工艺参数的设定和调节
制造业中的工艺参数优化与调整
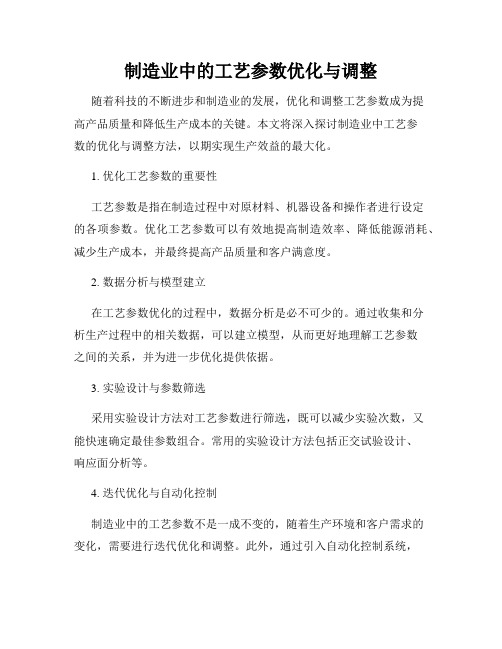
制造业中的工艺参数优化与调整随着科技的不断进步和制造业的发展,优化和调整工艺参数成为提高产品质量和降低生产成本的关键。
本文将深入探讨制造业中工艺参数的优化与调整方法,以期实现生产效益的最大化。
1. 优化工艺参数的重要性工艺参数是指在制造过程中对原材料、机器设备和操作者进行设定的各项参数。
优化工艺参数可以有效地提高制造效率、降低能源消耗、减少生产成本,并最终提高产品质量和客户满意度。
2. 数据分析与模型建立在工艺参数优化的过程中,数据分析是必不可少的。
通过收集和分析生产过程中的相关数据,可以建立模型,从而更好地理解工艺参数之间的关系,并为进一步优化提供依据。
3. 实验设计与参数筛选采用实验设计方法对工艺参数进行筛选,既可以减少实验次数,又能快速确定最佳参数组合。
常用的实验设计方法包括正交试验设计、响应面分析等。
4. 迭代优化与自动化控制制造业中的工艺参数不是一成不变的,随着生产环境和客户需求的变化,需要进行迭代优化和调整。
此外,通过引入自动化控制系统,可以实现对工艺参数的实时监测和自动调整,提高生产过程的稳定性和一致性。
5. 数据挖掘与智能优化随着大数据和人工智能的发展,数据挖掘技术可以更好地挖掘隐藏在大量数据背后的规律和关联。
通过将数据挖掘与智能优化相结合,不仅可以发现更精确的工艺参数优化方法,还可以实现更高水平的自动化和智能化生产。
6. 成本管理与效益分析优化工艺参数旨在降低生产成本并提高效益。
因此,制造企业需要建立科学的成本管理体系和效益分析模型,全面评估工艺参数的优化与调整对生产成本和效益的影响。
总结:制造业中的工艺参数优化和调整是提高制造效率、降低成本、提高产品质量的关键环节。
数据分析、实验设计、自动化控制、数据挖掘和智能优化等方法的应用,使得工艺参数优化与调整更加科学化和智能化。
通过不断迭代和持续优化,制造企业可以实现生产效益的最大化,为市场竞争提供有力支撑。
工艺参数的设定和调节(写写帮整理)

工艺参数的设定和调节(写写帮整理)第一篇:工艺参数的设定和调节(写写帮整理)第四节工艺参数的设定和调节技能压铸生产中机器工艺参数的设定和调节直接影响产品的质量。
一个参数可能造成产品的多个缺陷,而同一产品的同一缺陷有可能与多个参数有关,要求在试压铸生产中要仔细分析工艺参数的变化对铸件成形的影响。
压铸生产厂家通常由专人设定和调节机器参数。
下面以力劲机械厂有限公司生产的DCC280卧式冷室压铸机为例,说明压铸生产中主要工艺参数的设定和调节技能。
第四节工艺参数的设定和调节技能压铸生产中机器工艺参数的设定和调节直接影响产品的质量。
一个参数可能造成产品的多个缺陷,而同一产品的同一缺陷有可能与多个参数有关,要求在试压铸生产中要仔细分析工艺参数的变化对铸件成形的影响。
压铸生产厂家通常由专人设定和调节机器参数。
下面以力劲机械厂有限公司生产的DCC280卧式冷室压铸机为例,说明压铸生产中主要工艺参数的设定和调节技能。
一、主要工艺参数的设定技能DCC280卧式冷室压铸机设定的内容及方法如下:(1)射料时间:射料时间大小与铸件壁厚成正比,对于铸件质量较大、压射一速速度较慢且所需时间较长时,射料时间可适当加大,一般在2S以上。
射料二速冲头运动的时间等于填充时间。
(2)开型(模)时间:开型(模)时间一般在2S以上。
压铸件较厚比较薄的开型(模)时间较之要长,结构复杂的型(模)具比结构简单的型(模)具开型(模)时间较之要长。
调节开始时可以略为长一点时间,然后再缩短,注意机器工作程序为先开型(模)后再开安全门,以防止未完全冷却的铸件喷溅伤人。
(3)顶出延时时间:在保证产品充分凝固成型且不粘模的前提下,尽量减短顶出延时时间,一般在0.5S以上。
(4)顶回延时时间:在保证能顺利地取出铸件的前提下尽量减短顶回延时时间,一般在0.5S以上。
(5)储能时间:一般在2S左右,在设定时操作机器作自动循环运动,观察储能时间结束时,压力是否能达到设定值,在能达到设定压力值的前提下尽量减短储能时间。
工艺参数调整管理规定
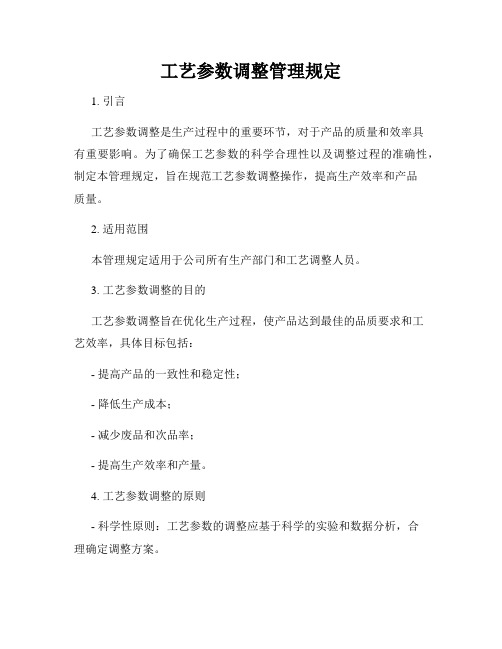
工艺参数调整管理规定1. 引言工艺参数调整是生产过程中的重要环节,对于产品的质量和效率具有重要影响。
为了确保工艺参数的科学合理性以及调整过程的准确性,制定本管理规定,旨在规范工艺参数调整操作,提高生产效率和产品质量。
2. 适用范围本管理规定适用于公司所有生产部门和工艺调整人员。
3. 工艺参数调整的目的工艺参数调整旨在优化生产过程,使产品达到最佳的品质要求和工艺效率,具体目标包括:- 提高产品的一致性和稳定性;- 降低生产成本;- 减少废品和次品率;- 提高生产效率和产量。
4. 工艺参数调整的原则- 科学性原则:工艺参数的调整应基于科学的实验和数据分析,合理确定调整方案。
- 稳定性原则:调整后的工艺参数应能够长期保持稳定,确保产品质量和生产效率的稳定性。
- 安全性原则:调整过程中应注意安全事项,确保人员和设备的安全性。
- 可追溯性原则:所有工艺参数调整的记录应完整、准确、可追溯。
5. 工艺参数调整的流程5.1. 调整前的准备工作- 审查历史数据:仔细分析历史数据,了解当前工艺参数的表现和问题。
- 设定目标:根据产品要求和生产效率,确定工艺参数调整的目标。
- 制定方案:根据目标和数据分析,制定工艺参数调整的方案。
5.2. 调整中的操作步骤- 仪器准备:确保使用的仪器设备处于正常工作状态。
- 测试样品准备:按照要求准备调整前后的样品。
- 测试参数设置:根据调整方案,设置仪器参数并进行测试。
- 数据记录:记录测试数据和仪器参数,并进行归档。
5.3. 调整后的确认工作- 数据分析:对调整后的数据进行分析,评估调整效果。
- 质量确认:对调整后的产品进行质量检验,确保达到要求。
- 参数调整稳定性验证:长期监测调整后工艺参数的表现,确保稳定性。
6. 工艺参数调整管理的责任与要求- 管理责任:各生产部门负责制定和执行工艺参数调整管理计划,确保操作规范。
- 人员要求:工艺调整人员应熟悉相关工艺知识和操作规程,并接受必要的培训。
回流焊接工艺参数设置与调制规范

回流焊接工艺参数设置与调制规范1. 初始参数设定流程图1.1、测温板制作依照《SMT PROFILE 标准参数测量规范》制作测温板制作。
1.2、温度设定a 、 以锡膏厂商提供的资料制定《焊锡膏(贴片胶)对应炉温要求》参数表,依此表设定温度,(见附表一)b 、以产品特性、PCB 材质与厚度、组件分布密度及吸热量设定温度,c 、考虑客户是否有特殊要求最佳的有铅锡膏回焊曲线温度:(peaktemp)215℃±5℃开制作测温板设定参数确定最高/低峰值温度温度测试PCB 裸板或PCBA 板 结束是否有热敏器件调试参数并测试NG0<Slope<3/sec0<Slope<3℃/sec回焊区冷却区预热区恒温区1)预热区自室温状态至130℃之间,其升温速率不可超过3℃/秒。
2)恒温区温度介于120℃~160℃之间,时间为60~120秒。
目标为90-110秒。
3)回焊区温度210℃以上,时间为15~45秒。
4)回焊区升温速率须小于3℃/sec。
5). BGA焊点脚Peak温度为215±5℃,表面温度小于230℃(除客户特殊要求外),其余零件焊点脚Peak温度一般应小于等于230℃。
6)冷却区冷却速率须小于4℃/sec最佳胶水温度曲线1801251.)最高温度145℃.2.)125℃~145℃时间 T:105~210S.3.)用同一机种基板上体积最大(即吸热最严重)的组件引脚或CHIP焊盘作为炉温测试点.最佳的无铅锡膏回焊曲线温度250 25060少于3℃1.)升温阶段:升温速率应低于3℃/Sec。
2.)最高温度不得低于230℃,最高温度不得高于250℃。
3.)预热段温度:30℃至150℃的时间: 60-90Sec;4.)恒温段温度:150℃至217℃的时间:60 —120Sec; 目标:90_100sec5.)回流段温度:大于217℃以上的时间:60 —90Sec;目标:70sec 峰值温度: 230-245℃。
制造工艺中的工艺参数监控与调整
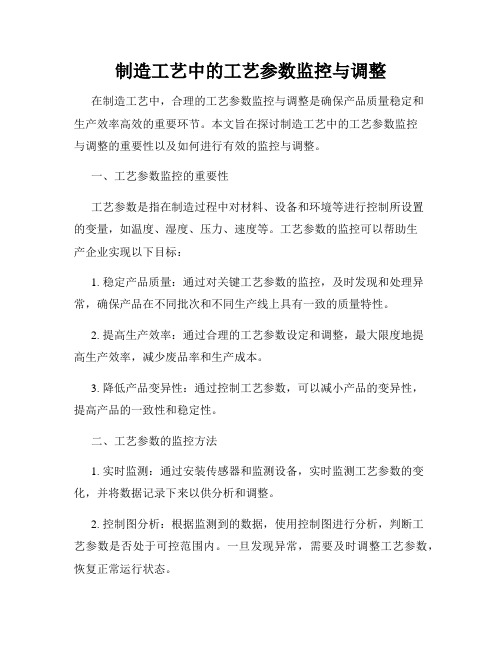
制造工艺中的工艺参数监控与调整在制造工艺中,合理的工艺参数监控与调整是确保产品质量稳定和生产效率高效的重要环节。
本文旨在探讨制造工艺中的工艺参数监控与调整的重要性以及如何进行有效的监控与调整。
一、工艺参数监控的重要性工艺参数是指在制造过程中对材料、设备和环境等进行控制所设置的变量,如温度、湿度、压力、速度等。
工艺参数的监控可以帮助生产企业实现以下目标:1. 稳定产品质量:通过对关键工艺参数的监控,及时发现和处理异常,确保产品在不同批次和不同生产线上具有一致的质量特性。
2. 提高生产效率:通过合理的工艺参数设定和调整,最大限度地提高生产效率,减少废品率和生产成本。
3. 降低产品变异性:通过控制工艺参数,可以减小产品的变异性,提高产品的一致性和稳定性。
二、工艺参数的监控方法1. 实时监测:通过安装传感器和监测设备,实时监测工艺参数的变化,并将数据记录下来以供分析和调整。
2. 控制图分析:根据监测到的数据,使用控制图进行分析,判断工艺参数是否处于可控范围内。
一旦发现异常,需要及时调整工艺参数,恢复正常运行状态。
3. 建立预警机制:通过设定预警值,当工艺参数超出设定范围时,及时发出警报,以便操作人员能够迅速采取措施进行调整。
三、工艺参数的调整方法1. 根据实际情况设定合理的目标值:在设定工艺参数时,应根据产品的要求和生产设备的性能,制定合理的目标值,确保产品的质量和性能满足要求。
2. 小范围试验:在生产过程中,可以进行小范围试验,通过对不同工艺参数进行微调,寻求最佳的参数组合,以达到最佳的生产效果。
3. 辅助工艺优化:除了对工艺参数的调整外,还可以通过改进工艺流程和优化设备等手段,提升产品的整体质量和生产效率。
四、工艺参数监控与调整的挑战与应对策略1. 多变因素的影响:制造工艺中,存在多个因素对工艺参数的影响,需要综合考虑各种因素的综合影响,并制定相应的监控和调整策略。
2. 数据处理与分析:大量的工艺参数数据需要及时收集和处理,并进行合理的数据分析。
机械加工工艺参数设定规定
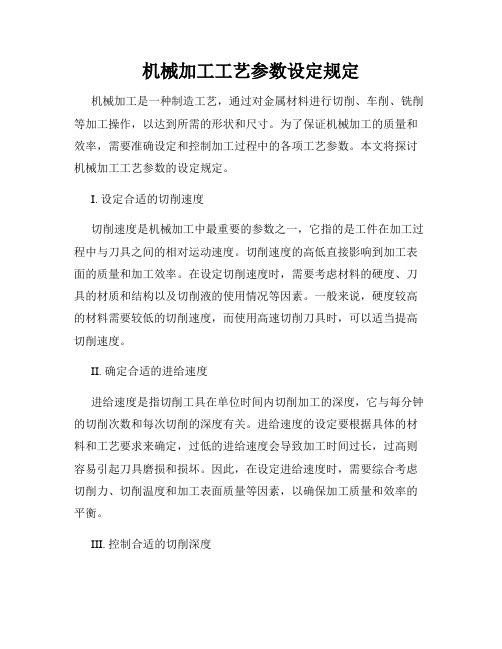
机械加工工艺参数设定规定机械加工是一种制造工艺,通过对金属材料进行切削、车削、铣削等加工操作,以达到所需的形状和尺寸。
为了保证机械加工的质量和效率,需要准确设定和控制加工过程中的各项工艺参数。
本文将探讨机械加工工艺参数的设定规定。
I. 设定合适的切削速度切削速度是机械加工中最重要的参数之一,它指的是工件在加工过程中与刀具之间的相对运动速度。
切削速度的高低直接影响到加工表面的质量和加工效率。
在设定切削速度时,需要考虑材料的硬度、刀具的材质和结构以及切削液的使用情况等因素。
一般来说,硬度较高的材料需要较低的切削速度,而使用高速切削刀具时,可以适当提高切削速度。
II. 确定合适的进给速度进给速度是指切削工具在单位时间内切削加工的深度,它与每分钟的切削次数和每次切削的深度有关。
进给速度的设定要根据具体的材料和工艺要求来确定,过低的进给速度会导致加工时间过长,过高则容易引起刀具磨损和损坏。
因此,在设定进给速度时,需要综合考虑切削力、切削温度和加工表面质量等因素,以确保加工质量和效率的平衡。
III. 控制合适的切削深度切削深度是指刀具在每次切削中削除工件材料的厚度。
切削深度的设定要根据工件的材质、硬度和稳定性来确定。
如果切削深度过大,会增加切削力和切削温度,容易导致刀具振动、工件变形和表面质量下降。
因此,在设定切削深度时,需要根据具体情况做出合理的选择,并进行试切实验以验证加工效果。
IV. 设定适当的切削液使用量切削液在机械加工过程中起到冷却、润滑和清洁的作用,能有效降低切削温度、减少切削力和延长刀具寿命。
切削液的使用量需要根据加工材料、切削速度和切削方式等因素来确定。
针对不同的工艺要求,有时需要调整切削液的类型和浓度。
在设定切削液使用量时,操作人员应掌握切削液的性能指标,并遵循相关的安全操作规范。
V. 考虑刀具的选择和磨损控制刀具的选择要根据不同的加工任务来确定,包括工件材料、形状和尺寸等方面的要求。
同时,刀具的磨损情况也需要及时控制,以保证加工质量和效率。
压铸机选用压铸工艺参数设定和调节
一、压铸机的选用步骤1)根据铸件的技术要求、使用条件和压铸工艺规范核算压铸机的技术参数及工艺性,初选合适机型。
2)根据初步构想的压铸型(模)技术参数和工艺要求核算出压铸工艺参数及压铸型(模)外形尺寸,选用合适机型。
3)评定压铸机的工作性能和经济效果,包括成品率、合格率、生产率及运转的稳定性、可靠性、和安全性等。
二、压铸机的选用方法1)在实际生产中,选择压铸机主要根据压铸合金的种类、铸件的轮廓尺寸和重量确定采用热室或冷室压铸机。
对于锌合金铸件和小型的镁合金铸件通常选用热室压铸机。
对于铝合金、铜合金铸件和大型的镁合金铸件选用冷室压铸机为主。
立式冷室压铸机适合于形状为中心辐射状和圆筒形的、同时又具备开设中心浇道条件的铸件。
2)根据压铸件的材料、轮廓尺寸、平均壁厚、净重来选择压铸机型号规格。
可通过计算来求得锁型(模)力的大小值、每次浇注量、压射室充满度等实际工艺参数作为选取机型的依据。
3)压铸型(模)大小应与压铸机上安装型(模)具的相应尺寸相匹配,其主要尺寸为压铸型(模)的厚度和型(模)具分型面之间的距离。
必须满足压铸机基本参数的要求:①压铸型(模)厚度H 设不得小于机器说明书所给定的最小型(模)具厚度,也不得大于所给定的最大型(模)具厚度,H设应满足如下条件Hmin+10mm≤ H 设≤ Hmax-10mm式中H 设—所设计的型(模)具厚度(mm);Hmin—压铸件所给定的型(模)具最小厚度,即“模薄”(mm);Hmax—压铸机所给定的型(模)具最大厚度,即“模厚”(mm)。
②压铸机开型(模)后,应使压铸机动型(模)座板行程(L)即压铸型(模)具分型面之间的距离大于或等于能取出铸件的最小距离。
L≥L 取如图1所示为推杆推出的压铸型(模)取出铸件的最小距离。
L取≥L 芯+L 件+K式中,K 一般取10mm。
三、压铸机选用方法举例例已知一盒形铸件,如图2所示。
下面以力劲机械厂有限公司生产的卧式冷室压铸机机型技术参数为依据进行选型分析。
生产工艺参数管理规定
生产工艺参数管理规定一、工艺参数的定义和分类工艺参数是生产过程中可以调节或控制的具体数值,以达到产品质量和性能要求的指标。
根据调节和控制的对象和程度,可以将工艺参数分为输入参数和输出参数。
输入参数影响着产品的工艺特性和性能,如温度、湿度、压力等;输出参数反映了产品的实际制造效果,如尺寸、外观、表面质量等。
二、工艺参数管理的重要性1.稳定产品质量:通过合理设置和控制工艺参数,可以降低产品制造过程中的变异性,保持产品的稳定性和一致性。
2.提高生产效率:合理调整工艺参数可以优化生产过程,减少工艺调整时间,提高生产效率。
3.减少不良品率:通过合理设置和控制工艺参数,可以有效防止生产过程中出现的不良品,减少不良品率,降低生产成本。
4.提高产品竞争力:优化工艺参数可以改善产品的质量和性能,提高产品的竞争力和市场占有率。
三、工艺参数管理的原则和方法1.根据产品特性和工艺要求,确定关键的工艺参数。
关键参数是对产品质量和性能具有重要影响的参数,需要进行严格控制和调整。
2.设置合理的工艺参数范围。
工艺参数范围应根据产品的设计要求和制造过程的变化规律进行确定,确保在合理范围内调整参数不会对产品质量和性能产生不良影响。
3.建立完善的参数管理制度。
制定合理的参数管理规定和操作方法,包括参数设定、参数调整、参数记录和参数变更等具体内容,明确责任和操作流程。
4.进行参数的实时监控和分析。
通过实时监控和分析参数的变化,及时发现异常情况,采取措施进行调整和修正,保证参数的稳定性和准确性。
5.进行参数调整和优化。
周期性地对工艺参数进行调整和优化,不断提高产品质量和性能,降低生产成本。
四、工艺参数管理的质量控制方法1.参数设定和调整的标准化。
根据产品特性,制定参数设定和调整的标准化方法,确保不同操作人员和设备都能按照相同的标准进行操作。
2.记录和追溯能力的建立。
对每一次设定和调整的参数进行记录,建立完善的数据追溯系统,方便日后分析和溯源。
工艺参数调整程序
工艺参数调整程序1. 背景为了确保生产过程中的质量和效率,工艺参数的调整是必不可少的。
本文档旨在制定一套标准程序,以指导工艺参数的调整过程。
2. 目标本程序的目标是确保工艺参数的调整过程准确、高效,并最大程度地减少对产品质量和生产效率的影响。
3. 程序步骤3.1 收集数据在开始调整工艺参数之前,需要收集与工艺参数相关的数据。
这些数据可能包括原始工艺参数设定值、生产数据、质量检测结果等。
确保数据的准确性和完整性是调整工艺参数的关键。
3.2 分析数据基于收集到的数据,进行数据分析,以了解当前工艺参数的表现和潜在问题。
可以使用统计方法、图表和其他分析工具来识别异常或偏差,并找出导致问题的可能原因。
3.3 制定调整方案根据数据分析的结果,制定具体的调整方案。
调整方案可能涉及改变工艺参数设定值、调整操作流程或引入新的控制措施等。
确保调整方案符合安全、可行和可控的原则。
3.4 执行调整按照制定的调整方案,执行工艺参数的调整。
在执行过程中,密切观察生产过程和质量指标的表现,及时记录相关数据,并与调整前进行对比。
3.5 监控效果调整完成后,持续监控工艺参数的表现和产品质量。
通过对监控数据的分析,评估调整效果是否达到预期目标。
如果需要进一步改进或优化,可以重新进行数据收集和分析,并制定新的调整方案。
4. 文件记录为了确保调整过程的可追溯性和复现性,应当对每次工艺参数调整进行详细记录。
记录内容应包括但不限于调整日期、工艺参数设定值、数据分析结果、调整方案、执行记录和调整效果评估等。
5. 培训和交流为了确保操作人员的理解和执行,有必要进行培训和交流。
培训内容应包括调整程序的要求、数据收集和分析方法、调整方案的制定和执行等。
同时,鼓励操作人员提供反馈和建议,以不断改进工艺参数调整程序。
6. 监督和改进为了保证程序的有效性和持续改进,建议定期进行监督和评估。
监督应包括对调整过程的监控和审核,以及对调整结果的评估。
根据监督和评估的结果,适时进行改进和优化。
化学技术实验中的关键工艺参数选择与设定方法总结
化学技术实验中的关键工艺参数选择与设定方法总结在化学技术实验中,关键工艺参数的选择与设定是确保实验准确性和可重复性的关键步骤。
不同的化学实验需要根据具体要求选择不同的工艺参数,如温度、压力、浓度等。
本文将总结一些常见的关键工艺参数选择与设定方法,帮助研究人员进行实验设计和工艺优化。
首先,温度是化学实验中最常见的关键工艺参数之一。
不同的化学反应需要在特定温度下进行,以确保反应速率和产物品质。
选择适当的反应温度应考虑到反应的热力学和动力学要求。
一般来说,较高温度可以加快反应速率,但过高的温度可能导致副反应、产物分解或安全问题。
因此,实验中应通过文献查询或试验确定最佳的反应温度范围,并通过较小的步长进行优化。
其次,压力也是一些特定化学实验中的关键工艺参数。
例如,在高压条件下进行催化反应可以提高反应速率和选择性。
在选择压力时,需要考虑反应物的物理性质和反应条件的安全性。
实验中可以通过改变反应器尺寸、添加催化剂或调整反应物浓度来调节压力。
此外,压力传感器的应用也是确保实验稳定性和数据准确性的重要手段。
浓度是另一个决定化学反应性质的重要参数。
在涉及液相反应的实验中,合理控制反应物浓度可以调节反应速率和副产物生成。
一般来说,较高的浓度可以增加反应物分子间的碰撞频率,从而加速反应进程。
然而,过高的浓度可能导致剧烈的副反应或产物结晶。
因此,实验中应以较小的步长逐渐增加反应物浓度,并对反应过程进行实时监测。
此外,反应时间也是决定化学实验成功与否的重要参数之一。
在实验设计时,需要确定反应时间范围,并进行步长优化。
反应时间的选择应考虑到反应物的性质、反应速率和理想产物的收率。
短时间可能导致不完全反应,而过长时间可能导致反应物分解、产物副产物生成或设备损坏。
因此,通过实验或模型计算确定最佳反应时间是确保实验结果准确和可重复的关键步骤。
最后,pH值和溶剂选择也是化学实验中需要注意的关键工艺参数。
在一些催化反应或酶催化反应中,pH值可以影响反应速度和选择性。
- 1、下载文档前请自行甄别文档内容的完整性,平台不提供额外的编辑、内容补充、找答案等附加服务。
- 2、"仅部分预览"的文档,不可在线预览部分如存在完整性等问题,可反馈申请退款(可完整预览的文档不适用该条件!)。
- 3、如文档侵犯您的权益,请联系客服反馈,我们会尽快为您处理(人工客服工作时间:9:00-18:30)。
第四节工艺参数的设定和调节技能压铸生产中机器工艺参数的设定和调节直接影响产品的质量。
一个参数可能造成产品的多个缺陷,而同一产品的同一缺陷有可能与多个参数有关,要求在试压铸生产中要仔细分析工艺参数的变化对铸件成形的影响。
压铸生产厂家通常由专人设定和调节机器参数。
下面以力劲机械厂有限公司生产的DCC280卧式冷室压铸机为例,说明压铸生产中主要工艺参数的设定和调节技能。
第四节工艺参数的设定和调节技能压铸生产中机器工艺参数的设定和调节直接影响产品的质量。
一个参数可能造成产品的多个缺陷,而同一产品的同一缺陷有可能与多个参数有关,要求在试压铸生产中要仔细分析工艺参数的变化对铸件成形的影响。
压铸生产厂家通常由专人设定和调节机器参数。
下面以力劲机械厂有限公司生产的DCC280卧式冷室压铸机为例,说明压铸生产中主要工艺参数的设定和调节技能。
一、主要工艺参数的设定技能DCC280卧式冷室压铸机设定的内容及方法如下:(1)射料时间:射料时间大小与铸件壁厚成正比,对于铸件质量较大、压射一速速度较慢且所需时间较长时,射料时间可适当加大,一般在2S以上。
射料二速冲头运动的时间等于填充时间。
(2)开型(模)时间:开型(模)时间一般在2S以上。
压铸件较厚比较薄的开型(模)时间较之要长,结构复杂的型(模)具比结构简单的型(模)具开型(模)时间较之要长。
调节开始时可以略为长一点时间,然后再缩短,注意机器工作程序为先开型(模)后再开安全门,以防止未完全冷却的铸件喷溅伤人。
(3)顶出延时时间:在保证产品充分凝固成型且不粘模的前提下,尽量减短顶出延时时间,一般在0.5S以上。
(4)顶回延时时间:在保证能顺利地取出铸件的前提下尽量减短顶回延时时间,一般在0.5S以上。
(5)储能时间:一般在2S左右,在设定时操作机器作自动循环运动,观察储能时间结束时,压力是否能达到设定值,在能达到设定压力值的前提下尽量减短储能时间。
(6)顶针次数:根据型(模)具要求来设定顶针次数。
(7)压力参数设定在保证机器能正常工作,铸件产品质量能合乎要求的前提下,尽量减小工作压力。
选择、设定压射比压时应考虑如下因素:1)压铸件结构特性决定压力参数的设定。
①壁厚:薄壁件,压射比压可选高些;厚壁件,增压比压可选高些。
②铸件几何形状复杂程度:形状复杂件,选择高的比压;形状简单件,比压低些。
③工艺合理性:工艺合理性好,比压低些。
2)压铸合金的特性决定压力参数的设定①结晶温度范围:结晶温度范围大,选择高比压;结晶温度范围小,比压低些。
②流动性:流动性好,选择较低压射比压;流动性差,压射比压高些。
③密度:密度大,压射比压、增压比压均应大;密度小,压射比压、增压比压均选小些。
④比强度:要求比强度大,增压比压高些。
3)浇注系统决定压力参数的设定①浇道阻力:浇道阻力大,主要是由于浇道长、转向多,在同样截面积下、内浇口厚度小产生的,增压比压应选择大些。
②浇道散热速度:散热速度快,压射比压高些;散热速度慢,压射比压低些。
4)排溢系统决定压力参数的设置①排气道分布:排气道分布合理,压射比压、增压比压均选高些。
②排气道截面积:排气道截面积足够大,压射比压选高些。
5)内浇口速度要求速度高,压射比压选高些。
(⑥温度合金与压铸型(模):温差大,压射比压高些;温差小,压射比压低些。
8)压射速度的设定压射速度分为慢压射速度(又称射料一速)、快压射速度(又称射料二速)、增压运动速度。
慢压射速度通常在0.1~0.8m/s范围内选择,运动速度由0逐渐增大,快压射速度与内浇口速度成正比,一般从低向高调节,在不影响铸件质量的情况下,以较低的快压射速度即内浇口速度为宜。
增压运动所占时间极短,它的目的是压实金属,使铸件组织致密。
增压运动速度在调节时,一般观察射料压力表的压力示值在增压运动中呈一斜线均匀上升,压铸产品无疏松现象即可。
(9)一速、二速转换感应开关的位置调节原则1)一速、二速运动转换应该在压射冲头通过压室浇注口后进行2)对于薄壁小铸件,一般一速较短、二速较长3)对于厚壁大铸件,一般一速较长,二速较短4)根据铸件质量(如飞边、欠铸、气泡等)调节转换点。
(10)金属液温度的调节合金液温度可从机器电气箱面板上显示和设定。
各种合金液其浇注温度不相同,同一压铸合金不同结构的产品,其厚壁铸件比薄壁铸件浇注温度要低。
(11)浇注量的选择所选择的每次浇注量应使所生产出来的产品余料厚度在15~25mm范围为宜,并要求每次合金液的舀取量要稳定。
(12)模温的控制模温是指压铸型(模)合型(模)时的温度,对于不同的合金液,其模温温度不同,一般以合金凝固温度的1/2为限。
在压铸生产中最重要的是型(模)具工作温度的稳定和平衡,它是影响压铸件质量和压铸效率的重要因素之一。
机器液压系统各个动作的工艺参数,如压力、速度、行程、起点与终点,各个动作的时间和整个工作循环的总时间都有一定的技术参数,要求调试人员一定要熟悉机器技术性能,根据液压系统图认真分析所有元件的结构、作用、性能和调试范围,搞清楚液压元件在设备上的实际位置,并了解机械、电气、液压的相互关系。
二、主要工艺参数的调节技能1.机器在调节时应注意的事项1)只能调节机器使用说明书上指出的可调参数。
调压时应按使用说明书的要求进行,不准大于规定的压力值,尽量防止调压过高,而致使油温增高或损坏元件。
2)不准在执行元件(液压缸、液压马达)运动状态下调节系统工作压力。
3)调压前应先检查压力表是否损坏,若有异常,待压力表更换后再调节压力。
4)调压前,先把所要调节的调压阀上的调节螺母放松,调压后,应将调节螺钉的紧固螺母拧紧,以免松动。
2.主要工艺参数的调节技能(1)开、合型(模)慢速段的调节开型(模)和合型(模)慢速段的速度统一由慢速油阀左侧的调节螺钉控制。
顺时针旋紧螺钉,则开、合型(模)慢速段速度减慢,逆时针旋松螺钉,则开、合型(模)慢速速度加快。
调节合适后,将固定螺母拧紧,如图3-93所示。
图3-93 开、合型(模)慢速段的调节(2)开、合型(模)常速(即快速)段的调节1)开型(模)常速段速度由开、合型(模)换向阀右侧的调节螺钉控制。
顺时针旋紧螺钉,则速度减慢,逆时针旋松螺钉,则速度加快。
调节合适后,将固定螺母拧紧,如图3-94所示。
图3-94 开型(模)常速(即快速)段的调节2)合型(模)常速段速度由开、合型(模)换向阀左侧的调节螺钉控制。
顺时针旋紧调节螺钉,则合型常速段速度减慢,逆时针旋松调节螺钉,则合型常速段速度加快。
调节合适后,将固定螺母拧紧,如图3-95所示。
图3-95 合型(模)常速(即快速)段的调节(3)低压大流量泵压力的调节起动机器作自动循环运动,用手旋转双泵流量控制阀上的调节螺钉,可调节低压压力到一定值(一般5×106Pa(50bar)左右),低压压力值从低压压力指示表上读出。
调节合适后,将固定螺母拧紧,如图3-96所示。
图3-96低压大流量泵压力的调节(4)射料二速工作压力的调节射料二速工作压力由控制二速压力的调节螺钉调节,用手旋转减压阀上的调节螺钉可调节压力大小,其压力示值从射料二速压力表中读出,此压力即为二速射料运动中的射料压力。
DCC400卧式冷室压铸机具体调节步骤如下:1)先旋松截止阀上调节螺钉,使二速蓄能器卸荷后再旋紧,如图3-97所示。
图3- 97 旋松截止阀2)旋松减压阀调节螺钉上的紧固螺母,如图3-98所示。
图3- 98 旋松减压阀3)一边用手按住起压按钮,一边慢速调节减压阀上调节螺钉,观察压力表上指针到所需要的示值(最大值1.4×107Pa(140bar))为止,如图3-99所示;4)将减压阀调节螺钉上的紧固螺母拧紧。
图3-99 起压并观察压力表(5)增压运动工作压力的调节增压运动工作压力由控制增压蓄能器的减压阀上的调节螺钉调节。
用手旋转减压阀上的调节螺钉,可调节其压力大小,其压力示值从增压压力表中读出。
DCC400卧式冷室压铸机增压压力具体调节步骤如下:1)先旋松截止阀(V54)阀上调节螺钉,使增压蓄能器卸荷后再旋紧,如图3-100所示;图3-100 旋松截止阀2)旋松减压阀调节螺钉上的紧固螺母,如图3-101所示。
图3-101 旋松减压阀3)一边用手按住起压按钮,一边调节减压阀(V51)上调节螺钉,观察压力表指针到所需要的示值为止,如图3-102所示;4)将减压阀调节螺钉上的紧固螺母拧紧。
图3-102 起压、观察压力表,调节螺钉(6)增压控制蓄能器压力的调节1)先旋松截止阀(V63)阀上调节螺钉,使增压控制蓄能器卸荷后再旋紧,如图3-103所示。
图3-103 旋松减压阀2)旋松减压阀(V65)调节螺钉上的紧固螺母。
3)一边用手按住起压按钮,一边调节减压阀(V51)上调节螺钉,顺时针旋转螺杆,压力增大;逆时针旋转螺杆,压力减小,观察压力表指针到所需要的示值(6×106Pa(60bar))为止,如图3-104所示。
4)将减压阀调节螺钉上的紧固螺母拧紧。
图3-104 起压、观察压力表(7)射料一速速度的调节射料一速运动速度由一速可调插装阀左侧控制,调节其螺杆可改变一速运动速度:顺时针旋转螺杆,速度减小;逆时针旋转螺杆,速度增大,如图3-105所示。
图3-105射料一速速度的调节(8)射料二速速度的调节射料二速的速度大小由二速插装阀上的调节手轮控制,用手旋转手轮可获得不同的速度:顺时针旋转手轮,速度减小;逆时针旋转手轮,速度增大,如图3-106所示。
图3-106射料二速速度的调节(9)增压速度的调节增压速度的大小由插装阀上的调节手轮控制,用手旋转手轮可获得不同的速度:顺时针旋转手轮,速度减小;逆时针旋转手轮,速度增大,如图3-107所示。
图3-107增压速度的调节(10)射料回锤速度调节射料回锤运动的速度由射料可调换向阀右侧控制,调节其螺杆可改变回锤运动速度:顺时针旋转螺杆,速度减小;逆时针旋转螺杆,速度增大,如图3-108所示。
图3-108 射料回锤速度调节(11)一速、二速运动行程的调节一速、二速运动行程的长短由二速感应开关的位置决定,两段行程的长短影响铸件的成形质量,例如欠铸、飞边、气泡等,一般在试压铸生产中根据产品质量作调节,如图3-109所示。
图3-109 一速、二速运动行程的调节第三节压铸机的选用一、压铸机的选用原则1)根据铸件的技术要求、使用条件和压铸工艺规范核算压铸机的技术参数及工艺性,初选合适机型。
2)根据初步构想的压铸型(模)技术参数和工艺要求核算出压铸工艺参数及压铸型(模)外形尺寸,选用合适机型。
3)评定压铸机的工作性能和经济效果,包括成品率、合格率、生产率及运转的稳定性、可靠性、和安全性等。
二、压铸机的选用方法1)在实际生产中,选择压铸机主要根据压铸合金的种类、铸件的轮廓尺寸和重量确定采用热室或冷室压铸机。