用吸收法消除玻璃中气泡的经验
夹层玻璃清除气泡新技术

夹层玻璃清除气泡新技术近几年来,国家对建筑安全的要求越来越高。
建筑安全玻璃的使用范围也越来越广,夹层玻璃至今还是安全玻璃类别中安全性能最好的一种,没有任何一种安全玻璃能与其相比美。
它广泛的用于汽车、火车、建筑等。
{TodayHot}夹层玻璃的衍生产品,防弹玻璃更是广泛的应用于金融机构,给经营产业的安全性做出了巨大的贡献,但是在生产中也产生了很多废品,废品的在利用是许多企业十分头痛的事情,只有白白扔掉。
我单位经过十年来的研究,终于摸索出了解决夹层玻璃气泡的新方法,我们愿无偿与大家共同分享此项技术之成果,下面我们将此项技术作以全面详细的介绍,供广大玻璃业的同行们采用。
一、干法夹层玻璃1、干法夹层,有的采用浮法玻璃,有的采用钢化玻璃胶合而成的夹层玻璃,浮法夹层玻璃原片比较平整,生产成品率高,除了破损之外,一般没有气泡,胶合层发白等问题。
但是普通夹层玻璃强度比较低,施工中的破损率比较高,继尔许多装饰公司广泛采用了钢化夹层玻璃,解决了安装中的破损问题。
{HotTag}这种玻璃的强度提高了,可是因钢化玻璃在淬火中产生了变形,给生产夹层玻璃带来了难以想象的困难。
许多企业开始来加厚PVB膜解决钢化玻璃的不平整,可是在进釜的加工过程中,因玻璃边部受热面积大、升温比较快,玻璃的导热系数和PVB的导热系数不同,玻璃的边部首先与PVB膜粘合在一起,使夹层玻璃中间的气体难以排出,造成了大量废品,难以使用。
我们单位在几年前,因为此种原因,每年损失不下几十万元,夹层玻璃废品不下几千平方米。
因此我们苦下功夫,刻苦钻研,终于研究出用硅油化学喷涂的方法解决了以上问题。
二、干法热弯夹层玻璃干法热弯夹层玻璃主要用于汽车前风挡,以前生产工艺复杂,成本过高,预热预压这一段工艺绝不可少,使用起来套硅胶条,预热抽真空等十分麻烦,且成品率也不高,采用玻璃专用夹,把胶片和玻璃固定好,直接送入高压釜,即省了人工,又降低成本,成品率也有所提高,望大家参考应用。
玻璃的熔制过程

硅酸盐形成和玻璃形成
6. 含有着色剂和乳浊剂的配合料的加热反应-1
着色剂可能发生氧化还原变化,或者与其它组份生成化合物和 固熔体以及参加硅酸盐生成的反应。
铁的氧化物 Fe2O3+CO → 2FeO + CO2 Fe2O3 ←→ 2FeO + 0.5O2
Fe2O3 + 6HCl → 2FeCl3 +3H2O 锰的氧化物
从三价变为五价,在800℃和1200℃之间,绝大多数As在玻璃中以As2O5存在,
当温使度玻高璃于1液20沸0℃腾时,搅A拌s2O,5又鼓重泡新,分解利为用As玻和A璃s2对O3流放出氧气,物又由理五澄价清变到法
硅酸盐形成和玻璃形成
3. 三组份配合料的硅酸盐和玻璃形成
SiO2+Na2SO4+CaCO3配合料(通常称芒硝配合料)
Na2SO4分解比较困难,所以必须在有碳或其它还原剂存在时,才能加速反应。 SiO2+Na2SO4+CaCO3+C配合料加热发生的反应过程如下:
硅酸盐形成和玻璃形成
4. 四组份配合料的硅酸盐和玻璃形成
4MnO2 → 2Mn2O3 + O2 Mn2O7 → 2Mn2O3 + 2O2 Mn2O3 → 2MnO + 0.5O2
硅酸盐形成和玻璃形成
6. 含有着色剂和乳浊剂的配合料的加热反应-2 铜的氧化物
钴的氧化物 乳浊剂反应
硅酸盐形成和玻璃形成
7. 配合料组份在加热时的挥发
挥发性比较大的有硼酸、硼酸盐、氧化铅、 砷的化合物、氧化锑和氯化物等。碱和氧化 锌也具有显著的挥发率,氟化物和硒的挥发 率非常大。
之后,配合料基本熔化成为液相,过剩的石英颗粒 继续熔化于熔体中,液相不断扩大,直至最后全部 固相转化为玻璃相,成为含有大量气泡、不均匀的 透明玻璃液。
浅谈瓶罐玻璃气泡的成因及解决办法

浅谈玻璃瓶罐气泡的种类和解决方法四川天马玻璃有限公司田文忠瓶罐玻璃气泡里一般都有可见的气态夹杂物,是种常见缺陷。
气泡严重影响了产品的外观质量和机械强度。
如何解决气泡问题就显得非常重要了。
1 玻璃瓶罐气泡的种类和表现形式玻璃瓶罐中的气泡大小不一,直径分市从零点几毫米到几毫米,其形状也各异。
根据大小:气泡可分为灰泡(直径≤0.8mm/)和气泡(直径>0.8 mm)两种,根据形状:气泡可分为球状气泡+椭圆形气泡和线状气泡三种;根据气泡的表现形式可分为以下几种类型:(1)位于瓶外壁用指甲抠或用它物轻敲可破.称为薄皮气泡。
(2)散布一大片、数量多的单个小气泡,称为麻点。
(3) 用50倍放大镜下能看见并已形成了空心的麻点,为“睁眼麻点:更小一些,还未形成空心的席点,为“闭跟”麻点(4)瓶壁内几个单独的大气泡。
(5)大气泡夹杂了小麻点(6)气泡集中在l0~20mm宽的范围内,从瓶口至瓶底,灰白色扁平椭圆状的一串,气泡较大,称为串泡。
2 气泡产生的原因及解决措施玻璃液中的气泡大多由配合料熔化时盐类分解产生的,少数由外来夹杂物在高温下氧化和玻璃液入耐火材料缝隙使其中空气排出而产生。
消除气泡方式一:是通过澄清过程中大气泡的逸出(同时带出些小气泡)二:小气泡在冷却过程中溶解来实现的。
因此,气泡缺陷主要是因为澄清剂用量不足、澄清时玻璃液粘度过大和外来夹杂物氧化而产生的,成形过程中也会产生为数不多的气泡。
按工艺流程,气泡产生原因可分为以下三个方面:2.原料及配合料方面澄清剂常用r玻璃的澄清剂有.r;砒、硝酸钠、萤石、幸(化锑等白砒一般与硝酸含Hj.其瞪清机理内砒用鼙一般为配合奉{的0.2 %~0 6 .硝酸钠的引入为白砒的4— 8倍刚为澄清{}'J用星偏!p引起的气泡一般较小,气泡数因澄清剂用量偏少程度异氧化锑的澄清作用与白砒类似,但SbzOs转化 Sb203的温度略低、因此仅适于作为培制软质玻璃的澄清剂萤石作为澄清剂.主要是通过降低玻璃的高温粘度而达到澄清效果.其用量一般按给配合料引八0、5 %的氟来计葬一原料水分过太原料中水分过大是由砂子带入的:为使配合料水分控制在3%~5%.砂子水分应控制在6%~ 8%。
浮法玻璃气泡产生的原因及解决方法

2021.02.022021.02.02欧阳索引创编 浮法玻璃气泡产生的及解决方法欧阳家百(2021.03.07)1 •气泡的分类通过生产实践,浮法玻璃气泡大概可分为两大类:即熔化澄 清气泡和非熔化澄清气泡(1 )熔化澄清气泡:即因原料.熔化、燃料.燃烧系统不稳定造成 的气泡;(2 )非熔化澄清气泡即因砖材质量、硝类冷凝物及冷却设备引起 的气泡。
2•浮法玻璃气泡产生的及解决方法(1) 原料泡配合料带人的空气形成气泡一生料团(片}或超细粉料团(片)、芒硝大颗粒.碎玻璃夹带进人的空气;二氧化碳一配合料 熔化时碳酸盐的分解产物;水汽一加进配合料中的水;氮气一空气 被夹带进配合料并被加人熔窑,氧气在玻璃液中的溶解度较大, 留下的大部分气体为氮气。
气体分可溶与不可溶气体不可溶气体 有氮气、二氧化碳.氢气。
可溶气体有氧气、二氧化硫、水。
(2) 熔化泡泡界线外熔窑周围的液⑥线:小气泡来自熔窑高温区域;因为 气泡被玻璃吸收或溶解的过程和时间有关,玻璃的温度越高,气 体被玻璃吸收的越多,使气泡变得更小。
0.2mm 直径以下的气泡欧阳索引创编2021.02.022021.02.02欧阳索引创编 —般来自熔化部。
直径0.5mm 的气泡一般在卡脖部位产生。
再 大一些的气泡则来自于冷却部或流道。
原因:玻璃液廁线周围有 耐火材料析出的玻璃相,长时间滞留在液⑥线耐火材料周围。
此 部位外部是池壁冷却风,冷却风使池壁砖缝内侧温度更低•易集 聚芒硝,在温度、熔窑压力和液直的变化下,集聚的芒硝进人玻 璃液,产生气泡。
池壁的重型保温、池壁砖的缝隙使玻璃液渗 出,逬入池壁保温层,致使气体沿池壁缝隙进人窑内玻璃液,产 生气抱。
解决方法稳定熔窑压力、稳定玻璃液对流.堵塞池壁缝 隙、稳定末对小炉火焰。
(3) 澄清泡微气泡一般指直径小于0.2mm 的气泡。
微气泡主要产生在 澄清部.:澄清温度过低,末对小炉火焰过强或过弱。
澄清区火焰 气氛还原性,燃油雾化不良,油中含有较多的颗粒碳,泡界线不 稳,火焰不稳定。
光学基础知识

光学加工基础知识§1 光学玻璃基本知识一. 基本分类和概念光学材料分类:光学玻璃、光学晶体、光学塑料三类。
玻璃的定义:不论化学成分和固化温度范围如何,一切由熔体过冷却所得的无定形体,由于粘度逐渐增加而具有固体的机械性质的,均称为玻璃。
光学玻璃分为冕牌K 和火石F 两大类,火石玻璃比冕牌玻璃具有较大的折射率nd 和较小的色散系数vd 。
二. 光学玻璃熔制过程将配合料经过高温加热,形成均匀的,高品质的,并符合成型要求的玻璃液的过程,称玻璃的熔制。
玻璃的熔制,是玻璃生产中很重要的环节.,玻璃的许多缺陷都是在熔制过程中造成的, 玻璃的产量、质量、生产成本、动力消耗、熔炉寿命等都与玻璃的熔制有密切关系。
混合料加热过程发生的变化有:物理过程配合料的加热,吸附水的蒸发,单组分的熔融,个别组分挥发.某些组分的多晶转变。
化学过程---- 固相反应,盐的分解,水化物分解,结晶水的排除,组分间的作用反应及硅酸盐的形成。
物理化学过程------ 低共熔物的组分和生成物间相互溶解,玻璃与炉气介质,耐火材料相互作用等。
上述这些现象的发生过程与温度和配合料的组成性质有关. 对于玻璃熔制的过程,由于在高温下的反应很复杂,尚待充分了解,但大致可分为以下几个阶段。
1. 加料过程硅酸盐的形成2. 熔化过程玻璃形成3. 澄清过程-----消除气泡4. 均化过程------消除条纹5. 降温过程——调节粘度6. 出料成型过程总之,玻璃熔制的每个阶段各有其特点,同时,它们又是彼此互相密切联系和相互影响的•在实际熔制中,常常是同时或交错进行的,这主要取决于熔制的工艺制度和玻璃窑炉结构特点。
三. 玻璃材料性能1 .折射率nd、色散系数vd根据折射率和色散系数与标准数值的允许差值,光学玻璃可以分为五类2. 光学均匀性光学均匀性指同一块玻璃中折射率的渐变。
玻璃直径或边长不大于150mm,用鉴别率比值法玻璃分类如表1-2。
1类或2类还应测星点。
控制熔化工艺消除浮法玻璃气泡

控制熔化工艺消除浮法玻璃气泡气泡的种类在实际生产过程中所产生的气泡不外乎是物理气泡与化学气泡,即由于物料中的游离水份与化学反应所产生的.而能在产品中残存的气泡来源,一是未澄清完全所留存在玻璃液中的一次气泡,二是因"重沸"而产生的二次气泡.工艺控制的理论依据①消除一次气泡的理论依据众所周知,对于同一料方的配料来说,玻璃液的澄清过程受诸多因素的影响:能产生澄清气体的原料成份能否集中分解并释放出澄清气体;熔体中的溶解气体能否快速析出;澄清流起点处含气泡的深层液流能否顺利上行排泡;以及澄清温度,时间,外界压力等.与此同时,已形成的极微小的来不及上浮逸出的气泡能否重新溶于玻璃液而消失.浮法玻璃生产通常使用的澄清剂为芒硝,芒硝在物料熔化过程中有如下的一些性质:芒硝的热还原反应:①Na2SO4+2C→Na2S+2CO2↑(400℃开始,500℃反应激烈)②Na2S+Na2SO4+2SiO2→2Na2SiO3+SO2↑+S↑(865℃)③2Na2SO4→2Na2O+2SO2↑+O2↑(1200℃~~1300℃)④2Na2SO4+2SiO2+C→2Na2SiO3+CO2↑+2SO2↑(720℃~~1000℃)首先,在正常状态下,温度越高,反应越剧烈,单位时间内放出的气体愈多.其次,芒硝在高温时分解放出SO2、CO2,芒硝成份中的SO3溶于玻璃液,而其还原产物SO2则几乎完全不溶于玻璃液,同时在熔化温度范围内SO2的溶解度随氧化气氛的增强而增大.基于上述芒硝的性质,如果我们在生产操作中能使大部分芒硝的热还原反应集中于某一区域,反应产物气体SO2、CO2就会集中地大量析出,这样,在气泡中气体分压及熔体表面张力的作用下,不仅能使熔体中的多种气体加速扩散到富集SO2的泡中,使气泡迅速长大,使气泡在增大了的浮力作用下,加快上行并拉动下层熔体快速上行,使深层气泡亦上升至玻璃液表面.操作者若同时控制上述区域的温度及环境压力,使上浮至液面表层的气泡快速逃逸,气泡的上浮澄清过程将圆满完成.②二次气泡产生的机理对于二次气泡产生的机理及生产实例已有大量的文献与资料报道,本文强调一点,即避免已溶入玻璃液的气体成份重新析出或反应生成气体而析出,在正常的生产情况下,外界因素造成玻璃液被重新加热或气氛条件突变而放出气体的情况是不会出现的,只有熔化部的澄清回流(或者说环流)及冷却部的生产回流才能造成玻璃液的重新被加热或故障因素造成气氛突变,使熔体内物质重新发生反应而放出气体.实际生产中的控制根据上述分析,我们在实际生产操作中做了如下调整:对于熔化工艺前段的控制,打破了以往的传统,避免芒硝在熔化初期过早大量分解,使后期芒硝澄清作用不足产生气泡.温度制度及风油比的调整见表从表不难看出:主要化料区的火焰气氛由调整前的还原性改为氧化性,而调整前热点处由氧化性改为还原性,这就符合了完全澄清所要求的化料区氧化气氛,抑制了芒硝分解.仅使少部分芒硝参加助熔作用,大部分以SO3形式溶于玻璃液中,热点区的还原气氛及高温降低了SO3的溶解度,使含有大量SO3的熔体进入热点区时,由于熔化所处的还原气氛及温度的影响,增大了SO3溶解的饱和倾向,热点区的高温又使SO3的分解倾向加大,最终使SO3在热点区域得以快速分离并分解,从而实现了相对集中放出澄清气体SO2及CO2的目的.由于放出的SO2、CO2气体几乎不溶于玻璃液,这样就使气体的成核,长大,浮力增加及上升得以快速实现.而适当提高的热点温度及上述释放出的大量SO2、CO2气体更容易使热点处深层含气泡的熔体上升,得以澄清.以SO2为主的气泡在合并,上升过程中由于泡内各种气体的分压平衡被连续破坏,就使溶解在熔体中的其他气体不断地渗析到这个气泡中,使熔体中的其他气体含量快速减少,配合气氛分段控制,对各小炉下废气抽力闸板的开度,即各小炉的排气量作了相应的理论计算和实际调整,按蓄热室热平衡表达式(如下)来控制,更完全地实现澄清的目的. 燃料流量&分烟道闸板开度助燃空气量&最大烟气温度一般情况下,对每个小炉来说,$值相对接近.而热点后区火焰气氛又变为氧化性,增大了SO2在玻璃液中的溶解度,使在热点区未分解的残余SO2重新溶解在玻璃液当中,微小的来不及上浮逸出的小气泡随温度的降低亦重新溶于玻璃液当中,彻底实现澄清的目的.其次,由于化料区温度,热点温度及未对小炉温度适当提高,不仅增大了化料速度,使热点前移,相应地增大了澄清面积,从而增加了澄清时间,同时也增加了玻璃液的澄清温度,有利于一次气泡的澄清.与此同时,上述调整使热点前移,拉长了热点至熔化部末端的距离(由于目前的熔窑大都采用了窄长脖与深水水包,使熔化部的澄清环流与冷却部的生产环流有效地被分开,避免了冷却部的环流返回到熔化部中去),有效地减小此段玻璃液沿流向在单位长度内的温度梯度,降低了澄清环流的强度.由于熔化部澄清环流强度的降低,使进入卡脖的玻璃液流量随之降低,从而使冷却部的生产环流亦有所降低.上述两大环流强度的降低,有效地使返向流减弱,避免了返向流中的"凉"玻璃液返回高温区被重新加热,导致气体溶解度等的一系列变化而释放出"二次"气体,形成气泡.这一点,从池底温度的变化可以说明两大环流的减弱.各部池底温度见表经过上述一系列的调整,玻璃板中气泡尺寸及数量发生了较大的改观,数据见表'.玻璃实物等级由建筑级和加工级提高为以制镜级为主的优质浮法玻璃.结束语由于大规模浮法玻璃生产操作,不可能完全实现理想控制状态,但通过上述一系列的在线工艺控制手段,可以使芒硝充分发挥其澄清效能.同时,在熔化初期,芒硝与碳粉在一定气氛下反应而生成的过渡产物Na2S:对物料颗粒的浸润而加速物料熔化的作用,从而使整个熔化过程变短,其增加澄清时间的作用机理,即还原性硫澄清机理的在线应用有待进一步讨论。
用吸收法消除玻璃中气泡_百度文库.
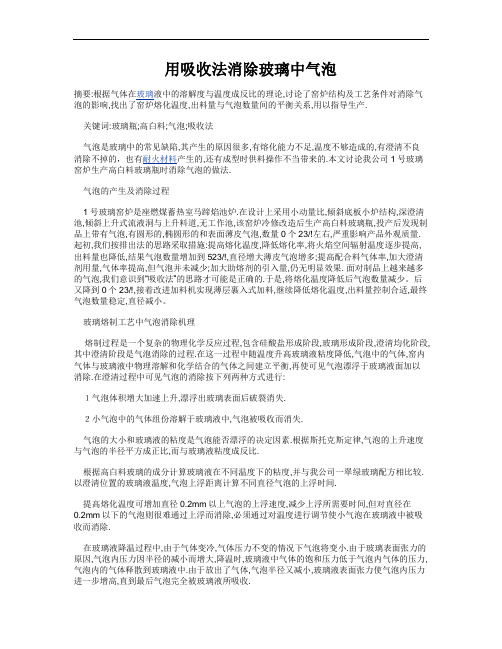
用吸收法消除玻璃中气泡摘要:根据气体在玻璃液中的溶解度与温度成反比的理论,讨论了窑炉结构及工艺条件对消除气泡的影响,找出了窑炉熔化温度,出料量与气泡数量间的平衡关系,用以指导生产.关键词:玻璃瓶;高白料;气泡;吸收法气泡是玻璃中的常见缺陷,其产生的原因很多,有熔化能力不足,温度不够造成的,有澄清不良消除不掉的,也有耐火材料产生的,还有成型时供料操作不当带来的.本文讨论我公司1号玻璃窑炉生产高白料玻璃瓶时消除气泡的做法.气泡的产生及消除过程1号玻璃窑炉是座燃煤蓄热室马蹄焰池炉.在设计上采用小动量比,倾斜底板小炉结构,深澄清池,倾斜上升式流液洞与上升料道,无工作池,该窑炉冷修改造后生产高白料玻璃瓶,投产后发现制品上带有气泡,有圆形的,椭圆形的和表面薄皮气泡,数量0个23/!左右,严重影响产品外观质量.起初,我们按排出法的思路采取措施:提高熔化温度,降低熔化率,将火焰空间辐射温度逐步提高,出料量也降低,结果气泡数量增加到523/!,直径增大薄皮气泡增多;提高配合料气体率,加大澄清剂用量,气体率提高,但气泡并未减少;加大助熔剂的引入量,仍无明显效果. 面对制品上越来越多的气泡,我们意识到“吸收法”的思路才可能是正确的.于是,将熔化温度降低后气泡数量减少。
后又降到0个23/!,接着改进加料机实现薄层裹入式加料,继续降低熔化温度,出料量控制合适,最终气泡数量稳定,直径减小。
玻璃熔制工艺中气泡消除机理熔制过程是一个复杂的物理化学反应过程,包含硅酸盐形成阶段,玻璃形成阶段,澄清均化阶段,其中澄清阶段是气泡消除的过程.在这一过程中随温度升高玻璃液粘度降低,气泡中的气体,窑内气体与玻璃液中物理溶解和化学结合的气体之间建立平衡,再使可见气泡漂浮于玻璃液面加以消除.在澄清过程中可见气泡的消除按下列两种方式进行:1气泡体积增大加速上升,漂浮出玻璃表面后破裂消失.2小气泡中的气体组份溶解于玻璃液中,气泡被吸收而消失.气泡的大小和玻璃液的粘度是气泡能否漂浮的决定因素.根据斯托克斯定律,气泡的上升速度与气泡的半径平方成正比,而与玻璃液粘度成反比.根据高白料玻璃的成分计算玻璃液在不同温度下的粘度,并与我公司一翠绿玻璃配方相比较.以澄清位置的玻璃液温度,气泡上浮距离计算不同直径气泡的上浮时间.提高熔化温度可增加直径0.2mm以上气泡的上浮速度,减少上浮所需要时间,但对直径在0.2mm以下的气泡则很难通过上浮而消除,必须通过对温度进行调节使小气泡在玻璃液中被吸收而消除.在玻璃液降温过程中,由于气体变冷,气体压力不变的情况下气泡将变小.由于玻璃表面张力的原因,气泡内压力因半径的减小而增大,降温时,玻璃液中气体的饱和压力低于气泡内气体的压力,气泡内的气体释散到玻璃液中.由于放出了气体,气泡半径又减小,玻璃液表面张力使气泡内压力进一步增高,直到最后气泡完全被玻璃液所吸收.玻璃液在澄清过程中,大气泡排出与小气泡吸收这两个阶段是必不可少的,前者要求必要的温度和持续时间,后者需要一定的温降梯度,如果这些条件有一项达不到就会使制品带上气泡.窑炉结构及所给出的工艺条件对消除气泡的影响1.窑炉结构该窑炉结构有两个特点:一是大倾角小动量比的小炉结构,二是下沉的深澄清池结构.这种结构使火焰有较高的速度和刚性,火焰紧贴玻璃液面,对料堆有一个向前的推力.据测量,当熔化温度不足,出料量偏大时,料堆移后,有的配合料还未完全熔化就到了澄清部,占用了澄清时间,使澄清不充分,本该排出的气泡留在了玻璃液中进入了冷却阶段.制品上直径0.2mm以上的气泡就是这样形成的.不同直径气泡上浮速度和所需时间不一样。
玻璃的熔制及熔-1
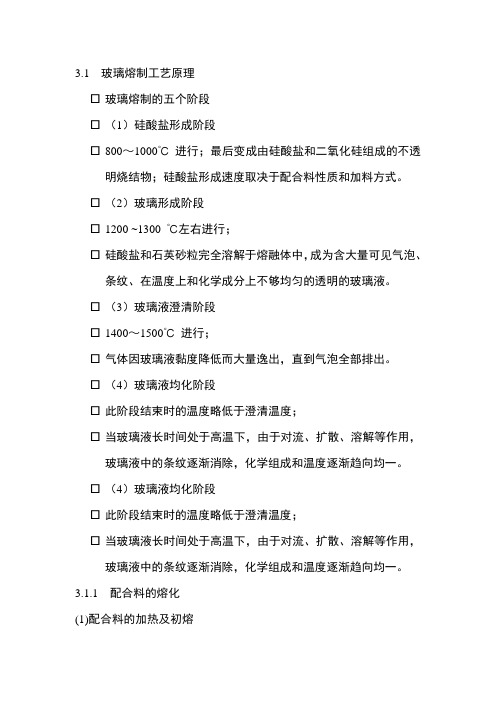
3.1 玻璃熔制工艺原理☐玻璃熔制的五个阶段☐(1)硅酸盐形成阶段☐800~1000℃进行;最后变成由硅酸盐和二氧化硅组成的不透明烧结物;硅酸盐形成速度取决于配合料性质和加料方式。
☐(2)玻璃形成阶段☐1200 ~1300 ℃左右进行;☐硅酸盐和石英砂粒完全溶解于熔融体中,成为含大量可见气泡、条纹、在温度上和化学成分上不够均匀的透明的玻璃液。
☐(3)玻璃液澄清阶段☐1400~1500℃进行;☐气体因玻璃液黏度降低而大量逸出,直到气泡全部排出。
☐(4)玻璃液均化阶段☐此阶段结束时的温度略低于澄清温度;☐当玻璃液长时间处于高温下,由于对流、扩散、溶解等作用,玻璃液中的条纹逐渐消除,化学组成和温度逐渐趋向均一。
☐(4)玻璃液均化阶段☐此阶段结束时的温度略低于澄清温度;☐当玻璃液长时间处于高温下,由于对流、扩散、溶解等作用,玻璃液中的条纹逐渐消除,化学组成和温度逐渐趋向均一。
3.1.1 配合料的熔化(1)配合料的加热及初熔(2)各种反应简介多晶转变盐类分解水分的逸出(3)成分的挥发R2O的挥发由纯碱引入时:引入量×0.032%由芒硝引入时:引入量×0.06% ☐另外要考虑氧化铈、煤粉的挥发量。
☐(4)影响配合料熔化的因素☐熔化温度:温度每升高10℃,反应速度增加☐10%;☐原料的形式:颗粒度的搭配、加料方式;☐原料的易熔性:助熔剂的多少、原料的活性;3.1.2 玻璃的形成☐(1)玻璃的形成过程☐玻璃的形成过程的速度取决于石英颗粒的熔解和扩散速度。
☐助溶剂的多少(熔化速度);☐熔体的黏度(扩散速度);☐熔体温度(熔化速度);☐石英颗粒(熔解快慢)。
3.1.3 澄清☐(1)目的☐消除玻璃液中的气泡☐(2)玻璃液中的气泡形态和种类☐形态:可见气泡、溶解气泡、化学结合的气☐体。
还有熔体表面上的气体。
☐种类:CO2、SO2、SO3、N2、O2、H2O、H2☐(3) 排泡与去气☐澄清是排出玻璃液中的可见气泡;☐去气是全部排除玻璃液中的气体,包括化学结合的气体。