风电叶片灌注树脂固化性能的影响
老化对风电叶片用环氧树脂性能的影响

数 ( 如形状 、长度和面积等 ) 有着密切的关系,叶
收稿 日期 :2 1— 4 0 0 lo - 8
劣的地方,而叶片的服役寿命要求达到2 3 年, 0 0 因
作者简介 : 卢
敏 ( 97 ) ,湖南攸 县人 ,湖南工业大 学硕 士生 18一 ,女
,
主要研 究方向为复合材料性 能及应用 ,
后 ,由于 水 的增 塑作 用 ,导致 玻璃 化转 变温度 有所
样 ,取平均值 。
下 降。分 图 b) 显示 ,湿热 老化后 为 7 .6 o 1 3 C,与
2 结 果 与讨论
21 D C . S 分析
老化前相 比玻璃化转变温度下 降了 5c左右 ;分图 C C )
显示 ,盐雾老化后 为 6 .8℃ ,比老化前下 降了 8 73
T mp rt r/ e ea ue * C
b)湿热老化
2) 盐雾试验 。试验设备为高铁检测仪器 ( 中国 )
有 限公司生产的 G - 0 4 L盐水喷雾试验机 ,盐雾试 T 70- 验参照 G / 0 2 — 19 B T 1 15 9 7进行 。为了较好 地模 拟海
如
言
。
洋 大气 环境 ,采用 中性盐雾 条件 ,试 验溶 液 为质量 分数为 1%的分析纯 N C 水溶液 , 0 a1 试验温度为 3 , 5℃
E ma l u n0 2 @ 1 3t m - i:l mi .8 8 6 .o
3 4
湖
南
工
业
大
学
学
报
2 1 芷 01
此 选材 很重 要 。通过 人工 加速 老化来 评估 叶 片基体 材 料 的性能 ,对 叶片 材料选 择 、结 构设计 具有 重要 意义 。本文 拟对 经过 湿热 、盐 雾 、冷热 老化 后 的树
风电叶片用真空导入环氧树脂的标准
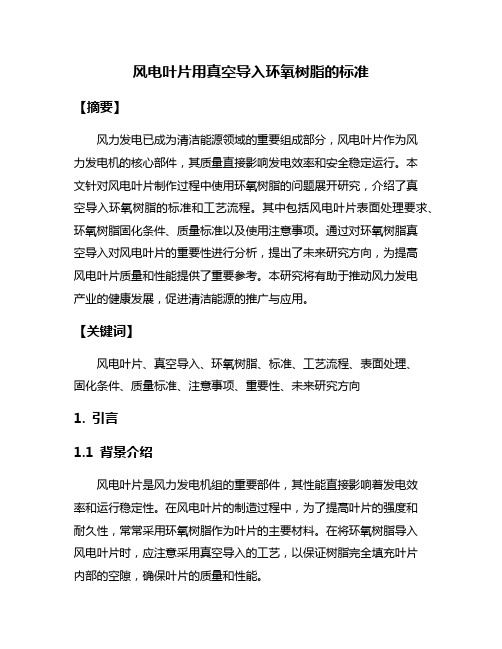
风电叶片用真空导入环氧树脂的标准【摘要】风力发电已成为清洁能源领域的重要组成部分,风电叶片作为风力发电机的核心部件,其质量直接影响发电效率和安全稳定运行。
本文针对风电叶片制作过程中使用环氧树脂的问题展开研究,介绍了真空导入环氧树脂的标准和工艺流程。
其中包括风电叶片表面处理要求、环氧树脂固化条件、质量标准以及使用注意事项。
通过对环氧树脂真空导入对风电叶片的重要性进行分析,提出了未来研究方向,为提高风电叶片质量和性能提供了重要参考。
本研究将有助于推动风力发电产业的健康发展,促进清洁能源的推广与应用。
【关键词】风电叶片、真空导入、环氧树脂、标准、工艺流程、表面处理、固化条件、质量标准、注意事项、重要性、未来研究方向1. 引言1.1 背景介绍风电叶片是风力发电机组的重要部件,其性能直接影响着发电效率和运行稳定性。
在风电叶片的制造过程中,为了提高叶片的强度和耐久性,常常采用环氧树脂作为叶片的主要材料。
在将环氧树脂导入风电叶片时,应注意采用真空导入的工艺,以保证树脂完全填充叶片内部的空隙,确保叶片的质量和性能。
随着风力发电技术的不断发展,对风电叶片的要求也越来越高。
为了满足这一需求,研究人员不断探索新的制造工艺和材料,以提高风电叶片的性能和可靠性。
本文旨在探讨风电叶片制造中真空导入环氧树脂的标准,旨在为风力发电行业提供指导,并为未来的研究提供借鉴。
1.2 研究目的本文旨在探讨风电叶片用真空导入环氧树脂的标准,旨在为风电行业提供具体、可操作的指导,确保风电叶片的质量和安全性。
具体研究目的包括:1. 探讨真空导入环氧树脂的工艺流程,确定最佳操作方法;2. 分析风电叶片表面处理要求,确保环氧树脂的附着力和耐久性;3. 研究环氧树脂固化条件,找到最佳的固化参数;4. 制定真空导入环氧树脂的质量标准,为质量监控提供依据;5. 提出风电叶片使用中的注意事项,帮助企业在生产和维护过程中避免问题发生。
通过对以上研究目的的实现,本文旨在强调环氧树脂真空导入对风电叶片的重要性,并为未来研究提供指导方向。
几种大型风力发电叶片用环氧树脂复合材料的对比分析
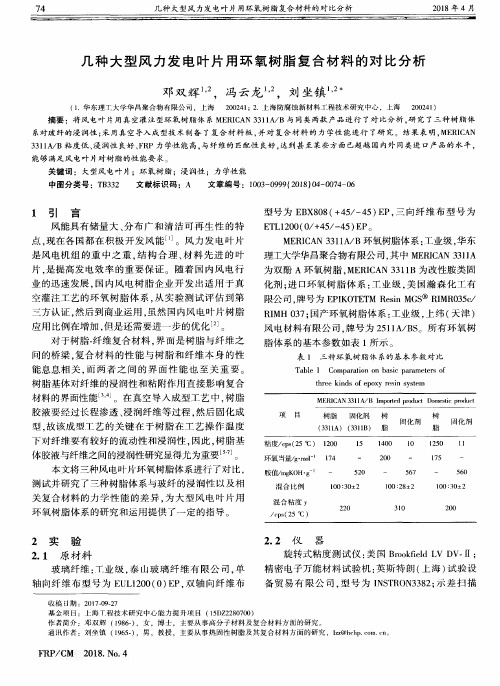
树脂 固 齐
同 化 剂
同化 剂
( 331IA ) (33 1 1B ) 脂
脂
2 实 验 2.1 原 材 料
玻璃 纤 维 :1 业 级 ,泰 山玻 璃 纤 维 有 限公 司 ,单 轴 向纤 维 布 型号 为 EULI200(0)EP,双轴 向纤 维 布
2.2 仪 器 旋 转式 粘度 测 试 仪 :美 国 Brookf ield LV DV.Ⅱ;
型号 为 EBX808(+45/一45)EP,三 向纤 维 布 型 号 为 ETL1200(0/+45/一45)EP。
MERICAN 331 1A/B环 氧树脂体 系 :1二业级 ,华 东 理工大学华昌聚合 物有 限公 司,其 中 MERICAN 3311A 为双 酚 A环 氧树 脂 ,MERICAN 3311B为改性 胺类 固 化剂 ;进 口环 氧树 脂 体 系 :工业 级 。美 国瀚 森 化工 有 限公 司 .牌 号为 EPIKOTETM Resin MGS ̄RIMR035c/ RIMH 037:国产 环 氧树脂 体 系 :工 业级 ,上 纬 (天 津 ) 风 电材料 有 限公 司 。牌 号为 251 1A/BS。所 有 环 氧树 脂体 系 的基本 参数 如表 1所 示 。
精 密 电子万 能材 料 试 验机 :英 斯 特 朗 (上 海 )试 验 设 备 贸 易 有 限 公 司 ,型 号 为 INSTRON3382;示 差 扫 描
收稿 日期 : 2017.O9.27 基金 项 目: 上 海 程 技 术 研 究 中心 能 力 提 升 项 目 (15DZ2280700) 作 者 简介 : 邛双辉 (1986一),女 ,博士 ,主要从事岛分子材料及复合材料方面的研究 。 通 讯 作 者 : 刘 坐 镇 (1965一),男 ,教 授 ,主 要 从 事 热 同 性 树 脂 及 其 复 合 材料 方 面 的研 究 ,Izz@hchp.COll1.Ci3。
风力发电机叶片用环氧乙烯基酯树脂
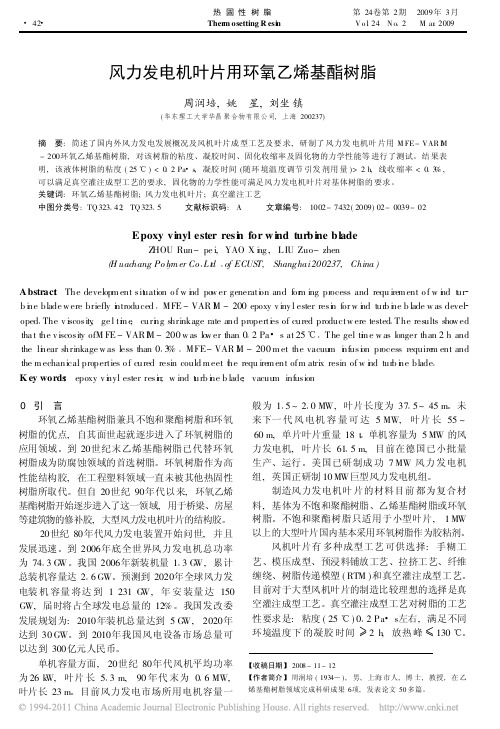
脂线收缩率的测定, 取一定量的树脂 ( 150~ 300 g) 加入 MEKP并搅匀后倒入长 1 000 mm, 30 mm的 半圆柱钢模具中, 待完全固化 (需放置 7~ 14 d) 后 测量其线收缩率。
1 1 1 原材料 主要原材料: 甲基丙烯酸、 E - 51环氧树脂和
苯乙烯均为市 售工业品; 扩链 剂富马酸双酯 为自 制; 阻聚剂对苯二酚、叔丁基对苯二酚和催化剂季 铵盐为市售工业品。 1 1 2 合成工艺
20世纪 80年代风力发电装置开始问世, 并且 发展迅速。到 2006年底全世界风力发电机总功率 为 74 3 GW。我国 2006年新装机量 1 3 GW, 累计 总装机容量达 2 6 GW。预测到 2020年全球风力发 电装 机 容量 将达 到 1 231 GW, 年 安 装量 达 150 GW, 届时将占全球发电总量的 12% 。我国发改委 发展规划为: 2010年装机总量达到 5 GW, 2020年 达到 30 GW。到 2010年我国风电设备市场总量可 以达到 300亿元人民币。
制造风力发电机叶 片的材料目前 都为复合材 料, 基体为不饱和聚酯树脂、乙烯基酯树脂或环氧 树脂。不饱和聚酯树脂只适用于小型叶片, 1 MW 以上的大型叶片国内基本采用环氧树脂作为胶粘剂。
风电叶片手糊成型环氧树脂体系的研究

风电叶片手糊成型环氧树脂体系的研究王萍;李文可;刘鲜红【摘要】采用树脂搭配系列固化剂的策略,开发出工艺窗口期宽泛的覆盖15~300min的多元化手糊环氧树脂体系.通过采用不同促进剂促进胺类固化剂获得差异化的可操作时间,同时对环氧树脂的分子结构进行改性,获得了强度和柔韧性满足要求的手糊环氧树脂产品DQ220E以及配套的DQ221H~DQ224H固化剂体系.该体系的工艺性能、力学性能、复合材料性能测试结果表明,各项指标满足风电叶片材料的要求.【期刊名称】《天津科技》【年(卷),期】2019(046)007【总页数】5页(P50-53,56)【关键词】多元化;手糊成型;环氧树脂;系统测试【作者】王萍;李文可;刘鲜红【作者单位】四川东树新材料有限公司四川德阳618000;四川东树新材料有限公司四川德阳618000;东方电气(天津)风电叶片工程有限公司天津300480【正文语种】中文【中图分类】TM3150 引言作为风力发电机组的重要组成部分,风电叶片主要用纤维增强环氧树脂复合材料制成。
环氧树脂以其优异的性能成为风电叶片最常用的基体树脂,目前大型风电叶片的制造主要采用真空灌注成型工艺(VARTM),各组件成型后需要进行粘接及补强,补强通常采用手糊成型工艺。
因此,手糊成型工艺是关键而重要的工序,国内外的研究机构及厂家对风电叶片手糊成型环氧树脂体系进行了深入研究。
1 实验部分1.1 仪器与试剂1.1.1 仪器流变仪:英国马尔文Bohlin CVO;拉力试验机:日本Shimadzu ACIC-100KN;差示扫描量热仪(DSC):德国Netzsch 200F3;真空干燥箱:上海精宏;邵氏硬度计:LX-D指针邵氏硬度计。
1.1.2 试剂DQ220E环氧树脂、DQ221H、DQ222H、DQ223H和DQ224H环氧固化剂:工业级,四川东树新材料有限公司。
进口环氧树脂:工业级。
1.2 固化机理手糊环氧树脂体系为树脂与胺类固化剂的混合体系,其固化机理为环氧树脂的环氧基与胺类固化剂的氨基反应。
关于风电叶片真空灌注成型工艺质量问题研究
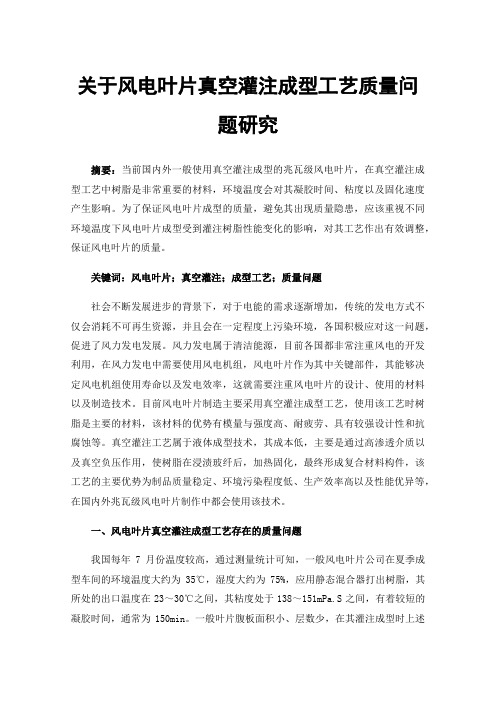
关于风电叶片真空灌注成型工艺质量问题研究摘要:当前国内外一般使用真空灌注成型的兆瓦级风电叶片,在真空灌注成型工艺中树脂是非常重要的材料,环境温度会对其凝胶时间、粘度以及固化速度产生影响。
为了保证风电叶片成型的质量,避免其出现质量隐患,应该重视不同环境温度下风电叶片成型受到灌注树脂性能变化的影响,对其工艺作出有效调整,保证风电叶片的质量。
关键词:风电叶片;真空灌注;成型工艺;质量问题社会不断发展进步的背景下,对于电能的需求逐渐增加,传统的发电方式不仅会消耗不可再生资源,并且会在一定程度上污染环境,各国积极应对这一问题,促进了风力发电发展。
风力发电属于清洁能源,目前各国都非常注重风电的开发利用,在风力发电中需要使用风电机组,风电叶片作为其中关键部件,其能够决定风电机组使用寿命以及发电效率,这就需要注重风电叶片的设计、使用的材料以及制造技术。
目前风电叶片制造主要采用真空灌注成型工艺,使用该工艺时树脂是主要的材料,该材料的优势有模量与强度高、耐疲劳、具有较强设计性和抗腐蚀等。
真空灌注工艺属于液体成型技术,其成本低,主要是通过高渗透介质以及真空负压作用,使树脂在浸渍玻纤后,加热固化,最终形成复合材料构件,该工艺的主要优势为制品质量稳定、环境污染程度低、生产效率高以及性能优异等,在国内外兆瓦级风电叶片制作中都会使用该技术。
一、风电叶片真空灌注成型工艺存在的质量问题我国每年7月份温度较高,通过测量统计可知,一般风电叶片公司在夏季成型车间的环境温度大约为35℃,湿度大约为75%,应用静态混合器打出树脂,其所处的出口温度在23~30℃之间,其粘度处于138~151mPa.S之间,有着较短的凝胶时间,通常为150min。
一般叶片腹板面积小、层数少,在其灌注成型时上述因素不会产生较大影响,而叶片的主梁以及壳体具有较大面积以及较多层数,上述因素会在较大程度上影响其灌注成型情况,应该结合实际生产情况来调整部分工艺。
下文将针对2.5MW风电叶片在30~45℃的高温环境下与10~20℃低温环境下,其叶片主梁以及壳体在灌注成型中经常出现的质量问题进行分析。
风机叶片树脂
风机叶片树脂
【原创版】
目录
1.风机叶片树脂的概述
2.风机叶片树脂的性能特点
3.风机叶片树脂的应用领域
4.风机叶片树脂的发展前景
正文
一、风机叶片树脂的概述
风机叶片树脂,又称为风力发电机叶片材料,是一种高性能的复合材料。
它主要用于风力发电机的叶片制造,具有轻质、高强、耐磨损、耐腐蚀等特点。
风机叶片树脂的性能直接影响到风力发电机的效率和稳定性,因此,选择合适的风机叶片树脂至关重要。
二、风机叶片树脂的性能特点
1.轻质:风机叶片树脂具有较低的密度,可以减轻整个风力发电机的重量,提高发电效率。
2.高强度:风机叶片树脂具有较高的拉伸强度和刚度,可以保证叶片在高速旋转过程中不易变形,提高使用寿命。
3.耐磨损:风机叶片树脂具有良好的耐磨性能,可以降低叶片在运行过程中因摩擦产生的损耗。
4.耐腐蚀:风机叶片树脂具有较强的耐腐蚀性,可以抵抗风力发电机工作环境中的盐雾、紫外线等腐蚀因素。
三、风机叶片树脂的应用领域
风机叶片树脂广泛应用于风力发电领域,尤其是海上风力发电。
由于
海上风力发电环境恶劣,对叶片材料的性能要求更高。
风机叶片树脂的优异性能使其成为海上风力发电机叶片的理想材料。
四、风机叶片树脂的发展前景
随着全球对可再生能源的需求不断增长,风力发电作为一种清洁、可再生的能源得到了广泛关注。
我国政府对风力发电产业的大力支持,使得风机叶片树脂在市场上的需求也不断增加。
风电环氧树脂
风电环氧树脂
风电环氧树脂是一种用于制造风力发电机叶片的特殊树脂。
它是由环氧树脂、填充剂、固化剂等材料混合而成的复合材料,具有优异的机械性能和耐久性。
在风力发电机叶片制造中,使用环氧树脂可以增强叶片的强度、刚度和耐久性,从而提高整个风力发电机的效率和寿命。
风电环氧树脂具有以下特点:
1.高强度:风电环氧树脂具有很高的强度和刚度,可以增强叶片的承载能力和抗风压能力,从而提高风力发电机的效率。
2.优良的耐久性:风力发电机经过长时间的使用和自然环境的影响,环氧树脂可以保持其优良的物理性能和化学性能,不易老化和开裂。
3.良好的成型性能:风电环氧树脂可以通过注塑、压模、层压等多种成型工艺进行加工,可以制造出各种形状和尺寸的叶片。
4.环保性:风电环氧树脂是一种绿色环保材料,不含有害物质,对环境没有污染。
目前,国内外许多企业都在积极研发和生产风电环氧树脂,以满足风力发电机叶片制造的需求。
未来,随着风力发电行业的不断发展和壮大,风电环氧树脂的市场前景将会越来越广阔。
- 1 -。
风力发电机叶片用环氧树脂胶粘剂的研究
风力发电机叶片用环氧树脂胶粘剂的研究近年来,全球能源危机不断升级导致能源价格不断上涨,温室气体排放增加,可再生能源的发展受到了越来越多的人的关注。
风力发电技术是可再生能源的主要开发技术之一。
然而,由于风力发电机叶片结构的复杂性,构型高度依赖外界环境,风速、风向极其不稳定,使受力设计和结构强度设计面临着很大的挑战。
为此,研究者百般尝试,以期解决叶片的结构问题以实现更好的可靠性和稳定性。
环氧树脂是结构胶粘剂的重要类型,主要用于风力发电机叶片内部结构的粘接补强。
由于其均匀的流动性,能够很好地使叶片的结构元件保持紧密而又均匀的拉伸,确保叶片在其受力时保持稳定。
环氧树脂也具有耐久、快速、抗震性能强等特点,使其具有广泛应用于风力发电机叶片结构的前景。
环氧树脂胶粘剂的实验表明,该材料具有良好的粘接性能,能够很好地将叶片的结构元件粘接起来,使单个叶片能够耐受高精度应力,其缝合强度较高,抗拉剪抗震能力也较强,耐温性能也更强。
此外,环氧树脂胶粘剂同样具有过渡性,它可以把处于不同温度状态的部件结合在一起,同时保持粘接部分均匀,确保结构性能稳定可靠。
因此,环氧树脂胶粘剂对于风力发电机叶片结构设计具有十分重要的意义,它不仅可以更好地将叶片的结构件粘接起来,而且能够增强叶片的稳定性,进一步提高风力发电机的可靠性和效率。
然而,尽管环氧树脂胶粘剂可以满足风力发电机叶片的结构需求,但其使用仍存在一些缺陷,其中最主要的是高昂的成本。
环氧树脂胶粘剂价格较高,对于廉价的发电机结构,它的使用可能会提高整体成本。
因此,为了进一步降低成本,研究者不断探索可以替代环氧树脂胶粘剂的其他胶水,以满足风力发电机叶片结构安全性和经济性的要求。
总之,环氧树脂胶粘剂可以有效地满足风力发电机叶片结构的安全性和经济性要求,为进一步完善发电机结构设计提供了重要参考。
未来,相关研究者将继续尝试把发电机叶片的结构设计推向更高水平,以满足不断变化的能源需求。
风电叶片用环氧树脂的研究
风电叶片用环氧树脂的研究陈诚杜明兵孙富安何明阳陈群(江苏工业学院江苏省精细石油化工重点实验室,常州213164)摘要:以BPA环氧树脂、BPF环氧树脂为基体树脂,1,4-丁二醇二缩水甘油醚为稀释剂,配制出可用于风电叶片的复合型环氧树脂。
考察了不同的原料配比与力学性能的关系,并采用Statistica6·0统计软件对配方进行优化。
研究结果表明:当BPA树脂:稀释剂=13·5(质量比),BPA树脂:BPF树脂=1·6(质量比),树脂固化物冲击强度为88·00KJ·m-2,拉伸强度为68·52MPa,弯曲强度为88·20MPa,其性能接近进口树脂。
关键词:复合材料,环氧树脂,风电叶片,力学性能风力发电是重要的洁净能源,其开发利用受到世界各国越来越多的重视。
当今,风力发电向大功率、长叶片方向发展,更加凸显出叶片材料的重要性。
纤维增强环氧树脂复合材料和真空辅助浸渗技术以其效率高、成本低、质量好的优点,成为生产大型叶片时材料和工艺的主流方向。
真空辅助浸渗技术制备风力发电转子叶片的关键是优选浸渗用的基体树脂,特别要保证树脂的最佳黏度及其流动特殊性[1-2]。
目前国外用于真空辅助浸渗技术的树脂主要有Shell公司、3M公司、HEXION公司、荷兰DSM高等复合材料中心等企业的产品[3-6]。
国内风电叶片制造业的环氧树脂基本依靠进口,这在很大程度上制约了风电业在国内的发展。
本文选用BPA环氧树脂、BPF环氧树脂和活性稀释剂的混合物为基体树脂,以RIMH237为固化剂,在降低树脂黏度的同时保持较好的力学性能,研制出满足真空辅助浸渗工艺的风电叶片用复合型环氧树脂。
1实验部分1·1原料双酚A环氧树脂1460,环氧值0·52,蓝星材料无锡树脂厂;双酚F环氧树脂,自制,环氧值0·59;黏度,1100mPa·s;环氧稀释剂1,4-丁二醇二缩水甘油醚,自制,环氧值0·69。
- 1、下载文档前请自行甄别文档内容的完整性,平台不提供额外的编辑、内容补充、找答案等附加服务。
- 2、"仅部分预览"的文档,不可在线预览部分如存在完整性等问题,可反馈申请退款(可完整预览的文档不适用该条件!)。
- 3、如文档侵犯您的权益,请联系客服反馈,我们会尽快为您处理(人工客服工作时间:9:00-18:30)。
风电叶片灌注树脂固化性能的影响刘魁1,杨孚标2,冯学斌1,雷志敏1,杜雷1,梁自禄1(1.时代新材料科技股份有限公司,湖南株洲412007;2.国防科学技术大学航天与材料工程学院,湖南长沙410073)摘要:采用不同固化条件固化环氧浇铸体,对其进行玻璃化转变温度和静力学性能测试,研究不同固化条件对环氧固化物性能的影响。
测试结果显示Tg存在最佳值。
通过测试结果可知环氧树脂在40℃10h预固化后再经过70℃3h后固化测得的拉伸强度、弯曲强度和压缩强度分别较40℃10h固化提高了11.64%、14.72%和20.61%,可以达到更好的固化性能。
通过研究环氧浇铸体拉伸和弯曲载荷-位移曲线,发现固化后的环氧树脂经过更高温度的后固化可以有效降低体系内的应力,获得更好更均匀的性能。
关键词:环氧树脂;固化工艺;力学性能;玻璃化转变温度Study on the curing properties of wind blade epoxide resin LIU Kui1,YANG Fubiao2,FENG Xuebin1,LEI Zhimin1,DU Lei1,LIANG Zilu1(1.Zhuzhou Times New Materials Science and Technology Co,Ltd,Zhuzhou 412007,China;2.NationalUniv. of Defense Technology ,College of Aerospace and Material Engineering , Changsha410073,China)Abstract: Cured the epoxide resin castings under different processes, tested the static mechanical properties and glass transition temperatures to study the influence on epoxide resin casting properties by different curing processes. The test results show that the best value of Tg is existing. The tensile strength, flexural strength and compressive strength of the epoxide resin casting under the process of 40℃ 10h pre-curing and 70℃3h post-curing are increased by 11.64%, 14.72% and 20.61% respectively comparing with the one under the curing process of 40℃10h. Obviously, the former one has better properties. It is found that the internal stress of epoxide resin casting can be effective reduced by post-curing process of a higher temperature, and this process also bring us better and more homogeneous epoxide resin properties.Keywords:epoxide resin, curing process, mechanical property, glass transition temperature1概述随着风电叶片的快速发展,环氧树脂大量的应用于叶片的生产中,环氧树脂作为叶片成型的主要基体材料能提供良好的力学性能[1]。
固化温度对固化物的性能具有重要影响[2],同一种树脂在不同固化条件下固化可能性能相差极大,因此需要寻求最佳固化制度[3]。
固化不好的环氧树脂存在交联密度不均一、内应力大、质脆和抗冲击性差等缺点,在很大程度上限制了它在风电叶片上的应用。
固化反应属于化学反应,受固化温度影响很大,温度升高反应速度加快,但固化温度过高常使固化物性能下降,所以存在固化温度上限,必须选择合适的固化速度和固化物性能折中的温度作为合适的固化温度。
按固化温度可以把固化剂分为四类:1)在室温下固化的固化剂;2)在室温至50℃固化的室温固化剂;3)在50℃-100℃的中温固化剂;4)在100℃以上的高温固化剂[4]。
为了更好的保证环氧灌注树脂在叶片作者简介:刘魁,男,硕士,高级工艺师,主要从事复合材料风力发电叶片的工艺研究上的应用,通过对环氧树脂在进行室温固化、中温固化、室温预固化再中温后固化以及中温预固化再更高温度后固化等条件下的玻璃化转变温度和力学性能测试的数据,研究环氧树脂在不同固化条件下其性能的变化。
2实验部分2.1材料与仪器双酚A型低粘度环氧树脂(环氧值0.54-0.58)与多元胺为主体的固化剂,按照100:30的质量份配比。
万能拉力机:美特斯CMT5105差示扫描量热议(DSC):瑞士梅特勒DSC821e2.2实验方法2.2.1树脂体系玻璃化转变温度(Tg)测试环氧树脂和固化剂按照比例进行混配,按设定好的固化程序进行固化。
采用梅特勒差示扫描量热仪对固化好的样品进行Tg分析。
测试玻璃化转变温度以20℃/min进行升温,氮气流量为50ml/min。
2.2.2树脂浇铸体制备及性能测试将环氧树脂和组装好的模具放置烘箱中40℃放置1h,对环氧树脂和固化剂按比例配好,搅拌均匀后放入真空脱泡箱内当真空度达到-0.1Mpa后脱泡15min,待脱泡完毕后缓慢放气,将胶液引流注入浇铸体模具中,然后再将浇铸体模具放入真空脱泡箱脱泡15min,将脱好泡的浇铸体放入烘箱中按设定的加热程序进行加热固化,固化方案如表1所示。
制备好的试样,在万能拉力机上按国标GB/T2567-2008测试其拉伸、弯曲和压缩性能。
表1 固化实验方案设计固化程序室温固化中温固化室温预固化中温后固化中温预固化中温后固化实验温度设置40℃10h 70℃3h 40℃10h+70℃3h70℃3h+80℃2h3结果与讨论3.1不同固化工艺对Tg的影响Tg是链段从冻结到运动的转变温度,而链段运动是通过主链的单键内旋转而实现的,高分子链段的柔顺性越好其Tg越低。
另外分子链端浓度对Tg也有影响,链端比分子链的中间段受到的制约要小些,运动比链中段要容易,所以分子链段越小链端浓度就越高其Tg就越低[5]。
表2 不同固化制度下的Tg温度固化条件40℃10h 40℃10h70℃3h70℃3h70℃3h80℃2h玻璃化温度52.04℃79.38℃79.69℃69.46℃不同固化制度下的Tg温度如表2所示,40℃10h固化其分子主要以线性大分子存在,但大分子没有充分交联成网络结构且分子的分子量不高,使得链端浓度较高,所以玻璃化温度较低。
再经过70℃3h后固化测得样品的Tg明显升高,说明在后固化中体系内自由体积膨胀,大分子和体系内的活性基团进一步反应,提高分子的交联度,这与直接在70℃3h下固化时的Tg值相差不多。
说明40℃10h固化的样品在70℃3h 后固化中固化较完全。
但70℃3h固化后再经过80℃2h的后固化Tg值明显降低。
说明环氧树脂固化工艺存在最佳固化条件,当固化温度和固化时间超过最佳条件,其固化物的玻璃化转变温度会出现降低。
3.2不同固化条件对力学性能的影响不同固化条件下环氧树脂浇铸体的拉伸、弯曲载荷-位移曲线如图1-8所示,从图中拉伸和弯曲的载荷-位移曲线观察在初步固化反应结束后样件测试的载荷-位移曲线分散性较大,再进行较高温度的后固化其载荷-位移有很好的重合度,可以断定后固化可以使样件达到较好的力学均一性。
从拉伸载荷-位移曲线观察40℃10h样件直接断裂无屈服阶段,样条的断裂伸长率为6.58%,比其它几组条件数据值要低,说明此条件可能固化温度较低反应物只形成了分子量不高的大分子交联体,没有充分交联成网络结构。
图1 40℃10h拉伸载荷-位移曲线图2 40℃10h70℃3h拉伸载荷-位移曲线图3 70℃3h拉伸载荷-位移曲线图4 70℃3h80℃2h拉伸载荷-位移曲线图5 40℃10h弯曲载荷-位移曲线图6 40℃10h70℃3h弯曲载荷-位移曲线图7 70℃3h弯曲载荷-位移曲线图8 70℃3h80℃2h弯曲载荷-位移曲线对环氧浇铸体进行静力学性能测试,通过测试拉伸、弯曲、压缩的强度和模量比较4种固化条件下环氧固化物性能的变化,如表3。
表3 不同固化制度测得力学性能抗拉强度(Mpa) 62.20 69.44 68.01 65.98弹性模量(Mpa) 3148.92 3152.76 3060.06 2748.35最大载荷伸长率% 6.58 7.83 7.26 7.20弯曲强度(Mpa) 97.42 111.76 79.84 94.13弯曲模量(Mpa) 3305.16 3151.17 3013.18 2866.83压缩强度(Mpa) 73.16 88.24 83.31 81.46弹性模量(Mpa) 2367.30 2418.10 2370.91 2085.80 力学性能测试结果见表3。
表3中的数据是所测试数据的平均值,可以看出环氧固化体在40℃10h70℃3h的各项拉伸、弯曲和压缩的强度及模量综合数据是4组工艺条件下最优的。
本固化剂是脂肪族胺和芳香胺的混合物且脂肪胺占有主要成分。
在温度较低时固化,伯胺反应占有绝对优势且叔胺本身存在空间位阻效应使得反应体系难以充分形成体形交联。
在40℃10h固化完后再进行70℃3h后固化测得拉伸强度升高至69.44Mpa,在高温后固化中大分子链进一步交联,使得分子链之间交联在一起,提高体系的交联密度。
经过70℃3h后固化其抗拉强度、弯曲强度和压缩强度分别较40℃10h固化提高了11.64%、14.72%和20.61%。
本环氧固化剂是以多元胺为主体的固化剂,首先是伯胺的活泼氢与环氧反应本身生成仲胺,再进一步与环氧反应生成叔胺,最后形成交联的网络结构。
伯胺基、仲胺基易发生反应[4],叔胺具有催化机能由于空间位阻现象使得在固化温度较低时反应中一般是伯胺基优先与环氧基进行反应,形成带有支链较少的大分子,而叔胺则较难参与反应。
在70℃固化时,由于反应温度高,分子运动剧烈环氧基与伯胺基反应的优先程度降低,伯胺反应优先的情况下且高温下分子运动剧烈叔胺的空间位阻效应降低,链增长反应和分子间的交联反应同时进行,使得大分子迅速交联成体型网络结构。