺流程、特性与功能、应用与发展1引言分类硅橡胶按其硫化机理不同可分为热硫化型、室温硫化型和加成反应型三大类。
这里主要介绍热硫化型橡胶。
特性(1)耐高、低温性在所有橡胶中,硅橡胶的工作温度范围最广阔(-100~350℃)。
例如,经过适当配合的乙烯基硅橡胶或低苯基硅橡胶,经250℃数千小时或300℃数百小时热空气老化后仍能保持弹性;低苯基硅橡胶硫化胶经350℃数十小时热空气老化后仍能保持弹性,它的玻璃化温度为-140℃,其硫化胶在-70~100℃的温度下仍具有弹性。
硅橡胶用于火箭喷管内壁防热涂层时,能耐瞬时数千度的高温。
(2)耐臭氧老化、耐氧老化、耐光老化和耐候老化性能硅橡胶硫化胶在自由状态下置于室外曝晒数年后,性能无显著变化。
(3)电绝缘性能硅橡胶硫化胶的电绝缘性能在受潮、频率变化或温度升高时变化较小,燃烧后生成的二氧化硅仍为绝缘体。
此外,硅橡胶分子结构中碳原子少,而且不用炭黑作填料,因此在电弧放电时不易发生焦烧,在高压场合使用十分可靠。
它的耐电晕性和耐电弧性极好,耐电晕寿命是聚四氟乙烯的1000倍,耐电弧寿命是氟橡胶的20倍。
(4)特殊的表面性能和生理惰性硅橡胶的表面能比大多数有机材料小,具有低吸湿性,长期浸于水中吸水率仅为1%左右,物理性能不下降,防霉性能良好,与许多材料不发生粘合,可起隔离作用。
硅橡胶的制备方法

硅橡胶的制备方法
硅橡胶是一种具有优异性能的材料,广泛应用于多个领域,例如橡胶密封件、橡胶管、橡胶减震器等。
硅橡胶的制备方法主要包括原料的配制、胶料的制备和硫化等步骤。
首先是原料的配制。
硅橡胶的主要原料是二甲基硅胶、硅橡胶增塑剂、硅橡胶填料等。
其中二甲基硅胶是硅橡胶的主要成分,它是由硅氧键和碳氧键构成的有机硅化合物。
硅橡胶增塑剂可以调整硅橡胶的硬度和弹性,常用的增塑剂有醋酸酯类和有机过硫酸酯类。
硅橡胶填料用于增加硅橡胶的粘度和硬度,常用的填料有碳酸钙、硅灰石等。
接下来是胶料的制备。
首先将二甲基硅胶和增塑剂按一定比例加入混合机中搅拌均匀,形成预混料。
然后将预混料加入开炼机中进行混炼,期间逐渐加入填料和其他助剂,同时控制温度和时间,使胶料充分混合,形成均匀粘稠的糊状物质。
最后是硫化。
硫化是硅橡胶制备过程中最重要的一步,通过硫化可以使胶料具有优异的耐热性和耐老化性能。
硅橡胶的硫化可以采用热硫化或者是加热固化剂硫化两种方法。
热硫化是在一定的温度和时间条件下进行,通常在150-200摄氏度的温度下进行热硫化。
加热固化剂硫化是通过在室温下使用加热硫化剂,例如过氧化二苯酮,在胶料中加入一定量的固化剂后进行硬化。
此外,硅橡胶的制备还可以采用溶剂法、胶体法等不同的制备方法。
溶剂法是在
适当溶剂中将原料混合并搅拌均匀,溶剂蒸发后得到硅橡胶。
胶体法是通过固化剂与胶体交联结构反应,形成硅橡胶。
总而言之,硅橡胶的制备方法包括原料的配制、胶料的制备和硫化等步骤。
通过合理控制原料比例和工艺条件,可以获得具有优异性能的硅橡胶材料。
了解硅橡胶制品第一阶段硫化和第二阶段硫化
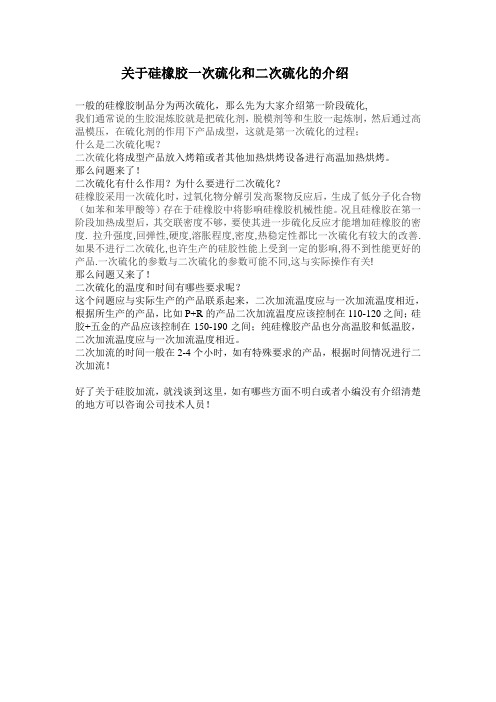
关于硅橡胶一次硫化和二次硫化的介绍
一般的硅橡胶制品分为两次硫化,那么先为大家介绍第一阶段硫化,
我们通常说的生胶混炼胶就是把硫化剂,脱模剂等和生胶一起炼制,然后通过高温模压,在硫化剂的作用下产品成型,这就是第一次硫化的过程;
什么是二次硫化呢?
二次硫化将成型产品放入烤箱或者其他加热烘烤设备进行高温加热烘烤。
那么问题来了!
二次硫化有什么作用?为什么要进行二次硫化?
硅橡胶采用一次硫化时,过氧化物分解引发高聚物反应后,生成了低分子化合物(如苯和苯甲酸等)存在于硅橡胶中将影响硅橡胶机械性能。
况且硅橡胶在第一阶段加热成型后,其交联密度不够,要使其进一步硫化反应才能增加硅橡胶的密度. 拉升强度,回弹性,硬度,溶胀程度,密度,热稳定性都比一次硫化有较大的改善.如果不进行二次硫化,也许生产的硅胶性能上受到一定的影响,得不到性能更好的产品.一次硫化的参数与二次硫化的参数可能不同,这与实际操作有关!
那么问题又来了!
二次硫化的温度和时间有哪些要求呢?
这个问题应与实际生产的产品联系起来,二次加流温度应与一次加流温度相近,根据所生产的产品,比如P+R的产品二次加流温度应该控制在110-120之间;硅胶+五金的产品应该控制在150-190之间;纯硅橡胶产品也分高温胶和低温胶,二次加流温度应与一次加流温度相近。
二次加流的时间一般在2-4个小时,如有特殊要求的产品,根据时间情况进行二次加流!
好了关于硅胶加流,就浅谈到这里,如有哪些方面不明白或者小编没有介绍清楚的地方可以咨询公司技术人员!。
硅胶按键硫化工艺流程
硅胶按键硫化工艺流程
1. 原料准备
- 液态硅橡胶(LSR)
- 硫化剂
- 填料(如玻璃纤维、石英粉等)
- 着色剂(可选)
2. 混合
- 将液态硅橡胶、硫化剂、填料和着色剂(如需)按照特定比例混合均匀。
- 使用真空脱泡机去除混合物中的气泡。
3. 注射成型
- 将混合好的硅橡胶料注入按键模具腔内。
- 采用高精度注射成型机进行注射成型。
4. 硫化
- 将注射成型后的按键在特定温度下进行硫化反应。
- 硫化温度和时间需根据硅橡胶类型和添加剂进行调整。
5. 冷却
- 待硫化反应完成后,将模具冷却至常温。
6. 脱模
- 打开模具,将硫化后的硅胶按键取出。
7. 后处理
- 对按键进行修边、除毛刺等后处理工序。
- 进行外观和尺寸检查,确保按键质量合格。
8. 包装入库
- 将合格的硅胶按键进行包装防护。
- 入库待后续组装使用。
通过以上工艺流程,可以生产出优质的硅胶按键产品,满足各种应用场景的需求。
精确控制每个工艺环节对于获得理想的按键性能至关重要。
单组分室温硫化硅橡胶技术简介
单组份室温硫化硅橡胶技术简介1、项目意义当电力、煤炭、石油等不可再生能源频频告急,能源问题日益成为制约国际社会经济发展的瓶颈时,越来越多的国家开始实行“阳光计划”,开发太阳能资源,寻求经济发展的新动力。
太阳能作为一种可再生的新能源,越来越引起人们的关注。
中国蕴藏着丰富的太阳能资源,太阳能利用前景广阔。
中国光伏发电产业于20世纪70年代起步,经过30多年的努力,已迎来了快速发展的新阶段。
在“光明工程”先导项目和“送电到乡”工程等国家项目及世界光伏市场的拉动下,我国光伏发电产业迅猛发展。
2008年太阳能电池的产量达到了200万千瓦。
2009年中国太阳能电池/模组制造商的产能较2008年倍增,达到8,000MW,电池产量超过4,000MW。
2009年可谓是太阳能产业在中国高速发展的时期,国家的补贴扶持政策陆续推出。
3月,财政部、住房和城乡建设部印发《关于加快推进太阳能光电建筑应用的实施意见》及《太阳能光电建筑应用财政补助资金管理暂行办法》,确定对光电建筑2009年的补助标准为20元/瓦。
7月,财政部、科技部、国家能源局发出《关于实施金太阳示范工程的通知》,提出对光伏并网项目和无电地区离网光伏发电项目分别给予50%及70%的财政补贴。
11月,财政部、科技部、国家能源局下发了《关于做好“金太阳”示范工程实施工作的通知》,要求加快实施“金太阳”示范工程。
随着这些政策的陆续出台,中国光伏产业将进入第二个阶段。
中国科学院党组已正式批准启动实施太阳能行动计划,该计划以2050年前后太阳能作为重要能源为远景目标,并确定了2015年分布式利用、2025年替代利用、2035年规模利用三个阶段目标,太阳能产业在中国市场发展前景广阔。
硅酮密封胶是室温硫化硅橡胶(RTV)的一种,是一种新型的有机硅弹性体。
HT-8258是本公司研究开发的单组份、中性固化、专为光伏组件铝边框和接线盒粘接要求而设计开发的硅酮密封胶。
该产品除了具有普通硅酮密封胶耐候性、耐高低温性、粘结性好的优点外,还具有优异的固化性能和耐黄变性能,阻燃等级达到UL94-HB级。
硅橡胶配方以及硫化工艺
硅橡胶常用硫化剂②乙烯基硅橡胶硫化剂BP膏状物用量(膏状物内含硫化剂BP为50%)。
硅橡胶常用补强剂的用量和性能硅橡胶的着色剂乙烯基硅橡胶和氟硅橡胶基本配方和物理机械性能开炼机混炼双辊开炼机辊筒速比为1.2~1.4:为宜,快辊在后,较高的速比导致较快的混炼,低速比则可使胶片光滑。
辊筒必须通有冷却水,混炼温度宜在40℃以下,以防止焦烧或硫化剂的挥发损失。
混炼时开始辊距较小(1~5mm),然后逐步放大。
加料和操作顺序:生胶(包辊)—→补强填充剂—→结构控制剂—→耐热助剂—→着色剂等—→薄通5次—→下料,烘箱热处理—→返炼—→硫化剂—→薄通—→停放过夜—→返炼—→出片。
胶料也可不经烘箱热处理,在加入耐热助剂后,加入硫化剂再薄通,停放过夜返炼,然后再停放数天返炼出片使用。
混炼时间为20~40分钟(开炼机规格为φ250mm ×620mm)。
如单用沉淀白炭黑或弱补强性填充剂(二氧化钛、氧化锌等)时,胶料中可不必加入结构控制剂。
应缓慢加入填料,以防止填料和生胶所形成的球状体浮在堆积胶的顶上导致分散不均。
如果要加入大量的填料,最好是分两次或三次加入,并在其间划刀,保证良好的分散。
发现橡胶有颗粒化的趋势,可收紧辊距以改进混炼。
落到接料盘上的胶粒应当用刷子清扫并收集起来,立即返回炼胶机的辊筒上,否则所炼胶料中含有胶疙瘩而导致产品外观不良。
增量性填料应当在补强性填料加完之后加入,可采用较宽的辊距。
装胶容量(混炼胶):φ160mm×320mm炼胶机为1~2 kg;φ250mm×620mm炼胶机为 3~5kg。
硅橡胶在加入炼胶机时包慢辊(前辊),混炼时则很快包快辊(后辊),炼胶时必须能两面操作。
由于硅橡胶胶料比较软,混炼时可用普通赋子刀操作,薄通时不能象普通橡胶那样拉下薄片,而采用钢、尼龙或耐磨塑料刮刀刮下。
为便于清理和防止润滑油漏入胶内,应采用活动挡板。
气相白炭黑易飞扬,对人体有害,应采取相应的劳动保护措施。
双组分室温硫化硅橡胶的配制
双组分室温硫化硅橡胶的配制双组分室温硫化硅橡胶是一种特殊的橡胶材料,具有优异的性能和广泛的应用领域。
本文将介绍双组分室温硫化硅橡胶的配制方法及其在工业中的应用。
一、双组分室温硫化硅橡胶的配制方法双组分室温硫化硅橡胶由两个组分组成,分别为基础胶和固化剂。
基础胶一般是硅橡胶乳液,而固化剂则是一种含有硫化剂和交联助剂的液体。
配制双组分室温硫化硅橡胶的步骤如下:1. 首先,将基础胶和固化剂分别搅拌均匀。
基础胶的搅拌可以采用机械搅拌或者手工搅拌的方式,确保基础胶的均匀性。
2. 然后,将固化剂缓慢地加入基础胶中,同时不断地搅拌,直到两者完全混合均匀。
3. 接下来,将配制好的双组分室温硫化硅橡胶倒入密封容器中,并密封保存。
二、双组分室温硫化硅橡胶的应用领域双组分室温硫化硅橡胶具有优异的性能,广泛应用于多个工业领域。
1. 电子电器行业:双组分室温硫化硅橡胶具有良好的绝缘性能和耐高温性能,常用于电子元器件的密封和绝缘保护,如电子线路板、继电器等。
2. 汽车工业:双组分室温硫化硅橡胶具有优异的耐油、耐燃油性能,常用于汽车零部件的密封和防水,如发动机密封、传感器密封等。
3. 医疗器械领域:双组分室温硫化硅橡胶具有生物相容性好、无毒无味的特点,常用于医疗器械的密封和接触部件,如医疗设备密封圈、输液管件等。
4. 建筑工程领域:双组分室温硫化硅橡胶具有优异的耐候性和耐老化性能,常用于建筑工程的密封和防水,如建筑门窗密封条、屋顶防水涂料等。
5. 其他领域:双组分室温硫化硅橡胶还广泛应用于航空航天、船舶制造、食品包装等领域,用于密封、绝缘、防水等用途。
三、双组分室温硫化硅橡胶的优势双组分室温硫化硅橡胶相比于传统的硅橡胶具有以下优势:1. 室温硫化:传统的硅橡胶需要高温硫化才能达到最佳性能,而双组分室温硫化硅橡胶可以在室温下快速硫化,提高生产效率。
2. 使用方便:双组分室温硫化硅橡胶的配制简单,只需将基础胶和固化剂搅拌均匀即可使用,无需额外的加热设备和工艺。
- 1、下载文档前请自行甄别文档内容的完整性,平台不提供额外的编辑、内容补充、找答案等附加服务。
- 2、"仅部分预览"的文档,不可在线预览部分如存在完整性等问题,可反馈申请退款(可完整预览的文档不适用该条件!)。
- 3、如文档侵犯您的权益,请联系客服反馈,我们会尽快为您处理(人工客服工作时间:9:00-18:30)。
硅橡胶常用硫化剂硫化剂结构式简称用量,份硫化温度℃用途过氧化苯甲酰硫化剂BP 4~6①~2②110~135通用型、模压、蒸汽连续硫化、粘合2,4-二氯过氧化苯甲酰硫化剂DCBP4~6①~2②100~120通用型、热空气硫化、蒸汽连续硫化、模压过苯甲酸叔丁酯硫化剂TBPB~135~155通用型、海绵、高温硫化用过氧化二叔丁基硫化剂DTBP~160~180乙烯基专用、模压、厚制品、炭黑胶料过氧化二异丙苯硫化剂DCP~150~160乙烯基专用、模压、厚制品、炭黑胶料、蒸汽硫化、粘合2,5-二甲基地,5-二叔丁基过氧化已烷硫化剂DBPMH(双2,5)~160~170乙烯基专用、模压、厚制品、炭黑胶料②乙烯基硅橡胶硫化剂BP膏状物用量(膏状物内含硫化剂BP为50%)。
硅橡胶常用补强剂的用量和性能类别名称用量,份(重量,以100生胶计)硫化胶性能拉伸强度,MPa (kgf/cm2)扯断伸长率,%补强填充剂气相白炭黑沉淀白炭黑处理白炭黑乙炔炭黑30~6040~7040~8040~60~ (40~90)~ (30~60)~(70~140)~ (40~60)200~600200~400400~800200~350弱补强填充剂硅藻土钛白粉石英粉碳酸钙氧化锌氧化铁50~20050~30050~150~ (30~60)~ (15~35)—~ (30~40)~ (15~35)~ (15~35)75~200300~400—100~300100~300100~300硅橡胶的着色剂名称颜色名称颜色氧化铁(三氧化二铁)铬绿(三氧化二铬)钛白(二氧化钛)红绿白镉黄(二氧化镉)炭黑群青黄黑蓝乙烯基硅橡胶和氟硅橡胶基本配方和物理机械性能配方及性能乙烯基硅橡胶氟硅橡胶通用型通用型高抗撕型通用型乙烯基硅橡胶(110-2)氟硅橡胶沉淀白炭黑2号气相白炭黑4号气相白炭黑八甲骨文基环四硅氧烷处理2号气相白炭黑二苯基硅二醇六甲基环三硅氮烷和八甲基环四硅氧烷混全物100—40~60—————100——45—60——3~6—100———40~50——8~10100————45~60——3100—40~45————4羟基氟硅油三氧化二铁有机过氧化物—3~5~1—3~5~1——~1—3~5~12~33~5~1 老化前物理机械性能拉伸强度,MPa 扯断伸长率,% 硬度(邵尔)撕裂台度,kN/m 脆性温度,℃~150~25045~65—-65~203~35045~65—-65~400~60040~5530~50-65~300~50045~60—-65~150~25040~60—-60 200℃×27h老化后拉伸强度,MPa ——~—~5扯断伸长率,% 硬度(邵尔)————300~50045~60——100~20045~65 250℃×72h老化后拉伸强度,MPa 扯断伸长率,% 硬度(邵尔)~150~25045~65~150~30045~65———~200~40050~60———压缩永久变形(压缩率30%)150℃×24h,% 200℃×24h,%—10~20—20~3030~50——40~6020~30—电性能击穿电压,MV/m 体积电阻Ω·cm18~201014~101520~251015~101620~251015~101620~251015~101612~151012~10156耐油性能2号航空煤油150℃×24h体积膨胀率,% ————15~20 7开炼机混炼双辊开炼机辊筒速比为~:为宜,快辊在后,较高的速比导致较快的混炼,低速比则可使胶片光滑。
辊筒必须通有冷却水,混炼温度宜在40℃以下,以防止焦烧或硫化剂的挥发损失。
混炼时开始辊距较小(1~5mm),然后逐步放大。
加料和操作顺序:生胶(包辊)—→补强填充剂—→结构控制剂—→耐热助剂—→着色剂等—→薄通5次—→下料,烘箱热处理—→返炼—→硫化剂—→薄通—→停放过夜—→返炼—→出片。
胶料也可不经烘箱热处理,在加入耐热助剂后,加入硫化剂再薄通,停放过夜返炼,然后再停放数天返炼出片使用。
混炼时间为20~40分钟(开炼机规格为φ250mm ×620mm)。
如单用沉淀白炭黑或弱补强性填充剂(二氧化钛、氧化锌等)时,胶料中可不必加入结构控制剂。
应缓慢加入填料,以防止填料和生胶所形成的球状体浮在堆积胶的顶上导致分散不均。
如果要加入大量的填料,最好是分两次或三次加入,并在其间划刀,保证良好的分散。
发现橡胶有颗粒化的趋势,可收紧辊距以改进混炼。
落到接料盘上的胶粒应当用刷子清扫并收集起来,立即返回炼胶机的辊筒上,否则所炼胶料中含有胶疙瘩而导致产品外观不良。
增量性填料应当在补强性填料加完之后加入,可采用较宽的辊距。
装胶容量(混炼胶):φ160mm×320mm炼胶机为1~2 kg;φ250mm×620mm炼胶机为 3~5kg。
硅橡胶在加入炼胶机时包慢辊(前辊),混炼时则很快包快辊(后辊),炼胶时必须能两面操作。
由于硅橡胶胶料比较软,混炼时可用普通赋子刀操作,薄通时不能象普通橡胶那样拉下薄片,而采用钢、尼龙或耐磨塑料刮刀刮下。
为便于清理和防止润滑油漏入胶内,应采用活动挡板。
气相白炭黑易飞扬,对人体有害,应采取相应的劳动保护措施。
如在混炼时直接使用粉状过氧化物,必须采取防爆措施,最好使用膏状过氧化物。
如在胶料中混有杂质、硬块等,可将混炼胶再通过滤胶机过滤,过滤时,一般采用80~140目筛网。
2.密炼机混炼采用此法可提高生产效率和改善劳动条件。
试验表明,密闭式混炼胶料的性能与开放式混炼胶料的性能相似。
用试验室2L密炼机的混炼时间为6~16分钟,混炼无特殊困难。
采用φ160mm 开炼机当装料系数为时,混炼也能正常进行。
排料温度与补强填充剂的类型有关:当采用弱补强性填充剂和沉淀白炭黑时,排胶温度在50℃以下;当使用气相白炭黑时,排胶温度为70℃左右。
3.胶料停放和返炼硅橡胶胶料混炼结束后,应经过一段时间的停放(一般以不少于24小时为宜),使各种配合剂(特别是结构控制剂)能与生胶充分起作用。
经停放后,胶料变硬,可塑性降低,使用前必须进行返炼。
返炼采用开炼机,开始时辊距较大(3~5mm),此时胶料较硬,表面是皱纹状,包在前辊(慢辊)上。
随着返炼时间的延长,胶料逐渐变软;慢慢缩小辊距(~),很快胶料即包在后辊(快辊)上。
“待胶料充分柔软,表面光滑平整后,即可下料出片。
返炼不足,胶片表面有皱纹;返炼过度则胶料发粘而导致粘辊。
返炼温度一般控制为室温。
如胶科长期存放(一个月以上)而出现胶料发粘变软,表面产生皱纹等现象时,可再加入5~10份左右的气相白炭黑,以改进胶料工艺性能,并保证硫化胶质量。
(二)压出一般硅橡胶比较柔软,故其压出效果较好,易于操作。
用硅橡胶可以压出各种不同形状和尺寸的制品,其加工设备和工具基本上与普通橡胶相似。
压出机一般是用φ30mm或φ65mm的单螺纹螺杆,长径比为10~12:1效果较好。
压出时尽量保持低温,以不超过40℃为宜,所以机筒和螺杆均须通冷却水。
对质量要求较高的产品可靠近机头部分加装80~140目滤网,以除去胶料中的杂质,改善压出质量。
硅橡胶从口型中出来时会膨胀,膨胀率取决于胶料的流动性能、坯料厚薄及胶料进入境口型时所受的压力。
然而,增加或降低引出速度会改变未硫化压出制品的伸长率,从而使其尺寸稍加改变。
根据经验,胶管比其口型尺寸膨胀约3%,而很软的胶料膨胀率比较大,硬度较高的胶料则比较小。
当压出其它形状制品时,口型的型孔很少与压出制品的横断面相同,这是由于流动胶料在不同点上的不同摩擦力起作用所致。
因此对某一口型,一定要经多次反复试验,这样才能得到所需形状的产品。
包覆电线的压出,在压出机上需要使用T型机头。
口型与压出机机筒成直角安装在T型机头上。
这样芯线就可以通过空心口型导管(芯型)包覆上硅橡胶护套。
增强胶管也可以用T型机头进行连续生产,先用一般方法压好内胶层,并经预硫化后,再在其外面编织增强钢丝或尼龙,然后使其通过T型机头在其外面包覆一层外胶层,最后送往硫化、在成型过程中,若向胶管内充填压缩空气.可防止内胶的塌瘪。
硅橡胶压出半成品柔软而易变形,因此通常必须立即进行硫化。
最常用的方法是热空气连续硫化;电线、电缆工业通常用高压蒸气连续硫化。
如在压出后不能连续硫化,为防止变形。
压出后应立即用圆盘、圆鼓或输送带接取,用滑石粉隔离以免相互粘结。
如发现胶料过软而不适于庄出时,可将胶料再混入3~5份气相白炭黑。
一般用于压出的胶料配方,其硫化剂用量应比模压制品适当增加。
硅橡胶的压出速度低于其它橡胶,当要求同其它橡胶达到相同压出速度时,应采用较高的螺杆转速。
(三)压延硅橡胶的压延机一般采用立式三辊压延机。
用于生产胶片时,中辊是固定的,中辊转速比上辊快,速比为~:1,下辊的转速和中辊相比当压延机开动时,上辊温度为50℃,中辊应保持为室温,下辊用冷却水冷却。
压延速度不宜过快,一般为60~300cm/min。
先以低速调整(30~60cm/min)辊距(中、下辊),以保证一定的压延厚度,然后再提高至正常速度(150~300cm/min)进行连续操作。
垫布(常采用聚酯薄膜)在中、下辍之间通过,在中、下辊间应保持少量积胶,以便使整布与胶料紧密贴合。
压延后将胶片卷辊扎紧,并送进烘箱或硫化罐中硫化。
卷取辊的芯轴应当是空心金属管子,胶卷厚度不能超过12cm,否则不能获得充分硫化。
一般出片利用中、上辊即可,辊温为常温。
有一种方法可在后延机上直接制成硫化的胶片或薄胶板。
此时辊温为:上辊60~90℃,中辊50~80℃,下辊110~120℃。
胶料经上、中辊除去气泡,获得所需规格并预热,然后由中辊转移至下辊进行一段硫化即可卷取。
当三辊压延机用于硅橡胶贴胶和擦胶时,织物则代替了垫布(聚酯薄膜)在中辊和下辊之间通过。
三辊压延机只适用于单面复胶,如果必须两面复胶,在长期生产的情况下应采用四辊压延机。
用于压延的胶料必须正确控制其返炼程度,最好在炼胶机上先不要充分返炼,以期在压延过程中获得足够的返炼,这样可以避免胶料在压延过程中因返炼过度而粘辊。
胶料配方对压延也有一定的影响,采用补强性填充剂的胶料压延工艺性能较好。
(四)涂胶涂胶是指把硅橡胶胶浆用浸浆或刮浆的方法均匀分布在织物上,用以改进薄膜制品的强力和屈挠性能,使织物耐潮,以制造耐高温电绝缘材料等。
1.胶浆制备供制胶浆用的硅橡胶胶料,其硫化剂多采用硫化剂BP(过氧化二苯甲酰),这是由于硫化剂BP在室温下不易挥发,且与织物有较好的粘合性的缘故。
用量比一般模型制品稍多。
补强填充剂若采用气相白炭黑,用量不宜超过40份,井应适当增加结构控制剂的用量。
溶剂应采用挥发性的,如甲苯、二甲苯等。